
книги / Оксидные композиционные материалы
..pdfВесьма показательны проведенные в работах [20–23] исследования по изучению длительного воздействия высоких температур на структурные изменения корундовой керамики. Материалы из оксида алюминия при длительных изотермических выдержках до 2000 ч в интервале температур 1300–1600 °С претерпевают структурные изменения, которые выражаются в ориентированной собирательной рекристаллизации.
Плотные материалы подвержены более интенсивному старению, под воздействием которого их прочность уменьшается в 2–4 раза. После термической обработки при 1300 °С в течение 2000 ч прочность при изгибе корундовой керамики с добавкой 0,2–0,3 мас.% МgО снижается от 475 до 175 МПа [22]. В наименьшей степени (на 10–15 %) снижается прочность при старении корундовой керамики с крупнозернистым наполнителем со связкой из дисперсного электрокорунда или глинозема, величина которой изменяется от 170 до 158 МПа [20].
Установлено, что в процессе термического старения скорость ползучести керамики из чистого А12О3 снижается в меньшей степени, чем у оксида алюминия, содержащего МgО [24].
Для корундовой керамики, подвергнутой старению, установлено явление закалки при термоударе [17]. Прочность образцов с размером кристаллов 70–100 мкм после термоудара повышалась на 10–15 %.
В работе [19] исследовано изменение электропроводности от термического старения. Установлено, что в области примесной проводимости электропроводность керамики уменьшается с увеличением размеров кристаллов. В области собственной проводимости величина электропроводности от размера кристаллов не зависит. Эффект влияния термического старения на величину электропроводности керамики в примесной области можно объяснить удлинением пути носителей тока внутри кристалла с увеличением его размера, а также изменением состояния и площади границ кристаллов в результате диффузии к ним примесей при длительном нагреве.
Спеченный корунд является хорошим изолятором. Так, его удельное объемное сопротивление при комнатной температуре составляет 1014–1016 Ом·см. С повышением температуры до
11
1000 °С удельное объемное сопротивление снижается до
106–107 Ом·см [16, 19].
Диэлектрическая проницаемость корунда равна 12. Угол диэлектрических потерь при радиочастотах для 20 °С составляет 0,15–1,5 мин, для 100 °С – 1–2 мин. Средняя пробивная напряженность спеченного оксида алюминия равна 150–200 кВ/см [18].
Корундовые материалы отличаются химической стойкостью. При обычной температуре на них не действует ни один химический реагент, а при высоких температурах это действие проявляется незначительно.
Сера, фосфор, мышьяк, их соединения и сплавы при температурах выше 1000 °С не оказывают значительного влияния на корундовую керамику.
Корунд отличается высокой стойкостью к действию восстановителей (углерод, окись углерода, углеводороды, водород и свободные металлы) при температурах до 1800 °С. Например, контакт корундового покрытия с вольфрамовой проволокой, накаленной до 1800 °С, в течение сотен часов не приводит к восстановлению оксида алюминия.
Корунд обладает химической стойкостью по отношению к шлакам, стеклу, расплавленным солям, щелочам и кислотам.
Таким образом, неисчерпаемые ресурсы исходного сырья в природе, высокие рабочие температуры, прочность, немагнитность, коррозионная и эрозионная стойкость, электроизоляционные свойства позволяют считать технологически оправданным использование оксида алюминия в качестве исходного материала для получения керамики с высокими термомеханическими и теплофизическими свойствами.
Контрольные вопросы
1.Какое исходное сырье используется для получения корундовой керамики?
2.В чем заключается метод получения технического глинозема?
3.В чем заключается метод получения электрокорунда?
4.В каких кристаллических модификациях существует безводная форма оксида алюминия?
12

5. Чем отличаются свойства различных кристаллических форм А12О3?
6.Какими физико-химическими свойствами и параметрами кристаллической структуры характеризуются модификации оксида алюминия?
7.Какие прочностные свойства имеет корундовая ке-
рамика?
8.Как влияет температура на физические свойства корундовой керамики?
9.Какие структурные изменения корундовой керамики происходят при воздействии высоких температур?
10.Какими наиболее востребованными эксплуатационными характеристиками обладают изделия из корундовой керамики?
2.ИССЛЕДОВАНИЕ МЕХАНИЗМА ДРОБЛЕНИЯ ПОРОШКА ОКСИДА АЛЮМИНИЯ*
2.1.Исследование закономерностей дробления
Вкачестве исходного материала использовали оксид алю-
миния марки ч.д.а. МРТУ-6-09-2046–64 со средним размером частиц 10 мкм, с удельной поверхностью 0,0975 м2/г, который
подвергали отжигу при температуре 1400 °С в течение 2 ч для перевода γ-модификации А12О3 в α-фазу А12О3. Затем порошок измельчали в дезинтеграторной установке IA12.
Использование улучшенных методов обработки и производства сверхтонких порошков позволяет получать высокую химическую однородность и дисперсность компонентов, снизить температуру и стабилизировать рост зерна в процессе спекания. С точки зрения этих преимуществ исследованы методы механического активирования и химического синтеза ультрадисперсных порошков.
Закономерности дробления грубодисперсных порошков описывают эмпирическими законами Кирпичева–Кика. В тонкодисперсных системах при дроблении существенное влияние
* Исследования выполнены при поддержке гранта РФФИ 06-08-00879а.
13
оказывает агрегатирование частиц порошка, которое учитывают введением предельного размера частиц.
На первом этапе исследованы методы механического активирования ультрадисперсных порошков в дезинтеграторе и шаровой мельнице. Изучен процесс дробления А12О3, основанный на оценке механизма конгломерации и дефектности кристаллической структуры. Методика определения закона дробления разработана на основании изучения изменения гранулометрического состава порошка в процессе дробления.
Установлено, что фактором, определяющим интенсивность дробления (при фиксированных внешних условиях), является дефектность кристаллической структуры частиц, а мерой агрегирования – удельная (на единицу массы) поверхностная энергия.
Если средний размер порошинок достаточно велик, то, вследствие их большой массы, инерционные силы превосходят силы молекулярного сцепления, и процесс дробления не будет зависеть от размеров частиц. В этом случае распределение частиц по размерам будет логарифмически нормальным. Это имеет место, например, при дроблении горных пород [26]. Однако для дисперсных систем нет оснований считать распределение частиц логнормальным и теоретический анализ дробления необходимо проводить с учетом двух факторов: концентратора напряжений, процесса агломерации.
Наибольший практический интерес представляет предельное распределение частиц после больших времен дробления. Разрушение некоторой выделенной частицы в процессе дробления можно представить зависимостью
Хk+1 = Хk + εkg(Хk), |
(1) |
где Хk = Х(tk), εk = ε(tk); X – размер частицы; t – время; ε – дисперсия; k – номер частицы; функция g(Х) может быть поло-
жительной или отрицательной; ε(t) > 0 – случайная функция времени.
При больших временах размола между дроблением и конгломерацией устанавливается равновесие, которое в дальнейшем во времени не изменяется. Выберем новое начало отсчета времени от момента установления равновесного распределения
14
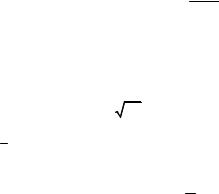
и обозначим новое время t′. Теперь набор Хk = Х(t′k) можно рассматривать не только как последовательность изменений размеров выделенной частицы, но и как набор размеров частиц в некоторый фиксированный момент времени t′ ≥ 0, поскольку состояние совокупности порошинок во времени не меняется. Из выражения (1) следует:
N |
Х |
k +1 |
− X |
k |
N |
|
∑ |
|
|
= ∑εk . |
(2) |
||
|
g(X k ) |
|
||||
k =1 |
|
|
k =1 |
|
В силу однотипности изменения размеров каждой частицы во времени при t′ ≥ 0 среднее значение и дисперсия εk не зависят от номера частицы k. Следовательно, правая часть равенства (2) при N→∞, т.е. при увеличении количества измельчаемого порошка, согласно центральной предельной теореме в формулировке Леви–Лендеберга, имеет нормальный закон распределения. В левой части равенства (2) при N→∞ функция
= x dx G(X ) ∫0 g(x)
также имеет нормальное распределение. Тогда ее функция плотности вероятности
|
|
|
|
|
|
2 |
|
|
|
1 |
AG(X ) −GU |
|
|||||
f(X) = |
|
exp − |
|
|
|
|
|
, |
σ 2π |
2σ2 |
|
||||||
|
|
|
|
|
||||
|
|
|
|
|
|
|
|
|
∞
где G = ∫G(X ) f (X )dx ,
0
σ2 = ∞∫(AG (X )−GU 2 )f (X )dx .
0
(3)
(4)
Предположим, что конгломерируются все частицы размера х ≤ а. Тогда при х < а g(х) > 0, а при х > а g(х) < 0. При дроблении хрупких материалов обычно считают, что в присутствии конгломерации g(х) = kх (закон Кирпичева–Кика) выполняются следующие требования: во-первых, g(а) = 0; во-вторых, чтобы
15
правильно учесть интенсивность процессов конгломерирования с уменьшением размера частиц, эта добавка должна быть возрастающей функцией при уменьшении х.
Целью экспериментальных исследований являлось определение параметров k, а и установление закона дробления частиц порошка А12О3 из условия совпадения экспериментально измеренной и теоретической функций распределения частиц по размерам, а также проверка закона распределения. Сравнение экспериментальной и теоретической функций распределения осуществляли по критерию nω2.
Разработанная модель дробления позволила определить размер, начиная с которого происходит процесс конгломерации и падает интенсивность процесса дробления k. Исходя из предположения, что конгломерируются частицы размера Х < а, получен закон дробления:
А(Х) = – K Х(1 – а/Х), |
(5) |
в котором учтен процесс агрегатирования (третий сомножитель).
Установлено, что частицы порошка А12О3 разрушаются по механизму Кирпичева–Кика и конгломерируются при Х ≤ а
(а ~ 0,4 мкм).
Показано, что активирование порошков А12О3 при измельчении связано, главным образом, с уменьшением размера частиц и увеличением удельной поверхности за счет нарушения атомной структуры твердого тела.
Установлена связь между способами механического активирования и размером частиц. Показано, что дезинтеграторный метод измельчения, по сравнению с измельчением в шаровой мельнице, является наиболее эффективным способом механической обработки для получения высокодисперсных порошков хрупких материалов.
С учетом установленных закономерностей проведены исследования по определению оптимальных режимов получения высокодисперсных порошков А12O3 с размером частиц 0,1–0,3 мкм и удельной поверхностью 10–25 м2/г.
16
PNRPU
2.2. Исследование кристаллической структуры порошка оксида алюминия
В процессе измельчения происходит уменьшение размера частиц и увеличение свободной поверхности за счет нарушения атомной структуры твердого тела. Вместе с тем, при механическом активировании аккумулируется механическая энергия в виде неравновесной концентрации дефектов кристаллической решетки.
Особенности тонкой кристаллической структуры измельченного порошка А12O3 изучали путем анализа зависимости физического уширения рентгеновских дифракционных линий.
|
В табл. 4 приведены значения ширины дифракционных пи- |
ков |
в зависимости от времени измельчения порошка А12O3 |
в шаровой мельнице. Показано, что дробление в шаровой мель- |
|
нице |
вызывает расширение пиков дифракции и физическое |
уширение зависит от времени дробления и размера частиц. Результаты изменения ширины дифракционных пиков в за-
висимости от частоты вращения дисков-роторов дезинтеграторной установки и параметры тонкой кристаллической структуры
измельченного |
порошка А12O3 представлены соответственно |
в табл. 5 и 6. |
Увеличение скорости измельчения приводит |
к уменьшению |
величины области когерентного рассеивания |
(ОКР) и ∆а/а. |
|
Для частиц размером от 4 до 0,5 мкм уменьшение величины ОКР и микронапряжений происходит за счет естественной релаксации напряжений с уменьшением размера частиц.
Вследствие того, что хрупкие материалы имеют сравнительно малую величину пластического деформирования, сосредоточенного в области максимальных напряжений, их разрушение происходит скалыванием и в процессе измельчения не наблюдается существенного роста микронапряжений, величина ОКР уменьшается.
Характер зависимостей ОКР = f(d) и ∆аа = f(d), представ-
ленных на рис. 1, качественно совпадает с результатами, полученными с использованием метода аппроксимирующих функций. Область однородности микродеформации слабо зависит от размера частиц и незначительно увеличивается с их ростом.
17
Таблица 4
Характеристики аналитических линий в зависимости от времени измельчения порошка А12О3 в шаровой мельнице
|
Характеристики |
|
|
Время измельчения, ч |
|
|
||
|
|
|
|
|
|
|
|
|
|
1 |
2 |
|
4 |
|
8 |
14 |
|
|
аналитических |
|
|
|||||
|
|
|
|
|
|
|
|
|
|
|
|
при размере частиц, мкм |
|
|
|||
|
линий |
|
|
|
|
|||
|
|
|
|
|
|
|
|
|
|
|
3–4 |
2–3 |
|
1–2 |
|
0,5–1 |
0,5–0,25 |
|
|
|
|
|
|
|
|
|
18 |
Межплоскостное |
0,2086 |
0,2018 |
|
0,2087 |
|
0,2087 |
0,2086 |
расстояние d, нм |
0,1042 |
0,1043 |
|
0,1042 |
|
0,1043 |
0,1042 |
|
|
|
|
||||||
|
|
|
|
|
|
|
|
|
|
β·10–3, рад (102) |
1,59 |
1,72 |
|
1,74 |
|
1,96 |
1,98 |
|
β·10–3, рад (204) |
5,19 |
4,8 |
|
4,62 |
|
4,82 |
4,71 |
|
β204/β102 |
3,264 |
3,676 |
|
2,655 |
|
2,459 |
2,379 |
|
|
|
|
|
|
|
|
|
|
ОКР, нм |
840 |
219,8 |
|
236,5 |
|
167 |
154 |
|
|
|
|
|
|
|
|
|
|
∆a/a·(10–4) |
7,2 |
3,87 |
|
4,63 |
|
4,08 |
3,64 |
Таблица 5
Изменение ширины дифракционных пиков
взависимости от частоты вращения дисков-роторов дезинтегратора при измельчении порошка А12O3
Вид |
Частота вра- |
β·10–3, |
β·10–3, |
ОКР, |
∆а/а·10–4 |
|
обработки |
щения дисков- |
рад (102) |
рад (204) |
нм |
||
роторов, об/с |
|
|||||
Исходный |
– |
1,17 |
3,69 |
200–800 |
5 |
|
порошок |
||||||
|
|
|
|
|
||
|
|
|
|
|
|
|
Измель- |
220 |
2,75 |
3,64 |
90 |
2 |
|
ченный |
||||||
250 |
1,99 |
3,78 |
100 |
2–3 |
||
в дезинте- |
||||||
300 |
2,85 |
4,02 |
100 |
3 |
||
граторе |
||||||
|
|
|
|
|
||
|
|
|
|
|
|
Таблица 6
Параметры тонкой кристаллической структуры порошка Al2О3, измельченного в дезинтеграторе
Размер частиц, мкм |
ОКР, нм |
∆а/а 10–4 |
4,0 |
210,0 |
7,38 |
|
|
|
3,0 |
158,3 |
5,93 |
|
|
|
3,0 |
125,0 |
6,00 |
|
|
|
2,0 |
91,7 |
5,80 |
|
|
|
0,5 |
77,1 |
6,90 |
|
|
|
19
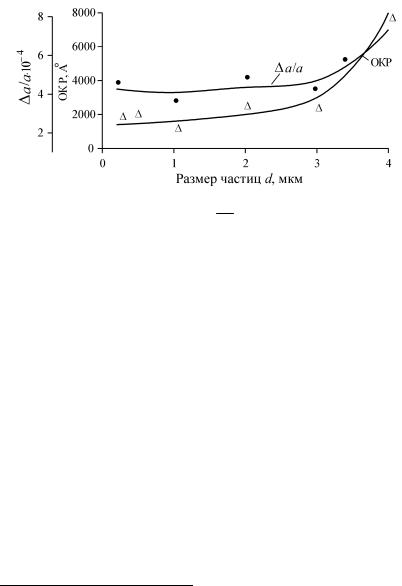
Рис. 1. Зависимость ОКР = f(d) и ∆аа = f(d) для порошка Al2О3,
измельченного в дезинтеграторной установке
На основе механически активированных порошков А12О3 с использованием в качестве пороформирующих элементов полых микросфер А12О3(МКС)* были предложены композиционные пористые материалы состава А12О3-Nb2O5-А12О3(МКС);
А12О3; А12О3-А12О3(МКС).
Отмывка измельченного порошка оксида алюминия от намолотого металла проводилась в 10%-ном растворе соляной кислоты. Химический состав порошка, мас.%:
–до измельчения: Al2О3 – 99,89, Fe2O3 – 0,01, SiO2 – 0,06, CaO – 0,01, Na2O – ост.;
–после измельчения и отмывки: Al2О3 – 99,93, Fe2O3 –
0,012, SiO2 – 0,02, CaO – 0,01, Na2O – ост.
Контрольные вопросы
1.В чем заключается сущность метода механического активирования порошков?
2.Какими факторами определяется интенсивность дробления оксидных порошковых материалов?
* МКС – полые микросферы А12О3 диаметром 100±10 мкм и толщиной стенки 3–5 мкм с насыпной плотностью 0,32 г/см3.
20