
Инструментальное оснащение технологических процессов металлообрабо
..pdf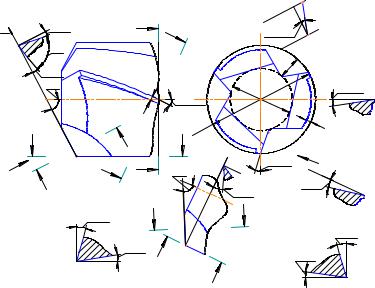
ваниями к шероховатости обрабатываемой поверхности, при обработке высокотвёрдых сталей, для конических или для комбинированных инструментов (зенкер - метчик и др.) зубья могут выполняться левыми, с углом наклона ω < 0. При этом стружка выходит из отверстия впереди зенкера, не ухудшая шероховатость обработанной поверхности, а осевая сила резания направлена к хвостовику.
N - N
γT
Vx |
|
|
b |
|
|
|
|
|
|
|
|
|
α |
|
|
|
|
f |
|
|
|
|
|
f |
|
|
S |
B |
N |
|
|
|
||
|
K |
|
A |
|
|
|
|
|
|
|
|
N |
M |
T |
|
|
|
|
α |
S-S |
R |
ïîï |
||
|
|
γïîï S' |
M
w > î
D
|
S |
f1 |
F |
B
A
K |
|
B |
|
|
l > î |
|
|
|
|
A |
|
|
h |
|
|
|
k |
|
|
d0 |
|
γïðîäT-T |
|
|
|
g |
|
|
B |
|
|
A |
|
F |
|
S'-S' |
l1>0 |
||
M-M |
|||
|
|||
|
|
||
a'ïîï |
|
γ2 |
|
|
|
||
R |
|
|
|
|
|
R-R α íñ |
|
|
|
γíñ |
S'
Рис.5.4. Геометрические параметры зенкера
Выбор инструментального материала режущей пластины осуществляется в зависимости от обрабатываемого материала и условий обработки (см. п. 5.1.2).
5.2.3. Назначение режимов резания при зенкеровании
Глубина резания при зенкеровании определяется как половина припуска по диаметру обработки отверстия. Предельные припуски при зенкеровании в зависимости от обрабатываемого материала и диаметра зенкера D приведены в табл.5.6.
111

|
|
|
Таблица 5 . 6 |
Значения предельных припусков при зенкеровании |
|||
|
|
|
|
Диаметр зенкера D, мм |
|
Припуск 2t |
|
|
Группа резания |
||
|
Р10, Р20, К, N |
|
Р30, Р40, Р50, M, S, H |
До 18 |
2,5…3,5 |
|
1,0…1,5 |
18…30 |
4,0…4,5 |
|
1,5…2,0 |
|
|
|
|
30…50 |
5,5…8,0 |
|
2,0…3,5 |
|
|
|
|
50…80 |
7,0…10 |
|
3,5…5,0 |
80…100 |
8,0…12 |
|
− |
Величина подачи при зенкеровании назначается в зависимости от прочностных характеристик обрабатываемых материалов и с учетом требований к параметрам шероховатости и точности обрабатываемых отверстий.
При зенкеровании рекомендуются три группы подач
(табл. 5.7).
Таблица 5 . 7
Группы подач при зенкеровании
Тип зенкера |
Условия обработки |
Группа |
|||
подачи |
|||||
|
|
|
|
||
|
|
|
Черновое зенкерование с точностью 13 квали- |
I |
|
Цилиндрический |
тета с последующей обработкой развертками. |
|
|||
зенкер |
из |
быстро- |
Зенкерование с получением Rа = 6,3…3,2 мкм |
II |
|
режущей стали |
под развертывание. |
|
|||
Зенкерование с точностью 10…12 - го квали- |
III |
||||
|
|
|
|||
|
|
|
тетов и Rа = 2,5…3,2 мкм |
|
|
Цилиндрический |
Черновое зенкерование. |
II |
|||
зенкер |
из |
твердого |
Зенкерование под нарезание резьбы и развер- |
III |
|
сплава |
|
|
тывание |
|
Рекомендуемая подача S 0 (мм) на оборот при зенкеровании определяется по формуле
S0 = S0 таб·KS d·KSM,
где S0 таб − табличное значение подачи (см. табл. 5.8);
KS d·KSM − поправочные коэффициенты соответственно на условия обработки и согласно группе резания обрабатываемого материала (см. табл. 5.9).
112
|
|
|
|
Таблица 5 . 8 |
|
Подачи S0 таб при зенкеровании |
|
||
|
|
|
|
|
Диаметр зенкера |
|
|
Группа подач |
|
D, мм |
|
I |
II |
III |
15 |
|
1,50 |
1,25 |
0,7 |
18 |
|
1,57 |
1,32 |
0,8 |
|
|
|
|
|
20 |
|
1,65 |
1,40 |
0,9 |
|
|
|
|
|
25 |
|
1,72 |
1,50 |
1,0 |
|
|
|
|
|
30 |
|
1,80 |
1,60 |
1,1 |
|
|
|
|
|
35 |
|
2,20 |
1,70 |
1,15 |
|
|
|
|
|
40 |
|
2,40 |
1,80 |
1,25 |
|
|
|
|
|
45 |
|
2,50 |
1,85 |
1,30 |
|
|
|
|
|
50 |
|
2,70 |
1,95 |
1,35 |
|
|
|
|
|
Таблица 5 . 9
Поправочные коэффициенты на подачу при зенкеровании
Отверстие |
|
Глухое |
|
|
Сквозное |
|
||
КS d |
|
0,5 |
|
|
|
1,0 |
|
|
Группы резания обраба- |
N |
N01 |
|
K |
P10, Р20, |
S, H |
S |
|
тываемого материала |
|
N10 |
|
|
P30 |
|
|
|
KS M при группе подач |
I |
1,0 |
0,83 |
|
0,57 |
0,40 |
0,36 |
0,27 |
II |
1,0 |
0,75 |
|
0,49 |
0,43 |
0,32 |
0,23 |
|
|
III |
1,0 |
0,87 |
|
0,52 |
0,45 |
0,36 |
0,23 |
Скорость резания, потребную мощность и машинное время при зенкеровании зенкерами, оснащенными твердым сплавом, можно определить по методике, изложенной в разделе 5.1.3 для процесса сверления, а также по рекомендациям [13, 16].
5.3. Развертывание
Процесс развертывания осуществляется режущим инструментом, который называется разверткой. Развертки – это осевые многолезвийные инструменты, которые используются для чистовой или получистовой обработки отверстий 6…8- го квалитетов точности и шероховатостью Rа 1,6…1,25 мкм.
Развертки не исправляют непрямолинейность оси предварительного отверстия, а копируют ее. Поэтому прямолинейность оси отверстия должна быть обеспечена на предшествующих технологических операциях.
113
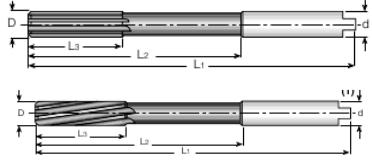
Выбор развертки для инструментального оснащения операции развертывания осуществляется соответственно следующему пошаговому подходу:
1.Выбор типа развертки.
2.Выбор геометрии и инструментального материала развертки.
3.Назначение режимов резания при развертывании.
5.3.1. Выбор типа развертки
По конструктивно-целевым признакам развертки делятся на следующие типы: машинные и ручные; цельные и сборные; цилиндрические и конические; стальные и твердосплавные; для обработки конструкционных сталей, легких сплавов, труднообрабатываемых материалов.
Внастоящее время для обработки заготовок из нержавеющих
ижаропрочных сталей и сплавов широко используются твердосплавные развертки, обеспечивающие высокие режимы резания и позволяющие снимать большие припуски по сравнению с быстрорежущими развертками.
Развертки цельные твердосплавные с цилиндрическим хвостовиком с прямыми и винтовыми канавками (ГОСТ 16086-70). Они
изготовляются диаметрами D = 3…10 мм; длиной рабочей части
L 3 = 12…20 мм и общей длиной L1 = 60…100 мм (рис.5.5).
а
б
Рис.5.5. Развертка цельная твердосплавная с цилиндрическим хвостовиком с прямыми канавками (а) и винтовыми (б)
Развертки с коническим хвостовиком с прямыми и винтовыми канавками (ГОСТ 16087-70) изготовляются диаметрами
114
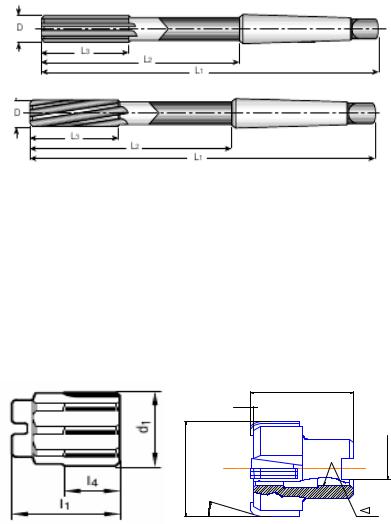
D = 6,5…12 мм; длиной рабочей части L3 = 18…22 мм и общей длиной L = 120…150 мм (рис.5.6).
а
б
Рис.5.6. Развертка цельная твердосплавная с коническим хвостовиком с прямыми канавками (а) и винтовыми (б)
Развертки насадные с напайными твердосплавными пластинами (ГОСТ 2832189) изготовляются диаметрами D = 25…80 мм; d = 13…32 мм; длиной рабочей части L3 = 22…32 мм и общей длиной l1 = 45…80 мм (рис. 5.7, а).
Развертки сборной конструкции (ГОСТ 11176-84) изготовляются диаметрами D = 52…300 мм; d = 22…80 мм; длиной рабочей части L3 = 25…58 мм и общей длиной l1 = 55…100 мм (рис. 5.7, б).
L |
1,6 |
|
D |
|
ϕ |
а |
б |
Рис.5.7. Развертки, оснащенные твердым сплавом, насадная (а) и сборная (б)
d
1:30
115
5.3.2.Выбор геометрии и инструментального материала развертки
Отличительным признаком как ручных, так и машинных разверток является геометрия режущей части. В основном используются развертки с прямыми зубьями, спиральные развертки с левыми винтовыми канавками и развертки с крутой спиралью (45°)
илевыми винтовыми канавками. Развертки с прямыми зубьями используют для обработки глухих отверстий, когда стружка должна отводиться по канавкам. Во всех остальных случаях обработки, особенно прерывистых пазов отверстий, используют развертки с левым направлением винтовых канавок, позволяющие отводить стружку вперед. Ими можно обрабатывать только сквозные отверстия или глухие, имеющие достаточно места для стружки.
Выбор инструментального материала режущей части разверток осуществляется в зависимости от обрабатываемого материала
иусловий обработки (см. глава 1, п. 1.5).
5.3.3. Назначение режимов резания при развертывании
Параметрами режима резания при развертывании являются: припуск на обработку, подача и скорость резания. Припуск под
развертывание принимают в среднем 0,15…0,25 |
мм на сторону |
||||
для черновых разверток и 0,05…0,12 мм для чистовых. |
|||||
При развертывании |
рекомендуются |
три |
группы подач |
||
(табл. 5.10). |
|
|
|
|
|
Таблица 5.10. Группы подач при развертывании |
|
|
|||
Тип развертки |
|
Условия обработки |
|
Группа |
|
|
|
подачи |
|||
|
|
|
|
|
|
|
Черновое |
развертывание |
с точностью 9-го |
|
|
Цилиндрические |
квалитета с последующей обработкой |
|
I |
||
Развертывание с точностью выше 9-го квали- |
|
||||
развертки |
тета с шероховатостью Ra = 1,25…0,63 |
|
II |
||
|
Чистовое развертывание с точностью 7-го |
|
|||
|
квалитета и Rа = 0,63…0,32 |
мкм |
|
III |
Рекомендуемая подача S 0 (мм) на оборот при развертывании определяется по формуле
S0 = S0 таб · KS d · KS M,
где S0 таб − табличное значение подачи (табл. 5.11);
116
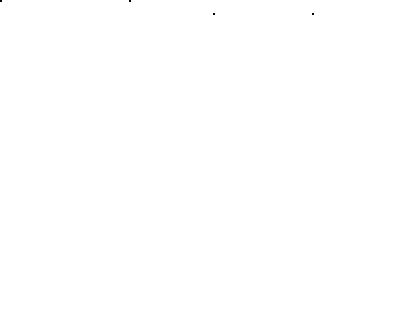
KS d · KS M − поправочные коэффициенты соответственно на условия обработки и соответственно группам резания обрабатываемого материала (табл. 5.12).
|
|
|
|
|
|
|
|
|
|
Таблица 5 . 1 1 |
||
Подачи S0 таб при развертывании |
|
|||||||||||
|
|
|
|
|
|
|
|
|
|
|
|
|
Диаметр развертки D, мм |
|
|
|
|
|
|
Группа подач |
|
|
|
||
|
I |
|
|
|
|
II |
|
|
III |
|||
|
|
|
|
|
|
|
|
|
||||
|
|
|
|
|
|
|
|
|
|
|
|
|
10 |
|
|
0,8 |
|
|
|
0,7 |
|
|
0,5 |
||
|
|
|
|
|
|
|
|
|
|
|
|
|
15 |
|
|
0,9 |
|
|
|
0,8 |
|
|
0,6 |
||
|
|
|
|
|
|
|
|
|
|
|
|
|
20 |
|
|
1,0 |
|
|
|
0,8 |
|
|
0,7 |
||
|
|
|
|
|
|
|
|
|
|
|
|
|
25 |
|
|
1,1 |
|
|
|
0,9 |
|
|
0,8 |
||
|
|
|
|
|
|
|
|
|
|
|
|
|
30 |
|
|
1,2 |
|
|
|
1,0 |
|
|
0,8 |
||
|
|
|
|
|
|
|
|
|
|
|
|
|
35 |
|
|
1,3 |
|
|
|
1,1 |
|
|
0,9 |
||
40 |
|
|
1,4 |
|
|
|
1,2 |
|
|
1,0 |
||
45 |
|
|
1,5 |
|
|
|
1,3 |
|
|
1,0 |
||
50 |
|
|
2,0 |
|
|
|
1,5 |
|
|
1,1 |
||
60 |
|
|
2,4 |
|
|
|
1,8 |
|
|
1,2 |
||
100 |
|
|
3,0 |
|
|
|
2,3 |
|
|
1,0 |
||
|
|
|
|
|
|
|
|
|
|
|
|
|
|
|
|
|
|
|
|
|
|
|
Таблица 5 . 1 2 |
||
Поправочные коэффициенты на подачу при развертывании |
||||||||||||
|
|
|
|
|
|
|
|
|
|
|||
Отверстие |
Глухое |
|
|
|
Сквозное |
|
||||||
KS d |
0,5 |
|
|
|
|
1,0 |
|
|||||
Группы резания обрабаты- |
N |
|
N01 |
|
K |
|
P10, Р20, |
S, H |
S |
|||
ваемого материала |
|
|
N10 |
|
|
|
P30 |
|
|
|
||
KS M при группе подач |
|
I |
2,64 |
|
1,6 |
|
2,0 |
|
1,0 |
1,0 |
0,5 |
|
II |
1,7 |
|
1,62 |
|
2,0 |
|
2,0 |
0,85 |
0,37 |
|||
|
III |
0,57 |
|
0,42 |
|
2,0 |
|
1,0 |
0,65 |
0,33 |
Скорость резания, потребную мощность и машинное время при развертывании развертками, оснащенными твердым сплавом, можно определить по методике, изложенной в разделе 5.1.3 для процесса сверления, а также по рекомендациям [13, 16, 21 и др.].
ГЛАВА 6. ФРЕЗЕРОВАНИЕ
Фрезы – это многозубые режущие инструменты, применяемые для предварительной и часто окончательной обработки плоскостей, фасонных, винтовых поверхностей, разрезки материалов. Точность обработки от 12 до 8-го (7-го) квалитетов, шероховатость Rа= 0,8...1,6 мкм. За один проход при фрезеровании снимается припуск до 5...8 мм, иногда до 12...20 мм.
В настоящее время для получения высоких результатов по производительности процесса фрезерования и стойкости фрез разработаны конструкции фрез, оснащенных СМП, которые практически вытеснили ранее широко применяемые фрезы с напайными твердосплавными пластинами.
Выбор режущего инструмента для фрезерной обработки осуществляется соответственно следующему пошаговому подходу:
1.Вид и схема фрезерования.
2.Выбор типа и конструктивных параметров фрезы.
3.Выбор конструктивных и геометрических параметров пластины и инструментального материала.
4.Назначение режимов резания при фрезеровании. Рассмотрим каждый шаг подробнее.
6.1. Вид и схема фрезерования
Фрезерованию подвергаются различные формы обрабатываемой поверхности (рис.6.1): 1 − плоские; 2 − плоские с уступом; 3 − уступы; 4 − открытые пазы; 5 − торцы; 6 − закрытые горизонтальные пазы; 7 − фасонные поверхности; 8 − узкие закрытые пазы; 9 − профильные канавки. Выбор способа обработки на многоосевом оборудовании позволил к традиционным операциям с использованием фрез добавить такие, как изготовление отверстий, обработка фасонных выборок, поверхностей вращения, резьбофрезерование и т.д.
Поэтому с точки зрения формы обрабатываемой поверхности и способа перемещения инструмента различают основные виды фрезерных операций: торцовое фрезерование (рис. 6.2, а), фрезерование уступов (рис. 6.2, б), фрезерование узких пазов (рис. 6.2, в), фрезерование фасонных и прямоугольных выборок (карманов) методом винтовой или круговой интерполяции с вре-
118
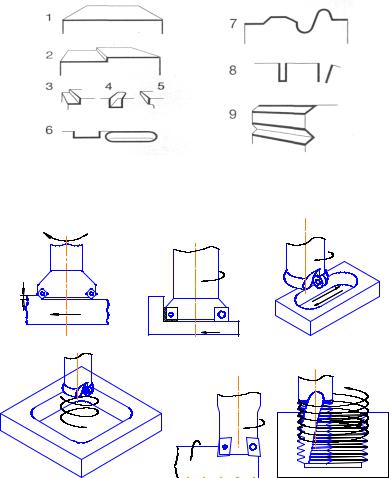
занием (рис. 6.2, г), фрезерование поверхностей вращения (рис. 6.2, д), резьбофрезерование (рис. 6.2, е) и т. д.
|
Рис.6.1. Виды поверхностей для фрезерования |
|
n,V |
|
|
|
|
n,V |
|
n,v |
S |
|
|
|
t |
|
|
S |
|
|
|
S |
|
а |
б |
в |
n,V
n,V
n,V
|
|
|
|
|
|
|
|
|
|
|
|
|
|
|
|
|
|
|
|
|
|
|
|
|
|
|
|
|
|
|
|
|
|
|
|
|
|
|
|
|
|
|
|
|
|
|
|
|
|
|
|
|
|
|
|
|
|
|
|
|
|
|
|
г |
|
|
|
|
д |
е |
Рис.6.2. Виды фрезерных операций: а − торцовое фрезерование; б − фрезерование уступов; в − фрезерование узких пазов; г − фрезерование
карманов; д − фрезерование поверхностей вращения; е − резьбофрезерование
119
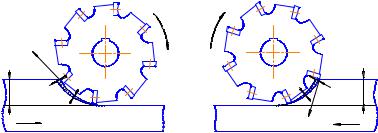
Существуют две различные схемы фрезерования, определяемые направлением движения заготовки относительно инструмента. Их различие заключается в условиях входа и выхода зубьев фрезы из резания.
Встречное фрезерование (рис.6.3, а) наиболее распространено, при нем направление подачи заготовки и направление вращения фрезы являются противоположными. Толщина среза начинается с нуля и возрастает до максимума при выходе зуба в конце резания.
n,V |
n,V |
|
|
_ |
|
|
|
V |
|
|
|
amax |
|
amax |
t |
t |
ai |
|
|
|
|
||
ai |
_ |
|
|
S |
V |
|
S |
а |
б |
|
|
Рис.6.3. Встречное (а) и попутное (б) фрезерование
При встречном фрезеровании зуб фрезы начинает работу с нулевой толщины среза, что вызывает скольжение зуба по обрабатываемой поверхности, возникают большие силы трения, резко возрастает температура в зоне резания. Увеличивающаяся нагрузка на зуб от силы резания, действуя на заготовку, как бы «отрывает» ее от стола станка, что вызывает вибрации технологической системы и ухудшает шероховатость обработанной поверхности.
Кроме того, каждый последующий зуб работает по наклепанной поверхности, образованной предыдущим зубом, так как существует начальное скольжение зуба при нулевой толщине среза. Другими словами, скольжение зуба по обработанной поверхности будет происходить до тех пор, пока толщина среза не станет больше радиуса закругления режущего лезвия.
При попутном фрезеровании (рис.6.3, б) направление подачи заготовки совпадает с направлением вращения фрезы. Резание начинается с максимальной толщины среза, который уменьшается до нулевого значения при выходе зуба из зоны фрезерования. Это помогает избежать скольжения зуба по обработанной поверхности, соответственно, облегчается процесс резания, выделяется меньшее
120