
- •1.1. Організаційні форми та методи проектування
- •1.1. Організаційні форми та методи проектування
- •1.2. Блок-схема етапів проектування. Програмно-цільова структура проектування
- •Рис. 1.2. Блок-схема процесу проектування
- •Одержано
- •Вимоги до змісту технічного регламенту
- •Позначка
- •Найменування
- •Примітка
- •Глибинний спосіб вирощування
- •Культивування умовно-асептичне
- •Вибір ферментеру
Ця класифікація придатна для рідкофазних аеробних або анаеробних біотехнологічних процесів. Недоліком цієї класифікації є те що вона не враховує ряд технологічних особливостей процесу:
-рівень асептики;
-вид технологічного процесу – періодичне, напівбезперервне або безперервне культивування;
-рівень сегрегації фаз – використання імобілізованих клітин, біоплівок, флокул та інше.
Класифікація ферментерів за способом введення енергії дозволяє згрупувати їх в блоки для яких можна розробити єдині методики інженерного розрахунку основних конструктивних елементів і режимів роботи.
Глибинне культивування біологічних агентів є найбільш поширеним методом, який використовується в біотехнології для отримання мікробних мас та біологічно активних речовин. Ферментери для глибинного культивування дозволяють найбільш ефективно створювати оптимальні умови в оточуючому біологічні агенти просто для реалізації їх потенціальних властивостей.
Обґрунтування вибору способу біосинтезу
Процес виробництва біологічно активних речовин в тому числі і біомаси технологічно і технічно може реалізовуватися різними способами. Особливості обраних способів біосинтезу впливатимуть на хід всього виробничого процесу. Тому технологічна схема, що покладена в основу виробництва повинна забезпечувати найкраще поєднання виробничих заходів з точним дотриманням оптимальних умов проведення кожної виробничої стадії.
Культивування продуцентів продуцентів біологічно активних речовин можна здійснювати двома способами: поверхневим і глибинним.
Поверхневий спосіб вирощування Культуру вирощують в тонкому шарі пористого(сипучого) середовища з
природною або примусовою аерацією.
Спосіб не є актуальним, оскільки суттєвими недоліками вирощування поверхневим методом являються велика трудомісткість робіт, необхідність у громіздкому обладнанні, недосконала гігієна праці. При цьому отримуваний продукт часто має незадовільну якість і активність препарату, як правило, низька. У зв’язку з цим поверхневий метод отримання біологічно активних речовин витіснився глибинним.
Глибинний спосіб вирощування
При глибинному способі культуру вирощують на рідкому середовищі при перемішуванні і примусовій аерації.
Метод глибинного вирощування застосовується в двох формах: культивування в умовно-асептичних умовах та культивування в асептичних умовах.
Культивування умовно-асептичне
Посівну культуру готують в стерильних умовах, але біосинтез проводять у відкритих ферментерах. Аерація з одночасним перемішуванням досягається за допомогою перемішувачів різних конструкцій, наприклад, типу полої труби. Такий перемішувач складається з вертикальної труби, що обертається, на нижньому кінці якої є два або чотири відрізки труб скошені під кутом45° в бік,
79
протилежний напрямку обертання. Вертикальна труба відіграє роль валу і приводиться в обертання від мотора через передачу. Відрізки труб зі скошеними кінцями, обертаючись разом із вертикальною трубою, перемішують середовище, засмоктують повітря і подають його в рідину; таким чином культуральна
рідина аерується. Для нагріву і охолодження середовища в ферментерах встановлюється також змійовик з підводом у нього пари та .водиБіосинтез триває 24 - 36 годин при працюючому перемішувачі. Процес закінчується при максимальному накопиченні біологічно активних речовин; рН культуральної рідини під кінець біосинтезу досягає 6,6 – 6,8.
В процесі біосинтезу систематично відбирають проби для аналізу культури на відсутність сторонньої мікрофлори, що вказує на нормальне протікання
процесу. Наявність поодиноких сторонніх мікроорганізмів в перший період біосинтезу (до 24 год) не затримує розвиток продуцента. По мірі накопичення біомаси розвиток сторонніх мікроорганізмів пригнічується і вони зникають. Однак, якщо інфекція не зникає і залишається до кінця процесу біосинтезу, то культура вважається браком.
Асептичний біосинтез
Даний спосіб має ряд переваг, оскільки передбачає скорочення виробничих площ, виключення тяжкої невиробничої ручної праці, покращення гігієни праці, спрощення механізації та автоматизації виробництва, можливість переходу на безперервний спосіб культивування. Крім того, найбільш раціонально використовуються поживні речовини, що дає можливість значно скоротити відходи виробництва у вигляді нерозчинних осадів твердого поживного середовища, одержати продукт вищої активності.
Глибинне культивування проводять у ємностях, що називаються ферментерами. Основна вимога до ферментеру– можливість проведення процесу культивування продуцента в асептичних умовах при інтенсивній аерації середовища. У процесі культивування маємо справу зі складною трьохфазною системою рідина – тверде тіло – газ. У такій системі утруднені масообмінні процеси, і тому ускладнюється апаратурне оформлення всієї стадії вирощування.
По заповненню ферментеру середовищем і перевірці температури, котра повинна бути не вищою28°С, у ферментер із посівного апарата спускають по трубопроводу посівну культуру. Кожне місце введення посівної культури в цей трубопровід і кожний вихід з нього у ферментер захищені паровими пробками.
Після того, як внесли посівну культуру, починається процес вирощування продуценту. Вирощування проводять при постійній аерації. Повітря для аерації через трубопровід поступає на очищення у фільтр і в очищеному вигляді подається в середовище. Необхідна для вирощування температура(27 - 28°С) підтримується подачею води в сорочку чи охолоджуючі труби. Для усунення піни, що утворюється в процесі вирощування додається піногасник із дозатора.
Оскільки продуцент ферментів належить до числа аерофільни мікроорганізмів, то для їхнього нормального розвитку та функціонування необхідне підведення кисню. При глибинному вирощуванні повітря, як прави-
80
ло, вводиться в нижню частину ферментера за допомогою різноманітних -об ладнань для рівномірного розподілення його по всьому перерізу ферментера.
Дихання мікроорганізму відбувається тільки за рахунок кисню, розчиненого в середовищі. Оптимальними є умови для дихання, якщо в середовищі наявна деяка кількість розчиненого вільного кисню. Фактично наявність розчиненого кисню в середовищі визначається відношенням між швидкістю вживання його культурою мікроорганізмів і швидкістю його розчинення в середовищі, яка, звісно, повинна бути більшою. В іншому разі вживання кисню буде визначатися не фізіологічною необхідністю мікроорганізму, а тією кількістю кисню,
що |
встигне |
розчинитися |
в |
умовах , аераціїщо приведе |
до |
кисневої |
недостатньості, |
що негативно |
вплине на розвиток культури: сповільнюються |
окислювальні процеси. Внаслідок цього культура, що виросла в умовах кисневого голодування, характеризується низькою інтенсивністю дихання і пониженою здатністю до біосинтезу Ферментні препаратиу.
Отже, основним призначенням аеруючого обладнання в ферментері є забезпечення умов для максимального розчинення кисню повітря, щоб в середовищі при вирощуванні культури знаходився вільний розчинений кисень.
Існує багато способів аерації і перемішування середовища. Для вибору оптимального варіанту ферментеру проаналізуємо конструкції деяких з них.
Вибір ферментеру
Ферментери з введенням енергії аеруючим газом. Самим простим і найбільш розповсюдженим є подача повітря в рідину через барботери або інші аеруючі пристрої (дифузори, форсунки та ін). Група ферментерів в які енергія вводиться аеруючим газом є найбільш поширеною і відомою. Апарати цієї групи здавна використовуються для отримання мікробної маси в асептичних та умовно асептичних типах біосинтезу. Технологічні переваги цих апаратів базуються на простоті конструкції, відсутності рухомих елементів і простоті ке-
рування, що обумовлює високу експлуатаційну надійність ферментерів цієї групи. Конструктивні особливості барботажних ферментерів визначаються типом аератора і об’ємом апарата. Серед барботажних ферментерів найбільш відомі апарати типу ВДА конструкції М.Ф.Осипова і М.І.Дерканосова, ще випускаються ферментери ВДА 2А-100 (розробка М.П.Гандзюка та інших) з новою системою аерації. Геометрична місткість серійних апаратів - 30 і 100м3.
Ступінь подрібнення повітря при використанні барботерів визначається числом отворів і їх діаметром. При цьому застосовуються барботери різноманітної форми (кільцеві, променеві, і т.д.). Діаметр отворів складає 0,5 – 2мм. Число отворів визначається з розрахунку, щоб їх сумарна площа забезпечувала необхідну швидкість повітря при виході з них. Для одержання макси-
мального ступеня диспергування повітря в деяких випадках допускається швидкість до 100м/с, однак при цьому спостерігається значна втрата напору, тому необхідно підвищити тиск повітря, що подається до 2 – 2,5 атм. Тому, щоб уникнути значних втрат напору, швидкість повітря повинна бути в межах5 – 10м/с.
81
Але використання барботерів має суттєві недоліки. Як би мілко не розпилювалося повітря, при проходженні через рідину окремі маленькі на початку бульбашки збільшуються, внаслідок чого величина поверхні контакту фаз зменшується і може виявитися недостатньою. Єдиний спосіб посилення масообміну в цьому випадку– збільшення подачі повітря. Тому при аерації за допомогою барботерів завжди необхідна велика затрата повітря.
Впроцесі росту культури постійно виникає нерівномірність розподілення
всередовищі поживних речовин і продуктів обміну, оскільки найближчі до поверхні культури шари середовища збіднюються першими й збагачуються останніми. Тому енергійне перемішування при вирощуванні продуцента є необхідною умовою нормального розвитку мікроорганізму і максимально можливого накопичення ферментного препарату.
Перемішування середовища за допомогою барботеру є недостатнім, особ-
ливо для ферментерів об’ємом4 – 5м3 і більше. Тому аерування і перемішування середовища тільки за допомогою барботеру допустиме лише у випадках, коли вимоги до активності вирощуваної культури не є високими, наприклад в посівних апаратах.
В процесі проектування відділення біосинтезу треба прийняти до уваги, що більшість ферментерів системи ВДА має циліндричну форму, має сорочку для терморегуляції культуральної рідини. Сорочка секційна і складається з10 поясів. Аераційна система представлена трубою та коробами, що прокладені на
дні ферментера. Для миття коробів змонтовано сопло. |
|
|
|||
Пластинчата |
аераційна |
система |
апаратів |
ВДА |
складається |
розподільного колектора та короба, який зверху закритий перфорованими пластинами з отворами діаметром 0,5 мм. В деяких апаратах змонтовані трубчасті системи аерації, що складаються з перфорованих трубок.
Ферментери з контактними пристроями. Суттєвим недоліком барбо-
тажних ферментерів є невисокий рівень швидкості розчинення кисню(1-2 кг/м3×год). Основною причиною цього є низький рівень -макроімікро турбулентності, недостатня циркуляція середовища.
Для ліквідації цього недоліку розроблені барботажні ферментери з нерухомими контактними елементами які забезпечують утворення та формування поверхні контакту фаз. До апаратів цієї групи відносяться барботажні колоні, газліфтні колоні, тарілчасті колоні. Збільшення поверхні фазового контакту реалізується слідуючим чином:
-додаткова диспергація газової фази в рідині;
-розділення рідкої фази на шари (санкціонування) для створення кінцевої кількості ступіней контакту фаз,
-забезпечення таких умов формування потоків газорідинної емульсії
при яких частота поновлення поверхні |
фазового контакту максимальна, |
|||||
збільшення часу перебування газової фази в рідині |
|
|
|
|||
Серед |
ферментерів |
з |
контактними |
елементами |
найбільш |
відо |
барботажні колоні з”затопленими” тарілками. Тарілки можуть бути різних |
|
|||||
конструкцій, |
але їх поєднує , |
тещо вони |
забезпечують |
формування |
та |
|
перерозподіл потоків газу та рідини. |
|
|
|
|
82
Найбільш простим типом контактних елементів є тарілка, яка перфорована круглими отворами які перекривають всю площу перерізу апарата можливе ярусне розташування тарілок по висоті апарата.
Перспективними визнані конструкції апаратів яких комбіновані контактні газорозподілюючі пристрої і вмонтовані теплообмінники.
Ферментери барботажно-ерліфтного типу застосовують для отримання мікробного білку. Апарат представляє собою вертикальну циліндричну місткість H/d<2. Характерною конструктивною особливістю є те що всередині апарату знаходиться один або декілька дифузорів(стаканів) або перегородок для примусового розділення потоків циркулюючої культуральної рідини. Одночасно вони виконують роль теплообмінників. В тому випадку, коли їх декілька, дифузори рівномірно розміщують по перерізу апарата або монтують
концентрично. Газорозподільний пристрій розташовують біля дна в зоні висхідних потоків.
До розгляду пропонується декілька найбільш поширених конструкцій промислових ферментерів .
Ферментери системи Лефрансуа– Маріє. (Ле Франсуа - Марійє). Для виробництва мікробного білку–гідролізно-дріжджового походження використовують апарати місткістю 250, 320, 600 та 1300 м3. Апарат представляє собою циліндричну місткість, всередині якого концентрично розташований дифузортеплообмінник. Ферментер не має системи піногасіння. Піна руйнується підвагою стовпа рідини при її циркуляції. Повітря в ферментер поступає через повітропровід, розташований по центру апарата. В нижній частині апарата повітропровід спирається конічну основу, яка утворює з дном кільцевий зазор (кювету) для виходу повітря. Утворена газорідинна дисперсія піднімається по дифузору майже до верху апарата. Діаметр дифузора повинен відповідати потоку диспергованої культуральної рідини. Частина повітря відділяється від потоку диспергованої рідини і через відкритий люк виходить з апарата, частина повітря з диспергованою рідиною по кільцевому зазору між стінкою апарата і дифузором сходить в низ. Піна зріджується і рідина повертається в кювету, рідина знову диспергується і піднімається по дифузору. Циркуляція проходить з швидкістю 2-3хв-1.Швидкість розчинення кисню в промислових апаратах не більше 2-3кг/м3*год.
Промислові апарати мають висоту12-15м,піна в них піднімається на1012м.Монолітний стовп рідини має 3,5-4,5м
Ерліфтно-периферійні та ерліфтнібагатозонні. Ерліфтні ферментери відрізняються від базової системи Лефрансуа конструкцією комунікацій для підведення поживних компонентів та установкою пінонаправляючих“парасолей”.
Ерліфтно-периферійний ферментер. Апарат складається з циліндричного
корпуса |
в |
середині |
якого |
концентрично |
розташовані |
два - дифуз |
теплообмінника. |
|
|
|
|
|
|
В |
центрі |
апарата |
розташована труба |
для підведення |
, повітряяка |
спирається на повітророзподільний пристрій, який утворює кільцевий зазор між
83
стінкою та дном ферментера через який виходить повітря. В нижній частині труби розташовані отвори для виходу повітря в центральний дифузор. Для до-
даткового |
охолодження |
використовують |
систему зовнішнього зрошення. |
Нагріта |
вода збирається |
в кільцевому |
кармані. Ферментер відрізняється |
помірними витратами на аерацію високою експлуатаційною надійністю, низькими експлуатаційними витратами. До недоліків відноситься низький рівень масопередачі кисню, (KLa=250-350 год –1).Причиною недостатньо високого рівня масопередачі кисню є погана диспергація повітря.
Ерліфтний багатозонний ферментер Апарати цієї серії, як і попередня конструкція представляють собою модифікований ферментер Лефрансуа. В апараті змонтовані три дифузора-теплообмінника. Повітря поступає через центральні труби, які спираються на кювети і утворюють з ними кільцеві зазори для виходу повітря в зони, які обіймають дифузори На повітряних трубах і в верхній частині над дифузорами встановлені парасолі для повернення піни в потік.
Ферментери з циркуляційними трубами. Ферментер системи Шоллер-
Зайделя. Аерація рідини забезпечується в12 циркуляційних трубах діаметром 0,35м, які змонтовані навколо корпуса ферментера. Повітря подається в циркуляційну трубу через керамічну свічку. Апарат має виносний механічний піногасник. Для охолодження використовують повітря або зовнішнє зрошення.
Ферментер системи УкрНДІСПа. Апарат розроблений О.У.Мамунею з співавторами представляє собою вертикальну циліндричну місткість об’ємом 600м3, всередині якої змонтовані циркуляційні труби з сорочками. В ферментері збережений багатозональний принцип ерліфтного перемішування. Поживне середовище по колектору безперервно подається повітророзподільний пристрій диспергується потоком повітрям і піднімається по циркуляційній трубі.
Серед ерліфтних апаратів особливе місце займаєгазліфтний ферментер, який виготовляє Дзержинський завод хімічного машинобудування місткістю 100 м3. Ферментер призначений для проведення біосинтезу в асептичних умовах, наприклад, для виробництва кормового концентрату лізину. Корпус апарата представляє собою вертикальну циліндричну місткість з еліптичними приварними днищем і кришкою. В корпусі апарата розміщені розташоване в днищі контактний пристрій для диспергації повітря, теплообмінні пристрої у вигляді
спіральних змійовиків, контактні диспергуючі пристрої захисні обичайки у вигляді стаканів циркуляційного контуру, відбиваючі перегородки в нижній частині спіральних змійовиків. Суттєвою відмінністю цього ферментеру від інших конструкцій є те, що в апараті змонтовані контактні пристрої у вигляді
провальних |
тарілок. Контактні |
елементи |
забезпечують |
диспергацію |
||
взаємодіючих |
фаз, оновлення |
поверхні |
фазового |
контакту, створюють |
||
циркуляційні потоки газорідинної дисперсії. Схема руху потоків культуральної |
||||||
рідини представлена. |
|
|
|
|
|
|
Технічна характеристика газліфтного ферментера місткістю 100 м3. |
|
|||||
Об’єм, м3 |
|
|
|
100 |
|
|
84
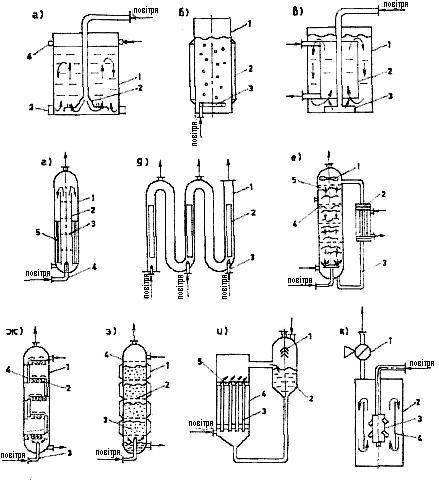
Коефіцієнт заповнення, % |
70 |
Витрати повітря, м3/год |
2250-6650 |
Площа поверхні теплообміну, м2 : |
|
сорочки |
75 |
змійовиків |
116 |
Потужність електродвигуна привода піногасника, кВт 13
Число обертів привода піногасника, с-1 |
12 |
|
Габаритні розміри, мм |
3992 * |
3560 * 15460 |
Маса, кг |
|
43000 |
Рис.5.2. Схеми ферментерів з підводом енергії газовою фазою:
а – Ферментер барботажний Н0/D≤2: 1 – корпус, 2 – повітрярозподілювач, 3 – карман, 4 – колектор; б – Ферментер барботажний колонний 2<H0/D<10: 1 – корпус, 2 – сорочка, 3 – повітрярозподілювач; в – Ферментер барботажний ерліфтний Ho/D<2: 1 – корпус, 2 – дифузор-теплообмінник, 3 – повітрярозподілювач; г – Ферментер газліфтний колонний 2<H0/D<10: 1 – корпус, 2 – дифузор, 3 – диспергатор, 4 – повітрярозподілювач, 5 – теплообмінник; д – Ферментер газліфтий петльовий колонний: 1 – корпус, 2 – дифузор, 3 – повітряпровідний патрубок; е – Ферментер газліфтний рециркуляційний колонний: 1 – піногасник, 2 – теплообмінник, 3 – циркуляційна труба, 4 – диспергатор, 5 – корпус; ж – Ферментер тарілчастий колонний: 1 – корпус, 2 – тарілка, 3 – повітряпровідна труба, 4 – переливна труба; 3 – Ферментер з плаваючою на-
85
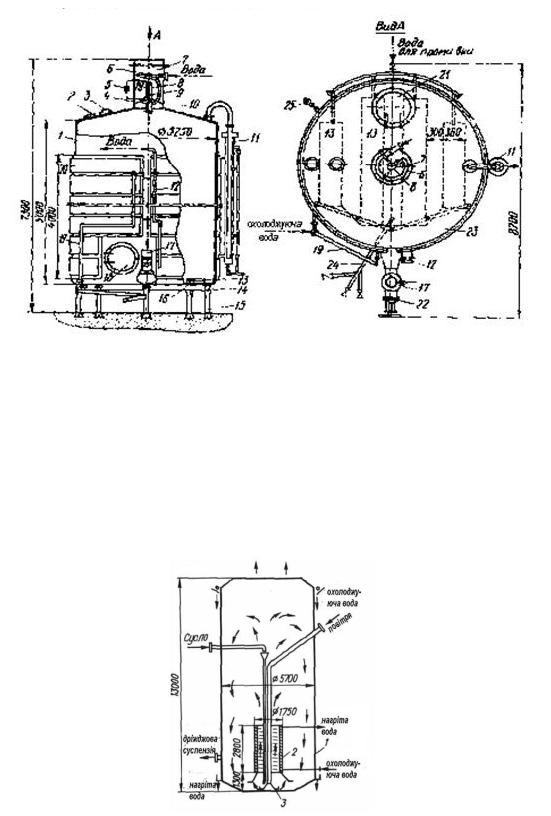
садкою колонний: 1 – рубашка, 2 – тарілка, 3 – насадка, 4 – корпус; и – Ферментер трубчастий: 1 – піногасник, 2 – ємність, 3 – труби, 4 – корпус, 5 – розподільна перетинка;к – Ферментер газліфтний пульсаційний: 1 – клапан, 2 – корпус, 3 – аератор, 4 – дифузор-теплообмінник.
Рис.5.3 . Апарат для вирощування дріжджів ВДА-100:
1 — резервуар; 2 — смотрове вікно; 3 — освітлювач; 4 — муфта; 5 — чотирьохходовий кран; 6 — шланг; 7 — витяжна труба; 8 — циліндр; 9 — шток; 10 — заслінка; 11 — гідрозатвір; 12 — колектор для відводу води; 13 — розподільні короби; 14 — балка; 15 — стійка; 16 — сопло; 17 — труба для подачі повітря; 18, 21 — люки; 19 — колектор для подачі води; 20 — охолоджуюча сорочка; 22 — засувка; 23 — колектор; 24 — труба для відводу культуральної рідини; 25 — мірне скло.
Рис. 5. 4. Апарат для вирощування дріжджів системи Лефрансуа—Марійе: 1 — корпус; 2 — дифузор; 3 — кювета
86
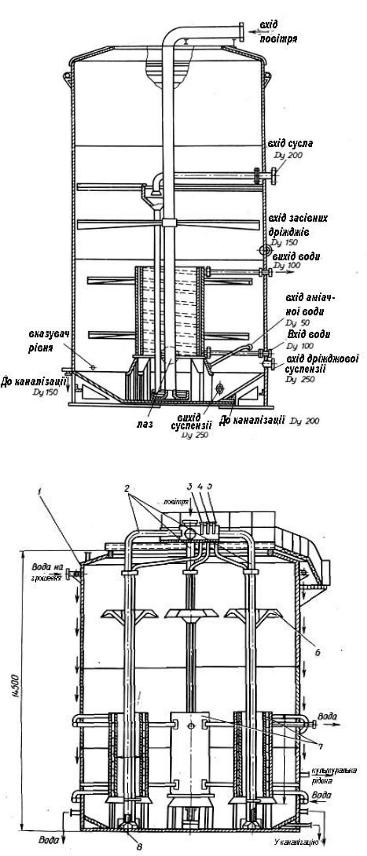
Рис.5.5. Апарат для вирощування дріжджів з аерліфтною системою повітрярозподілення
Рис.5.6. Апарат для вирощування дріжджів — ферментер місткістю 1300 м3: 1
— корпус; 2 — газовід; 3,4,5 — штуцери для подачі поживного та аміачного середовищ та засівних дріжджів; 6 - відбійник; 7 – циркуляційні дифузори; 8
— кювета
87
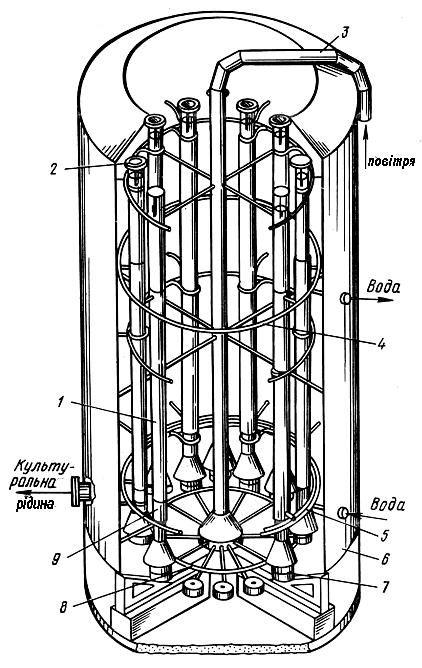
Рис.5. 7. Ферментер системи УкрНИИСПа:
1 — циркуляційна труба; 2 — відбивачі; 3 — повітрепідвід; 4, 5 — колектори для води; 6 — корпус; 7 — повітрерозподілювач; 8 — колектор повітря; 9 — колектор рентабельного середовища
Крім базового показника– способу введення енергії, ці ферментери поєднує той факт, що вони призначені для широкого спектру технологічних процесів (їх поєднує універсальність). До специфічної особливості треба віднести те, що на стадії промислового біосинтезу такі ферментери мають значний геометричний об’єм (від 150 до 1300м3).
Переваги у порівнянні з іншими простота оформлення, технологічна про-
стота.
88
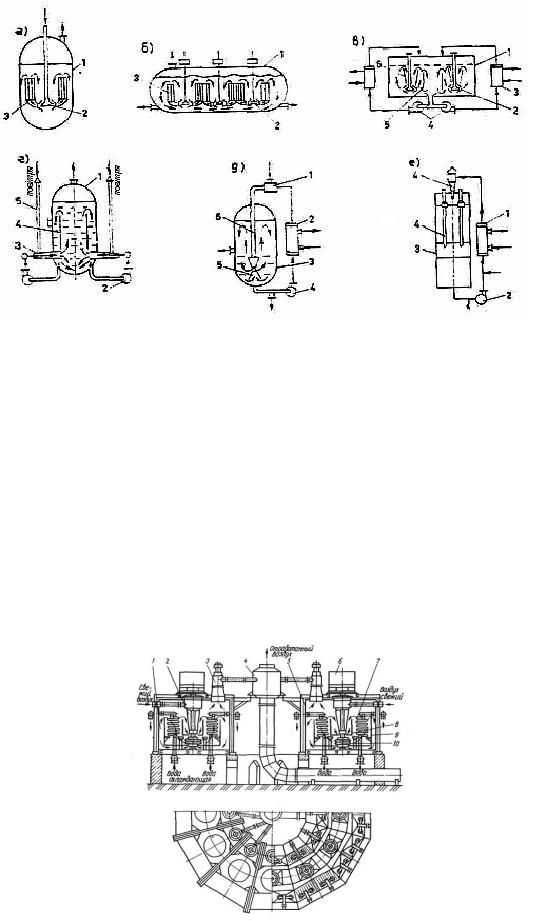
Ферментери з підводом енергії рідкою фазою:
Рис. 5.8 . Ферментери з підводом енергії рідкою фазою:
а — одновальний ферментер із самозасмоктуючою мішалкою: 1 — корпус, 2 — самозасмоктуюча мішалка, 3 — циркуляційний контур-теплообмінник;
б — ферментер із самозасмоктуючими мішалками багатовальний: 1 — корпус, 2 — самозасмоктуюча мішалка, 3 — теплообмінник;
в — ферментер із самозасмоктуючими мішалками багатовальний з зовнішнім циркуляційним контуром: 1 — корпус, 2 — самозасмоктуюча мішалка, 3 — теплообмінник, 4 — насос, 5, 6 — дифузор;
г — ферментер ежекційний: 1 — корпус, 2 — насос, 3 — ежектор, 4 — ди- фузор-теплообмінник, 5 — повітрезабірник;
д — ферментер струменевий з затопленим струменем: 1 — ежектор, 2 — теплообмінник, 3 — корпус, 4 — насос, 5 — розсікач, 6 — труба с насадкой;
е — ферментер струменевий з падаючим струменем: 1 — теплообмінник, 2 — насос, 3 — корпус, 4 — ежектор.
Рис.5. 9 . Ферментер з ежекційною системою аерації Б-50:
89
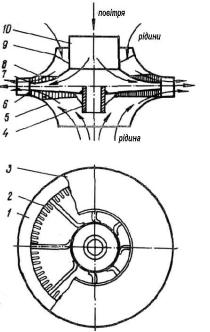
1 — кільцевий канал; 2 — повітревід; 3 — пеногасник; 4 — сепаратор; 5
— циліндр; 6 — привід; 7 — теплообмінник; 8 — дифузор; 9 — циліндричний стакан; 10 — ежекційний пристрій
Рис.5. 10. Ежекційний перемішуючий пристрій (одноступенева турбіна)
1 – щілина; 2,8 — рассікачі; 3, 5 — тарілки; 4 — втулка; 6 — кільцеве сопло; 7 — лопасть; 9 — лопатки; 10— повітровід.
Ферментери з введенням енергії рідкою і газовою фазами
|
Група апаратів з перемішуючими пристроями, в які енергія вводиться од- |
|
|||||||||
ночасно як рідкою фазою за допомогою перемішуючого пристрою, так і газо- |
|
||||||||||
вою фазою при її примусовій подачі в ферментер. Ферментери з комбінованим |
|
||||||||||
введенням |
енергії найбільш |
поширені |
на |
стадії |
біосинтезу |
аеробних |
|||||
біологічних агентів. Переваги цих апаратів в їх мобільності тому, що в них мо- |
|
||||||||||
же |
бути |
створений |
будь |
який |
оптимальний |
для |
біологічного |
аге |
|||
гідродинамічний |
режим |
за |
рахунок зміни швидкості обертання мішалки |
||||||||
швидкості циркуляції рідини, яку перекачує насос або зміни швидкості руху |
|
||||||||||
газової фази. Основним конструктивним елементом ферментерів є механічний |
|
||||||||||
перемішуючий пристрій – мішалка, яка забезпечує високу інтенсивність транс- |
|
||||||||||
порту |
кисню |
та високий |
рівень |
диспергації газової |
фази |
нерозчинни |
субстратів та забезпечує гомогенність взаємодіючих фаз. До цієї групи апаратів відносяться ферментери в рідку фазу, яких енергія вводиться одночасно перемішуючим пристроєм і насосом або тільки насосом. В свою чергу енергія газової фази доставляється звичайним чином – через аеруючі пристрої відомих конструкцій.
Основні конструктивні відмінності в цій групі ферментерів базуються на різній кількості мішалок, які розташовані в одній місткості, різній кількості мішалок на одному валу, різній конструкції газорозподільного пристрою та використанні специфічних циркуляційних контурів.
90
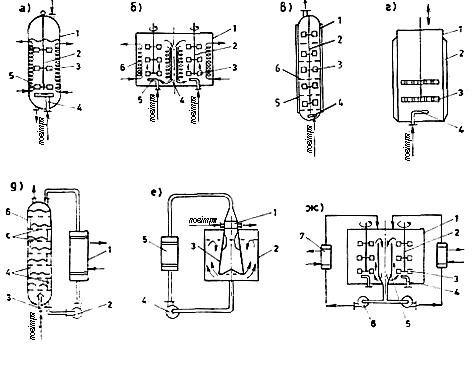
Ферментери цієї групи переважають в асептичних виробництвах завдяки можливості надійної герметизації внутрішнього об’єму апарата. Ферментери використовують як для отримання посівного матеріалу, так і для проведення виробничого біосинтезу.
Рис. 5.11. Ферментери з підводом енергії рідкою та газовою фазами:
а — ферментер з мішалками одновальний: 1 — корпус, 2 — вал, 3 — мішалка, 4 — повітрерозподілювач, 5 — теплообмінник;
б — ферментер з мішалками багатовальний: 1 — корпус, 2 — вал, 3 — мішалка, 4 — дифузор, 5 — повітрерозподілювач , 6 — теплообмінник;
в— ферментер з мішалкою колонний: 1 — корпус, 2 — вал, 3 — мішалка, 4
—повітрерозподілювач, 5 — сорочка, 6 — тарілки;
г — ферментатор с вібромішалками: 1 — корпус, 2 — сорочка, 3 — вібромішалка, 4 — повітрерозподілювач;
д — ферментер з комбінованим вводом енергії колонний: 1 — теплообмінник; 2 — насос, 3 — повітрерозподілювач, 4 — переливні пристрої, 5—тарілки, 6 — колонна;
е — ферментер с з комбінованим вводом енергії: 1 — аератор, 2 — корпус, 3 — дифузор, 4 — насос, 5 — теплообмінник;
ж— ферментер з мішалками багатовальний з циркуляційним контуром: 1
—корпус, 2 — вал, 3 — мішалка, 4 — барботер, 5 — дифузор, 6 — насос, 7 — теплообмінник.
Ферментери з одновальними мішалками і барботажною аерацією
Ця група є найбільш поширеною і відомою, що має промислове застосування. Типове обладнання має місткості, які відповідають ряду преференційних чисел R-10 для апаратів місткістю більше1м3.Ряд R-10 визначається геомет-
91
ричною прогресією з коефіцієнтом 10Ö 10 ( об’єми, м3, 1,0, 1,25 1,6, 2,0, 2,5, 3,2, 4,0, 5,0, 6,3, 8,0, 10, 12,5, 16, 20, 25, 32, 40, 50, 63, 80, 100, 125, 160 і т. д. ). Фер-
ментери які використовуються в якості посівних апаратів вибирають в діапазоні місткості – 0,1-10 м3. Найбільш поширені – 0,63, 2,0, 5,0 10 м3.
Нижче у таблиці5.1. представлені технічні характеристики типових ферментерів для отримання посівного матеріалу.
Таблиця 5.1.
Місткість, м3 |
0,63 |
2,0 |
5,0 |
10 |
|
Діаметр, м |
0,9 |
1,2 |
1,6 |
2,0 |
|
Поверхня |
2,5 |
6,9 |
-- |
- |
|
теплообміну |
|||||
|
|
|
|
||
Потужність |
|
|
|
|
|
електродвигуна, |
1,7 |
7 |
10 |
20 |
|
кВт |
|
|
|
|
|
Число обертів |
25 |
25 |
25 |
25,5 |
|
двигуна, с-1 |
|||||
Число обертів |
|
|
|
|
|
валу мішалки, с- |
4,5 |
4,5 |
3 |
3 |
|
1 |
|
|
|
|
|
|
|
|
|
|
Ферментери місткістю 5м3 маючи типові геометричні розміри можуть відрізнятись конструкцією аераторів або циркуляційних контурів.
Конструктивно ці апарати поєднує , тещо циліндричний корпус має еліптичні дно, в верхній частині розташований люк, оглядові вікна, штуцера підведення поживного середовища, посівного матеріалу, аератора, виходу відпрацьованого повітря та пробовідбірник.
На рис.5.12 показаний ферментер ВМ –10-1К 01 передбачений для отримання посівного матеріалу в виробництві лізина. Конструктивно апарат представляє собою вертикальну місткість, яка обладнана пристроями для аерації, терморегуляції та перемішування. Мішалка представляє собою двохярусну конструкцію: в нижньому ярусі розташована самовсмоктуюча мішалка, яка виконує роль диспергатора повітря, в верхньому ярусі – мішалка (відкрита дискова турбіна).Для терморегуляції використовують виту сорочку, що розташована на корпусі апарата. Ферментер виготовлений з сталі08Х22Н6Т,вал мішалки – з сталі 14Х17Н2, деталі зовнішніх пристроїв – з сталі ВСт3сп5.
92
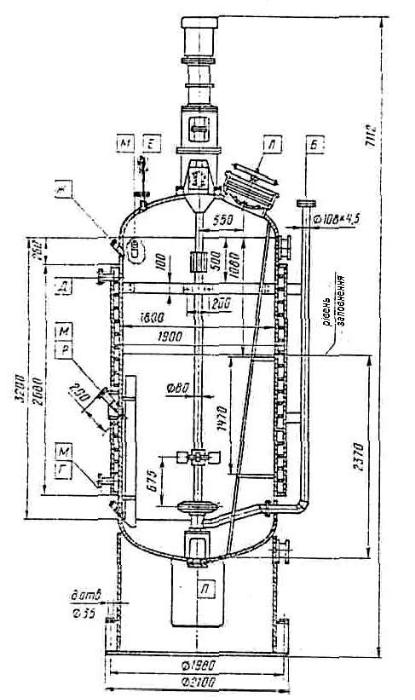
Рис. 5.12.Ферментер ВМ 10-1К-01
.
Технічні характеристики ферментера ВМ 10-1К-01 Таблиця 5.2.
Місткість, м3 : |
|
номінальна |
10 |
робоча |
6 |
Тиск, МПа |
|
робочий |
0,03- 0,05 |
надлишковий: |
0,3 |
при стерилізації |
0,3 |
в сорочці |
|
93
Температура, С: |
|
поживного сере- |
25-31 |
довища |
|
стерилізації |
133-146 |
охолоджуючої во- |
10-12 |
ди |
|
Витрати повітря, |
432 |
м3 /год |
|
Поверхня |
14,8 |
теплообміну, м2 |
|
Потужність елек- |
15 |
тропривода, кВт |
|
Число обертів |
4,23 |
мішалки,с-1 |
|
Габаритні розміри, |
2360*2100*7112 |
мм |
|
Маса, кг |
5702 |
Ферментери для проведення виробничого біосинтезу мають ряд специфічних ознак:
-місткість ферментерів для промислового біосинтезу більша ніж місткість посівних апаратів (більше 10 м3 );
-вони повинні на протязі тривалого часу підтримувати високий рівень асептичності;
-гідродинамічні умови в ферментері повинні забезпечувати рівномірне розподілення взаємодіючих фаз;
-інтенсивність масопередачі повинна відповідати вимогам споживання кисню біологічними агентами;
-теплообмінні пристрої розраховуються на відведення теплоти в режимах максимальної фізіологічної активності.
Таблиця 5.3. Серійні моделі ферментерів Сумського машинобудівного за-
воду
Об’єм, |
Висо- |
Діамет |
Потужність |
Число обертів |
|
електродвигуна, |
|||||
м3 |
та, м |
р, м |
мішалки, с-1 |
||
|
|
|
кВт |
|
|
1,0 |
3030 |
1100 |
2,5; 3; 3,5; |
3,067; 4,083; |
|
(8/6/4Т) |
6,117 |
||||
|
|
|
|||
1,0 |
2845 |
1100 |
2,8 |
4,500 |
|
2,0 |
3870 |
1300 |
4,5 |
3,167 |
|
3,2 |
3960 |
1500 |
10 |
3,167 |
|
5,0 |
4140 |
1700 |
10 |
3,000 |
|
5,0 |
4470 |
1700 |
10 |
3,000 |
94
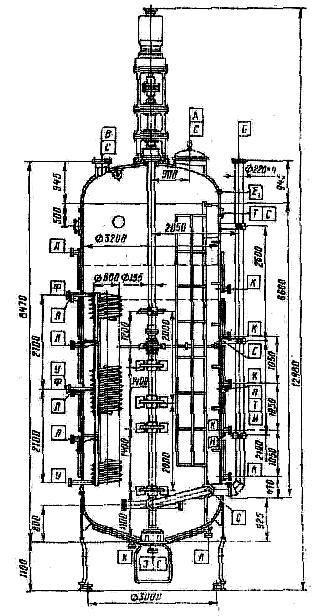
10,0 |
7130 |
2000 |
20 |
3,167 |
50,0 |
11470 |
3000 |
75 |
3,000 |
Для проведення промислового біосинтезу широко використовується ферментери місткістю 50 м3 Сумського заводу.
Дзержинськхіммаш засвоїв випуск серійного ряду апаратів місткістю –5, 15, 20, 30, 50, 63 та 100 м3.Більшість відомих заводів по випуску ферментних препаратів, лимонної кислоти, антибіотиків на ділянці промислового біосинтезу використовують 63м3 апарати.
Кемеровський завод хімічного машинобудування виготовляє ферментер місткістю 63 м3.(рис 5.13).
Рис. 5.13. Ферментер Ф-63-1К-01
95
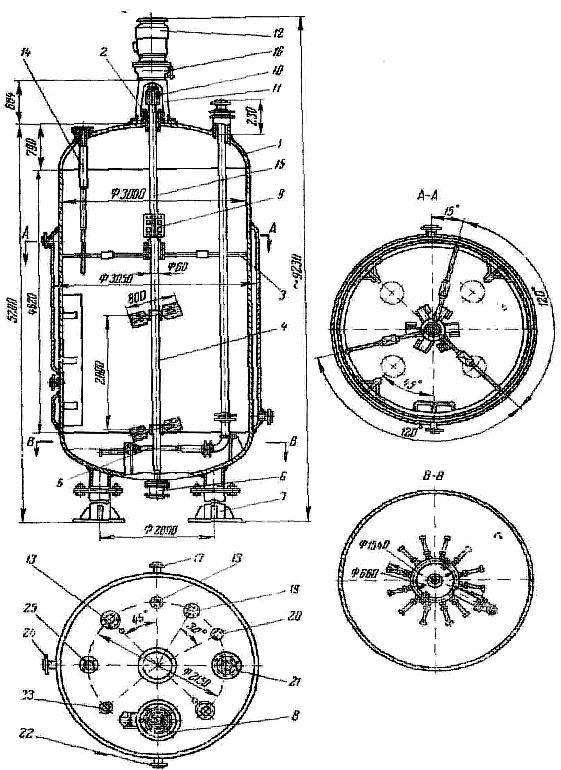
Рис. 5.14..Ферментер з турбінною мішалкою та барботером, розроблений КБ ВНИИФСа (об`єм 40 м3): 1 — корпус; 2 — сальник; 3 — тяги; 4 — вал с мішалками; 5 — барботер; 6—підп`ятник; 7 — стійка; 8 — лаз-павук діаметром 400 мм; 9 и 10 — муфти; 11 — стійка; 12 — електродвигун; 13 — смотрове скло; 14 — гільза для термометра; 15—проміжний вал; 16 — редуктор; 17, 18 и 19 — штуцери для виходу води, для гільзи термометру та для наповнення; 20, 21 и 22
— штуцера для завантаження посівного середовища, для барботера та подачі води; 23, 24 и 25 — штуцера для манометра, відбору проби та виходу повітря.
96
В |
промисловості |
|
використовують |
ферментери |
виробництваVEB |
|
||||
Chemieanlagenbau Erfurt-Rudisleben місткістю 63 та 100 м3 з комбінованим вве- |
|
|||||||||
денням |
енергії. Ферментер |
місткістю 100 |
м3 |
(рис.5.15 |
а) має |
вертикальний |
|
|||
циліндричний корпус, по центру якого розташований вал декількома ярусами |
|
|||||||||
відкритих турбін. Лопаті мішалок розсувні .В нижній частині ферментеру роз- |
|
|||||||||
ташований квадратний барботер. Для відведення тепла корпус ззовні має |
|
|||||||||
секціоновану |
сорочку, |
а |
всередині –пласкі |
вертикальні |
трубчасті |
|
||||
теплообмінники, які одночасно виконують роль відбиваючих перегородок. Ха- |
|
|||||||||
рактерною рисою цього ферментера є те, що він має нижній привід мішалки, |
|
|||||||||
потужність електродвигуна-120/180 кВт, швидкість обертання валу мішалки1 |
|
|||||||||
та 2 с-1. |
|
|
|
|
|
|
|
|
|
|
Ферментери з комбінованим введенням енергії місткістю більше10 м3 |
|
|||||||||
мають ряд загальних конструктивних ознак: |
|
|
|
|
|
|||||
- вони обладнані багатоярусними мішалками; |
|
|
|
|
||||||
- |
введення |
газової |
фази |
здійснюється |
через |
|
барботери |
різн |
конструкцій;
-промислове використання орієнтоване на проведення асептичного біосинтезу;
-використання приводу мотор-редуктор дозволяє змінювати в широко-
му діапазоні рівень зрізових зусиль.
-при необхідності в типовому корпусі можлива установка додаткових пристроїв – дифузори, центральні або периферійні аератори, різні конструкції піногасників ( вмонтовані, виносні ), секційонування за допомогою тарілок різних конструкцій.
-додаткова турбулізація поживного середовища забезпечується за -до помогою відбиваючих перегородок;
-для створення циркуляційних контурів поживного середовища використовують вбудовані в ферментер спіральні теплообмінники або дифузори.
Таблиця 5.4. Технічна характеристика промислових ферментерів з комбінованим введенням енергії
Об’єм, м3 |
40 |
50 |
63 |
|
|
|
(м. Суми) |
|
|
Коефіцієнт за- |
60-65 |
62 |
|
|
повнення, % |
|
|||
|
|
|
||
Висота корпусу, |
6,2 |
7,772 |
6,470 |
|
м |
||||
|
|
|
||
Внутрішній |
|
|
|
|
діаметр апарата, |
3,0 |
3,0 |
3,2 |
|
м |
|
|
|
|
Тип мішалки |
відкрита |
відкрита |
відкрита |
|
(мішалок) |
турбіна |
турбіна |
турбіна |
|
Кількість ярусів |
2 |
3 |
3 |
|
мішалок |
||||
|
|
|
97
Число обертів |
3 |
3 |
3,27 |
|
мішалки, с-1 |
||||
Потужність елек- |
14 |
75 |
90 |
|
тродвигуна, кВт |
||||
|
|
|
||
Поверхня охо- |
|
|
|
|
лодження м 2: |
|
|
|
|
Сорочка |
28,2 |
- |
50 |
|
Теплообмінник |
- |
4 змійовика |
4 спір. ( 40) |
|
(30) |
||||
|
|
|
||
|
|
кільцевий з |
кільцевий з |
|
Тип барботера |
|
12 проме- |
12 проме- |
|
|
|
нями |
нями |
|
Витрати повітря |
|
|
432 |
|
м3/год |
|
|
||
Маса, кг |
|
|
5702 |
Ферментер, ( рис. 5.15 б) що серійно випускається Дзержинськхіммаш місткістю 100 м3 має циліндричний корпус з приварними еліптичними дном і кришкою. По центру апарата проходить вал з багатоярусною мішалкою. Нижня мішалка, яка розташована безпосередньо над барботером представляє собою закриту турбіну з криволінійними лопатями і статором для випрямлення потоку. Над нижньою закритою турбіною розташовані дві закриті турбіні мішалки з прямими лопатями. В самій нижній частині апарата встановлена пропелерна мішалка. Барботер – трубчастий, квадратний. Всередині апарата симетрично розташовані чотири трубчасті змійовики. Поверхня теплообміну складається з секціонованої сорочки і змійовиків. В ферментері використовується верхній привод мішалки з електродвигуном потужністю 120/180 кВт частота обертання валу мішалок 2 та 3 с-1.
Торцьові ущільнення
Забезпечення необхідного рівня асептики в процесі біосинтезу залежить від засобів герметизації ферментера. Найбільш вразливим місцем для герметизації у ферментерів з комбінованим введенням енергії є місце введення валу мішалки в ферментер.
Для забезпечення асептичності біосинтезу в якості герметизуючого пристрою валів, що обертаються, використовують торцеві ущільнення з паровим
захистом. Торцеві ущільнення є невід’ємною частиною ферментерів з комбінованим введенням енергії, які працюють в асептичних умовах.
Торцеві ущільнення випускає Дзержинськхіммаш для герметизації валів апаратів, що працюють при надлишковому тиску до0,25 МПа, температурі середовища –від 30 до 250 С та швидкості обертання валу до 10 с-1.
Виготовляється шість типів торцевих ущільнювачів: ТД-6, ТДП, ТДМ, ТДПЗ, ТТ, ТСК ( ТД – подвійне, ТДП –подвійне з вбудованим підшипником,
98
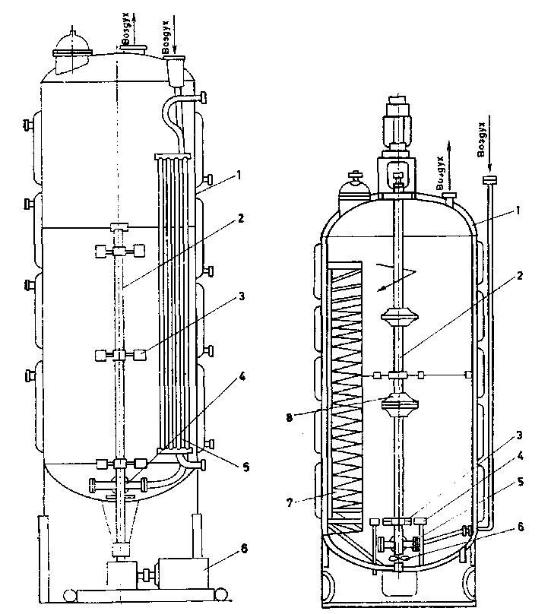
ТДМ – подвійне для малогабаритних апаратів, ТДПЗ – подвійне з підшипником і захистом, ТСК –одинарне з сильфоном з корозійностійкої сталі. торцеві ущільнення, що контактують з поживним середовищем, виготовляються із сталі Х18Н10Т і Х17Н13М2Т, а також з титану ВТ1-0.Тривалість безвідказної роботи
– не менше 2000 годин. Припустиме биття валу в зоні торцевого ущільненняне більше 9,25 мм, кутове биття валу – не більше 0,25 мм.
Рис. 5.15. А. Схема ферментера фірми «Рудислебен» (Німеччина):
1 — корпус, 2 — вал, 3 — мішалка, 4 — барботер, 5 - теплообмінник, 6 — привід мішалки. Б. Схема ферментера (Дзержинськхіммаш): 1 — корпус, 2 — вал, 3 — турбінна мішалка із криволінійними лопатями, 4 — статор, 5 — барботер, 6 — пропелерна мішалка, 7 — змійовиковий теплообмінник, 8 — турбінна мішалка із прямими лопатями.
99
В біотехнологічних виробництвах де існують високі вимоги до рівня асептики використовують торцеві ущільнювачі типа ТТ з термічним затвором (рис. 5.16). Корпус ущільнювача заповнюють високов’язким авіаційним маслом МС-20 або МК 22, яке створює термічний затвор і змащує тертьові пари. Корпус ущільнювача має сорочку, в яку подається пара для стерилізації.
При експлуатації торцевого ущільнювача потрібна циркуляція запорної рідини (масла).Для цього використовують природну циркуляцію масла В цій схемі залучені теплообмінник та фільтр масла.
Технічна характеристика торцевих ущільнювачів, типа ТТ для вертикальних валів, які працюють при надлишковому тиску0,3 МПа і залишковому– 0,02-0,03МПа представлена в табл.5.5.
Табл.5.5. Характеристика торцевих ущільнювачів, типа ТТ для вертикальних валів
|
|
Число |
Тем- |
|
|
Умовне |
Діамет |
пера- |
|
||
обертів |
|
||||
познач |
р валу |
тура |
Маса |
||
валу |
|||||
ущільнен |
мішал |
сере- |
|||
мішалки |
|
||||
ня |
ки, мм |
дови- |
|
||
, с-1 |
|
||||
|
|
|
ща |
|
|
ТТ-40-3 |
40 |
5 |
10-150 |
18 |
|
ТТ-50-3 |
50 |
5 |
10-150 |
18 |
|
ТТ-65-3 |
65 |
5 |
10-150 |
25 |
|
ТТ-80-3 |
85 |
5 |
10-150 |
35 |
|
ТТ-95-3 |
95 |
5 |
|
45 |
|
ТТ-110-3 |
110 |
3,3 |
|
55 |
|
ТТ-120-3 |
120 |
3,3 |
|
65 |
Таким чином, підбір обладнання для забезпечення оптимальних умов протікання стадії біосинтезу є надзвичайно важливим етапом в організації цього процесу. Оскільки єдиною метою кожного технологічного процесу є отримання максимальної кількості біологічно активних речовин або біомаси при повному використанні біологічного потенціалу біологічних агентів, необхідно ретельно аналізувати та підбирати найкращі умови для протікання кожної стадії виробництва.
Конструкція ферментеру для вирощування продуцента БАР повинна
сприяти забезпеченню |
умов |
для |
утворення |
високоактивної культуральної |
рідини. Найважливіші умови – |
хороша |
аерація і |
перемішування середовища, |
|
забезпечення необхідного |
температурного режиму, |
а також асептичність про- |
цесу біосинтезу. На основі порівнянь описаних вище технічних засобів, що забезпечують аерацію культури, перемішування середовища, а також охолодження середовища для підтримання необхідного температурного режиму, для ви-
рощування продуценту БАР оптимальною є конструкція ферментеру з комбінованим введенням енергії.
100
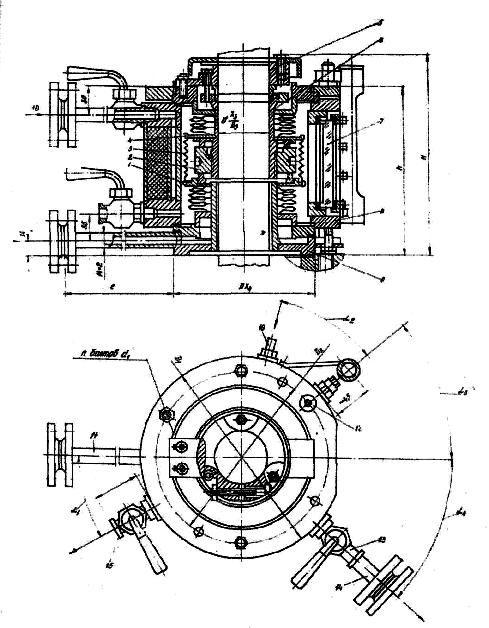
Рис.5.16. Торцеве ущільнення типу ТТ:
1 - нерухоме ущільнююче кільце; 2 - рухоме ущільнююче кільце; 3 - пружина; 4
-нерухоме ущільнююче кільце; 5 - водило; 6 - втулка; 7- покажчик рівня; 8 - корпус; 9 - уловлювач протікань; 10 - вхід пари; 11 - відвід протікань з уловлювачу; 12 - вхід запираючої рідини; 13 – вихід повітря: 14 – вихід конденсату; 15
-вихід запираючої рідини.
Основні фактори впливу, що визначають вибір ферментеру
Основні фактори впливу, що визначають вибір ферментеру базуються на тому, що на сьогоднішній день відсутня узагальнена система вибор ферментаційного обладнання. Для вибору використовують власний досвід або досвід існуючих виробництв. Базовою особливістю біотехнологічних процесів є їх висока індивідуальність стосовно базового етапу біосинтезу– стадії культивування.
101
Для формування підходів до вибору ферментерів необхідно зазначити, що відправною позицією є визначення технологічних ознак етапу біосинтезу. Ці ознаки були визначені нами під час розробки систем класифікації стадії культивування БА.
Перелік фактори впливу.
1.Консистенція ПС. В цьому випадку визначають тип ПС, яке може бути рідким, ущільненим, сипким. При цьому рідкі ПС можуть мати у своєму складі розчинені або нерозчинені субстрати. Багатофазні системи мають специфічні ознаки, що визначає інтенсивність масообмінних процесів.
2.Технологічне рішення стадії біосинтезу– періодичний процес, напівперіодичний або безперервний.
3.Рівень асептичності (асептичні, умовно асептичні, неасептичні). В
цьому випадку приймається до уваги те що процес отримання посівного матеріалу характеризується значно більшою вимогливістю до забезпечення асептичності.
4.Рівень аеробності який враховує потреби у розчиненому кисні та інтенсивність його доставки до БА. Складовою цього процесу є розділення ефектів перемішування та аерації. Прикладом ефекту перемішування є рівень введеної енергії, а ефект аерації оцінюється по інтенсивності масопередачі.
5.Рівень припустимого турбогіпобіозу. Причиною “гіпобіозу” є турбулізація середовища тому пропонується термін турбогіпобіоз(Биотехнол бактер синтеза с. 230). Таким чином для кожної системи культивування існує такий рівень турбогіпобіозу при якому спостерігається зниження інтенсивності
ростових процесів та інтенсивності утворення метаболітів і цей процес супроводжується ушкодженням клітин та іншими гіпоефектами, які визвані турбулентністю середовища, а саме зрізовими зусиллями які виникають в результаті взаємодії культурального середовища з конструктивними елементами ферментеру та в результаті взаємодії (контакту) фаз.
6.Продуктивність процесу по цільовому продукту і в цьому випадку враховується вид цільового продукту– біомаса, метаболіт або їх композиція. Продуктивність процесу дозволяє визначити потрібний об’єм, тривалість циклу
роботи. Умовно пропонується використовувати лабораторні місткістю 0,5—100 л, пілотні місткістю 100л—10 м3, промислові (для ведення робіт основного технологічного процесу) місткістю 10 — 100 м3 и більше.
1. |
Інтенсивність |
термодинамічних |
процесів. Інтенсивність |
тепловиділення обумовлює конструкцію систем тепловідведення. |
|||
Остаточний вибір |
типу ферментеру здійснюється |
після проведення -мо |
дельних досліджень на пілотних лабораторних установках. Обов’язковим елементов попередніх досліджень є визначення критеріїв масштабування в ними, як правило вибирають:
· |
інтенсивність |
масопередачі |
кисню(об’ємний |
коефіцієнт |
масопередачі); |
|
|
|
|
· |
швидкість потоків (масштабування |
за гідродинамічними |
показни- |
|
ками); |
|
|
|
|
102
· питомі витрати енергії для досягнення ідентичних показників по виходу цільового продукту, досягнення необхідного об’ємний коефіцієнт масопередачі та інш.
8. Характер потоків. В залежності від структури потоків виділяють ферментери з режимом ідеального змішування(наприклад лабораторні апарати з швидкістю обертання мішалки не менше300 об/хв. і часом вирівнювання концентрації – час гомогенізації 2 – 8 хв). Режим ідеального витиснення (тубулярний - поршневий).
5.2. Проектування відділення виділення цільового продукту
В результаті біосинтезу отримують культуральну рідину або твердофазну культуру, що включає клитини мікроорганізмів, залишки поживних речовин, різні позаклітинні продукти метаболізму та. Вмістін біомаси або іншого цільового продукту в культуральній рідині зазвичай не перевищує3—4% сухої
речовини. Концентрування і отримання товарної форми продукту культуральної рідини або твердофазної культури здійснюють при подальшій переробці.
Продукти мікробного синтезу випускають в трьох основних товарних формах:
-концентрати – зневоднена культуральна рідина, що містить біомасу (кормові концентрати амінокислот, вітамінів, антибіотиків, неочищені ферментні препарати);
-зневоднена мікробна біомаса (хлібопекарські кормові дріжджі, бактерійні добрива і ін.);
-технічні або очищені препарати ферментів, антибіотиків, амінокислот і т.д. Залежно від товарної форми, яку необхідно отримати, а також від властиво-
стей цільового продукту і культуральної рідини(або твердофазної культури), що переробляється, використовують ті або інші способи концентрації і виділення продуктів мікробіологічного синтезу. Простий спосіб переробки культуральної рідини — обезводнення шляхом випаровування або висушування без виділення цільового продукту в чистому вигляді. Отримуваний концентрат, крім основного продукту, містить біомасу культури– продуцента БАР, залишки поживних речовин і піногасник, інші метаболіти. Такі концентрати за-
стосовують в основному для приготування рідких |
або |
сухих кормових |
препаратів амінокислот, вітамінів і . інАналогічним |
чином |
отримують |
неочищені ферментні препарати з твердофазних культур. |
|
|
Для зневоднення мікробної біомаси і отримання технічних або очищених продуктів біосинтезу використовують різні способи: флотацію, сепарацію, фільтрацію, екстракцію іонний обмін, адсорбцію, кристалізацію, мембранні способи і ін. Як правило, технологія виділення і очищення товарного продукту включає декілька стадій виділення і очищення.
103
5.3.Отримання концентратів
Утих випадках, коли допускається застосування продукту біосинтезу в неочищеному вигляді (шкіряна, спиртова промисловість, сільське господарство), доцільно випускати цей продукт у вигляді концентрату. Це найбільш простій і
дешевий спосіб отримання товарної .формиТехнологію приготування мікробних концентратів розглянемо на прикладі кормових концентратів лізину (ККЛ), що випускаються в рідкій і сухій формах. Вміст лізину в цих концентратах складає відповідно 7—10 і 15—20% на суху речовину.
Рідкі ККЛ отримують шляхом випаровування культуральної рідини у ваку- ум-випарних установках до вмісту сухої речовини45—50%. Для придушення сторонньої мікрофлори і зниження втрат лізину при термообробці початкову рідину заздалегідь підкисляють до рН5,5—6,0 і стабілізують шляхом додавання 0,17% бісульфату натрію. Залежно від типу вживаних випарних установок і режиму проведення процесу випаровування втрати лізину складають від1 до 20%. Якнайкращі результати досягаються при використанні вакуум-випарних установок з падаючою плівкою (наприклад, «Вігант» виробництва Германії).
Сухий ККЛ отримують, висушуючи рідкий концентрат в розпилюючих сушарках. Отриманий препарат володіє високою гігроскопічністю, що приводить до налипання продукту на стінках апаратів і трубопроводів і вимагає його
герметичної упаковки. Для зниження гігроскопічності сухого ККЛ упарену рідину перед сушкою змішують з наповнювачами, наприклад з пшеничними висівками. Отримуваний продукт зручніший для використання, оскільки менш гігроскопічний, хоча містить менше лізину.
У кормових концентратах лізину, крім самого лізину (близько 15% на суху речовину), є інші амінокислоти(до 15%), вітаміни групи В(від 10 до 340 мкг/г), бетаїн (до 13%), зольні і інші елементи.
Твердофазні культури мікроорганізмів, широко вживані для отримання готових препаратів, або висушують до вологості 10—12% і відправляють у такому вигляді споживачам, культуральної рідині без попереднього відділення біомаси, з водної фази(нативного розчину) після відділення біомаси або з біомаси після розділення фаз або піддають екстракції з подальшим отриманням технічних або очищених препаратів ферментів. Розглянемо коротко технологію отримання сухих твердофазних культур.
Отримана на стадії біосинтезу твердофазная культура має вологість 35—60% і є злиплою біомасою. Перед висушуванням необхідно подрібнити вологу
культуру за допомогою дезінтеграторів або дробарок різних типів до гранул розміром 2—3 мм.
Подрібнену культуру негайно висушують в установках стрічкового, тунельного, барабанного або іншого типу. Особливість процесу сушки твердофазних культур полягає в тому, що цільові продукти їх метаболізму термолабільні речовини, тому сушку треба здійснювати в м’яких режимах, індивідуальних для конкретної культури. Як правило, тривалість сушки культури не повинна перевищувати 5 - 8 хв, а температура продукту на виході -40—42°С.
104
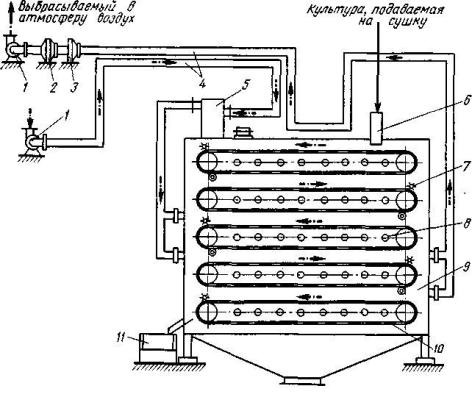
Рис. 5.17. Схема конвейерної сушарки: 1 — вентилятори; 2,3 — фільтри; 4
—воздуховоди; 5 — кондиціонер; б — штуцер для подачи вологої культури; 7
—рихлители; 8 — калорифери; 9 — сушильна камера; 10 — лента конвейера; 11 — конвейер для вивантаження висушеної культури.
Конвейєрна сушарка, вживана у виробництві ферментних препаратів, у виробництві кормових антибіотиків, зображена на рис.5.17. Це герметизирована камера, усередині якої розташований багатоярусний стрічковий конвейєр. Волога культура поступає на верхній ярус конвейєра, проходить послідовно по всіх ярусах, висушується і розвантажується на конвейєр для видалення сухої культури з сушильної установки. Сушильний агент (повітря) подається вентилятором через кондиціонер. Для нагрівання повітря в камері встановлені калорифери. Гідність конвейєрних сушарок—висока продуктивність (3,5—4,0 т/добу) при порівняно невеликих габаритних розмірах. Недолік таких установок полягає в нерівномірному висушуванні частинок культури різного розміру. Найбільш крупні частинки висихають до необхідної вологості(12—15%), а дрібні пересихають, що приводить до інактивації ферментів. Втрати активності ферменту в такій сушарці 10—16%.
Висушену культуру упаковують в крафт-мішки, маркірують і відправляють споживачам.
5.4. Отримання очищених препаратів
При виробництві ферментів, амінокислот, антибіотиків і інших продуктів мікробного синтезу стоїть завдання виділити цільовий продукт з культуральної рідини і отримати його в чистому вигляді. Це складне технічне завдання, для її
105
вирішення потрібне багатостадійне селективне розділення .сумішейВ технології отримання очищених продуктів мікробного синтезу характерне зменшення масштабності стадій від початкових до кінцевих (зменшення об’єму рідини що переробляється). Це обумовлено малою концентрацією цільових продуктів в культуральнії рідині і їх концентрацією в процесі виділення і очищення. Наприклад, у виробництві антибіотиків вміст цільового продукту в культуральнії рідині складає всього0,05—3,0%, а в перерахунку на сухий залишок (тобто ступінь чистоти продукту) —от 1 до 15%. Окремі етапи виробництва розрізняються і тривалістю— від декількох годинників до декількох діб.
У схемі виробництва очищених продуктів мікробного синтезу можна виділити чотири основних, практично загальних для всіх випадків етапу технології. Перший —мікробіологічний синтез; другий — розділення фаз культуральної рідини; третій — виділення концентрату або напівпродукту з відповідної фази (нативного розчину, біомаси, культуральної рідини); останній
— отримання з концентрату або напівпродукту чистої речовини. Продукти мікробного синтезу виділяють безпосередньо з культуральної рідини без попе-
реднього |
відділення |
біомаси, з водної фази(нативного |
розчину) |
після |
|
|||
відділення біомаси або з біомаси після розділення фаз. |
|
|
|
|
||||
Перший спосіб використовують в тих випадках, коли розділення фаз з яких- |
|
|||||||
небудь |
причин |
представляє |
великі |
труднощі; |
промисловості |
він |
||
застосовується достатньо рідко. Технологічно вигідніше виділяти продукт з на- |
|
|||||||
тивного |
розчину. Це |
можливо, якщо |
цільовий продукт |
після |
закінчення |
біосинтезу знаходиться у водній фазі або може бути переведений в неї зміною
значення |
рН. У |
тих випадках, коли цільовий |
продукт |
практично |
не |
розчиняється у воді, його виділяють з твердої фази— біомаси. |
|
|
|||
5.4.1. Розділення фаз культуральної рідини |
|
|
|
||
Ця процедура вимагає великих витрат, оскільки пов’язана з переробкою ве- |
|
||||
ликих об’ємів суспензій. Для інтенсифікації цієї стадії і |
зниження |
втрат |
|||
цільового |
продукту |
рідина перед розділенням , фазяк правило, піддають |
|
спеціальній обробці. В результаті змінюється структура осаду, що забезпечує максимальний ступінь переходу продукту в ту фазу, з якої його далі виділяють, а також видалення домішок, що утрудняють добування цільового продукту. За-
лежно від вимог до повноти відділення дисперсної фази і особливостей культуральної рідини для розділення використовують процеси фільтрації, відцентрової сепарації або фракціонування на віброситі.
При виділенні продуктів мікробного синтезу з нативного розчину або біомаси в промислових умовах вибір методів обмежений і визначається фізикохімічними властивостями цих продуктів. Так, для виділення антибіотиків використовують екстрагування, іонообмінну сорбцію, осадження продукту з нативного розчину, сорбцію з нативного розчину макропористими неіоногенними сорбентами і екстракцію з біомаси органічним розчинником.
106
Одне з провідних місць в технології виділення біологічно і активних речовин з нативних розчинів займають процеси екстрагування. Розчинник, рН середовища, співвідношення фаз і інші умови підбирають так, щоб концентрувати цільовий продукт не менше чим 2в—5 разів, а також забезпечити високу вибірковість процесу. Так, якщо продукт, що виділяється, є кислотою, то в кислій водній фазі залишаються практично всі речовини, добре розчинні у воді, органічні основи, а також кислоти, сильніші, ніж екстрагована. Якщо вміст цільового продукту в нативном розчині зазвичай досягає15—20%, то в екстракті воно підвищується до80—85%, тобто вдається відокремити більше 80% домішок. Слід зазначити, що домішки, ті, що перейшли в екстракт, як правило, близькі по хімічній структурі до цільового продукту, і їх відділення може бути утруднене.
Іонообмінну сорбцію доцільно застосовувати для виділення продуктів біосинтезу лише при чималій обмінній місткості сорбенту по цільовому продукту (близько 10 мг-екв на 1 г сорбенту). Іонообмінну сорбцію використовують для виділення речовин, що є достатньо сильними електролітами і ті що дисоціюють у водному середовищі з утворенням багатозарядних іонів. Підбір
сорбентів, умов сорбції і елюції забезпечує високу селективність процесу і дозволяє концентрувати цільовий продукт 10в разів і більш. Іонообмінну сорбцію застосовують також для подальшого очищення біологічно активних речовин, проводячи за допомогою спеціальних сорбентів демінералізацію, нейтралізацію і обезбарвлення розчинів. Переваги методу іонообмінної сорбції
—простота апаратурного оформлення і відсутність потреби в органічних розчинниках, недоліки — значна тривалість процесу і необхідність регенерації сорбентів.
Для |
селективного виділення з нативних розчинів |
деяких продукті |
|||
метаболізму з середньою молекулярною масою, добре розчинних у воді і таких, |
|||||
що |
мають |
гідрофільна |
і |
гідрофобну , частинизнайшли |
застосування |
макропористі сорбенти неіоногенного типу. Концентрація продукту при цьому |
|||||
значно |
менше, |
ніж при |
іонообмінній сорбції, що пов’язане |
з меншою |
сорбційною місткістю по витягуваній речовині. Разом з тим сорбція макропористими сорбентами дозволяє виділяти з нативного розчину продукти, які не можуть бути витягнуті іншими відомими методами(наприклад, цефалоспорин С).
Метод осадження або кристалізації з нативних розчинів застосовується для виділення речовин, здатних утворювати з деякими реагентами нерозчинні з’єднання або кристалізуватися за певних умов з водного середовища. Основним чинником, що обмежує застосування процесу осадження біологічно -ак тивних речовин з нативного розчину, є низька концентрація цих речовин в розчинах (зазвичай не більше1—2%). При цьому залишкова концентрація цільового продукту в матковому розчині не повинна перевищувати0,1 — 0,2% (інакше помітно зростають втрати продукту). Метод осадження знайшов про-
мислове застосування у виробництві ферментів і тетрациклін антибіотиків. В деяких випадках він дозволяє відокремити з’єднання, близькі до цільових продуктів по хімічній структурі.
107
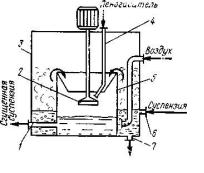
Екстрагування цільового продукту органічним розчинником з біомаси використовують в тих випадках, коли він не розчиняється у водному середовищі і міститься головним чином в твердій фазі. Продукт екстрагують з вологої або висушеної біомаси, підбираючи розчинник, що забезпечує отримання достатньо концентрованого екстракту. Потім розчинник випаровують і виділяють цільовий продукт з екстракту.
5.4.2. Виділення цільової речовини і отримання готового продукту
На |
наступному |
етапі |
технологічного |
циклу |
цільовий |
про |
відокремлюють від основної маси домішок і концентрують. При цьому вико- |
|
|||||
ристовують в основному ті ж процеси, як і при виділенні продукту з нативного |
|
|||||
розчину в різних поєднаннях. У необхідних випадках проводять додаткове |
|
|||||
очищення розчинів спеціальними сорбентами. |
|
|
|
|||
На останній стадії |
виробництва |
цільовий продукт виділяють у вигляді |
||||
твердої фази за допомогою кристалізації (осадження) з подальшою сушкою або |
|
|||||
випаровуванням розчинника з відповідного розчину. Отриманий твердий про- |
|
|||||
дукт після подрібнення і фасування направляють споживачам або використо- |
|
|||||
вують для приготування лікарських форм препаратів. |
|
|
|
|||
Кількість і зміст технологічних етапів, що проводяться на двох останніх |
|
|||||
стадіях |
виробництва, визначаються, з |
одного боку, |
складом культуральної |
|
рідини, що переробляється, з іншого боку — вимогами, що пред’являються до чистоти готового продукту. Найбільші труднощі виникають в тих випадках, коли мікроорганізми продукують разом з цільовим продуктом комплекс близьких до нього по хімічній природі речовин.
Докладніший опис конкретних процесів, використовуваних для виділення і очищення продуктів мікробного синтезу, приведений нижче.
4.3.2.1.Флотація
Цей спосіб концентрації суспензій застосовують у виробництві кормових дріжджів. Він полягає в тому, що отриману на стадії біосинтезу культуральну рідину вспенивают, і при цьому велика частина дріжджів концентрується в пінній фракції. Відокремлюючи піну від основної маси рідини, отримують напівпродукт із змістом біомаси 2—в 4 рази вище, ніж в початковій культуральній рідині.
108
Рис. 5.18. Схема флотатора: 1 — штуцер для виходу суспензії, що згущує; 2
— механічний піногасник; 3— корпус; 4 — труба подачі води ; 5 — внутрішній стакан; 6 — штуцер для введення дріжджової суспензії; 7 — штуцер для виведення освітленої рідини.
Процес |
здійснюють |
в спеціальних апаратах— флотаторах. Вони |
є |
циліндровою |
місткістю, в |
якій встановлений стакан меншого |
діаметру. |
Кільцевий простір між стінками корпусу і стакана розділений вертикальними перегородками на декілька секцій; перегородка між першою і останньою секціями суцільна (доходить до дна), а інші до дна не доходять. У нижній частині секцій, встановлені барботери, а у верхній частині центрального стакана – механічний дисковий піногасник. Дріжджова суспензія подається в пер-
шу, найбільшу секцію флотатора і послідовно проходить через всі ,секції
перетікаючи |
під вертикальними перегородками. Через барботери |
подається |
||
повітря, і відбуваються інтенсивне піноутворення |
і |
флотація |
дріжджів. |
|
Піна, що |
утворюється, переливається через |
верхній |
край |
внутрішнього |
циліндра і потрапляє в зону дії пристрою для механічного пеногашения(у необхідних випадках на його диск додатково подають воду або хімічний пеногаситель. Зібрана у внутрішньому стакані суспензія дріжджів, що згущує,
відводиться |
через штуцер і |
поступаєна |
сепараторів |
для подальшої |
концентрації. |
Звільнену від |
дріжджів рідину після попереднього очищення |
скидають в каналізацію. Втрати дріжджів на стадії флотації складають зазвичай
5-7%.
4.3.2.2.Фільтрація
Увиробництвах, де цільовим продуктом є один з метаболітів, розчинений в культуральній рідині, для відділення кліток біомаси від розчину найчастіше ви-
користовують |
фільтрацію. |
Вона |
полягає |
в |
розділенні суспензії |
при її |
|||
пропусканні через пористу перегородку. Основна характеристика процесу— |
|||||||||
швидкість |
фільтрації (кількість |
фільтрату, |
що |
отримується |
з |
одиниці |
|||
фільтруючої |
поверхні |
в |
одиницю ). часуШвидкість |
фільтрації |
прямо |
пропорційна різниці тиску з обох боків фільтрувальної перегородки і обернено пропорційна гідравлічному опору перегородки з шаром осаду, що накопичився на ній:
dV/Fdτ = p/ η(Rоc-Rф.п.) (5.1.)
де V —объем фільтрату, м3; F — площа поверхні фільтрації, м2; τ — тривалість фільтрації, з; p — різниця тиску, Па; η — кінематична в’язкість фільтрату, Па с; Rоc — опір осаду, м-1; Rф.п — опір фільтрувальної перегородки, м-1.
Опір осаду залежить від його фізико-механічних властивостей і товщини, і його можна визначити по формулі
Rоc = rосmocV/F (5.2.)
де Rоc — питомий опір шару осаду масою1 кг на площі 1м2, м/кг; moc — маса осаду, що виділяється з 1 м3 суспензії, кг/м3.
109
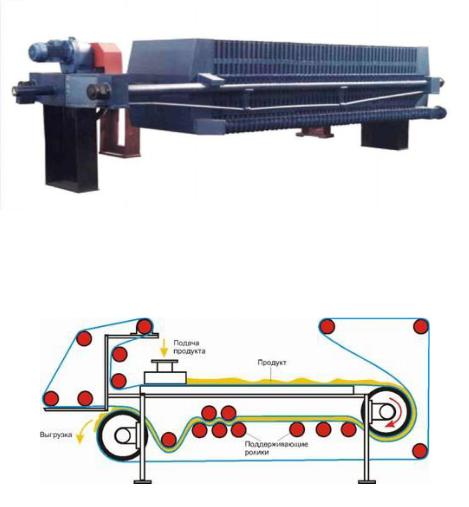
Підставивши вираз (5.2) |
в (5.1.), отримаємо диференціальне рівняння, |
що |
|||||||
описує |
процес |
фільтрації |
для |
нестискуваного |
осаду |
на |
нестискувані |
||
перегородці: |
|
|
|
|
|
|
|
|
|
dV/Fdτ = p/ η(rосmocV/F + Rср.п) |
(5.3.) |
|
|
|
|
||||
Як видно з рівняння(5.3), в процесі фільтрації з накопиченням осаду |
|||||||||
гідравлічний опір лінійно зростає, що призводить до безперервного зниження |
|||||||||
швидкості фільтрації. |
|
|
|
|
|
|
|
||
Крім того, осад, що утворюється, зазвичай здатний стискатися, тому при |
|||||||||
підвищенні тиску шар ущільнюється, |
замість очікуваного |
збільшення |
|||||||
швидкості фільтрації спостерігається її зниження. |
|
|
|
||||||
Процес |
фільтрації, |
при |
якому |
відбувається |
накопичення , осаду |
здійснюють у фільтрах застарілої конструкції— фильтр-прессах. Вони характеризуються низькою швидкістю фільтрації, але головне — низьким ступенем механізації (вивантаження осаду проводять уручну); неможливо забезпечити дотримання санітарно-гігієнічних вимог.
Останнім часом з’явились фільтри, у яких операції фільтрації, промивання осаду та його зняття з фільтруючої перегородки автоматизовані. Це фільтрпреси рамні, стрічкового та баштового типу.
Рис. 5.19. Рамний фільтр-прес
Рис. 5.20. Фільтр-прес стрічкового типу.
110
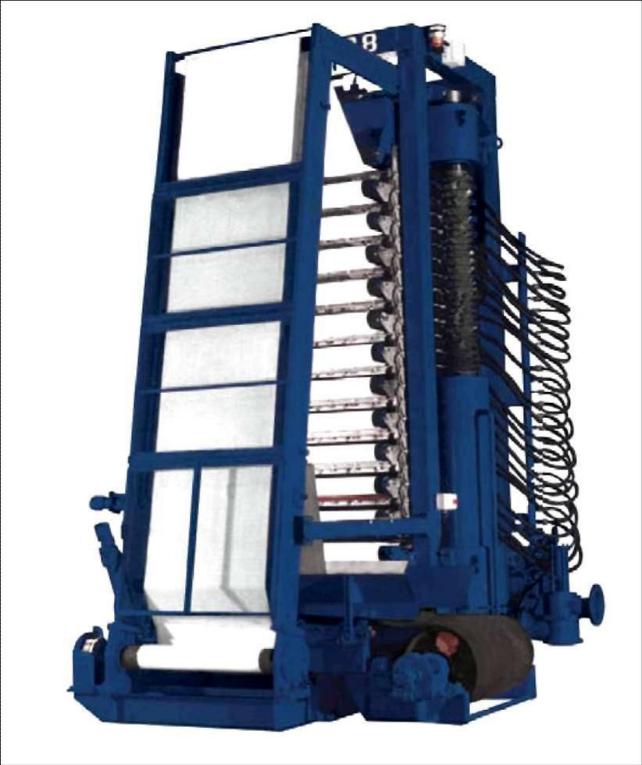
Рис. 5.21. Фільтр-прес автоматичний камерний баштового типу ФПАКМ.
111
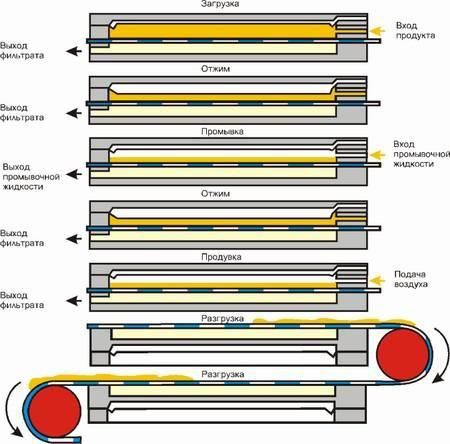
Рис.5.22. Схема роботи ФПАКМ
З метою підвищення продуктивності устаткування фільтрації і зниження
витрат ручної праці все ширше |
застосовують фільтри з |
|
механізованим |
||
зніманням осаду, зокрема барабанні вакуум-фільтри. Вони представляють ба- |
|||||
рабан, занурений нижньою частиною в ємність, куди безперервно поступає |
|||||
культуральна |
рідина. Поверхня |
барабана |
перфорована |
і |
обтягнута |
фільтруючою тканиною, а сам барабан роздільний перегородками на секції. При його обертанні секції послідовно підключаються до збірок фільтрату, промивних вод і до колектора стислого повітря.
Під дією розрідження у внутрішній частині барабана відбувається фільтрація культуральної рідини. Фільтрат, що утворюється, відводиться в збірку, а осад залишається на зовнішній поверхні фільтрувальної тканини. Після проходження зон тієї, що підсушила, промивання і вторинної підсушила осідань віддаляється за допомогою ножа, закріпленого на певній відстані від поверхні
барабана. Таким чином, товщина шару осаду в зоні фільтрації практично незмінна, що дозволяє вести процес фільтрації в безперервному режимі при постійній швидкості.
Проте при фільтрації деяких культуральних рідин, зокрема культуральній рідині актиноміцетів, питомий опір драглистого осаду, що утворюється, дуже великий. Навіть тонкий шар осаду, який залишається після того, що зрізає ножем, призводить до різкого зниження швидкості фільтрації. Для інтенсифікації процесу рідину заздалегідь обробляють(кислотна або теплова коагуляція обробка електролітами) або використовують барабанні вакуум-фільтри з намив-
112
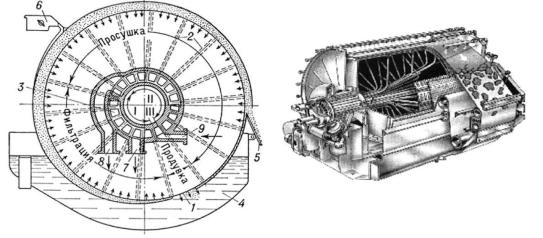
ним шаром допоміжного матеріалу фільтрації. Останній є тонкодисперсний порошком (найчастіше перліт або діатоміт), який намивають на фільтрувальну тканину перед початком фільтрації культуральної рідини. Він оберігає пори фільтрувальної тканини від закупорювання, збільшуючи тим самим швидкість фільтрації. Крім того, в барабанних вакуум-фільтрах, призначених для роботи з намивним шаром, передбачено повільне переміщення ножа для того, що зрізає осаду до поверхні барабана в процесі фільтрації(0,1—0,2 мм за оборот). Це забезпечує постійне оновлення поверхні фільтрації, іотже, високу швидкість фільтрації. Наприклад, при фільтрації культуральної рідини тетрацикліну на барабанному вакуум-фільтрі з намивним шаром перліту досягається середня швидкість фільтрації 150—180 л/(м2-ч), а для фільтр-пресу цей показник не перевищує 25—30 л/ (м2-ч).
Рис. 5.23. Барабанний вакуум-фільтр
5.4.2.3.Центрифугування
Центрифугування - процес розділення рідких неоднорідних систем у полі дії відцентрових сил. У мікробіологічній промисловості центрифуги широко використовують для розділення суспензій на рідину й тверді, фазищо містять мікроорганізми, ферменти, амінокислоти й інші продукти біосинтезу кристалічної або аморфної структур.
Залежно від властивостей дисперсних систем центрифугування здійснюють методами відцентрового фільтрування й осідання.
Відповідно до методів розділення центрифуги підрозділяють на:
- відстійні (О), фільтруючі (Ф), комбіновані (К) центрифуги та сепаратори
(С).
Швидкість розділення сумішей в центрифугах значно вища, ніж у фільтрах і відстійниках, завдяки більшій рушійній силі, що виникає при обертанні ротора центрифуги разом з суспензією, що знаходиться в нім, або емульсією. Ефективність роботи центрифуги кількісно оцінюєтьсяфактором розділення. Він показує, в скільки разів відцентрове прискорення, що розвивається в центрифузі, більше прискорення вільного падіння:
113
Фр=ω2 R/g |
(5.4.) |
де Фр —фактор розділення (або критерій Фруда —Fr); ω — кутова швидкість обертання ротора, с-1; R — радіус обертання частинки (відстань від частинки до осі ротора), м; g — прискорення вільного падіння, м/с2.
Залежно від значення Фр центрифуги підрозділяють на звичайні (Фр<3500) і надцентрифуги (Фр>3500), а залежно від організації процесу— періодичної і безперервної дії.
Розглянемо принцип дії осаджувальної центрифуги на прикладі машини з ротором тручастого типу. Суспензія поступає у внутрішню порожнину ротора через донний штуцер. При обертанні ротора відбувається осадження твердих частинок, що містяться в суспензії, на його внутрішніх стінках, а освітлена рідина викидається через верхню частину ротора і збирається. Швидкість осадження частинок суспензії залежить від співвідношення між відцентровою -си лою, що діє на тверду частинку, і силою опори середовища. Відцентрова сила
Fц направлена радіально від осі ротора до периферії і для частинок сферичної
форми рівна
Fц=4/3 π (ρч - ρж)r3 ω2R (5.5.)
де ρч та ρж — щільність твердої частинки і рідини, кг/м3; r —радиус частинки, м; з — кутова швидкість обертання рідини, с-1; R — радіус обертання частинки, м.
Сила опору середовища Fс згідно закону Стокса, рівна:
Fс = 6 π μ r v |
(5.6.) |
де μ —динамічна в’язкість рідини, Па-с; v — швидкість руху частинки, м/с. |
|
Швидкість осадження |
частинок твердої фази в центрифузі визначається з |
умови рівності відцентрової сили і сили опору середовища
4/3 π (ρч - ρж)r3 ω2R=6 π μ r v |
(5.7.) |
Звідки |
|
V = 2 (ρч - ρж)r2 ω2R/=9 μ |
(5.8.) |
Фільтруючі центрифуги застосовуються для грубодисперсних суспензій, для виділення кристалічних і аморфних продуктів, промивання осадів, що виходять, а також для відділення вологи. Відстійні центрифуги застосовують для розділу погано фільтруючих суспензій, емульсій, для розділу суспензій з великим розміром часток твердої фази.
Центрифуги класифікують за наступними ознаками:
·за фактором розділення - нормальні центрифуги з фактором розділення Fr < 3000; швидкісні або надцентрифуги (Fr > 3000). Він показує, в
скільки разів відцентрове прискорення, що розвивається в центрифузі, більше прискорення вільного падіння:
Fr = ω2 R/g (5.9.)
де Fr — фактор розділення (або критерій Фруда); ω — кутова швидкість обертання ротора, с-1; R — радіус обертання частинки (відстань від частинки до осі ротора), м; g — прискорення вільного падіння, м/с2.
- За способом вивантаження осаду:
114
-ручна через борт (Б), ручна через днище (Д), саморозвантажна — гравітаційна (С), ножова (Н), шнекова (Ш) і вібраційна (В). Цифри, що йдуть за літерним позначенням, характеризують діаметр барабана й конструктивну модифікацію центрифуги.
· За конструктивними ознаками:
горизонтальні (Г), вертикальні (В), підвісні з верхнім приводом (П) і маятникові (М).
·По організації процесу - періодичні та безперервнодіючі.
Головними факторами для вибору типу центрифуги є:
·для суспензій - ступінь дисперсності твердої фази, в'язкість рідкої фази, різниця густин твердої й рідкої фаз, а також концентрація твердої фази в суспензії;
·для емульсій - стійкість емульсії, що обумовлюється роздробленістю крапель однієї рідини в іншій, в'язкістю дисперсного середовища й співвідношенням густини фаз.
При виборі центрифуг головними факторами є також їхні технічні характеристики й фізичні властивості оброблюваного матеріалу, дисперсна сполука твердої фази, в'язкість рідкої фази, концентрація суспензії, а також фактор розділення.
Ефективність роботи центрифуг характеризуєтьсяіндексом продуктивно-
сті
Σ = F·Fr, (5.10)
де F — поверхня розділення,м2 , Fr – фактор розділення.
Високі значення індексу продуктивності Σ мають центрифуги з ножовим зніманням осаду, які відрізняються також універсальністю, тому можуть застосовуватися для розділення суспензій і концентрації твердої фази.
Тип промислової центрифуги, якщо її аналог, що працює в промисловості на тім же продукті, невідомий, вибирають на основі аналізу технологічних вимог, які пред'являються до процесу розділення властивостей суспензії та осаду, потужності виробництва.
В результаті аналізу по переліченим факторам, визначають групу типів і розмірів центрифуг для обробки вибраного продукту (табл.5.6.). Найбільш доскона-
лими по конструкції вважаються центрифуги зі шнековим вивантаженням оса-
ду, потім - з поршньовим, потім - саморозвантажні, з ножовим та з ручним вивантаженням осаду.
Центрифуги безперервної дії, відстійні, горизонтальні зі шнековим вивантаженням осаду типу (НОГШ) призначені для розділення суспензій з об'ємною концентрацією твердої фази від 5 до 50% і розмірами часток від 5 до 500 мкм, а також для гідравлічної класифікації шламів по розміру твердих часток.
115
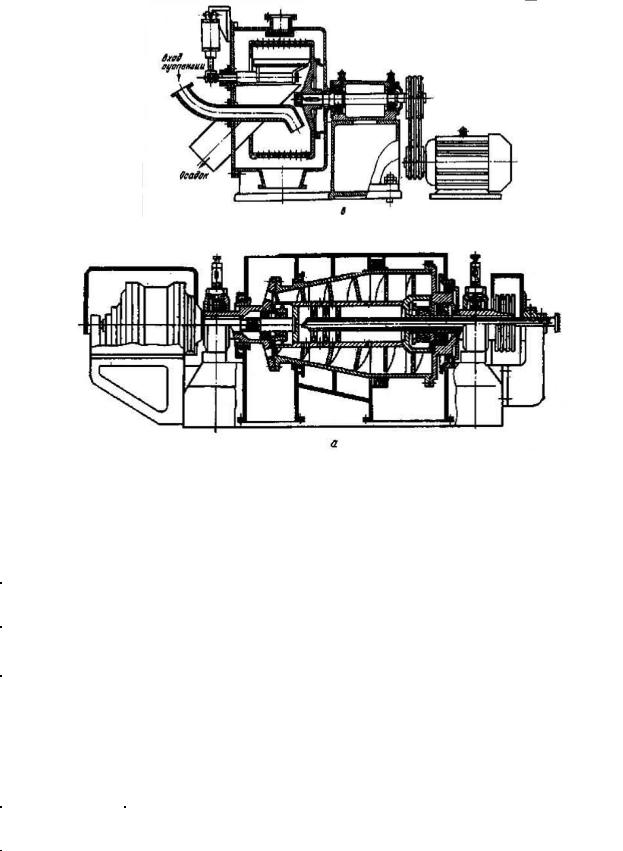
Рис. 5.24.Центрифуга автоматична горизонтальна фільтруюча типа АГ
Рис. 5.25. Центрифуга НОГШ: безперервної дії, відстійна, горизонтальна зі шнековим вивантаженням осаду
Вибір типорозміру центрифуги по продуктивності
|
|
Таблиця 5. 6. |
|
Продуктивність |
Індекс центрифуги, що рекомендується до за- |
|
|
|
|
|
|
по суспензії, |
по осаду, |
стосування |
|
м3 / год |
т/год |
|
|
1-5 |
0,15-0,5 |
ОМД-80, ОГШ-35, ФГН-63, ФГН-90, |
|
|
|
ФМД-80 ФМБ-80, ФМБ-120, ФМД-120, |
|
|
|
ФПН-100, ФПД-120 |
|
5-15 |
0,5-3,0 |
ОГШ-35, ОГШ-50, ОГН-180, ФГН-90, |
|
|
|
ОГН-90, ФГН-125, ФВШ-35, 1/2 ФГП-40, 1/2 |
|
|
|
ФГП-63 |
|
15-25 |
3-6 |
ОГШ-5, 20ГН-220, ФГШ-35, ФГШ-40, |
|
|
|
ФГН-180, 1/2 ФГП-80 |
|
25 |
6 |
ОГШ-63, ОГШ-80, ФГН-200, 1/2 ФГП-120 |
|
116
5.4.2.4. Осадження в сепараторах
Швидкість осадження частинок твердої фази зростає із збільшенням частоти обертання ротора центрифуги, радіусу обертання частинок, їх розміру, а також із зростанням різниці щільності твердої і рідкої фаз. Ефективність процесу центрифугування знижується із збільшенням в’язкості середовища.
Один з найбільш поширених видів центрифуг, вживаних в мікробіологічній промисловості, - сепаратори.
Сепаратори використовують для розділення, концентрування, очищення, прояснювання, для постадійної обробки рідини, наприклад, послідовного відділення грубодисперсного осаду з тонкодисперсних суспензій, для виконання двох або більше операцій по переробці рідких сумішей.
При виборі типу сепаратора необхідно визначати в першу чергу його технологічне призначення.
На відміну від інших центрифуг в сепараторові є пакет конічних тарілок, закріплених на валу ротора. Суспензія, що розділяється, через розподільну трубу і внутрішню порожнину тарілкотримача подається до нижньої(периферичною) частини міжтарільчатого простору барабана. При цьому важчі частинки твердої фази відкидаються до нижніх поверхонь тарілок, сповзають вниз і накопичуються на стінці барабана у вигляді твердого осаду або суспензії, що згущує. Освітлена рідка фаза відводиться з верхньої частини барабана.
По технологічному призначенню сепаратори поділяються на 4 групи:
·сепаратори-роздільники - для розділення суміші взаємонерозчинних рідин;
·сепаратори-згущувачі - для концентрування або згущення суспензій і емульсій (наприклад, відділення кашалотовою жиру, застосовуваного для піногасіння, від культуральної рідини);
·сепаратори-прояснювачі - для виділення твердих суспензій з рідини (наприклад, відділення ферментів після висалювання, осадження розчинниками й т.д.);
·комбіновані сепаратори (однеабо багатосекційні) - для одночасного або послідовного виконання двох або більше операцій переробки рідкої -су міші.
Нині найбільше застосування у мікробіологічній промисловості одержали сепаратори-прояснювачі, оскільки, наприклад, при глибинному методі культивування, коли для піногасіння використовують різні жири, необхідно відділяти отриману КР від жиру перед подальшою її обробкою, тому що часточки жиру будуть перешкоджати нормальному технологічному процесу, особливо при концентруванні, осіданні та розпиленні.
При виборі сепаратора-прояснювача можуть бути використані два типи сепараторів залежно від типу барабана:
·сепаратори тарілчасті - для розділення суспензій з невеликою різницею у відносній густині поділюваних фаз(при цьому можна виділяти частки розміром від 0,01 мкм);
117
·сепаратори багатокамерні з циліндричними вставкамидля розділення суспензій зі значною різницею у відносній густині фаз.
Сепаратори із циліндричними вставками мають більший обсяг шламового простору, ніж тарілчасті сепаратори, однак менший фактор розділення.
Залежно від об'ємного вмісту зважених часток у суспензії можуть бути використані сепаратори з різною системою видалення осаду.
Сепаратори з ручним вивантаженням осадучерез порівняно невелику ємність шламового простору й необхідності зупинки сепаратора для очищення від шламу можна використовувати при прояснюванні тонкодисперсних суспензій з вмістом зважених часток не більше 0,5%.
Сепаратори з відцентровим періодичним вивантаженнямосаду мають великий шламовий простір для нагромадження осаду і періодичне відцентрове вивантаження його на ходу.
Сепаратори з відцентровим періодичним вивантаженням осаду дозволяють прояснювати тонкодисперсні суспензії або розділяти стійкі емульсії з вмістом у них зважених часток 0,5—5% об. при різниці відносних густин не менш
3%.
Тривалість робочого циклу сепарації залежить від концентрації зважених часток у вихідному продукті та продуктивності сепаратора по даному продукту. Сепаратори з відцентровим періодичним вивантаженням осаду можна успішно застосовувати для обробки продуктів, тверда фаза яких несхильна до сильного ущільнення під дією інтенсивного поля відцентрових сил.
Сепаратори з безперервним вивантаженням осадумають для цієї мети спеціальні сопла. Сепаратори зі соплами дозволяють прояснювати тонкодисперсні суспензії або розділяти стійкі емульсії з концентрацією твердої фази 6-12%. Застосування сопел з отворами різного діаметра дозволяє регулювати концентрацію згущеної твердої фракції.
За способом подачі вихідної суміші й способу відводу отриманих рідких фракцій розрізняють сепаратори: відкриті, закриті й герметичні.
Увідкритих сепараторах подача в барабан рідкої суміші та відвід отриманих рідких фракцій йде відкритим потоком, не ізольованим від доступу повітря.
Унапівзакритих сепараторах рідина подається в барабан(відкритим потоком, а відвід однієї або обох фракцій— під тиском по закритих трубопроводах. Процес сепарації в напівзакритих сепараторах також не ізольований від доступу повітря.
Угерметичних сепараторах подача в барабан рідкої суміші й відвід рідкої фракції відбуваються під тиском по закритих трубопроводах, герметично з'єднаним із впускним і випускним патрубками. Процес сепарації ізольований
від доступу повітря з виробничого. Застосування сепарування дозволяє з високою швидкістю обробляти -бі
льші обсяги важкофільтруємих суспензій, значно інтенсифікувати виділення й концентрування мікроорганізмів без істотних втрат і змін цільових продуктів.
118
Рушійною силою процесу сепарування є відцентрова сила. Швидкість осадження часток у сепараторі визначається за рівнянням
Wос |
= |
d 2 n2 R( r |
1 - r |
2 )p 2 |
|
|
18mc 900 |
(5.11.) |
|||||
|
|
де d — діаметр твердої частки, м; n — частота обертання барабана, хв-1; R — радіус барабана, м; ρ1 — щільність твердої частки, кг/м3; ρ2 — щільність рідкої фази, кг/м3; μc — динамічна в'язкість, Па • с.
З рівняння видно, що ефективність сепарації в значній мірі збільшується із ростом частоти обертання барабана і його діаметра, розміру часток і величини різниці густин твердої й рідкої фаз. Зі збільшенням в'язкості середовища ефективність сепарації зменшується. У ряді випадків в'язкість середовища можна зменшувати шляхом її нагрівання, якщо це не впливає на якість цільового
продукту. |
|
|
Максимальна |
продуктивність вітчизняних сепараторів становить50...80 |
|
м3/год по вихідній, |
дріжджовій суспензії. Пропускна продуктивність сепара- |
|
тора по |
вихідній суспензії кормових дріжджів звичайно на 2540 % нижче |
|
зазначеній |
у паспорті продуктивності по воді, і конкретно визначається для |
|
кожного виду виробництва після промислових випробувань. |
||
Істотним недоліком сепараторів є швидка забиваємість мундштуків і |
міжтарільчатого простору механічними включеннями й мертвими дріжджами. Тривалість роботи сепараторів без чищення залежить від якості вихідної
суспензії й правильної експлуатації й становить12...24 години. Позитивний вплив на роботу сепараторів робить стадія флотації, при якій сепарируєма суспензія звільняється від ряду механічних домішок, що засмічують міжтарільчатий простір і отвори в мундштуках. Для більш ефективної роботи сепараторів вхідна дріжджова суспензія попередньо пропускається через сітчасті фільтри.
Продуктивність сепаратора по живленню дріжджовою суспензією визначається як
П = hб К кон |
4pw 2 z × tg a (R max3 - Rmin3 ) |
´ |
||||
|
|
|
||||
|
|
|
|
27 |
|
|
r1 - r2 |
|
|
|
(5.12.) |
||
× r 2 |
× |
|
Cк |
|
||
|
|
- Сн |
||||
m |
|
Ск |
де ηб = 0,25 — ККД барабана сепаратора; Kкон — коефіцієнт концентрації; ω - кутова швидкість барабана, рад/с; z — кількість тарілок; α = 45—60° — кут нахилу утворюючої тарілки; Rmax і Rmin — максимальні та мінімальний розрахункові радіуси тарілки; ρ1 і ρ2 — густини дисперсійного середовища й дисперсної фази, кг/м8; μ — в'язкість дисперсійного середовища, Па• с; r — наведений радіус твердої частинки, м; Cн і Ск — об'ємна частка твердих часток (дріжджових кліток) у вихідній суспензії та у концентраті, %.
119
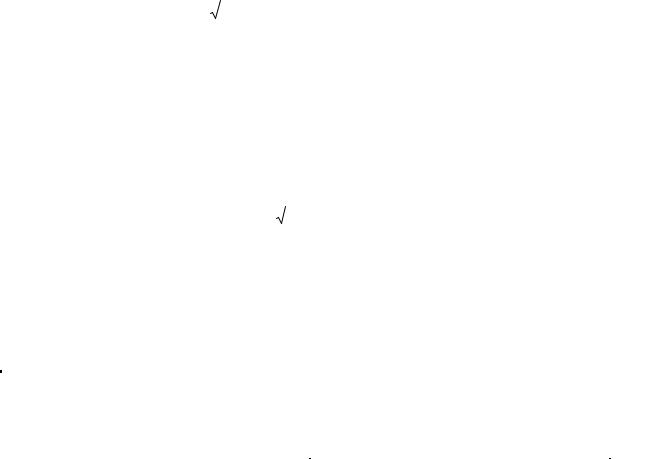
Наведена формула використовується для розрахунку сепараторів із соплами. Коефіцієнт концентрації Kкон враховує вплив вмісту твердої або квазітвердої фази (наприклад, дріжджових кліток) у вихідній суспензії на процес сепарування, що протікає в пакеті тарілок.
Діаметр отворів сопел сепаратора
d = [ |
|
4Q |
]1/2 |
||
|
|
|
|||
p × zc × Kист ×w × |
R2 - r 2 (Cк / Сн - 1) |
||||
|
(5.13.) |
де Q — продуктивність сепаратора, м3/год; zc — кількість сопел; Kист — коефіцієнт витікання, для осадів звичайно дорівнює0,7; R — відстань від осі обертання барабана до вихідного отвору сопла, м; r — відстань від осі обертання барабана до поверхні рідини в ньому, м.
Із цього рівняння можна визначити концентрацію дріжджів у згущеній суспензії
Ск |
= |
4Q ×Сн |
|
|
+ Cн |
p × zc × Kист ×w × d 2 |
|
|
|||
|
|||||
|
|
R2 - r 2 |
|||
|
|
|
(5.14) |
У виробництві згущення суспензій до вмісту дріжджів11-12 % АСБ здійснюється шляхом послідовного сепарування у 2-3 ступені.
Технічна характеристика сепараторів
|
|
|
|
|
Таблиця 5.7 |
|||
|
|
Робоча |
Потужність |
Габарити, мм |
|
|||
Марка |
Продуктивність, |
частота |
електро- |
|
|
|
Маса, |
|
м3/год |
обертання, |
двигуна, |
Довжина |
Ширина |
Висота |
кг |
||
|
||||||||
|
|
об/хв |
кВт |
|
|
|
|
120
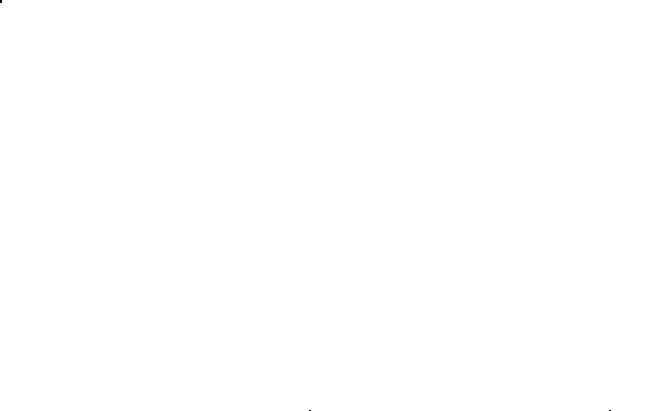
ОМІ |
10 |
6500 |
7 |
935 |
630 |
1290 |
482 |
ОМБ-ЗС |
15 |
5500 |
10 |
1100 |
730 |
1375 |
835 |
АСГ-1А |
0, 002-0,1 |
17 900 |
0,6 |
710 |
285 |
420 |
41,4 |
АСГ-ЗМ |
0, 05-0,2 |
9000- |
1,0 |
980 |
425 |
665 |
116 |
СПВ-12 |
0, 1-0,2 |
11000 |
4,5 |
945 |
600 |
1340 |
510 |
СФЭ |
0, 3-0,45 |
7450 |
4,5 |
885 |
715 |
1015 |
398 |
ВСМ |
До 2,5 |
3000 |
10 |
1085 |
870 |
1455 |
1090 |
ВСЛ |
2,0 |
6500 |
14 |
1500 |
1100 |
1868 |
1412 |
ВСН |
3,0 |
4170 |
14 |
1290 |
1570 |
1610 |
1135 |
ВСП |
0,6 -0,8 |
5000 |
14 |
1520 |
1270 |
1677 |
1530 |
ВСТ |
2,0 |
5000 |
14 |
1520 |
1240 |
1660 |
1410 |
АСЭ-3 |
0,5 |
5000 |
14 |
1250 |
950 |
1550 |
1365 |
АИС |
1,5 |
5000 |
15 |
1260 |
1020 |
1500 |
1365 |
А-АЛС-1 |
0, 5-1,5 |
5000 |
13 |
1492 |
810 |
1470 |
1465 |
ВСБ-М |
18,0 |
5000 |
10 |
1220 |
750 |
1500 |
830 |
ВСЖ-2 |
25,0 |
5000 |
10 |
1060 |
970 |
1430 |
770 |
ДСГ-4 |
18,0 |
4700 |
10 |
1000 |
600 |
1240 |
830 |
ДСГ-35 |
До 0,035 |
5100 |
20 |
1665 |
750 |
1493 |
1262 |
|
|
4770 |
|
|
|
|
|
Залежно від способу вивантаження осаду сепаратори ділять на машини без- перервно-циклічної дії з ручним або механізованим вивантаженням осаду і безперервної дії. У сепараторах безперервно-циклічної дії рідкі(точніше, текучі) фракції віддаляються з барабана безперервно, а твердий осад — періодично, у міру накопичення. При розділенні емульсій з мінімальним змістом твердих частинок (до 0,1%) використовують сепараторів з ручним вивантаженням осаду, при розділенні суспензій із змістом твердої фази до3— 5% —с механізованим вивантаженням осаду під дією відцентрової сили. Осад в такому сепараторові вивантажується періодично, після припинення подачі суспензії. За допомогою спеціального механізму відкривають отвори в зовнішній стінці барабана, через які осад віддаляється.
Сепаратори безперервно забезпечують розділення дії суспензій з безперервним відведенням всіх фракцій, що утворюються.
Для вивантаження осаду в таких машинах використовують сопла або клапани, встановлені в периферичній частині барабана.
Сепаратори безперервно-циклічної дії з механізованим вивантаженням осаду широко застосовують для відділення біомаси у виробництві антибіотиків, ферментів, бактерійних препаратів. Для розділення дріжджових суспензій використовують в основному сепаратори безперервної дії різної продуктивності.
121
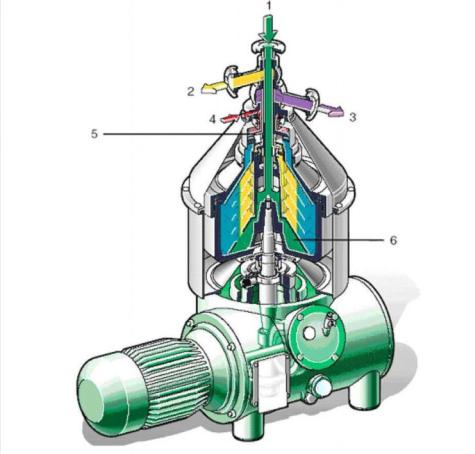
Рис.5.26. Сепаратор фірми АльфаЛаваль
5.4.2.5. Випарювання
Випарювання – процес утворення парової фази, який відбувається в усій масі рідини і, головним чином, на межі між паровою бульбашкою і рідиною. Випарювання настає при температурі кипіння, при якій тиск насиченої пари рідини дорівнює зовнішньому тиску. Процес пароутворення до настання моменту кипіння називають випаровуванням.
Випарювання є тепловим процесом і використовують для зневоднення розчинів, суспензій з метою концентра-
ції твердої фази або розчиненої речовини. Процес випарювання проводять у випарних апаратах різної конструкції.
Випарні апарати класифікують за наступними ознаками:
·періодичної та безперервної дії;
·роду теплоносіїв;
·методу обігріву;
·розташування і виду поверхні теплообміну(компонування й конструкція поверхні нагрівання);
·розташування робочого середовища;
·режиму та кратності циркуляції розчину.
122
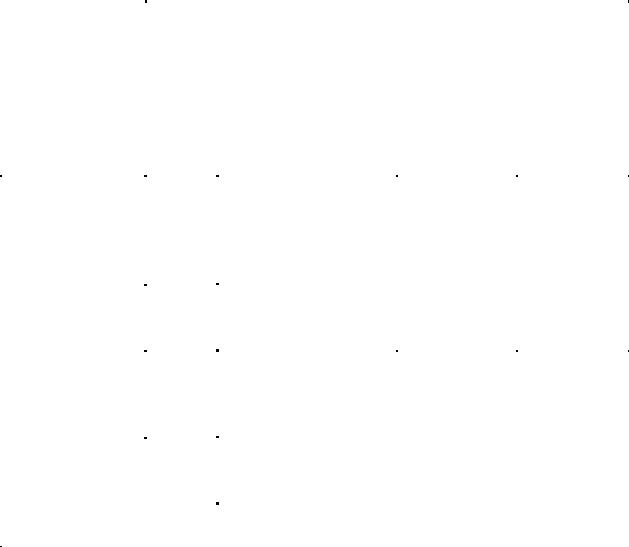
Цільові продукти мікробного синтезу в основному термолабільні та деякою мірою можуть інактивовуватись при температурах вище 50...80 °С протягом 5...15 хв. Тому процеси випарювання повинні протікати при режимах, що забезпечують мінімальні втрати цільових продуктів від термічної інактивації.
Для кожного продукту біосинтезу, що концентрується, час перебування у випарному апарату при відповідній температурі визначається дослідним шляхом. На підставі дослідних даних вибирається відповідна конструкція випарного апарата, що забезпечує оптимальний час перебування середовища в апарату при заданій продуктивності при мінімальних витратах енергії.
У таблиці 5.8. наведені порівняльні показники випарних апаратів, які застосовуються та рекомендуються до використання в мікробіологічній промисловості. за цим даними можна орієнтовно вибрати необхідний апарат для концентрування конкретного продукту.
Порівняльна характеристика вакуум-випарних апаратів для сгущення термолабільних біологічних суспензій
Таблиця 5.8.
|
|
|
Типи апаратів |
|
|
|
|||
|
циркуляційні |
тонкошарові |
|
плівкові |
|
||||
|
|
з при- |
з плас- |
з та- |
|
|
з пе- |
с обе- |
|
|
|
з вис- |
зі сті- |
рто- |
|||||
Показник |
з при- |
мусо- |
тинча- |
рілчас- |
ремі- |
||||
род-ною |
вою |
стим |
тим |
хід- |
каю- |
шу- |
вою |
||
|
ною |
чою |
повер- |
||||||
|
цирку- |
цирку- |
тепло- |
тепло- |
ван- |
||||
|
ля-цією |
ля- |
об- |
об- |
плів- |
плів- |
ням |
хнею |
|
|
кою |
кою |
нагрі- |
||||||
|
|
цією |
міном |
міном |
плівки |
||||
|
|
|
|
|
|
|
|
вання |
|
Максимальна |
|
|
|
|
|
|
|
|
|
продуктивність |
|
|
|
|
|
|
|
|
|
за випаровува- |
120 |
120 |
8 |
7 |
250 |
250 |
0,5 |
2,5 |
|
ною вологою, |
|
|
|
|
|
|
|
|
|
т/год |
|
|
|
|
|
|
|
|
|
Коефіцієнт теп- |
900.. |
1500.. |
1800.. |
1800... |
1700... |
2000... |
2000... |
|
|
лопередачі, |
10 000 |
||||||||
1800 |
2400 |
2500 |
2200 |
2700 |
3200 |
3600 |
|||
вт/(м2.°с) |
|
|
|
|
|
|
|
|
|
Максимальна |
|
|
|
|
|
|
|
|
|
в'язкість концен- |
0,6 |
1,5 |
0,4 |
0,4 |
1 |
1 |
15 |
15 |
|
трованого сере- |
|||||||||
|
|
|
|
|
|
|
|
||
довища, Па·с |
|
|
|
|
|
|
|
|
|
Час перебування |
|
|
|
|
|
|
0,1...0, |
0,01... |
|
середовища в |
60... 150 |
30..90 |
3...6 |
1...3 |
4...6 |
2...6 |
|||
апарату, хв |
|
|
|
|
|
|
4 |
0,1 |
|
|
|
|
|
|
|
|
|
||
Доцільна кіль- |
2...3 |
1...3 |
2...3 |
2...3 |
1...2 |
2...4 |
1 |
1 |
|
кість ступенів |
|||||||||
|
|
|
|
|
|
|
|
123
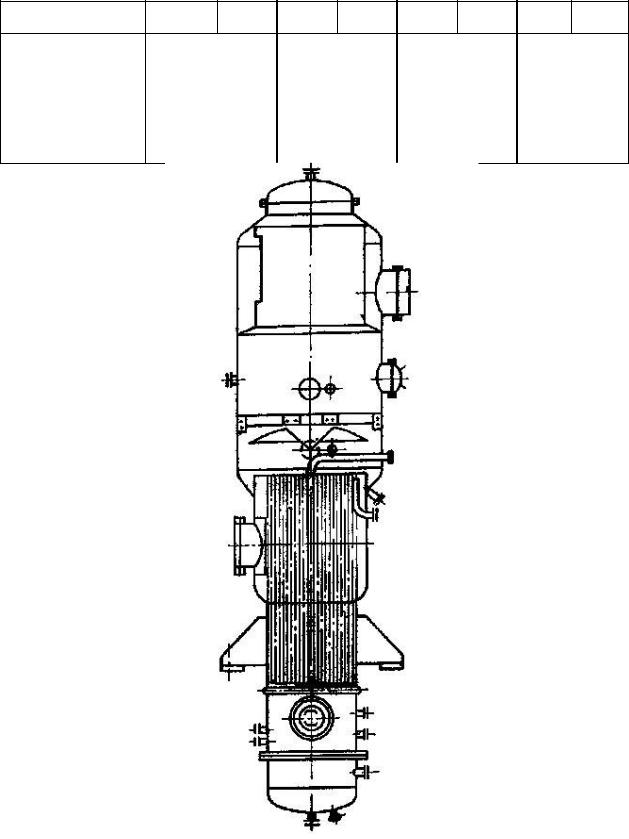
випарювання
Продукти біосин- Кормові біома- си
тезу, що концен- (дріжджі, бак- труються
терії й ін.)
Ферменти, антибіотики, вітаміни й ін.
Кормові біомаси, ферменти, антибіотики, амінокислоти, вітаміни
й ін.
Ферменти, антибіотики, вітаміни, мікробні клітини й ін.
Рис. 5.27. Схема тонкоплівкового вакуум-випарного апарату – використовується для сгущення термолабільних розчинів в біотехнологіях отримання кормових дріжджів, ферментів, антибіотиків, амінокислот, вітамінів
124
Температура нагрівання випарюваного середовища залежить як від термолабільности цільових продуктів, так і хімічного складу середовища, що концентрується. при випарюванні ряду конкретних середовищ приймаються приблизні максимальні температури їхнього нагрівання:
·для кормових дріжджів і біомас інших мікроорганізмів, розчинів амінокислот без вуглеводів — 70...80 °с ;
·для культуральних рідин, що містять вуглеводи й цільові амінокислоти,
—до 60°с;
·для культуральних рідин і екстрактів, що містять ферменти, — 30...40
°с ;
· для культуральних рідин, що містять вітаміни й антибіотики — 50...60
°с.
Температури кипіння нижче 100 °с досягаються шляхом створення відповідного вакууму у випарних апаратах.
5.4.3. Мембранні методи розділення
Звичайна фільтрація використовується для відділення від рідини достатньо крупних частинок твердої фази(50—100 мкм і більш). Для відділення дрібніших частинок (2—5 мкм), а також для розділення розчинів використовують мембранні способи. До них відносятьсямікрофільтрація, діаліз,
електродіаліз, зворотний осмос і ультрафільтрація. Особливістю всіх цих методів є застосування напівпроникних мембран.
Переваги мембранних методів розділення біологічних суспензій і розчинів наступні: відсутність температурних, механічних і хімічних дій на продукт, що переробляється; простота апаратурного оформлення, відсутність рухомих деталей; низька енергоємність процесу; можливість забезпечення герметичності і асептики процесу.
5.4.3.1. Мікрофільтрація
Це процес, близький до звичайної фільтрації. Мікрофільтрація через пористі мембрани з діаметром пір від0,1 до 10 мкм застосовується для відділення дрібних частинок твердої фази, зокрема мікроорганізмів (в цьому випадку її називають стерилізуючою фільтрацією). Завдяки великому числу пір на одиниці поверхні мембрани (кількість пір досягає 70—80% загального об’єму мембрани) процес мікрофільтрації протікає з достатньо високою швидкістю. Проте у міру накопичення затримуваних частинок у поверхні мембрани і закупорювання пір дрібними частинками швидкість фільтрації падає. Щоб запобігти цьому, використовують різні способи турбулизации середовища у поверхні мембрани, наприклад механічне перемішування або вібрацію. Процес мікрофільтрації зазвичай ведуть при різниці тиску 0,1—0,2 МП а.
Слід зазначити, що інтерес до мікрофільтрації як до способу стерилізації розчинів термолабільних компонентів засобів ферментацій останніми роками зріс.
125
5.4.3.2. Діаліз і електродіаліз
Діаліз - процес очищення розчинів високомолекулярних речовин (наприклад, ферментів) від розчинених в них низькомолекулярних речовин за допомогою напівпроникної мембрани.
З одного боку мембрани знаходиться початковий розчин, з іншої – чиста вода. Присутні в розчині низькомолекулярні речовини шляхом дифузії проходять через мембрану і віддаляються разом з водою. Це так званий діаліз проти води. Білки або інші високомолекулярні речовини, молекули яких більше пір мембрани, залишаються в розчині, і, таким чином, їх розчин очищається від низькомолекулярних домішок. Ступінь очищення залежить від співвідношення кількостей води і ліалізуємого розчину, тривалості діалізу і коефіцієнта дифузії. Так, при діалізі ферментного розчину протягом 24 ч і співвідношення розчину і води 1:50 кількість домішок (вуглеводів, амінокислот, зольних елементів і ін.) зменшується в 3,5—4 рази, а активність ферменту на 1 г сухих речовин зростає в 2,7—3,0 разу. Мембрани для діалізу виготовляють з пергаменту, армованого целофану і інших матеріалів.
Швидкість процесу дифузійного перенесення речовин при діалізі невелика. Вона значно вище тоді, коли домішки, що видаляються, заряджені. Для заряджених частинок застосовують електродіаліз. Він полягає в пропусканні постійного електричного струму через діліалізуємий розчин. При цьому позитивно заряджені іони рухаються через одну мембрану до катода, негативні іони —через іншу мембрану до анода. Щоб уникнути зворотної дифузії при електродіалізі використовують селективні мембрани, проникні тільки або для аніонів, або для катіонів. Швидкість електродіалізу визначається в основному силою струму і змінюється в широких межах. Електродіаліз на відміну від звичайного диализа широко застосовують не тільки в лабораторних, але і в промислових умовах, наприклад, для очищення ферментних розчинів після осадження ферментів методом висолювання.
5.4.3.3. Ультрафільтрація
Так називають процес концентрації розчинів високомолекулярних з’єднань (наприклад, ферментів) з одночасним очищенням їх від низькомолекулярних домішок шляхом пропускання розчину через мембрану з порами розміром від 0,01 до 0,1 мкм. На відміну від мікрофільтрації або звичайної фільтрації при ультрафільтрації затримуються окремі молекули розчиненої високомолекулярної речовини; при ультрафільтрації відбувається не розділення фаз, а перерозподіл розчинених в рідкій фазі речовин. Тим часом проблема забивання пор фільтруючого матеріалу, характерна для звичайної фільтрації, має не менше, а можливо, і більше значення.
Важливою характеристикою будь-якої ультрафільтраційної мембрани є її селективність, що визначає ступінь затримання розчиненої речовини.
Селективність мембрани залежить від розмірів і форми молекул розчиненої речовини. Слід мати на увазі, що практично у всіх випадках існують молекули, що затримуються мембраною лише частково.
Для процесу ультрафільтрації характерне явище концентраційної поляризації
— підвищення концентрації розчиненої речовини поблизу поверхні мембрани.
126
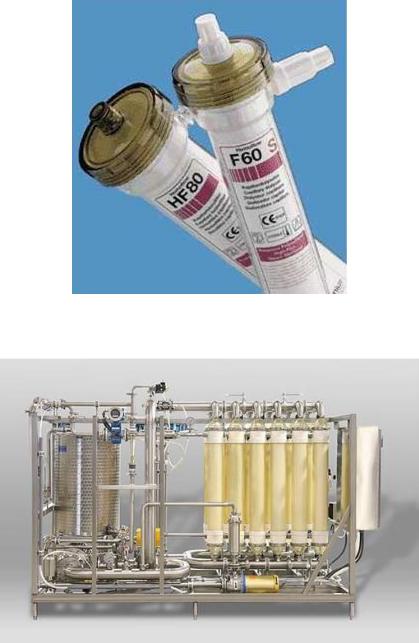
Воно пов’язане з тим, що через мембрану проходять в основному молекули розчинника. Внаслідок цього знижується швидкість фільтрації. Для зменшення концентраційної поляризації застосовують хімічні інгібітори, що перешкоджають утворенню поляризаційного шару, або установки фільтрації спеціальної
конструкції, де забезпечується турбулізація потоку або підвищення його швидкості при пропусканні через вузькі канали.
Для ультрафільтрації, як правило, використовують пористі полімерні мембрани на основі полиуретанов, складних ефірів целюлози, поливинилового спирту і ін. Такі мембрани отримують шляхом опромінювання зарядженими частинками полімерної плівки з подальшим її травленням. Для забезпечення механічної міцності в умовах гідравлічного тиску основну тонку мембрану прикріплюють до грубішої підкладки товщиною 125—250 мкм.
На практиці застосовують установки пластинчастого, трубчастого, рулонного типів, а також апарати з мембранами у вигляді порожнистих волокон.
Рис.5.28. Фільтруючі елементи у вигляді порожнистих волокон.
127
Рис.5.29. Загальний вигляд ультрафільтраційної установки.
5.4.3.4. Зворотній осмос
Якщо розчин деякої речовини відокремлений від чистого розчинника напівпроникною перегородкою, то при рівності тиску з обох боків відбувається дифузія чистого розчинника в розчин. Рушійною силою цього процесу є градієнт концентрації, оскільки концентрація розчинника в розчині завжди нижча. Цей процес називають осмосом, а його рушійну силу— осмотичним тиском. Осмотичний тиск чисельно рівний зовнішньому тиску, який необхідно прикласти до розчину, щоб процес дифузії через мембрану припинився (точніше, досяг динамічної рівноваги). Якщо до розчину прикласти тиск вище осмотичного, то дифузія молекул розчинника відбуватиметься в протилежну сторону — з розчину в чистий розчинник. Процес, що супроводжується концентрацією розчину, отримав назву зворотного осмосу.
Процес зворотного осмосу принципово аналогічний ультрафільтрації і відрізняється лише тим, що для нього використовують мембрани з порами меншого розміру (до 0,01 мкм) і вищий тиск (7—8 МПа замість 0,3—1 МПа). За допомогою зворотного осмосу зазвичай концентрують розчини низькомолекулярних речовин, що характеризуються високим осмотичним тиском. Зворотний осмос застосовують також для отримання чистого розчинника (наприклад, в опріснювальних установках).
Устаткування, використовуване для проведення зворотного осмосу, подібно до установок для ультрафільтрації.
5.4.3.5. Осадження
Осадженням називають процес, в якому додавання певних реагентів або зміна физико-хімічних умов викликає випадання розчиненої речовини(частіше за весь білок) в осад. Осадження широко застосовується у ферментній
промисловості. Найчастіше для осадження ферментів використовують нейтральні солі (в цьому випадку процес називаютьвисолюванням) або органічні розчинники, а також методи, засновані на зміні температури або рН розчину, додаванні високомолекулярних полімерів і ін.
5.4.3.6 Висолювання
Відомо, що розчинність білків в розчинах солей нижча, ніж в чистій воді. Залежність розчинності від концентрації солі описується рівнянням
lgS = β-КC, |
(5.14.) |
де S — розчинність білка, г/л; β,К - константи, що характеризують властивості |
білка і солі (β залежить також від температури і рН); С — концентрація соли, г/л.
Як видно з рівняння, додавання соли до розчину білка призводить до того, що при певній концентрації соли розчинність білка стає нижчим за його концентрацію в розчині, і білок починає випадати в осад. Ступінь осадження білка залежить від його початкової концентрації в розчині, концентрації соли і властивостей системи. На цьому явищі заснований процес висолювання білків.
128
Він пов’язаний з посиленням орієнтації диполів води іонами солей, що приводить до руйнування шару гідрату навколо молекул білка і його коагуляції.
Найчастіше для проведення висолювання використовують сульфат амонію (завдяки його високій розчинності у воді і низькій вартості), рідше — хлорид натрію. Концентрація соли, що додається у ферментний розчин, зазвичай близька до концентрації насичення і для сульфату амонію складає70—75 г на 100 мл розчину, що висолюється. Сіль додають в сухому вигляді, невеликими порціями, при постійному перемішуванні, щоб уникнути утворення локальних зон з підвищеною концентрацією .солиПісля додавання розрахункової кількості соли осад утворюється не-відразу, а протягом деякого часу - від 30 хв до декількох годин.
Різні білки випадають в осад при різних концентраціях соли в розчині, у зв’язку з цим процес висолювання використовують не тільки для виділення ферментів, але і для їх очищення від небажаних домішок. Наприклад, осадження глюкоамилази сульфатом амонія в кількості60% насичення приводить до неповного виділення цільового продукту. Та зате при цьому фермент практично повністю звільняється від супутньої йому глікозилтрансферази, що осідає при концентрації соли 90% насичення.
У осадках, отриманих при висолюванні, міститься від 25 до 80% соли, тому препарати харчового або медичного призначення необхідно піддавати додатко-
вому очищенню (наприклад, за допомогою електродіалізу). |
|
|
|||
5.4.3.7. Осадження органічними розчинниками |
|
|
|
||
При додаванні до розчину ферменту органічного розчинника(етанолу, мета- |
|
||||
нолу, ізопропанолу, ацетону і ін.) знижується діелектрична постійна середови- |
|
||||
ща. При цьому, як при висолюванні, руйнується оболонка гідрату білка, і він |
|
||||
випадає в осад. Концентрація розчинника, необхідна для осадження різних |
|
||||
білків, природно, також |
розрізняється, що |
дозволяє |
проводити |
їх |
|
фракціонування. Так, при осадженні етанолом комплексу ферментів з екстракту |
|
||||
поверхневої культури Asp. |
oryzae КС |
близько70—80% протеолітичних |
|
||
ферментів випадає в осад при концентрації спирту50%, а амілази майже не |
|
||||
осідають. Після відділення |
отриманого |
осаду і |
додавання |
до надосадкової |
рідини етанолу до концентрації 70—72% отримують осад, що містить переважно амілази.
На процес осадження ферментів органічними розчинниками істотно впливає температура. В більшості випадків цей процес проводять при температурі від0 до 5°С; для цього водний розчин ферменту охолоджують до1—2°С, а розчинник – до мінус 10—15°С з урахуванням того, що при змішуванні води із спиртом суміш нагрівається. Підвищення температури приводить до денатурації ба-
гатьох ферментів, оскільки їх термолабильность при додаванні органічних розчинників сильно зростає.
Недолік процесу осадження органічними розчинниками полягає в тому, що вживані реагенти порівняно дорогі, вогненебезпечні і вельми отруйні, тому потрібне виконання відповідних заходів безпеки. Не дивлячись на це, осаджен-
129
ня органічними розчинниками досить широко застосовується у ферментній промисловості.
5.4.4. Сушіння
Сушіння є кінцевою стадією виробництва багатьох продуктів мікробного |
|
||||||||||
синтезу, іноді її застосовують як проміжний процес при отриманні високоочи- |
|
||||||||||
щених препаратів. |
|
|
|
|
|
|
|
|
|
|
|
Для сушки біологічних об’єктів застосовують різноманітні способи і уста- |
|
||||||||||
новки. Вони розрізняються по агрегатному поляганню вологи у висушуваному |
|
||||||||||
матеріалі (сушка з рідкого стану або з |
твердого), а |
також |
за |
способом |
|
||||||
підведення теплоти (контактна, конвективна і радіаційна). |
|
|
|
|
|
|
|||||
Вибір способу сушки залежить від виду початкового матеріалу(концентри- |
|
||||||||||
рованний розчин, паста, суспензія), його вологості, термостабильности і т.д. |
|
||||||||||
Найбільші |
труднощі |
зазвичай |
виникають |
при |
висушуванні |
ж |
|||||
мікроорганізмів у виробництві бактерійних препаратів і |
сухих |
дріжджів, |
|
||||||||
ферментів, деяких антибіотиків і інших термолабільних препаратів. |
|
|
|
|
|||||||
При контактній сушці матеріал нагрівається в результаті безпосереднього |
|
||||||||||
зіткнення з гарячими поверхнями(плитами, |
вальцями |
і |
.т п.). |
На |
цьому |
|
|||||
принципі засновані шафові і вальцовие сушарки. Проте вони малопридатні для |
|
||||||||||
сушки термолабільних препаратів і мають ряд недоліків. |
|
|
|
|
|
|
|||||
В процесі конвективної сушки |
теплота |
підводиться |
до |
висушуваного |
|
||||||
матеріалу за допомогою газоподібного сушильного агента-теплоносія, який |
|
||||||||||
служить і для відведення вологи, що випаровується. Цей метод найширше |
|
||||||||||
застосовується в біотехнології і лежить в основі роботи розпилюючих, пневма- |
|
||||||||||
тичних, аерофонтанних сушарок і сушарок з киплячим шаром. |
|
|
|
|
|
||||||
При радіаційній сушці теплота передається від нагрітого джерела до вису- |
|
||||||||||
шуваного матеріалу за допомогою інфрачервоного випромінювання. Цей ме- |
|
||||||||||
тод застосовується при сушці сублімації деяких мікробних препаратів. |
|
|
|
||||||||
Конвективна сушка. Сушильним агентом при конвективній сушці можуть |
|
||||||||||
бути повітря, топкові гази, а в окремих случаях—инертний газ. Інтенсивність |
|
||||||||||
сушки визначається швидкістю теплообміну між сушильним агентом і вису- |
|
||||||||||
шуваним матеріалом, яка залежить від коефіцієнта теплообміну, різниці тем- |
|
||||||||||
ператур (рушійної сили процесу теплопередачі) і поверхні контакту. Кількість |
|
||||||||||
теплоти, що передається висушуваному матеріалу в одиницю часу (у Вт) |
|
|
|
||||||||
Q = α(tc-tп)F, |
(5.15) |
|
|
|
|
|
|
|
|
|
|
де α — коефіцієнт |
теплообміну, Вт/(м2·К); tc і |
tп —температури |
сушильного |
|
|||||||
агента і поверхні матеріалу, Со; F — площа поверхні висушуваного матеріалу, |
|
||||||||||
м2. |
|
|
|
|
|
|
|
|
|
|
|
Як видно з рівняння, для підвищення швидкості теплопередачі, отжеі, |
|
||||||||||
інтенсивності |
процесу |
сушки необхідно |
прагнути |
збільшити |
коефіцієнт |
теплообміну і поверхню висушуваного матеріалу. Перше досягається в основному шляхом створення відповідного аеродинамічного режиму в сушильній установці, друге — подрібненням матеріалу. Можливості підвищення температури сушильного агента, як правило, обмежені термочутливістю препарату.
130
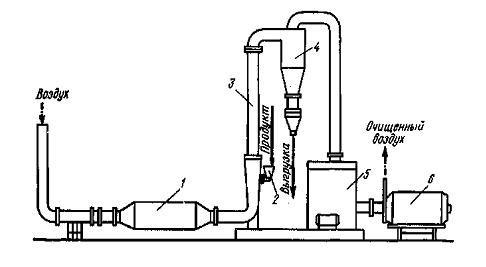
Найбільш простій сушаркою, заснованою на конвективному теплопереносе, є пневматична сушарка (рис.5.30). Повітря, підігріте в калорифері разом з тим, що подається через живильник матеріалом, поступає в сушильну трубу. Сухі частки препарату відділяються від повітря в циклоні, а відпрацьоване повітря поступає на додаткове очищення у фільтрі. Пневматичні сушарки застосовуються у виробництві деяких антибіотиків.
Рис.5.30. Схема пневматичної сушарки: 1 — калорифер; 2 — живильник; 3
— сушильна труба; 4 — циклон-віддільник; 5 — фільтр; 6 — вентилятор
Для висушування пастоподібних, сипких і рідких матеріалів використовують сушарки з киплячим шаром, в яких забезпечуються висока інтенсивність тепло- і масообміну, безперервність процесу. На рис.5. 31. зображена установка для сушки кормового концентрату лізину в суміші з висівками. Сушарка складається з двох камер, розділених подвійною сіткою; дном нижньої камери також служить подвійна сітка. Суміш рідкого концентрату лізину з висівками поступає в гранулятор і у вигляді тонких ниток видавлюється у верхню камеру
сушарки. Під дією потоку гарячого повітря частинки пасти відриваються від гранулятора і підсушуються. Потік нагрітого повітря проходить через сітки першої і другої камер з швидкістю, що забезпечує підтримку гранул в зваженому стані і мінімальне віднесення частинок з сушарки з відпрацьованим повітрям. Сушка гранул в киплячому шарі відбувається спочатку на верхньому, а потім на нижньому ярусі сушарки. Висушені гранули через шлюзовий затвор
вивантажуються з апарату і пневмотранспортом подаються в приймальний бункер.
Більш ефективніша сушарка розпилювального типу (рис.5.32.) У ній суспензія висушуваного висушуваного матеріалу безперервно подається зверху на відцентровий механізм і розпилюється на частинки розміром60—70 мкм. Теплоносій поступає знизу через направляючу насадку конічної форми з тангенціальними щілинами забезпечуючу високу швидкість руху теплоносія. Завдяки великій поверхні контакту, високим швидкостям руху частинок суспензії і -су шильного агента висушування продукту відбувається швидко (10 – 15с).
131
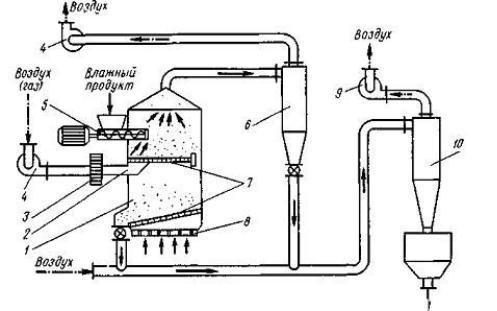
Рис.5.31. Схема сушарки з «киплячим» шаром: 1—сушильна камера; 2— газовод; 3, 8 —- калорифери; 4, 9 — вентилятори; 5 —гранулятор; 6, 10
— циклони; 7 — сітки.
Висушені частинки осідають на дно сушильної камери і вивантажуються через нижній люк, а відпрацьований сушильний агент відводиться по трубі і прямує на очищення в циклони і скрубери. Винос продукту з сушарки з відпрацьованим газом досягає 15—20%. Слід зазначити, що при сушці кормових дріжджів температура теплоносія на вході в розпилювальну сушарку 300від до 400°С. Таку ж температуру мають і сухі дріжджі, що виходять з апарату; білки, що містяться в біомасі, при цьому не розкладаються.
Сушіння сублімацією — один з найефективніших способів зневоднення живої біомаси дріжджів, бактерійних препаратів та інших термолабільних біологічних об’єктів.
При 0° С колоїдна система матеріалів, у тому числі їх волога, замерзає і надалі відбувається процес сублімації, тобто випаровування твердого тіла без його розплавлення; у даному разі з твердого агрегатного стану вода переходить у пароподібний, проминувши рідку фазу. За такого способу сушіння молекулярна структура матеріалу зберігається майже без змін і висушений матеріал характеризується доброю дисперсністю і пористістю, тим часом як за звичайного сушіння відбувається значне зменшення об'єму матеріалу.
Сублімаційна сушарка (рис.5.33.) складається з сушильної камери— субліматора 1, конденсатора-виморожувача 2 і вакуум-насоса 3. Попередньо заморожений матеріал кладуть на полиці субліматора, що обігрівається парою або гарячою водою. Пара, яка виділяється під час випаровування, потрапляє в конденсатор, де конденсується на його стінках і перетворюється на лід, який скребками видаляється з апарата. Вакуум-насосна установка створює в сушильній
132
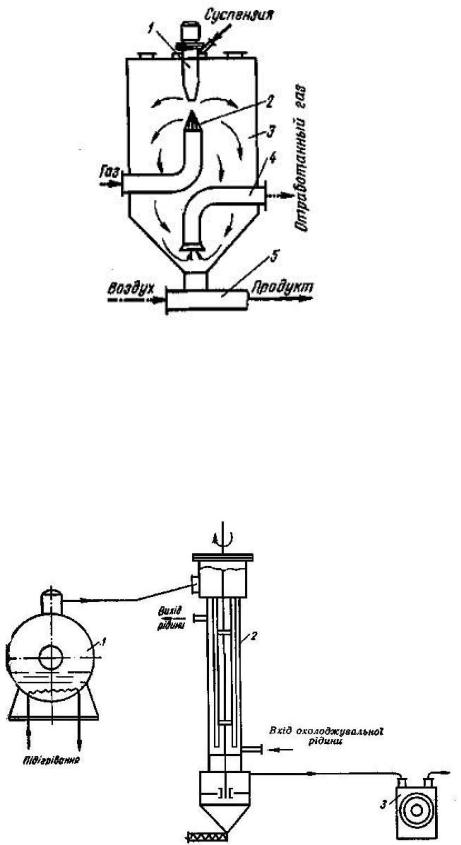
камері залишковий тиск 0,1—1,0 мм рт. ст. Цей тиск забезпечує сушіння при температурі 15° С.
Рис. 5.32. Схема сушарки розпилювального типу: 1 – розпилювальний механізм; 2 – розподільник газу; 3 – сушильна камера; 4 - газовідвод; 5– труба пневмотранспорту
Як показали розрахунки і експлуатація, сушіння сублімацією за теплоенергетичними показниками приблизно рівноцінне сушінню при атмосферному тиску, хоча витрати на побудову сушарки значно вищі.
133
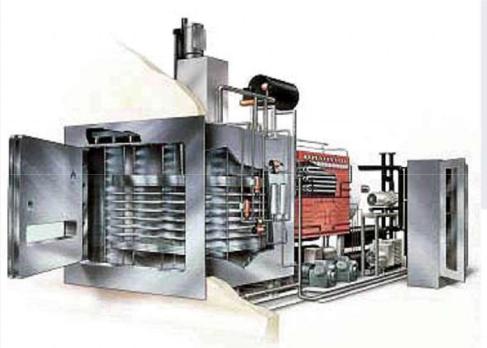
Рис.5.33.Схема сублімаційної сушарки: субліматор - 1, конденсаторвиморожувач – 2, вакуум-насос - 3.
Рис.5.34.Загальний вигляд промислової сублімаційної сушарки.
[11] c. 137-169,с.249-304, с. 304-350, с.377-472
Запитаня для самоперевірки
1.Назвіть стадії основного технологічного процесу 2. Які основні : вимоги до вибору типового ферментера ?
3.Класифікація ферментерів. Параметри підбору ферментера. 4.Назвіть основні фактори, що визначають вибір ферментера.
5.Принципи вибору методів виділення та отримання товарного продукту: товарні форми продуктів мікробного синтезу. Отримання концентратів – стадії.
6.Принципи вибору методів виділення та отримання товарного продукту: стадіх отримання зневодненої форми.
7.Що таке флотація: принцип дії, конструкції апаратів?
8.Що таке фільтрування: параметри, види, конструкції?
9.Що таке центрифугування: параметри, види, конструкції?
10.Що таке сепарування: параметри, види, конструкції?
11.Що туке випарювання: параметри, види, конструкції?
12.Що таке сушіння: параметри, види, конструкції?
13.Осадження: органічними розчинниками, висолювання.
14. Що ьаке баромембранні процеси: мікрофільтрація. Принцип дії, матеріали, конструкції установок.
15.Принцип дії : мікрофільтрації, ультрафільтрації, звортнього осмосу.
134
5.КОМПОНУВАННЯ ОБЛАДНАННЯ І БУДІВЕЛЬНА ЧАСТИНА ПРОЕТУ
Ця частина проекту характеризується переходом від абстрактн розрахунків та схем до наочного бачення майбутнього підприємства. Проектування промислових будівель мікробіологічних виробництв повинно задовольняти, в першу чергу, вимоги досконалої технології, забезпечувати необхідні санітарно-гігієнічні умови для працівників, бути простими у компонуванні, уможливлювати зміни технологічного процесу, відповідати вимогам економіки, індустріалізації будівництва, а також естетики.
Винятково важливим завданням як на стадії проектування, так і під час напрацювання продуктів мікробіологічного синтезу є забезпечення відповідності якості препаратів сучасним вимогам і дотримання принципів і правил Належної Виробничої Практики (GМР).
Питання проектування у будівництві відповідно до ДБН регламентує Держбуд України. Згідно з класифікатором усі ДБН поділені на3 частини, кожна з яких поділяється на групи:
1.Організація, керування, економіка будівництва.
2.Норми проектування:
-загальні норми проектування,
-основи та фундаменти,
- інженерне |
обладнання |
будівель |
і |
споруд(бетонні |
та |
залізобетонні |
конструкції, |
сталеві |
конструкції, крівлі, |
|
|
підлоги), |
|
|
|
|
|
-зовнішні мережі (опалення, вентиляція і кондиціонування, теплова ізоляція обладнання і трубопроводів),
-споруди транспорту, |
х^ |
-гідротехнічні і енергетичні споруди, меліоративні системи і споруди,
-планування й забудівля населених пунктів,
-громадські будівлі,
-промислові підприємства, виробничі будівлі і споруди, допоміжні будівлі (генеральні плани промислових підприємств, виробничі будівлі, споруди промислових будівель).
3. Організація, виробництво та приймання робіт.
Крім загальних норм і правил будівництва, існують галузеві норми, вимоги, правила, інструкції та інші документи стосовно конкретики та специфіки цієї галузі. Наприклад, в мікробіологічній промисловості затверджені норми технологічного проектування гідролізних виробництв, БВК, лізину, бактеріальних засобів захисту рослин тощо.
5.1. Принципи компонування
Основою для компонування обладнання є
-технологічна схема,
-специфікаційна таблиця обладнання,
135
-правила компонування,
-стандартні схеми промислових будівель,
-визначені площі допоміжних приміщень.
5.2. Правила вибору типу будівлі
Компонування починають з вибору типу будівлі, в якій буде розташован обладнання. При цьому дотримуються таких основних правил:
1. Якщо матеріальні потоки рухаються переважно в горизонтальних напрямах, то обирають одноповерхову будівлю, якщо у вертикальних (наприклад,
|
потоки рідини, або твердої сировини, або напівфабрикатів рухаються са- |
||||
|
моплином) - багатоповерхову. |
|
|
|
|
2. |
Якщо технологічний процес супроводжується виділенням |
великої |
|||
|
кількості тепла, газів, шкідливих речовин, які в результаті аварії можуть по- |
||||
|
трапити в атмосфер) приміщення, якщо не вимагають стерильності атмо- |
||||
|
сфери, то обирають будівлю павільйонного типу з встановленням етаже- |
||||
|
рок для закріплення обладнання. |
|
|
|
|
3. |
Якщо процес повинен перебігати в стерильних умовах, то всю будівлю |
||||
|
або її частину огороджують і герметизують відомими методами, наприклад, |
||||
|
облаштуванням у приміщеннях стерильних кімнат, тамбурів тощо. |
|
|
||
Наприклад, виробництво |
флориміцину |
потрібно розташовувати |
у |
трьох |
|
з'єднаних між собою будівлях: |
|
|
|
||
а) |
підготовка ПС (стерильні умови не потрібні); |
|
|
||
б) підготовка ПМ і ферментація продуцента(стерильні умови потрібні, голов- |
|||||
ки ферментерів повинні |
знаходитись |
в окремому приміщенні |
і |
відділені |
суцільним міжповерховим перекриттям); в) оброблення КР, в основному, відбувається в горизонтальних напрямах,
але враховуючи наявність самопливних потоків(потоки фільтратів) потрібно, щоб будівля була двоповерховою. Можливе застосування і одноповерхової з майданчиками для обслуговування апаратів.
Наприклад, виробництво лимонної кислоти відбувається в нестерильних умовах, в основному, в горизонтальних напрямах, тому бажано обрати одноповерхову будівлю, але передбачити в ній стерильне приміщення для блока інокуляції.
Компонування обладнання може бути виконано графічно(розроблення поверхових планів, повздовжніх і поперечних розрізів) або об'ємним методом - створенням зеальноїабо комп'ютерної просторової моделі цеху, що проектується.
Під час розроблення проекту компонування обладнання графічним методом жлани його розташування викреслюють в масштабі1:100 або 1:50. На плани наносять все без винятку обладнання, що встановлюється у цьому виробничому приміщенні, в юму числі резервні насоси. Кількість планів повинна відповідати кількості поверхів.
Апарати зображують у вигляді зовнішніх контурів. Наприклад, вертикальні циліндричні апарати зображають у вигляді кіл з осями та позначеннями люків і приводів. Розрізи потрібно виконувати так, щоб показати по можливості усі апарати, всі встановлюють в цьому приміщенні.
136
5.3.Деякі правила компонування обладнання
1.Обладнання розташовують за принципом технологічного потоку зверху донизу по горизонталі, уникаючи повернення і перехрещення потоків.
2.Велике і важке обладнання встановлюють на власних фундаментах, які спираються на грунт або закріплюються на етажерках, не з'єднаних жорстко з каркасом будівлі; це дає можливість реконструкції виробництва без руйнування будівлі
вцілому.
Обладнання повинно бути розташовано так, щоб була можливість проведення ремонтів без великих робіт із демонтажу обладнання(наприклад, для ремонту ферментерів повинне бути залишене місце для розміщення поруч двигуна, розібраної мішалки тощо).
3. Якщо обладнання складається з групи однакових одиниць апаратів, то ці групи об'єднують і розташовують в окремому ізольованому приміщенні(наприклад, групи ферментерів об'єднують у ферментаційне відділення, насоси - у насосне відділення, сепаратори - у сепараторне відділення тощо).
4.Сепаратори або центрифуги бажано розташовувати на І-му поверсі на окремих фундаментах і відокремлювати від інших приміщень капітальними звуконепроникливими мурами на усю висоту приміщення.
5.Приміщення для ферментерів за їх кількості 20 і більше доцільно розділити на 2 ряди і між ними розташувати інокулятори; за меншої кількості ферментерів доцільно відокремити інокулятори в спеціальному приміщенні, бажано з торця ряду ферментерів.
6.У ферментаційному відділенні доцільно встановлювати суцільне перекриття яа рівні 0.8 м нижче верхньої головки ферментера. Цей рівень регулюють або висотою оундаменту, або встановлюють суцільний робочий майданчик для обслуговування рерментерів.
7.Вентиляційне обладнання розташовують у торцях виробничих приміщень.
8.Великі сушарки розпилювального або пневматичного типу бажано розташоіувати на відкритих майданчиках, оскільки вони є особливо вибухонебезпечним обладнанням.
9. Стрічкові, барабанні, невеликі розпилювальні сушарки разом з іншим обладнанням із переробки вибухонебезпечних порошків(подрібнювачі, змішувально-фасувальне обладнання тощо), а також обладнання, в якому застосовують органічнічні легкозаймисті та вибухо- і пожежонебезпечні розчинники, розташовують у приміщеннях, що відносяться за вибухо- і пожежонебезпекою до класів В-ІІ або В-ІІа і мають перекриття або поверхні в стінах, що легко скидаються.
10.У приміщенні необхідно передбачати не менше двох виходів, розташованій
упротилежних кінцях.
11.Забороняється захаращувати обладнанням віконні прорізи .
12.У разі встановлення технологічного обладнання зовні будівлі рекомендується його розташовувати по торцях будівлі або навпроти глухих стін. Якщо це неможливо, то відстань між зовнішнім обладнанням та вікнами повинна бути не мен-
137
ше 12 м.
13. У розривах між зовнішньою етажеркою і будівлею можна розташовувати лише трубопровідну естакаду.
14. Бажано окремі апарати, в яких використовують природний газ або гас винести з приміщення. Якщо апарат ставлять навпроти вікна, то для будівель категорій А, Б, В ця відстань повинна бути більше 4 метрів, а для будівель Г, Д - більше 10м.
15.Виробнича площа відкритої установки, що стоїть окремо, висотою до 30 м не повинна перевищувати 5200 м2, а за висоти 30 м і більше - не повинна перевищувати 3000 м2. Якщо потрібна більша площа, то установку ділять на секції з відстанню між секціями не менше 15 м. Ширина зовнішніх установок висотою до 18 м не повинна перевищувати 42 м, а висотою більше 18 м - 46 м.
16.Технологічне обладнання із сильними кислотами та лугами розташовують у піддонах з бортом не менше 15 см.
17.Забороняється розташування обладнання з пожежо- і вибухонебезпечними, а також агресивними і токсичними речовинами, над і під допоміжними приміщеннями.
18.Стерильні приміщення відокремлюють глухою стінкою по всій висоті. В них дозволяється прохід тільки через тамбур, споряджений засобами для зберігання стерильності, наприклад, встановленням устаткування для створення підвищеного тиску стерильного повітря в тамбурі.
Проходи
1.Відстань від повздовжніх стін до апаратів реакторного типу повинна бути не менше 2 м або 1,2... 1,5 діаметра найбільшого з апаратів.
2.Ширина основних проходів в місцях, де постійно працюють - не менше 2 метрів.
3.Проходи між апаратами, а також між ними і стіною, повинні бути не менше 1 метра.
4.Прохід між апаратами, які потребують постійного обслуговування, -1,5 метра.
5.Проходи для огляду і регулювання приладів, між рядами насосів - не менше 0,8 метра.
6.Проходи між компресорами - не менше 1,5 метра.
7.Проходи біля віконних прорізів - не менше 1 метра.
8.Потрібно передбачати вільні місця для розбирання і чищення обладнання наприклад, сепараторів, ультрафільтрів тощо).
9.Центральні або основні проходи проектують прямими і вільними для людей
ітранспорту.
6.4. Деякі вимоги GМРдо будівельного проектування і компонування обладнаня
Упродовж останнього десятиріччя в Україні створена певна система контролю якості фармацевтичних препаратів, зокрема одержаних мікробіологічним методом.
138
Поштовхом для їїстворення стало прийняття в 1996 році Закону України „Про |
|
||||||
лікарські засоби", який регулює правові відносини, пов'язані з розробленням, |
|
||||||
державною реєстрацією, виробництвом, контролем якості і реалізацією |
|
||||||
лікарських засобів. |
|
|
|
|
|
|
|
У |
межах |
своїх |
повноважень |
керівництво |
цією |
роботою |
здійснюю |
Міністерство охорони здоров'я України і Державний комітет з медичної і
мікробіологічної |
промисловості (Держкоммедбіопром), які |
безпосередньо |
|
|||
підпорядковані Кабінету міністрів України. |
|
|
|
|||
Держкоммедбіопром |
скеровує |
роботу |
Державного |
наукового |
центру |
|
лікарських засобів, |
Державної інспекції |
за контролем якістю лікарських засобів, |
|
Фармакологічного і Фармакопейного комітетів; у склад останнього входить Лабораторія фармакопейного аналізу. При Міністерстві охорони здоров'я існує також Бюро реєстрації лікарських препаратів.
На всі ці органи згідно зі стратегією ВОЗ покладене важливе завдання забезпечувати гарантії якості продуктів медичного призначення.
Все ж для ліцензування ліків і міжнародного визнання високої якості фармацевтичних препаратів, які виробляють в Україні, і можливості постачання їх на міжнародні ринки, необхідно здійснювати проектування і виробництво лікарських засобів відповідно до вимог і стандартів Належної виробничої прак-
тики лікарських |
засобів(Good manufacturing practice for medicinal products - - |
GМР), яка прийнята Європейським Союзом у 1991 році. Вона вимагає створення |
|
і впровадження |
на кожному підприємстві, яке виробляє лікарські засоби, |
ефективної комплексної системи контролю якості ліків. До цієї роботи має залучатись не тільки дирекція, але і всі працівники підприємства.
Отже, відтепер необхідне поєднання національних заходів контролю якості ліків з вимогами GМР.
З 01.01.2002 року правила GMР стали в Україні обов'язковими.
Система якості базується на основних принципах та стандартах СМР і стосуються таких сторін виробництва лікарських засобів:
1.Управління якістю.
2.Персоналу.
3.Приміщень і обладнання.
4.Документації.
5.Виробництва.
6.Контролю якості.
7.Робіт за контрактом.
8.Рекламацій і відкликання продукції.
9.Самоінспекція.
Забезпечення якості - всеосяжне поняття, що охоплює всі питання, які окремо і загалом впливають на якість продукції.
Основний принцип вимог СМР, який стосується приміщень і обладнання (тобто питань будівельного проектування, вибору і компонування обладнання) полягає в тому, що «приміщення і обладнання належить розташовувати, проектувати , пристосовувати і експлуатувати таким чином, щоб вони повністю відповідали
операціям, які проводяться; їх розташування і конструкція повинні зводити ло
139
мінімуму ризик помилок і забезпечувати можливість ефективного очищення і обслуговування з метою запобігання перехресної контамінації, накопичення пилу чи бруду і взагалі будь-яких несприятливих факторів для якості продукції».
Під час проектування і будівництва необхідно дати обгрунтування розмірів будівлі , площі окремих виробничих і допоміжних приміщень.
Плануванняпримвщень здійснюють згідноз логічною послідовністю операцій технологічного процесу і належними рівнями чистоти.
Для зберігання і зважування вихідних і кінцевих виробництваантибіотиків , гормонів і сильнодіючих препаратів, а також продукції немедичного призначення повинно здійснюватись вокермих приміщеннях і на окремому обладнанні.
Приміщення різних класів чистоти повинні бути відокремлені одне від одного перегородками та повітряними шлюзами, а також передбачені заходи щодо забезпечення стерильності окремих приміщень.
Технологічне обладнання належить проектувати, розміщати і експлуатувати так, щоб воно використовувалось за прямим призначенням і не було небезпечним для продукції.
[11] с. 517-583
Запитаня для самоперевірки
1.Які основні принципи компонування обладнання?
2.Як вибирати будівлі для біотехнологічного виробництва?
3.Перелічте основні правила клмплнування обладнання ?
4.Охарактеризуйте вимоги GMP до будівельного проектування і компонування обладнання.
140
РЕКОМЕНДОВАНА ЛІТЕРАТУРА
Нормативно-технічна
1.ДСТУ 2424-94 “Промислова мікробіологія”
2.ДСТУ 2636-94 “Загальна мікробіологія”
3.ДСТУ 3803-98 “Біотехнологія. Терміни та визначення.”
4.РДМУ 64-080-87 Методические указания. Порядок составления и выдачи исходних данных на проектирование новых, расширение, реконструкцию и техническое перевооружение предприятий и производственных объектов медицинской и микробиологической промышленности. Москва: Министерство медицинской и микробиологической промышленности
СССР.
5.ГНД 09-001-98 Продукція медичної та мікробіологічної промисловості. Регламенти виробництва лікарських засобів. Зміст, порядок розробки, узгодження та затвердження.
6.ОСТ 64-043-87 Условные графические обозначения технологического оборудования, используемого в химико-фармацевтической промышленности.
7.Надлежащая производственная практика лекарственных средств / под ред. Н.А. Ляпунова, В.П. Георгиевского, Е.П. Безуглой - К.: МОРИОН, 1999. – 896 с.
8.ОСТ 42У-2-92. Продукция медицинской и микробиологической промышленности. Технологические регламенты производства.
9.ДБН А.2.2-3-97 “Проектування. Склад, порядок розроблення, погодження та затвердження проектної документації для будівництва”. – К.: Укрархбудінформ, 1997.
10.ДСТУ “Документація. Звіти в сфері науки і техніки. Структура і правила оформлення” ДСТУ 3008-95.
Базова
11. Сидоров Ю.І., Влязло Р.Й., Новіков В.П. Процеси і апарати мікробіологічної та фармацевтичної прормисловості.- Львів: Інтелект-Захід, 2008.- 736 с.
Допоміжна
12.Гартман Т.Н. Основы компьютерного моделирования химикотехнологических процессов: Учеб.пособие для вузов/ Т.Н. Гартман, Д.В. Клушин.-М.:ИКЦ «Академкнига», 2006.-416 с.
141