
692
.pdfлебедками, одна из которых установлена на поверхности у ствола, другая — на верхнем ярусе полка.
Работа в забое была организована в три семичасовые смены, по 8 чел. в каждой. По циклограмме за 5 смен сооружали 3 м готового ствола.
Принятая технология проходки вызвала необходимость изменения конструкции рассечки. Более рациональное решение — примыкание ствола к венттоннелю сверху с сооружением горизонтальной рамы проема, что упростило характер работ и обеспечило большую их безопасность.
Такая технология позволила значительно сократить срок строительства вентиляционного ствола, уменьшить объем работ по монтажу горного комплекса и исключить временную армировку ствола.
2.5.2.Проходка ствола
сприменением шагающего полка ПШП-1
Технология проходки ствола с армировкой для будущего клетьевого подъема и совмещением процессов гидроизоляции с разработкой грунта и монтажом обделки была применена на шахте № 530 первого участка Правобережной линии Ленинградского метрополитена. Технология разработана отделом СКТБ ГТМ совместно со СМУ № 11 Ленметростроя [Метрострой. 1983. № 8. С. 5–6].
Ствол шахты проходили с применением замораживания (в зоне неустойчивых четвертичных отложений) и обычным способом. Обделка чугунная диаметром 6 м.
Во время замораживания грунтов монтировали горный комплекс. Для проходки ствола применили трехъярусный шагающий полок, конструкция которого обеспечивала использование двухбадьевого подъема с двумя машинами.
Монтаж горного комплекса, проходческого полка и обустройство поверхности завершились до окончания процесса замораживания. Полок монтировали в пределах копра и форшахты. Грунт разрабатывали заходками на глубину 1 м с устройством опережающего зумпфа — от центра ствола секторами к наружному контуру, участками для двух тюбингов. Грунт выдавался двумя бадьями емкостью 1 м3. На рабочем горизонте горного комплекса бадья устанавливалась на специальную тележку и подавалась в опрокидыватель.
После завершения монтажа очередного кольца производилось первичное нагнетание цементно-песчаного раствора. Контрольное нагнетание и чеканка швов велись с верхнего и среднего ярусов проходческого полка постоянно и прекращались только на время монтажа армировки ствола и передвижки полка. Ярусы армировки устанавливали с шагом 3 м. Ее монтаж осуществлялся с верхнего яруса проходческого полка.
Расстрелы подавали к месту установки по лесопуску и укладывали на верхнем ярусе полка, затем с помощью подъемной машины устанавливали на заранее смонтированные столики. Параллельно обшивался лесоспуск, лестничное отделение, наращивались проводники, после чего полок передвигался и начиналась разработка забоя на очередную заходку.
В процессе сооружения был опробован полок с новым принципом шагания за счет «плавающего» промежуточного яруса. Сборно-разборный каркас полка состоит из двух ярусов: нижнего и верхнего, жестко соединенных между собой направляющими стойками («лыжами»). Внутри каркаса расположен средний, подвижной ярус. На нижнем и среднем ярусах предусмотрены четыре горизонтальных стопора для фиксирования полка в стволе (рис. 2.24).
Верхний и средний ярусы связаны вертикальными силовыми цилиндрами, размещенными по периферии под углом 120°. Это обеспечивает самостоятельное шагание полка по стволу без использования подъемных машин с канатами.
Гидропривод и пульт управления установлены на среднем ярусе. Полок оснащен звукосветовой сигнализацией, связанной с забоем и рабочим горизонтом горного комплекса на поверхности. К нижнему ярусу подвешено устройство для монтажа обделки.
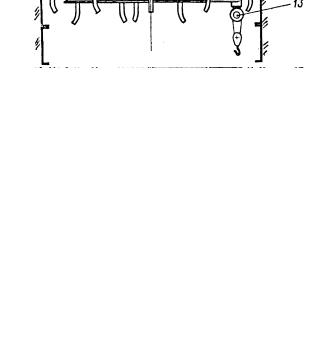
Рис. 2.24. Полок шагающий двухбадьевой:
1 — верхний ярус; 2 — «лыжа»; 3 — направляющая для бадьи; 4 — средний ярус; 5 — насосная станция; 6 — пульт управления;
7 — гидроцилиндр шагания; 8 — нижний ярус; 9 — монорельс кольцевой; 10 — пульт сигнализации; 11 — стопор; 12 — ляды; 13 — таль электрическая
Скорость проходки ствола в соответствии с заложенной в циклограмме составила 1,5 м/сут, а максимально достигнутая скорость — 2,4 м/сут, что говорит о резервах принятой технологии. Применение двухбадьевого и трехъярусного шагающего полка позволило сократить сроки сооружения ствола, а устройство в процессе проходки постоянной армировки — сэкономить время на монтаж по переоборудованию ствола для двухклетьевого подъема.
Полок шагающий проходческий типа ПШП-1 имеет наибольший размер по высоте — 10,37 м и массу — 10 т.
2.5.3. Возведение монолитной крепи ствола шагающим комплексом ЦНИИподземмаша
Сооружение неглубоких (до 15 м) шахтных стволов в метро- и тоннелестроении ведут в основном с помощью высокопроизводительных экскаваторов. При этом средние скорости проходки, как правило, не превышают 0,5–0,6 м в смену, что обусловлено в первую очередь отсутствием средств механизации для крепления стен.
В городском подземном строительстве в настоящее время применяют три основных вида крепи: деревометаллическую, сборную из железобетонных тюбингов и монолитную бетонную или железобетонную, возводимую, как правило, посредством наборной опалубки.
Преимущественный выбор вида крепи в строительных организациях часто обусловлен не технико-экономическим расчетом и требованиями эксплуатации ствола, а традиционной, отработанной технологией ведения работ. Причем надежная и экономичная монолитная крепь, хорошо зарекомендовавшая себя в шахтном строительстве, с помощью которой сооружают более 90 % стволов, не нашла здесь широкого применения из-за отсутствия необходимых средств механизации и опыта.
Все работы по устройству деревометаллической крепи стволов выполняют вручную. Частое применение дорогостоящей конструкции объясняют неоднократностью ее использования. Однако, как показывает опыт, даже в условиях малой обводненности окружающие породы плотно обжимают крепь, что исключает возможность ее изъятия для повторной эксплуатации. Кроме того, процесс извлечения не безопасен, поэтому крепь в
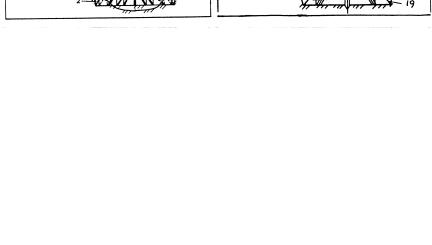
большинстве случаев вынуждены оставлять в грунте. В результате потери на 1 м ствола составляют 300–500 кг металлопроката и 0,7–1,4 м3 лесоматериалов [Метрострой. 1988. №
5.С. 5–6].
Сцелью совершенствования средств и способов крепления стволов ЦНИИподземмашем разработана документация на «Комплекс шагающий для возведения монолитной крепи стволов “КСБ-1”» (рис. 2.25, а). Он предназначен для механизированного сооружения монолитной бетонной крепи стволов диаметром 7 м в
свету (7,6 м в проходке) в грунтах естественной влажности с коэффициентом крепости ƒ ≤ 1,2 в условиях городской застройки.
Рис. 2.25. Шагающие комплексы ЦНИИподземмаша:
а — комплекс КСБ-1; б — комплекс КШБ-1; 1 — опалубка шагающая; 2 — нож-уплотнитель; 3 — оборудование для подачи бетона в ствол; 4 — гидрооборудование; 5 — насосная станция; 6 — экскаватор;
7 — гидродомкраты передвижки; 8 — шарниры; 9 — гидродомкрат горизонтального распора; 10 — то же вертикального; 11 — подъемная установка; 12 — оборудование для подачи бетонной смеси; 13 — рама горизонтального распора; 14 — стойки; 15 — центральная опора;
16 — кронштейны; 17 — погрузочная машина; 18 — шагающая опалубка
Трехсекционная облегченная опалубка рассчитана на возведение монолитной бетонной крепи заходками по 1 м по совмещенной схеме. Секции соединены между собой опорами жесткости и гидродомкратами отрыва опалубки от бетона крепи; на каждой из них расположены съемные поддоны и приварены кронштейны с шарнирами для крепления гидродомкратов перемещения. Нож-уплотнитель предназначен для разработки породной бермы по периметру ствола диаметром в проходке 7,6 м, оформления стенок ствола с одновременным их уплотнением и выполнения функций поддона опалубки. Нож состоит из шести сболченных секций с приваренными к ним кронштейнами для крепления гидродомкратов перемещения. Общая масса опалубки — около 6 т.
На поверхности устанавливают приемный бункер, а также насосную станцию, которую посредством гидрокоммуникаций связывают с гидродомкратами отрыва и перемещения опалубки.
Сооружение ствола с помощью комплекса КСБ-1 начинают с устройства воротника (устья). Для этого экскаватором отрывают котлован проектных размеров. Одновременно на поверхности собирают нож-уплотнитель и шагающую опалубку, оборудуют насосную станцию и гидрокоммуникации. После выравнивания дна котлована на него краном устанавливают и центрируют нож-уп-лотнитель, на который опускают опалубку, монтируют гидродомкраты и присоединяют гидрокоммуникации. Затем наружную поверхность ножа закрывают толем. Изолировав его таким образом от возможного последующего схватывания с бетоном, приступают к бетонированию нижней части воротника. Смесь подают за опалубку из подвешенной на кране бадьи или бетононасосом. После укладки на высоту ножа и опалубки бетон выдерживают в течение 4–5 ч.
Забетонировав воротник ствола, грейферным оборудованием осуществляют выемку грунта ядра забоя на глубину заходки. По периметру забоя оставляют породную берму шириной 200–400 мм (в зависимости от устойчивости пересекаемых пород), в которую
задавливают нож-уплотнитель, выдвигая штоки гидродомкратов перемещения, причем опалубка в это время удерживается на месте за счет распора в бетон крепи.
Благодаря конусности поверхности, нож, перемещаясь, срезает породу бермы с одновременным уплотнением грунта обнажаемых стен ствола. При этом увеличивается время устойчивости последних до 12 ч и более. Этого времени достаточно, чтобы переставить опалубку и уложить бетонную смесь.
После задавливания ножа с одновременным уплотнением грунта стен, опалубку отрывают от бетона, опускают гидродомкратами перемещения на нож, устанавливают в положение для бетонирования и осуществляют его. Продолжительность цикла — 7 ч. Комплекс обслуживает звено из трех человек.
Следует отметить, что в стволах незначительной глубины (до 15 м) выемку породы целесообразно производить с помощью экскаватора с грейферным рабочим органом (типа «Поклен»), а бетонную смесь подавать за опалубку насосом.
Таким образом, применение КСБ-1 позволяет: обеспечить комплексную механизацию основных операций крепления монолитным бетоном неглубоких стволов, сооружаемых в мягких породах; исключить необходимость применения в этих условиях временной деревометаллической крепи (с экономией до 458 кг металла и до 0,93 м3 лесоматериалов на каждый метр ствола), вдвое увеличить скорость проходки; благодаря шагающему с упором на забой принципу перемещения опалубки и ножа-уплот-нителя отказаться от канатной подвески; сократить вспомогательное оборудование и повысить безопасность ведения работ.
Техническая характеристика КСБ-1 |
|
|
Диаметр ствола в свету, м |
7 |
|
Диаметр ствола в проходке, м |
7,6 |
|
Коэффициент крепости по шкале М.М. Протодьяконова ƒ |
до 1,2 |
|
Вид крепи |
монолитный бетон, |
|
железобетон |
||
|
||
Способ перестановки опалубки |
шагающий |
|
с упором на забой |
||
|
||
Глубина заходки, м |
1 |
|
Расход бетона на 1 м ствола, м3/м |
6,9 |
|
Установленная мощность двигателя, кВт |
20 |
|
Производительность по креплению, м3/чел.-смен |
2,3 |
|
Техническая производительность комплекса, м/смен |
1 |
Комплекс предназначен для механизированного сооружения по совмещенной схеме неглубоких стволов (устьев) с крепью из монолитного бетона или железобетона.
Той же группой конструкторов разработан проект комплекса КШБ-1 — для сооружения стволов диаметром 5,5 м с монолитной бетонной крепью в мягких грунтах (рис. 2.25, б).
С помощью КШБ-1 можно проходить стволы глубиной до 40 м, при этом забой разрабатывается гидравлической с принудительным внедрением погрузочной машиной со сменным (ковш или грейфер) органом. После успешных испытаний КШБ-1 рекомендован к серийному производству. При работе звена, состоящего из двух проходчиков, скорость посадки может достигать 100 м в месяц [Метрострой. 1988. № 1. С. 7–8 ].
Комплекс КШБ-1 обеспечивает применение совмещенной схемы ведения работ. При этом основные операции выемки породы и возведения постоянной монолитной крепи выполняются последовательно. Схемы этапов сооружения ствола представлены на рис. 2.26.
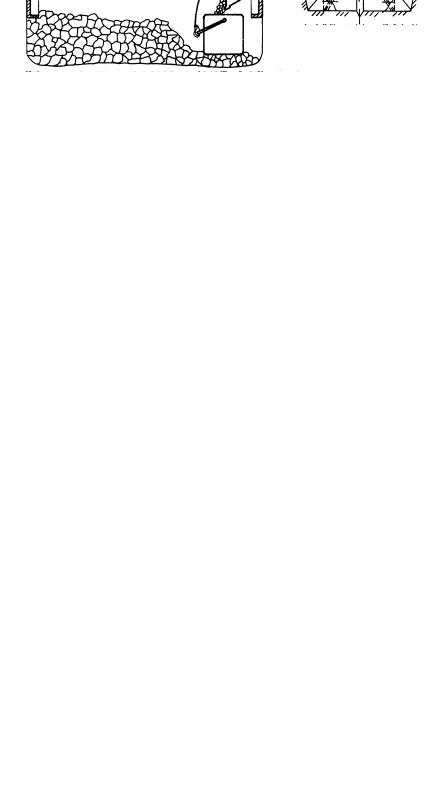
а) |
б) |
в) |
Рис. 2.26. Схемы этапов сооружения ствола проходческим комплексом КШБ-1
Цикл начинают с разработки грунта ядра на величину заходки (см. рис. 2.26, а), оставляя породную берму по периметру ствола. Ширина ее колеблется от 200 до 400 мм в зависимости от устойчивости пересекаемого массива. Затем задавливают нож-уплот- нитель, который при этом срезает и направляет к центру забоя породу бермы, одновременно оконтуривая и уплотняя стены ствола (см. рис. 2.26, б). Третья фаза (см. рис. 2.26, в) — отрыв опалубки от бетона крепи предыдущей заходки; снятие горизонтального распора рамы; перемещение на гидродомкратах шагания одновременно опалубки, рамы и центральной опоры с породопогрузочной машиной на следующую заходку; разжатие опалубки, распор рамы и бетонирование, после чего производят вертикальный распор комплекса и начинают выемку породы очередного цикла.
Выбор технологии и основных параметров оборудования комплекса КШБ-1 обусловлен горно-геологическими технико-эксплуатационными и экономическими требованиями.
По аналогии с комплексом КШБ-1 группой специалистов ЦНИИподземмаша была создана ковшовая гидравлическая погрузочная машина принудительного внедрения в грунт в комплексе с проходческим полком диаметром 7,9 м (рис. 2.27).
Рис. 2.27. Комплекс для сооружения выработок с горной крепью
Комплекс включает в себя: вертикальный подъем грунта 1, проходческий полок 2, механизм поворота 3, погрузочную машину 4, центральную трубу 5 со звездочкой 6, круговые фланцы 7, упорные подшипники 8, полую толстостенную цилиндрическую обойму 9, фланцы 10, подкосы 11.
|
Техническая характеристика комплекса |
Вместимость ковша, м3 |
0,25 |
Техническая производительность, м3 /ч |
до 20 |
Продолжительность рабочего цикла, с |
40 |
Тип привода |
гидравлический |
Напряжение в сети, В |
380 |
Масса машины без полка, кг |
3000 |
Количество проходчиков в звене, чел. |
2–3 |
Особенность породопогрузочной машины заключается в том, что она жестко крепится под проходческим полком и может быть использована в стволах диаметром от 6 до 8,5 м. На каждую последующую заходку машина опускается вместе с полком. Она способна разрабатывать и грузить породу без предварительного рыхления с f ≤ l,2, a более крепкие породы — после буровзрывных работ. Крепь ствола — чугунные тюбинги высотой 0,75–1,0 м.
Работа породопогрузочной машины в сочетании с полком осуществляется следующим образом.
После монтажа комплекса в забое производят бурение шпуров, их заряжение, взрывание и проветривание выработки. Затем полок с погрузочной машиной опускают к забою, раскрепляют его в крепь и начинают выемку породы по всему сечению. При этом погрузочная машина, жестко соединенная с центральной трубой, приводится в движение механизмом поворота, установленным на полке. Принцип поворотного механизма заимствован от экскаватора ЭО-2621. Для большей надежности центральная труба пропущена в толстостенную цилиндрическую обойму, снабженную круговыми фланцами, упорными подшипниками и подкосами.
После выемки породы комплекс с породопогрузочной машиной поднимается на безопасную высоту и производится цикл буровзрывных работ на следующую заходку.
Породопогрузочную машину впервые применили на одном из стволов Тимирязевского радиуса, который уже был в проходке.
Объем погруженной породы составил 678 м3, количество занятых проходчиков — 2 человека в смену вместо 9, продолжительность сооружения одного кольца — 1смена вместо 3 (до использования комплекса).
Испытания комплекса показали его достаточную надежность, удобство в эксплуатации, удовлетворительные технико-экономи-ческие показатели.
Для проводки глубоких вертикальных стволов впервые в мировой практике разработан комплекс шагающего оборудования КШО (рис. 2.28), позволяющий исключить применение лебедок для подвески проходческого полка, а при проходке стволов с параллельным армированием — лебедок для подвески забойной опалубки.

Рис. 2.28. Комплекс шагающего оборудования КШО
Комплекс состоит из шагающего полка, устройства для погрузки взорванной породы, забойной секционной опалубки, снабженной шаблонами для ее перемещения на шаг армировки, равной 4168 или 3125 мм, и коробами для формирования лунок под расстрелы армировки, а также из установки бурения шпуров.
Техническая характеристика
Диаметр ствола, обслуживаемого комплексом, м |
5–8 |
Скорость проходки ствола, м/мес. |
100 |
Проходческий шагающий полок: |
|
ход вертикального гидроцилиндра, мм |
4400 |
ход горизонтального гидроцилиндра, мм |
450 |
Устройство для погрузки породы: |
|
машинная производительность, м3/мин |
1,3 |
продолжительность цикла черпания, с |
30 |
средний расход сжатого воздуха, м3/мин |
50 |
емкость грейфера, м3 |
0,65 |
скорость подъема грейфера, м/с |
0,48 |
Установка для бурения шпуров: |
|
машинная производительность для пород крепостью f = 7–9, м/мин |
0,55 |
количество одновременно буримых шпуров, шт. |
3 |
диаметр колонки, мм |
42–55 |
ход автоподатчика, м |
4,5 |
Применение нового комплекса, имеющего по сравнению с существующим подвесным оборудованием целый ряд преимуществ, позволяет: исключить применение машины для разбуривания лунок в бетонной крепи, предназначенных для установки в них расстрелов постоянной армировки; сократить металлоемкость проходческого копра; снизить стоимость оборудования в 8–9 раз и эксплуатационные расходы на один метр ствола в 2–3 раза.
2.5.4. Применение шагающих комплексов ВПТИтрансстроя
Отделом инженерных сооружений ВПТИтрансстроя были предложены новые конструкции оборудования для проходки вертикальных стволов: комплексы шагающие с опиранием на забой КШС и КСУ в породах с крепостью f = 0,8–8 с обделкой из монолитного бетона или железобетона (табл. 2.6).
Таблица 2.6
Технические характеристики комплексов
|
Параметры |
КСУ |
КШС |
|
|
|
|
|
|
|
Диаметр ствола в свету, м |
7,0 |
8,5 |
|
|
Диаметр ствола в проходке, м |
8,0 |
9,5 |
|
|
Глубина ствола, м |
200 |
200 |
|
|
Толщина крепи, мм |
500 |
500 |
|
|
Погрузочная машина: |
|
|
|
|
вместимость ковша, м3 |
0,3 |
0,3 |
|
|
радиус копания, м |
4,2 |
4,8 |
|
|
цикл черпания, с |
20 |
20 |
|
|
Техническая производительность, м3/ч |
54 |
54 |
|
|
|
|
Окончание табл. 2.6 |
|
|
|
|
|
|
|
Параметры |
КСУ |
КШС |
|
|
|
|
|
|
|
Бурильная машина: |
|
|
|
|
диаметр шпура, мм |
32 |
32 |
|
|
частота вращения, м/мин |
2 |
2 |
|
|
скорость перемещения на забой, м/с |
0,1 |
0,1 |
|
|
Техническая производительность комплекса, м/мес. |
120 |
120 |
|
Комплексы могут работать по двум технологическим схемам: с выдачей породы на поверхность в транспортных сосудах и со спуском породы через пробуренную по центру ствола передовую скважину на подходящую горизонтальную или наклонную выработку.
Отличительной особенностью комплексов (рис. 2.29) является применение гидрофицированного забойного оборудования, позволяющего использовать АСУ операциями проходческого цикла, и его компактность — стволы можно проходить практически с нулевой отметки.
Проходческий цикл начинается с разработки и погрузки породы ядра забоя, оставляя по периметру ствола берму 100–200 мм в зависимости от устойчивости пород. Затем гидродомкратами перемещения задавливается режущий нож, который механическим путем срезает берму и одновременно оформляет стены ствола. После этого убирают распор полка рамы погрузочной машины и отрывают секции опалубки от бетона, включают пульт управления на слив масла, и весь комплекс забойного оборудования опускается на нож, опалубка центрируется и производится бетонирование следующей заходки. Затем цикл повторяется.
В крепких породах вначале осуществляется бурение, заряжание шпуров, подъем забойного оборудования на безопасную высоту, взрывание, проветривание, опускание забойного оборудования, распор полка и рамы погрузочной машины и только после этого — разработка и погрузка породы.
Одной из особенностей комплексов является шагающий принцип перемещения забойного оборудования с одновременным опусканием опалубки, проходческого полка и бурильной машины.
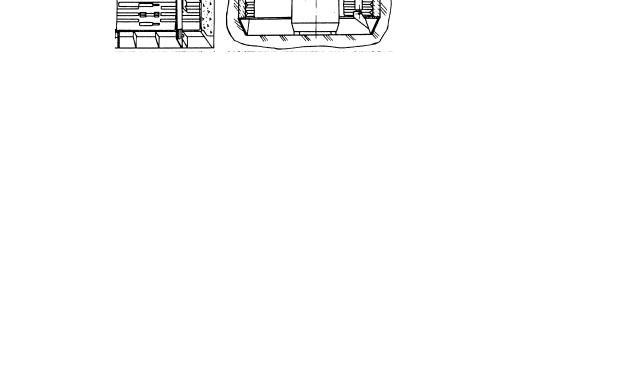
а) |
б) |
Рис. 2.29. Шагающие комплексы ВПТИтрансстроя:
а— комплекс КШС; б — комплекс для стволов диаметром 3–5 м
сшагающей опалубкой
Применение этих комплексов позволяет повысить производительность труда в 3–4 раза за счет механизации разработки и погрузки породы, исключения ручной доработки и оформления стенок ствола, совмещения указанных выше операций. Количество занятых рабочих уменьшается на 30– 50 %, в зависимости от диаметра ствола.
Следующий шаг в совершенствовании стволопроходческой техники — создаваемое институтом «ВПТИтрансстрой» модульное мобильное оборудование. Оно обеспечивает проходку стволов в различных горно-геологических условиях, в частности в водонасыщенных безнапорных породах, и его можно комплектовать в различных вариантах в соответствии с конкретными условиями сооружения стволов.
Комплексным проектно-конструкторским отделом МПСО «Союзтоннельстрой» на основе принципов действия КШБ-1 разработана и внедрена опалубка шагающая ОШ-3, предназначенная для возведения крепи из монолитного бетона (железобетона) при строительстве вертикальных подземных сооружений небольшой глубины.
Интересная конструктивная разработка шагающей опалубки была предложена Криворожским филиалом ВНИИОМШСа. Опалубка секционного типа, разработанная для восьми диаметров стволов от 4,5 до 8,0 м, состоит из двух основных узлов, соединенных между собой демпферными устройствами: собственно опалубки 1 и несущего кольца 2. Несущее кольцо и опалубка перемещаются в стволе поочередно (рис. 2.30).
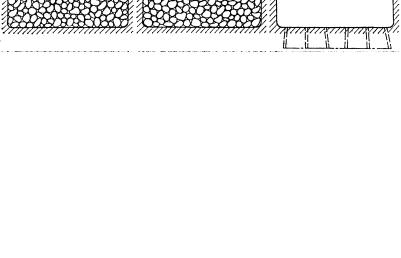
а) |
б) |
в) |
Рис. 2.30. Этапы перемещения шагающей секционной опалубки:
а— исходное положение; б — перемещение опалубки на новую заходку
ибетонирование обделки; в — опускание несущего кольца и закрепление
его в лунках на новой заходке
При перемещении опалубки на следующую заходку несущее кольцо занимает соответствующее положение в предыдущей заходке и с помощью ригелей 4, передвигаемых пневмоцилиндрами 3 удерживается в лунках бетонной крепи, образуемых при помощи шарнирных выступов на наружной стороне опалубки. Спуск опалубки и несущего кольца производится с помощью демпферного устройства (пневмоталей 5). Управление шагающей опалубкой — дистанционное. После опускания опалубки на взорванную породу забоя она центрируется и раскрепляется в породу, устанавливаются шарнирные выступы и производится бетонирование. Перед заряжанием и взрыванием зарядов, ригели, поддерживающие опорное кольцо, выдвигаются из лунок, и кольцо опускается под собственным весом. Затем ригель вновь задвигается в лунки и раскрепляет кольцо. Во время опускания опорного кольца опалубка удерживается на крепи ствола силами сцепления ее с бетоном, а также шарнирными выступами, входящими в лунки [43].
Применение проходческого оборудования, оснащенного механизмами шагания, позволяет отказаться от использования проходческих лебедок для его подвески, что значительно упрощает и снижает стоимость оснащения ствола.
Испытание и внедрение технологий и комплексов нового поколения подтвердили перспективность создания облегченных шагающих агрегатов для проходки стволов с максимальным отделением забойного оборудования от поверхности, обеспечивающих комплексную механизацию основных строительных операций.
Упомянутые образцы, несомненно требующие дальнейшего совершенствования, обладают рядом преимуществ по сравнению с традиционными, в частности, способствуют значительному росту месячных скоростей сооружения стволов (до 30–40 %). Однако широкое внедрение в практику метростроения этого сравнительно несложного в изготовлении оборудования сдерживается отсутствием реальных производственных мощностей для его серийного выпуска.
2.6. Современные технологические схемы сооружения шахтных стволов
2.6.1. Совмещенная и параллельно-щитовая схемы проходки шахтных стволов
В отечественной практике вертикальные шахтные стволы в основном проходят буровзрывным способом по совмещенной технологической схеме, при которой опалубку для возведения бетонной крепи устанавливают на взорванную породу, что исключает необходимость временной крепи, поддона у опалубки и уплотнения зазора между поддоном и породной стенкой ствола.
Изредка осуществляется скоростная проходка стволов по параллельно-щитовой проходческой схеме, при которой бетонную крепь возводят с проходческого полка. Защита проходчиков в забое осуществляется по этой схеме щитом-оболочкой, подвешенным к полку, или к лебедкам на поверхности и опускаемым по мере проходки ствола.