
3016
.pdf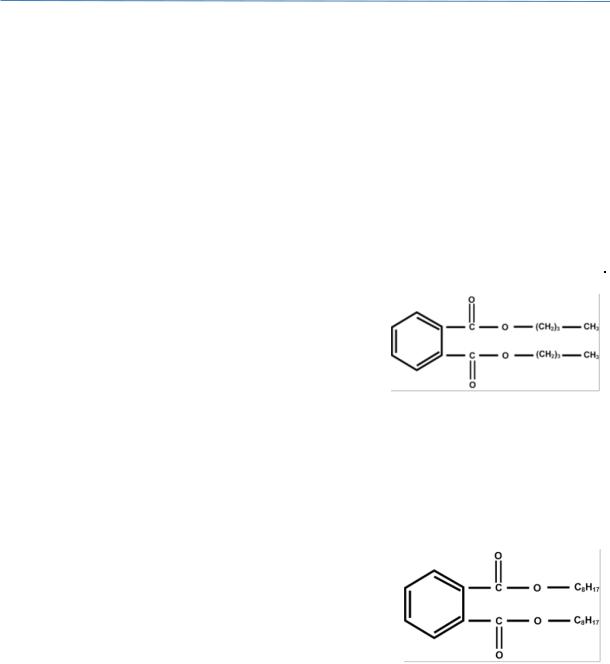
Сборник научных статей аспирантов и аспирантов-стажеров
и удерживает их на расстоянии, причем это расстояние может изменяться в определенных пределах.
Пластификатор должен соответствовать следующим требованиям: совместимость с полимером связки; высокая температура кипения и низкое давление пара; высокая эффективность придания пластичности; химическая и термическая стабильность; придание пластичности при низких температурах [2].
|
|
|
|
Таблица 4 |
|
|
Дибутилфталат ДБФ |
|
|
|
|
|
|
|
Показатели |
|
Значения показателей |
|
Химическая формула |
|
|
|
|
|
Внешний вид |
|
Прозрачная жидкость |
|
|
без механических примесей |
|
|
||
|
|
|
||
Плотность, кг/м3 |
1050 |
|
|
|
Растворим |
|
В органических |
|
|
|
растворителях |
|
|
|
|
|
|
|
|
Малорастворим |
|
В воде |
|
|
|
|
|
|
|
|
|
|
|
Таблица 5 |
|
|
ДиоктилфталатДОФ |
|
|
|
|
|
|
|
Показатели |
|
Значения показателей |
|
Химическая формула |
|
|
|
|
|
|
|
Бесцветная или слегка |
|
|
|
|
желтоватая прозрачная |
|
|
Внешний вид |
|
маслянистая жидкость |
|
|
|
|
со слабым фруктовым |
|
|
|
|
запахом |
|
|
Плотность, кг/м3 |
|
980 |
|
|
Растворим |
|
В органических |
|
|
|
растворителях |
|
|
|
|
|
|
|
По результатам анализа научно-технической литературы и патентов [3–6] в качестве пластификатора выбран пластификатор – дибутилфталат.
Растворитель для органической фазы требуется только на начальной стадии процесса изготовления листового керамического материала. Растворитель позволяет быстрее смешать компоненты органической фазы, получить органическую фазу нужной вязкости для более полной гомогенизации с порошками керамического
61

Наука и молодежь СГУПСа в третьем тысячелетии
наполнителя, придать керамической композиции текучесть, что делает возможным формирование листового материала.
В качестве растворителей могут быть использованы: этанол, толуол, метилэтилкетон, ксилен и др.
Компоненты шликера должны быть подобраны таким образом, чтобы они растворялись в сольвенте (растворителе).
Есть множество плюсов в использовании бинарного растворителя:
растворимость компонентов шликера различна в каждом сольвенте;
возможность контроля скорости высыхания ленты;
возможность контролирования реологических свойств шликера.
|
|
|
|
|
Таблица 6 |
Характеристики растворителей |
|
|
|||
|
|
|
|
|
|
|
|
Характеристики |
|
||
Растворитель |
Совмести- |
|
ПДК, |
T кип., |
Стои- |
мость |
|
мость |
|||
|
|
мг/м3 |
°С |
||
|
с ПВБ, ДБФ |
|
р./л |
||
|
|
|
|
||
Толуол |
нет |
|
50 |
110 |
60 |
МЭК |
да |
|
200 |
79,6 |
130 |
Ортоксилол |
нет |
|
50 |
144,9 |
87 |
Этиловый спирт |
да |
|
1000 |
78,39 |
200 |
Изопропиловый спирт |
нет |
|
10 |
82,4 |
– |
МЭК/этанол (60/40) мас. % |
да |
|
200 |
75 |
158 |
Толуол/этанол (32/68) мас. % |
да |
|
50 |
77 |
155 |
Исходя из анализа свойств в качестве растворителя была определена азеотропная смесь толуол/этанол (32/68) мас. %.
Требования, предъявляемые к материалам для приготовления алюмонитридногошликера:
–керамический порошок должен содержать около 100 % основного материала, кислорода не более 0,2 %, гранулометрический состав d = 50 менее 1 мкм и обеспечение заданных электро- и теплофизических свойств;
–органическая связка и пластификатор должна иметь совместимость с растворителем и пластификатором, температура удаления
62
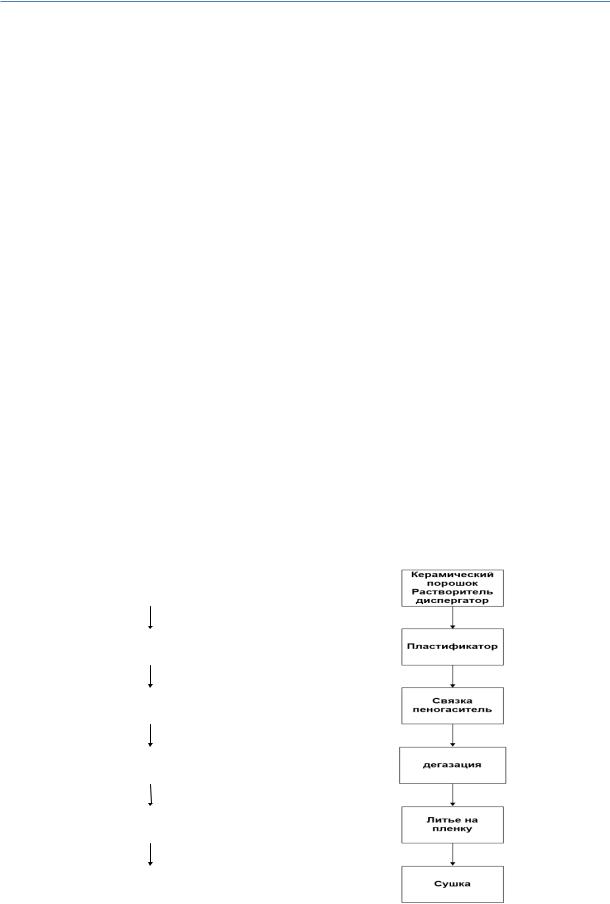
Сборник научных статей аспирантов и аспирантов-стажеров
должна быть ниже температуры окисления порошка нитрида алюминия и иметь хорошее связующие и пластифицирующие свойства;
– растворитель должен иметь совместимость с органической связкой и пластификатором, не взаимодействовать с порошком нитрида алюминия и легко удаляться из керамической ленты.
Проанализировав все требования к материалам и исследовав порошки AlN зарубежного и отечественного производства был выбран порошок AlN японской производства и спекающая добавка Y2O3, подходящие по совместимости свойств органическая связка ПВБ, пластификатор ДБФ и растворитель этанол/толуол. Из выбранных материалов опробованы составы с различным процентным соотношением компонентов, по качеству отлитого шликера и его реологическим свойствам определены процентные соотношения компонентов состава.
Процесс приготовления шликера осуществляется в 2 этапа. На первом этапе готовят суспензию керамического порошка с растворителем и диспергатором, на втором этапе происходит приготовление самого шликера, то есть смешение суспензии из порошка сорганической связкой и пластификатором. Данный состав шликера изготавливали при разной последовательности введения компонентов рис. 1.
Способ 1 |
Способ 2 |
Керамический
порошок
Растворитель
диспергатор
Связка
Пластификатор
пеногаситель
Вакуумирование
Литье на пленку
Сушка
Рис. 1. Способы приготовления алюмонитридногошликера
63
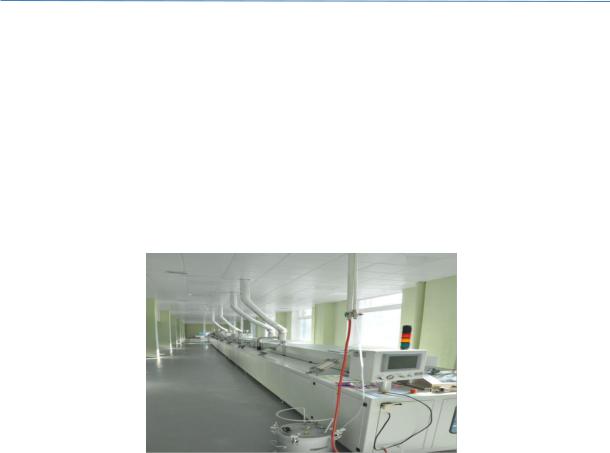
Наука и молодежь СГУПСа в третьем тысячелетии
При приготовление шликера по способу 1 (рис. 1) на керамической ленте наблюдались дефекты: трещины и пузыри, когда изменили последовательность введения связки и пластификатора, способ 2 (рис. 1), керамическая лента отлилась без дефектов. Также на качество керамической ленты влияла стадия дегазации шликера, режимы, заданные при литье шликера: скорость движения ленты, зазор ножа и температуру зон сушки.
Подготовленный отвакуумированныйшликер отливали на литьевой машине (рис. 2).
Рис. 2. Линия литья керамической ленты КЕКО
Основная цель процесса отливки – это получение сырой керамической ленты с заданными параметрами (толщина, гибкость) табл. 7.
Таблица 7
Характеристики шликера и керамической лента из нитрида алюминия
Наименование сырья, |
Наименование показателей |
Значения |
||
|
материалов |
|||
|
для проверки |
показателей |
||
|
полупродуктов |
|||
|
|
|
||
1. |
Шликер |
Вязкость, сПа∙с |
85–90 |
|
Плотность, г/см3 |
1,400±0,002 |
|||
|
|
|||
2. |
Керамическая лента |
Толщина, мм |
0,63± 0,04 |
Отливку приготовленного шликера проводили на литьевой машине производства фирмы KEKO. Шликер загружался в приемный бункер для шликера. В течение 30 мин прогревали машину для установления заданных температур согласно заданному режиму на участках сушки в первой и второй зоне. Выставляли необходимую тол-
64
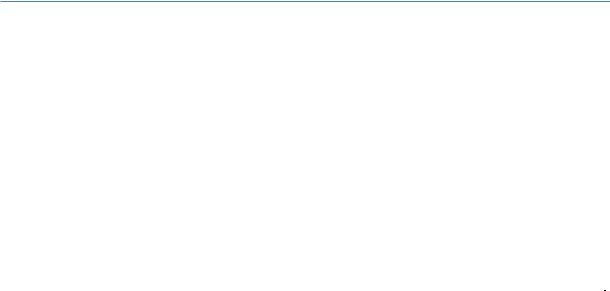
Сборник научных статей аспирантов и аспирантов-стажеров
щину будущей керамической ленты, с помощью микровинтов и микрометров. После чего запускали транспортерную ленту, выставляя скорость движения ленты согласно заданному режиму. Затем отрывали кран и подавали шликер в литьевую коробку.
Захваченный транспортной лентой шликер вытягивался в керамическую ленту и продвигался от первой зоны сушки к второй, затем попадал в третию более нагретую зону. Режим, используемые при отливки керамической ленты из нитрида алюминия представлены в табл. 8.
|
|
|
|
|
|
|
Таблица 8 |
||
Режимы литья керамической ленты из нитрида алюминия |
|
||||||||
|
|
|
|
|
|
|
|
|
|
Тол- |
Скорость |
Температура сушки |
|
Температура |
|
||||
щина |
движения |
по зонам, ° С |
воздуха по зонам, °С |
||||||
ленты, |
транспортерной |
1 |
2 |
3 |
1 |
|
2 |
|
3 |
мм |
ленты, м/мин |
|
|
||||||
|
|
|
|
|
|
|
|
||
0,8 |
0,5 |
20 |
25 |
30 |
20 |
|
22 |
|
25 |
После прохождения керамической ленты через все зоны сушки она наматывалась вместе с транспортерной лентой на бобину лентоприемника. После чего срезалась и направлялась на стадию нарезки для получение заготовок заданных размеров с учетом последующей усадки в процессе спекания. Резка осуществляется с помощью резака гильотинного типа на столике, снабженном механизмом перемещения ленты и измерительной шкалой. Нарезанные заготовки подложек передавали на удаления органической связки – медленное и мягкое удаление связующего из материала, без деформации изделий.
Процесс удаления органической связки идет на воздухе (окислительная атмосфера). В муфельной печи с задатчиком скорости подъема температуры. Полученные нарезанные заготовки укладывали в капсель в один ряд, который затем помещали в печь, и запускали установленный режим нагрева. При удалении органической связки в материале протекают следующие процессы. При температуре порядка 160 °С происходит разложение связки поливинилбутираля на масляный альдегид и воду. Далее при нагреве происходит разложение дибутилфталата при 340 °С. Скорость удаления связки на первой и второй стадии 1 °/мин данная скорость нагрева не приведет к деформациям изделий. При удалении связки предусмотрены две стадии выдержки для более полного прохождения реакций разложения.
65
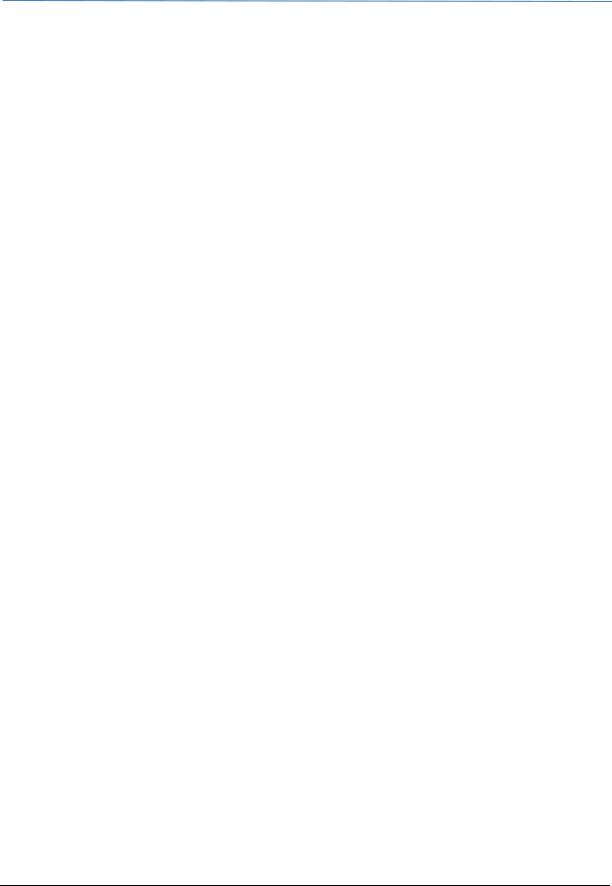
Наука и молодежь СГУПСа в третьем тысячелетии
Процесс спекания алюмонитридных подложек заключается в подготовке компактов для спекания в атмосфере азота. До основного процесса спекания удаляется связующее путем предварительного отжига при температуре порядка 350 °С в инертной атмосфере. Далее подготовленные компакты загружаются в капсель из нитрида бора. Капсель помещается в высокотемпературную печь. Спекание производится в атмосфера азота при давлении последнего 0,12 МПа при температуре 1 800–1 850 °С в течение 10 ч. Спеченные алюмонитридные подложки показали теплопроводность – 180 В/м·К.
Заключение
В результате экспериментальных исследований было выявлено, что наиболее оптимальным является состав шликера с использованиемпорошкаAlN японской производства, спекающей добавки Y2O3, органической связкиполивинилбутираля (ПВБ), пластификатора дибутилфталата ирастворителя азеотропной смеси толуол/этанол (32/68) мас. % для получения тонких алюмонитридных подложек и корпусов с высокой теплопроводностью – 180 В/м·К методом литья на основу.
Библиографический список
1.Organic Additives and Ceramic Processing, Second Edition: With Applications in Powder Metallurgy, Ink, and PaintISBN-13: 9780792397656, Publisher: Springer US, Publication date: 8/31/1996, Edition description: 2-nd ed. 1996. P. 335.
2.Mistier R.Е., Twiname Е.R. Таре Casting. Theory and practice. American Ceramic Society. 2000. 298 c.
3.CN101791818, МПК C04B35/10. Method for preparing aluminium oxide ceramics green ceramic chip by tape casting / Kai Cheng, Qingshui Xia, She Zhang. Опубл. 4.08.2012.
4.P63136677, МПК C04B33/32. Manufacture of piezoelectric ceramic thin plate / Kawanami Hiroshi. Опубл. 8.06.1988.
5.US2009208645. МПК C04B37/02. Manufacturing process for thin films made of metal/ ceramic composite / Silvian Jean Franncois, Chartier Thierry, Geffroy Pierre-Marie. Опубл. 20.08.2009.
6.DE3809693. МПК C04B35/111. Process for producing ceramic tapecasting compositions for thin-film circuits / Hoffmann Carl, Grote Dieter. Опубл. 12.10.1989.
Научный руководитель д-р техн. наук, проф. П.М. Плетнев
66

Сборник научных статей аспирантов и аспирантов-стажеров
И.А. Жильников
(факультет «Мосты и тоннели»)
Анализ напряжений смятия в болтовом соединении листов, выполненных из композиционного материала
В настоящие время в практике строительства все чаще используются стержни, выполненные из композиционных однонаправленно армированных материалов: стеклопластика или углепластика. Для соединения таких стержней в конструкцию обычно используются болтовое соединение. Из курса сопротивления материалов известно, что болтовые соединения рассчитываются на срез и на смятие. Однако если композитные стержни соединяются стальными болтами, то прочностные характеристики стали значительно превышают аналогичные характеристики материала матрицы композитного стержня. По этой причине актуальным является расчет напряженно деформированного состояния композитного стержня в зоне его контакта со стальным болтом. Это является задачей теории упругости. Заметим также, что материал композитного стержня обладает существенной анизотропией. По этой причине использование простых формул сопротивления материалов для расчета такого рода соединений не дает достоверного распределения напряжений.
Постановка задачи. Задано болтовое соединение трех композитных пластин. Необходимо получить и проанализировать картину распределения напряжений, как в плане каждого из листов, так и по толщине. Так же следует выявить наиболее загруженный слой стеклопластика, и сравнить полученные напряжения с расчетным сопротивлением.
Соединение состоит из трех листов пластика одинаковой ширины и высоты 100 мм и 18 мм соответственно. Между собой листы скреплены металлическим болтом класса точности Б диаметром 12 мм. Размеры модели соединения представлены на рис. 1.
Работа представленной сборки моделируется в расчетном комплексе ANSYS LS-DYNA. Конечно-элементная модель представлена на рис. 2. Каждая деталь сборки разбита кубическими элементами размером 1,5 мм. Сетка болта и вокруг отверстия имеет сгущение до 1 мм (рис. 2, 3).
67
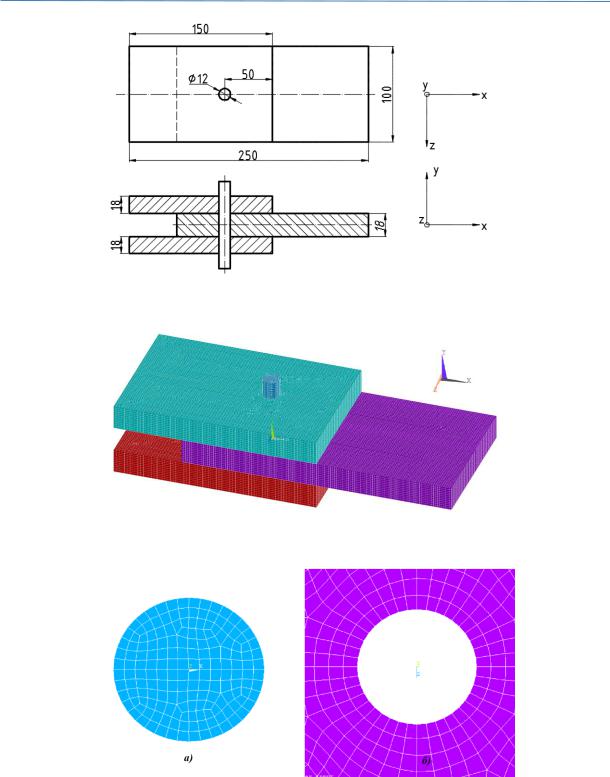
Наука и молодежь СГУПСа в третьем тысячелетии
Рис. 1. Болтовое соединение листов
Рис. 2. Конечно-элементная модель соединения
Рис. 3. Сгущение сетки болта и области отверстия
Нагружение производится узловыми силами, приложенными к торцу среднего листа, равнодействующая которых составляет
68
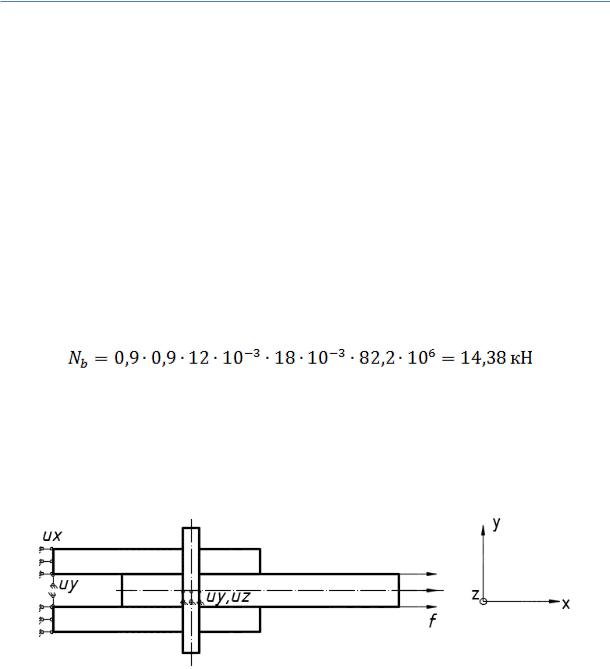
Сборник научных статей аспирантов и аспирантов-стажеров
14,38 кН. Данное усилие совладает с расчетной несущей способностью одного болта по смятию пластика вдоль волокон, и определено по формуле (1) СТО АПАТЭКа.
N |
b |
m m dtRc , |
(1) |
|
b b 1 |
|
|
|
|
1 |
|
где mb = 0,9 – коэффициент условий работы по табл. 81 СНиП 2.05.03–84* для нормальной и грубой точности болтов; mb1 = = 0,9 – коэффициент условий работы болтов по табл. 82 СНиП 2.05.03–84* для случая непосредственного прикрепления элемента в узле; d = 12 мм – диаметр болта; t = 18 мм – толщина
элемента; R1c 82, 2 МПа – расчетное сопротивление стеклопластика сжатию вдоль волокон.
.
Граничные условия: болту запрещены вертикальное и горизонтальное перемещения поперек листа, для этого в середине болта выбрано сечение, где UY и UZ равны нулю; верхний и нижний листы имеют заделку, торцовым узлам запрещены любые линейные перемещения (см. рис. 4).
Рис. 4. Схема закрепления и нагружения сборки
Загружение среднего листа представляет собой функцию от времени, которая задается в виде массива данных. На рис. 5 представлен график загружения среднего листа.
Нагружение сборки разделено на два участка: первый: 0 –0,03с – линейное увеличение нагрузки от нуля до расчетной; второй: 0,03 –
– 0,05с – нагрузка не изменяется и равна Nb = 14,38 кН. Второй участок нагружения необходим для анализа равновесного состояния сборки, т.е. по графикам напряжения f (t) будут наблюдаться колебания.
69
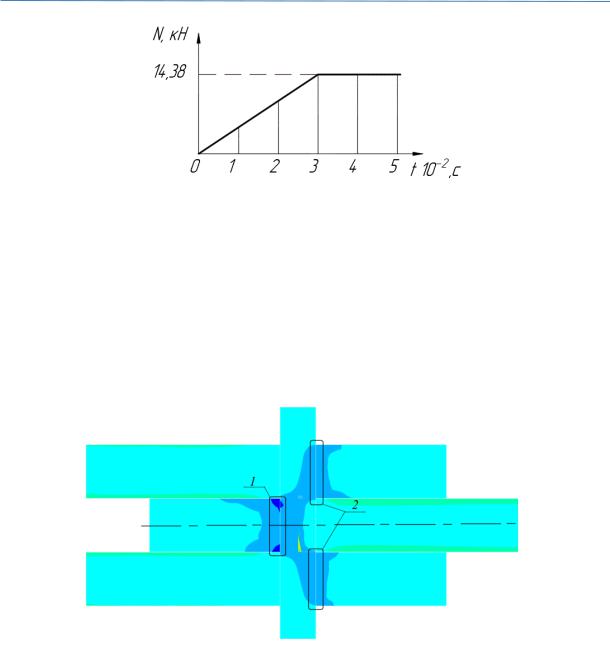
Наука и молодежь СГУПСа в третьем тысячелетии
Рис. 5. График загружения конечно элементной модели от времени
Результаты расчета. В результате расчета получено напря- женно-деформированное состояние болтового соединения. На рис. 6 представлен разрез конечно элементной модели вдоль оси OX, на котором виден результат взаимодействия болта и стыкуемых листов. Зона 1 – давление среднего листа на болт, зона 2 – давление болта на крайние листы. Напряженное состояние отдельных элементов сборки рассмотрено ниже.
Рис. 6. Напряженно-деформированное состояние соединения: 1 – зона контакта болта и среднего листа; 2 – зона контактов болта и крайних листов
Из трех листов пластика наиболее загруженным является средний, следовательно, необходимо рассмотреть его напря- женно-деформированное состояние в первую очередь.
На рис. 7 представлен разрез среднего листа с полями напряжений x , поля \ синего цвета – зоны сжатия, где видны концен-
трации напряжений в верхних и нижних слоях пластика. Поля цветами цвета от голубого до красного – зоны растяжение.
70