
- •1.1. Організаційні форми та методи проектування
- •1.1. Організаційні форми та методи проектування
- •1.2. Блок-схема етапів проектування. Програмно-цільова структура проектування
- •Рис. 1.2. Блок-схема процесу проектування
- •Одержано
- •Вимоги до змісту технічного регламенту
- •Позначка
- •Найменування
- •Примітка
- •Глибинний спосіб вирощування
- •Культивування умовно-асептичне
- •Вибір ферментеру
ж розділу, незалежно від того, чи є методика самостійним аналітичним методом, фрагментом характеристики на готову продукцію чи стандарт підприємства на напівпродукт.
У колонці 4 зазначають періодичність та порядок відбирання проб речовин: від кожної технологічної операції чи від кількох – при періодичних процесах, через який проміжок часу - при безперервних процесах.
Колонка 5 містить конкретний нормативний параметр (показник) операції чи стадії технологічного процесу або припустимі його інтервали. Виконання цих вимог відображається у протоколі виготовленнясерії. Рекомендовані з
урахуванням зазначеного на підприємствіформи таких протоколів (операційних листків) для кожної стадії (операції) складають окремий додаток до технологічного регламенту.
Складовою частиною блоку нормативно технічних документів які відповідають вимогам ГНД є технічний регламент. Далі по тексту наведені ті розділи регламенту, які використовуються у курсових та дипломних проектах.
Вимоги до змісту технічного регламенту
1.Загальна характеристика виробництва.
2.Апаратурна схема, специфікація обладнання та КВП.
3.Загальна схема системи контролю якості.
4.Безпечна експлуатація виробництва та охорона навколишнього се-
редовища.
Загальна характеристика виробництва. У цьому розділі наводиться інформація, стосовно таких показників: повна назва виробництва, цеху, рік введення в експлуатацію, потужність виробництва (проектна та фактична на час створення регламенту або розробки курсових та дипломних проектів), за яким проектом побудовано, за яким останнім проектом реконструйовано і здано в експлуатацію (яким документом, ким і коли затверджено).
Необхідно навести перелік продукції, яка виготовляється чи планується до виготовлення за даним технічним регламентом
До технічного регламенту додається креслення , цехудільниці, де виготовляється продукція у М1:100, М1:200 або М1:400 з характеристикою приміщень за таблицею 3.5.
Представленню таблиці передує |
вибір |
класів |
чистоти виробничих |
|||||||
приміщень в залежності від типів робіт, які в них проводяться. |
|
|
|
|||||||
Таблиця 3.5. |
Характеристика виробничих приміщень |
|
|
|
||||||
|
|
|
|
|
|
|
|
|
|
|
Найменування |
|
Техноло- |
Клас чис- |
|
Категорія |
|
Клас зон |
Додатко |
||
|
гічні |
|
з ОНТП 24- |
|
ві вимо- |
|
||||
приміщень |
|
тоти |
|
|
за ПУЕ |
|
||||
|
блоки |
|
86 |
|
ги |
|
||||
|
|
|
|
|
|
|
|
|||
1 |
|
2 |
3 |
|
4 |
|
5 |
|
6 |
|
Основне і допоміжне технологічне обладнання, контрольно-вимірювальні пристрої, транспортні засоби, технологічний одяг та оснащення приміщень повинні відповідати класу чистоти, категорії приміщень з вибухопожеженебез-
43
пеки, класу вибухопожеженебезпечних зон, додатковим технологічним умовам, наведеним у таблиці (табл 3.5.).
Апаратурна схема, специфікація обладнання та КВП
Апаратурна схема (АС) представляє собою графічне зображення технологічного процесу у вигляді умовних позначень апаратів та трубопроводів у відповідності з вимогами ГОСТ, ДСТУ, ГСТУ, ОСТ. Послідовність розташування апаратури на АС відповідає стадіям та операціям ТС. Точки контролю на
АС відповідають точкам контролю на ТС і супроводжуються відповідними контрольно вимірювальними приладами.
В цьому розділі регламенту(проекту) наводяться креслення апаратурної схеми виробництва та відомості специфікації обладнання, представленого на
кресленні, умовні |
позначення матеріальних комунікацій(трубопроводів), |
|
позиції контролю |
та регулювання технологічних параметрів, технологічних |
|
елементів сигналізації і |
блокування, місць відбору проб, а також контрольно- |
|
вимірювальних приладів |
і засобів протиаварійного захисту. |
Апаратурна схема виробництва входить у графічну частину проекту, а відомість специфікації обладнання та контрольно – вимірювальних приладів, як складова АС наводиться у пояснювальній записці.
Існує ряд вимог стосовно визначення специфіки будівель, тому на кресленні АС наводяться поверхові відмітки.
Трубопроводи показують у вигляді магістральних(у верхній частині креслення) та місцевих, які з’єднують магістральні трубопроводи з апаратурою.
Креслення апаратурної схеми повинне відобразити все технологічне обладнання, включаючи допоміжне (допоміжні збірники, теплообмінна апаратура, аварійні місткості, насоси, компресори тощо).
На схемі не наводиться обладнання, яке використовується в кількох виробництвах (наприклад, складські місткості заводу, централізовані станції для отримання води фармацевтичної якості). У цьому разі на кресленні стрілкою з написом показують, звідки надходить сировина, повітря та ін.).
У технологічних процесах з великою кількістю обладнання і приладів дозволяється креслити кожну стадію окремо, не розриваючи індексацію.
Обладнання та прилади показують і нумерують на кресленнях послідовності, що відповідає ходу технологічного процесу. Все обладнання нумерують, використовуючи позначення з використанням літер, які визначають тип обладнання (індекс), з додаванням арабської цифри, яка позначає порядковий номер у схемі. Умовні позначення обладнання та приладів хімікофармацевтичних виробництв повинні відповідати документаціїЄСКД, ОСТ 64-043-87 та ГОСТ 21.404-85. У разі відсутності стандартного умовного графічного позначення будь-якого обладнання використовується умовне позначення з бажаним зображеннямконструкційних особливостей у вигляді
фронтальної проекції апарату. |
|
|
|
|
||
На |
апаратурі |
та |
трубопроводах |
зображуються |
всі |
-контроль |
вимірювальні прилади та система автоматизації (КВП та СА), технологічні еле-
44
менти сигналізації і блокування, засоби протиаварійного захисту, а також місця |
|
|||||||||||||||
відбору проб для аналізів, |
потрібних для забезпечення надійного контролю та |
|
||||||||||||||
керування технологічним процесом. |
|
|
|
|
|
|
|
|
|
|
|
|
||||
Контрольно-вимірювальні та регулювальні прилади нумерують так, як і |
|
|||||||||||||||
технологічне обладнання, використовуючи індекс та |
порядковий |
номер |
по |
|||||||||||||
схемі. Контрольні точки на схемі позначають індексом(контрольКт |
|
|||||||||||||||
технологічний) та Кх (контроль хімічний) з наскрізною нумерацією. |
|
|
|
|
||||||||||||
Апаратурну схему обов’язково |
супроводжує відомість специфікацій об- |
|
||||||||||||||
ладнання, КВП та |
СА(табл. 3.6) |
з |
їх |
технічними |
характеристиками, яка |
|
||||||||||
виконується за формою 1 ГОСТ 21.104-79. |
|
Форма 1 по ГОСТ 21.104-79 |
|
|||||||||||||
|
|
|
|
|
|
|
|
|
||||||||
Таблиця 3.6. Специфікація обладнання та КВП |
|
|
|
|
|
|
|
|||||||||
|
|
|
|
|
|
|
|
|
|
|
|
|
|
|
|
|
Позиція |
|
Позначка |
Найменування |
|
Кіль- |
|
Маса |
|
Примітка |
|
|
|
||||
|
|
кість |
|
|
|
|
||||||||||
|
|
|
|
|
|
|
|
|
|
|
|
|
|
|
|
|
1 |
|
2 |
|
|
3 |
|
|
4 |
|
5 |
|
|
6 |
|
|
|
|
|
|
|
|
|
|
|
|
|
|
|
|
|
|
|
|
У колонці 1 наводять індекс та номер за схемою обладнання та КВП. У |
|
|||||||||||||||
колонці 2 зазначають: для стандартного обладнання та приладівпозначення |
|
|||||||||||||||
нормативно-технічної документації, тип, марку та шифр; для нестандартного - |
|
|||||||||||||||
номер креслення, імпортного - марку, шифр, які відповідають чинному норма- |
|
|||||||||||||||
тивно-технічному документу. Якщо в апаратурній схемі наведено декілька оди- |
|
|||||||||||||||
ниць однакового обладнання та КВП, то у колонках2, 3, 6 вони описуються |
|
|||||||||||||||
лише одноразово із зазначенням кількості одиниць у колонці4 та всіх індексів |
|
|||||||||||||||
та номерів за схемою у колонці1. У колонці 3 наводять коротку технічну ха- |
|
|||||||||||||||
рактеристику обладнання та КВП. |
Для окремих груп обладнання та приладів |
|
||||||||||||||
рекомендовано наводити такі відомості: Для сховищ-збірників та мірників- |
|
|||||||||||||||
місткість, спосіб наповнення продуктом (заливання, заповнення під вакуумом, |
|
|||||||||||||||
закачування насосом тощо), спосіб передачі продукту в інший апарат(спуск |
|
|||||||||||||||
самопливом, перетискання стиснутим повітрям тощо); якщо місткості працю- |
|
|||||||||||||||
ють під тиском, зазначають робочий тиск, тип оглядового або вимірювального |
|
|||||||||||||||
пристрою. Якщо для вимірювання рідин, що надходять в апарат, замість |
|
|||||||||||||||
мірника використовується автоматичний пристрій, змонтований безпосередньо |
|
|||||||||||||||
на трубопроводі, то у |
характеристиці |
|
такого |
пристрою |
наводять |
його |
||||||||||
продуктивність та габаритні розміри. |
|
|
|
|
|
|
|
|
|
|
|
|||||
Для автоклавів, реакторів, випарних апаратів - тип реактора (особливості |
|
|||||||||||||||
конструкції), робочий тиск, місткість. |
|
|
|
|
|
|
|
|
|
|
|
|||||
Для апаратів безперервної діїпродуктивність, спосіб нагрівання або |
|
|||||||||||||||
охолодження |
із |
зазначенням |
площі |
|
поверхні |
теплообміну |
або |
способ |
вимірювання температури, тип та частота обертання мішалки, пристрою для завантаження, розвантаження, огляду, габаритні розміри.
45
Для теплообмінників (нагрівачів та холодильників) – тип конструкції (змійовиковий, трубчастий, «труба у трубі», пластинковий тощо), площу поверхні теплообміну, габаритні розміри.
Для фільтрувальної апаратури– конструкцію фільтру, фільтруючий матеріал, площу фільтруючої поверхні, максимальну масу (місткість) відфільтрованого продукту (осаду), продуктивність для фільтрів безперервної дії.
Для ректифікаційних колон– тип конструкції (тарілчасті, насадкові, ротаційні тощо, періодичної чи безперервної дії), висоту, діаметр, кількість та форму тарілок та тарілчастих колон; діаметр, висоту, спосіб формування плівки, площі поверхні теплообміну, робочий тиск.
Для сушарок – тип конструкції (камерна, валкова, вакуумна, з псевдокиплячим шаром, розпилювальна тощо), спосіб нагрівання та площа поверхні нагрівання, спосіб завантаження та вивантаження, габаритні розміри.
Для розмелювального обладнання – конструкцію, продуктивність, спосіб завантаження та вивантаження, габаритні розміри; пристрій для попередження пиловиділення, споживану потужність та частоту обертання.
Для допоміжного стандартного обладнання – компресорів, повітродувок, насосів для транспортування продукту, вакуумних насосів, обладнання холодильних установок – продуктивність, споживану потужність, частоту обертання.
Для контрольно-вимірювальних та регулюючих приладів– тип регулювання, діапазон вимірювань, клас точності, особливості конструктивного виконання та роботи приладу. Для транспортних пристосувань– конструкцію, продуктивність, потужність двигуна.
Для електричних та електрифікованих апаратів та приладів, які встановлюються в блоках усіх категорій вибухонебезпеки, у колонці 3 необхідно додатково зазначати виконання виробу щодо вибухозахисту. У колонці 6 зазначається категорія вибухонебезпеки технологічних апаратів, яка вважається такою ж, як і категорія того технологічного блоку, до складу якого входить даний апарат. Для апаратів, які підлягають контролю Держнагляду за охороною праці, у колонці 6 зазначається також реєстраційний номер апарату.
Комплектні технологічні лінії, установки, наприклад, для ректифікації, молекулярної дистиляції, вакуум-випарювання, знесолення води тощо надаються в одній позиції з наступним переліком назв комплектуючих виробів, які входять до цієї установки. Для обладнання та приладів у колонці6 зазначають матеріал робочої зони обладнання та приладу(датчика), тобто тих частин обладнання та приладу, які мають безпосередній контакт з речовинами, реакційними масами або продуктами, що виділяються у процесі виробництва. Якщо у робочій зоні використовується антикорозійний захист, надається коротка характеристика цього захисту.
У колонці 3 також наводять назву заводу, фірми, країни - виготовлювача обладнання та назву підприємства-розробника нестандартизованого обладнання.
46

На апаратурній схемі також повинні бути відображені сигналізатори, які сповіщають про нерегламентовану зміну технологічних параметрів, що можуть призвести до аварійних ситуацій; сигналізатори довибухонебезпечних концентрацій, газоаналізатори ГДК.
Безпечна експлуатація виробництва та охорона навколишнього середовища
У регламенті необхідно відображати заходи, які забезпечують надійність охорони навколишнього середовища в період експлуатації та у випадках аварійних ситуацій і зупинок виробництва на ремонт.
Позначається наявність систем очистки технологічних та вентиляційних
викидів |
від |
забруднюючих |
речовин |
і |
ефективність очистки, газу(пилу, |
|||||
аерозолів |
тощо), |
аварійних та |
дренажних |
ємностей, піддонів, факелів, |
||||||
абсорбентів тощо, попереджувальних засобів для уникнення залпових викидів |
||||||||||
до довкілля. |
За |
можливості |
переробки |
аварійних |
та |
дренажних |
стоків |
|||
зазначається, куди вони спрямовуються(очищення, утилізація, |
складування). |
|||||||||
Залповим |
викидом у |
повітря вважається |
викид |
забруднюючих |
,речовин |
|||||
тривалість |
якого |
не |
перевищує20 хвилин |
протягом |
робочої зміни, а |
концентрація забруднюючих речовин більш, ніж у 2 рази перевищує звичайну, регламентовану концентрацію у заданій точці контролю.
У технічному регламенті для окремих типівтехнологічного та іншого обладнання встановлюються граничні обсяги утворення забруднюючих речовин, які організовано виводяться до джерела викиду в атмосферне повітря при експлуатації технологічного обладнання. Показник встановлює граничні значення концентрації забруднюючих речовин у мг/м3 і розраховуються як середні значення часових вимірів у трубопроводі перед газопилоуловлювачами і після
них або безпосередньо у джерелі .викидуПерелік |
такого |
обладнання |
визначається галузевими нормативними документами. |
|
|
Регламентовані норми викидів забруднюючих |
речовин |
на одиницю |
продукції надаються у інформаційних матеріалах до технічного регламенту відповідно до номенклатури виготовлення продукції і наводяться у вигляді таблиці 3.7.
Таблиця 3.7. Регламентні норми викидів забруднюючих речовин
(вказується найменування та кількість продукції, на яку складається норма).
Найменування забруд- |
Один. |
Норма викидів, г/од. продукту |
|||
нюючих речовин |
виміру |
||||
|
|
|
|||
|
|
у повітря |
у воду |
на сховище |
|
|
|
|
|
|
47
Характеристика стоків наводиться у таблиці 3.8. До таблиці вносяться усі технологічні стоки, стоки від промивання обладнання та змивання підлог.
Таблиця 3.8. Характеристика стічних вод
|
|
|
|
Характеристика |
Куди |
||
Найме- |
|
Періоди |
Кількість |
скидаєт |
|||
Відділенн |
стоку |
||||||
нування |
чність |
стоків, |
ься |
||||
я, апарат |
|
|
|||||
стоку |
скиду |
м3/доба |
|
|
|
||
Забруд- |
Конц., |
|
|||||
|
|
|
|
нення |
мг/л |
|
|
1 |
2 |
3 |
4 |
5 |
6 |
7 |
|
|
|
|
|
|
|
|
Контроль складу та кількість промислових стоків, пилогазоподібних викидів та відходів виробництва слід передбачати для всіх процесів.
[4], [5], [6], [7], [8]
Запитаня для самоперевірки
1.Які існують типи регламентів виробництва, їх склад?
2.Вимоги до оформлення регламентів на продукцію медичної та мікробіогі чної промисловості.
3.Вимоги до технологічної схеми виробництва. Основні стадії технологічного процесу.
4.Склад регламенту виробництва: характеристика сировини, матеріалів та напівпродуктів.
5.Що показує апаратурна схема виробництва?
4.В чому полягає опис стадій технологічного процесу?
5.Що представляє собою матеріальний баланс партії, серії.
6.В чому суть контролю виробництва?
48
4. ПРЕДФЕРМЕНТАЦІЙНІ ПРОЦЕСИ
Біотехнологічне виробництво, умовно розділено на декілька блоків, що визначається послідовністю їх виконання та дозволяє виявити існуючі між ними зв’язки. Ця послідовність покладена в основу технологічної схеми виробництва і представляє собою блок – схему. До таких блоків відносять:
- роботи підготовчого характеру (предферментаційні процеси) до цих робіт відносяться стадії санітарної підготовки виробництва, підготовки поживного середовища, підготовка обладнання та комунікацій, підготовки аераційного повітря та інше;
-роботи основного виробництва, до цих робіт відносяться підготовка посівного матеріалу, виробничий біосинтез, виділення цільового продукту (біологічно-активної речовини) та інше;
-в окремий блок виділені роботи по пакуванню маркуванню та відвантаженню готової продукції;
-роботи екологічного забезпечення до цих робіт відносяться роботи
по знешкодженню повітряних та рідких викидів та роботи по використанню відходів виробництва.
4.1. Санітарна підготовка виробництва
Невід’ємною частиною підготовчих робіт на біотехнологічних підприємствах є проведення робіт санітарно-гігіенічного призначення. Основним спря-
муванням |
санітарної |
підготовки виробництва є |
забезпечення мінімальної |
кількості |
контамінантів |
у всіх учасників виробничого |
процесу: в поживному |
середовищі, технологічному аераційному повітрі на поверхнях обладнання, яке контактує з культуральною рідиною, забезпечення чистоти на виробничих
ділянках де |
чистота та асептика пливають на якісні показники продукції. Ро- |
||||||||
боти санітарно-гігіенічного призначення суттєво впливають на створення без- |
|||||||||
печних умов праці і охороні здоров’я працівників підприємства . Санітарна |
|
||||||||
підготовка |
виробництва |
реалізується |
виконанням |
робіт |
по |
щоденному |
|||
позмінному |
та |
генеральному |
прибиранні |
виробничих |
|
приміщень |
централізованою підготовкою обладнання.
Для забезпечення необхідного рівня санітарного стану виробництва проводиться комплекс робіт з всіма учасниками технологічного процесу:
-складовою частиною санітарної підготовки є підготовка персоналу, як можливого джерела контамінації, при цьому персонал проходить навчання та контроль знань;
-готуються виробничі приміщення, які обробляються мийними, дезінфікуючими та мийно-дезінфекційними засобами для зниження рівняза гального забруднення та мікробної контамінації;
-готують обладнанням, яке проходить багатостадійну обробку, що включає – миття, дезінфекцію, ополіскування та стерилізацію;
-готують комунікації, які миються, стерилізуються;
49
- складовою частиною підготовки обладнання є перевірка його на герметичність та ефективність проведеної стерилізації.
Вякості дезинфікуючих засобів використовуються загальновизнані в біотехнологічній практиці речовини: розчин хлораміну, розчин їдкого натру – каустична сода та інші дезінфектанти та детергенти. На сьогоднішній день єдиним загальновизнаним способом стерилізації апаратури та комунікацій є термічна стерилізація насіченою водяною парою. Для миття внутрішніх частин обладнання, які забруднені органічними речовинами передбачене використання розчину каустичної соди.
Приготування дезинфікуючих розчинів
Вбіотехнологічних виробництвах при масовій обробці значних об’ємів обладнання та поверхонь, при обробці приміщень віддають перевагу дешевим і достатньо ефективним дезинфікуючим речовинам, таким як розчин хлорного вапна (2- 10%), розчин хлораміну Б(1-5%), для обробки обладнання і
комунікацій використовують розчин |
каустичної соди(40%), який має |
властивості дезинфікуючої речовини та детергента. |
|
Хлорне вапно — білий порошок з різким запахом, що володіє сильними |
окислювальними властивостями. Головною складовою частиною її є гіпохлорит
— кальцієва сіль хлорноватистої кислоти— Са(С1О)2, яка при взаємодії з водою розпадається утворенням високо реакційних сумішей. Згубну дію на мікрофлору надають, як хлор, так і кисень у момент його виділення. Додавання хлориду амонію в розчин хлорного вапна значно підсилює її дію. Виходить активоване хлорне вапно, витрата якого в50 разів менша, ніж хлорного вапна. Згідно ГОСТ 1692—58 хлорне вапно марок А і Б містить активного хлору35 % і марки В — 32 %.
Хлорамін Б —бензосульфохлорамід натрію—білий кристалічний порошок, добре розчинний у воді(1 :20), містить 25—29 % активного хлору (ВТУ 27/24—79—65). Він бактерицидний проти вегетативних форм в концентрації 0,25—0,5 % і температурі 30 °С, спороцидний — при 50—60°С.
Водний розчин з масовою часткою хлораміну Б (монохлораміну Б) від 0,3 до 3% використовують для обробки боксів, прилеглих приміщень, виробничих приміщень, а в технологічних приміщеннях місць, куди потрапляють компоненти поживного середовища чи культуральна рідина. Хлор у складі хлораміну Б стійко зв’язаний з органічною основою, тому при правильному зберіганні хлорамін може протягом кількох років зберігати активний хлор. Хлорамін має бактерицидні, віруліцидні і спороцидні властивості, особливо в кислому і нейтральному середовищі. Водні розчини хлораміну Б не втрачають активний хлор протягом 15 днів, тому їх можна приготувати заздалегідь. Хлорамін ХБ за хімічною будовою подібний до хлораміну. Бактерицидні і спороцидні властивості хлораміну ХБ і умови його використання такі ж, як і для хлораміну Б. Але хлорамін ХБ характеризується рядом негативних властивостей: він зумовлює подразнювальну дію на слизові оболонки дихальних шляхів з явищами отруєння, знебарвлює тканину;
Існує |
багато |
різних методів порівняння дезинфікуючих препаратів. |
Найбільше |
широко |
використовується метод фенольного коефіцієнта, який за- |
50
сновано на порівнянні інгібуючої дії фенолу і даного засобу на ріст визначених мікроорганізмів і чітко контрольованих умовах. Для фенолу приймається за 1, а ефективність використаного засобу характеризується фенольним коефіцієнтом. Так перекис водню має фенольний коефіцієнт 0,01; хлорамін – 130.
Дезінфекція приводить, як правило, до зниження рівня мікробної контамінації на 40 – 60% від початкового вмісту. При виборі дезінфікуючої речовини необхідно враховувати не тільки її бактерицидні властивості і спектр дії, а й можливу токсичність для організму людини.
Підготовка приміщень
Прибирання підлоги, зовнішньої поверхні обладнання і трубопроводів виконують використовуючи розчини антисептиків та детергентів, наприклад водним розчином хлораміну Б з концентрацією від 0,3 до 3%.
При появі дріжджової інфекції один раз в добу все робоче приміщення обробляють 1 %-ним розчином хлораміну. Цим же розчином протирають зовні апаратуру і комунікації; змочують килимки при вході у всі приміщення. Окрім боротьби із сторонньою мікрофлорою, в цеху ферментації проводять профілактичні заходи. Періодично, не рідше за один раз в тиждень, підлоги, стіни, а також поверхню апаратів, збірок, трубопроводів миють 1—2%-ним розчином хлорного вапна (рекомендується міняти антисептик).
Підготовка обладнання
Підготовка обладнання як складова санітарної підготовки виробництва направлена на досягнення необхідного рівня чистоти та асептичності. Наприклад, підготовка інокуляторів, ферментерів та установки для проведення безперервної стерилізації (УБС) включає такі операції.
Миття обладнання. Миття обладнання проводять наступним чином. Спочатку миють водою, протягом двох хвилин з передачею води у збірник нейтралізації, перед скидом рідини у систему каналізування рідких викидів. Миття продовжують розчином лугу 1%, протягом 10 хвилин при 40°С, з поверненням розчину в збірник нейтралізації. Проводиться ополіскування очищеною або пом’якшеною водою, з передачею води в збірник нейтралізації;
В тому випадку коли у обладнання(на поверхні) присутні стійкі до видалення забруднення миття проводять розчином кислоти1%, при 20 °С, з повертанням розчину у збірник нейтралізації; проводять ополіскування очищеною
’
або помякшеною водою, з передачею води в збірник нейтралізації; процес завершується ополіскуванням очищеною водою, протягом 5 хвилин, з повертанням води в збірник рециркуляційної води.
Сучасні підприємства мають механізовані пристрої для миття обладнання такі як гідромонітори. Для механічного миття устаткування, цистерн, місткостей та ін. застосовуються мийні машини типа ММ-4А і гідромонітори Г- 13А. Вони опускаються через люк на опорному пристосуванні всередину апарату, і під дією струменя гарячої рідини тиском0,6—1 Мпа проводиться очи-
51
щення внутрішніх поверхонь. Мийна машина ММ-4А складається з нерухомого і поворотного корпусів, приводного механізму, редуктора і соплового апарату із
заспокоювачем. Для приєднання шланга на поворотному корпусі є стакан з різьбленням. Миюча рідина при температурі до80 °С приводить в обертання робоче колесо гідротурбіни, яке через вертикальний вал черв’ячного редуктора обертає із швидкістю0,03—0,04 с-1 сопловий апарат, що складається з двох сопів з діаметром вихідного перетину11мм. Струмінь рідини перед виходом з сопел проходить через заспокоювач, що збільшує дальність струменя і під тиском 0,6—1,0 МПа і витраті води до 30 м3/г протягом 20—25 хв вимиває апарат. Для запобігання попаданню води в зазор між вертикальним валом і поворотним корпусом встановлено торцеве ущільнення. Габаритні розміри машини 175×122×355 мм, маса 10 кг. Гідромонітор Г-13А працює при тиску миючого розчину 0,6 - 0,8 МПа і витраті 18—22 м3/ч. Температура миючого розчину 75
–90 °С. Тривалість промивки регулюється поворотом маховика крана регулятора і коливається від5 до 30 мин. Конструкція гідромонітора аналогічна конструкції машини ММ-4А. Положення крана регулятора відповідають чотирьом циклам миття: 5–15, 15–20, 20–35, 25–30 хв. Габаритні розміри гідромонітора 400 × 195 × 140 мм.
Механізовані миючі установки фірми «Керхер» (Германія). Більш довершеною конструкцією є миючі пересувні установки «Керхер». Миючий пристрій
–розбризкуюча головка, укріплена на опорном, пристосуванні, - опускається всередину апарату і під натиском гарячого струменя води в3—5 МПа швидко і ефективно очищає його внутрішню поверхню. Залежно від конструкції апарату, предмета миттю, застосовуються різні опорні пристосування для миючого пристрою. Для миття апаратів малої місткості миючий пристрій кріпиться на короткій вертикальній трубі і занурюється через люк апарату, що знаходиться на кришці. Опора лягає на фланець кришки апарату, закріплюється, а глибина занурення регулюється. Крім обертання навколо власної осі розбризкуючі сопла обертаються одночасно навколо подовжньої осі миючої головки апарату,
завдяки чому струменя миючого розчину досягають всі точки внутрішньої поверхні апарату.
На всмоктуючій стороні насоса температура миючої рідини складає50– 60 °С, на нагнітальній стороні після нагріву в теплообміннику 90–95 °С.
Бак з миючим розчином і регулюючим вентилем для подачі розчину, насос, що створює тиск струменя, необхідний для миття і очищення бака з фільтром, куди стікає миюча рідина із зливного отвору апарату, змонтовані на пересувному візку. Рідина для миття може бути використана багато разів завдяки циркуляційному контуру і фільтрації через вбудований фільтр. Внутрішня миюча головка може працювати з двома або чотирма соплами. При двох соплах струмінь довший і сильніший, що необхідне при митті великих або сильно забруднених апаратів.
Миюча установка фірми «Керхер» дозволяє отримувати всі види струме- ню–паровий, гарячий, теплий і холодний, – з автоматичним дозуванням хімікатів. Частота обертання миючого пристрою вибирається залежно від сту-
52
пеня забруднення апарату і його радіусу. Чим більше радіус і ступінь забруднення, тим менше швидкість обертання
Обов’язковим елементом підготовки є перевірка якості проведених робіт для цього проводять профілактичний огляд та перевірку на герметичність. Як правило, така перевірка проводиться після стерилізації коли проявляються можливі нещільності у місцях зєднання елементів обладнання та апаратури.
Перевірка на герметичність ємкісного обладнання, з’єднань, та комунікацій проводиться за допомогою найбільш простого і доступного метода
– омилювання розчином господарського мила. І по виділенню бульбашок виявляють нещільності. Сучасні технології використовують галоїдні течешукачі, що дозволяють фіксувати галогенопохідниі алканів. Тетрахлорметан закачують в герметично закрите обладнання та комунікації до тиску0,5 МПа та за допомогою датчика - течешукача галогенопохідних проводять огляд всіх з’єднань обладнання та комунікацій. Особливу увагу приділяють фланцевим з’єднанням та ущільненню кришок мічткісного обладнання. У випадку виявлення нещільних
з’єднань проводять розбору та профілактичне ущільнення обладнання та комунікації. Для з’єднань проводять їх підтягування та перепаковування, а для обладнання підтягування кришок, або з’єднань і в випадку необхідності заміну ущільнюючих прокладок люків та кришок. В якості ущільнюючого матеріалу використовують термостійку гуму, пароніт, фторопласт.
Пароніт ГОСТ 481-80 - азбестовий матеріал прокладки типу. Застосовують в хімічній і нафтохімічній промисловості, в машинобудуванні, металургії і металообробці, електротехніці і електроенергетиці для забезпечення необхідної герметичності з’єднань різного типу в умовах дії агресивних середовищ, високих температур і тиску. Пароніт буває загального призначення і маслобензостойкий. Пароніт загального призначення застосовується в середовищах: прісна перегріта вода, насичена і перегріта пара, сухі нейтральні і інертні гази; повітря; водні розчини солей, рідкий і газоподібний аміак, спирти; рідкий кисень і азот; важкі і легкі нафтопродукти; температура робочого середовища від
-50 до +450.
Стерилізація обладнання
Складовою проектування є розробка способів підготовки обладнання і в цьому випадку стерилізація є невідємним компонентом загальної підготовки обладнання. Ця операція має принципове значення для асептичних виробництв.
Одним з факторів, що найістотніше впливають на біосинтез біологічно активних речовин, є забезпечення стерильності виробництва(взагалі), зокрема стерильності комунікацій та обладнання, що безпосередньо контактує з культуральною рідиною. В біотехнології застосовують різні способи стерилізації, але при цьому контамінуюча мікрофлора повинна бути повністю зруйнована або видалена. Процес дії на контамінанти при якому вони руйнуються або повністю віддаляються називають стерилізацією. Можна сказати і так«Стерилізація – сукупність фізичних, хімічних, механічних способів позбавлення від вегетативних та спорових форм мікроорганізмів».
В біотехнології застосовують три групи методів стерилізації:
-механічні;
53
-хімічні;
-біологічні.
Видалення і деструкція мікробів може бути досягнуте різними способами. |
|
|||||||
Деструкція, що приводить до повної втрати життєздатності мікроорганізмів, є |
|
|||||||
надійним |
способом |
стерилізації. В |
даний |
час |
в |
промислових |
умовах |
|
застосовується простій і економічний метод стерилізації середовищ із застосу- |
||||||||
ванням |
вологого |
тепла. Істотним |
чинником, що |
|
забезпечує |
надійну |
||
стерилізацію при тепловій обробці, є тривалість процесу. Стійкість до тепла за- |
|
|||||||
лежить від виду мікроорганізму. Наприклад, спори і конідії цвілевих грибів в 2– |
|
10 разів стійкіше в порівнянні з неспороносною |
паличкою, віруси |
і |
||
бактеріофаги – в 2–5 разів, а спори бактерії – в 3 000 000 разів. |
|
|
||
Склад і властивості поживного середовища, а також спосіб подальшого |
|
|||
культивування |
мікроорганізмів-продуцентів |
визначають |
вибір |
способу |
стерилізації і устаткування для цього важливого технологічного процесу. |
|
|||
Основним визнаним в біотехнології стерилізаційним прийомом є обробка |
|
обладнання та комунікацій насиченою водяною парою приt = 125-145°С, при |
|
|||||||
цьому існує висока гарантія досягнення необхідного рівня асептичності. |
|
|||||||
Як приклад можна розглянути стерилізація ферментаційного обладнання |
|
|||||||
та іншого обладнання де передбачається розмноження мікробних контамінантів |
|
|||||||
проводиться гострою парою(пара, що безпосередньо контактує з об’єктом |
|
|||||||
стерилізації) t = 110° С, за тиску 0,2 МПа протягом 1,5 год з подальшим охо- |
|
|||||||
лодженням протягом 3,5 |
год. Пара подається як |
в середину апарату, так і в |
|
|||||
прилеглі комунікації, так і в сорочку обладнання. В процесі стерилізації водяна |
|
|||||||
пара не утворює шкідливих для процесу біосинтезу речовин і основними про- |
|
|||||||
дуктами, що утворюються після стерилізації є вторинна водяна пара та конден- |
|
|||||||
сат. |
|
|
|
|
|
|
|
|
У більш розгорнутому вигляді цей процес реалізується таким чином. |
|
|||||||
Після закінчення кожного циклу біосинтезу в посівному і основному |
|
|||||||
ферментерах і видаленню з них культуральної рідини ферментери відкривають |
|
|||||||
і миють гарячою водою з брандспойта, миючого пристрою (гідромонітору) |
|
|||||||
очищаючи від залишків біомаси. |
|
|
|
|
|
|
||
Послідовність носить стандартній характер і як правило включає такі ро- |
|
|||||||
боти. Барботер продувають повітрям. Після огляду, а при необхідності і ремон- |
|
|||||||
ту ферментер знову миють водою, закривають люк і разом з іншою апаратурою |
|
|||||||
стерилізують гострою та глухою насиченою парою. |
|
|
|
|||||
Перед стерилізацією апаратуру і комунікації промивають водою темпера- |
|
|||||||
турою 100 °С з магістрального трубопроводу. |
|
|
|
|
||||
Стерилізаційну колонку УБС, витримував УБС, холодильник, комунікації |
|
|||||||
від холодильника до |
ферментеру |
і |
лінію |
транспортування культуральної |
||||
рідини, стерилізують при надлишковому тиску0,15 – 0,18 МПа протягом 2 ч, |
|
|||||||
пропускаючи |
пару |
в |
основній |
ферментер. Стерилізація |
ферментера |
|
||
продовжується 2 – 3 години під надлишковим тиском 0,12 – 0,15 МПа. |
|
|
||||||
Одночасно |
стерилізують |
фільтри |
тонкого |
очищення |
по |
|||
(стерилізуючи індивідуальні фільтри) і повітряні комунікації, відпрацьований |
|
|||||||
пару направляють також у ферментер. Стерилізують фільтри 1 годину під над- |
|
54
лишковим тиском 0,12–0,15 МПа. В тому випадку коли індивідуальні фільтри мають патрон або набивку з термостійкого матеріалу, після заповнення фільтру стерильним волокнистим фільтруючим матеріалом через його сорочку пропускають пару протягом 2—3 ч під надлишковим тиском0,1 – 0,2 МПа. У нормальних умовах фільтри перезаряджають не частіше за один раз на місяць(при
намоканні волокон – негайно). В кінці стерилізації пропарюють пробовідбірники, продуктовий штуцер для засіву, зливну лінію від ферментера до трапа протягом 30 хвилин. Пара для стерилізації повинна бути насиченою та сухою. Вологість пари знижує в нім приховану теплоту паротворення, а отже, і ефективність дії на мікроорганізми. Недоцільно застосовувати і перегріту пару, оскільки при температурі, однаковій з насиченою парою, при її охолодженні без конденсації виділяється набагато менше тепла. У присутності повітря температура пари нижча за загальний ,тисктому повітря потрібно повністю заздалегідь видаляти. Зазвичай це досягається гравітаційним способом– витісненням парою, що має вищу щільність, ніж повітря. Видалення повітряних пробок дозволяє прогріти всі деталі устаткування і усунути разом з ними можливе джерело інфекції.
Завдяки хорошій теплопровідності металу і обмиванню внутрішньої поверхні ферментера конденсатом пари цим способом досягається надійна стерилізація. Проте перед стерилізацією з ферментера необхідно видалити осад і вимити його, інакше в осаді може зберегтися стороння мікрофлора і надалі бути джерелом інфекції.
Тривалість стерилізації, як правило, дається без урахування часу, що витрачається на видалення повітря і прогрів ферментера.
Слід приділяти більшу увагу тим частинам ферментеру та комунікацій, що визначаються, як важкодоступні: штуцерам, пробовідбірникам, датчикам, в трубопроводах – запорній арматурі, фланцям, фасонним деталям, тупиковим місцям і відкритим закінченням труб.
В практиці роботи біотехнологічних виробництв показана висока ефективність стерилізації апаратури і комунікацій розчином активованого хлорного вапна у поєднанні з пропарюванням. Для цього обмитий виробничий ферментер об’ємом 100 м3 заповнюють холодною водою і при перемішуванні повітрям додають 10—15 кг хлорного вапна. Додають стільки ж хлориду амонію, доливають водою до повного об’єму і перемішують30 мин. Після 1,5 год витримки розчин перекачують у вільний, такий, що підлягає стерилізації ферментер або спускають в каналізацію. При повторному використанні хлорної води в неї знов вносять в тих же кількостях хлорне вапно і хлорид амонію.
Одночасно обробляють установку безперервної стерилізації і продуктові комунікації. Їх заповнюють 0,01–0,015 % розчином активованого хлорного вапна і витримують 2 години, після чого хлорну воду видаляють. Потім установку стерилізації, комунікації до ферментеру і лінії транспортування культуральної рідини пропарюють при надмірному тиску0,15 МПа протягом 1,5 ч, пропускаючи пару у ферментер. Стерилізацію продовжують 1,5 ч під надмірним тиском 0,12 МПа. Протимікробні фільтри і повітряні комунікації стерилізують паром, як вказано вище.
55
Для забезпечення і підтримки асептичності після закінчення стерилізації
уферментер через барботер подають стерильне повітря, підтримуючи
надмірний тиск 0,02—0,03 |
МПа (щоб |
уникнути попадання |
сторонньої |
|||
мікрофлори). |
|
|
|
|
|
|
Потрібно |
зауважити, |
що |
роботи |
по підготовці |
обладнання мають |
|
специфічні вимоги по техніці безпеки. Роботи з підготовки до внутрішнього ог- |
||||||
ляду, очищенню, |
миттю |
або |
ремонту |
ферментера |
повинні |
вестися під |
керівництвом старшого майстра або механіка цеху. Спочатку потрібно переконатися у відсутності діоксиду вуглецю і в неможливості надходження у -фер ментер пари. Роботу у ферментере ведуть з притоком в нього повітря. Робочий повинен надіти аварійний пояс з мотузком і протигаз. Протягом всього часу роботи у ферментере у його люка повинен стояти спостерігач, призначений старшим майстром.
Підготовка УНС до роботи
Установка безперервної стерилізації складається :з приймального бачка; насоса; теплообмінника - рекуператора № 1; колонки інжектора швидкісного нагріву; витримувача; теплообмінника № 2; теплообмінника № 3.
Перед стерилізацією УНС миють в ручному режимі: а) лужним розчином з масовою часткою NaОН 2-4% протягом 1,5 годин, з подальшим поверненням лужного розчину в збірник для нейтралізації;
б) |
миють очищеною водою протягом1-1,5 |
годин, до тих пір, доки рН не |
буде дорівнювати значенню рН очищеної води; |
|
|
в) |
миють кислим розчином з масовою |
часткою Н3N2О-4% протягом |
1.0-1.5 годин, з поверненням розчину в збірник для нейтралізації; |
||
г) |
промивають очищеною водою протягом1,0-1.5 годин, до тих пір, до- |
ки значення рН не буде дорівнювати значенню рН очищеної води.
Лужні та кислотні розчини готують в приймальному збірнику, додаючи по колектору до очищеної води розраховані кількості кислоти або лугу. Температуру розчину доводять до50-60°С при тиску 1 МПа. Після чого розчин направляють на промивку.
Відпрацьовані миючі розчини направляють в збірник нейтралізації стічних вод.
Стерилізацію УНС можна проводити спеціальним розчином(на 1м3 розчину - додають Н3РОз в кількості 1 дм3, хлористий натрій в кількості2 кг.). Продовжують стерилізацію 30 хвилин при температурі 135°С.
4.1. Підготовка поживних середовищ
Стадія допоміжних робіт підготовка поживних середовищ включає ряд операцій:
·зберігання компонентів поживних середовищ та допоміжних речовин;
·контроль показників якості;
·дозування та приготування композиції компонентів поживного середовища;
·при необхідності стерилізація.
56
Вибір способу підготовки поживного середовища визначається типом біотехнологічного виробництва. І в цьому випадку приймаються до уваги:
·тип культивування (поверхневе або глибинне);
·тоннажність виробництва.
·рівень асептичності стадії біосинтезу можливі варіанти– асептичне, умовно асептичне та не асептичне;
·термолабільність середовища взагалі або його компонентів (субстратів);
·спосіб стерилізації (періодичний або безперервний);
Термінологія: - “Стерилізація – сукупність |
фізичних, |
хімічних, |
|
|||||
механічних |
способів |
позбавлення |
від |
вегетативних |
та |
спорових |
фор |
|
мікроорганізмів”. |
|
|
|
|
|
|
|
|
Контамінація (забруднення) явище |
коли відбувається |
проникнення |
|
|||||
забруднювачів механічних або біологічних– біозабруднення. Біозабруднення |
|
|||||||
життєздатна або не життєздатна мікрофлора або її частки, які можуть спричи- |
|
|||||||
нити зміни якісних показників готової продукції. |
|
|
|
|
Складські приміщення та зберігання компонентів поживного середо-
вища
Сухі компоненти для приготування поживних середовищ зберігають в основній виробничий будівлі або в спеціальному складському приміщенні. Для зберігання використовують силосні башти (силоси), резервуари, збірники.
На заводи сировина надходить в цистернах, мішках, коробах, бочках то-
що. |
|
|
|
|
Всі ці продукти зберігають на центральних заводських складах, елеватор- |
|
|||
них банках, бункерах, підземних сховищах тощо. Звідси заводськими транс- |
|
|||
портними засобами сировину спрямовують в цехові склади і сховища. |
|
|||
Для |
зважування |
сировинних |
матеріалів |
викорис |
найрізноманітніші ваги, що є в арсеналі харчової та хімічної промисловості: від лабораторних електронних ваг до ваг, розрахованих на зважування 10…20 тонн сировини (елеваторні шкальні ковшові автоматичні ваги Одеського ВО“Точ-
маш” 120К10А та 341В20Л).
Транспортування сипких продуктів до бункерів реакторів змішувачів здійснюють за допомогою різноманітних конвеєрних ліній, норій та іншими пристроями.
При поверхневому способі культивування поживне середовище готують в
стерилізаторі або спеціальній ємності з перемішуючим |
пристроєм, куди дозу- |
ють окремі компоненти, змішують їх з водою |
або водним розчином |
збагачувачів (розварена маса, соли, кислоти, кукурудзяний екстракт). При глибинному способі культивування цех приготування середовища ізолюють від інших виробничих приміщенні, щоб запобігти попаданню нестерильної, забрудненої мікроорганізмами сировини в основне виробництво. У цеху приго-
тування |
поживного середовища |
передбачаються |
спеціальні |
місткості, |
забезпечені мішалкою, сорочкою для обігріву, введенням гострої пари, а також |
||||
різними |
введеннями з дозуючими пристроями для внесення |
в місткості |
||
компонентів середовища. |
|
|
|
57
При великій продуктивності підприємства живильні середовища можна готувати централізований для всього підприємства в окремому будівель або в приміщенні, розташованому в безпосередній близькості до цеху стерилізації.
Вибір будівельного рішення по розміщенню допоміжних цехів на промисловому майданчику залежить від багатьох чинників, і не тільки від продуктивності підприємства.
Способи приготування поживних середовищ різні і залежать від складу вхідних в середу компонентів. Для одних компонентів потрібна попередня обробка: подрібнення, дроблення, відварювання, екстрагування і т.д. Ці підготовчі
операції проводять в спеціальних місткостях і в спеціальних . апаратах Підроблені компоненти середовища(подрібнена макуха, глютен, картопля, розчинена в гарячій воді і частково розбавлений кукурудзяний екстракт) подають при постійному перемішуванні через дозуючі пристрої в ємність для приготування середовища. Рекомендується точно встановлювати послідовність введення в суміш окремих компонентів. Ця вимога перш за все відноситься до мінеральних солей при приготуванні середовища для глибинного культивування.
Залежно від властивостей компонентів середовище можна готувати розчиненням або суспендуванням початкових матеріалів в холодній або підігрітій воді. Для приготування середовища можна використовувати декілька невеликих апаратів, в одному з яких готують водний розчин екстракту, в іншому клейстеризують крохмаль або розчиняють солі. В основному ж апараті проводять тільки змішування цих напівпродуктів в певних співвідношеннях і доводять суміш до певного об’єму водою. Якщо потужність підприємства невелика, готувати середовище можна в одній місткості, але при певній послідовності операції.
Цех приготування поживного середовища на великих підприємствах зазвичай має в своєму розпорядженні цілу систему апаратів різної місткості, в яких готують окремі компоненти поживного середовища.
З точки зору варіантів приготування компонентів поживного середовища існує два варіанти технологічного рішення:
-готують поживне середовище, що готове до використання;
-готують поживне середовище у вигляді концентрату, що потребує розведення перед застосуванням.
Як обов’язковий елемент технологічного рішення використовують установку фільтрів перед насосами при транспортуванні компонентів ПС дляза тримки механічних часток, що можуть ушкодити насоси.
Термін стерильність є некоректним, тому використовують термінасептичність – стан виробництва коли відсутня контамінуюча мікрофлора.
Для стерилізації використовують 3 способи впливу:
-фізичний ;
-хімічний;
-біологічний
Дамо характеристику цим способам:
58
Хімічні способи. В основі способів – висока специфічна (вибіркова) чутливость мікроорганізмів до різних хімічних речовин, що обумовлено фізико-
хімічною |
структурою |
їх |
клітинної |
оболонки |
та |
протоплазми. Хімічна |
|
стерилізація |
поділяється |
|
на |
стерилізацію |
розчинами(речовинами) та |
||
стерилізацію газами. |
|
|
|
|
|
|
|
Фізичні способи стерилізації. Представлені: |
|
|
·Теплова (термічна) стерилізація: парою під тиском; текучою парою; тіндалізація; повітряна;
·Радіаційна стерилізація;
·Ультразвукова стерилізація;
·Стерилізація струмами високої та надвисокої частоти;
·Стерилізація ультрафіолетовим випромінюванням;
·Стерилізація ІЧта лазерним випромінюванням.
Оскільки спосіб стерилізації впливає на якість отримуваної продукції, необхідно ретельно аналізувати кожний із можливих методів та підібрати найоптимальніший із .нихНедоліки способу термічної стерилізації: неможливість стерилізації розчинів, що містять термолабільні речовини, небезпека роботи з парою під тиском. Приготування поживного середовища проводять різними способами в залежності від способу стерилізації. Якщо процес стерилізації проводять періодичним способом безпосередньо у ферментері, то всі компоненти середовища розчиняють у воді і змішують в одному реакторі. У випадку проведення безперервного процесу стерилізації компоненти середовища вуглеводного складу готують окремо від компонентів середовища, що містять азотисті речовини.
Періодична стерилізація здійснюється безпосередньо у ферментері та передбачає нагрівання поживного середовища до135°С, витримку її при цій температурі протягом години, охолодження до 45 – 35 °С. Такий процес має ряд недоліків:
-достатньо велика тривалість процесу;
-утворення в процесі стерилізації злиплених комків різної величини;
-протікання цукрово-амінних реакцій, які приводять до утворення меланоїдінів, які, в свою чергу, сповільнюють ріст мікроорганізмів.
Специфіка цього процесу повинна враховувати особливості поживного
середовища – термолабільність вуглецевого та азотного субстратів та необхідності високого рівня асептичності. Термічна стерилізація, що запропонована в дипломному проекті включає набір типових блоків:
-приготування вихідного поживного середовища для виробничого біосинтезу;
-приготування цукромісної частини поживного середовища;
-приготування азотовмісної частини поживного середовища;
- приготування комплексного і ростового підживлюючого середовища для виробничого біосинтезу.
59
Вибір способу стерилізації обумовлюється властивостями поживного середовища і як правило використовують серед фізичних способів– термічну стерилізацію, а для термолабільних ПС використовують фільтрування.
Термічний спосіб найбільше відповідає техніко-економічним вимогам виробництва. Отже з метою знезараження поживного середовища використаємо метод термічної стерилізації. Цей метод оснований на тому, що при високих температурах гинуть як вегетативні клітини, так і спори мікроорганізмів.
Характеристикою |
процесу стерилізації |
являється |
питома швидкість |
гибелі мікроорганізмів: |
|
|
|
k = -1/N(dN/dτ) |
(4.1) |
|
|
де k - відносна кількість мікроорганізмів, що гинуть за одиницю часу; |
|||
N – число особин в популяції. |
|
|
|
З формули (1) після логарифмування отримаємо: |
|
||
k = -1/τ ln(N0/N) |
(4.2) |
|
|
N = Noe (-kτ) |
(4.3) |
|
|
де N0 - кількість живих мікроорганізмі перед стерилізацією. Отже, k не |
|||
залежить від концентрації мікроорганізмів, |
залежить |
від температури |
стерилізації, виду мікроорганізму, характеристики стерилізуємого об’єкту. Так як процес стерилізації проходить в декілька етапів(нагрівання середовища або апарату до температури стерилізації; витримування при цій температурі протягом часу, що забезпечує гибель мікроорганізмів; охолодження стерилізуємого об’єкту), то інтеграл можна записати так:
t |
(4.4) |
ln N 0 / N = òkt × dt |
|
0 |
|
N = N0e 0-∫ k dτ |
(4.5) |
За теорією Ф.Х.Дейндорфера і А.Е.Хемфрі ліву частину рівняння(4.5) позначимо
Ñ= N0еτ 0-∫ k dτ - критерій стерилізації (4.6). Коли k = const і τ= const , то Ñ
Ñ= N0e-kτ (4.7)
|
Ñ = kτ |
(4.8) |
|
|
|
|
|
Щоб розрахувати ефективність стерилізації, по таблицям знаходять ек- |
|
||||
спериментальне значення k, що встановлюється за експериментальними даними |
|
|||||
для |
найбільш |
стійкого |
еталонного |
мікроорганізмуспори Bacillus |
|
|
stearothermophilus. Для розрахунку і обґрунтування режиму стерилізації в умо- |
|
|||||
вах |
реального |
|
виробництва |
часто використовують наближений метод. |
Т |
|
Річардса. Цей метод передбачає: |
|
|
|
·врахування критерію стерилізації об’єкта;
·витримування об’єкта при температурі стерилізації;
·охолодження.
Річардс довів, що обробка при to < 1000С складає 2% загального критерію стерилізації і провів розрахунок критерію стерилізації в інтервалі від100 до 1250С при прогресуванні температури відпрацювання 10С/хв. Пізніше було розраховано критерій стерилізації для температури 143 0С - максимальної температури, яка використовується на теперішній час. Якщо температура нагрівання
60
або охолодження відрізняється від прийнятого в таблицях, то використовується співвідношення:
Ñ5Ñ (t!tcтер-100) (4.9) |
|
температури |
від100 |
0С |
до |
температури |
||||
де |
τ – тривалість зміни |
|||||||||
стерилізації. |
|
|
|
|
|
|
|
|
|
|
Ефект стерилізації визначається за сумою критеріїв стерилізації: |
|
|||||||||
SÑ5Ñн1Ñв1Ñох (4.10) |
|
|
|
|
|
|
|
|||
По Річардсу повна стерилізація досягається |
приÑ540, Σпроте |
у |
||||||||
промисловості використовуються режими, де ΣÑ580-100 і вище. |
|
|
||||||||
Цей |
метод |
може |
бути |
використаний |
для |
визначення |
показник |
|||
асептичної ефективності: |
|
|
|
|
|
|
|
|||
S = nз/n, |
(4.11) |
|
|
|
|
|
|
|
||
де nз - кількість загружених операцій, |
|
|
|
|
|
|||||
n – загальне число проведених операцій. |
|
|
|
|
|
|||||
В |
основі |
розглянутих |
методів лежить |
гіпотеза |
про |
експоненціальні |
залежності кількості клітин, що вижили від часу теплової дії. Однак, в реальних умовах ця гіпотеза нерідко не відповідає дійсності, і в таких випадках для розрахунку режимів стерилізації використовують імовірнісні методи, які полягають у встановленні імовірності виживання мікроорганізмів при даному режимі стерилізації у даному обладнанні або ймовірності отримання чистих операцій.
Побудова імовірнісної моделі процесу стерилізації засновується на основі розподілу Пуассона.
Кінетика термічної стерилізації рідких поживних середовищ |
|
||||
Теплова |
стерилізація |
рідких |
поживних |
середовищ |
здійснюєтьс |
циклічним чи безперервним способами. Циклічна теплова обробка звичайно |
|||||
проводиться безпосередньо в культиваторі, |
але може застосовуватися і з вико- |
ристанням спеціальної ємності. При циклічному методі одночасно нагрівається весь обсяг середовища. Після цього середовище витримується протягом визначеного часу, а потім охолоджується до температури культивування.
Ефект стерилізації визначається за сумою критеріїв стерилізації:
SÑ5Ñн1Ñв1Ñох (4.12)
Біологічно активні речовини отримують або при поверхневому способі культивування на сипких твердих поживних середовищах, або глибинним на
рідких поживних середовищах. |
|
|
|
|
|
Для |
стерилізації твердих сипких середовищ |
можуть |
застосовуватися |
||
теплові і холодні способи стерилізації. Теплова стерилізація здійснюється па- |
|||||
рою (під |
вакуумом, при |
атмосферному |
або |
під |
надмірним ),тиском |
інфрачервоними променями, електронагрівом, за допомогою високочастотного і надвисокочастотного нагріву. До способів холодної стерилізації відносяться: іонізуюче випромінювання, хімічна стерилізація окислом етилену, ультразвукова, радіаційна дія і фільтрація через стерилізуючі фільтри.
61
За принципом дії розрізняють стерилізацію безперервну і періодичну. По конструктивному оформленню стерилізатори періодичної дії для стерилізації сипких поживних середовищ діляться на горизонтальні одноступінчаті і двохступеневі, суміщені двохступеневі з одним вертикальним ступенем, а інший — горизонтальною і безперервної дії — горизонтально вібраційні.
Як теплоносій для всіх перерахованих стерилізаторів застосовується насичена водяна пара. Перевагами теплової обробки парою є її легке транспортування, здатність проникнення в труднодоступні вузли стерилізаторів, трубопроводів і арматури, велика тепловіддача при конденсації, нетоксичність. Конденсат водяної пари не змінює складу середовища, зволожуючиі спори, сприяє збільшенню швидкості їх загибелі в 10— 1 000 разів.
При стерилізації окислом етилену застосовуються газові стерилізатори шафового типу періодичної дії з рециркуляцією окису етилену. Для стерилізації сипких середовищ іонізуючим випромінюванням застосовується пучок наведених прискорених електронів до5 МЕВ, що отримують від сильноточних прискорювачів.
Рідкі середовища також стерилізують шляхом теплової обробки водяною парою, проте конструктивно установка відрізняється від стерилізаторів для твердих середовищ.
Процеси періодичної стерилізації рідких середовищ здійснюються або в спеціальних апаратах, або безпосередньо у ферментерах після їх завантаження.
У промисловості для стерилізації рідких середовищ широко застосовуються установки стерилізації УНС-5. УНС-20 і УНС-50 продуктивністю відповідно 5, 20, 50 м3/ч, а також зарубіжні установки фірми«Де-лаваль» і роторного типу.
Стерилізація рідких розчинів може бути здійснена також шляхом видалення мікроорганізмів при їх фільтрації через асбестоцелюлозні мембранні фільтри типів МФАЗ і -4.
|
Стерилізатор горизонтального типу для стерилізації твердих поживних |
|
|||
середовищ. |
|
|
|
|
|
|
В біотехнології для стерилізації сипких поживних середовищ парою ши- |
|
|||
роко |
застосовуються |
циліндрові |
стерилізатори |
горизонтального, |
типу |
забезпечені пароводяною сорочкою. Усередині стерилізатора розташовано два |
|
||||
вали із закріпленими на них лопатями, кут повороту яких по відношенню до ва- |
|
||||
лу легко регулюється. Це дозволяє встановити оптимальний радіальний зазор |
|
||||
між лопатями і стінками апарату залежно від фізико-хімічних властивостей |
|
||||
компонентів і складу середовища. Вали обертаються в різні боки, при цьому се- |
|
||||
редовище безперервно перемішується в протилежних напрямах, рухаючись від |
|
||||
одного торця апарату до іншого по складній траєкторії. Таке конструктивне |
|
||||
рішення забезпечує інтенсивне перемішування середовища, значне зниження |
|
||||
комкообразования і однорідність середовища різнокомпонентного складу, що |
|
||||
істотно впливає на процес культивування. |
|
|
|
||
|
Для прискорення нагріву середовища призначена пароводяна сорочка, в |
|
|||
яку |
подається пара під |
тиском 0,2до |
МПа. Середовище |
витримують при |
|
62
заданій температурі стерилізації з періодичним включенням перемішуючих пристроїв.
Об’єм апарату і потужність встановленого електродвигуна передбачає одночасну стерилізацію до 400 кг сухих компонентів середовища і до600 л води для отримання середовища з вологістю 58—60 %.
Вивантаження стерильного поживного середовища проводять через нижній розвантажувальний люк, забезпечений внутрішньою і зовнішньою кришками, щільно прилеглими за допомогою гвинтового ущільнювача до апа-
рату. |
Стерилізатор, окрім |
цього, |
забезпечений завантажувальними |
люками, |
|||
численними |
штуцерами |
для |
підведення пари і відведення конденсату, |
||||
підведення і відведення охолоджуючої води, засобів |
|
|
|||||
|
Біохімічний та мікробіологічний контроль стадій підготовки поживного |
||||||
середовища |
|
|
|
|
|
|
|
|
Кожну партію сировини(висівки, макуха, паростки, буряковий жом та |
||||||
ін.), |
що поступила, |
піддають |
мікробіологічному |
контролю на |
мікробну |
||
забрудненість. На МПА й суслоагарі проводять посіви з сировини після |
|||||||
відповідного розведення. Через 24—72 год проводять підрахунок колоній й ви- |
|||||||
значають ступінь мікробної забрудненості даної сировини мікроорганізмами. |
|||||||
|
Залежно від мікробіологічної забрудненості призначається режим |
||||||
стерилізації. |
|
|
|
|
|
|
|
|
Кожна |
партія |
сировини, що поступає, може |
значно відрізнятися від |
раніше прийнятою, тому при кожному нових постачанні проводять біохімічний контроль сировини.
Сировину аналізують на вміст тієї поживної речовини, джерелом якої воно є. Так, у висівках, борошні визначають вміст крохмалю, в буряковому жомі, вижимках плодів й овочів — пектину. Визначають також вміст в сировині азоту, фосфору й інших з'єднань. Проводять пробне вирощування, особливо ретельно ведуть дослідження складу кукурудзяного екстракту, оскільки це не стабільний продукт. Тільки після всебічного вивчення партії сировини, що поступила, остаточно коректується й встановлюється дозування компонентів й порядок приготувань середовища.
4.2. Устаткування та апаратура для стерилізації поживних середовищ
Допоміжне устаткування. Місткістне устаткування. При виробництві біологічно активних речовин необхідно здійснювати численні допоміжні операції в рамках проведення допоміжних робіт. Приготування по-
живного |
середовища |
супроводжується |
експлуатацией |
різних |
типів |
|||
місткосткісного устаткування і зараз актуально звернути увагу на цей вид -ус |
|
|||||||
таткування. Це тим більше актуально у зв’язку з тим, що коректний вибір ус- |
|
|||||||
таткування як елемент проектування, дозволяє впливати на ефективність |
|
|||||||
технології. |
|
|
|
|
|
|
|
|
|
До допоміжних |
видів |
устаткування відносяться: резервуари |
і збірники |
|
|||
для |
зберігання |
рідких |
продуктів, реактори-змішувачі |
для |
змішування |
|||
компонентів |
поживних середовищ, мірники |
рідких середовищ, збірники- |
|
63
приймачі |
для |
прийому |
і |
короткочасного |
зберігання |
рідких |
продукт |
|||
(культуральної |
рідини, ультраконцентратів, пермеатів), |
насоси |
для |
подачі |
||||||
рідких розчинів, дозатори, живильники сипких і рідких середовищ, машини для |
|
|||||||||
механічного миття устаткування, повітродувки, компресори і ін. |
|
|
|
|||||||
Тип допоміжного устаткування, матеріал для його виготовлення, одинич- |
|
|||||||||
на місткість, кількість штуцерів, люків, огрівальних або охолоджуючих соро- |
|
|||||||||
чок, перемішуючих пристроїв і т.д. залежать від конкретного призначення апа- |
|
|||||||||
рату, технологічних і інших вимог виробництва. |
|
|
|
|
|
|
||||
Ємкісне устаткування До міст кісного устаткування, вживаного на |
|
|||||||||
біотехнологічних |
підприємствах |
для |
зберігання |
рідких |
середовищ |
|||||
компонентів середовищ, відносяться резервуари і місткісні апарати. |
|
|
|
|||||||
Для тривалого зберігання рідких продуктів на складах загальнозаводсько- |
|
|||||||||
го зберігання частіше застосовують резервуари горизонтального типу, чим вер- |
|
|||||||||
тикального. Бурякову мелясу, кукурудзяний екстракт, метанол, етанол, ацетон і |
|
|||||||||
іншу сировину, необхідну для отримання продуктів мікробіологічного синтезу, |
|
|||||||||
зберігають в резервуарах великої одиничної місткості — від 100 до 10 000 м3. |
|
|||||||||
Для |
підтримки однорідності |
сировини |
резервуари |
забезпечені |
перелив- |
ними трубами, розташованими на різних рівнях, і системою гомогенізації. Для адекватного представлення апаратів на апаратурній схемі потрібно пам’ятати, що резервуари забезпечені штуцерами: для завантаження сировини і подачі стислого повітря, манометра, запобіжного клапана, воздушника, покажчика рівня, спуску залишку продукту, трубою передавлювання і люками. Оскільки
резервуари |
знаходяться на відкритому просторі загальнозаводських складів, |
|
|||||||
вони як правило, обладнані підігрівачами змієвикового типу, всередину яких |
|
||||||||
подається пара для розігрівання продукту в холодну пору року. |
|
|
|
||||||
Видача рідких середовищ може здійснюватися самопливом, а також пе- |
|
||||||||
редавлюванням стислим повітрям або інертним газом при тиску від0,3 до 1,6 |
|
||||||||
МПа. На біотехнологічних підприємствах застосовуються резервуари об’ємом |
|
||||||||
1, 2, 3, 5, 10, 50, 100, 250/500, 2000 до 3000 м3. |
|
|
|
|
|
||||
Для |
тимчасового |
зберігання |
рідкої |
сировини, розчинів |
солей, |
|
|||
компонентів поживних середовищ, екстрактів культуральних рідин, фугатов, |
|
||||||||
ультраконцентратов, пермеатов, інших проміжних продуктів виробництва, а та- |
|
||||||||
кож для |
здійснення деяких технологічних процесів застосовуються сталеві |
|
|||||||
зварні міскісні апарати– збірники з сорочками або без них і без механічних |
|
||||||||
перемішуючих пристроїв. |
|
|
|
|
|
|
|
|
|
Суттєвою відмінністю збірників від реакторів і є відсутність мішалки у |
|
||||||||
збірників. Збірники, як правило знаходяться у виробничих приміщеннях. |
|
|
|||||||
Основними характеристиками апаратів місткостей є їх геометрична та |
|
||||||||
робоча місткість, робочий |
тиск і матеріал, з якого |
апарат виготовлений. |
|
||||||
Місткісні апарати можуть бути суцільнозварними або із з’ємними кришками; |
|
||||||||
вони можуть мати сорочки або інші внутрішні елементи для теплообміну, люки |
|
||||||||
для завантаження і вивантаження, а також штуцера нетехнологічного призна- |
|
||||||||
чення для встановлення приладів контролю і регулювання параметрів процесу. |
|
||||||||
Місткісні |
апарати |
бувають |
вертикального |
або |
горизонтального. |
тип |
64
Вертикальні місткості, як правило, мають відношення висоти до діаметру, що |
|
дорівнює 5. |
|
Умовне позначення апаратів включає літери і цифри. Літерні позначення |
|
відповідають шифру типу корпусу апарата. Перші букви позначають: Г — го- |
|
ризонтальний, В — вертикальний, друга і третя букви позначають тип днища; Е |
|
— еліптичне, До — конічне, П — плоске (друга буква в позначенні вертикаль- |
|
них апаратів визначає нижнє днище, а третя — верхнє). Цифри після букв по- |
|
значають наявність або |
відсутність роз:’єму1 — суцільнозварною (без |
роз’єму); 2 — роз’ємний. Наступні цифри указують на наявність внутрішніх |
|
устроїв і обігріву: 1 — без сорочки і без внутрішніх устроїв; 2 — з трубним |
|
пучком; 3 — з сорочкою; 4 — із змійовиком; 6 — з зануреним насосом. Цифри, |
|
що стоять після другого тире, позначають номінальний об’єм апарату(м3), а |
|
останнє число — робочий |
тиск (МПа). Наприклад, позначення ГЕЕ1-2-50-Об |
відповідає |
горизонтальному |
апарату |
з |
еліптичними, |
д |
||
суцільнозварному, з трубним пучком, номінальним |
об’ємом 50 |
м3, робочим |
|
||||
тиском в апараті 0,6 МПа. |
|
|
|
|
|
|
|
Вертикальні місткісні апарати можуть бути з двома еліптичними днища- |
|
||||||
ми, з еліптичним днищем і кришкою місткістю від 0,01 до 200 м3; вертикальні з |
|
||||||
еліптичним і плоскими днищами, а також з еліптичним днищем і плоскою |
|
||||||
кришкою місткістю від 0,01 до 32 м3; вертикального і горизонтального типу з |
|
||||||
двома плоскими днищами, а також з плоским днищем і кришкою місткістю від |
|
||||||
0,01 до 100 м3; вертикальні з плоскими і сферичними днищами, а також з пло- |
|
||||||
ским днищем і сферичною кришкою місткістю від1 до 32 м3; горизонтальні з |
|
||||||
двома конічними днищами з кутом при вершині 140° місткістю від 4 до 100 м3 і |
|
||||||
вертикальні з конічним днищем і еліптичною кришкою місткістю від0,04 до 50 |
|
||||||
м3. Місткісні апарати вертикального типу працюють під тиском від0,6 до 1,6 |
|
||||||
МПа, горизонтальні суцільнозварні апарати з конічним неотбортованним і |
|
||||||
верхнім плоским днищами — не більше 0,07 МПа. |
|
|
|
||||
Всі місткісні апарати, за винятком вертикальних з верхніми плоскими |
|
||||||
днищами можна експлуатувати з будь-якими робочими середовищами при |
|
||||||
щільності середовища 1600 кг/м3, щільності теплоносія (для апаратів з сороч- |
|
||||||
кою) 1200 кг/м3; товщині |
теплоізоляції 60 мм |
і щільності теплоізоляції400 |
|
||||
кг/м3. |
|
|
|
|
|
|
|
Вибір |
матеріалу |
апарату |
проводять |
з |
урахуванням |
його корозійної |
|
стійкості в робочому середовищі і впливу металу на біологічно активні речовини в процесі виробництва.
Місткісні апарати забезпечені наступними технологічними штуцерами: входу середовища, виходу середовища, переливу, труби передавлювання, входу і виходу теплоносія, входу і виходу повітря, а також штуцерами для приладів контролю — манометра, запобіжного клапана, покажчика рівня, термометра і ін.
Місткісні апарати, усередині яких розташовані трубний пучок і занурений насос забезпечені відповідними додатковими штуцерами. Вони розраховані для експлуатації при щільності робочих середовищ до1600 кг/м3, щільність теплоносія 1200 кг/м3 і при надмірному тиску в апараті не більше 0,6 МПа.
65
Суцільнозварні апарати горизонтального типу з еліптичним днищем без внутрішнього трубного пучка розраховані для зберігання робочих середовищ щільністю 1600 кг/м3 при надмірному тиску в апараті0,6; 1 і 1,6 МПа.
Коефіцієнт заповнення об’єму апарату складає до 0,9 від номінального об’єму. Горизонтальні суцільнозварні апарати з конічними неотбортованними
днищами працюють при тиску до0,07 Мпа. Вертикальні суцільнозварні апарати з нижнім конічним(90°) неотбортованним і верхнім плоским днищем призначені для прийому, зберігання і видачі рідких невибухонебезпечних, не- взриво-пожежних і нетоксичних середовищ при атмосферному тиску і можуть бути використані як відстійники. Апарати можуть бути забезпечені пристроєм як для періодичного, так і постійного підігріву або охолоджування.
Мірники призначені для прийому, зберігання і видачі рідин і розраховані на максимальний робочий тиск до0,6 МПа. Залежно від температурного режи-
му апарати можуть бути з сорочкою або без сорочки. |
|
|
|
|||
Корпус |
апаратів |
виготовляють |
з |
вуглецевої |
сталі |
Вмстз |
корозієстійких сталей Х18Н10Т, Х17Н13М2Т, ОХ22Н5Т, а також з двошарової |
|
|||||
сталі. |
|
|
|
|
|
|
Збірники. |
Місткості |
без перемішуючих |
пристроїв— збірники |
встанов- |
|
люють між апаратами різних технологічних стадій виробництва з метою підвищення коефіцієнта використання основного технологічного устаткування,
забезпечення ритмічності його роботи, а також для сполучення безперервних і |
|
||||||||||||||
періодичних стадій. Устаткування місткості у вигляді збірок виконує роль лан- |
|
||||||||||||||
ки тимчасового запізнювання наприклад для накопичення культуральної рідини |
|
||||||||||||||
перед її подачею на упарювання. |
|
|
|
|
|
|
|
|
|
|
|||||
|
Номінальна |
місткість |
судин |
і |
апаратів визначається |
їх |
внутрішнім |
||||||||
об'ємом без урахування об'єму кришок, що відкриваються, штуцерів і люків. |
|
||||||||||||||
Наявність захисної футеровки, покриттів і внутрішніх устроїв при розрахунку |
|
||||||||||||||
внутрішнього об'єму не враховується. |
|
|
|
|
|
|
|
|
|
||||||
|
Номінальна місткість збірники |
|
|
|
|
|
|
|
|
|
|||||
|
Vн = Vж /ц |
|
|
|
|
|
|
|
|
|
|
|
|
|
|
|
де Vж — об'єм завантажуваної в збірку рідини, м3; ц — коефіцієнт за- |
|
|||||||||||||
повнення збірники (рівний 0,7 — 0,8). |
|
|
|
|
|
|
|
|
|
||||||
|
Номінальну місткість (м3) циліндрових апаратів і судин, що виготовля- |
|
|||||||||||||
ються з металевих матеріалів і пластичних мас, слід вибирати з наступного ря- |
|
||||||||||||||
ду (ГОСТ 13372—78): 0,01; 0,016; 0,025; 0,040; 0,063; 0,100; 0,125; 0,160; 0,200; |
|
||||||||||||||
0,250; |
0,320; |
0,400; |
0,500; |
0,630; |
0,800; |
1,00; |
1,25; |
1,60; |
2,00; |
2,50; |
3,20; |
4,00; |
|
||
5,00; 6,30; 8,00; 10,0; 12,5; 16,0; 20,0; 25,0; 32,0; 40,0; 50,0; 63,0; 80,0; 100; 125; |
|
||||||||||||||
160; 200. У основі запропонованих стандартних характеристик місткостей -за |
|
||||||||||||||
кладено існування двох рядів преференцийных чисел R-10 (місткість більше 1) |
|
||||||||||||||
і R-5 (менше 1). |
Ряд |
R-10 |
визначається геометричною прогресією |
з |
|||||||||||
коефіцієнтом 10 Ö10 (об’єми, м3, 1,0, 1,25 1,6, 2,0, 2,5 і т. д.). |
|
|
5 |
|
|||||||||||
|
Ряд R-5 визначається |
геометричною |
|
прогресією |
|
|
|
|
|||||||
|
|
з коефициентом Ö10 |
|
(об’єми, м3, 0,01, 0,16, 0,25, 0,04, 0,063, 0,1 і т. д).
66
Внутрішній об'єм корпусів не повинен відрізнятися від номінального більш ніж на 10 % у бік збільшення і на 5 % — у бік зменшення.
За внутрішнім обсягом апарату визначають діаметр і висоту, які також повинні відповідати стандарту (ГОСТ 9617 — 76); внутрішній діаметр судини або апарату, що виготовляється із сталевих листів або поковок, слід вибирати з ряду (мм): 400, (450), 500, (550), 600, (650), 700, 800, 900, 1000, (1100), 1200, (1300), 1400, (1500), 1600, (1700), 1800, (1900), 2000, 2200, 2400, 2500, 2600, 2800, 3000, 3200, 3400, 3600, 3800, 4000, 4500, 5000, 5600, 6300, 7000, 7500, 8000, 8500, 9000, 9500, 10000, 11000, 12000, 14000, 16000, 18000, 20000.
Розміри, в дужках, допускається застосовувати лише для обігріваючих або охолоджуючих сорочок судин і апаратів.
Довжини обичайок корпусів судин і апаратів, зокрема проміжні розміри, що мають, вибирають з наступного ряду(мм): 60, 80, 100, 120, 140, 160, 180, 200, 220, 250, 280, 320, 360, 400, 450, 500, 550, 600, 650, 700, 800, 900, 1000, 1100, 1250, 1400, 1600, 1800, 2000, 2200, 2500, 2800, 3200, 3600, 4000, 4500, 5000, 5500, 6000, 6500, 7000, 7500, 8000, 8500, 9000, 9500, 100000, 11000 12000 13000, 14000, 15000, 16000, 17000, 18000, 19000, 20000, 21000, 22000, 23000, 24000, 25000, 26000, 27000, 28000, 29000, 30000.
Основні розміри корпусів циліндрових сталевих зварних судин і апаратів визначені в ГОСТ 9931-79. Випускаються апарати дев'яти типів, з яких шість вертикальних (позначення В) і три горизонтальних(позначення Г) з різними формами днища і кришок(Е – елиптичне; З – сферичне; П – плоске; До – конічне).
Вибір устаткування місткості проводять виходячи з добового потоку рідини, що переробляється, тривалості операції (для періодичного процесу) або швидкості процесу (для безперервного процесу). При виборі об'єму і числа апаратів слід враховувати їх габаритні розміри, виробничі площі, які має в своєму розпорядженні підприємство, можливість технологічного маневрування, наявність паралельних потоків.
Апарати з механічними перемішуючими пристроями – реактори застосовуються в біотехнології для проведення різних хімічних реакцій(наприклад, нейтралізація, підкислення), для інтенсифікації масо- і теплообміну, а також для отримання суспензій, емульсій і сумішей твердих речовин. Це змішувачі для приготування розчинів компонентів живильних середовищ, збірники культуральної рідини, місткості для змішування рідин із стабілізаторами або
захисними засобами — реактори і т.д. |
|
|
|
Безперервна |
стерилізація. Використовуючи |
лінії |
безперервної |
стерилізації можна переробити за відносно короткий час будь-яку кількість матеріалу без перегрівання і перетримування. Стандартні лінії мають деякі відмінності, але працюють за єдиним принципом.
Наприклад, в лінію може бути включена буферна ємність між реакто- ром-змішувачем і нагрівачем.
Нагрівач може бути виконаний у вигляді колонки, в яку знизу подається рідина, а зверху через перфоровану трубку – гостра пара.
67
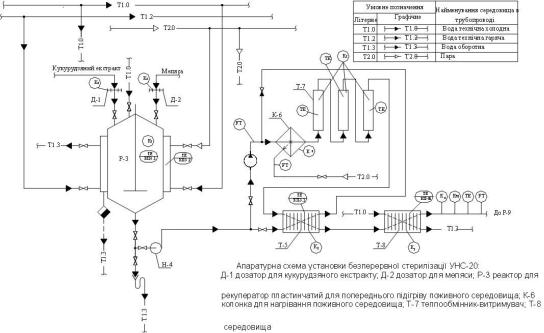
Вважається, що найбільш досконалим нагрівачем є колонка, в яку зверху тангенціально подається рідина, а в центр закрученого потоку подається пара.
Рис.4.1.Апаратурна схема установки безперервної стерилізації УБС-20.
Витримувач може бути виконаний у вигляді змійовика або, як показано на рис.4.1. у вигляді колонки, яку споряджають внутрішніми пристроями для вирівнювання внутрішніх потоків.
Як правило, лінію споряджають декількома колонками-витримувачами, що дає можливість змінювати час витримки. Відкачку залишків ПС з колоноквитримувачів здійснюють як окремим насосом (як показано на схемі), так насо-
сом, який встановлений |
на відкачкуЖС з реактора-змішувача 1. В деяких |
||||
лініях відсутні |
ємність 5 |
для часткового |
охолодження |
стерильного ЖС, |
|
оскільки це ускладнює підтримку сталої температури і витрати гострої пари в |
|||||
процесі нагрівання, а втрата тиску іноді унеможливлює без додаткового насосу |
|||||
перетискання ПС у ферментер. |
|
|
|
||
Кінцевими |
холодильниками служать |
нерозбірні |
теплообмінники типу |
||
“труба в трубі”, оскільки лише вони забезпечують зберігання стерильності ПС, |
|||||
але відоме застосування і спіральних теплообмінників |
у |
лініях стерилізації |
|||
фірми “Альфа-Лаваль”, а також нерозбірних пластинчастих. Оскільки усі лінії |
|||||
працюють в безперервному стаціонарному режимі, то |
це |
полегшує їх |
|||
автоматизацію. |
|
|
|
|
|
Вибір лінії УНС і технологічні розрахунки лінії
Вибір лінії УБС диктується об’ємом ПС, що підлягає стерилізації, і часом додаткових операцій на стадії ферментації.
68
Наприклад, якщо потрібно переробити150 м3 ПС при часі додаткових операцій 15...20 годин, з яких лише третина часу може бути витрачена на завантаження стерильного ПС, тобто 5 - 6 годин, то продуктивність лінії повинна бути близько 150/5 = 50 м3/год. Отже, потрібно обрати лінію УНС-50. Якщо ж, наприклад, об’єм ЖС становить 10 м3, то використання цієї лінії приведе до того, що загальний час роботи лінії повинен бути10/50 = 0,2 год = 12 хв. За цей час не встигне навіть встановитись стаціонарний режим роботи лінії. Зниження продуктивності лінії шляхом зменшення витратиЖС від насосу 2 економічно недоцільне, оскільки продуктивність лінії потрібно зменшувати в5...10 разів. В даному випадку доречно встановити лініюУНС-5, час роботи якої буде становити 10/5 = 2 години, що цілком прийнятно. При дуже великих об’ємахЖС
можна встановлювати декілька паралельно працюючих ліній з максимально можливою продуктивністю
Будівельні рішення при проектуванні відділення стерилізації поживних середовищ
Приміщення для зберігання сировини, допоміжних матеріалів, готової продукції і пакування матеріалів повинні бути достатньо просторі, правильно освітлені, обладнанні так, щоб забезпечити необхідний температурний режим, умови чистоти і сухості для розміщених матеріалів. Ці приміщення повинні мати необхідну кількість шаф і полиць. Зберігати сировину треба в сухих прохолодних приміщеннях, розміщених так, щоб подача сировини у виробничі цехи була зручною. Складські приміщення повинні мати спеціальні майданчики для розвантаження, навіси для захисту від атмосферних осадів.
Заводські складські приміщення облаштовуються резервуарами. Це місткості великого об’єму від100 до 10 000 м3, що забезпечують централізоване зберігання рідких компонентів. Перевагою цього способу зберігання сировини є усереднення складу джерел поживних середовищ, о забезпечує отримання якісної готової продукції. Для зберігання сипких матеріалів використовують силоси висотою від 10 до 30 м. Переміщення різних матеріалів і сировини в межах підприємства здійснюється за допомогою пневмотранспорту.
Зовнішні транспортні зв’язки підприємства представлені стандартними транспортними мережами, а транспорт на площі промислового майданчика представлений трубопроводами, повітропроводами, системами пневмотранспорту, для здійснення перевезень між цехами використовується система електротранспорту.
4.4. Підготовка технологічного повітря
В тому випадку коли продуцент біологічно активної речовини є строгим аеробом ефективне забезпечення мікроорганізмів розчиненим киснем є необхідним елементом процесу біосинтезу. При цьому необхідною умовою вирощування глибинної культури продуцента ферментів є асептичніс, томуь повітря, що подається на аерацію, має бути стерильним.
69
|
Існує достатня кількість методів забезпечення стерильності повітря– об- |
||||
робка |
повітря |
хімічними, фізичними |
або |
іншими |
чинниками. Для |
біотехнологічних виробництв традиційними методами підготовки повітря є метод фільтрування через перегородки з різних матеріалів. Вибір методу стерилізації повітря в загальному вигляді є вибором фільтруючого матеріалу і способу його фіксації в корпусі фільтра.
Виходячи з теорії стерилізації повітря, для видалення контамінантів використовують волокнисті фільтруючі матеріали з різних мінеральних або органічних речовин, пористі перегородки з кераміки або полімерних матеріалів.
Атмосферне повітря завжди містить дрібні тверді або рідкі частинки, які
несуть на |
собі різноманітні |
мікроорганізми. У |
містах середня |
концентрація |
|
мікрофлори |
3 |
4 |
3 |
3 |
районах ця |
досягає 10 |
– 10 |
клітин/м (кл/м ). В озеленених |
концентрація становить 103 – 3.104 кл/м3. Саме там намагаються розташовувати підприємства тонкого мікробіологічного синтезу.
Основною вимогою, що ставиться до аеруючого повітря, є його стерильність. Ефективність роботи системи очищення повітря оцінюють коефіцієнтом проскоку Кп, %
Кп = Х*100/Х0 |
(4.13) |
де Х, Х0 – концентрація мікроорганізмів у повітрі відповідно після і до системи очищення повітря, кл/м3.
Для асептичних процесів біосинтезу Кп повинен становити 10-8...10-11 %, для промислових систем – 10-4...10-6
Звичайні методи очищення, що ґрунтуються на дії відцентрових сил (циклони), інерції (віддільники), промивці (скрубери, пінні апарати), а також електрофільтри, не знайшли розповсюдження, оскільки дозволяють одержувати повітря з Кп = 3...5%. Ці методи застосовують лише для попереднього перед стерилізацією очищення атмосферного повітря.
Для стерилізації повітря з належними характеристиками використовують два методи: знищення мікрофлори за допомогою нагрівання або іонізуючого випромінювання, наприклад, за допомогою УФ-опромінювання, та вилучення її методом фільтрування. Перший метод є більш надійним та ефективним, але для промислових масштабів є неприйнятним, оскільки у виробничих умовах витра-
чають занадто великі об’єми повітря, щоб можна було б |
говорити про |
||||
економічну доцільність таких рішень. В промислових умовах використовують в |
|||||
основному метод фільтрування крізь шари насипного, пористого або волокни- |
|||||
стого матеріалу. Для |
попередньої |
стерилізації використовують |
глибинні |
||
(набивні) фільтри |
на |
основі |
волокнистих |
матеріа. Дляів |
остаточної |
стерилізації перед входом у ферментер встановлюють індивідуальні фільтри з розгорнутою поверхнею або абсолютні, які діють як сита, патронного типу Абсолютні сита, створюють велику втрату тиску повітря й швидко забиваються, тому застосовують їх рідко.
Попри того, що волокна набивного фільтру розташовані між собою на відстанях на порядок більше діаметрів мікрочастинок, вони діють досить ефективно. При великих швидкостях частинки, проходячи шар волоконного
70
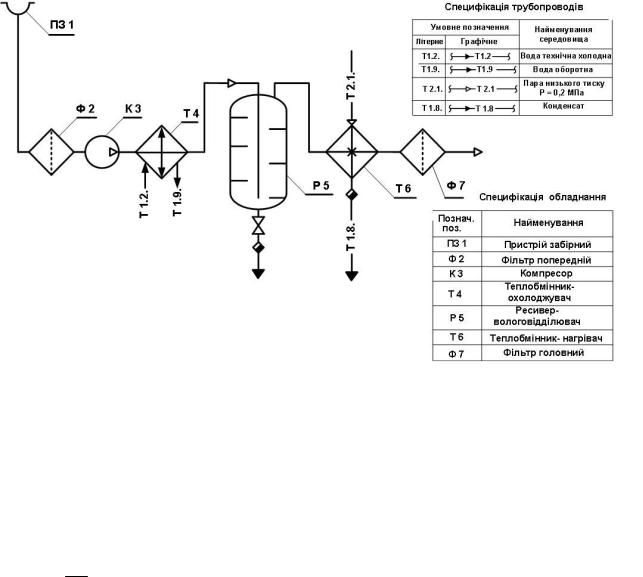
фільтру, скоріше або пізніше зустрічають на своєму шляху волокно і затримуються ним (інерційний механізм осадження).
Рис.4.2.Апаратурна схема підготовки та стерилізації аераційного повітря.
При |
малих |
швидкостях |
затримка |
відбувається |
в |
основному |
механізмами |
осадження, дії електростатичних сил, |
сил Ван-дер-Ваальса. |
Для |
кожного типу аерозолю та волокна існує деяка критична швидкість, при якій фільтр є неефективним. При таких швидкостях інерційний механізм вже не діє, а для інших швидкість є завеликою. Товщину шару волокна знаходять за формулою
Х 0
n Х = nфН (4.14)
де nф – константа фільтрації, яку знаходять експериментально; Н – товщина шару волокна.
Існуючи методики розрахунків товщини шару волокна без використання експериментальної константи фільтрації для процесів стерилізації повітря -да ють малодостовірні результати, тому в даному підручнику не приводяться.
В якості фільтрувальних матеріалів використовують перхлорвінілове волокно з термостійкістю 60...70°С (марки ФП, ФП-15-1,5), поліакрилонітрильне волокно з термостійкістю до 180°С (ФПАН-10-3,0) або до 250°С (ФПАР-15-1,5) скловолокна (СТВ) або базальтові волокна. Товщини волокон коливаються від 1,5 до 21 мкм. базальтові волокна випускають товщиною від0,5 до 1 мкм. Всі волокна, крім перхлорвінілових, допускають стерилізацію гострою парою. Перхлорвінілові стерилізують токсичними газами (наприклад, оксидом етилену
71
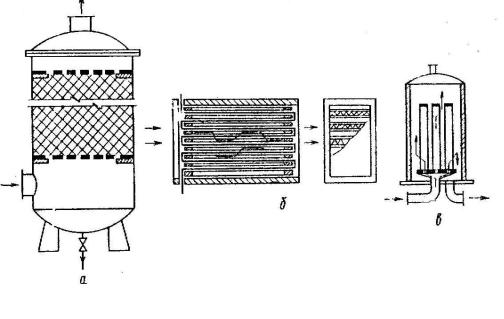
або газоподібним формаліном). Волокна укладають у вигляді готових пресованих шарів з щільністю упакування 0,043...0,19 від об’єму (переважно 0,1...0,15).
Набивні фільтри мають ряд недоліків:
а). Внаслідок відносно невеликої площі перерізу для перепуску великих об’ємів повітря доводиться збільшувати швидкість фільтрування(1...3 м/с), що веде до утворення каналів і до так званих краєвих ефектів, завдяки яким повітря без фільтрування проходить вздовж стінки апарата.
б). Попадання крапельної вологи веде теж до утворення каналів і -про ходженню повітря через них без фільтрування.
в). Набивні фільтри мають значний гідравлічний опір і важкі експлуатації.
Нині їх застосовують лише в якості першого ступеню стерилізаційного очищення. На рис. 4.3 та 4.4 наведені конструкції набивних фільтрів Гіпромедпрому та КБ ВНДІФСа.
Рис. 4.3. Основні типи фільтрів тонкого очищення і стерилізаці, де а – набивний (глибинний); б – з розгорнутою поверхнею (рамковий); в - сітчастий (абсолютний) патронного типу.
В якості індивідуальних фільтрів широко застосовують рамочні або патронні фільтри з тканиною Петрянова на основі перхлорвінілового волокна.
На рис.4.3. представлена конструкція фільтру ВНДІФСа з тканиною ФПП-15 патронного типу.
Фільтр уявляє собою сталевий циліндр з від’ємною кришкою і конічним дном. Усередині апарата встановлюють 73 циліндричних перфорованих трубок, обгорнутих тканиною Петрянова. Загальна площа фільтрування – 17,5 м2. Після проходження крізь тканину повітря стерилізується. Продуктивність цього фільтра 1000 м3/год.
72
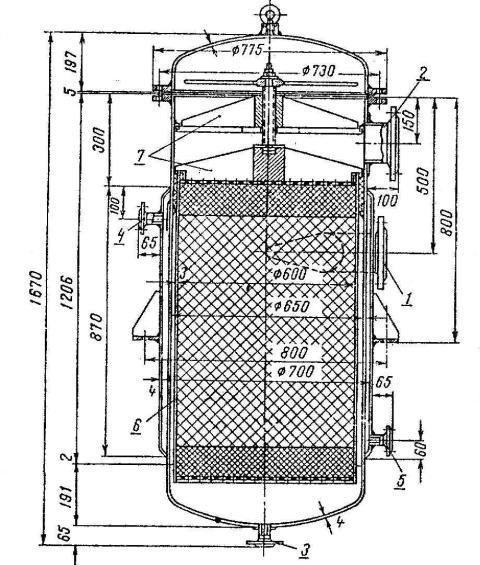
Рис 4.4. Набивний фільтр конструкції Гіпромедпрому, де 1 – штуцер для |
|
||||
входу повітря; 2 – штуцер для виходу повітря; 3 – штуцер для продування; |
4, 5 |
|
|||
– штуцери для пари та конденсату; 6 – патрон; 7 – пристрій для притискання. |
|
||||
До системи очищення повітря входять різні апарати (обладнання): |
|
|
|||
· фільтр для |
очищення повітря |
від пилу та інших |
механічних |
домішок |
|
(фільтр для вилучення механічних часток); |
|
|
|
||
· система |
стабілізації |
термодінамічних |
показників |
п |
|
(кондиціонери); |
|
|
|
|
|
·головний повітряний фільтр (груповий фільтр) для очищення всього повітря, що поступає із повітродувки;
·індивідуальний повітряний фільтр перед кожним ферментером і посівним апаратом.
Вибір фільтру попередньої очистки повітря орієнтований на ефективне видалення крупних фракцій контамінантів з повітря, які можуть пошкодити компресійне обладнання. Фільтр попередньої очистки повітря встановлюють перед повітродувкою, щоб у неї не потрапляли пил та механічні забруднення повітря. Перевага віддається фільтрам простої конструкції, які можна регенерувати.
73
Після цього повітря потрапляє в головний повітряний фільтр, який використовують для підготовки повітря групи ферментерів. Фільтруючим матеріалом багатошарова конструкція яка складається з шару активованого вугілля висотою 700 – 900мм, над та під яким укладають шар скляної вати (100
– 150мм) для усунення можливості провалу та уносу частинок вугілля. Діаметр волокна скловати дорівнює 21 мікрометру.
Суттєве значення при виборі технології очистки повітря має стабілізація термодинамічних показників, так як вологість повітря має суттєвий вплив на ефективність очистки.
Головний повітряний фільтр встановлюється поблизу повітродувки, при роботі якої повітря внаслідок адіабатичного стискання нагрівається до 120– 180°С і вище. Якщо повітря, що поступає у ферментер має температуру вищу за 60°С, його необхідно охолодити, для чого встановлюються кондиціонери, що охолоджуються водою. Для стабілізації потоку повітря і попередження його пульсацій потрібно мати ланцюг часової затримки цю роль може виконувати місткість – ресивер.
Для остаточного очищення повітря перед кожним ферментером встановлюється індивідуальний повітряний фільтр. Фільтруючим матеріалом може бути тонка скляна вата, волокна якої мають діаметр не більше 1 – 2мкм широко використовують базальтове тонке та супертонке волокно (БСТВ). Діаметр волокна дорівнює 0,7-1,0мкм.
Конструкція цього фільтра є дещо складною, оскільки для завантаження та розвантаження необхідно виймати із фільтра фільтруюче завантаження. Часто її укладають недостатньо точно, що не забезпечує необхідної щільності, і тому повітря частково проникає безпосередньо із кільцевого простору вгору на вихід, обминаючи фільтруючий шар.
Широке розповсюдження мають фільтри в яких фільтруючі елементи виготовлені з тканини Петрянова (ацетилцелюлози).
У зв’язку з тим, що при виробництві ферментних препаратів напір повітря із повітродувки не перевищує 5–6 м вод.ст., бажано знизити втрати напору в повітряних фільтрах. Цього можна досягти, використовуючи як фільтруючий матеріал тканину Петрянова. Переваги цієї тканини перед іншими фільтруючими матеріалами в тому, що спостерігається малий опір рухові повітря і висока ефективність стерилізація повітря.
До недоліків відносяться недостатня механічна міцність і швидке псування при змочуванні. Тому необхідно приймати заходи для захисту тканини від змочування конденсатом пари в процесі стерилізації ферментеру.
Вибір конструкції (типу) фільтра обумовлює вибір методу стерилізації. Фільтри в яких використовуються мінеральні волокна, керамічні або металокерамічні перегородки стерилізують гострою парою. Для фільтрів з полімерних волокон загальновизнаним є метод стерилізації хімічними речови- нами-аерозолем формаліна.
Існує цілий набір методів стерилізації повітря, але всі вони повинні гарантувати ефективність вилучення контамінантів Е=99,999999%. В
74
біотехнологічній практиці застосовується типова багатоступенева система очистки, яка дозволяє послідовно вилучати механічні та мікробні контамінанти.
Нами пропонується використати стандартну очистку, яка складається з блоків:
-Попереднє очищення повітря;
-Стабілізація термодинамічних параметрів повітря;
-Стерилізація повітря у головних фільтрах;
-Стерилізація повітря в індивідуальних фільтрах.
[11] с.177-238
Запитаня для самоперевірки
1. Дайте перелік стадій предферментаційних процесів.
2.Санітарна підготовка виробництва: перелік стадій.
3.Які існують методи стерилізації повітря?
4.Дайте перелік стадій підготовки поживного середовища (ПС).
5.Які існують способи стерилізації і як врни використовуються для стерилізаціхх поживного середовища?
6.Устаткування та апаратура для приготування та стерилізації ПС: класифікація та характеристика.
75
5. СТАДІЇ ОСНОВНОГО ТЕХНОЛОГІЧНОГО ПРОЦЕСУ
Стадії основного технологічного процесу починаються з отримання посівного матеріалу, продовжуються у вигляді промислового біосинтезу і закінчується виділенням та стандартизацією готового продукту.
5.1. Проектування відділення біосинтезу
Найбільш складною і відповідальною ділянкою біотехнологічного виробництва є стадія біосинтезу, основною метою якого є отримання максимальної кількості цільового продукту у межах генетично детермінованих властивостей біологічних агентів, за рахунок оптимізації факторів оточуючого середовища. В умовах промислового виробництва оточуюче середовище штучно створюється в спеціальній апаратурі– ферментері (біологічному реакторі). В загальному вигляді ферментер виконує дві функції– здійснює транспортні, масообмінні процеси, а також функціонує як теплообмінник. По сутності процесів, що протікають в ферментері він відноситься до біологічних систем, але конструктивне оформлення реалізується, як для звичайного хімічного реактора. Це реальне протиріччя може бути ліквідоване тоді, коли при виборі, проектуванні та оптимізації роботи ферментера конструктор буде виходити з фенотипічних оз-
нак біологічних агентів. Постійне розширення інформаційного кола |
про |
фізіологію біологічних агентів, прогрес у використанні рекомбінантних культур |
|
і клітинних гібридом висуває ряд вимог до конструкції ферментаційного облад- |
|
нання. Серед базових вимог(обмежень), які потрібно враховувати |
при |
конструюванні або виборі типового ферментера необхідно виділити слідуючи: - гідродинамічна обстановка в ферментері повинна забезпечити одночасну реалізацію масопереносу в двох-(поживне середовище – клітини біологічного агента, трьох- ( газ – поживне середовище - клітини біологічного агента), і чьотирьохфазних ( газ – поживне середовище – клітини біологічного агента – не-
розчинний або слабо розчинний субстрат) системах;
-негативний вплив турбогіпобіозу (зрізових зусиль) на суспендовані клітини або на клітинні агломерати, найбільш вразливі до зрізових зусиль клітини міцеліальних грибів, клітини тварин та клітини рослин;
-широкий спектр діапазонів швидкостей росту, час генерації знаходиться в діапазоні від десяти хвилин до декількох діб;
-значна кількість біологічних агентів висуває високі вимоги до рівня асептики в процесі культивування;
-при культивуванні аеробних біологічних агентів єдиним економічно доцільним джерелом кисню є повітря, при цьому виникає ряд обмежень в процесі масопередачі на фазових переходах газ– культуральна рідина та культуральна рідина – клітина;
-процеси біосинтезу супроводжуються інтенсивним піноутворенням,
що |
обумовлює |
зниження |
корисного |
об’єму |
ферментера |
і |
визн |
негомогенність культуральної рідини; |
|
|
|
|
76
-інтенсифікація біотехнологічних процесів несуттєво залежить від
конструктивних |
змін |
в |
апарату; процесиі |
біосинтезу |
в |
основному |
детерміновані генетичним потенціалом біологічного агента. |
|
|
||||
Вибір типового ферментеру, конструювання нового ферментаційного об- |
||||||
ладнання, модернізація відомих конструкцій можливе тільки в тому випадку, |
||||||
коли врахована |
специфіка |
технологічного процесу і фенотипічні ознаки |
||||
біологічних агентів. Конструктивний розрахунок |
ферментеру, розрахунок |
|||||
гідродинамічних, |
масообмін |
|
них, теплообмінних характеристик, |
врахування |
умов диспергації фаз утворення потоків, рівень сегрегації поживного середовища можна реалізувати тільки для конкретних груп апаратів.
На сьогоднішній день відома значна кількість класифікацій ферментерів в
яких |
враховуються |
різні |
конструктивні, експлуатаційні |
та |
технологічні |
||
особливості ферментерів. В більшості випадків ферментери класифікують по |
|||||||
засобу |
введення |
енергії, так |
як |
енергетичні |
чинники |
обумовлюють |
гідродинамічні та масообмінні показники. Існують три основні засоби введення енергії в поживне середовище (рис 5.1.).
В основі проектування відділення біосинтезу, під час попереднього вибору ферментеру користуються схемою у відповідності з якою ферментери розділені по принципу введення енергії у культуральну рідину і ця класифікація орієнтована на виробництво мікробного білку(кормового білку). Запропонована класифікація орієнтована на аеробні процеси, як найбільш поширені в
біотехнології |
і вибір враховує інтенсивність масопередачі кисню у вигляді |
||
об’ємного |
коефіцієнту масопередачі. Представлена |
система |
класифікації |
враховує ефекти, що виникають при введенні визначеної кількості енергії. Ба- |
зовим ефектом є швидкість сорбції кисню кгО2 / м3 год Кl a (Kv а).
Висновки з представленої схеми: Для ферментерів 1 групи Kv а£4,0-4,5.
Ферментери з введенням енергії газовою фазою придатні для культивування бактерій та дріжджів.
Для ферментерів 2 групи Kv а³5,0-6,0, максимальний рівень турбогіпобіозу.
Для ферментерів 3 групи Kv а може приймати будь-яке значення, але ці апарати як правило використовують для процесів де потрібний мінімальний рівень турбогіпобіозу.
В основі проектування відділення біосинтезу, під час попереднього вибору ферментеру користуються схемою у відповідності з якою ферментери розділені по принципу введення енергії у культуральну рідину і ця класифікація орієнтована на виробництво мікробного білку(кормового білку). Запропонована класифікація орієнтована на аеробні процеси, як найбільш поширені в
біотехнології і вибір враховує інтенсивність масопередачі кисню у вигляді об’ємного коефіцієнту масопередачі. Представлена система класифікації враховує ефекти, що виникають при введенні визначеної кількості енергії. Базовим ефектом є швидкість сорбції кисню кгО2 / м3 год Кla (Kv).
Висновки з представленої схеми: для ферментерів 1 групи Кv ≤ 4.0-4.5.
77
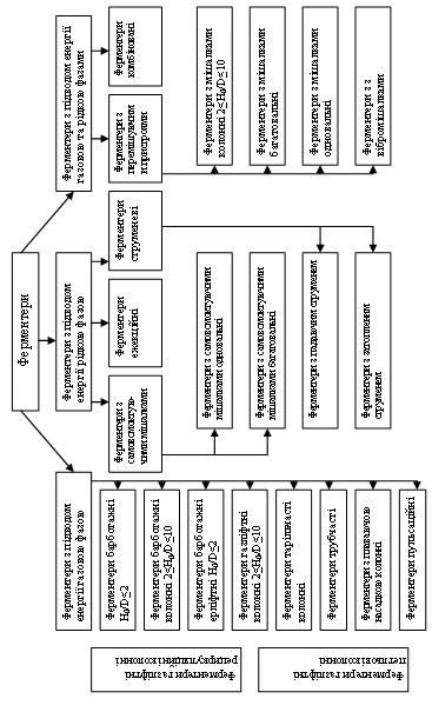
Ферментери з введенням енергії газовою фазою придатні для культвування бактерій і дріджів.
Рис.5.1. Схема класифікації ферментерів для аеробного біосинтезу
Для |
ферментерів 2 групи Kv |
³5,0-6,0, |
максимальний |
рівень |
турбогіпобіозу. |
|
|
|
|
Для |
ферментерів 3 групи Kv може |
приймати |
будь-яке значення, але ці |
апарати як правило використовують для процесів де потрібний мінімальний рівень турбогіпобіозу.
78