
3016
.pdf
Сборник научных статей аспирантов и аспирантов-стажеров
готовлении передачи. Подрезание зуба колеса приводит к уменьшению толщины зуба, что уменьшает нагрузочную способность передачи, и изменению угла наклона зуба, что уменьшает пятна контакта и увеличивает время приработки.
Для передач со стальным венцом колеса особенно критична проблема изменения угла наклона зуба, так как это явление увеличивает время приработки в десятки раз по сравнению с передачами с бронзовым венцом из-за большой твердости рабочих поверхностей.
Для того что бы определить форму зуба колеса на этапе проектирования, необходимо использовать современные программы для трехмерного моделирования, которые позволяют получить геометрическую модель, соответствующую виду готовой передачи, и использовать ее для исследовательских и конструкторских задач.
Трехмерная модель строится на основе данных полученных в результате математических вычислений, недостающие для построений данные определяются с использованием возможностей программы. Основную сложность представляет моделирование зуба колеса, из-за отсутствия математического описания его формы.
Получение точной геометрической модели позволит создать алгоритм расчета зуба спироидного колеса, производить прочностные расчеты и исследовать влияние формы и положения червяка на геометрию спироидного колеса.
Для устранения подрезания необходимо обеспечить условия, при которых в срезании металла с поверхности колеса участвовало только нормальное сечение витков фрезы. Единственно верного способа устранить подрезание не существует, так как это явление зависит от комплекса параметров: межосевого расстояния передачи, диаметра червяка, углов наклона правой и левой сторон витка червяка, диметра венца колеса.
В ходе работы были разработаны алгоритм и программа расчета, обеспечивающие корректировку параметров производящего червяка для уменьшения или полного исключения подрезания зубьев спироидного колеса.
Проблемы моделирования геометрии рабочей поверхности зуба колеса
Так как данные, полученные в ходе расчета, не описывают форму боковой поверхности зубьев колеса, то принято решение ис-
51
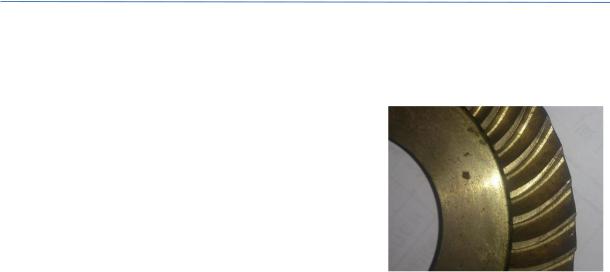
Наука и молодежь СГУПСа в третьем тысячелетии
пользовать программы трехмерного моделирования для построения их реальной геометрии. Обоснование использования средств трехмерного моделирования изложено ранее.
Две основные проблемы при моделировании зуба колеса, это определение его профиля, так как в большинстве случаев толщина зуба изменяется по мере удаления от оси колеса (рис. 1), и нахождение траектории по которой он нарезается.
Сложная форма зубьев колеса обусловлена особенностями расположения звеньев передачи в пространстве и сложностью процессов формирования зубьев колеса. Траектория перемещения боковой поверхности витка червяка по поверхно-
сти зуба колеса является суммой перемещений червяка и колеса, при этом обороту червяка соответствует поворот колеса на угол меньший в u раз. Пятна контакта при этом перемещаются поступательно вдоль оси червяка. Расчет процесса огибания наиболее сложный и важный этап для проведения построений и исследований.
Профиль зуба колеса в зависимости от формы и расположения инструмента может по мере удаления от оси колеса утолщаться или утончаться, а в некоторых случаях, при ошибках проектирования, его поверхность может срезаться полностью уже при изготовлении передачи. Изменение профиля зуба колеса происходит из-за дополнительного подрезания поверхностью витка, удаленной от нормального сечения фрезы. Интенсивность подрезания возрастает при увеличении расстояния от оси фрезы до зоны срезания металла. Для диагностики интенсивности подрезания необходимо наличие модели колеса и червяка.
Моделирование процесса огибания витками червяка боковых поверхностей зубьев колеса
Для более детального исследования зависимости формы и расположения фрезы на геометрию зубьев колеса, необходимо наличие точной модели передачи, что требует алгоритма, позволяющего определять взаимные перемещения точек элементов передачи и, следовательно, найти траекторию перемещения поверхности винтовой линии червяка по поверхности колеса при работе передачи.
52
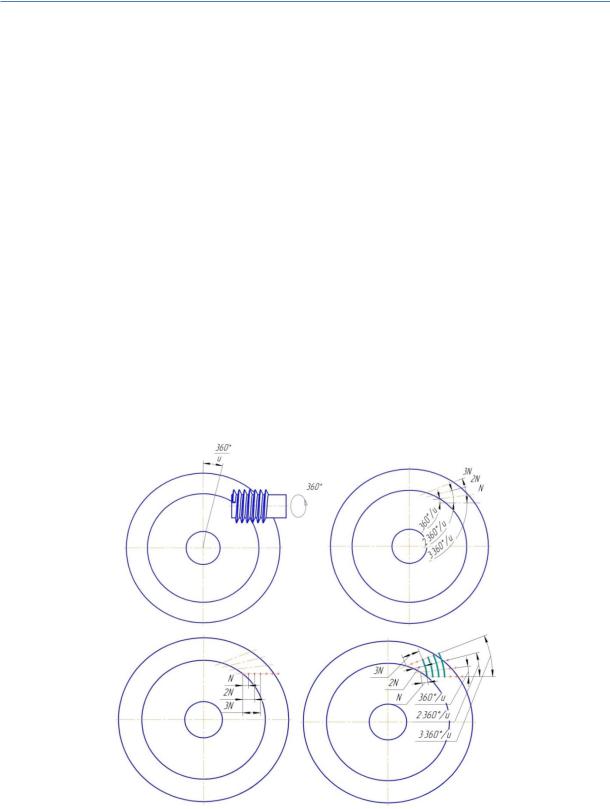
Сборник научных статей аспирантов и аспирантов-стажеров
Для упрощения математических расчетов и процесса моделирования, построения эскизов для нахождения траектории витка червяка также осуществляется в программе трехмерного моделирования.
За основу построений принято условие, что червяк вращается быстрее колеса в u раз, т.е. на каждый оборот червяка колесо поворачивается на 360 ͦ/u (рис. 2, а). Таким образом, можно рассчитать поворот колеса при любом количестве оборотов червяка, например, за три оборота – N (рис. 2, б). Данное условие справедливо для всех типов спироидных передач с одно, двух и многозаходными червяками.
Также известно, что за один оборот червяка винтовая линия смещается на определенное расстояние, равное ее шагу. Шаг линии определяется при расчетах геометрии червяка отдельно для каждой передачи. Это дает возможность найти величину смещения пятна контакта вдоль оси червяка при его повороте на любой угол. Для удобства за точку начала отсчета шага винтовой линии принимают точку пересечения внутреннего венца колеса и оси червяка (рис. 2, в).
|
|
б) |
а) |
|
|
|
|
|
|
|
|
|
|
г) |
|
в) |
|||
|
|
||
|
|
||
|
|
|
Рис. 2. Построения при нахождении траектории огибания:
а– схема взаимодействия червяка и колеса; б – траектория перемещения червяка при условно неподвижном колесе; в – нахождение координат
вершин витков червяка в нормальном сечении; г – определение траектории витка червяка, по поверхности колеса
53
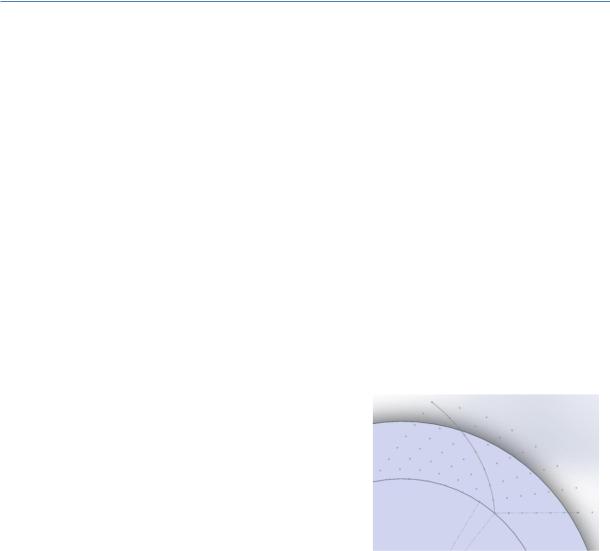
Наука и молодежь СГУПСа в третьем тысячелетии
Таким образом, для нахождения траектории огибания червяка, необходимо отложить между внутренним и внешним диаметрами венца колеса вдоль оси червяка, количество точек, соответствующее числу заходов винтовой линии инструмента. Скопировав полученный набор точек на угол 360 ͦ/u, получаем координаты вершин витков после совместного перемещения червяка и колеса (рис. 2, г). Продолжать построения необходимо число раз, равное числу точек, вместившихся между внутренним и внешним диаметрами венца колеса. Соединив последовательно первую точку начального графика со второй точкой последующего, вторую с третьей и т.д. получаем приближенную траекторию смещения пятна контакта передачи в нормальном сечении червяка (рис. 3). Для увеличения точности построений, необходимо производить построения при неполных оборотах червяка, либо вывести данные зависимости в формулы и построить по ним график перемещений.
Однако, так как за ось построений принято сечение червяка, найденная траектория описывает перемещения только нормального сечения витка червяка. Для нахождения траектории перемещений в зоне внедрения витка червяка в поверхность колеса, необходимо с учетом угла наклона винтовой линии найти координату точки характерной для данного явления, провести новую ось, параллельную оси червяка и производить построения по методике указанной выше. Пере-
сечение кривой, полученной в ходе дополнительных построений траектории нормального сечения витка, свидетельствует о наличии дополнительного изменения геометрии зуба колеса, о подрезании. Таким образом, имеется возможность оценки величины подрезания графическим методом.
В дальнейших построениях в программах трехмерного будет использоваться только траектория нормального сечения витка червяка, так как это упрощает моделирование, позволяет более наглядно оценить величину подрезания и дает широкие возможности для модификации изготавливающего инструмента.
54
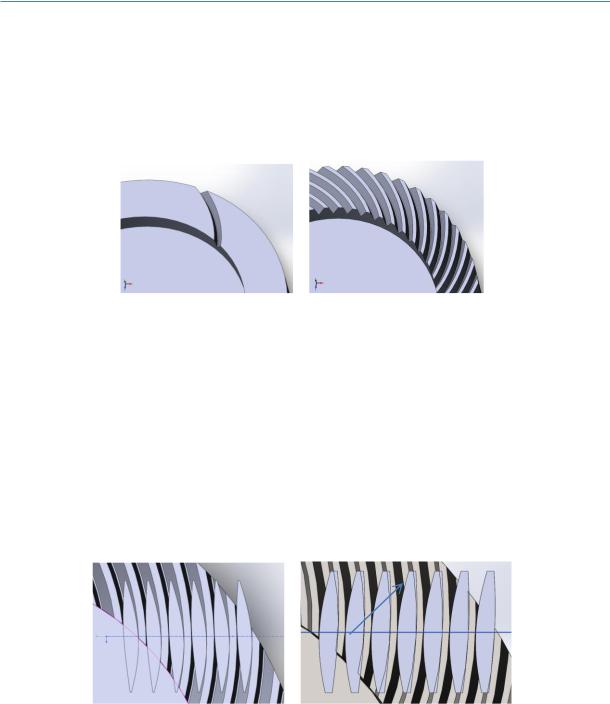
Сборник научных статей аспирантов и аспирантов-стажеров
Вырез профиля витка червяка по траектории его перемещения (рис. 4, а), дает элемент геометрии, копировав который относительно оси колеса число раз равное числу зубьев колеса, получается модель колеса, при изготовлении которого был исключен фактор подрезания
(рис. 4, б).
а) |
б) |
Рис. 4. Моделирование колеса без учета подрезания:
а – вырез по траектории профиля витка червяка; б – модель колеса
Приведя в зацепление с червяком созданную таким образом модель колеса, становится видна степень внедрения витков червяка в боковую поверхность зуба колеса (рис. 5). Так по рис. 5, б можно измерить степень утончения зуба при изготовлении передачи, оценить с какой стороны зуб колеса подвергается наибольшему подрезанию и прогнозировать смещение пятна контакта относительно оси червяка.
а) |
б) |
Рис. 5. Сечение червяка по поверхности зуба колеса
вразличных передачах:
а– пример передачи без подрезания зубьев; б – пример интерференции поверхностей элементов передачи приводящей к подрезанию зубьев
Способы регулирования интенсивности подрезания зубьев
Созданные трехмерные модели, позволяют оперативно изменять параметры передачи и отслеживать их влияние на величину подрезания, что в разы упрощает процесс поиска «идеального зацепления», для передачи с любыми параметрами. Для создания
55
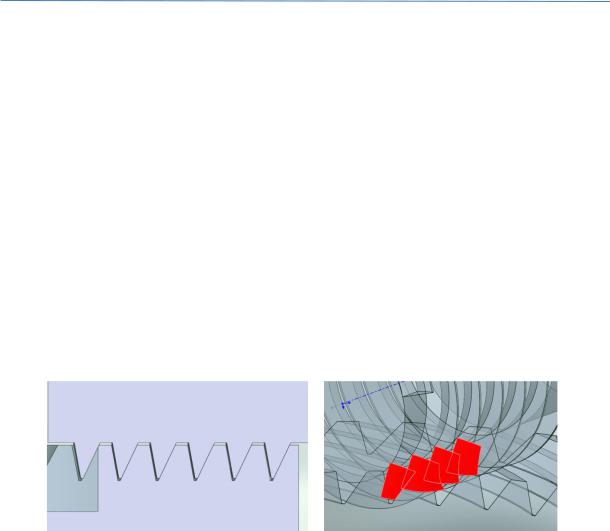
Наука и молодежь СГУПСа в третьем тысячелетии
«идеального зацепления» необходимо и достаточно, чтобы в процессе формировании зуба колеса участвовало только нормальное сечение витка фрезы. Признаками «идеального зацепления» являются: одинаковая толщина и наклон зуба по всей его длине, отсутствие интерференции боковой поверхности зубьев с червяком (см. рис. 5, а), равномерный контакт зубьев колеса и витка червяка в каждом сечении (рис. 6, а), равномерное распределение пятен контакта во всех полностью контактирующих парах (рис. 6, б).
В ходе исследований было выявлено четыре способа изменения геометрии зуба колеса, влияющих на величину подрезания:
–изменением межосевого расстояния;
–изменением диаметра венца колеса;
–изменение диаметра червяка;
–изменение угла наклона профиля винтовой линии фрезы.
а) |
б) |
Рис. 6. Признаки идеального зацепления:
а – контакт зубьев колеса и витков червяка; б – пятна контакта передачи
Межосевое расстояние – один из входных параметров для расчета передачи, под него с помощью эмпирических коэффициентов подбирается диаметр и ширина венца колеса. Наружный диаметр колеса ограничен только габаритами передачи и его увеличение практически не влияет на геометрию зацепления, в то время как уменьшение внутреннего диаметра венца, приводит к увеличению интенсивности подрезания у основания зуба колеса, что увеличивает пятно контакта в первой паре и уменьшает его в последующих парах зацепления (см. рис. 6, б). Неравномерная нагрузка на витки червяка увеличивает его износ, большая нагрузка на зуб, особенно в ослабленной зоне, возникшей из-за уменьшения сечения при подрезании, увеличивает вероятность его излома. Таким образом, при контроле размеров колеса, основное внимание необходимо уделять внутреннему диаметру венца. Изменение межосевого расстояния возможно только
56
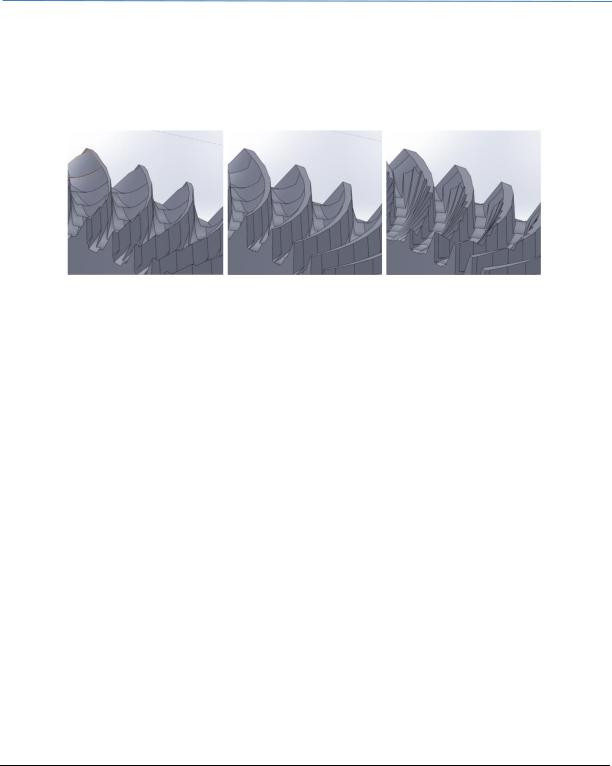
Сборник научных статей аспирантов и аспирантов-стажеров
в узких пределах (рис. 7), и необходимость в ней возникает только при значительных, обусловленных конструктивно изменениях диаметра колеса или ширины венца, для нахождения величины соответствующей зубу колеса оптимальной толщины.
aw > aw ном |
aw = aw ном |
aw< aw ном |
Рис. 7. Влияние изменения межосевого расстояния на геометрию зуба колеса
Диаметр червяка также влияет на интенсивность подрезания. Так уменьшение диаметра положительно влияет на геометрию зацепления, однако это в свою очередь снижает его ресурс, максимальный вращающий момент и увеличивает его изгиб при работе передачи.
Изменение угла наклона профиля винтовой линии фрезы, самый простой способ оптимизировать геометрию зацепления. Так увеличение углов наклона профиля винтовой линии значительно уменьшает интенсивность подрезания, однако приводит к увеличению радиальных нагрузок на подшипники червячного узла. Малый угол наклона зуба колеса способствует нагнетанию смазки в зацепление, что очень важно при продолжительной работе передачи.
Таким образом, единственно верного способа решить проблему создания идеального зацепления спироидной передачи не существует, так как геометрия передачи зависит от комплекса параметров и требует рассмотрения в каждом случае проектирования передачи.
Научный руководитель канд. техн. наук, доц. В.Ю. Игнатюгин
57

Наука и молодежь СГУПСа в третьем тысячелетии
А.А. Денисова
(аспирант кафедры «Физика»)
Получение алюмонитридных изделий методом литья на основу
При изготовлении алюмонитридных изделий используют различные способы формования, а именно: осевое двухстороннее прессование, осевое двухстороннее прессование с использованием ультразвука, горячее прессование, коллекторное прессование, инжекционное формование, прессование-спекание с использованием спарк-плазмы (SPS), литье термопластичных шликеров и литье на основу. Производство тонких теплопроводящих пластин из алюмонитридной керамики, применяемых в полупроводниковых приборах, возможно только методом литья на основу. Применение технологии литья керамической ленты на основу имеет много преимуществ перед традиционными технологиями производства керамических подложек: производительность технологического оборудования при литье керамической ленты на основу в десятки раз больше, чем на оборудовании для изостатического прессования, горячего прессования, инжекционного литья и литья термопластичных шликеров; энергопотребление в несколько раз меньше; практически полностью отсутствуют сложные и трудоемкие процессы механической обработки (шлифование по плоскости и по контору и т.д.); технология пленочного литья дает возможность изготовления подложек толщиной 100 мкм; технология пленочного литья на основу обеспечивает изготовление многослойных корпусов на основе нитрида алюминия; применение технологии пленочного литья дает возможность группового изготовления подложек картами 165×165 мм, а также, некоторых типов корпусов для полупроводниковых приборов (до нескольких сотен с одной пластины); групповой метод позволяет проводить автоматизированный контроль основных параметров и отбраковку.
К характеристикам, ограничивающим применение процесса, можно отнести максимальную толщину подложек до 1,5 мм обусловленную изостатическим замоноличеванием стеков и резкой на заготовки.
При использование данного метода необходимо разработать состав шликера, подобрав совместимые по литейным свойствам
58

Сборник научных статей аспирантов и аспирантов-стажеров
компоненты. Существует два вида шликера: водный и органический. Так какнитрид алюминия (AlN) взаимодействует с водой, в настоящей работе при литье керамической пленки на основу использован шликер с органической связкой. Использование шликера на органической основе позволяет получить более устойчивую суспензию и пластичную ленту после сушки.
Основная цель процесса приготовления шликера заключается в том, чтобы перемешать порошок с растворителем, связкой, пластификатором и диспергатором и получить шликер с заданными реологическими характеристиками (вязкость). Для выбора состава шликерарассматривали следующие компоненты:
органические связующие: поливинилбутираль (ПВБ), поливиниловый спирт (ПВС) и поливинилацетат (ПВА);
пластификаторы: дибутилфталат (ДБФ), диоктилфталат (ДОФ), полиэтиленгликоль (ПЭГ) и глицерин;
растворители: ацетон, этиловый спирт, толуол, изобутиловый спирт, метилэтилкетон, азеотропная смесь толуол/этиловый спирт, орто-ксилол/этиловый спирт, МЕК/толуол, МЕК/этиловый спирт, МЕК/изопропиловый спирт.
Связка служит для получения сырой керамической ленты. Связка образует некую сетку, которая соединяет всю химическую систему вместе на время всего технологического процесса. Также можно сказать, что сырая керамическая лента – это полимерная матрица с большим количеством керамического порошка. Связка придает керамической ленте гибкость, прочность, пластичность, гладкость, твердость [1].
Количество связующего компонента должно находиться в определенных пределах, поскольку это влияет на качество керамики (наличие пор, прессуемость, температурная кривая удаления связки, геометрические размеры изделия).
Выбор связующего компонента зависит от состава шликера (растворитель, керамический материал), температурного графика (режима) выгорания, размера исходных частиц порошка [1].
59
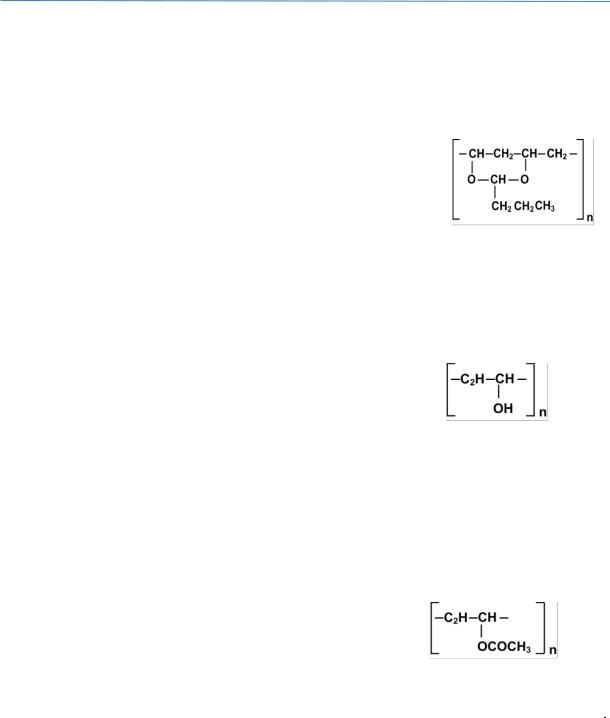
Наука и молодежь СГУПСа в третьем тысячелетии
Таблица 1
|
|
|
Поливинилбутираль ПВБ |
|
|
||
|
|
|
|
|
|
|
|
Показатели |
|
|
Значения показателей |
|
Химическая |
||
|
|
|
формула |
||||
|
|
|
|
|
|
|
|
Степень полимер |
|
|
500–1600 |
|
|
||
Плотность, кг/м3 |
1100 |
|
|
|
|
||
|
|
В спиртах, кетонах, слож. эфирах, |
|
||||
Растворим |
|
|
хлор. углеводородах, этанола |
|
|||
|
|
|
с бензолом |
|
|
||
Не растворим |
|
|
В бензине, диэтиловом эфире |
|
|||
|
|
|
|
|
|
|
Таблица 2 |
|
|
|
Поливиниловый спирт ПВС |
||||
|
|
|
|
|
|
|
|
Показатели |
|
|
Значения показателей |
|
Химическая формула |
||
Степень полимер |
|
|
500–5000 |
|
|
|
|
Плотность, кг/м3 |
|
|
1270–1300 |
|
|
|
|
Растворим |
|
|
В воде |
|
|
|
|
Не растворим |
|
|
В органических |
|
|
|
|
|
|
растворителях |
|
|
|
||
|
|
|
|
|
|
||
|
|
|
|
|
|
|
Таблица 3 |
|
|
|
Поливинилацетат ПВА |
|
|
||
|
|
|
|
|
|
||
Показатели |
|
|
Значения показателей |
|
Химическая формула |
||
Степень полимер |
|
|
1800–2000 |
|
|
|
|
Плотность, кг/м3 |
|
|
1100–1200 |
|
|
|
|
|
|
|
В уксусной кислоте, |
|
|
|
|
Растворим |
|
|
ацетоне, метаноле, |
|
|
|
|
|
|
этилацетате, бензоле, |
|
|
|
|
|
|
|
|
|
|
|
||
|
|
|
метилен-хлориде |
|
|
|
|
Не растворим |
|
В бензине, минеральных |
|
|
|
|
|
|
|
маслах |
|
|
|
|
|
|
|
|
|
|
|
В результате экспериментальных исследований было выявлено, что наиболее оптимальным является использование поливинилбутираля (ПВБ), так как для его удаления требуется плавный режим обжига.
Пластификатор используется для получения гибкой ленты, т.е. сырая пленка может деформироваться без трещин. Это достигается за счет того, что пластификатор окружает молекулы полимера
60