
692
.pdfпроходки составляла 1 000 м, а к концу — 2 300 м; из них 500 приходились на уклон, равный 40 ‰; большая длина откатки требовала применения мощных электровозов типа 10К.
На шахте подготовили 10 электровозов. Основными откаточными были электровозы типа 10К, имеющие два электродвигателя мощностью по 31 кВт. Пробная эксплуатация электровозов 10КР не оправдала надежды из-за слабых тяговых качеств, поэтому использовались они, как и 7 КР, для формирования составов (на маневровых работах у ствола и во время ремонта основных электровозов).
Всмену работало 5–6 электровозов, не считая занятых на маневровых операциях. При этом 1–2 постоянно находились на ремонте и профилактическом осмотре.
Питание контактной сети осуществлялось от трех источников: от ствола шахты № 321, шахты № 320 и непосредственно в тоннеле в районе наиболее трудного участка пути на уклоне 40 ‰. Тем самым создали возможность резервирования электровозной откатки. Суммарная мощность источников питания достигала 200 кВт.
Существующие технологические схемы клетьевого подъема с двух горизонтов (нулевой площадки и эстакады) обусловливают необходимость формирования поверхностного горного комплекса, требующего значительных размеров площадки, что часто бывает трудно выполнить в условиях плотной городской застройки и сложных сетей подземных коммуникаций.
Впрактике горно-добывающих отраслей применяется скиповый подъем, обладающий большой производительностью, а спуск всех материалов осуществляется в вагонетках, тележках и специальных контейнерах в клетях только с нулевого горизонта. Очевидно, что назрела необходимость использовать скиповый подъем и в метростроении. Вариант горного комплекса, оснащенного скиповым подъемом для выдачи грунта применительно к условиям метростроения, впервые был разработан около полувека тому назад, однако в то время он не получил распространения [Метро. 1994. № 2. С. 23–24]. Позднее подобная установка для шахт Ленметростроя была запроектирована институтом «Гипрошахт» и реализована при строительстве станций «Василеостровская» и «Выборгская» (рис. 2.5).
Водном стволе применили две подъемные установки: клетьевую — 1 и скиповую — 2. Обе
машины смонтированы на поверхности в башне, сооруженной в такой же обделке, что и ствол шахты. Клеть 3 рассчитана на грунтовую вагонетку вместимостью 2 550 кг (1,5 м3), подъем для скипа 4–5 м2. Для двух подъемных машин необходимы два помещения и, соответственно, более высокие затраты на оборудование и строительные работы, часто связанные с разрушением существующих зданий и последующим их восстановлением. Новая схема может быть применена в условиях плотно застроенной центральной части города.
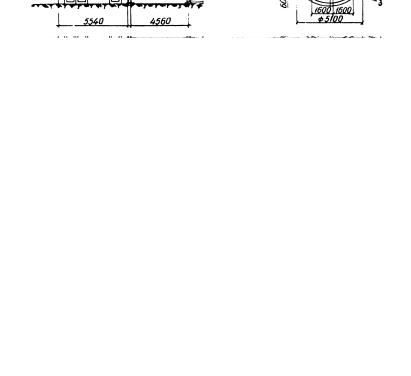
Рис. 2.5. Общий вид скиповой подъемной установки для шахт Ленметростроя
Несколько иное конструктивно-технологическое решение горного комплекса было разработано и в дальнейшем реализовано при строительстве ст. «Парк Победы» в Москве специалистами АО «Трансинжстрой» и СКТБ «Тоннельметростроя» [Метро и тоннели. 2003. № 2. С. 20–21]. Новый горный комплекс КШГ-2 оснащен как серийным, так и оригинальным оборудованием: боковыми опрокидывателями ОБ-1,5; толкателями верхнего действия ТВД; грузовыми платформами ПГУ-8 с оборудованием для подачи в ствол длинномерных (до 12,5 м) материалов. Комплекс КШГ-2 производительностью до 16 тыс. м3/мес. по грунту в плотном теле включает в себя также тюбинговый копер с двумя приемными площадками на верхнем разгрузочном и нулевом горизонтах, две грузолюдские клети, две подъемные машины (одна из которых — двухбарабанная для грузолюдских клетей со скоростью подъема 2,5 м/с при глубине до 40 м и 3,8 м/с при глубине более 40 м, другая — для грузовой платформы со скоростью подъема 1 м/с), материальную эстакаду и два грунтовых бункера емкостью 40 м3 каждый.
Верхний разгрузочный горизонт оборудован комплексом для обмена вагонеток с качающимися площадками, средствами электровиброочистки и вентиляторами пылеотсоса.
На околоствольной площадке, кроме того, расположены кран-балка грузоподъемностью 3,2 (5,0) т для подачи грузов на материальную эстакаду, приемный узел для сухой смеси и песка с переподъемником, обеспечивающим подъем вагонеток с отметки –4,5 м на нулевой горизонт, механизированный склад цемента и др.
Возможность доставки длинномерных материалов и крупногабаритного оборудования в грузовой платформе позволило отказаться от устройства в стволе лесоспускного отделения, опасного в эксплуатации.
Нижний откаточный горизонт в районе околоствольного двора выполнен двусторонним и оборудован двумя агрегатами АПТ-2 для механизированного обмена вагонеток, каждый из которых включает в себя две качающиеся площадки (входную и выходную), привод для открывания стопоров клети стволовые двери шлагбаумного типа, задерживающий стопор, толкатель и путевой тормоз. Такая схема механизации работ позволила увеличить производительность подъема грунта в два раза за счет сокращения времени обслуживания вагонеток на приемных горизонтах и увеличения скорости подъема.
Все механизмы агрегатов оборудованы пневмоили гидроприводом и управляются одним оператором с дистанционного пульта управления. Продолжительность цикла
обмена вагонеток на верхнем приемном горизонте и одновременно на нижнем откаточном (в околоствольном дворе) составляет около 20 с по сравнению с 60–80 с на традиционных комплексах.
Для устройства гидроизоляции обделок при ремонте и реконструкции стволов с использованием металлоблоков БМ и АМБ (примененных на ст. «Парк Победы»), был разработан специальный механизированный комплекс — трехъярусный полок, позволяющий одновременно производить монтаж обделки типа БМ и АМБ и внутренних конструкций (горизонтальных ярусов и лестниц). Полок состоит из трех ярусов, соединенных между собой трубами, и подвешивается на четырех канатах к двум лебедкам грузоподъемностью 10 т каждая.
Для монтажа обделки БМ и АМБ комплекс оснащен круговой поворотной балкой («поворотной рукой») с электрической талью, размещенной под вторым ярусом полка, а для монтажа внутренних конструкций — специальной кран-балкой с электрической талью, размещенной под третьим ярусом на круговом монорельсе. Монтаж обделки и внутренних конструкций производят снизу вверх по мере подъема полка. Спуск и подъем людей осуществляют в бадье БП-1, оснащенной рамкой и прицепным устройством. Рамка передвигается по канатным направляющим, одновременно являющимися канатами подвески полка. Подача элементов обделки и внутренних конструкций осуществляется по бадьевому подъему с использованием прицепного устройства бадьи, направляющей рамки и канатов подвески полка. Бетон подается сверху бетононасосами по бетоноводу. Работы по монтажу обделки БМ и АМБ и внутренних конструкций ведут заходками по 3 м по следующей схеме: центровка и фиксация полка выдвижными упорами в ячейках тюбинговой обделки; подача элементов обделки на третий ярус, перекрепление на электроталь и установка в проектное положение с частичной прихваткой электросваркой и окончательной сваркой после монтажа кольца; обетонирование смонтированных колец; монтаж внутренних конструкций с использованием электрической тали на кран-балке под третьим ярусом полка. После подъема полка на 3 м операции повторяются.
При возведении ст. «Пролетарская» Люблинской линии на шахте № 933 СМУ № 14 пройден ствол диаметром 8,5 м, на котором впервые был применен высокопроизводительный шахтный комплекс КШГ-4, имеющий два независимых клетьевых подъема. Один из них работал на горизонте бункерной эстакады с производительностью 60 подъемов в час, второй — на нулевой отметке с производительностью 35 подъемов в час. Клети имели грузоподъемность 4 т, скорость движения — 2,5 м/с [Метро. 1992. № 2. С. 2–6].
2.2.3. Вертикальные конвейеры и элеваторы
Проблема повышения производительности вспомогательных устройств, в частности шахтного подъема, при строительстве подземных сооружений стала особенно актуальной
всвязи с широким внедрением различных способов скоростной проходки тоннелей. Одно из направлений в решении этой задачи за рубежом — использование для подъема грунта конвейеров и аналогичных устройств непрерывного действия.
По сравнению с традиционными шахтными подъемами (вагонеточным, грейферным, скиповым) устройства непрерывного действия обладают рядом преимуществ: обеспечивают высокую производительность подъема разработанного грунта при значительной глубине заложения тоннеля, повышение безопасности ведения работ, вследствие малых габаритов дают возможность использовать ствол для раздельной транспортировки грунта, строительных материалов и людей. Кроме того, операции по выдаче грунта легко поддаются автоматизации, полностью устраняется ручной труд.
Вподземном строительстве за рубежом применяют различные шахтные конвейеры и элеваторы. Так, в США при строительстве системы канализационных коллекторов в Чикаго использовали тяжелый ленточный конвейер фирм «Lokor», «Conrad Stolz» (Германия), обеспечивший скоростную проходку роторным комбайном «Jarva» с диаметром планшайбы 9,75 м. Средний темп проходки на участке длиной 7,6 км по доломитовому известняку составил 2,25 м/ч. Ширина резинотросовой ленты конвейера — 1,6 м, общая длина — 190 м. Она армирована стальными тросами как в продольном, так и
впоперечном направлении. Полотно снабжено гофрированными болтами высотой 400 мм,
съемными резиновыми карманами (ковшами) шириной 800 мм и глубиной 380 мм. Общее количество карманов — 569 шт. Масса ленты в сборе — 34,5 т.
Комплекс для погрузки грунта на конвейер состоит из опрокидывателя приемного бункера на две вагонетки емкостью 38,2 м3, виброгрохота для отделения фракций более 35 мм, камнедробилки и ленточного перегружателя длиной 10,8 м. Длина участка конвейера в зоне погрузки 5,6 м. Вертикальная его часть длиной 82 м заключена в кожух сечением 2,1×1,88 м с теплоизоляцией. Разгрузочный наземный участок конвейера составляет около 6 м.
Привод включает два рабочих электродвигателя с фазным ротором по 200 кВт каждый, один дополнительный двигатель холостого хода мощностью 50 кВт и редуктор. Рабочая скорость элеватора — 138 м/мин. Уменьшенная скорость холостого хода, равная 15 м/мин, введена для снижения интенсивности износа подшипников и осей шкивов диаметром 1500 мм, испытывающих при работе элеватора значительные нагрузки и вибрации. Управляют конвейером машинист погрузочного комплекса и машинист пункта приема грунта.
Номинальная производительность конвейера — 900 т/ч, средняя — около 700 т/ч. Монтаж оборудования составляет около 3 мес. Элеваторы данного типа обеспечивают подъем грунта с глубины до 240 м. Существенный недостаток ленточных ковшовых конвейеров — их высокая стоимость.
В Японии широкое распространение получили цепные элеваторы с опрокидными ковшами, шарнирно соединенными с тяговым органом. Такую конструкцию применили, в частности, на строительстве ст. «Мидзута-те» Токийского метрополитена. Вертикальный участок составлял 28,7 м, горизонтальный — 10,6 м. При скорости движения цепи 15 м/мин и емкости ковшей 0,1 м номинальная производительность составила 60 м3/ч, наибольшая кусковатость песчаного грунта равнялась 50 мм. Установленная мощность привода — 36 кВт. У ковшовых цепных конвейеров два основных недостатка: значительный износ цепей и металлоконструкций, а также трудности, связанные с очисткой ковшей от налипшего грунта.
Уменьшение габаритов, массы и энергоемкости машин, полная автоматизация — основные направления совершенствования конвейеров. Фирма «Синко Кико» разработала и серийно выпускает шахтные элеваторы с непрерывной загрузкой и порционной разгрузкой грунта (рис. 2.6), транспортируемого на горизонтальных полках [Метрострой. 1982. № 2. С. 19–31].
Грузонесущие полки шарнирно закреплены на четырех тяговых цепях и обладают необходимой жесткостью в направлении сверху вниз и подвижностью в направлении снизу вверх. В зоне загрузки элеватора промежутки между полками перекрываются закрепленными на них открылками, что предупреждает просыпание грунта, подаваемого шнековым питателем. Решена и очистка полок от налипшего грунта: после разгрузки они поворачиваются рабочей поверхностью вниз, что дает возможность в случае необходимости применять различные устройства для очистки. Высота элеватора регулируется путем наращивания вертикальной несущей конструкции и уменьшения длины горизонтального участка, снабженного передвижной несущей рамой.
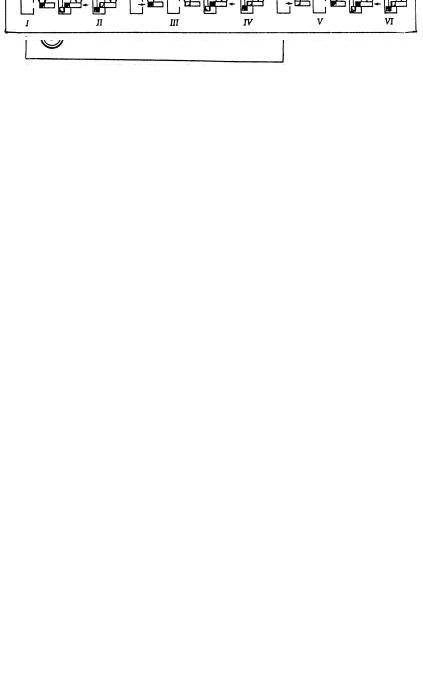
Рис. 2.6. Шахтный элеватор с непрерывной загрузкой и порционной разгрузкой грунта
Полочные шахтные элеваторы применяют в Японии на многих объектах подземного строительства, в том числе при щитовой проходке тоннелей метрополитена. Наибольшая производительность, достигнутая при сооружении тоннеля в глинистых грунтах, — 1000 м3/сут. Эти машины малошумны, что позволяет использовать их в условиях городского строительства и в ночное время.
Японской фирмой «Токю Кэнсэцу» разработан и изготовлен шахтный подъемник возвратнопоступательного действия. Принцип его действия показан на рис. 2.7.
Рис. 2.7. Схема, характеризующая принцип действия шахтного подъемника фирмы «Токю Кэнсэцу» (Япония)
На обеих ветвях грузонесущей цепи монтируют четное число бадей через одинаковое расстояние по вертикали. В плане их устанавливают вплотную друг к другу.
Положение I на рис. 2.7 (левые бадьи 1, 3 выше правых 2, 4) можно условно принять за исходное. В положении II первые находятся в крайнем нижнем положении, вторые — в крайнем верхнем, при этом нижняя левая бадья — под загрузкой. После заполнения бадьи система возвращается в исходное положение и грунт из нижней левой бадьи 1 перегружается в нижнюю правую 2 (положение III). В положении IV нижняя левая бадья заполняется снова, а из нижней правой грунт подается в верхнюю левую. В положении V система снова находится в исходной позиции: грунт из обеих левых бадей перегружается соответственно в нижнюю и верхнюю правые. В положении VI верхняя правая бадья разгружается в приемный бункер, а левые снова заполняются из расходного бункера и из нижней правой бадьи. Таким образом, выдача грунта происходит через такт, при каждом подъеме правых бадей.
На рис. 2.7 показаны две пары бадей. Очевидно, что количество пар может быть любым в зависимости от расстояния между бадьями при данной высоте подъема, и от того, в какую сторону должна производиться выдача грунта. Каждая бадья представляет собой небольшой бункер с дугообразным дном и одной подвижной стенкой, закрепленной на горизонтальном валу. Днища всех левых бадей выполнены с общим наклоном в правую сторону, правых — в левую. Соответственно зеркально расположены и поворотные стенки:
улевых бадей справа, у правых — слева.
Вположении «закрыто» стенки фиксируются стопорами. Приводом служит гидродвигатель, установленный под днищем бадьи и соединенный с валом стенки цепной передачей. Во время разгрузки бадьи стенка совершает один оборот. Основная часть грунта высыпается из бункера под действием силы тяжести, остатки счищаются с боков и днища наружной стороной поворотной стенки. Если грунт вязкий и тяжелый, поворотную стенку снабжают одной-двумя дополнительными лопастями разной высоты для послойной очистки налипшего грунта. Аналогичная однолопастной поворотной стенке конструкция используется как дозатор и на откаточном горизонте для подачи грунта из промежуточного бункера в нижнюю левую бадью.
2.2.4. Спуск и подъем людей в вертикальных выработках
При проходке устьев, технологических отходов и самих неглубоких стволов выдачу грунта на поверхность и доставку материалов в забой осуществляют с помощью грузовых подъемов, оснащенных специально переоборудованными в этих целях кранами, лебедками и другими машинами. Спуск и подъем людей в стволах глубиной до 25 м обычно не механизирован, хотя в течение смены могут иметь место: одно- и многоразовые перемещения проходчиков, маркшейдеров, лиц технического надзора с поверхности в выработки и обратно; ежесуточные плановые ремонтно-профилактические осмотры ствола и оборудования; периодические посещения мест работ представителями заказчика, органов Госгортехнадзора, ВГСЧ, проектной организации и др.; непредвиденные спуски при аварийных и спасательных работах. Пешие передвижения людей с различной физической подготовкой и разного возраста, нередко с инструментами или приборами происходят по мало приспособленным навесным, выдвижным или секционным лестницам, либо лестничным отделениям. Применение тех или иных решений зависит от глубины размещения рабочих мест, частоты пользования, условий подземной среды и имеет весьма условные требования.
Приставные и навесные лестницы, устанавливаемые как вертикально, так и с углом наклона к горизонту 75°, используют при перепаде высоты рабочих площадок не более 10 м. При превышении этой величины устраивают промежуточные площадки для отдыха. В целях обеспечения безопасности лестницы длиной более 5 м должны быть снабжены дуговыми ограждениями или канатом с ловителем для закрепления карабина предохранительного пояса. Изготовляют их из профильной стали в условиях строительной площадки [Метрострой. 1990. № 1. С. 21–25].
Стволы глубиной более 10 м в процессе проходки, как правило, оборудуют постоянными лестничными отделениями (параллельно с армированием) или маршевыми спусками. Первые устраивают между стационарными полками из маршей с перилами из профильного металла и обшивки из досок или металлического сетчатого ограждения. Их высота (3–8 м) зависит от принятого шага размещения полков. Для беспрепятственного продвижения по стволу в последних предусматривают проемы. Маршевые спуски с ограждением по размерам в плане выполняют в 1,5–2 раза меньше лестничного отделения. Небольшие размеры маршевого спуска в плане позволяют осуществлять более гибкую его привязку в сечении ствола. Трудоемкость изготовления и монтажа за счет сборности и укрупнения элементов снизилась, а замена дерева металлом повысила пожарную безопасность.
Лестничное отделение и маршевую лестницу устраивают вслед за проходкой с отставанием от 4 до 20 м от забоя, которое зависит от ряда факторов: способа разработки забоя, степени механизации погрузки и выдачи грунта, организации работ в стволе. Для заполнения пространства между полком или площадкой и забоем используют приставные, навесные, выдвижные, телескопические и другие лестницы.
При проходке стволов глубиной более 25 м, спуск, подъем и выход людей на поверхность требуется механизировать. Независимо от наличия механического подъема стволы во всех случаях оборудуют лестничными отделениями.

В настоящее время внедряются более совершенные способы сооружения стволов с применением проходческих комплексов. При этом используют бадьи большой вместимости и новые типы погрузочных машин и полков. Доставка людей осуществляется в таких бадьях с помощью грузолюдских подъемов. На случай экстремальных ситуаций предусматривается аварийноспасательная лестница. Ее длина должна обеспечивать одновременное размещение на ней всех работающих самой многочисленной смены. Аварийно-спасательная лестница крепится к канату лебедки, имеющей механический и ручной приводы. Во время производственного процесса она располагается над проходческим полком и опускается в забой через специальный проем только в случае аварии. Для сообщения между полком и забоем, кроме спасательной, предусматриваются телескопическая или канатная лестницы.
Применение приставных, навесных, выдвижных, телескопических и других вертикальных лестниц не целесообразно из-за больших затрат времени и не соответствует современным эргономическим требованиям. Скорость передвижения по ним в 8–10 раз меньше, чем при подъеме проходческой бадьи; затрачиваемая энергия резко возрастает с увеличением угла наклона лестницы. При подъеме по вертикальной лестнице трудно быть в устойчивом равновесии на ступеньке и для его сохранения требуются дополнительные физические усилия, вызывающие преждевременную усталость и, следовательно, являющиеся источником несчастных случаев.
На безопасность людей при эксплуатации лестниц (больше, чем у других конструкций) влияют и неблагоприятные факторы специфических шахтных условий, такие как влажность, температура, притоки воды, грязь и др. Лестницы не снабжены приспособлениями, предохраняющими людей от случайно падающих предметов. Поэтому наиболее частые случаи падения человека в шахту связаны с использованием лестницы вертикальной конструкции. Кроме того, подъем пострадавшего на поверхность становится проблемой и осуществляется в каждом конкретном случае импровизированно.
Наличие лестницы в забое неблагоприятно отражается также на выполнении горнопроходческих операций. Чтобы создать нормальные производственные условия для защиты от случайных повреждений, лестницу убирают на безопасную высоту. Монтажные и демонтажные процессы, а также перемещение по стволу ведут с применением ручного труда без должного обеспечения требований безопасности.
Высокие аэродинамические сопротивления, связанные с несовершенством конструкций лестниц, большой загруженностью площади сечения ствола и относительно небольшими расстояниями между полками или площадками, зачастую приводят к нарушению поступления нормативного количества воздуха в забой и к увеличению энергетических затрат на проветривание. Предпочтительным по темпам и качеству и потому чаще встречающимся на практике методом организации сооружения стволов является армирование с устройством лестниц после проходки ствола на полную глубину, завершения работ по устройству сопряжений околоствольного двора и гидроизоляции. В период же строительства в нарушение элементарных требований охраны труда часто пользуются вертикальными лестницами.
Внедрение перевозки людей бадьями сдерживается высокими затратами на оснастку грузолюдских подъемников, потребностью в специальных лебедках для навески спасательной лестницы, значительной продолжительностью монтажных и пусконаладочных работ. Производительность бадьевого подъема снижается из-за двойственности назначения системы — перевозки людей и выдачи на поверхность грунта. В результате затраты значительно превышают получаемый эффект, поэтому для комплексного решения проблемы механизации сооружения ствола предпочитают крановую проходку грузовыми бадьями с устройством пешеходных лестниц.
Негативное влияние на выбор бадей в качестве средства для перевозки людей оказывают и конструктивные особенности бадей: неприспособленность их для этой цели и несоответствие условиям транспортировки пострадавших при несчастном случае; ограниченность провозной способности: при численности смены 6–8 чел. и норме на 1 м2 днища бадьи — 4 чел. их доставку на рабочие места и подъем на поверхность осуществляют в два или несколько приемов (табл. 2.1).
Таблица 2.1
Основные характеристики бадьевого подъема
Величина показателя для бадей типа:
Наименование показателей
БП-1 БП-1,5 БПС-2 БПС-2,5 БПС-3
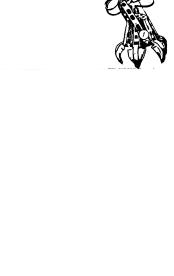
Вместимость бадьи, м3 |
1 |
1,5 |
2 |
2,5 |
3 |
||
Площадь днища бадьи, м2 |
0,8 |
1 |
1,2 |
1,2 |
1,6 |
||
Кол-во |
одновременно |
3 |
4 |
5 |
5 |
6 |
|
размещаемых людей |
|||||||
|
|
|
|
|
Таким образом, для улучшения условий труда при сооружении стволов и повышения безопасности персонала необходим отказ от пеших перемещений по лестницам и совершенствование соответствующих транспортных средств. Значительные возможности для решения этой проблемы появляются при использовании одноконцевой вспомогательной установки людского подъема, которая состоит из временной клети, перемещающейся по жестким односторонним проводникам, шкива для каната и лебедки с механическим и резервным ручным приводом. Установка может применяться как средство для перевозки людей, так и в качестве аварийноспасательного устройства. Она позволяет заменить дорогостоящие и трудоемкие при обслуживании грузолюдские подъемные средства и ускорить оснастку стволов проходческим оборудованием. Размеры клети должны обеспечивать не только одновременную перевозку всех рабочих наиболее многочисленной смены, но и иметь достаточно места для размещения носилок с пострадавшим и для двух сопровождающих.
Анализ производственных процессов в забое, ремонтно-про-филактических осмотров ствола, а также аварийно-спасательных работ позволил определить минимально необходимый размер полезной площади пола клети — не менее 1,8×1 м для размещения одновременно 9 человек. Клеть таких размеров не мешает проходке и дает возможность хранить ее в пределах ствола.
Применение лебедок с комбинированным приводом типа ЛППР и ЛПЭРП не противоречит требованиям техники безопасности и обеспечивает подъем людей на поверхность при обесточивании установки. Использование установки позволяет предотвратить усталость людей при спуске-подъеме, а также сократить время на их доставку. Так, теоретически спуск пешком на глубину 25 м бригады из 10 человек (при средней скорости движения 0,3 м/с) занимает 15 мин, а с помощью установки (при минимальной скорости перемещения клети 1,3 м/с) с учетом времени посадки в клеть и выхода из нее — не более 6 мин. Чтобы не нарушать стабильность строительного процесса, установка подъема-спуска должна работать строго по графику. Потребность в ней не исключается и при наличии главного грузолюдского бадейного подъема. Ежесуточные профилактические осмотры машин и механизмов, проведение ремонта и других операций не будут оказывать большого влияния на нормальное функционирование ствола.
2.3. Механизированные комплексы для проходки и возведения крепи стволов
2.3.1. Стволовая проходческая машина ПМС
Институтом «КузНИИшахтострой» создана и испытана в промышленных условиях стволовая проходческая машина ПМС (рис. 2.8).
Рис. 2.8. Стволовая проходческая машина ПМС: 1 — грейфер;
2 — стреловой манипулятор;
3 — силовой блок;
4 — блок механизма поворота
иотклонения манипулятора; 5 — кабина оператора; 6 — подвеска кабины
Машина ПМС предназначена для проходки вертикальных шахтных стволов диаметром от 5,0 до 8,0 м в свету с максимальной глубиной, зависящей от производительности применяемых
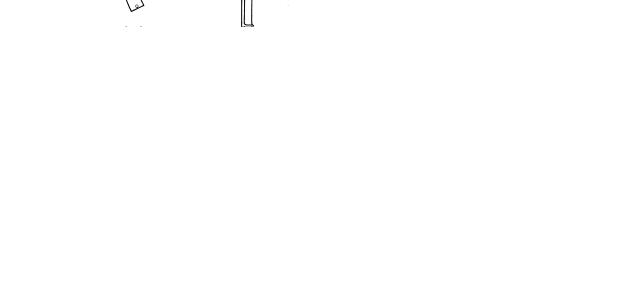
подъемных механизмов. Основной функцией машины ПМС является погрузка разработанного грунта. Кроме того, с ее помощью можно вести его разработку, бурение шпуров, установку элементов сборной обделки и другое путем использования сменных рабочих органов манипулятора: бурильных машин, молотов, грузовых захватов и пр. (рис. 2.9).
а) |
б) |
в) |
Рис. 2.9. Навеска сменных рабочих органов на манипулятор ПМС:
а— бурильная установка; б — варианты устройств для монтажа тюбингов;
в— схема подвески гидромолота к стреле машины
Согласно основной технологической схеме, машину подвешивают к канату лебедки. На время работы она обычно жестко соединяется с проходческим полком, опускаясь в процессе проходки ствола вместе с ним (или при помощи специального устройства — независимо от него). Для профилактического обслуживания и защиты от действия взрыва при буровзрывной разработке грунта машину складывают и поднимают лебедкой выше нижней площадки полка [41, 43, 46]. В табл. 2.2 приведена техническая характеристика машины ПМС.
Таблица 2.2
Характеристика машины ПМС |
||
|
|
|
Показатель |
Значение |
|
показателя |
||
|
||
|
|
|
Вместимость грейферов, м3 |
0,25; 0,33 |
|
Техническая производительность, м3/мин |
0,9; 1,2 |
|
Продолжительность рабочего цикла, с |
18 |
|
Тип привода |
гидравлический |
|
Напряжение электросети, В |
380; 660 |
|
Габаритные размеры в транспортном положении без |
|
|
рабочего органа, мм: |
|
|
в плане |
1200×1200 |
|
высота |
10 000 |
|
Масса машины в комплекте поставки, кг |
6 350 |
|
Кол-во проходчиков для обслуживания машины, чел. |
1 |
Перед традиционными пневматическими монорельсовыми машинами типа КС с канатной подвеской грейфера, ПМС обладает рядом существенных преимуществ:
более высокая степень заводской готовности, так как ее основная часть (манипулятор, блок механизма поворота манипулятора и кабина) транспортируется в сборке на специальной крепежной раме. Это позволяет свести монтаж машины в стволе к болтовому соединению нескольких фланцев, подвески рабочего органа и подключению силового кабеля;
один тип ПМС можно применять в широком диапазоне диаметров стволов без дополнительных затрат на изготовление и установку кругового монорельса;
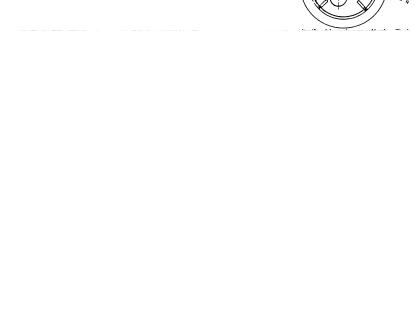
компактность машины освобождает значительную часть поперечного сечения ствола, облегчает расположение технологических трубопроводов и другого оборудования;
электропривод обеспечивает пониженный уровень шума (85 дБ вместо 112 дБ), отсутствие водомасляной эмульсии в атмосфере от выхлопа сжатого воздуха, снижение затрат на электроэнергию, легкость регулирования режима работы, надежную защиту конструкции машины от действия экстремальных нагрузок;
жесткая связь рабочего оборудования машины дает возможность повысить ее быстродействие (минимальная продолжительность цикла черпания — 16 с), снизить удельную металлоемкость, расход электроэнергии при увеличении технической производительности, а также расширить технологические возможности за счет навески различных сменных органов;
связь невращающейся кабины с корпусом машины при помощи специальной подвески одновременно с возможностью изменения компоновки машины позволяет удалить оператора от источников вибрации, шума, увеличить обзорность и т.д.;
проход машины через полок способствует более надежному предохранению ее от действия взрыва, уменьшению высоты подъема полка перед взрывом, созданию хороших условий для профилактического обслуживания в стволе и возможности выдачи для крупного ремонта на поверхность.
Перечисленные достоинства машины ПМС указывают на возможность эффективной замены ею пневматических грузчиков типа КС-3 с ручным вождением, которые все еще применяются при строительстве вертикальных стволов на метрополитенах России.
На рис. 2.10, а представлен один из возможных технологических вариантов использования машины при проходке ствола буровзрывным способом с креплением тюбингами.
При этом машину предполагается применять не только для погрузки грунта, но также для бурения шпуров и монтажа тюбингов.
Применение машины ПМС-1 и комплекта навесного оборудования для погрузки горной массы, отбойки грунта, бурения шпуров и монтажа обделки обеспечивает комплексную механизацию всех процессов при сооружении шахтных стволов. Особый интерес представляет использование пневмомолота для отбойки грунта, что дает возможность отказаться от буровзрывных работ при проходке стволов в условиях города.
а) |
б) |
в) |
Рис. 2.10. Технологические схемы проходки стволов с использованием машины ПМС:
а, б — положение машины в процессе и после работы (соответственно) при проходке ствола буровзрывным способом с креплением тюбингами; в — рабочее положение машины при возведении ствола с обделкой