
692
.pdfИз проведенного анализа данных треста Донецкшахтопроходка сделан вывод, что при средней скорости проходки 80–120 м/мес. применение параллельно-щитовой технологической схемы не дает ощутимых преимуществ перед совмещенной технологической схемой в скорости сооружения стволов, и в то же время существенно усложняется и удорожается оснащение и организация проходки. Однако некоторые отечественные исследователи считают целесообразным увеличение объемов применения параллельной технологической схемы, как более эффективной.
В связи с этим во ВНИИОМШСе ведутся работы по созданию технологии проходки стволов и средств механизации с возведением постоянной крепи и одновременным армированием. Работой предусматривается:
замена призабойного щита-оболочки временной ограждающей (в случае необходимости упрочняющей) анкерной крепью и металлической сеткой, возводимой с помощью специальной установки;
возведение постоянной крепи с отставанием от забоя на 8–12 м; спуск жестких бетонных смесей в специальных контейнерах и укладка смесей за опалубку;
армирование ствола заходками одновременно с наращиванием постоянных проходческих трубопроводов.
Соотношения скоростей проходки при параллельно-щитовой и совмещенной технологической схемам, установленные в процессе исследований, приведены в табл. 2.7.
Исследования показали, что при снижении скорости и производительности труда от установки временной крепи и при спуске бетона в контейнерах разрабатываемая параллельная технология имеет ощутимое преимущество перед совмещенной технологической схемой только в лучших условиях работы временной крепи.
Таблица 2.7
|
|
|
|
Сравнительные характеристики |
|||||
|
|
|
различных технологических схем проходки стволов |
||||||
|
|
|
|
|
|
|
|
|
|
|
|
Объем |
|
Техническая скорость, м/мес. |
|
|
|||
|
Высота |
|
|
|
|
|
|
|
|
|
при параллельно-щитовой |
при совмещенной |
|
||||||
Диаметр |
бетонной |
|
|||||||
ствола, |
опа- |
смеси |
|
проходке |
|
|
проходке |
|
|
лубки, |
|
|
|
|
|
||||
м |
на 1 м |
|
|
|
|
|
|
|
|
|
|
|
|
|
|
|
|||
м |
|
При суточной скорости, м/сут |
|
|
|||||
|
ствола, м |
|
|
|
|||||
|
|
|
|
|
|
|
|
|
|
|
|
|
4 |
8 |
12 |
4 |
8 |
12 |
|
5 |
3 |
8 |
110 |
201 |
280 |
97 |
163 |
211 |
|
9 |
3 |
15 |
110 |
201 |
280 |
88 |
140 |
174 |
|
5 |
6 |
8 |
115 |
219 |
315 |
101 |
174 |
230 |
|
9 |
6 |
15 |
115 |
219 |
315 |
92 |
148 |
186 |
|
Это преимущество важно, но недостаточно, чтобы отвлечь производственниковшахтостроителей от технологически простой и надежной схемы проходки.
Расчеты показывают, что при совмещенной технологической схеме напряжения в бетонной крепи в течение первых двух суток твердения бетона могут превосходить ее прочность из-за ползучести пород, что неблагоприятно скажется на конечной прочности и несущей способности крепи.
2.6.2. Устройство временной крепи при сооружении стволов по параллельной технологической схеме
Отставание бетонной крепи от забоя при параллельной схеме проходки требует защищать проходчиков временной крепью (или щитом). Исследования и опыт применения новоавстрий-ского метода проведения горных выработок показали преимущества набрызг-бетонной временной крепи, так как при ней лучше используется несущая способность массива.
Основоположник новоавстрийского метода профессор Л. Мюллер так характеризует основные принципы этого современного, наиболее экономичного метода.
Породный массив вокруг подземной выработки является, по существу, несущим элементом крепи. Поэтому одна из главных задач — всемерное сохранение естественной прочности массива. Следует по возможности предотвращать разрыхление породы, поскольку оно приводит к значительной потере прочности и развитию одноосных и двухосных напряженных состояний, так как горные породы их не выдерживают.
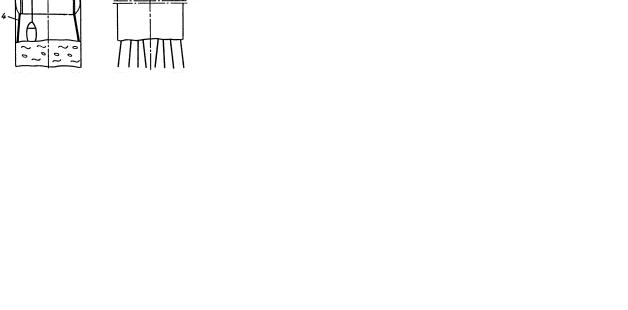
При значительных деформациях массива временная крепь должна сооружаться на всей породной поверхности выработки. Наиболее эффективна набрызг-бетонная крепь. Она должна быть тонкой и податливой, что приведет к минимуму восприятия изгибающих моментов и трещинообразования. Если необходимо усилить временную крепь, то нужно не увеличивать толщину слоя набрызг-бетона, а применить дополнительно металлическую сетку и анкерную крепь.
Нанесение тонкого слоя (1–5 см) набрызг-бетона позволит значительно легче механизировать и автоматизировать работы по возведению временной крепи с совмещением уборки породы в забое ствола, чем при возведении крепи с помощью установки анкеров и сетки, в то же время исключается расход металла. В условиях, где потребуется усиление набрызг-бетонной временной и постоянной крепей, установку анкеров и сетки целесообразней производить с нижних этажей проходческого полка, а не в призабойном пространстве.
Опыт применения в отечественной практике параллельно-щитовой технологической схемы проходки стволов показал, что при высоких скоростях проходки набрызг-бетонную временную крепь можно не применять или наносить с проходческого полка на значительном расстоянии от забоя, желательно ограждать проходчиков в забое от падения породы со стенок ствола средствами, не требующими затрат труда проходчиков и времени проходческого цикла.
При этом щит-оболочку при параллельной проходке целесообразно заменить легкой каркасно-пластинчатой временной крепью, быстро устанавливаемой в призабойном пространстве и поднимаемой перед взрывом породы.
Б.А. Гей совершенствовал каркасно-пластинчатую крепь, применяемую при проходке геолого-разведочных вертикальных выработок, для условий буровзрывной проходки шахтных стволов и рекомендует использовать такую крепь при проходке стволов по параллельной технологической схеме [Шахтное строительство. 1991. № 3. С. 17–19].
Крепь (рис. 2.31) состоит из трубчатых колец 1, пластинчатых затяжек 2, одетых своими проушинами на кольца, трубчатых ограничителей 3, опорной жесткой части 4. Крепь подвешивается к проходческому полку 5, на котором установлена лебедка с червячной самотормозящей передачей, канат которой полиспастно огибает шкивы на опорной части крепи. Наружный диаметр крепи в подвешенном состоянии меньше диаметра закрепленного ствола на 5–10 см.
a) б)
Рис. 2.31. Каркасно-пластинчатая крепь:
а — рабочее положение крепи; б — положение крепи в момент взрыва породы; 1 — трубчатые кольца; 2 — пластинчатые затяжки; 3 — трубчатые
ограничители сближения колец; 4 — опорная часть крепи; 5 — проходческий полок; 6 — опалубка; 7 — бетонная крепь ствола
Крепь устанавливается в рабочее положение путем опускания полка с упором крепи на взорванную в забое породу до выгиба пластинчатых затяжек и упора их в выступы пород-
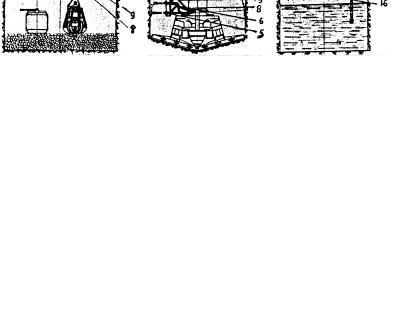
ной стенки ствола или упора трубчатых ограничителей в кольца. При опускании крепи и упоре ее в породу выбирается полиспастный канат лебедкой на полке, которым фиксируется рабочее сжатое положение крепи во время уборки породы в забое и выполнение других проходческих работ.
В трещиноватых с возможными вывалами породах рекомендуется навешивать с полка за крепь полотнища стальных сеток и применять затяжки с проемами для бурения шпуров и закрепления сетки анкерами. Перед подъемом крепи в безопасный от взрыва участок ствола с лебедки на полке сматывают часть навитого каната и этим удлиняют крепь, уменьшая арочный изгиб затяжек и проверяя отсутствие или наличие прижатия сетки сдвинувшейся породной глыбой.
При отсутствии зажатия сетки породной глыбой крепь удлиняют до полного выпрямления затяжек и поднимают, а при наличии зажатия определяют простукиванием зажатую затяжку и закрепляют породную сдвинувшуюся глыбу сеткой и анкерами ниже и выше, закрепляя анкерами верх и низ полотнища, уменьшая диаметр крепи и поднимая ее.
Затяжки рекомендуемой крепи при арочном их изгибе будут упираться в выступающие части породной стенки и поддерживать их.
Применение легкой каркасно-пластинчатой крепи и практическое исключение ее зажимов позволяют избежать аварийности и улучшить показатели параллельной проходки.
2.6.3. Крепление шахтных стволов набрызг-бетоном без присутствия людей в забое
В журнале «Подземное пространство мира» № 5–6 за 1993 г. в публикации «Дистанционное набрызг-бетонирование при сооружении шахтных стволов и тоннелей» приводится информация о том, что английская фирма «Бритиш Коул» в 1986 г. разработала систему крепления шахтных стволов набрызг-бетоном без присутствия людей в стволе. С помощью этой технологии и оборудования на различных объектах в Великобритании и Африке возведена крепь более чем на 20 скважинах и стволах глубиной до 220 м и диаметром от 0,7 до 4,5 м.
Система включает подачу раствора насосом во вращающийся диск, который наносит набрызгбетонную смесь на породные стенки выработки. Вращающийся диск установлен по центральной оси ствола на восьмиколесной раме.
Между тем более тридцати лет назад в России Х.А. Абрамсоном было разработано устройство для крепления шахтных стволов набрызг-бетоном без присутствия людей в зоне возведения крепи. Это оригинальное техническое решение предусматривало возможность применения его при сооружении стволов с помощью буровзрывного способа разработки забоя, бурения шахтных стволов и стволопроходческих комбайнов (рис. 2.32).
а) |
б) |
в) |
Рис. 2.32. Конструктивно-технологические схемы для крепления шахтных стволов набрызг-бетоном без присутствия людей в зоне работ:
а — буровзрывной способ; б — комбайновый; в — бурений; 1 — пневмобетономашина; 2 — приемный бункер; 3 — став труб для подачи сухой смеси;
4— соплодержатель; 5 — сопло, наносящее 1-й слой бетона; 6 — то же, 2-й; 7 — то же, 3-й; 8 — шланг для подачи сухой смеси; 9 — то же для воды;
10 — затирочное приспособление; 11, 19 — полки; 12 — кабина; 13 — сопло для обмывки стенок; 14 — щитки полка; 15 — насос для откачки раствора из ствола; 16 — всасывающий шланг; 17 —
нагнетательный шланг; 18 — буровая колонна; 20 — кабина машиниста; 21 — контейнер для подачи сухой смеси; 22 — направляющая рама; 23 — монорельс; 24 — тельфер
В качестве вращающейся турели по центру ствола, на которой закреплена система сопел для подготовки поверхности породных стенок (промывки напорной струей воды) и нанесения двух слоев набрызг-бетонной смеси, при буровзрывном способе используется кабина породопогрузочной машины, при комбайновом — вал, оборудованный системой породоразрушающих инструментов, при бурении — подвесной полок с насосной установкой для откачки раствора, необходимого для заполнения ствола в процессе бурения [Метро. 1994. № 3. С. 28–29].
При этом следует обратить внимание, что содержание данного изобретения неоднократно публиковалось в разных журналах, брошюрах, монографиях и учебниках.
Разработку этого изобретения должны были выполнить в первую очередь профилирующие институты ЦНИИподземмаш, ВНИИОМШС, КузНИИшахтострой, Криворожский филиал института Гипроцвет и др., отвечающие за развитие стволостроения.
К сожалению, этого не произошло. Несмотря на прошедшие десятилетия, данное техническое решение остается актуальным и в настоящее время с учетом совершенствования техники набрызг-бетонирования.
Одна из причин сложившейся ситуации — отсутствие заинтересованности метро- и тоннелестроительных организаций в применении тонкостенных высокопрочных крепей оболочек, поскольку это снижает стоимость сооружения стволов, где затраты на крепь составляют более 60 %.
2.6.4. Прогрессивные технологии проходки восстающих выработок способом бурения
сприменением химических материалов для крепления
Вмировой практике широко применяется проведение вертикальных выработок способом бурения снизу вверх. Повышение износостойкости режущего инструмента, надежности оборудования, снижение его относительной стоимости позволяют прогнозировать перспективы применения указанного способа проходки [25, гл. 18, 43; ч. 3, гл. 5].
ВНИИОМШС (Харьков) для проходки с поверхности вертикальных шахтных стволов диаметром до 5,9 м в грунтах крепостью 120 МПа разработал бур «Эффект» (рис. 2.33) в составе штанговой установки с эрлифтом. Его действие, основанное на использовании нетрадиционной схемы разрушения грунтового массива, более эффективно и экономично по сравнению с традиционным буровзрывным способом. Бур «Эффект» оснащается специальным шарошечным инструментом и состоит из отдельных сборочных единиц, компонуя которые можно бурить стволы любого диаметра в пределах от 2,8 до 5,9 м.
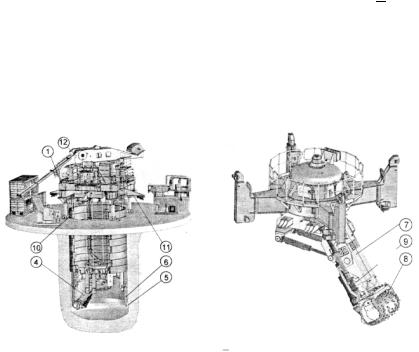
Работа бура «Эффект» реализует технологию разрушения грунта крупным сколом, обеспечивающим:
минимальные затраты и расход породоразрушающего инструмента;
уборку из забоя и выдачу разрушаемого грунта на поверх-ность в неизмельченном виде; вертикальность бурения высокой точности; высокие скорости бурения шарошечным инструментом по грунтам, склонным к адгезии.
Бур «Эффект» не содержит технически сложных и малонадежных конструктивных элементов, прост в обслуживании; своей конструкцией в сочетании с оригинальной технологией обеспечивает минимальный объ-ем выемки грунта. Максимальная высота бура 15 м, максимальная масса 200 т. Эксплуатация бура обеспечивается бригадой из четырех человек. Бур удобен для перевозки железнодорожным и автомобильным транспортом, несложен в монтаже на буровой площадке.
В Западной Европе для проходки стволов диаметром до 8,5 м также используют буровые установки с последовательным расширением ствола и извлечением породы через бурильные трубы эрлифтом или способом восстающего бурения.
Однако концепции создаваемого стволопроходческого оборудования не решают проблему строительства шахтных стволов в неустойчивых породах и забоях с большим дебетом воды. При насыщении водой илистых грунтов забой становится неустойчивым — происходит вынос водоносного грунта из-под крепления забоя в выработку. Изменение физико-механических свойств грунта с помощью специальных способов его стабилизации (искусственное замораживание, цементация, водопонижения и т. д.) может дать хороший эффект, но шахтные стволы пересекают обычно разнородные слои с различными реологическим свойствами, водоотдачей, поэтому эффективность выбранного способа закрепления может быть значительно снижена. Существующие методы длительны по времени или экономически затратны — контроль за целостностью создаваемого закрепленного массива ведется по косвенным признакам.
Уравновешивание гидростатического напора водоносных горизонтов заполнением шахтного ствола водой усложняет применение механизмов для выемки грунта, а в некоторых регионах, например в Санкт-Петербурге, где уровень грунтовых вод может быть на 2–3 м ниже поверхности и наличие валунов на всех горизонтах делает это невозможным.
Интересное техническое решение в этом плане предложено специалистами немецкой фирмы «Herrenknecht AG». Совмещение нескольких технологий проходки в одном агрегате обещает положительный результат. Немецкими инженерами используется идея сооружения шахтных стволов способом погружения крепи в тиксотропной оболочке, являющимся одним из классических методов, описанных в учебниках и в данном пособии (см. п. 2.4). Он заключается в следующем [Метро и тоннели. 2005. № 4. С. 22–23].
На балочные пакеты 1 (рис. 2.34) передается нагрузка от гидроцилиндров 2 задавливания ствола. На этих же балках установлены удерживающие гидроцилиндры 3, сквозь полые штоки которых проходят резьбовые штанги, соединяющие бетонное стартовое кольцо с конструкцией балочных пакетов.
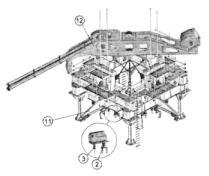
Рис. 2.34. Конструктивные решения стволопроходческого комплекса фирмы «Херренкнехт»
Подобная структура позволяет постоянно контролировать процесс «движение – удержание» погружаемого ствола. В стартовом кольце 4, снабженном мощной стальной режущей кромкой 5, расположена собственно проходческая машина 6. Ее рабочий орган представляет из себя телескопическую стрелу 7 с вращающимся фрезбарабаном 8. На стреле расположен насос 160 кВт 9, откачивающий разработанный грунт. Стоит заметить, что машина рассчитана на глубину подводной экскавации до 85 м, таким образом будет уравновешено гидростатическое давление водонапорных слоев.
Разработка грунта идет секторами по всей площади забоя. При необходимости, например, при встрече с крепкими породами, большими валунами возможно перерезание за периметр режущей кромки. Также в зависимости от физико-механических свойств грунта предусмотрены три фиксированных высотных положения машины относительно забоя. Гидротранспорт разработанного грунта осуществляется на расположенный на поверхности сепараторный узел производительностью 300 м3/ч и позволяющий отделять частицы до 20 мк. Вода после сепарации возвращается обратно в ствол.
Оператор, управляющий комплексом при помощи компьютера, располагает всей информацией, необходимой для выполнения всего технологического цикла:
•контроль за положением рабочего органа;
•производительностью насосов;
•усилием продавливания и удержания;
•контроль за точностью сборки сегментов крепи и т. д.
Высокий уровень компьютеризации не исключает и ручные режимы управления. Кольцо обделки состоит из четырех высокоточных железобетонных сегментов 10
толщиной 350 мм с закладными деталями для крепления:
•направляющей шины для подъема и опускания машины по стволу в случае необходимости;
•труб для зонда навигационной (инклинометрической) системы;
•рукавов высокого давления для подачи бентонитовой суспензии к форсункам стартового кольца.
Сборка сегментов крепи погружаемого ствола ведется на поверхности с помощью четырех монтажных кранов 11, инсталлированных в балки узла продавливания 12. Точность сборки кольца обеспечивается лазерными приборами, установленными на раме балочных пакетов. На ней же смонтирована конструкция с лебедками 13, обеспечивающими подъем и опускание проходческой машины, а также транспортноэнергетической линии.
Эти две системы гидравлически связаны с общей системой управления движением ствола. Лазерная измерительная система является частью общей системы стволопроходческого комплекса. Она используется для наблюдения за положением тюбингов при их установке. Для этого на балочной раме размещены восемь лазеров для измерения расстояния до верхнего тюбинга
сточностью ±0,6 мм на 1 м. Данные отображаются на компьютере, что дает возможность корректировать ход ствола шахты.
Чтобы учесть все возможные отклонения ствола, стартового кольца и машины, выпол-
няются измерения:
• позиции машины с помощью инклинометрической измерительной системы, установленной внутри машины,
• ствола и положения стартового кольца с машиной с помощью зонда, опускаемого в измерительные трубы.
Погрешности измерений до 4 мм на 80 м.
При достижении стволом проектной отметки машина выдается наверх, а в случае отсутствия водонапорных слоев производится подводное бетонирование. Затем через систему подачи бентонитовой суспензии нагнетается цементный раствор за стартовое кольцо и обделку ствола. После осушения ствол готов к дальнейшим работам.
Первый стволопроходческий комплекс подобного типа фирмы «Herrenknecht AG» уже показал высокую эффективность в песчаных обводненных грунтах. В агрегате, приобретенном ООО «СТИС», немецкие инженеры учли пожелания практиков. Возросла общая мощность основных узлов. Резцы фрезбарабана позволяют разрушать валуны с прочностью до 120 МПа.
Проходка с применением VSM-7700/5500 (табл. 2.8) с ноября 2005 г. осуществляется на строительстве приемных шахт на объекте «Продолжение Главного коллектора канализации Северной части Санкт-Петербурга».
Фактором, ограничивающим область применения и сдерживающим повышение темпов сооружения, а в ряде случаев — ухудшающим экономические показатели проходки стволов способом бурения является существенное отставание уровня технологии и отсутствие систем крепления, взаимоувязанных с основными операциями проходческого цикла.
Результаты патентных исследований и анализ научно-техни-ческих источников свидетельствуют о том, что с начала 80-х гг. ряд зарубежных фирм, в первую очередь Японии, Германии, США, проявляют растущий интерес к использованию химических материалов и технологий для возведения тампонажных завес и крепи в процессе проходки горных выработок. В качестве примера можно привести техническое решение, заявленное фирмой «Штабаг-БАУ» (Германия), согласно которому для поддержания выработки при щитовой проходке в породу вокруг выработки нагнетают жидкий твердеющий состав.
Таблица 2.8
|
Технические данные |
||
стволопроходческого комплекса VSM-700/5500 |
|||
|
|
|
|
Внутренний диаметр ствола, мм |
|
5 500–7 700 |
|
Наружный диаметр ствола, мм |
|
6 200–8 400 |
|
Максимальный диаметр резания, мм |
|
8 500 |
|
Глубина ствола, м |
|
до 85 |
|
Стволопроходческая машина |
|
|
|
Вращающий момент, кНм |
|
до 81 |
|
Скорость вращения, об./мин |
|
до 80 |
|
Диаметр режущей части, мм |
|
1 200 |
|
Ширина режущей части, мм |
|
1 540 |
|
Поворот стрелы, град |
|
±190 |
|
Наклон стрелы, град |
|
48 |
|
Удлинение стрелы (телескоп), м |
|
1 |
|
Производительность насоса, м3/ч |
|
275 |
|
Максимальная скорость выдачи грунта м3/ч |
|
60 |
|
Поверхностный комплекс |
|
|
|
Удерживающие гидроцилиндры, кН |
|
8×3 000 ход 1 200 мм |
|
Задавливающие гидроцилиндры, кН |
|
8×2 300 ход 1 500 мм |
|
Лебедка подъема машины: |
|
|
|
— сила тяги (без полиспаста), кН |
|
150 |
|
— вращающий момент привода (дин.), кНм |
|
81,7 |
|
— вращающий момент привода (стат.), кНм |
|
130,8 |
|
Сепараторная установка |
|
|
|
Производительность, м3/ч |
|
300 |
|
Степень отделения, мк |
|
20 |
|
Плотность перекачиваемой пульпы, кг/дм3 |
|
1,3 |
|
Питающий насос 90 кВт, м3/ч |
|
400 |
|
Суммарная установленная электрическая мощность |
994 |
|
|
комплекса, кВт |
|
|
|
|
|
|
К последним достижениям относятся успешно проведенные фирмой «Фостер Миллер» (США) исследования, включающие натурные экспериментальные работы по обоснованию возможности скоростного крепления стволов снизу вверх полимерной крепью.
Таким образом, имеющаяся информация позволяет сделать вывод о применении хи-
мических материалов для целей крепления выработок, как об устойчивой тенденции) в
мировой практике последующих лет.
а
Институтами Минуглепрома и Минхимпрома бывшего СССР были проведены поисковые работы, в результате которых разработаны концепции и подтверждена практическая осуществимость скоростного крепления с применением химических (полимерных) материалов восстающих выработок, проводимых способом бурения. В основе концепций лежат следующие положения.
Высшему техническому уровню соответствует технология, обеспечивающая одновременные (в одном технологическом цикле при цикличной технологии проходки) проведение выработки способом бурения и крепление ее без присутствия людей в забое. По показателям технологичности процесса возведения монолитные виды крепи имеют существенные преимущества по сравнению с иными видами. Химически укрепляющие растворы обладают рядом свойств, обеспечивающих возможность создания новых видов крепи и прогрессивных технологий их возведения.
Всоответствии с изложенным предусматривается создание специального оборудования
иукрепляющего раствора, обеспечивающих формирование в процессе проходки монолитной полимерной или полимерпородной крепи путем подачи в заопалубочное пространство быстротвердеющего раствора и наполнителя — продуктов разрушения пород буровым органом по трассе проведения выработки. При этом:
укрепляющий раствор под действием избыточного давления распространяется в укрепляемой среде и при отверждении в заданный промежуток времени образует замкнутый цилиндр крепи с необходимыми геометрическими параметрами, обладающими заданными физико-механическими свойствами;
распространение химического раствора в направлении проходки обеспечивается перемещением щита-опалубки, снабженного смесителями многократного использования для смешивания компонентов химического раствора и подачи в заопалубочное пространство;
для заданной толщины возводимой крепи соблюдается определенное соотношение
между подачей химического раствора, скоростью перемещения щита-опалубки и его длиной, а также количеством источников нагнетания (смесителей) и временем гелеобразования химического раствора.
Вчасти пространственных схемно-конструктивных решений предпочтительными являются опора привода перемещения щита-опалубки на буровой орган или податчик и размещение транспортных емкостей с компонентами на верхнем горизонте при проходке сверху вниз и на нижнем горизонте при восходящем бурении. Нагнетательно-дозирующее оборудование и энергосистемы могут располагаться в зависимости от протяженности выработки, как в горизонтальной выработке, так и в стволе в составе щита-опалубки.
Вкачестве иллюстрации на рис. 2.35, а показана схема крепления ствола полимергрунтовой, а на рис. 2.35, б полимерной крепью [Шахтное строительство. 1991. №
1.С. 17–18].
П.П.Гальченко и В.В. Чернышенко считают, что в ближайшем будущем целесообразно применение полимерной крепи в скважинах диаметром до 2 м с коротким сроком службы, а применение полимергрунтовой крепи (наполненные системы) в выработках диаметром до 3–3,5 м с более длительным сроком службы, пройденных в неустойчивых породах. В перспективе возможна разработка систем и для крепления стволов большего диаметра.
Результаты теоретических, лабораторных исследований и стендовых испытаний, достигнутый технический уровень, наличие сырьевой и производственной базы в России позволяют предположить возможность разработки серийного оборудования и перспективы широкого промышленного применения химических материалов для целей крепления при буровой проходке.
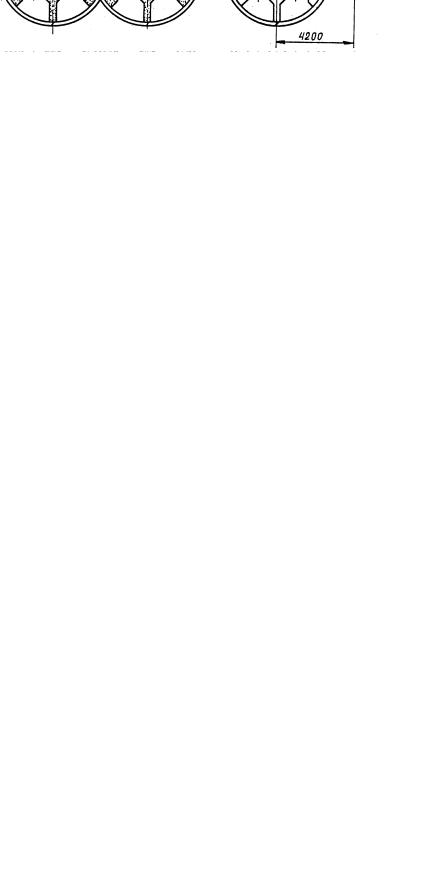
а) |
б) |
Рис. 2.35. Схемы проходки стволов с полимерной крепью:
а — проходка ствола снизу вверх с помощью бурения; б — расширение ствола сверху вниз; 1 — буровой комбайн типа 2KB; 2 — расширитель; 3 — щит-опалубка; 4 — привод перемещения опалубки; 5 — электрогидролинии; 6 — гидропривод и нагнетательная установка; 7 — емкости с химкомпонентами; 8 — полимергрунтовая крепь; 9 — расширитель буровой установки типа БГА; 10 — переставное пикетажное кольцо; 11 — полимерная крепь
3.СООРУЖЕНИЕ ЭСКАЛАТОРНЫХ ТОННЕЛЕЙ
3.1.Нетрадиционные конструктивно-технологические решения эскалаторных тоннелей
3.1.1.Эскалаторы в спаренных тоннелях
Впрактике отечественного метростроения четырехленточные эскалаторы преимущественно размещают в наклонных тоннелях диаметром 9,5 м с обделкой из чугунных тюбингов, что приводит к значительному превышению необходимых пространственных объемов в верхней части сооружения [38, п. 34.3; 46, гл. 6].
С целью сокращения объема проходческих работ и экономии чугунного литья, разработано несколько вариантов технических решений, один из которых предполагает сооружение тоннелей эллиптического сечения с уменьшенным вертикальным диаметром и использованием чугунных тюбингов для кольца диаметром 7,5 м и стальных клинчатых прокладок в своде и лотке (рис. 3.1, а).
а)
б) |
в) |
Рис. 3.1. Варианты технических решений четырехленточных эскалаторов:
а— тоннель эллиптического сечения; б, в — спаренные тоннели в одном
иразных уровнях соответственно

При этом сохраняется существующая технология проходки и может быть использовано имеющееся оборудование, но объем работ сокращается на 10–15 %. В зависимости от инженерногеологических условий в каждом конкретном случае требуются соответствующие расчетные обоснования.
Заслуживает внимания предложение Метрогипротранса сооружать четырехленточные эскалаторы в спаренных тоннелях наружным диаметром 6 м с обделкой из чугунных тюбингов, имеющих общую среднюю стенку из стальных элементов. Подобное решение с установкой вместо стенки колонн с верхним и нижним прогонами было реализовано на двух станциях Будапештского метрополитена.
Целесообразность возведения четырехленточных эскалаторов при существующем дефиците чугунных тюбингов обусловливает необходимость сооружения спаренных наклонных тоннелей с обделкой из железобетонных блоков (рис. 3.1, б, в). Конструкция такой обделки состоит из четырех элементов двух типов с внутренней изоляцией стальным листом толщиной 6 мм. По боковым и торцевым граням изоляции привариваются по 2–3 монтажных уголка с отверстиями для болтовых скреплений. После монтажа уголки срезают, а швы перекрывают привариваемыми накладками. Основные показатели на 1 м длины эскалаторного хода по перечисленным выше вариантам приведены в табл. 3.1.
Таблица 3.1
Сравнительные характеристики вариантов четырехленточных эскалаторных тоннелей
|
изм. |
Величины показателей для тоннеля с обделкой |
||||
Наименование материалов и |
|
|
|
|
||
Круговая |
Эллиптиче |
Двойная |
Двойная |
|||
изделий |
Ед. |
|||||
диаметром |
диаметром |
диаметром |
||||
|
ская |
|||||
|
|
|||||
|
|
9,5 м |
2×6,0 м |
2×5,8 м |
||
|
|
|
||||
|
|
|
|
|
|
|
Грунт по наружному |
м3 |
70,8 |
60 |
53 |
49 |
|
очертанию обделки |
|
|
|
|
|
|
Чугунные тюбинги |
т |
21,4 |
15 |
11,5 |
— |
|
Сварные элементы |
т |
— |
0,2 |
1,4 |
— |
|
Железобетонные блоки |
м3 |
— |
— |
— |
6,9 |
|
обделки |
|
|
|
|
|
|
Металлоизоляция |
т |
— |
— |
— |
1,7 |
|
железобетонной обделки |
||||||
|
|
|
|
|
||
Внутренние железобетонные |
м3 |
6 |
5,2 |
3,8 |
2,8 |
|
и бетонные конструкции |
|
|
|
|
|
|
Чеканочные канавки с |
|
|
|
|
|
|
заполнением свинцовым |
м |
52,8 |
42 |
48,2 |
— |
|
шнуром |
|
|
|
|
|
Проходку спаренных эскалаторных тоннелей рекомендуется вести последовательно. При наличии в их верхней зоне неустойчивых водоносных грунтов возможно предварительное контурное замораживание. Вначале закрепляется контур первой очереди проходки (вокруг одного тоннеля), затем — второй (в зоне другого). Монтаж обделки может выполняться укладчиками, конструкция которых аналогична укладчикам для одиночных тоннелей. В тоннелях с чугунной обделкой диаметром 6 м при сборке конструкции первой очереди устанавливается общая для двух выработок средняя стенка из сварных элементов. Применение для наклонных ходов спаренных тоннелей с обделкой из железобетонных блоков способствует сокращению объемов работ, трудозатрат, общему удешевлению и ускорению строительства. Упрощаются также отделочные работы: открывается возможность использования лакокрасочных покрытий по металлоизоляции или несложного прикрепления к ней декоративных плит [Метрострой. 1987. № 5. С. 14–16].
Развитие технологии сооружения спаренных тоннелей перспективно в связи с более четким разделением пассажиропотоков в вестибюле и распределительном зале путем смещения в вертикальной плоскости одного тоннеля относительно другого. При значительной величине такого смещения (см. рис. 3.1, в) расположение одной пары эскалаторов относительно другой по ширине может быть сближено примерно на 1 м и общая ширина, занимаемая четырьмя лентами, будет такой же, как и в тоннеле диаметром 9,5 м.
Применение спаренных тоннелей дает возможность при малых пассажиропотоках в первый период эксплуатации отнести монтаж двух эскалаторов и отделочные работы во втором тоннеле на более поздний срок.