
8544
.pdf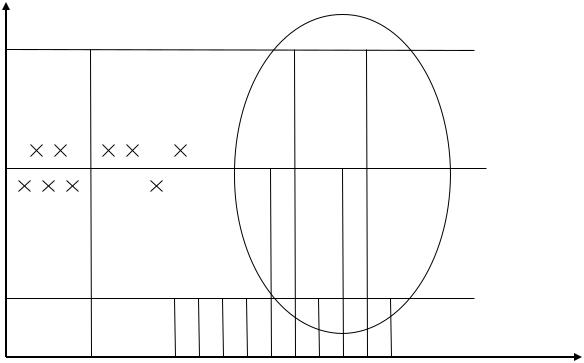
необходимости остановки производства и проведении корректировки процесса в соответствии со знаниями специалиста, управляющего производством.
Однако в этом случае решение о корректировке принималось тогда, когда брак уже был получен. Контрольная карта (рис.3) состоит из центральной линии, двух контрольных пределов (над и под центральной линией) и значений характеристики
(показателя качества), нанесенных на карту для представления состояния процесса.
Верхний
предел
Центральная
линия
|
|
|
Нижний |
|
|
|
предел |
|
Рис.3. Контрольная карта |
|
|
В определенные периоды |
времени отбирают |
(все подряд; выборочно; |
|
6 |
11 12 13 14 |
15 16 17 18 19 20 |
Номер выборки |
периодически из непрерывного потока и т. д.) n изготовленных изделий и измеряют контролируемый параметр. Результаты измерений наносят на контрольную карту, и
в зависимости от этого значения принимают решение о корректировке процесса или о продолжении процесса без корректировок.
Сигналом о возможном сбое технологического процесса могут служить:
1)выход точки за контрольные пределы (точка 6): процесс вышел из-под контроля;
2)расположение группы последовательных точек около одной контрольной границы, но не выход за нее (11, 12, 13, 14), что свидетельствует о нарушении уровня настройки оборудования;
3)сильное рассеяние точек (15, 16, 17, 18, 19, 20) на контрольной карте относительно средней линии, что свидетельствует о снижении точности технологического процесса.
При наличии сигнала о нарушении производственного процесса должна быть выявлена и устранена причина нарушения. Таким образом, контрольные карты используются для выявления определенной причины, но не случайной. Под
40
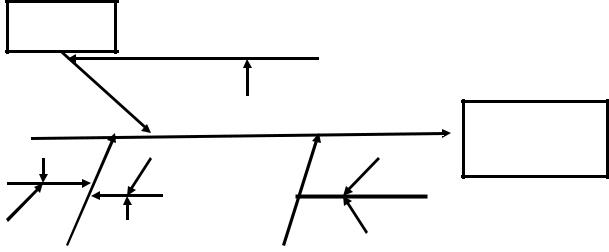
определенной причиной следует понимать существование факторов, которые допускают изучение.
Часто при определении факторов, влияющих на какой-либо результативный показатель, характеризующий качество, используют схемы Исикавы. Они были предложены профессором Токийского университета Каору Исикава в 1953 г. при анализе различных мнений инженеров. Иначе схему Исикавы называют диаграммой причин и результатов, диаграммой «рыбий скелет», деревом и т. д.
Она состоит из показателя качества, характеризующего результат, и
факторных показателей (рис.4).
«Крупная кость»
Основной
показатель
качества
Факторные |
|
Результат |
показатели |
|
|
|
|
|
Рис. 4. Структура диаграммы причин и результатов Построение диаграмм включает следующие этапы:
– Выбор результативного показателя, характеризующего качество изделия
(процесса и т. д.).
–Выбор главных причин, влияющих на показатель качества. Их необходимо поместить в прямоугольники «большие кости».
–Выбор вторичных причин «средние кости», влияющих на главные.
–Выбор (описание) причин третичного порядка «мелкие кости», которые влияют на вторичные.
–Ранжирование факторов по их значимости и выделение наиболее важных.
Диаграммы причин и результатов имеют универсальное применение. Так, они широко применяются при выделении наиболее значимых факторов, влияющих,
например, на производительность труда.
Отмечается, что число существенных дефектов незначительно, и вызываются они, как правило, небольшим количеством причин. Таким образом, выяснив причины
41

появления немногочисленных существенно важных дефектов, можно устранить почти все потери.
Эта проблема может решаться с помощью диаграмм Парето. Диаграмма Парето – это схема, построенная на основе группирования по дискретным признакам, ранжированная в порядке убывания и показывающая кумулятивную частоту.
Различают два вида диаграмм Парето:
1)По результатам деятельности. Они служат для выявления главной проблемы
иотражают нежелательные результаты деятельности (дефекты, отказы и т. д.).
2)По причинам (факторам). Они отражают причины проблем, которые возникают в ходе производства.
Рекомендуется строить много диаграмм Парето, используя различные способы классификации как результатов, так и причин, приводящих к этим результатам.
Лучшей следует считать такую диаграмму, которая выявляет немногочисленные,
существенно важные факторы, что и является целью анализа Парето.
Построение диаграмм Парето включает следующие этапы:
1. Выбор вида диаграммы (по результатам деятельности или по причинам,
факторам).
2.Классификация результатов (причин). Разумеется, что любая классификация имеет элемент условности, однако большинство наблюдаемых единиц какой-либо совокупности не должны попадать в строку «прочие».
3.Определение метода и периода сбора данных.
4.Разработка контрольного листка для регистрации данных с перечислением видов собираемой информации. В нем необходимо предусмотреть свободное место для графической регистрации данных.
5.Ранжирование данных, полученных по каждому проверяемому признаку в порядке значимости. Группу «прочие» следует приводить в последней строке вне зависимости от того, насколько большим получилось число.
6.Построение столбиковой диаграммы (рис. 5).
Значительный интерес представляет построение диаграмм Парето в сочетании с диаграммой причин и следствий. Выявление главных факторов, влияющих на качество продукции, позволяет увязать показатели производственного качества с каким-либо показателем, характеризующим потребительское качество.
Число дефектных изделий
42
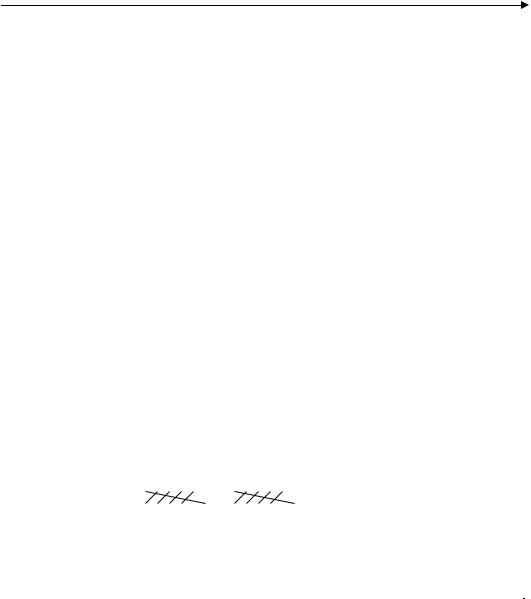
|
|
|
|
|
|
|
|
|
|
|
|
|
|
|
|
|
|
|
|
|
|
|
|
|
|
|
|
|
|
Г |
Б |
В |
А |
Прочие Виды дефектов |
Рис. 5. Связь между видами дефектов и числом дефектных изделий (диаграмма Парето)
Гистограмма – это графический метод представления данных,
сгруппированных по частоте попадания в определенный интервал. Она используется для получения распределения значения показателя качества, вычисление средних значений и дисперсии. Метод гистограмм является эффективным инструментом обработки данных и предназначен для текущего контроля качества в процессе производства, изучения возможностей технологических процессов, анализа работы отдельных исполнителей и агрегатов.
Контрольный лист – это бланк, на котором предварительно отмечены контролируемые параметры (рис. 6), с тем, чтобы можно было быстро и точно записать данные измерений, при этом автоматически упорядочить данные для облегчения их дальнейшего использования.
Типы дефектов |
Группы данных |
Итого по типам дефектов |
|
||
|
|
|
А. Трещины |
|
10 |
Б. |
|
|
В. |
|
|
Г. |
|
|
Прочее |
|
|
Итого |
|
100 |
Рис. 6. Контрольный лист
Диаграммы рассеивания (разброса) основаны только на достоверных данных, применяются для получения корректной информации, выявления причинно-
следственных связей. Представляют собой графики, которые позволяют выявить корреляцию между двумя различными факторами.
При разделении данных на группы в соответствии с их особенностями группы
43
именуют слоями (стратами), а сам процесс разделения расслаиванием
(стратификацией). Желательно, чтобы различия внутри слоя были как можно меньше, а между слоями как можно больше.
В результатах измерений всегда есть больший или меньший разброс параметров. Если осуществлять стратификацию по факторам, порождающим этот разброс, легко выявить главную причину его появления, уменьшить его и добиться повышения качества продукции.
Применение различных способов расслаивания зависит от конкретных задач.
В производстве часто используется способ, называемый 4М, учитывающий факторы,
зависящие от: человека (man); машины (machine); материала (material); метода
(method).
То есть расслаивание можно осуществить так:
–по исполнителям (по полу, стажу работы, квалификации);
–по машинам и оборудованию (по новому или старому, марке, типу);
–по материалу (по месту производства, партии, виду, качеству сырья);
–по способу производства (по температуре, технологическому приему).
Метод расслаивания в чистом виде применяется при расчете стоимости изделия, когда требуется оценка прямых и косвенных расходов отдельно по изделиям и партиям, при оценке прибыли от продажи изделий отдельно по клиентам и по изделиям и т.д. Расслаивание также используется в случае применения других статистических методов: при построении причинно-следственных диаграмм,
диаграмм Парето, гистограмм и контрольных карт.
2.5. Статистические методы контроля качества
Тема: Статистические методы контроля качества
Целью методов статистического контроля является исключение случайных изменений качества продукции. Такие изменения вызываются конкретными причинами, которые нужно установить и устранить. Статистические методы контроля качества подразделяются на:
1)статистический приемочный контроль по альтернативному признаку;
2)выборочный приемочный контроль по варьирующим характеристикам
качества;
3)стандарты статистического приемочного контроля;
4)система экономических планов;
5)планы непрерывного выборочного контроля;
6)методы статистического регулирования технологических процессов.
44
Каждая из разновидностей статистических методов контроля качества имеет свои преимущества и недостатки. Например, выборочный приемочный контроль по варьирующим характеристикам имеет то преимущество, что требует меньшего объема выборки. Недостаток этого метода заключается в том, что для каждой контролируемой характеристики нужен отдельный план контроля. Если каждое изделие проверяется по пяти характеристикам качества, необходимо иметь пять отдельных планов проверок.
Основной характеристикой партии изделий, в отношении которой применяется статистический приемочный контроль по альтернативному признаку является генеральная доля дефектных изделий.
q = D / N, (1)
где D – число дефектных изделий в партии объемом N изделий.
В практике статистического контроля генеральная доля q неизвестна и ее следует оценить по результатам контроля случайной выборки объемом n изделий, из которых m дефектных.
Под планом статистического контроля понимают систему правил,
указывающих методы отбора изделий для проверки, и условия, при которых партию следует принять, забраковать или продолжить контроль. Различают следующие виды планов статистического контроля партии продукции по альтернативному признаку:
– одноступенчатые планы, согласно которым, если среди n случайно отобранных изделий число дефектных m окажется не больше приемочного числа С
(m ≤ C), то партия принимается; в противном случае партия бракуется;
– двухступенчатые планы, согласно которым, если среди n1 случайно отобранных изделий число дефектных m1 окажется не больше приемочного числа C1
(m1 ≤ C1), то партия принимается; если m1 ≥ d1, где d1 браковочное число, то партия бракуется. Если же C1 < m1 < d1, то принимается решение о взятии второй выборки объемом n2. Тогда, если суммарное число изделий в двух выборках (m1 + m2) ≤ C2, то партия принимается, в противном случае партия бракуется по данным двух выборок;
– многоступенчатые планы являются логическим продолжением двухступенчатых. Первоначально берется выборка объемом n1, и определяется число дефектных изделий m1. Если m1 ≤ C1, то партия принимается. Если m1 ≥ d1 (d 1 >
C1+1), то партия бракуется. Если C1 < m1 < d1, то принимается решение о взятии второй выборки объемом n2. Пусть среди n1 + n2 имеется m2 дефектных изделий.
Тогда, если m2 ≤ c2, где c2 второе приемочное число, партия принимается; если m2 ≥ d2 (d2 > c2 + 1), то партия бракуется. При c2 < m2 < d2 принимается решение о
45
взятии третьей выборки. Дальнейший контроль проводится по аналогичной схеме, за исключением последнего k–того шага.
На k–м шаге, если среди проконтролированных изделий выборки оказалось mk дефектных, и mk ≤ ck, то партия принимается; если, же mk > ck, то партия бракуется. В многоступенчатых планах с числом шагов k принимается, что n1
=n2=...= nk;
– последовательный контроль, при котором решение о контролируемой партии принимается после оценки качества выборок, общее число которых заранее не установлено и определяется в процессе контроля по результатам предыдущих выборок.
Одноступенчатые планы проще в смысле организации контроля на производстве. Двухступенчатые, многоступенчатые и последовательные планы контроля обеспечивают при том же объеме выборки большую точность принимаемых решений, но они более сложны в организационном плане.
Для успешного применения статистических методов контроля качества продукции большое значение имеет наличие соответствующих руководств и стандартов, которые должны быть доступны широкому кругу инженерно– технических работников. Стандарты на статистический приемочный контроль обеспечивают возможность объективно сравнивать уровни качества партий однотипной продукции как во времени, так и по различным предприятиям.
Остановимся на основных требованиях к стандартам по статистическому приемочному контролю.
Прежде всего, стандарт должен содержать достаточно большое число планов,
имеющих различные оперативные характеристики. Это важно, так как позволит выбирать планы контроля с учетом особенностей производства и требований потребителя к качеству продукции. Желательно, чтобы в стандарте были указаны различные типы планов: одноступенчатые, двухступенчатые, многоступенчатые,
планы последовательного контроля.
Основными элементами стандартов по приемочному контролю являются:
1.Таблицы планов выборочного контроля, применяемые в условиях нормального хода производства, а также планов для усиленного контроля в условиях разладок и для облегчения контроля при достижении высокого качества.
2.Правила выбора планов с учетом особенностей контроля.
3.Правила перехода с нормального контроля на усиленный или облегченный и обратного перехода при нормальном ходе производства.
4. Методы вычисления последующих оценок показателей качества
46
контролируемого процесса.
Первая система планов статистического приемочного контроля, нашедшая широкое применение в промышленности, была разработана Доджем и Ролигом.
Планы этой системы предусматривают сплошной контроль изделий из забракованных партий и замену дефектных изделий годными.
Во многих странах получил распространение американский стандарт МИЛ– СТД–ЛО5Д. Отечественный стандарт ГОСТ–18242-72 по построению близок к американскому и содержит планы одноступенчатого и двухступенчатого приемочного контроля. В основу стандарта положено понятие приемлемого уровня качества (ПРУК), которое рассматривается как максимально допустимая потребителем доля дефектных изделий в партии, изготовленной при нормальном ходе производства.
При контроле изделий по нескольким признакам стандарт рекомендует классифицировать дефекты на три класса: критические, значительные и малозначительные.
2.6. Система управления качеством
Тема: Система управления качеством
Системы управления качеством на предприятиях появились в связи с развитием деятельности по управлению качеством продукции. Ужесточающаяся конкуренция и осознание роли качества как основы конкурентоспособности вынуждали предприятия перейти от отдельных разрозненных элементов управления качеством к их объединению в единую, комплексную систему управления — с
учётом всех факторов, влияющих на качество. В результате система качества получила статус одной из систем управления предприятием, наряду с системами управления персоналом, производством, снабжением и другими.
Внедрение системы качества позволяет организовать и проводить плановую,
регулярную работу по качеству. При наличии необходимой материальной базы,
современной технологии и квалифицированного, заинтересованного персонала, это повышает стабильность качества всей выпускаемой продукции, а не только отдельных образцов для выставок и презентаций. Такая система служит дополнительной гарантией качества для заказчиков, многие из которых практикуют проверку систем качества у потенциальных поставщиков, результаты которой могут влиять на заключение контрактов. Распространение подобных взаимоотношений поставщиков с заказчиками в мировой торговле привело к появлению серии международных стандартов ИСО 9000 на системы качества, а затем — к
47
возникновению и развитию сертификации этих систем независимыми органами.
Система менеджмента качества — это совокупность взаимосвязанных и взаимодействующих элементов для разработки политики и целей и достижения этих целей, для руководства и управления организацией применительно к качеству. В
качестве элементов системы менеджмента качества, как правило, выделяют организационную структуру, ответственность, процедуры, процессы и ресурсы,
обеспечивающие управление качеством.
Создать систему качества означает разработать и внедрить её в деятельность предприятия. При создании системы качества требуется выполнить значительный объём работ, который будет зависеть от размеров предприятия, особенностей производства и характера выпускаемой продукции и от того, насколько действующая на предприятии организация работ по качеству соответствует рекомендациям стандарта ИСО 9001 или соответствующего отраслевого стандарта.
Основным документом системы качества является "Руководство по качеству",
где содержится описание системы качества, структура ее документации, методики или ссылки на них. Указания по разработке "Руководства по качеству" содержатся в
ISO 10013.
Выполнение всех предусмотренных стандартом требований должно быть документально оформлено в виде методик. Кроме разработки методик, на предприятии должны быть разработаны и документально оформлены программы периодического анализа соответствия процессов, методов, оборудования,
квалификации персонала требованиям действующей документации, методики принятия соответствующих корректирующих мероприятий.
Документация управления качеством подразделяется на три уровня. К
документам первого (высшего) уровня относятся "Руководство по качеству" и "Политика в области качества". В "Руководстве по качеству" содержится информация о системе качества предприятия, роли и ответственности персонала в области обеспечения качества. В этот документ также входят методики координации работ по обеспечению качества. Руководство издается в виде самостоятельного документа и утверждается на уровне высшего руководства фирмы. Основным назначением
"Руководства по качеству" является определение общей структуры Системы качества и выполнение функции постоянного справочного материала при внедрении и организации функционирования этой системы (ДСТУ ISO 9004-1-95 5.3).
Документация второго уровня — это методики и инструкции, которые описывают процедуры выполнения требований стандартов ISO серии 9000. В
основном предназначается для руководителей среднего звена.
48
Документация третьего уровня предназначена для конкретных подразделений,
участков, рабочих мест. Это документация методологического, инструктивного и руководящего характера. Вся документация взаимосвязана и скоординирована в
"Руководстве по качеству", направлена на достижение целей, изложенных в
"Политике в области качества".
Функционирование системы качества — это выполнение руководством предприятия и подразделений своих функций в системе качества. Поскольку в реализации функций системы качества в той или иной мере участвуют практически все подразделения предприятия, возникает необходимость планирования,
координации и методического обеспечения работ подразделений в системе качества.
Кроме этого нужно проводить внутренние проверки и совершенствовать систему,
организовывать деятельность кружков качества, представлять систему качества на переговорах с заказчиками, а также — проводить сертификацию продукции и системы качества. Иначе говоря, нужно решать целый ряд задач по «обслуживанию» самой системы качества. В связи с этим следует опасаться чрезмерного увлечения этой деятельностью со стороны службы качества в ущерб выполнению содержательных функций.
В процессе функционирования системы качества руководством предприятия в соответствии со стандартом ИСО 9001 (пункт 5.6) должен проводиться периодический анализ и оценка эффективности системы качества. Для этого используется обратная связь с потребителями, результаты внутренних проверок, а
также аудитов со стороны заказчиков и сертификационных органов. Главными критериями эффективности системы качества служат: обеспечение и постоянное улучшение качества продукции на основе имеющейся материальной базы и персонала, снижение потерь от брака и рекламаций, темпы модернизации и обновления выпускаемой продукции, внедрение достижений науки и техники,
положительные отзывы потребителей и заказчиков.
3. Эволюция подходов к управлению качеством
3.1. Классическая и современная философия качества
Тема: Классическая и современная философия качества
В истории философии качества существуют четыре перекрывающиеся и
49