
1326
.pdf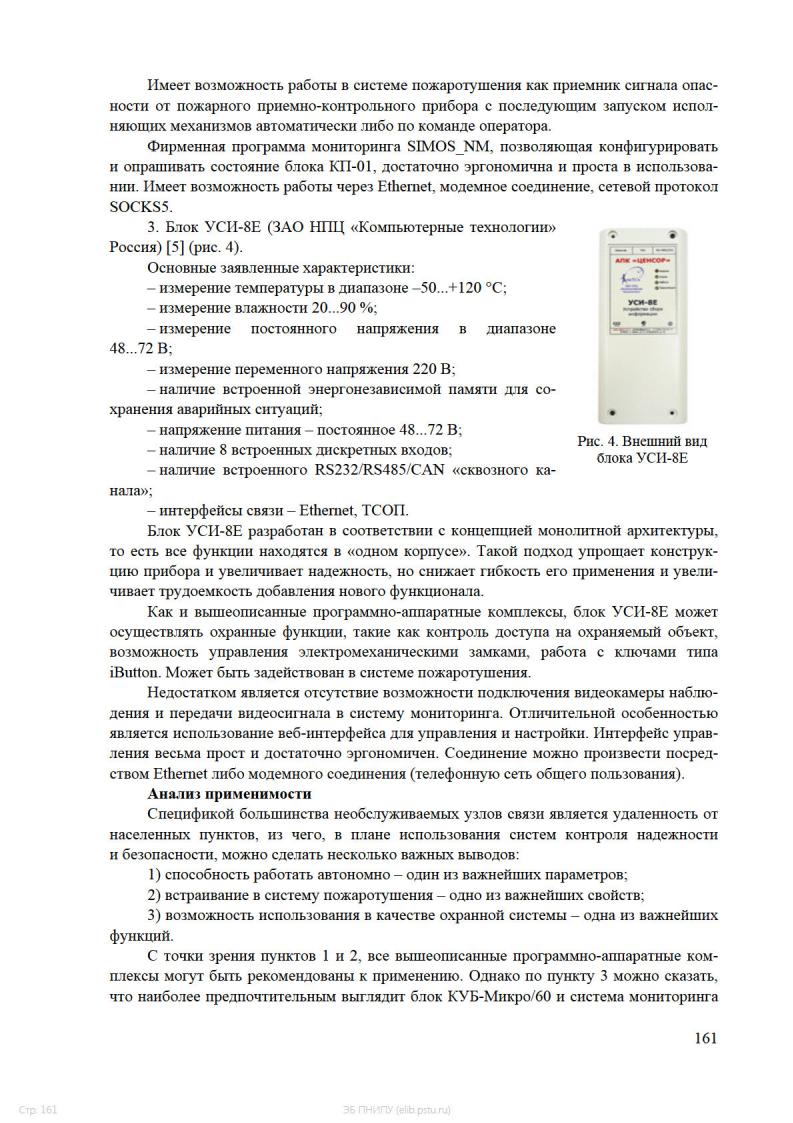
«КУБ-TTx» в связи с возможностью использования в качестве системы видеонаблюдения. Также преимуществом КУБ-Микро/60 является модульная архитектура, что позволяет очень гибко подстраивать систему под конкретные условия.
Заключение
В статье были проанализированы современные программно-аппаратные комплексы контроля безопасности и надежности, приведены основные характеристики и параметры таких систем, произведен анализ применимости в условиях необслуживаемого узла технологической связи.
Список литературы
1.СТО Газпром 2-3.5-454–2010. Правила эксплуатации магистральных газопроводов.
2.СТО Газпром 2-3.5-051–2006. Нормы технологического проектирования магистральных газопроводов.
3.Технотроникс [Электронный ресурс]. – URL: http:// www.ttronics.ru.
4.Научно-технический центр «Симос» [Электронный ресурс]. – URL: http:// www.simos.ru.
5.Аппаратно-программный комплекс Ценсор [Электронный ресурс]. – URL: http:// www.censor-m.ru.
Получено 2.10.2013
Стр. 162 |
ЭБ ПНИПУ (elib.pstu.ru) |
УДК 622.244.5
П.Р. Ширяев, Г.А. Цветков
Пермский национальный исследовательский политехнический университет
РАЗРАБОТКА ТЕХНОЛОГИИ ПОВЫШЕНИЯ БЕЗОПАСНОСТИ ПРИ БУРЕНИИ СКВАЖИН, ОСНОВАННОЙ НА ПРИМЕНЕНИИ ВОЛОКОННО-ОПТИЧЕСКИХ ДАТЧИКОВ
Рассматриваются риски, возникающие при бурении пластов с различными механическими свойствами, и возможные последствия. Дается краткое описание приборов, которые могут использоваться при оценке риска во время бурения. Показано, что существует возможность повышения точности измерительной системы за счет использования волоконно-оптических датчиков.
Ключевые слова: бурильная колонна, бурение, риски, безопасность, каротаж, волоконно-оптический датчик (ВОГ), точность установки датчиков.
P.R. Shiryaev, G.A. Tsvetkov
Perm National Research Polytechnic University
DEVELOPMENT OF TECHNOLOGY SAFETY IMROVEMENT DURING DRILLING,
BАSED ON THE APPLICATION FIBER OPTIC SENSORS
Discusses the risks arising from the drilling layers with different mechanical properties, and possible consequences. There is a short description of devices that can be used in the risk assessment during drilling. It is shown that it is possible to improve the accuracy of the measurement system through the use of fiber optic sensors.
Keywords: drillstring, drilling, risks, security, logging, fiber optic sensor (FOG), the accuracy of the sensors positioning.
Бурение скважин сопряжено с постоянным риском происшествия чрезвычайной ситуации, последствиями которой могут быть выход из строя оборудования, невозможность продолжения бурения и необходимость бурения новой скважины. Причиной появления рисков является то, что на пути к пласту-коллектору необходимо пробурить несколько километров породы, разные пласты которой имеют различные механические свойства. Например, при бурении скважины в породе, в которой велики механические напряжения, и несвоевременной обсадке скважины возможно разрушение породы вокруг скважины за счет внутренних механических напряжений в породе и последующий обвал ствола скважины. Если свойства породы таковы, что диаметр пробуриваемой скважины заметно превышает диаметр нижней части бурильной колонны, то в бурильной колонне могут возникать колебания, в результате которых нижняя часть бурильной колонны будет ударяться о стенки скважины. Это может привести к повреждениям элементов бурильной колонны, не позволяющим продолжать бурение скважины без ремонта оборудования [1].
163
Стр. 163 |
ЭБ ПНИПУ (elib.pstu.ru) |
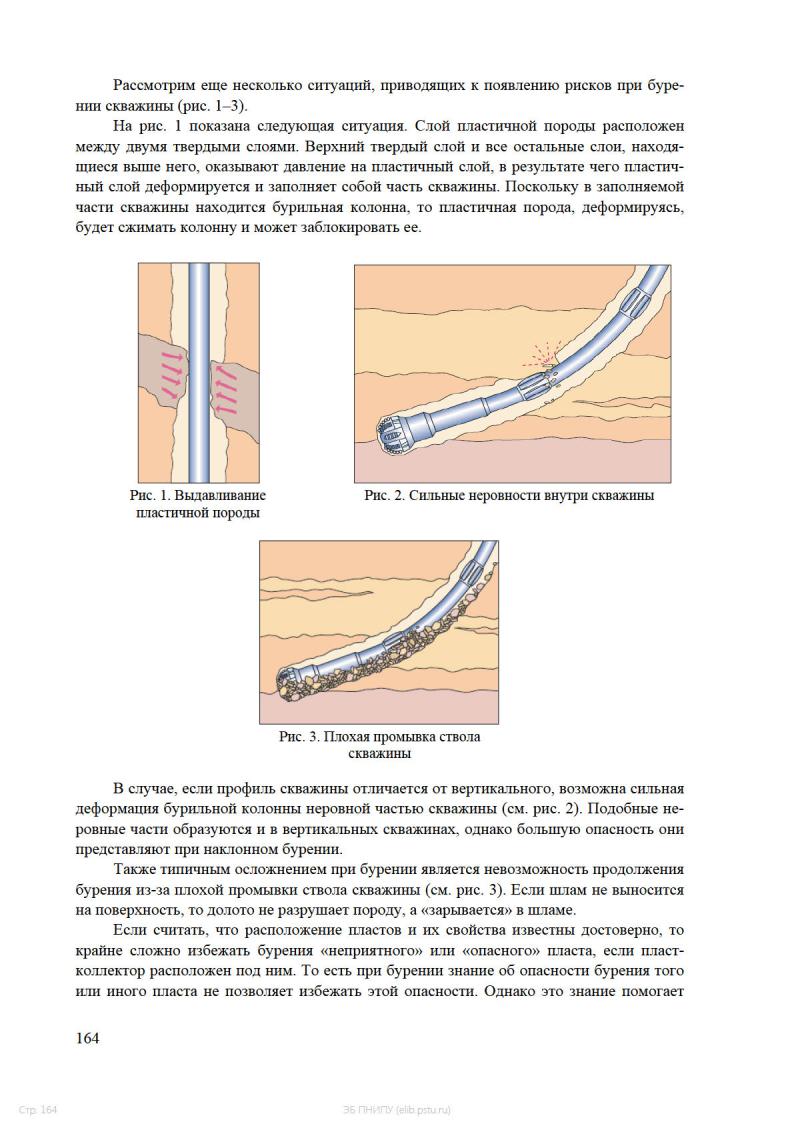
просчитывать риски возможных осложнений и предсказывать возможные потери, которые могут случиться при прохождении того или иного пласта.
Разработаны методы, позволяющие узнать о свойствах породы, в которой бурится скважина и, соответственно, помогающие просчитывать риски. Распространенным способом является каротаж во время бурения (до начала бурения проводятся геофизические изыскания, каротаж во время бурения лишь дополняет и уточняет ранее полученную информацию). Ранее считалось, что определение трех параметров: горизонтального сопротивления пласта, вертикального сопротивления и относительного угла наклонения (между осью скважины и нормальной плоскостью формации) – невозможно. Однако
внастоящее время существуют приборы, позволяющие определять эти три параметра одновременно. Основными элементами такого прибора являются передающие и принимающие антенны. Однако приборы, которые не могут одновременно определять вертикальное сопротивление и относительный угол наклонения, также основаны на использовании антенн, передающих и принимающих сигнал. Отличие нового прибора состоит
втом, что принимающие и передающие антенны расположены на непараллельных плоскостях, в результате чего исчезает функциональная связь между вертикальным сопротивлением и относительным углом наклонения [2].
Существенное влияние на точность прибора оказывает точность установки антенн по углу. Ошибка в установлении угла приведет к ошибке в измерении амплитуды принимаемого сигнала, которая вызовет ошибку в определении сопротивления пласта. Кроме очевидной погрешности установки антенн датчик имеет и множество других погрешностей, влияющих на его точность. Неправильное определение сопротивления пласта повышает риски при бурении этого пласта.
Впоследнее десятилетие широкое распространение в измерительной технике получают оптоволоконные датчики. Считается, что датчики из оптоволокна способны измерять любые физические характеристики, а кроме того, точность датчиков на основе оптоволокна во многих случаях оказывается выше, чем у традиционных. Однако сказанное не говорит о том, что волоконно-оптический датчик работает идеально и не имеет погрешностей. Например, погрешность от углового рассогласования при установке будет характерна и для волоконно-оптических датчиков. Тем не менее, наличие погрешностей не отменяет того, что волоконно-оптические датчики перспективны и потенциально имеют очень высокую точность. Из этого следует, что использование воло- конно-оптических датчиков для определения амплитуды и сдвига фазы сигнала в приборе, определяющем горизонтальное и вертикальное сопротивление и относительный угол наклонения, вместо установленных в нем антенн, способно повысить точность такого прибора и снизить риски. Снижение рисков приведет к повышению безопасности и снижению потерь при бурении.
Список литературы
1.Кейн С.А., Мищенко Р.Н. Инженерные задачи бурения наклонно-направленных
игоризонтальных скважин. – Ухта: Изд-во УГТУ, 2011.
2.Патент US 7,948,238 B2. Прибор с наклонной антенной, определяющий свойства формаций (толщи пород) при сопротивлении электромагнитной волны.
Получено 17.10.2013
165
Стр. 165 |
ЭБ ПНИПУ (elib.pstu.ru) |
УДК 629.7.036.3.001.2
А.С. Соснин, С.Ф. Минацевич
Пермский национальный исследовательский политехнический университет
МЕТОДИКА УПРАВЛЕНИЯ БЕЗОПАСНЫМ СОСТОЯНИЕМ ЛОПАТОК ТУРБОМАШИН ПРИ КОНТРОЛЕ АМПЛИТУД ПРЕДЕЛЬНЫХ КОЛЕБАНИЙ ЛОПАТОК БЕСКОНТАКТНЫМ МЕТОДОМ
Рассмотрена предлагаемая авторами методика управления безопасным состоянием турбомашин в эксплуатации с использованием только одного периферийного датчика, которая позволяет получить исчерпывающую достоверную информацию об амплитудах колебаний.
Ключевые слова: турбомашина, лопатки, датчик, дискретно-фазовый метод (ДФМ), диагностика.
A.S. Sosnin, S.F. Minatsevich
Perm National Research Polytechnic University
METHODOLOGY OF CONTROL OF THE SAFE CONDITION OF TURBOMACHINE BLADES UNDER THE CONTROL OF THE LIMIT AMPLITUDE OF OSCILLATIONS OF THE BLADES BY NON-CONTACT METHOD
The present paper addresses analyzes of methodologies of control of the safe condition of turbomachine blades. In this article bases of a proposed methodology of control of the safe condition of turbomachine blades and its operation using only one peripheral sensor, which allows to receive reliable information about the vibration amplitudes. The conclusions drawn regarding of the methodology in operating.
Keywords: turbomachine, blades, sensor, discrete-phase method (DFM), diagnostics, methodology, non-contact method, safety, control, oscillations, flutter, self-oscillations, monitoring, fatigue stress, amplitude.
Введение
Впроцессе эксплуатации элементов технических устройств энергетической промышленности возникает целый ряд проблем, которые могут привести к техногенным катастрофам и человеческим жертвам.
Впервую очередь, это связано с тем, что большая часть оборудования (85–90 %) выработала свой ресурс и нуждается в полной или частичной замене. Однако современное состояние экономики в энергетической промышленности не позволяет достичь поставленных целей. Поэтому весьма актуальным становится вопрос разработки новых, эффективных технологий, методик и способов оценки работоспособности и восстановления ресурса элементов технических устройств. И для обеспечения безопасной эксплуатации ответственных конструкций все более широкое распространение получает концепция, основанная на «прогнозировании и предупреждении» вместо используемой старой концепции «обнаружение и устранение» [1].
166
Стр. 166 |
ЭБ ПНИПУ (elib.pstu.ru) |
Рабочие лопатки осевого компрессора и газовой турбины газотурбинного двигателя являются весьма ответственными деталями, от надежной работы которых в значительной мере зависит надежная работа двигателя в целом и безопасность лопаточной машины [2].
Рост стоимости жизненного цикла турбоагрегатов выдвигает проблему полного
ибезопасного использования ресурсных возможностей каждой турбомашины – недопущения снятия с эксплуатации по ресурсным ограничениям исправных турбоагрегатов
инедопущения отказов в пределах назначенных ресурсов. Важная роль в ее решении отводится непрерывному контролю технического состояния лопаток – мониторингу выработки ресурса (МВР) лопаток в реальных условиях их эксплуатации. Наличие такой информации позволяет оптимизировать сроки проведения ремонтов с продлением межремонтного периода эксплуатации, снижать трудоемкость путем проведения восстано- вительно-ремонтных работ на стадии раннего развития дефектов, уменьшать общую длительность ремонтных работ за счет своевременной поставки запасных частей, предупреждать аварийные ситуации и повышать общую надежность работы турбоагрегатов.
Воснове современных методик эксплуатационного МВР лопаток турбомашин лежат методы расчета их напряженно-деформированного состояния (НДС) и теплонагруженного состояния (ТНС) по параметрам состояния двигательной установки, которые замеряются в эксплуатации и записываются на магнитные регистраторы параметров. Далее с помощью моделей НДС и ТНС проводится расчет напряжений в наиболее нагруженных точках лопаток.
По этим данным с использованием характеристик длительной прочности конкретных материалов определяется статическое повреждение лопаток [3].
Автоматизированный контроль деформационных характеристик лопаток турбоагрегатов при их эксплуатации позволяет выявлять неисправности лопаточного аппарата на ранней стадии их возникновения и принимать оперативные меры по их устранению. Реализованным на практике методом оперативного и длительного контроля состояния лопаточных венцов турбоагрегатов является бесконтактный дискретно-фазовый метод (ДФМ). ДФМ основан на преобразовании дискретных значений (фаз) перемещений торцов лопаток, определяемых в пределах периода каждого оборота ротора, в пропорциональные временные интервалы, длительности которых подвергаются статистической обработке, в результате чего определяются максимальное, минимальное и среднее значения контролируемого перемещения за время накопления (усреднения) [4].
Методика управления вибрационным состоянием бандажированных лопаток паровых турбин
Известна методика управления вибрационным состоянием бандажированных лопаток паровых турбин, разработанная доктором технических наук К.Н. Боришанским. Для определения амплитуд колебаний периферийных сечений лопаток в бандажные полки части лопаток устанавливаются магниты, а расположенные против торцов лопаток индукционные датчики ДФМ выполняются с сердечниками, поперечные сечения которых имеют форму вытянутого прямоугольника, составляющего угол β с осью турбины. Два датчика, расположенные на небольшом расстоянии S друг от друга, образуют «обычную» пару (поперечное сечение сердечника одного из датчиков составляет угол β с осью турбины, второго – угол β). Измерения выполняются в момент прохождения маг-
167
Стр. 167 |
ЭБ ПНИПУ (elib.pstu.ru) |
нита мимо датчиков, т.е. один раз за оборот. Для возможности замера на постоянных оборотах частоты некратных колебаний или амплитуды кратных обычно используют показания трех пар датчиков ДФМ, т.е. устанавливают 6 датчиков ДФМ в проточной части и один дополнительный для контроля числа оборотов. Методика позволяет получить достаточно полную информацию о природе зарегистрированных колебаний, дает возможность глубже понять характер силового взаимодействия потока с колеблющимися лопатками, осуществлять непрерывный контроль вибрационного состояния лопаток, а также получать дополнительную информацию об общей вибрации турбоагрегата [5].
Методика управления деформационным состоянием рабочих лопаток турбин
Известна методика управления деформационным состоянием рабочих лопаток турбин, разработанная доктором технических наук А.И. Данилиным. Она основана на использовании специальных устройств, которые целесообразно выделить в самостоятельный класс средств измерений – дискретно-фазовые преобразователи перемещений (ДФПП). Особенность преобразователей данного класса заключается в том, что значения дискретных фаз перемещений формируются с помощью расположенного в технологическом отверстии корпуса турбоагрегата одноили двухканального первичного преобразователя, в котором конструктивно и функционально интегрированы объект контроля, источник и приемник зондирующего излучения (ЗИ) оптического или радиоволнового диапазона и электронные узлы первичной обработки сигналов. Такое конструктивное решение позволяет обеспечить получение необходимой информации при минимальном уровне препарирования турбомашины (используется одно технологическое отверстие в корпусе 8–10 мм), что не оказывает заметного влияния на прочность конструкции двигателя в целом. Сигнализаторы предаварийных деформаций лопаток турбоагрегатов, построенные на базе дискретно-фазовых преобразователей перемещений, позволяют как в эксплуатации, так и в процессе опытно-конструкторской доводки новых или модифицируемых турбоагрегатов выявлять конструктивнотехнологические недостатки или же неисправности контролируемых узлов (лопаток) на ранней стадии их возникновения и предупреждать о необходимости принятия оперативных мер по их устранению [6].
Рассмотренные методики позволяют на ранних стадиях возникновения обнаружить дефект лопаток турбомашины, но не избежать его появления. Авторами предложена методика управления безопасным состоянием лопаток турбомашин, позволяющая определить опасное состояние колеблющихся рабочих лопаток и прекратить работу турбоагрегата при данных условиях, тем самым продлить срок эксплуатации лопаток турбомашин.
Методика управления безопасным состоянием лопаток турбомашин при контроле амплитуд предельных колебаний лопаток
При экспериментальном исследовании вынужденных колебаний лопаток получают графики зависимости амплитуд динамических напряжений от частоты вращения ротора. По ним определяется наибольшая амплитуда напряжений в лопатке σv (по всем режимам работы двигателя и для всех опасных точек лопатки). Ее сопоставляют с пределом выносливости σ–1л натурной лопатки, характеризующим способность материала сопротивляться разрушению при высокочастотном циклическом нагружении.
168
Стр. 168 |
ЭБ ПНИПУ (elib.pstu.ru) |
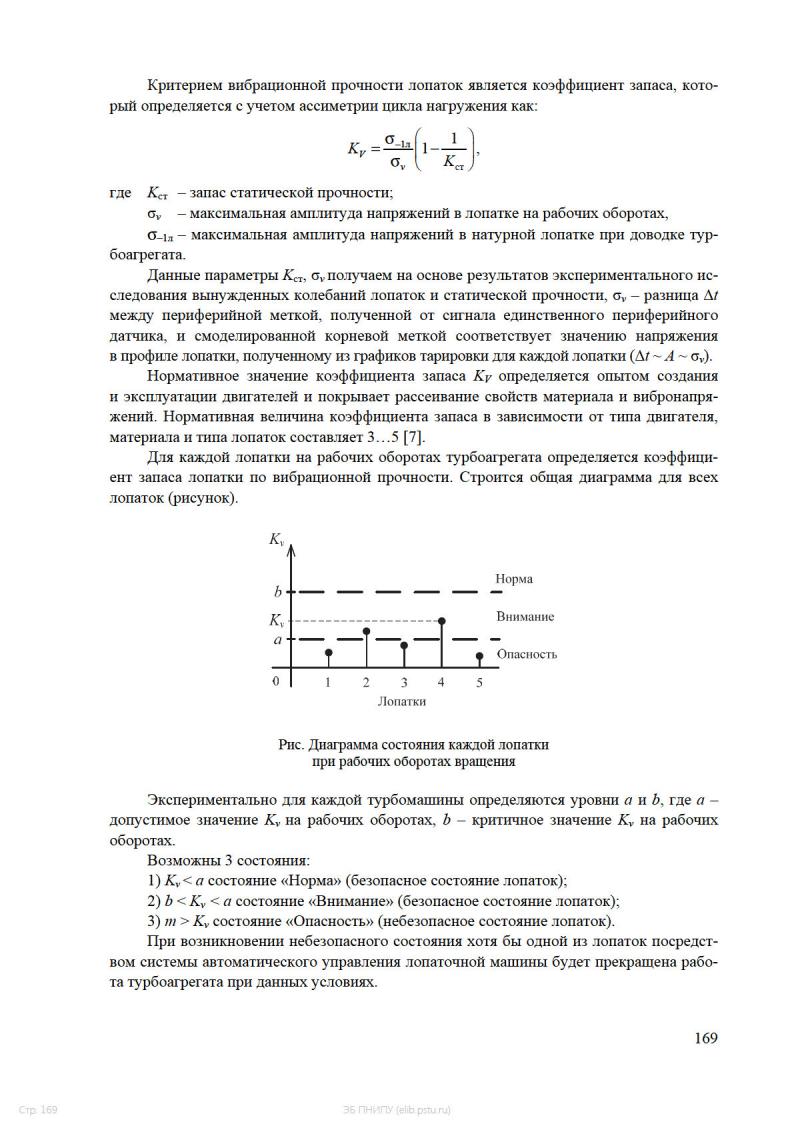
Заключение
Принимая за основу предлагаемую методику определения безопасного состояния лопаток турбомашин с использованием одного периферийного датчика на основе дис- кретно-фазового метода (ДФМ), в дальнейшем будет разработана модель системы автоматического управления безопасным состоянием лопаток турбоагрегатов в эксплуатации.
Список литературы
1.Смирнов А.Н., Абабков Н.В. Анализ проблем, связанных с безопасной эксплуатацией элементов энергетического машиностроения // Вестн. Кузбас. гос. ун-та. – 2010. –
№2. – С. 12–17.
2.Кузменко М.Л., Чигрин В.С., Белова С.Е. Статическая прочность рабочих лопаток и дисков компрессоров и турбин ГТД: учеб. пособие. – Рыбинск: РГАТА, 2005. – 74 с.
3.Данилин А.И., Гречишников В.М. Методика эксплуатационного мониторинга выработки ресурса лопаток турбоагрегатов // Вестн. Самар. гос. аэрокосм. ун-та. – 2011. –
№1. – С. 150–154.
4.Данилин А.И., Гречишников В.М. Сигнализаторы предаварийных деформаций лопаток турбоагрегатов на базе дискретно-фазовых преобразователей перемещений // Вестник транспорта Поволжья. – 2011. – № 4. – С. 37–40.
5.Боришанский К.Н. Анализ автоколебаний бандажированных рабочих лопаток
мощных паровых турбин дискретно-фазовым методом // Энергетические машины
иустановки. – 2008. – № 3. – С. 29–35.
6.Гречишников В.М., Данилин А.И. Математическая модель дискретно-фазовых преобразователей перемещений вращающихся узлов энергоагрегатов // Компьютерная оптика. – 2011. – Т. 35, № 4. – С. 495–499.
7.Газотурбинные двигатели. Т. 4. Динамика и прочность авиационных двигателей
иэнергетических установок / А.А. Иноземцев [и др.]. – М.: Машиностроение, 2008. –
С. 141–143.
Получено 17.10.2013
Стр. 170 |
ЭБ ПНИПУ (elib.pstu.ru) |