
книги / Проблемы науки о материалах и развитие высоких технологий в России
..pdfв матричный гамма-твердый раствор, и упрочняющих интерметаллидных, карбидных и боридных фаз,
В сплавы, предназначенные для работы при сравнительно невысоких температурах (750...850 °С) длительное время, вводят повышенное количество хрома (до 16... 18 %), молибдена и вольфрама (до 10…12 % суммарно), титана, ниобия и алюминия (до 8...10 % суммарно). Это дает возможность получить большое количество упрочняющей фазы, высокую легированность и жаропрочность матрицы.
Для высокотемпературной (975...1050 °С) работы в сплавах ограничивают содержание хрома (6... 10 %), молибдена (3...4 %) и титана. Введение дополнительно кобальта и вольфрама несколько повышает температуру солидуса.
При работе в средах повышенной агрессивности (например, содержащих соли, соединения ванадия и др.) важнейшим элементом, обеспечивающим коррозионную стойкость, считается хром.
Положительное влияние на жаростойкость никелевых сплавов оказывают РЗМ. Это влияние связывают с затруднением образования оксисульфидов. Иттрий и гафний улучшают адгезию окалины к металлу.
Никелевые жаропрочные сплавы являются сложными многокомпонентными и многофазными системами, в которых под действием высоких температур и напряжений непрерывно протекают фазовые и структурные превращения, т.е. с физикохимических позиций эти сплавы являются динамическими системами.
Никелевые сплавы подразделяют на деформируемые и литые. Принципы легирования и упрочнения этих сплавов одинаковы, но при создании деформируемых сплавов необходимо обеспечить сплавам достаточную технологическую пластичность при обработке давлением, в том числе при температурах 700...800 °С, а литые сплавы должны иметь удовлетворительные литейные свойства (жидкотекучесть, пористость). В связи
41
с этим в литейных сплавах допускается более высокое содержание углерода, бора и требуется более строгий контроль по количеству легкоплавких примесей.
Литые сплавы, обладающие высоким сопротивлением ползучести, имеющие большую объемную долю гамма'-фазы и добавки тугоплавких элементов, используют для наиболее высоконагруженных и высокотемпературных деталей турбин, например для лопаток. Для более крупных и сложных по геометрии деталей турбин, которые нельзя изготовить отливкой на нужный размер, а необходимо обрабатывать ковкой или прокаткой, например диски, используют деформируемые сплавы с меньшим содержанием гамма'-фазы и меньшей прочностью. Деформируемые сплавы всегда используются при более низких температурах, чем литые.
С ростом температур эксплуатации значение межзеренного разрушения жаропрочных сплавов возрастает. Применение сплавов, полученных направленной кристаллизацией (НК), позволяет резко уменьшить роль границ зерен в разрушении, так как после направленной кристаллизации границы зерен располагаются в основном параллельно приложенному усилию, а границы, перпендикулярные направлению деформации, отсутствуют. Еще более высокие характеристики жаропрочности показывают сплавы, имеющие монокристаллическую структуру, т.е. когда деталь выращивается из одного центра кристаллизации (затравки) и не имеет большеугловых границ зерен.
Монокристаллическая структура сложнолегированных жаропрочных сплавов не соответствует представлениям о монокристаллах чистых металлов, имеющих одну кристаллическую решетку. В жаропрочных сплавах, закристаллизованных из одного центра, имеются различные фазы: гамма-фаза, карбиды, гамма'-фаза и, следовательно, межфазные границы. Однако в них отсутствуют границы зерен, что сильно повышает жаропрочность.
42
Получение сплава НК или с монокристаллической структурой заключается в проведении контролируемой кристаллизации из жидкого состояния, когда поверхность раздела между расплавом и твердой фазой поддерживается плоской и перпендикулярной к желательному направлению кристаллизации. Это возможно, когда по всему сечению детали тепловой поток распространяется параллельно направлению роста.
Таким образом, в настоящее время применяют жаропрочные сплавы, полученные равноосной кристаллизацией, направленной кристаллизацией и с монокристаллической структурой.
Отметим, что последние два технологических процесса значительно повышают стоимость деталей; их применяют только в особо ответственных случаях.
Поскольку детали из жаропрочных сплавов на никелевой основе часто используются с защитными покрытиями (например алитирование, хромалитирование и др.), следует учитывать возможные изменения структуры и свойств сплавов при технологических нагревах и охлаждениях в процессе их нанесения.
Сплавы на основе кобальта
Жаропрочные сплавы на основе кобальта имеют более низкие характеристики жаропрочности по сравнению со сплавами на основе никеля. Уровень жаропрочности кобальтовых сплавов связан с упрочнением твердого раствора при легировании и с выделением упрочняющих фаз.
Кобальтовые сплавы вследствие специфики механизма упрочнения содержат повышенное количество углерода, обычно от 0,25 до 1 % С.
Преимуществом сплавов на основе кобальта является их хорошая коррозионная стойкость при повышенных температурах, например в продуктах сгорания топлива, содержащего серу, они характеризуются высокой стабильностью структуры при длительных сроках службы под нагружением и, следова-
43
тельно, имеют более пологий ход кривых зависимости прочностных свойств от температуры и времени выдержки. Кобальтовые сплавы имеют более высокую теплопроводность и меньший коэффициент термического расширения, чем никелевые жаропрочные сплавы. Поэтому кобальтовые сплавы более подходят для изготовления деталей, предназначенных для длительной работы в коррозионной среде, в условиях термической усталости и имеющих сравнительно крупные размеры (например, сопловые и рабочие лопатки мощных газовых турбин).
В кобальтовых сплавах могут образовываться следующие фазы: аустенитная гамма-матрица с ГЦК-структурой, карбиды, бориды, карбонитриды и ТПУ-фазы (топологически плотноупакованные фазы). Интерметаллидная гамма'-фаза в них не выделяется. При тщательном контроле состава образования ТПУ-фаз, оказывающих отрицательное влияние на жаропрочность и пластичность, можно избежать, следовательно, жаропрочные кобальтовые сплавы будут состоять из гамматвердого раствора и упрочняющих карбидных и карбонитридных фаз.
Кобальт образует неограниченные растворы с никелем, железом и благородными металлами и ограниченные растворы с широкой областью гомогенности – с марганцем, тугоплавкими металлами.
Высокую растворимость имеют также бор (до 1 % при
1000 °С) и углерод (0,3…0,4 % при 1100 °С).
Благородные металлы дорого стоят и дефицитны; марганец и железо отрицательно влияют на жаропрочность и жаростойкость сплавов на основе кобальта, и легирование этими элементами не применяется. Поэтому основным из элементов, стабилизирующим ГЦК-структуру, в сплавах кобальта является никель. Содержание никеля в жаропрочных кобальтовых сплавах обычно составляет 10...30 %. Важное значение в этих сплавах имеет хром, который обеспечивает высокую коррозионную стойкость и положительно влияет на их жаропрочность.
44
Содержание хрома в деформируемых сплавах обычно составляет 18...20 %, а в литых сплавах 23...28 %, что значительно выше, чем допустимо в сплавах на никелевой основе.
Порошковые жаропрочные никелевые сплавы
При изготовлении крупногабаритных деталей газотурбинных двигателей (ГТД) из литых заготовок возникают трудности, связанные с разбросом механических свойств по объему детали, что связано с ликвационными неоднородностями в заготовке. Проблема решается при использовании в технологиях ГТД порошковой (гранульной) металлургии. Развитие гранульной технологии связано с применением жидкофазного спекания в процессе компактирования гранул. Жидкофазное спекание гранул не является конечной операцией в технологии, поскольку полное уплотнение детали ею не обеспечивается. Для доуплотнения заготовок в этом случае может применяться горячее изостатическое прессование (ГИП) без капсулы. В процессе такого технологического передела важно проследить за структурными изменениями, реализующимися в сплаве. К порошковым жаропрочным сплавам относятся:
ЭП741НП, ЭП741П, ЭП975, ЭП962П, ВЖ136.
Наиболее распространенным является сплав ЭП741НП, из которого изготавливают диски и валы ГТД.
В результате многоступенчатого анализа было установлено следующее:
1.Различия в распределении никеля, хрома, молибдена, вольфрама, кобальта, титана по диаметру частиц фракций < 20
и< 120 мкм в сплавах не обнаружены, т.е. они однородны по химическому составу.
2.Точечный анализ междендритных областей показал увеличение концентрации титана, алюминия, никеля, но расстояние между этой фазой и осью дендрита меньше размеров области возбуждения рентгеновского излучения, поэтому коли-
45
чественный анализ междендритного пространства не проводили.
Гранулы сплава ЭП741НП, имеющие наиболее широкое применение в промышленности, исследованы более детально. Количественный анализ средних концентраций по основным заданным элементам показал содержание никеля до 63 %; кобальта – 16 %; титана – 2 %; хрома – 10 %; молибдена – 3 %; вольфрама – 7 %; алюминия – 6 %; у поверхности гранул, как
вмелкой, так и в крупной фракции, зафиксировано повышенное содержание алюминия, что связано с наличием на поверхности гранулы оксида алюминия.
Компактирование гранульного сплава проводили следующим образом: гранулы фракции < 200 мкм на воздухе помещали в открытую форму, изготовленную из оксида алюминия, далее, минуя операцию утряски, загружали в вакуумную печь. Спекание образцов велось при остаточном давлении 0,0133 Па,
вприсутствии жидкой фазы, после чего их относительная плотность достигала 91…94 %. Для увеличения относительной плотности образцы подвергали ГИП по стандартной технологии с дальнейшей термической обработкой.
Структура гранульных сплавов, обработанных методом ГИП при 1200 °С, аналогична структуре сплавов, спеченных
вприсутствии жидкой фазы. Распределение легирующих элементов по структуре образцов из ЭП741НП определялось при помощи микрорентгеноспектрального анализа.
Вструктуре спеченного сплава ЭП74ШП элементы распределяются равномерно, за исключением небольших колебаний концентрации вольфрама. На границах зерен наблюдается повышение содержания никеля, титана, гафния, ниобия, алюминия, что подтверждает полученные ранее результаты. Количество хрома, кобальта, вольфрама и молибдена меньше, чем
взерне. Кроме того, на границах зерен после спекания обнаружены карбиды с повышенным содержанием ниобия, гафния и титана, в основном 40...50 % ниобия.
46
После спекания и ГИП в зерне наблюдаются равномерные колебания содержания никеля, что, по-видимому, связано с выделением упрочняющей гамма-фазы, поскольку ГИП является разновидностью ТО. Отмечены пики по ниобию и гафнию (карбиды в зерне).
На границах зерен после спекания и ГИП зафиксировано повышенное содержание никеля, титана, алюминия, гафния, ниобия, пониженное – хрома, кобальта, вольфрама, молибдена, По ходу ТО протекают процессы рекристаллизации и модифицирования структуры. Происходит выделение упрочняющей гамма-фазы, имеющей размер 0,5…0,85 мкм и равномерно распределенной по образцу, что соответствует содержанию ме-
таллов на границах зерен после спекания.
После ТО в зерне наблюдаются заметные колебания содержаний никеля, алюминия и незначительные – титана и вольфрама. Это связано с выделением и модифицированием гамма-фазы. На границах зерен находятся карбиды ниобия, гафния и титана.
Исследования показали, что после ГИП относительная плотность образцов, спеченных в жидкой фазе, не достигла 100 %, поэтому при получении заготовок, годных для дальнейшей обработки, необходимо применять способы деформации в изотермических условиях (штамповка, раскатка).
2.3.Тугоплавкие металлы и сплавы
Ктугоплавким принято относить металлы с температурой плавления выше 1539 °С. В Периодической системе Менделеева (рис. 9) они расположены в IV–VIII группах (подруппы А).
Физические свойства. Тугоплавкие металлы обладают особыми физико-химическими и механическими свойствами, существенно отличающими их от других металлов (табл. 4).
Тугоплавкие металлы характеризуются высокой прочностью межатомных связей, определяющих их кристаллическую
47
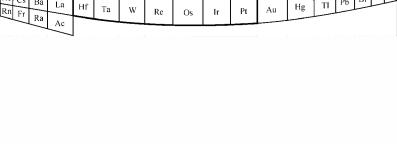
структуру и свойства: высокую температуру плавления, повышенную механическую прочность, значительное электросопротивление.
Рис. 9. Расположение тугоплавких металлов в Периодической системе Менделеева
Из тугоплавких металлов наиболее легкими являются титан (γ = 4,541 г/см3), ванадий (γ = 6,11 г/см3), цирконий (γ = 6,489 г/см3) и хром (γ = 7,19 г/см3). Остальные тугоплавкие металлы плотностью γ > 8,10 г/см3 относятся к тяжелым и сверхтяжелым. Наибольшая плотность у осмия (γ = 22,5 г/см3), платины, иридия, рения и вольфрама (γ = 19,3 г/см3). Вследствие низкого температурного коэффициента линейного расширения молибдена и вольфрама и высокой температуры плавления обеспечивается надежная работа конструкций из этих металлов, эксплуатируемых при высоких температурах. Высокое электросопротивление тугоплавких металлов обусловлено особенностями их электронной структуры – возникновением дополнительного рассеивания электронов за счет d- и s-перехо- дов. Электропроводность вольфрама и молибдена почти в три раза меньше электропроводности меди, но больше, чем железа, никеля и платины. Температура, давление и другие параметры весьма существенно влияют на электросопротивление тугоплавких металлов. обеспечивается надежная работа конструкций из этих металлов, эксплуатируемых при высоких температурах. Высокое электросопротивление тугоплавких металлов
48
Таблица 4
Физические и механические свойства технически чистых тугоплавких металлов IVА, VА, VIА групп Периодической системы Менделеева
|
Свойства |
W |
Re |
Ta |
Mo |
Nb |
Hf |
V |
Cr |
Zr |
Ti |
|
|
Кристаллическая |
|
|
|
|
|
|
|
|
|
|
|
|
решетка (20 °С): |
|
|
|
|
|
|
|
|
|
|
|
|
тип |
ОЦК |
ГПУ |
ОЦК |
ОЦК |
ОЦК |
ГПУ |
ОЦК |
ОЦК |
ГПУ |
ГПУ |
|
|
параметр |
416,48 |
277 |
322,96 |
314,66 |
329,6 |
350 |
303,33 |
288,50 |
361 |
331,32 |
|
|
Удельная тепло- |
|
|
|
|
|
|
|
|
|
|
|
|
емкость c, при |
135,34 |
153 |
142 |
250 |
269 |
147 |
502 |
462 |
275 |
523 |
|
49 |
20 °С, Дж/(кг·К) |
|
|
|
|
|
|
|
|
|
|
|
Теплопровод- |
167 |
71,4 |
54,5 |
147 |
52,5 |
2,23 |
3,1 |
6,7 |
16,7 |
17,2 |
||
|
||||||||||||
|
ность λ, Вт/(м · К) |
|||||||||||
|
Давление пара |
1,33 |
0,157 |
0,665 |
1,995·10–3 |
0,133 |
|
13,3 |
|
|
|
|
|
металла над чис- |
(при |
(при |
(при |
(при |
(при |
– |
(при |
– |
– |
– |
|
|
тым металлом |
|||||||||||
|
3036 °С) |
2220 °С) |
2996 °С) |
2127 °С) |
2262 °С) |
|
727 °С) |
|
|
|
||
|
pпара, Па |
|
|
|
|
|||||||
|
|
|
|
|
|
|
|
|
|
|
||
|
Скорость испаре- |
1,47 |
|
1,16·10–3 |
0,282 |
1,63 |
|
|
|
|
|
|
|
ния металла с по- |
(при |
– |
(при |
(при |
(при |
– |
– |
– |
– |
– |
|
|
верхности νиспар, |
3036 °С) |
|
2194 °С) |
1827 °С) |
1727 °С) |
|
|
|
|
|
|
|
г/(м2·с) |
|
|
|
|
|
|
|||||
|
Удельное сопро- |
|
|
|
|
|
|
|
|
|
|
|
|
тивление ρ (при |
55 |
198 |
124–136 |
57,7 |
130–150 |
327–439 |
248 |
130–140 |
397–440 |
421–478 |
|
|
20 °С), кОм·м |
|
|
|
|
|
|
|
|
|
|
49
Окончание табл. 4
|
Свойства |
W |
Re |
Ta |
Mo |
Nb |
Hf |
V |
Cr |
Zr |
Ti |
|
Температурный |
|
|
|
|
|
|
|
|
|
|
|
коэффициент со- |
|
|
|
|
|
|
|
|
|
|
|
противления α |
4,45 |
4,67 |
6,5 |
5,44 |
7,1 |
6,05 |
8,3 |
6,2 |
5,8 |
8,4 |
|
(при температуре |
|
|
|
|
|
|
|
|
|
|
|
0÷100 °С), 10–6/°С |
|
|
|
|
|
|
|
|
|
|
|
Работа выхода |
|
|
|
|
|
|
|
|
|
|
|
электрона Авыхэл , |
4,51 |
4,8 |
4,1 |
4,29 |
4,0 |
3,53 |
4,13 |
4,5 |
4,16 |
3,95 |
|
эВ |
|
|
|
|
|
|
|
|
|
|
|
Предел прочно- |
784–981 |
804,42 |
372,78 |
784,8– |
392,4– |
392,4– |
343,4– |
490,5 |
245,3– |
294,3– |
50 |
сти σв (при 20 °С), |
|
|
|
882,9 |
588,6 |
590 |
392,4 |
|
343,4 |
588,6 |
МПа |
|
|
|
|
|
|
|
|
|
|
|
|
|
|
|
|
|
|
|
|
|
|
|
|
Относительное |
|
|
|
|
|
|
|
|
|
|
|
удлинение δ (при |
0 |
32 |
70 |
10–15 |
50 |
40 |
25 |
0 |
35–40 |
40–72 |
|
20 °С), % |
|
|
|
|
|
|
|
|
|
|
|
Твердость по |
|
|
|
|
|
|
|
|
|
|
|
Бринеллю НВ |
280–360 |
100–135 |
125 |
150–220 |
70–80 |
160–180 |
80 |
90–150 |
70 |
60 |
|
(при 20 °С) |
|
|
|
|
|
|
|
|
|
|
|
Плотность γ, г/см3 |
19,3 |
21,0 |
16,6 |
10,22 |
8,57 |
13,1 |
6,11 |
7,19 |
6,489 |
4,541 |
|
Тχ, °С |
200–400 |
–196 |
–196 |
0–200 |
–196 |
– |
– |
–60 |
–110 |
–196 |
|
Температура |
3380 |
3180 |
2996 |
2620 |
2500 |
2220 |
1919 |
1875 |
1850 |
1668 |
|
плавления, °С |
||||||||||
|
|
|
|
|
|
|
|
|
|
|
|
|
Температура ки- |
6000 |
5900 |
5300 |
4800 |
3300 |
5400 |
3400 |
2430 |
3600 |
3500 |
|
пения, °С |
|
|
|
|
|
|
|
|
|
|
50