
692
.pdf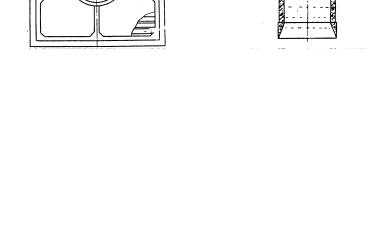
строительства шахтного ствола. Размещение его в фундаменте позволяет использовать бетонный узел в первом и втором периодах строительства. При этом исключается демонтаж механической части приствольного бетонного узла в переходные периоды.
а) |
б) |
Рис. 2.18. «Фундамент-опорная конструкция» (а) и технологическая схема сооружения устья ствола методом ПКТО (б): 1 — монолитная железобетонная плита; 2 — наружные балки-стены; 3 — место расположения узла приготовления бетона; 4 — внутренние балки-стены диаметром D = (0,5... 0,7 м) + dпк, где dп — наружный диаметр погружной крепи; 5 — угловые опоры; 6 — бетонная погружная крепь; 7 — кольцевая опалубка;
8 — гидравлические домкраты
На рис. 2.18, б показана «фундамент-опорная» конструкция в период погружения крепи системой гидродомкратов. В основании фундамента надшахтного здания укладывают железобетонную плиту. В ее центре имеется отверстие, а по периметру, в теле плиты, установлены шарнирные балки угловых упоров, с горизонтальной плоскостью которых взаимодействуют гидравлические домкраты. Материалом погружной крепи является железобетон, укладываемый между обечайками кольцевой опалубки. Устье ствола проходят методом ПКТО с применением системы «фундамент-опорная конструкция» известным способом.
Создание этой системы осуществляют в подготовительный период в следующем порядке. Вначале (фаза 1) разрабатывают котлован под постоянный фундамент надшахтного здания
(башенный копер) с учетом вентиляционного и других технологических каналов. Затем (фаза 2) сооружают «фундамент-опорную конструкцию» и узлы примыкания каналов технологического назначения, устанавливают опалубку, монтируют арматуру и закладные детали, укладывают бетон, снимают опалубку, засыпают котлован и укладывают (при необходимости) дополнительный пригруз. В заключительной фазе 3 ведут монтаж оборудования и сооружают устье ствола методом ПКТО.
Объемы вспомогательных работ определяются в каждом конкретном случае индивидуально и зависят от диаметра ствола, глубины погружения и свойств пересекаемых крепью грунтов. Максимальная продолжительность вспомогательных работ, включая полный демонтаж проходческого оборудования после погружения крепи, составляет около 30 рабочих смен.
С целью исключения просадок поверхности, которые могут возникнуть в результате выноса плывунных грунтов из-под ножевой части крепи в забой ствола, крепь необходимо погружать одновременно с выемкой грунта. При этом особое внимание следует уделять контролю за погружением участков крепи, находящихся под водой.
Для контроля состояния основания грунта под «фундаментопорной конструкцией», а также для заполнения пустот песчано-глинистыми смесями используют контрольные и тампонажные трубки диаметром 50 мм, которые устанавливают по окружности ствола в плиту на расстоянии 1,5–2 м друг от друга.
Технологическая схема сооружения устьев стволов методом ПКТО с применением постоянных фундаментов башенных копров и надшахтных зданий позволяет совместить работы переходного периода с проходческими.
При оснащении ствола башенным копром его подземную часть целесообразно сооружать на отдельной площадке и затем надвигать на уже имеющийся постоянный фундамент. Такая конструкция фундамента позволяет: исключить сооружение времянок и сэкономить около 500 м3 бетона; сократить на 6–8 мес. продолжительность переходных периодов (благодаря параллельному ведению работ по сооружению надземной части постоянного башенного копра и работ по монтажу проходческого оборудования); снизить сметную стоимость сооружения устья ствола методом ПКТО по приведенной технологии.
Конструкцию фундамента типа монолитной плиты можно использовать не только при проходке устьев методом ПКТО в сложных горно-геологических условиях, но и при строительстве стволов обычным способом с применением проходческих копров и надшахтных зданий обычных конструкций.
2.4.4.Проходка ствола способом опускной крепи
сбуровой выемкой грунта
При сооружении стволов в неустойчивых грунтах, включающих участки полускальных
искальных грунтов с прочностью до 5 МПа, одним из перспективных направлений является буровой метод их разработки. Этот способ в настоящее время эффективно используют в КНР для проходки стволов диаметром в свету до 6,5 м. Для стволов небольшого диаметра применяемые средства вращательного бурения грунтов относительно мобильны. Способ опускной крепи успешно конкурирует с замораживанием
ибурением, при этом можно проходить стволы на глубину 200 м и более.
Для проходки стволов способом бурения эффективны буровая выемка грунта по всей площади сечения и ударно-канатное бурение с обратной промывкой. Эта техника применяется в отечественной и зарубежной практике строительства подземных сооружений способом «стена в грунте» и ее рекомендуют при глубине траншеи более 50 м. При ударно-канатной выемке долото перемещается по забою и обеспечивает вертикальность выработки, разрушая крепкие прослойки грунтов и включения. Сопоставление единичных расценок на бурение скважин показывает, что в мягких грунтах, включая глины, мергель и мел низкой прочности, стоимость ударно-канатной выемки примерно в 1,4 раза меньше, чем стоимость выемки роторной передвижной установкой, а в грунтах большей крепости — во столько же раз дороже, но вчетверо дешевле выемки установки реактивно-турбинного бурения, широко применяемыми в отечественной угольной промышленности.
Для буровой ударно-канатной выемки грунта в опускной крепи ствола любого диаметра разработан мобильный буровой комплекс (рис. 2.19).
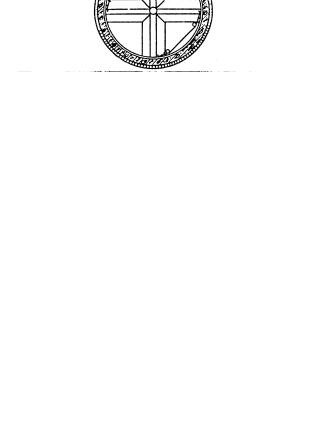
Рис. 2.19. Комплекс для буровой ударно-канатной выемки грунта в опускной крепи:
1 — горно-проходческий копер; 2 — поворотный сектор платформы; 3 — двухбарабанная лебедка; 4 — возвратно-поворотная шкивная платформа;
5 — компрессор; 6 — полок; 7 — тиксотропная оболочка; 8 — направляющая рамка; 9 — керноразрушитель; 10 — ударное плоское долото; 11 — долотная направляющая; 12 — опускная крепь; 13 — опалубка; 14 — колонна труб пульпо-эрлифта; 15 — пульпоотстойник
В этом случае буровая выемка грунта осуществляется ударами перемещаемых по забою (с перекрытием зон действия) плоских ударных долот, поднимаемых и сбрасываемых ударноканатными станками. Образующаяся грунтоводяная пульпа выдается эрлифтом. Вначале разрабатывается кольцевая траншея у ножа опускной крепи, а затем теми же долотами, но опущенными отвесно без направляющих рамок, разбуривается выступ.
Расположение соседних шкивов копра и возвратно-пово-ротной платформы у оси поворота последней и разнесение шкивов по высоте обеспечивают допустимые углы девиации канатов при поворотах платформы на большие углы.
Канатно-полиспастная подвеска долотной направляющей позволяет поднимать ее без разборки пульпо-эрлифтной колонны и использовать канаты подвески для наклонно направленного спуска долот. Разнонаклонность скосов долотной направляющей обеспечивает радиальное ориентирование долот, опускаемых без направляющей рамки.
Вертикальность спуска крепи периодически контролируется по наклону каната с фо- нарем-центратором, опущенным в колонну пульпо-эрлифта. Отклонения крепи можно устранить, прекращая работу части станков или изменяя наклон долот.
Перед подходом к грунтовой прослойке или водоупорному слою, в которых масса крепи оказывается недостаточна для среза ножом уступа грунта шириной 10 см, в бетон крепи закладывают опорные элементы и применяют гидродомкраты.
Ударные долота для комплекса рекомендуется изготавливать из толстолистовой стали, снабжать проушинами для канатной подвески через коуш, направлять и восстанавливать изношенное лезвие долота релитом.
Производительность комплекса, включающего четыре самоходных станка БС-2, o6eспечивает опускание крепи ствола в мягких (до ƒ = 2) грунтах со скоростью более 100
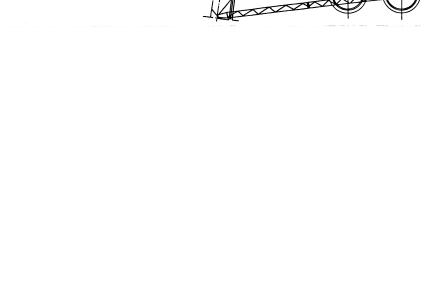
м/мес. Мощность привода станка 75 кВт, масса долота 3,5 т, стоимость 30 тыс. р. (в ценах 1984 г.).
В Германии при применении однодолотной ударно-штан-говой выемки (мощность ударной машины 30 кВт, мощность средств промывки 43 кВт) в мягких грунтах крепь диаметром в свету 6,5 м опускали со средней скоростью 30 м/мес., максимальные темпы (в глине) достигали 5 м/сут.
Рекомендуемый комплекс отличается высокой мобильностью и простотой конструкции. Его можно изготовить непосредственно в условиях строительной организации, осуществляющей проходку. Комплекс можно эффективно применять и для бурения скважины ниже опускной крепи, а также для бурения неглубоких стволов и скважин большого размера в грунтах различной крепости. Применение его взамен специализированных буровых установок позволяет получить эффект благодаря его большой мощности, высокой мобильности, малой стоимости, незначительных затрат на долота, быстроте их смены и эффективной обратной промывке. Комплекс хорошо сочетается с обычным способом проходки.
Применение способа опускной крепи с буровой выемкой грунта и рекомендуемого комплекса позволит существенно ускорить и удешевить строительство шахтных стволов.
2.4.5.Устройство заглубленных фундаментов и шахт с использованием инвентарных оболочек
При сооружении различных объектов в значительном числе случаев приходится возводить фундаменты глубокого заложения с большой грузонесущей способностью. Сложности возникают, когда надо это выполнить в слабых, неустойчивых и водоносных грунтах, а также когда не требуется свайных ростверков — забивки свай (близкорасположенные здания, внутри промышленных объектов, фундаменты под тяжелое технологическое оборудование и т.д.).
Одним из технических направлений, позволивших решить эту задачу, являлось устройство фундаментов глубокого заложения колонного типа погружением железобетонных колец, заполняемых бетоном. Для снятия сопротивления трения между грунтом и погружаемыми кольцами использовался глинистый тиксотропный раствор — тиксотропная рубашка. Для образования кольцевой щели, в которую он заливался, первое кольцо оснащалось режущим башмаком высотой 500 мм, в сторону грунтовой стенки [Шахтное строительство. 1988. № 2. С. 11–12].
Более 30 лет назад этот вариант был весьма успешно применен в Москве при сооружении фундамента под административный корпус, примыкающий к старому зданию Министерства обороны в районе Арбата (рис. 2.20).
Рис. 2.20. Технологическая схема сооружения фундаментов колонного типа
Глубина колонных фундаментов диаметром 3 м составляла 12,5 м. Были использованы стандартные железобетонные кольца. Разработка грунта и выгрузка его в автосамосвалы производилась четырехлопастным одноканатным грейфером вместимостью 1 м3. Скорость погружения колец зависела от производительности разработки грунта.
Весь комплекс работ по сооружению 70 колонных фундаментов осуществлялся с помощью самоходных кранов КС-5363, которые производили выгрузку с автомашин железобетонных колец, спуск и подъем грейферов, выгрузку грунта в самосвалы.
Таким образом, была реализована поточная организация работ и комплексная механизация всего технологического про-цесса.
По такой универсальной технологии можно сооружать различные объекты в наиболее сложных гидрогеологических условиях. При этом не ограничены габариты, форма и глубина таких фундаментов. В 1973 г. на строительстве станции метрополитена в Вашингтоне (США) для устройства ограждающих стен котлована, в котором возводилась станция, впервые применили инвентарные оболочки. Протяженность ограждения — 1219 м, диаметр труб-оболочек составил 91,44 см, межцентровое расстояние между оболочками
— 2,44 м, глубина погружения — 22 м. Процесс погружения осуществлялся с помощью вибромолота. Извлечение грунта из оболочки производилось шнекобурильной машиной. Для заполнения одной оболочки требовалось 12,3 м3 бетона. После схватывания бетона, на что требовалось 10–15 мин оболочки извлекали. В незатвердевшую бетонную массу в течение 30 мин задавливали стальные сваи. Такая технология позволила возвести ограждающее устройство безаварийно и в короткий срок.
В 1992 г. была выполнена «Разработка предложений по совершенствованию конструктивно-технологических решений сооружения коллекторных тоннелей», в числе которых — проходка смотровых колодцев и шахт с использованием инвентарных оболочек.
Согласно этим предложениям сооружение временной монтажной шахты совмещается с устройством в ней, после вывода проходческого щита на трассу коллектора, постоянного смотрового колодца из монолитного или сборного железобетона.
Работы проводятся в следующей технологической последовательности (рис. 2.21):
—погружение сборной крепи оболочки до проектной глубины коллектора;
—опускание и монтаж проходческого щита;
—извлечение сегментов оболочки для формирования проема и вывода щита на трассу;
—проходка заданного по проекту участка коллектора;
—сооружение смотрового колодца;
—извлечение оболочки с одновременным заполнением зазора между вмещающим грунтом и колодцем.
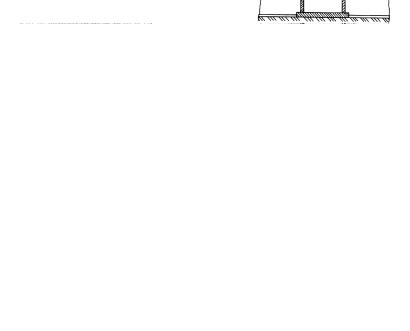
а) |
б) |
в) |
г) |
Рис. 2.21. Схема сооружения смотровых колодцев
сиспользованием извлекаемой оболочки:
а— погружение сборной оболочки; б — разборка проемов и проходка коллектора; в — сооружение смотрового колодца;
г— извлечение оболочки
сзаполнением зазора песком
Погружение оболочки осуществляется с помощью специального силового устройства, конструкция которого выполнена в форме двухконсольной балки на шарнирной опоре, которая закреплена на вертикальной стройке угловой опоры. К внутренней консоле подвешен гидроцилиндр, создающий нагрузку на опускную крепь. Наружная консоль через опорную стойку передает реактивную нагрузку гидроцилиндра на горизонтальную площадку угловой опоры.
Для создания необходимой нагрузки на опускную крепь порядка 150–200 т достаточно 3–4 силовых домкрата, оснащенных гидроцилиндрами с ходом штока, соответствующего ширине кольца крепи.
При извлечении оболочки домкратная система перекрепляется упором с одной стороны на стенки возведенного колодца, а с другой стороны — на балочные пакеты, установленные на ребра сегментов оболочки.
Для снижения сопротивления трения о грунт при погружении и извлечении оболочки зазор между грунтом и опускной крепью заполняется тиксотропным раствором. Этот зазор формируется уширением ножевого кольца на 100 мм относительно наружного периметра оболочки. Ножевое кольцо сборной конструкции при извлечении последней демонтируется для повторного использования.
С целью предотвращения утечки тиксотропного раствора при открытии проемов для вывода щита необходимо, чтобы первые кольца были шириной 0,5 м (в зависимости от габаритов щита и характеристики вмещающего грунта), а зазор заполнен манжетой из мягкопластичной глины с включением гравия. Можно также над разбираемыми элементами устраивать пояс из цементо-пес-чаного раствора посредством инъекционной трубы, опущенной в тиксотропный раствор.
Рассматриваемые варианты технических решений по сооружению различного типа и назначения заглубленных фундаментов и других аналогичных объектов можно рекомендовать для использования в практике подземного строительства.
2.4.6.Сооружение стволов метрополитена комбинированным способом
При строительстве Сырецко-Печерской линии Киевского метрополитена в слабых неустойчивых водонасыщенных грунтах была разработана и впервые применена при
проходке ствола № 221 новая комплексная технология, включающая обычный способ проходки ствола (выше водоносного горизонта) и метод продавливания в тиксотропной оболочке с гидравлическим пригрузом (на уровне и ниже водоносного горизонта) [Метро и тоннели. 2002. № 4. С. 10–11].
До отметки водоносного горизонта (14,0 м) проходку ствола диаметром 6 м вели горным способом с разработкой грунта отбойными молотками заходкой в 1 м и выдачей его на поверхность с помощью грейфера с объемом ковша 1 м3, размещенного на кране типа КС-5363. После выемки грунта осуществляли монтаж (14 колец обделки из чугунных тюбингов) и устройство предохранительного (верхнего) и рабочего (нижнего) полков с проемами для пропуска грейфера.
Вдальнейшем разработали грунт по внешнему контуру обделки на глубину 2,3 м. При этом в центре забоя было создано опережение диаметром 4 м на глубину 1 м, а по фланцу 14-го кольца обделки установлены прижимные стальные планки толщиной 20 мм. После этого перпендикулярно к оси ствола прошли боковую штольню трапециевидного сечения высотой 2,3 м и длиной 3 м с установкой крепежных рам и их затяжкой обрезными досками в кровле и в боках выработки. Размеры рам поверху составляли 2,74, а понизу — 3,19 м. По кругу на отметке 16,3 м заходками по 2 м прошли кольцевую штольню (нишу)
скреплением кровли и боков забоя полурамами и затяжкой из обрезных досок толщиной 40 мм. В штольне установили монтажную лебедку, а к кольцу тюбинговой крепи с накладками навесили 8 гидроцилиндров, смонтировали гидросистему и маслостанцию. После разработки грунта выемки глубиной 1,7 и диаметром 1,2 м, при помощи крана и монтажной лебедки собрали ножевую часть и на ней первое кольцо обделки. При этом нож с высокой точностью выставляли в плане и профиле. Подработав грунт на величину заходки, нож с первым кольцом обделки опустили на 1 м и смонтировали второе кольцо, устанавливая направляющие (8 шт.) и бетонируя промежуточный оголовник. Затем собрали проходческий полок, а в кольцевой нише смонтировали коллекторную сеть гидропромыва и подачи бентонитовой суспензии.
Всоответствии с принятой технологией, дальнейшая проходка ствола осуществлялась в тиксотропной оболочке. Грунт разрабатывался при помощи грейфера подводным способом. При помощи 8 гидроцилиндров, расположенных на границе кольцевой ниши, производилось задавливание сборной крепи. После проходки на 1 м с монтажного полка лебедкой или краном собирали очередное кольцо обделки. По фланцам между кольцами обделки производили гидроизоляцию из одного слоя гидростеклоизола. Кроме того, выполняли зачеканку (законопачивание) монтажных (межтюбинговых в кольце и межкольцевых) швов и устанавливали тюбинговые пробки. При помощи ручных лебедок, размещенных на перекрытии устья ствола, перемещали проходческий полок на смонтированное кольцо. Далее цикл повторялся.
При опускании крепи путем продавливания гидроцилиндрами между обделкой и грунтом на уровне промежуточного оголовника постоянно поддерживалось наличие бентонитовой суспензии (тиксотропного раствора). Ее применение обеспечивало существенное снижение сил трения по внешней поверхности колец обделки при проходке ствола до отметки 52,2 м.
Разработанная технология и ее технико-экономические показатели сравнивались с технологией продавливания крепи ствола № 222 с поверхности. Как оказалось, новая технология имеет существенные преимущества: исключается большой объем земляных и бетонных работ при строительстве воротника и самой форшахты; появляется возможность осуществлять продавливание обделки на большую глубину в сравнении с традиционным способом погружения колодца с поверхности; сокращается объем металлоконструкции и работ по их монтажу для обустройства продавливающей установки. Однако одним из главных факторов выбора новой технологии проходки в сложных условиях является эффективное продавливание части ствола без увеличения числа гидроцилиндров.
Для проходки ствола № 220 в районе ст. «Герцена» Сырецко-Пе-черской линии, с учетом особого места ее расположения (с тыльной стороны здания института международных отношений), была запроектирована технология строительства комбинированным спосо-
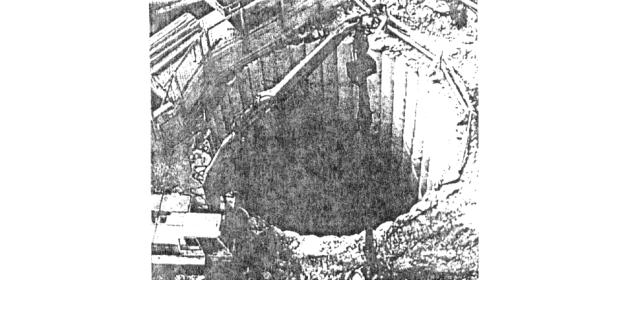
бом в два этапа с применением буронабивных свай. Свайные работы выполняли по специальной технологии, разработанной АО «Трансмост», с применением способа «стена в грунте» из секущих бетонных и железобетонных свай. Технология основана на бурении скважин диаметром 1020 мм с обсадной трубой внутренним диаметром 820 мм. Глубина скважин составляет 36 м, а сооружаемого ствола на первом этапе — 32,1 м.
Скважины располагали по концентрической окружности диаметром 9800 мм (рис. 2.22). Порядок их бурения определялся одиннадцатью этапами, что зависело от очередности их выполнения в пределах одного этапа. Всего было пробурено 44 скважины по 5 в каждом этапе. Так, например, на первом этапе первую скважину бурили с удалением шлама и заполняли бетоном без помещения армокаркаса. Через одну скважину на расстоянии 1400 мм по дуге окружности бурили третью и также бетонировали ее без армокаркаса. Рядом с первой бурили 44-ю и заполняли ее песком. Затем между первой и третьей по варианту «секущая скважина» бурили вторую скважину, устанавливали в нее армокаркас и бетонировали.
Рис. 2.22. Устье ствола с креплением из секущих бетонных (первичных)
ижелезобетонных (вторичных) свай
Вследующем варианте сооружали скважину «номер четыре» и заполняли ее песком. Работы на втором этапе выполнялись в том же порядке, однако отличительной особенностью было разбуривание скважины «номер четыре» и ее бетонирование после установки армокаркаса.
После выполнения всех работ по созданию защитной стенки из секущих буронабивных свай производилась выемка грунта с помощью строительного крана и грейферного выемочно-погру-зочного органа.
Проходка ствола с глубины 32,1 м осуществлялась по следующей технологии. К закладным деталям в буронабивных сваях приваривали консоли с укосинами, к которым крепили гидродомкраты для задавливания ножевой секции. После ухода ножевой секции в грунт на высоту кольца на ней монтировали железобетонные тюбинги диаметром 6,1/5,6 м
иосуществляли выемку грунта грейферным краном. Задавливание колец крепи с ножевой секцией проводилось комбинированным методом, включая способ опускных секций (колец) в тиксотропной оболочке с внешней стороны крепи и гидропригруза внутри ствола.
После достижения проектной глубины ствола на промежуточный оголовок последовательно до самого устоя наращивали железобетонные кольца и засыпали пространство между ними и буронабивными сваями песком.
Разработанная технология имеет следующие преимущества:
создание кольцевой стены из буронабивных свай полностью исключило деформации основания и фундамента важнейшего объекта — корпуса Института международных отношений;
исключается процесс забивки свай, сопровождающийся ударными динамическими нагрузками на основание, фундамент и здание и шумовыми эффектами при его реализации; задавливание секций опускной крепи с промежуточной опорной конструкцией на границе буронабивных свай и грунтового массива позволило исключить предельное сопротивление трения при внедрении ножевого кольца в чередующиеся песчаные и
глинистые грунты; наращивание колец крепи ствола производилось с промежуточного устройства без
опускания ее в забойную часть при горном способе, что нельзя осуществить при гидравлическом пригрузе (на 1 м выше уровня грунтовых вод) в стволе.
При проходке ствола № 217 была применена специальная технология, заключающаяся в следующем. На первом этапе проходка в верхней части выполнялась путем продавливания железобетонных тюбингов диаметром 7,7/7,0 м в тиксотропной оболочке сверху, начиная от оголовника. Второй этап состоял из проходки средней части ствола продавливанием в тиксотропной оболочке железобетонных тюбингов диаметром 6,1/5,6 м с их монтажом без кольцевой штольни. На третьем этапе проходка ствола осуществлялась горным способом с подводкой железобетонных блоков снизу.
При разработке новых технологий и крепей важное значение имеет уровень унификации конструкций и видов работ для повышения производительности и общей эффективности строительства подземного объекта. С этой целью в Киевметрострое были сконструированы, изготовлены и внедрены обделки из универсальных железобетонных блоков типа Н-61, К-61, С-61 диаметром 6,1/5,6 м, которые использованы для крепления стволов и околоствольных дворов. Их преимущество заключается в унификации элементов, а главное — в более низкой стоимости по сравнению с чугунными.
Анализ результатов внедрения разработанных комбинированных технологий проходки стволов метрополитена показал, что они эффективны в сложных инженерногеологических условиях и позволяют получить значительный экономический эффект за счет высокого уровня механизации технологических процессов, применения специальных способов и железобетонной обделки взамен чугунной в обводненных грунтах.
Таким образом, внедрение разработанных технологий проходки стволов позволило достичь высоких технико-экономи-ческих показателей без опасных деформаций грунтового массива вблизи важных объектов.
2.5.Проходка стволов
сприменением шагающих комплексов
Внастоящее время в отечественной и зарубежной практике используются эффективные средства разработки и погрузки породы при сооружении неглубоких стволов: грейферные погрузчики, гидравлические погрузочные машины ковшового типа с принудительным внедрением
впороду и т.п.
Ведущими зарубежными фирмами много внимания удаляется созданию комплексов для бурения стволов и скважин большого диаметра на полное сечение. Однако оборудование подобного типа весьма дорого, громоздко и ограничено в применении.
2.5.1. Сооружение ствола со спуском грунта через скважину
Использование гидравлических породопогрузочных машин с принудительным внедрением в породу способствует повышению технико-экономических показателей сооружения вертикальных стволов, однако этому типу присущ один общий недостаток — опалубка и погрузочная машина подвешиваются на лебедках, что увеличивает время их перестановки на следующую заходку.
Оптимальным вариантом является отделение проходческого оборудования от поверхностного комплекса, т.е. создание шагающего агрегата, опирающегося на забой и примыкающие участки ствола; отказ от тяжелых лебедок для подвески полка и погрузочной машины с опалубкой для возведения крепи [Метро. 1996. № 2. С. 10–12].
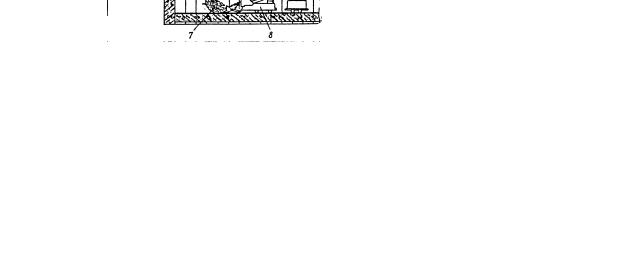
Ленинградским отделом СКТБ Главтоннельметростроя совместно с ТО № 3 Ленметростроя был разработан и реализован проект производства работ по проходке шахты № 319 4-го участка Московско-Петроградской линии метрополитена, предусматривающий спуск грунта через скважину Д-426 мм, пробуренную заранее в венттоннель, монтаж укрупненных элементов постоянного обустройства ствола и использование его в качестве армировки при проходке.
Ствол шахты (рис. 2.23) сооружался с применением замораживания в зоне неустойчивых четвертичных отложений и обычным способом в протерозойских глинах. Скважина для спуска грунта бурилась по центру ствола со смещением на 50 см по его оси в сторону, противоположную выходу на трассу.
Горный комплекс состоит из тюбингового копра высотой 10 м, где размещается подъемная лебедка, и тельеферной эстакады. Высота копра определилась из условия его работы только на одном горизонте, нулевом, с которого подаются тюбинги, материалы и осуществляется спуск людей. На этом горизонте был предусмотрен специальный проем, перекрытый лядой, для транспортировки укрупненных элементов постоянного обустройства ствола.
В форшахте и частично в копре был смонтирован шагающий проходческий полок. Его применение исключило использование лебедок для перемещения полка, позволило вести работы на двух горизонтах и повысить безопасность работ. После проходки первых десяти колец ствола собиралось верхнее звено постоянного обустройства, площадка которого соединена лестницей с верхним ярусом полка. Забой разрабатывался заходками на глубину 1 м: вначале ядро, затем боковые штроссы секторами к наружному контуру, участками по два тюбинга.
Puc. 2.23. Технологическая схема сооружения ствола:
1 — лебедка; 2 — ось барабана; 3 — тельеферная эстакада; 4 — постоянное обустройство ствола; 5 — шагающий проходческий полок; 6 — скважина для спуска грунта; 7 — приемный лоток; 8 — погрузочная машина; 9 — проем для прохода к лестнице; 10 — то же для спуска людей, тюбингов и материалов;
11 — ось подъема; 12 — ось ствола; 13 — проем для спуска звеньев для постоянного обустройства ствола
Грунт спускали по скважине Д-426 мм, устье которой было перекрыто съемной воронкой с решеткой из двух стержней арматуры. Грунт поступал на приемный лоток, обшитый металлическим листом, с которого породопогрузочной машиной перегружался в вагонетки. Емкость приемного лотка обеспечивала независимость транспортировки породы от ее разработки.
Для прочистки скважины было предусмотрено устройство из троса с ершиком и двух лебедок. Одна из них установлена на нижнем ярусе полка, другая — в венттоннеле.
Обделка монтировалась тельфером, расположенным на нижнем ярусе проходческого полка. Первичное нагнетание цементно-песчаного раствора осуществлялось в первое установленное кольцо и заканчивалось до начала сборки очередного.
Контрольное нагнетание велось в 6–7-е кольцо от забоя, затем производилась чеканка с верхнего и среднего ярусов проходческого полка. Спуск звена осуществлялся двумя