
508
.pdfВ формулах (2) и (3):
D — диаметр барабана, мм; z — число зубьев звёздочки тяговой цепи; рц — шаг тяговой цепи, мм; число 60 осуществляет перевод минут в секунды, 103 — миллиметры в метры.
Потребную мощность двигателя определяют с учетом потерь во всех звеньях кинематической цепи:
P = Pâû õ / η, |
(4) |
где η — общий КПД привода.
Например, по схеме, представленной на рис. 3, общий КПД равен:
η = η1 η2 η3 ηì , |
(5) |
где η1, η2, η3 — КПД соответственно конической, цилиндрической зубчатых передач и цепной передачи; ηм — КПД муфты.
Значения КПД отдельных ступеней с учетом потерь на трение в подшипниках приведены в прил. А. Выбранный электродвигатель должен иметь номинальную по каталогу мощность Рэд,
ближайшую большую потребной Р. Допускается перегрузка не более 5 %. Следует помнить, что
элементы привода рассчитывают не по номинальной мощности двигателя Рэд, а по потребной мощности Р, которую он фактически будет развивать при установившемся режиме.
Для выбора частоты вращения электродвигателя следует вначале ориентировочно определить потребную частоту вращения по формуле
n = nâû õu , |
(6) |
где и — ориентировочное общее передаточное отношение привода, определяемое как произведение передаточных отношений отдельных ступеней.
Для схемы на рис. 3
u = u1 u2 u3 , |
(7) |
где u1…u3 — передаточные отношения соответственно конической, цилиндрической зубчатых передач и цепной передачи, назначаемые по прил. А.
При выборе ориентировочных передаточных отношений необходимо учитывать следующие соображения:
1)передаточные отношения открытых передач (ремённой, цепной) принимать больше, чем передач редуктора для уменьшения стоимости привода;
2)в коническо-цилиндрическом и двухступенчатом цилиндрическом редукторах передаточное отношение первой (быстроходной) ступени принимать больше, чем тихоходной; в этом случае можно обеспечить равное либо приемлемое погружение колёс обеих ступеней в масляную ванну;
3)передаточные отношения редукторных зубчатых передач рекомендуется принимать стандартными;
4)для зубчатых и цепных передач наиболее распространенный термин — передаточное число: отношение большего числа зубьев к меньшему;
5)стандартные передаточные числа зубчатых передач по ГОСТ 2185 приведены в табл. 1.
Таблица 1
|
Значения передаточных чисел u |
|
|
1-й ряд |
2,5; 3,15; 4; 5; 6,3 |
|
|
2-й ряд |
2,8; 3,55; 4,5; 5,6; 7,1 |
Примечания: 1. Первый ряд следует предпочитать второму.
2. Фактические значения могут отличаться от номинальных не более чем на 2,5 % при u ≤ 4,5 и на 4 % при u > 4,5.
Для схемы на рис. 3 n = nIV u . По потребной частоте вращения назначают номинальную часто-
ту вращения электродвигателя nэд. Обычно принимают пэд, ближайшую к потребной частоте вращения п. При нахождении п посередине интервала пэд предпочтение отдают быстроходным двигателям, приводы с использованием которых оказываются, как правило, более дешёвыми. Для решения этой задачи в приводах с ремённой передачей следует выполнить технико-экономические расчёты (см. разд. 9).
Общее передаточное отношение привода уточняют после выбора двигателя:
u = nýä / nIV . |
(8) |
Точное передаточное отношение привода и разбивают по ступеням, оставив без изменения ранее принятые значения передаточных чисел редукторных передач и откорректировав передаточ-
21
ное отношение открытой передачи. Так, для схемы на рис. 3 оставляют неизменными u1 и u2 и уточняют передаточное отношение цепной передачи по формуле
u3 = u / (u1 u2 ). |
(9) |
По формулам (8) и (9) рассчитывают окончательные передаточные отношения для проектирования ступеней привода. Кинематический расчёт привода завершают определением мощностей, частот вращения и вращающих моментов на каждом его валу. Так, для привода, схема которого приведена на рис. 3, мощности на валах, кВт:
PI = P; PII = PIη1; PIII = PIIη2; PIV = Pâû õ = PIIIη3 . (10)
Частоты вращения валов, об/мин, для схемы на рис. 3:
nI = nэд ; nII = nI / u1; |
|
nIII = nII / u2; |
nIV = nIII / u3. |
(11) |
|||||
Вращающие моменты на валах, Н м: |
|
|
|
||||||
T = |
P |
|
= |
P 103 30 |
= |
9550P |
, |
(12) |
|
ω |
π n |
|
n |
||||||
|
|
|
|
|
|
где Р, кВт, и п, об/мин, — мощность и частота вращения на соответствующем валу, определённые по формулам (10) и (11).
Проверку правильности расчётов следует вести сравнением мощности PIV и частоты вращения nIV, рассчитанных по формулам (10) и (11), с заданными параметрами PIV и nIV либо рассчитанными по формулам (1), (2) или (3). Погрешность должна быть близка к нулю.
После расчётов всех кинематических параметров привода расчёт передач можно вести в любой последовательности.
Пример 1. Выбрать электродвигатель и выполнить кинематический расчёт привода ленточного конвейера (см. рис. 3) по следующим исходным данным: окружное усилие на барабане Ft = 8 кН; скорость ленты υ = 0,8 м/с; диаметр барабана Dб = 300 мм; срок службы L = 6 лет.
Решение.
1) Мощность на приводном валу по формуле (1): PIV = Ft υ = 8 103 0,8 = 6400 Âò = 6,4 êÂò.
2) Общий КПД привода по формуле (5):
η = η1 η2 η3 ηì ,
где коэффициенты полезного действия: η1 — конической зубчатой передачи; η1 = 0,95 (см. прил. А); η2 — цилиндрической зубчатой передачи; η2 = 0,96 (см. прил. А); η3 — цепной передачи; η3 = 0,93 (см. прил. А); ηм — муфты; ηм = 0,98 (см. прил. А).
η= 0,95 0,96 0,93 0,98 = 0,83.
3)Потребная мощность электродвигателя по формуле (4):
P = PIV / η = 6,4 / 0,83 = 7,71 êÂò.
4) Частота вращения приводного вала по формуле (2):
n |
= |
60000 υ |
= |
60000 0,8 |
= 50,93 î á/ ì èí . |
|
|
||||
IV |
|
π Dá |
|
π 300 |
|
|
|
|
5) Назначены передаточные отношения:
—быстроходной ступени редуктора u1 = 3,55; тихоходной — u2 = 2,8 (см. табл. 1 и разд. 7);
—цепной передачи — ориентировочно u3 = 4,5 (см. прил. А); ориентировочное общее передаточное отношение привода по формуле (7):
u= u1 u2 u3 = 3,55 2,8 4,5 = 44,73.
6)Потребная частота вращения вала электродвигателя по формуле (6): n = nIV u = 50,93 44,73 = 2278 î á/ ì èí .
7)Выбор электродвигателя. В соответствии с потребными мощностью и частотой вращения принят электродвигатель АИР112М2/2895 (см. прил. Б). Его паспортные данные: номинальная мощ-
ность: Pэд = 7,5 кВт (перегрузка 2,8 %); номинальная частота вращения nэд = 2895 об/мин; диаметр хвостовика dхв = 32 мм.
8)Уточнённое передаточное отношение по формуле (8):
22

u = nýä = 2895 = 56,84. nIV 50,93
Рассчитанное передаточное отношение больше ориентировочного, так как из двух вариантов (nс = 1500 и 3000 об/мин) принят быстроходный. Оставлены без изменения u1 = 3,55 и u2 = 2,8; уточнено предварительно принятое передаточное отношение цепной передачи по формуле (9):
u |
|
= |
u |
|
= |
56,84 |
= 5,72. |
|
3 |
u u |
2 |
3,55 2,8 |
|||||
|
|
|
|
|||||
|
|
|
1 |
|
|
|
9) Мощности на валах по формуле (10):
РI = Р ηм = 7,71 · 0,98 =7,56 кВт;
РII = РI η1 = 7,56 · 0,95 = 7,18 кВт;
РIII = РII η2 = 7,18 · 0,96 = 6,89 кВт;
РIV = РIII η3 = 6,89 · 0,93 = 6,41 кВт. 10) Частоты вращения валов по формуле (11):
|
|
nI |
= nýä = 2895 |
î á/ ì èí ; |
nII |
= nI |
/ u1 = 2895 / 3,55 |
= 815,5 î á/ ì èí ; |
|
nIII |
= nII |
/ u2 |
= 815,5 / 2,8 = 291,2 î á/ ì èí ; |
|
nIV |
= nIII |
/ u3 |
= 291,2 / 5,72 = 50,92 î á/ ì èí . |
11) Вращающие моменты на валах по формуле (12): TI = 9550 7,56 / 2895 = 24,94 Í ì ;
TII = 9550 7,18 / 815,5 = 84,08 Í ì ;
TIII = 9550 6,89 / 291,2 = 226 Í ì ;
TIV = 9550 6,41/ 50,92 =1202 Í ì .
Анализ расчётов.
1.Окончательно принятые передаточные отношения находятся в рекомендуемых пределах.
2.Рассчитанные в пп. 9 и 10 значения PIV и nIV соответствуют заданным.
7. РАЗБИВКА ПЕРЕДАТОЧНОГО ОТНОШЕНИЯ
Разбивку общего передаточного отношения привода необходимо выполнять таким образом, чтобы передаточные отношения открытых ступеней привода (ремённая, цепная, открытая зубчатая передачи) были больше, чем у редукторных передач. Это позволит уменьшить стоимость при-
вода, так как стоимость корпусных деталей редуктора высока.
Большинство заданий содержит горизонтальные двухступенчатые цилиндрические или кониче- ско-цилиндрические редукторы. Во избежание серьезных затруднений при конструировании таких редукторов студент при разбивке передаточного числа редуктора должен задаться целью обеспече-
ния равного погружения ведомых колёс обеих ступеней в масляную ванну.
Для смазки зацепления погружением и разбрызгиванием (картерное смазывание) колесо быстроходной цилиндрической ступени рекомендуется погружать в масло на глубину (3…5)m, но не менее 10 мм (m — модуль колеса, мм), коническое колесо — на длину зуба. Тихоходное цилиндрическое колесо можно погружать глубже быстроходного, но не более 0,25ra2 (ra2 — радиус вершин колеса, мм). Невыполнение данных требований может привести к необходимости постановки смазочной шестерни либо к проектированию двухступенчатого цилиндрического редуктора с наклонной плоскостью разъёма. А для коническо-цилиндрического редуктора может потребоваться дорогостоящая циркуляционная система смазки.
Для обеспечения равного погружения колёс обеих ступеней двухступенчатого цилиндрического или коническо-цилиндрического редуктора рекомендуется передаточное число быстроходной ступени принимать большим, чем тихоходной, на два стандартных значения. Например, рекомендуются такие сочетания передаточных чисел:
uб uт = 3,15 · 2,5; 3,55 · 2,8; 4 · 3,15; 4,5 · 3,5; 5 · 4.
23
В червячно-зубчатом и шестеренно-червячном редукторах ориентировочно можно принимать
изуб = (0,03…0,06) ир, при этом uзуб = 2…2,5 (до 3).
Вкоробках скоростей передвижные шестерни не должны иметь слишком малые размеры по отношению к диаметру вала, что выполняется при ип < 2,5…3.
Впланетарных редукторах Джеймса рекомендуется передаточное отношение i = 3…8. В процессе расчёта передач их передаточные отношения будут изменяться. Откорректированные передаточ-
ные отношения должны обеспечивать значения nвых, отличающиеся от заданных не более чем на 5 %. При расчёте других передач привода в этом случае пересчёт n и T можно не производить.
8.ВЫПОЛНЕНИЕ РАСЧЁТОВ
Всоответствии с ГОСТ 2.106 и СТО СГУПС 1.01СДМ.01 [13] любой расчёт должен содержать:
1)цель расчёта (если она не указана в заголовке);
2)условия расчёта и исходные данные. В соответствии с этим требованием в каждом разделе
пояснительной записки должен быть пункт «Исходные данные»;
3)расчётную схему; например, в расчётах передач необходимо приводить кинематическую схему по ГОСТ 2.703 с элементами по ГОСТ 2.770 в двух проекциях; остальные разделы должны содержать эскизы и схемы;
4)расчёт. Последовательность либо алгоритм расчёта следует приводить с обозначениями пунктов, а при необходимости — подпунктов, аналогично изложению материала в СТО [13];
5)выводы, в частности, для зубчатых передач необходимы выводы типа: «Контактная прочность достаточна»; «Изгибная прочность достаточна»;
6)при выполнении расчётов с использованием ЭВМ обязательны пункты либо подпункты:
а) исходные данные, вводимые в ЭВМ, и расчётная схема; б) алгоритм расчёта, содержащий все формулы, по которым рассчитывает ЭВМ, с их сквозной
нумерацией; при сложных алгоритмах достаточно привести блок-схему; в) распечатка результатов расчёта; г) анализ результатов.
Параметры основных критериев работоспособности и расчёта (прочность, износостойкость и т.д.) имеют единицу измерения мегапаскаль (МПа). В этой же единице в справочниках приведены механические характеристики машиностроительных материалов. Так как 1 МПа = 1 Н/мм2, то в расчётных зависимостях силы должны выражаться в ньютонах, а длины — в миллиметрах. Следовательно, исходные параметры и результаты расчётов будут иметь единицы измерения: Н, мм, Н мм и МПа. Для этих единиц рассчитаны коэффициенты межосевого расстояния в расчётных формулах зубчатых передач, поэтому вращающий момент, рассчитанный в Н м, необходимо переводить в Н мм.
9.ТЕХНИКО-ЭКОНОМИЧЕСКИЕ РАСЧЁТЫ
Взаданиях, содержащих ремённые передачи, требуется выполнить технико-экономические расчёты, связанные с выбором электродвигателя с оптимальной частотой вращения. При выполнении кинематического расчёта привода часто возникает ситуация, когда потребная частота вращения двигателя находится в промежутке между стандартными её значениями. Обоснованный выбор быстроходного или тихоходного двигателя выполняется на основании техникоэкономических расчётов. Основой выбора является стоимость двух вариантов.
Стоимость привода складывается из стоимости электродвигателя, редуктора, ремённой передачи и муфты. В упрощённых расчётах в обоих вариантах следует принимать одинаковые редукторы, следовательно, варьируются размеры и стоимость только двигателей и деталей ремённых передач. В этом случае при наличии в приводе ремённой передачи стоимость каждого варианта в рублях определяют по формуле
С = Сэд + Сш1 + Сш2 + nзам z Ск, |
(13) |
где Сэд — стоимость электродвигателя (см. прил. Б); Сш1 и Сш2 — стоимость соответственно малого и большого шкива; Ск — стоимость клинового ремня (табл. 2); z — число клиновых ремней; nзам — число замен ремней за время службы привода.
Стоимость каждого шкива складывается из стоимости материала См и стоимости изготовления Си. Стоимость стальной или чугунной заготовки Сз = 25 р./кг. Стоимость материала определяется произведением:
См = СзVρ = Сзπd2Bρ/4, |
(14) |
24
где V — объём заготовки, мм3; ρ — плотность материала; плотность стали ρ = 7,85·10-6 кг/мм3; плотность чугуна ρ = 7,1 · 10-6 кг/мм3; d — расчётный диаметр шкива, мм; B — ширина шкива, мм, определяется по формуле
B = (z –1)e + 2f , |
(15) |
где e и f —параметры канавок шкива, мм [11].
Стальные диски проектируют при d < 400 мм. При больших диаметрах принимают чугунное литьё с ободом, ступицей и спицами. Для чугунных шкивов, которые из-за спиц имеют меньший объём, чем сплошной диск, стоимость материала следует определять умножением См из формулы (14) на 0,7. Стоимость изготовления Си зависит от размеров детали, сложности и времени её изготовления. Рекомендуются следующие значения:
при d < 200 мм Си = 350 р.;
при d = 224…500 мм Си = 600 р.; при d > 500 мм Си = 1000 р.
Число замен определяют (с округлением в большую сторону) по формуле
nзам = tΣ/ Lh , |
(16) |
где tΣ — ресурс привода, ч — формула (21) и табл. 5 в разд. 11; Lh —долговечность ремня, ч. Стоимость ремней по данным ООО «РЕМСБЫТКОМПЛЕКТ» приведена в табл. 2.
Таблица 2
Стоимость клиновых ремней
Сече- |
Длина ремня |
Стоимость |
Сече- |
Длина ремня |
Стоимость |
ние |
lр, мм |
ремня Ск, р. |
ние |
lр, мм |
ремня Ск, р. |
|
|
|
|
|
|
|
600 |
15,5 |
|
710 |
19 |
|
850 |
18 |
|
1060 |
25 |
|
950 |
20 |
|
1400 |
33 |
Z (О) |
1200 |
26 |
A (A) |
1900 |
39 |
|
1400 |
16 |
|
2240 |
46 |
|
1800 |
36 |
|
2500 |
51 |
|
2000 |
40 |
|
3000 |
62 |
Сече- |
Длина ремня |
Стоимость |
Сече- |
Длина ремня |
Стоимость |
ние |
lр, мм |
ремня Ск, р. |
ние |
lр, мм |
ремня Ск, р. |
|
|
|
|
|
|
|
950 |
36 |
|
1180 |
58 |
|
1400 |
52 |
|
1500 |
82 |
|
1900 |
60 |
|
2240 |
120 |
B (Б) |
2500 |
79 |
С (В) |
3350 |
180 |
|
3350 |
105 |
|
4350 |
210 |
|
4250 |
132 |
|
5300 |
285 |
|
6000 |
225 |
|
6300 |
355 |
Примечания: 1. Стоимость ремней, не вошедших в таблицу, следует рассчитывать методом интерполяции.
2.В обозначении сечения в скобках приведены обозначения русскими буквами по устаревшим стандартам.
Вприл. Б и в данном разделе приведена стоимость в рублях по состоянию на 1 марта 2010 г. В последующие годы для определения стоимости элементов следует умножать табличную стоимость на коэффициент инфляции, задаваемый преподавателем.
Пример 2. Выполнить технико-экономические расчёты по выбору оптимального электродвигателя привода, состоящего из клиноремённой передачи и двухступенчатого цилиндрического редуктора (см. схему задания № 01), по следующим исходным данным. Передаточные отношения ступеней редуктора: u2 = 3,55; u3 = 2,8; частота вращения приводного вала nIV = 50,93 об/мин, потребная частота
вращения вала электродвигателя n = 2278 об/мин; мощности на валах: РI = 7,55 кВт; РII = 7,17 кВт. Класс нагрузки Н 1,0 (постоянная).
Решение.
Приняты варианты электродвигателей с nэд = 2895 об/мин и nэд = 1440 об/мин (см. прил. Б). Общие передаточные отношения привода:
u′ = |
2895 |
= 56,84; |
u′′ = |
1440 |
= 28,27. |
|
50,93 |
|
|
50,93 |
|
Передаточные отношения ремённой передачи:
25
u′ = |
56,84 |
= 5,72; |
u′′= |
28,27 |
= 2,84. |
|
3,55 2,8 |
3,55 2,8 |
|||||
1 |
|
1 |
|
Вывод. Оба значения находятся в рекомендуемых пределах (см. прил. А).
Расчёты клиноремённой передачи выполняются по программе DM-9 в компьютерной системе GWBASIC. Исходные данные к расчётам:
вариант 1 – РI = 7,55 кВт; |
nэд = 2895 об/мин; |
u1′ = 5,72; |
вариант 2 – РI = 7,55 кВт; |
nэд = 1440 об/мин; |
u1′′ = 2,84. |
Алгоритм расчёта клиноремённой передачи приведен в разд. 15. Необходимые для техникоэкономических расчётов параметры приведены в табл. 3.
Порядок компьютерных расчётов
1. В папке DETALI выводят курсор на gwbasic.exe (вход в систему BASIC) и нажимают клавишу
ENTER.
2.Нажимают функциональную клавишу F3 (на дисплее высветится «LOAD» – загрузка) и набирают DM-9 ENTER.
3.Нажимают функциональную клавишу F2 (на дисплее высветится «RUN» – запуск) и набирают ENTER. Клавишу ENTER в дальнейшем нажимают после каждого ввода.
4.Вводят исходные данные (пример для быстроходного варианта):
7.55 — передаваемая мощность на валу ведущего шкива, кВт;
5.72 — передаточное отношение;
2895 — частота вращения ведущего вала, об/мин;
1 — спокойная нагрузка;
2 — число смен;
0 — оптимальное межосевое расстояние;
2 — клиноремённая передача;
2000 — необходимый ресурс ремня, ч;
1 — нормальное сечение;
4 — максимальное число ремней.
Распечатки результатов расчёта приведены на рис. 4 и 5.
********************************************************************
**************** Р А С Ч Е Т Н Ы Е П А Р А М Е Т Р Ы *****************
** Тип ремня |
А |
** |
** Межосевое расстояние (мм) |
527 |
|
** Передаточное отношение |
5.64 |
|
** Отклонение передаточного отношения (проц.) |
–1.4 |
|
** Длина ремня (мм) |
2000 |
|
** Диаметр ведущего шкива (мм) |
90 |
|
** Диаметр ведомого шкива (мм) |
500 |
|
** Сила предварительного натяжения (Н) |
1006 |
|
** Ресурс ремня (ч) |
2950 |
|
** Угол обхвата меньшего шкива (град) |
135 |
|
** Сила, действующая на валы (Н) |
1027 |
|
** Число клиновых ремней |
3 |
|
** |
|
** |
********************************************************************
Рис. 4. Распечатка результатов расчёта быстроходного варианта клиноременной передачи
26

********************************************************************
**************** Р А С Ч Е Т Н Ы Е П А Р А М Е Т Р Ы *****************
** Тип ремня |
|
|
|
|
|
А |
** |
|
||||
** Межосевое расстояние (мм) |
|
|
|
327 |
|
|
||||||
** Передаточное отношение |
|
|
|
3 |
|
|
||||||
** Отклонение передаточного отношения (проц.) |
|
5,36 |
|
|
||||||||
** Длина ремня (мм) |
|
|
|
|
|
1250 |
|
|
||||
** Диаметр ведущего шкива (мм) |
|
|
95 |
|
|
|||||||
** Диаметр ведомого шкива (мм) |
|
|
280 |
|
|
|||||||
** Сила предварительного натяжения (Н) |
|
|
1907 |
|
|
|||||||
** Ресурс ремня (ч) |
|
|
|
|
|
8562 |
|
|
||||
** Угол обхвата меньшего шкива (град) |
|
|
148 |
|
|
|||||||
** Сила, действующая на валы (Н) |
|
|
1929 |
|
|
|||||||
** Число клиновых ремней |
|
|
|
4 |
|
|
||||||
** |
|
|
|
|
|
|
|
|
** |
|||
******************************************************************** |
|
|||||||||||
|
|
|
|
|
|
|
Рис. 5. Распечатка результатов расчёта тихоходного варианта |
|||||
|
|
|
|
|
|
|
|
клиноременной передачи |
|
|
||
|
|
|
|
|
|
|
|
|
|
|
|
Таблица 3 |
|
|
|
|
|
|
|
Результаты расчётов клиноремённых передач |
|||||
|
|
|
|
|
|
|
|
|
|
|
|
|
|
|
Номер |
Сече- |
|
Длина |
|
Диаметр |
Диаметр |
Число |
Долговеч- |
|
|
|
|
ние |
|
ремня |
|
малого |
большого |
ремней |
ность рем- |
|
||
|
|
варианта |
|
|
|
|||||||
|
|
ремня |
|
lр, мм |
|
шкива d1, мм |
шкива d2, мм |
z |
ня Lh, ч |
|
|
|
|
|
|
|
|
|
|
|
|
|
|
|
|
|
|
1 |
А |
|
2000 |
|
90 |
500 |
3 |
2950 |
|
|
|
|
2 |
А |
|
1250 |
|
95 |
280 |
4 |
8562 |
|
|
|
|
Стоимость электродвигателей (см. прил. Б): |
|
|
|
|
||||||
|
|
АИР112М2/2895 – Ñ′ |
= 6200 р.; |
|
|
|
|
|
||||
|
|
|
|
|
ýä |
|
|
|
|
|
|
|
|
|
АИР132S4/1440 – Ñ′′ |
= 7100 р. |
|
|
|
|
|
||||
|
|
|
|
|
ýä |
|
|
|
|
|
|
При классе нагрузки Н1,0 ресурс привода tΣ = 32000 ч (см. табл. 5). За время работы привода не-
обходимо сделать число замен ремней: |
|
|
|
|
||
′ |
= tΣ/ Lh = 32000/2950 = 10,85 ≈ 11; |
|
|
|||
— в первом варианте nçàì |
|
|
||||
— во втором варианте n′′ |
= 32000/8562 = 3,74 ≈ 4. |
|
|
|
||
çàì |
|
|
|
|
|
|
Стоимость ремня сечения |
А длиной lр = 2000 мм |
′ |
= 41 р., длиной lр = 1250 мм |
′′ |
= 30 р. (по |
|
Ñê |
Ñýä |
|||||
интерполяции табл. 2). Стоимость ремней: |
|
|
|
|
||
— в первом варианте Ñ′ = n′ |
z Ñ′ = 11 · 3 · 41 = 1353 р.; |
|
|
|||
ð |
çàì |
ê |
|
|
|
|
— во втором варианте Ñð′′ |
= 4 · 4 · 30 = 480 р. |
|
|
|
|
Параметры шкивов для сечения А: расстояние от центра крайней канавки до торца шкива f = 15 мм, шаг канавок e = 12 мм [11]. Ширина шкивов по формуле (15):
Â′ = (3 – 1) · 12 + 2 · 15 = 54 мм; Â′′ = (4 – 1) · 12 + 2 · 15 = 66 мм.
Стоимость материала шкивов по формуле (14): Ñì′1 = 25 · π · 902 · 54 · 7,85 · 10-6 /4 = 67 р.; Ñì′ 2 = 0,7 · 25 · π · 5002 · 54 · 7,1 · 10-6 /4 = 1317 р.; Ñì′′1 = 25 · π · 952 · 66 · 7,85 · 10-6 /4 = 92 р.; Ñì′′2 = 25 · π · 2802 · 66 · 7,85 · 10-6 /4 = 798 р.
Стоимость шкивов
Ñø′ 1 = Ñì′1 + Си = 67 + 350 = 417 р.; Ñø′ 2 = 1317 + 600 = 1917 р.; Ñø′′1 = 92 + 350 = 442 р.; Ñø′′2 = 798 + 350 = 1148 р.
27
Общая стоимость вариантов согласно формуле (13):
Ñ′ = 6200 + 417 + 1917 + 1353 = 9887 р.;
Ñ′′ = 7100 + 442 + 1148 + 480 = 9170 р.
Выводы: 1. На основании технико-экономических расчётов принят электродвигатель АИР112М2/2895, с использованием которого привод оказался дешевле, чем с двигателем АИР132S4/1440.
2. Анализ последних расчётов показывает, что наибольшее влияние на стоимость вариантов оказывает стоимость электродвигателей, поэтому в большинстве случаев вариант с менее дорогим быстроходным двигателем оказывается дешевле.
10. МАШИНОСТРОИТЕЛЬНЫЕ МАТЕРИАЛЫ
Материалы деталей должны соответствовать основным критериям работоспособности и расчёта и требованиям технологичности и экономии. Машиностроительные материалы должны обладать достаточной прочностью и жёсткостью и высокой ударной вязкостью для восприятия динамических нагрузок. В машиностроении широко применяют чёрные металлы, точнее сплавы.
Чистые металлы в машиностроении не применяют.
К чёрным металлам относят стали и чугуны. Стали — сплавы железа с углеродом (обычно до 1,5 %) и другими элементами. Конструкционные стали содержат углерода до 0,55 %, обладают высокой прочностью, способностью к легированию, термической и химико-термической обработке. Стальные детали изготовляют давлением (прокаткой, ковкой, штамповкой), резанием, шлифованием, сваркой. Их литейные свойства низкие. В машинах применяют:
а) стали углеродистые обыкновенного качества, регламентируемые по механическим свойствам; используются без термообработки; обозначаются по типу «сталь Ст3 ГОСТ 380–88», где 3 — номер в порядке повышения прочности;
б) стали углеродистые качественные, маркируемые по химическому составу; обозначаются по типу «сталь 45 ГОСТ 1050–88», где 45 — содержание углерода в сотых долях процента (0,45 % углерода);
в) стали легированные — содержат кроме железа и углерода другие специально вводимые (легирующие) добавки, наличие которых дополнительно обозначают буквами названия легирующего элемента, например, В — вольфрам, Г — марганец, М — молибден, Н — никель, С — кремний, Т
— титан, Ф — ванадий, Ю — алюминий; пример обозначения: сталь 30ХГСА ГОСТ 4543–71, содержащая 0,3 % углерода, а также до 1 % хрома, марганца и кремния; буква А в конце обозначения свидетельствует о высоком качестве стали (с пониженным содержанием серы и фосфора).
Стали качественные и легированные подвергают термической и химико-термической обработке для повышения характеристик прочности и износостойкости. Термическую обработку применяют для повышения механических характеристик без изменения химического состава сталей. Применяют следующие виды термической обработки:
а) отжиг, заключающийся в том, что деталь нагревают до температур выше критических (не менее 750 °С) с последующим медленным охлаждением (вместе с выключенной печью);
б) нормализация — отжиг с охлаждением на воздухе (в штабеле с другими нагретыми деталями); эта термообработка более дешёвая и более распространённая, чем отжиг;
в) закалка — с нагревом до температур выше критических с последующим быстрым охлаждением (в масле или воде); после закалки вследствие искажения кристаллической решётки и появления в связи с этим больших внутренних напряжений деталь приобретает чрезвычайную хрупкость; её снижают обязательной следующей термической обработкой;
г) отпуск производят после закалки с нагревом деталей до температур ниже критических; высокотемпературный отпуск с нагревом до 600 °С в совокупности с закалкой называют улучшением; такую обработку выполняют для повышения твёрдости стали при сохранении высокой ударной вязкости; среднетемпературный отпуск (до 400 °С) выполняют для рессор и пружин; низкотемпературный (до 200 °С) — для режущего и мерительного инструмента.
Химико-термическая обработка заключается в насыщении поверхности детали элементами, повышающими её твёрдость и износостойкость при сохранении высокой ударной вязкости сердцевины. Насыщение азотом называется азотированием, насыщение углеродом — цементацией. Последующая за цементацией закалка с низким отпуском значительно повышает износостой-
кость и контактную прочность поверхности.
28
В учебном пособии [11], справочниках [2, 3, 8] и табл. 6 приведены механические характеристики сталей. В их числе предел прочности σв, МПа, предел текучести σт, МПа, предел выносливости σ-1, МПа, твёрдость по Бринеллю НВ и по Роквеллу HRC.
Чугуны — сплавы железа и углерода с содержанием последнего 2…6,67 % (обычно 2,2…4,3). Если углерод в структуре чугуна представлен в виде химического соединения Fe3C (цементита), то такие чугуны называют белыми. Они плохо обрабатываются и применяются в деталях с отбеленной поверхностью, например, для шкивов плоскоремённых передач с целью повышения твёрдости, износостойкости и коррозионной стойкости рабочей поверхности.
Серые чугуны содержат углерод в виде графита, их используют только в виде отливок, так как их пластичность практически равна нулю. Выплавляют серые чугуны СЧ10, 15, 20, 25, 30, 35 по ГОСТ 1412–85 и чугуны повышенной прочности с шаровидным графитом ВЧ35, 40, 45, 50, 60, 70 по ГОСТ 7293–85. Из серых чугунов отливают корпусные детали редукторов, крышки подшипников, станины, стойки, плиты и др.
Сплавы цветных металлов выполняют на основе алюминия, меди, олова и других металлов. Сплавы на основе алюминия и магния имеют высокую удельную прочность. Алюминиевые сплавы подразделяют на деформируемые (дюралюмины) и литейные (силумины). Применяют для корпусных деталей и в авиационной технике.
Многие цветные металлы используют как антифрикционные материалы в узлах трения. Латунь — сплав меди с цинком. Однофазная латунь — деформируемая (например, патронная
латунь), двухфазная — литейная, используется как антифрикционный материал.
Бронза — сплав меди с оловом, алюминием, железом и другими элементами, кроме цинка. Обладает высокими антифрикционными свойствами, сопротивлением коррозии и технологичностью. Наилучшие антифрикционные свойства у оловянистых бронз, например, БрО10Ф1 ГОСТ 613–79. Безоловянистые бронзы, например, БрА10Ж4Л ГОСТ 493–79, обладают высокими механическими характеристиками, но их антифрикционные свойства хуже, чем оловянистых.
Пластические массы — материалы на основе высокомолекулярных органических соединений. По природе смол пластмассы подразделяют на термореактивные и термопластичные. Термореактивные смолы в процессе изготовления под действием высокой температуры становятся неплавкими (текстолит, гетинакс, стеклопласты и др.). Термопластичные пластмассы, размягчающиеся при высокой температуре, пригодны для повторного использования (полиэтилен, фторопласты, полиамиды, полиуретаны и др.).
11. РАСЧЁТ ЦИЛИНДРИЧЕСКОЙ ЗУБЧАТОЙ ПЕРЕДАЧИ
Основными критериями работоспособности и расчёта зубчатых передач являются контактная и изгибная прочность.
11.1.Коэффициент долговечности
Взубчатом зацеплении передача движения осуществляется за счет непосредственного контакта сопряжённых зубьев. Наиболее распространено эвольвентное зацепление. Теория зубчатого зацепления изложена в учебных пособиях [4, 5]. Зубчатые передачи рассчитаны на длительную работу. При наработке меньше базовой размеры передачи могут быть уменьшены вследствие повышения предельных и допускаемых напряжений. На рис. 6 приведена кривая выносливости материала, по
которой принимают предел выносливости σ0lim . Он соответствует базовому числу циклов NG. При числе циклов нагружения N < NG предельное напряжение σ′lim будет иметь большее значение и его следует принимать по криволинейному участку, который соответствует уравнению
(σ′lim )m N = (σ0lim )m NG = const . |
(17) |
29
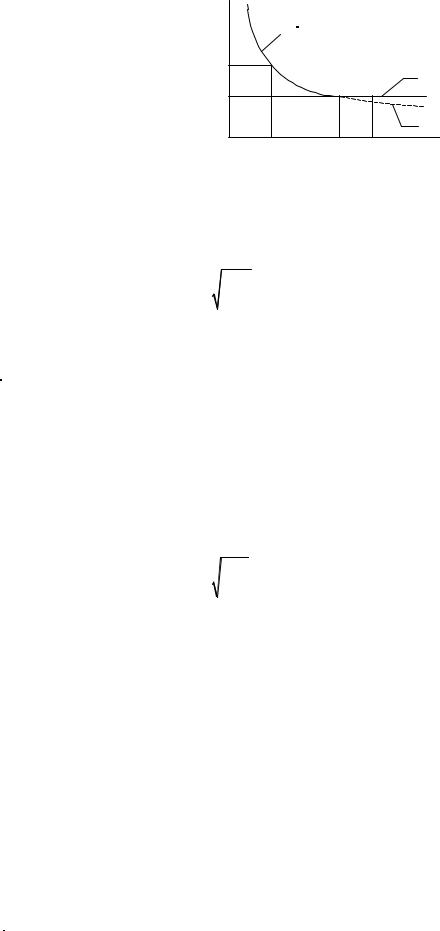
σ |
σm N = const |
|
|
|
|
||
σ' |
|
|
|
lim |
|
1 |
|
|
|
|
|
σo |
|
|
|
lim |
|
|
|
|
|
2 |
|
|
N < NG |
NG N > NG |
N |
|
Рис. 6. Кривая выносливости |
|
Показатель степени т характеризует крутизну наклона кривой выносливости. Число циклов нагружения учитывают коэффициентами долговечности КНд и КFд. При N ≥ NG КНд = КFд = 1. Эти коэффициенты также учитывают переменность нагрузки. При постоянной нагрузке класс Н 1,0. Он соответствует коэффициенту эквивалентности KНE = 1. Коэффициент долговечности по контактным напряжениям определяют по формуле
|
|
|
|
KHä = KHE 3 |
|
N |
≤1, |
|
|
(18) |
|
||||
|
|
|
|
|
|
|
|
||||||||
|
|
|
|
|
|
|
NHG |
|
|
|
|
|
|||
где NHG — база контактных напряжений, принимается по табл. 4. |
|||||||||||||||
|
|
|
|
|
|
|
|
|
|
|
|
|
|
Таблица 4 |
|
|
|
|
|
|
|
|
База контактных напряжений |
||||||||
|
|
|
|
|
|
|
|
|
|
|
|
||||
Средняя твёрдость поверх- |
|
200 |
250 |
|
300 |
350 |
– |
– |
– |
|
|||||
|
|
|
|
||||||||||||
ности HB |
|||||||||||||||
|
|
|
|
|
|
|
|
|
|
|
|||||
Средняя твёрдость поверх- |
|
– |
25 |
|
32 |
38 |
47 |
56 |
60 |
|
|||||
|
|
|
|
|
|
|
|||||||||
ности HRC |
|
|
|||||||||||||
|
|
|
|
|
|
|
|
|
|
|
|||||
|
|
|
|
|
|
|
|
|
|
|
|||||
NHG, млн циклов |
|
10 |
17 |
|
25 |
36 |
68 |
114 |
143 |
|
Примечания: 1. Для промежуточных значений твёрдости базу контактных напряжений определять методом линейной интерполяции.
2. В таблице приведена твёрдость поверхности в различных единицах измерения (HB и HRC), что позволяет определить соответствие между ними.
Коэффициент долговечности по изгибу: |
|
||||
|
|
|
|
|
|
KFä = KFE m |
N |
|
≤1 , |
(19) |
|
|
|||||
|
|
NFG |
|
где NFG — база изгибных напряжений; m — показатель степени; принимать т = 6 и NFG = 10·106 при твёрдости сердцевины H ≤ 350НВ; т = 9 и NFG = 150·106 при твёрдости сердцевины H ≥ 40
HRC.
Коэффициент эквивалентности по изгибным напряжениям KFE и базовый ресурс tΣ прини-
мать по табл. 5.
Наработка (число циклов нагружения) при постоянной частоте вращения:
N = 60cnt∑ , |
(20) |
где с — число потоков мощности; в планетарном редукторе оно равно числу сателлитов (с = пс); в обычных редукторах с = 1; п — частота вращения вала зубчатой передачи, об/мин; tΣ — машинное время (ресурс), ч, определяется по формуле
t∑ = L S 2008Ï Â , |
(21) |
где L — срок службы привода, лет; S — число смен работы, рекомендуется принимать S = 2; 2008
— число рабочих часов в году, равно 40 · 52 – 9 · 8 (40 — число рабочих часов в неделю; 52 — число недель в году; 9 — количество праздничных дней в году; 8 — число часов работы в одну смену); ПВ — относительная продолжительность включения, принимать ПВ = 0,15 при лёгком режиме, ПВ = 0,25 при среднем режиме, ПВ = 0,4 при тяжёлом режиме.
Таблица 5
Коэффициенты эквивалентности
Класс |
Коэф. эквива- |
Коэф. эквива- |
Коэф. эквива- |
Базовый |
|
|
|
|
|
30 |
|
|
|
|