
692
.pdfСенной площадях и в других районах города. При этом, как правило, огромные строительные площадки загромождаются металлоломом, лесоматериалами, тюбингами и различным мусором, что неизбежно приводило к пожарам (на Сенной площади, ул. Чкалова и т.д.);
—применение двухэтажной кабины вместимостью по 75 чел. на каждом этаже позволит ограничиться проходкой ствола круглого сечения диаметром 8,5 м для каждого входа с размещением в них по два лифта (всего на станции их четыре). Экономический эффект возрастает в 1,7 раза;
—необходимо разработать новую технологию и организацию возведения станции метрополитена в условиях плотно застроенной центральной части города, основывающейся на ранее реализованных рациональных решениях с размещением подъемных машин в башенных копрах; целесообразно использовать многоканатные подъемные машины в качестве одноканатных; опускную крепь для стволов некруглого сечения, жидкий азот для замораживания и другое с целью сокращения объемов строительной площадки [Метро. 1993. № 3. С. 26–27].
Несмотря на ряд неоспоримых преимуществ предложенного для ст. «Адмиралтейская» решения о замене сочетания эскалатор–лифт на лифтовой подъем, оно имеет и ряд существенных недостатков. В частности, этому решению можно противопоставить преимущество эскалаторов, заключающееся в возможности эвакуации пассажиров по лестницам в случае отключения электроэнергии. Кроме того, для электроснабжения лифтов требуются автономные дизель-электрические источники.
Возможно и другое решение проблемы — эвакуация пассажиров по тоннелю, оборудованному движущимися тротуарами, аналогичными существующими в аэропорту Пулково.
Разработаны три возможных варианта соединения тоннелями с траволаторами платформы ст. «Адмиралтейская» с прилегающими территориями центральной части города: 1 — с садом у Зимнего дворца и Эрмитажа; 2 — с садом у здания Адмиралтейства (рис. 1.12, а); 3 — с садом на Исаковской площади (рис. 1.12, б).
Во всех вариантах, кроме решения задачи по эвакуации в аварийных ситуациях, предусмотрена связь подземной станции метрополитена с наиболее посещаемыми жителями города туристическими центрами, такими как Эрмитаж, Зимний дворец, Казанский и Исаакиевский соборы. Соединение станции с отелем «Астория» облегчает перемещение гостей и деловых людей, проживающих в гостинице, без использования наземного транспорта и исключает пересечение улиц и площадей, не оборудованных подземными переходами.
Оборудование подъемников возможно за счет применения комплекса лифтов «ОТИС 2000R» с вместимостью кабин 5, 8, 13 чел. при высоте машинных помещений, не превышающих 3 м.
Освоение подземного пространства города в настоящее время решается специализированной организацией «Ленподземстрой». Ее проекты предусматривают возведение бытовых, культурных и торговых объектов под площадями Восстания, Труда, Мужест-ва и т.д.
Таким образом, предлагаемое решение проблем, связанное с безопасностью пассажиров метрополитена за счет использования тоннелей с траволаторами, соединяющими ст. «Адмиралтейская» с наиболее посещаемыми объектами, обеспечит значительный экономический эффект. Применение лифтовых входов на этой станции сохранит от разрушения здания в Кирпичном переулке и на ул. Гоголя, исключит переселение жителей этих домов из центра в другие районы города, а следовательно, имеет огромную социальную значимость.
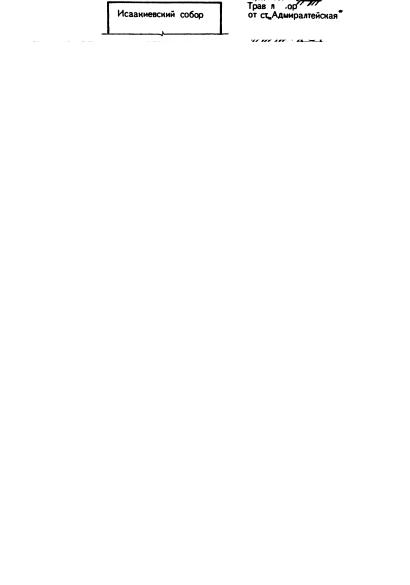
а)
б)
Рис. 1.12. Варианты соединения тоннелями с траволаторами платформы ст. «Адмиралтейская» с центральной частью города
2. СТРОИТЕЛЬСТВО ШАХТНЫХ СТВОЛОВ
2.1. Этапы развития и совершенствования технологий строительства шахтных стволов
Строительство метрополитенов закрытым способом, как правило, осуществляют через шахтные стволы, глубина которых определяется глубиной заложения линии метрополитена и колеблется в пределах от 20 до 80 м. Шахтные стволы располагают в 10– 20 м от оси основных сооружений метрополитена, увязывая их местоположение с принятой системой вентиляции с целью рационального использования стволов в качестве постоянных сооружений. На практике чаще всего применяют стволы кругового очертания внутренним диаметром 5,1 и 5,6 м, что позволяет использовать для них типовые обделки перегонных тоннелей. Неглубокие стволы подземных вестибюлей метрополитена, через которые выполняют работы по замене оборудования эскалаторов, могут иметь прямоугольное сечение [1, гл. 1; 2, гл. 1; 41–42, гл. 6; 46, гл. 5].
Длительное время на проходке стволов при строительстве метрополитенов использовали большой объем ручного и небезопас-ного труда. Первый подвесной механизированный полок для шахтных стволов метрополитена был разработан специалистами Метрогипротранса и изготовлен заводом № 5 Мосметростроя в 1960 г. Полок был выполнен в виде металлической конструкции с проемами для бадьевого и грузового
подъемов и подвешивался через прицепное устройство и направляющие блоки к лебедке, установленной на поверхности. Полок оснащался механизмами для погрузки разработанного грунта в бадью и сборки обделки и позволял вести механизированную проходку ствола сразу после сооружения форшахты. На одной балке полка был закреплен тельфер ТЭ-2 с грейферным погрузчиком КС-3, на другой шарнирно-грузовой барабан тельфера с приспособлением для монтажа элементов обделки. В рабочем положении полок фиксировался выдвижными балками и распирался в ребра обделки. Конструкция полка позволяла одновременно с проходкой осуществлять армировку ствола непосредственно с полка. Впервые полок был применен СМУ № 6 при проходке ствола на Калужском радиусе. Средняя скорость проходки ствола составила 1,7 м/сут. После окончания работ полок был использован СМУ № 3 на стволе шахты № 708-бис, при этом погрузчик КС-3 был заменен на БЧ-1у.
В 1987 г. при проходке ствола диаметром 8,5 м применили механизированный полок с ковшовой гидравлической погрузочной машиной принудительного действия, разработанной ЦНИИподземмашем. Полок имел центральную трубу, установленную в толстостенной цилиндрической обойме с возможностью вращения от гидравлического привода вокруг вертикальной оси. На трубе жестко крепилась погрузочная машина, способная разрабатывать и грузить грунт прочностью 100–1200 Н/см² без предварительного рыхления, а более крепкие грунты — после буровзрывной разработки. Конструкция машины позволяет использовать ее при сооружении стволов диаметром от 6 до 8,5 м.
С1986 г. стали интенсивно внедряться технологии сооружения стволов с помощью механизированных стволопроходческих комплексов КСПМ, механизированных опалубок типа ОШ и ОШС (ОСМГ), передвижных опалубок, исключающих необходимость возведения временной крепи и др.
Наиболее механизированными в настоящее время являются работы по проходке стволов глубиной до 15 м, с помощью экскаваторов типа «Поклен» и «Атлас», на долю которых приходится около 80 % объема механизированной разработки грунта; удельный вес разработки забоя грейферами составляет около 17 %.
С1989 г. для проходки стволов глубиной до 40 м стали применять механизированный комплекс «КБШ» с креплением монолитным бетоном, предполагающий применение совмещенной технологической схемы работ. При работе забойного звена из двух проходчиков комплекс обеспечивает скорость проходки ствола до 100 м/мес.
Проходка вертикальных стволов в слабых неустойчивых грунтах длительное время оставалась весьма трудоемким и небезопасным процессом до внедрения способа опускной крепи, при котором основные операции выносятся на поверхность. Впервые он был применен в период Великой Отечественной войны на строительстве IV очереди Московского метрополитена с использованием активной регулируемой нагрузки, создаваемой гидравлическими домкратами. Однако тогда основной недостаток способа — большие нагрузки, вызываемые трением опускной крепи о грунт, преодолеть не удалось.
Этот недостаток был устранен после разработки способа опускной крепи в тиксотропной оболочке (рубашке) при котором слой глинистого раствора между погружаемой крепью и грунтом практически полностью снимает сопротивление сил трения.
Впервые в практике отечественного метростроения проходка шахтного ствола способом погружения крепи в тиксотропной оболочке (ПКТО) была осуществлена в 1971 г. по предложению специалистов ЦНИИподземмаша и СМУ № 6 на строительстве ЖдановскоКраснопресненского диаметра Московского метропо-литена. В том же году этот метод применили при сооружении шахтного ствола на перегоне между станциями «Пушкинская» и «Баррикадная», а в 1975 г. — на Рижском радиусе. Среднемесячные скорости проходки стволов были достаточно скромны и составляли: при разработке забоя механизированным способом 0,5–0,6 м/смену, при разработке забоя вручную — 0,2–0,3 м/смену.
В настоящее время работы по проходке стволов регламентируются требованиями СП 32-105- 2004, и для обоснованного выбора технологии должны быть проведены подробные изыскания и исследования инженерно-геологических и других условий в пределах участка сооружения ствола.
При этом для точного определения положения контакта водоносных грунтов и водоупора по периметру ствола необходимо закладывать не менее трех геологических скважин.
При сооружении стволов обычным способом (согласно пп. 3.2, 3.3 СНиП Ш-44-77) следует использовать надшахтный комплекс оборудования (копер, подъемную машину, бункерную и тельферную эстакаду и др.), предназначенный для основных тоннельных работ. Надшахтный копер при сборной обделке ствола допускается сооружать из тюбинговых колец.
Временные сооружения и оборудование, необходимые для проходки стволов методом ПКТО, могут размещаться в пределах призмы обрушения только с принятием мер по обеспечению их нормальной работы в случае возможной деформации грунта. Способ закрепления осей опускной крепи на местности должен обеспечивать возможность проверки их положения в любой момент ее погружения. Реперы для контроля вертикальных отметок надлежит устанавливать за пределами возможных осадок и перемещений грунта. При этом сооружение устьевого участка ствола с воротником следует осуществлять в открытом котловане с использованием подвижного кранового оборудования, а отметка подошвы котлована должна быть не менее чем на 0,5 м выше уровня грунтовых вод.
Бетон в конструкцию воротника следует укладывать после установки футляров для инженерных коммуникаций, а при способе опускной крепи — также тампонажных трубок для заполнения пустот в основании сооружения, анкерных стоек и болтов крепления направляющих брусьев. Правильность установки закладных деталей должна подтверждаться актом на скрытые работы. Укладку бетона необходимо выполнять послойно и равномерно по периметру ствола с систематическим контролем положения закладных деталей и опалубки. Распалубку конструкции разрешается производить по достижении бетоном не менее 50 % проектной прочности. Снятие наружной опалубки перед засыпкой пазух котлована является обязательным.
Обделка ствола должна возвышаться над уровнем строительной площадки не менее чем на 0,5 м.
Качество сборки ножевой части и монтажа колец в пределах опорного воротника при проходке ствола методом ПКТО должно быть обследовано техническим надзором с участием представителя маркшейдерской службы и зафиксировано актом на скрытые работы. Правильный монтаж оборудования, обеспечивающий безопасность работ, должен быть зафиксирован актом с участием представителя отдела техники безопасности, главного механика вышестоящей организации и горно-технической инспекции. Акт приемки выполненных подготовительных работ и монтажа механизмов является разрешением на производство работ по погружению крепи.
При проходке стволов в нескальных грунтах глубина заходки не должна превышать ширину кольца более чем на 10–15 см. Малоустойчивые грунты следует разрабатывать в две заходки по 50–60 см, начиная от центра забоя и заканчивая у внутренней поверхности тюбингового крепления, с окончательной доборкой грунта по мере установки тюбингов. В случае обнаружения плывунных грунтов необходимо остановить работы и вызвать представителя проектной организации. При наличии притока грунтовых вод проходку ствола следует вести с опережающим водосборником.
При проходке стволов с предварительным замораживанием грунтов на каждой заходке следует сначала разрабатывать грунт в пределах не замороженного ядра, а затем разрабатывать замороженный грунт. При разработке грунта внутри ледогрунтового ограждения, вода, остающаяся в не замороженном состоянии, также должна удаляться. В случае поступления в забой значительного количества воды, указывающего на наличие изъяна в ледогрунтовом ограждении, работы должны быть приостановлены. Ствол необходимо залить водой до нормального уровня грунтовых вод и провести дополнительное замораживание грунтов.
Временную крепь при проходке стволов с монолитной бетонной обделкой в неустойчивых нескальных грунтах следует выполнять из металлических колец, устанавливаемых на расстоянии не более 1 м, с затяжкой боковой поверхности досками, а в малоустойчивых
скальных грунтах — анкерной с металлической сеткой или из набрызг-бетона. Металлические сегменты в кольцах необходимо соединять профильными накладками и штырями, обеспечивающими кольцам необходимую жесткость, а подвеску колец выполнять на стальных крючьях — не менее двух на каждый сегмент. Между кольцами следует устанавливать распорные стойки по числу крючьев. Все пустоты за деревянной затяжкой должны быть тщательно забучены [46, гл. 5].
Тампонаж пустот за обделкой (первичное нагнетание) при проходке стволов обычным способом в нескальных и малоустойчивых скальных грунтах следует производить за каждым установленным кольцом вне зависимости от наличия временного крепления выработки.
Разработку грунта при проходке ствола способом опускной крепи в несвязных и слабых глинистых грунтах следует выполнять стреловым краном, оборудованным грейфером. Совмещение ручной разработки грунта с одновременной выдачей его из ствола грейфером не допускается. Погружать крепь необходимо одновременно с разработкой забоя по мере выемки грунта. Для исключения прорыва глинистого раствора
взабой ствола и обрушения грунта выработки необходимо:
—обеспечивать своевременную подачу глинистого раствора в пространство, образуемое уступом ножевой части, чтобы уровень раствора постоянно находился выше подошвы опорного воротника на 2 м;
—обеспечивать, чтобы в зоне неустойчивых несвязных грунтов при погружении крепи ее ножевая часть была постоянно вдавлена в грунт не менее чем на 0,5 м;
—разработку грунта выполнять слоями по 0,3–0,5 м, не допускать опережения средней
частью забоя нижней кромки ножа более чем на 0,5 м;
—при пересечении зоны несвязных водоносных и плывунных грунтов погружение крепи осуществлять под слоем воды, уровень которой в стволе должен превышать уровень водоносного горизонта не менее чем на 1 м, а выемку грунта производить из средней части забоя с оставлением по контуру выработки бермы, срезаемой ножевой частью при погружении крепи; откачку воды начинать только после погружения ножевой части в водоупор на глубину не менее 1,5 м;
—предусматривать средства быстрой подачи воды в ствол на случай необходимости его аварийного затопления.
Проверка вертикальности опускной крепи и положения в плане должна выполняться после каждой посадки крепи и не реже чем через 1 м по мере ее опускания; замеченные смещения и перекосы должны выправляться немедленно.
Тампонаж пространства за крепью, заполненного тиксотропным раствором, должен осуществляться путем замены глинистого раствора цементно-песчаным после проходки ствола. В отдельных случаях, при обосновании, глинистый раствор может быть оставлен за крепью.
При сооружении стволов обычным способом в обводненных или искусственно замороженных несвязных водонасыщенных грунтах и плывунах гидроизоляционные работы необходимо выполнять в процессе проходческих работ. При этом болтовые комплекты с гидроизоляционными шайбами следует устанавливать при монтаже обделки, а контрольное нагнетание производить в непосредственной близости от забоя с подвесного полка. Дополнительное контрольное нагнетание, подтяжку болтов, замену при необходимости болтовых комплектов, а также чеканку швов тюбинговой обделки следует вести с временных полков. При проходке стволов с применением БВР чеканочные работы рекомендуется выполнять на расстоянии 20–30 м от забоя. При сооружении рабочих стволов в условиях отсутствия притока воды гидроизоляционные работы допускается не производить.
При монтаже колец обделки, погружаемой в тиксотропной оболочке, болтовые
скрепления и пробки в отверстия для нагнетания необходимо устанавливать с гидроизоляционными шайбами, швы между тюбингами конопатить просмоленным канатом. Чеканочные работы выполнять после окончания проходки ствола.
Бетонирование монолитной обделки ствола, проходимого обычным способом, следует выполнять с применением передвижной опалубки участками по 4–6 м. Положение опалубки и
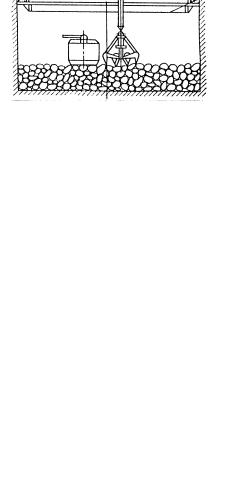
состояние крепления выработки должно систематически контролироваться маркшейдерской службой. Положение обделки ствола относительно вертикальной оси следует проверять через дватри цикла передвижки опалубки, которая производится после достижения бетоном прочности на сжатие не менее 0,8 МПа.
Подачу бетонной смеси за опалубку следует предусматривать бетоноводами, с креплением их к расстрелам. При повышенных требованиях к качеству бетона транспортировать бетонную смесь необходимо в условиях, исключающих ухудшение ее свойств. При этом отклонение стенок монолитной бетонной обделки ствола по радиусу от центра ствола должно быть в пределах 50 мм, а величина уступов на контактах смежных заходок — не более 30 мм.
При подаче бетонной смеси в ствол по вертикальным трубам при выходе ее из бетонопровода имеет место расслаивание. Для предотвращения этого следует применять легкие, но достаточно прочные заполнители, например доменные шлаки. Бетонная смесь в процессе движения по трубопроводу расчленяется на отдельные порции массой 15…20 кг (6–8 л), внутри которых расслаивания не происходит. Благодаря этому при падении порций смеси в приемный сосуд (бункер, за опалубку) происходит вторичное перемешивание с ранее уложенной смесью и восстановление однородности бетона.
Применяющиеся в настоящее время системы разводки бетонной смеси позволяют комплексно ме-ханизировать процесс воз-ведения постоянной кре-пи в стволе при минимальных затратах труда и времени. При обычной схеме разводки (рис. 2.1) к нижней части гасителя скорости крепят хобот, состоящий из набора конусных патрубков, соединяемых между собой серьгами. Такая конструкция хобота позволяет перемещать его для направления бетонной смеси за опалубку. Длина хобота легко регулируется изменением числа пат-рубков. Удельная продол-жительность возведения постоянной крепи в стволе с использованием передвижных призабойных опалубок без совмещения производства работ с про-ходческими (погрузкой) обычно не превышает 2–3 ч. При частичном совмещении этих работ удельная продолжительность возведения крепи, снижается до 0,5– 1,0 ч.
Установку временных расстрелов для вентиляционного трубопровода и других коммуникаций, армирование ствола, устройство лестниц для периода строительства при проходке ствола обычным способом следует выполнять с подвесного и рабочих полков. Армирование ствола с установкой направляющих проводников для клетьевого подъема допускается выполнять только при незамороженных грунтах. Армирование надшахтного копра следует проводить с подвесного полка, используемого для проходки и армирования ствола.
На участке проходки с опускной крепью армирование следует выполнять после завершения проходческих и гидроизоляционных работ.
Для монтажа армировки необходима предварительная установка контрольного яруса. Монтаж армировки сверху вниз следует выполнять по отвесам. При армировании в направлении снизу вверх установку контрольного яруса на горизонте
околоствольного двора также необходимо выполнять по отвесам, опущенным с верхнего контрольного яруса или с помощью проекциометра. Горизонтальность расстрелов следует обеспечивать с помощью металлических подкладок под их полки, а заделку лунок в бетонной обделке необходимо выполнять после сборки и проверки правильности установки всех расстрелов яруса.
Предназначенные для строительства трубопроводы водоотлива, вентиляции, подачи сжатого воздуха и воды следует крепить к обделке ствола. При этом вентиляционные трубопроводы до подвесного полка должны быть жесткими, от подвесного полка до забоя
— гибкими. Короткие расстрелы и мелкие детали армировки следует спускать в ствол в бадьях, а длинные — при помощи серьги на канате.
Контроль геометрических параметров армировки (расположения расстрелов и проводников) необходимо осуществлять по результатам маркшейдерской съемки. Качество работ по монтажу армировки следует определять выборочным контролем.
При монтаже армировки необходимо соблюдать следующие допуски: отклонение расстояний между ярусами расстрелов от проектного положения ± 15 мм; разность в положении расстрела по высоте в местах крепления к тюбингам не более 1:200 его длины; отклонение расстрелов на двух смежных ярусах по вертикали ±5 мм; отклонение каждого проводника от вертикали ±5 мм; смещение стыков проводников от середины ребра расстрелов ±50 мм; отклонение армировки по всей высоте ствола от проектного вертикального положения — не более 1:2000 глубины ствола.
Остаточный приток воды в ствол после завершения его проходки не должен превышать 0,15 м3/ч. После окончания строительных работ следует выполнить ремонт гидроизоляции до полного устранения фильтрации воды через обделку.
2.2.Шахтные комплексы
2.2.1.Горный комплекс на поверхности
Совершенствование проходческой техники и технологии сооружения тоннелей и связанное с этим увеличение темпов проходки и, соответственно, объемов выдаваемого на поверхность грунта и опускаемых вниз материалов потребовало механизировать, а затем и автоматизировать горные комплексы на поверхности, обеспечить более четкую и производительную работу откаточных средств и шахтных подъемов. Наиболее трудным звеном в механизации стала поверхностная откатка на горизонте верхних приемных площадок бункерных эстакад [25, гл. 8].
Для устранения этого узкого места в 1955 г. Мосметростроем и Метрогипротрансом была разработана и внедрена на шахте № 512 Щербаковского радиуса в опытном порядке комплексная механизация работ на верхней приемной площадке для транспортировки грунта в вагонетках емкостью 1,5 м3 (взамен вагонеток емкостью 0,75 м3).
Эстакада была оборудована тремя поперечными тележками, двумя толкателями верхнего действия, двумя круговыми опрокидами, компенсатором высоты, гасителями скорости, а также имела в одном конце вспомогательный подъем. Общая длина откаточного горизонта составила 53,4 м, ширина — 7 м. На этой шахте были впервые установлены выдвижные автоматические решетки для перекрытия клетьевых проемов ствола независимо от стволового.
Общий уровень механизации работ на эстакаде составил 92 % против 35 % на обычной, а ее производительность повысилась на 150 %. В дальнейшем такие горные шахтные комплексы нашли применение при строительстве тоннелей на линиях глубокого заложения. Одновременно на шахте была изменена схема околоствольных выработок и организована круговая откатка подвижного состава за счет устройства двустороннего околоствольного двора с подходной выработкой и обгонной штольней от прокладываемой трассы тоннелей, а также осуществлена механизация откатки с применением толкателей верхнего действия. Такая организация и механизация работ позволили сократить трудоемкость откатки 1 м3 грунта в 2,6 раза.
Впроцессе совершенствования технологий строительства метрополитенов совершенствовалась
икомпоновка горного комплекса на поверхности. В частности, при строительстве ст. «Площадь 1905 года» в г. Екатеринбурге была принята компоновка горного комплекса с использованием бокового опрокида БОК-1М и козлового крана КК-4 (рис. 2.2).
Такая компоновка позволила в 2,8 раза (по сравнению с традиционной) сократить расход металлоконструкций, уменьшить на 3 м высоту копра и снизить стоимость комплекса.

Спуск и подъем осуществлялся по стволу диаметром 5,6 м с обделкой из чугунных тюбингов. Ствол был оборудован двумя шахтными грузолюдскими клетями 3×1,5 м. Здание подъемной машины 2БМ-2500 смонтировано из трехслойных панелей типа «сэндвич» по несущему металлическому каркасу.
Центральными звеньями комплекса являются грунтовая и материальная эстакады. Первая, длиной 32 м, имеет три ветки путей с колеей 600 мм и оборудована боковым опрокидом, обеспечивающим нормативные скорости проходки перегонных тоннелей с помощью агрегата АБТ-5,5. Аккумулирование грунта осуществляется в глухих полуторакубовых вагонетках, которые отстаиваются в двухпутевой подходной выработке длиной более 100 м. Порожняк накапливается в грунтовой эстакаде, оборудованной толкателем верхнего действия.
Материальная эстакада длиной около 20 м располагается по другую сторону ствола, являясь продолжением грунтовой эстакады. Она оборудована монорельсом для электротельфера грузоподъемностью 3,2 т и, кроме того, обслуживается одной консолью козлового крана КК-4. Спуск длинномерных материалов и оборудования осуществляется по лесоспускному отделению ствола при помощи лебедки ЛТМ-5. Ходовое отделение ствола через подземную галерею соединяется с поверхностью рядом с грунтовой эстакадой.
Рис. 2.2. Горный комплекс на стройплощадке:
1 — трехкамерный шлакоотстойник; 2, 4 — площадки для складирования материалов; 3 — двухконсольный козловой кран; 5 — навес лебедки лесоспуска; 6 — грунтовая эстакада; 7 — пандусный съезд; 8 — боковой опрокид;
9 — подъездная дорога; 10 — здание подъемной машины; 11 — шахтный ствол; 12 — склад цемента; 13 — ленточный конвейер; 14 — материальная эстакада; 15 — склад сыпучих материалов; 16 — копер из чугунных тюбингов
У материальной эстакады смонтирован расходный склад цемента емкостью 25 т. Здесь же расположен склад песка, который грузят в вагонетки при помощи ленточного перегружателя. Для увеличения производительности горного комплекса предусматривается устройство второго бокового опрокида со стороны материальной эстакады.
Простота и надежность в связи с уменьшением количества механизмов; работа в одном уровне, значительно повышающая безопасность труда; удешевление и сокращение сроков строительства; снижение затрат на отопление комплекса в зимний период — основные преимущества этой компоновки.
Более детально варианты подъемов и типы шахтных комплексов для линий метрополитенов глубокого и мелкого заложения рассмотрены в «Справочнике инженера-тоннельщика» [38, гл. 20].
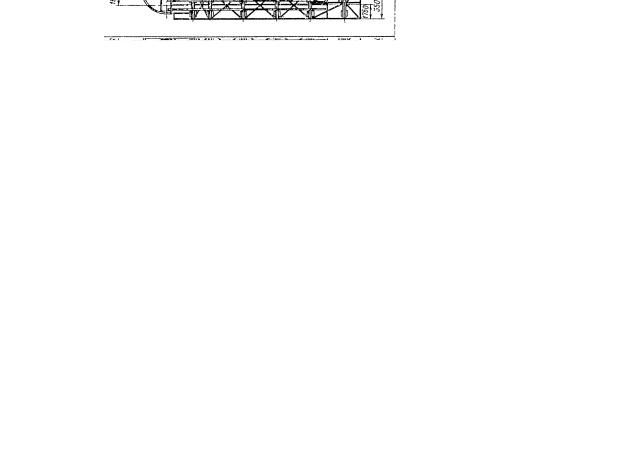
2.2.2. Высокопроизводительные шахтные комплексы для метрополитенов
Уже первая скоростная проходка на шахте № 218 Ленметростроя показала, что дальнейшее повышение строительных темпов невозможно, если производительность вертикального подъема не будет увеличена. Так как возможности двухклетьевого подъема оказались полностью исчерпаны, выдвигалось даже предложение сооружать не один, а два ствола, чтобы на забой работали два подъема.
Однако в СМУ № 15 Ленметростроя считали несколько иначе [Метрострой. 1981. № 4. С. 20–22] и, когда было принято решение осуществить очередную скоростную проходку на шахте № 410, обратились к проектировщикам с предложением производить спуск блоков не клетью, а специальным устройством, используя отделение лесоспуска. Такой проект (рис. 2.3) был создан Ленметрогипротрансом.
На эстакаде 1 горного комплекса блоки грузились на специальную тележку 2, затем с помощью лебедки 3 по стволу опускались в околоствольный двор и там, на разгрузочной эстакаде 4, поступали на тюбинговозки.
Предложенный спецспуск позволил частично разделить грузопотоки и повысить производительность подъема на 14–16 %. В итоге был достигнут новый рекорд проходки перегонных тоннелей — 876 м/мес.
Однако подъем со спецспуском имел ряд недостатков: он металлоемок, монтаж его требовал длительного времени. Поиски новых путей привели к созданию трехклетьевого подъема.
Рис. 2.3. Устройство для опускания блоков обделки через отделение лесоспуска
Созданный Ленметрогипротрансом совместно со строителями проект (рис. 2.4) предусматривал в стволе с тем же внутренним диаметром размещение не только трех клетей (причем третья — с противовесом), но и пропуск в околоствольный двор всех коммуникаций: кабелей, водопровода, сжатого воздуха, труб постоянного и аварийного водоотлива, воздуховодов, лестничного отделения для спуска в шахту длинномеров. При этом пришлось уменьшить габарит клети до минимальных размеров (2,8×1,15 м).
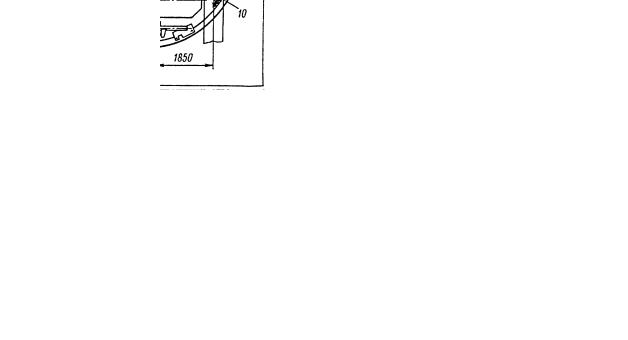
Рис. 2.4. Трехклетьевой подъем:
1 — противовес клети; 2 — отделение лесоспуска; 3 — лестница; 4 — водоотлив; 5 — водоотлив аварийный; 6 — водопровод; 7 — сжатый воздух; 8 — воздуховоды; 9 — кабели
диспетчерской связи; 10 — электрокабели
Достоинства трехклетьевого подъема, прежде всего, в более полном разделении грузопотоков: хотя все три клети грузолюдские, две из них работают только на подъем вагонеток с породой, а третья — с противовесом, подает в шахту не только блоки, но и вагонетки с материалом, а также опускает и поднимает людей. Удобно и то, что она работает с нулевого горизонта и нет надобности в переподъеме материалов.
Трехклетьевой подъем прост в монтаже, более безопасен в эксплуатации. Горные комплексы с трехклетьевым подъемом были сооружены на шахтах № 316 и 321, где достигнуты соответственно скорости проходки 1070 и 1250 м перегонного тоннеля в месяц.
Для высокопроизводительной работы на шахте № 321 был смонтирован также принципиально новый горный комплекс, ранее не применявшийся на Ленметрострое. Он состоит из четырех бункеров под породу с челночным обменом груженых и порожних вагонеток. Для вертикальной транспортировки вагонеток, тюбингов и людей в трехклетьевом подъеме были применены две подъемные машины типа 2Ц2×1,1.
Разгрузка и подача тюбингов осуществлялись с помощью тельферной эстакады с тремя монорельсами. Две монорельсовые балки с двумя электроталями грузоподъемностью 5 т на каждой из них использовались для доставки обделки к стволу. Третья с кареткой грузоподъемностью 5 т предназначалась для транспортировки длинномерных материалов: рельсов, труб, лесоматериалов.
Опыт обычной и скоростной проходок подтвердили расчеты высокой производительности шахтного подъема и горного комплекса, суммарное количество подъемов которых составляло 500–550.
На шахте № 320 был смонтирован типовой горный комплекс с подъемной машиной типа 2БМ-2000/1030 2А. Его максимальная производительность достигала 300–320 подъемов в смену.
При наличии двух шахт создавалась не только возможность обеспечить большое количество подъемов, но и надежную гибкую схему работы.
Поскольку шахтные подъемы использовались не в полную мощность, имелся некоторый резерв. Только в дни наибольшей скорости проходки число подъемов приближалось к максимальному: например, при сооружении 40 м в сутки оно составило 710 подъемов, а в день рекордной проходки 48 м — 1 975. Максимальное количество подъемов при проходке 20 м в смену — 825.
Наиболее ответственным и трудным звеном из всей цепи механизмов, как и рассчитывали, была электровозная откатка. Длина плеча откатки к началу скоростной