
книги / Оксидные композиционные материалы
..pdfпредыдущих формул и имея для постоянной скорости сдвига – dVz/dr = γ, получаем
|
|
|
|
|
|
|
τ |
|
|
|
|
|
|
|
(τ3wQ)/ πR3 = |
∫w γτrz2 dτrz . |
|
(21) |
|||||||||
|
|
|
|
|
|
|
|
0 |
|
|
|
|
|
Дифференцируя и используя правило Лейбница, опреде- |
|||||||||||||
ляем γw: |
|
|
|
|
|
|
|
|
|
|
|
|
|
|
|
dV |
z |
|
|
1 |
|
|
|
dθ |
|
|
|
γw = |
− |
|
|
= |
|
|
|
τw |
|
+3Q . |
(22) |
||
|
|
πR |
3 |
dτw |
|||||||||
|
|
dr w |
|
|
|
|
|
|
|
Подставив уравнение (19) в (22), получаем следующее соотношение:
γw = |
γэф |
3 |
+ |
d ln γэф |
|
||
|
|
|
. |
(23) |
|||
4 |
|
||||||
|
|
|
|
d ln τw |
|
Соотношение (23) используется в расчете истинной скорости сдвига при течении пластической массы.
Результаты эксперимента показывают, что для данных материалов зависимость τw = f (γэф ) в двойных логарифмических
координатах выражается прямой линией в достаточно широкой области значений γэф . При этом справедливо эмпирическое
уравнение
τw = K′ (γэф )n . |
(24) |
В этом уравнении n – угловой коэффициент графика зависимости lgτw= f (lgγэф ):
n = |
d ln τw |
. |
(25) |
|
|||
|
d ln γэф |
|
Тогда из уравнения (23) следует, что
|
3n +1 |
|
|
||
γw = |
|
|
γэф . |
(26) |
|
4n |
|||||
|
|
|
|
61
Подставив выражение (26) в (24), получаем |
|
τw = Kγnw , |
(27) |
где K = K′[4n/(3n+1)]n. |
|
Уравнение (27) известно как степенной закон |
течения, |
а материалы ему подчиняющиеся − как «степенные». |
|
Таким образом, для построения кривой течения (27) достаточно измерить перепад давления по длине капилляра и определить скорость течения. С помощью уравнения (27) и кривых течения, построенных в двойных логарифмических координатах, можно определить две реологические координаты K и n в степенном законе течения. По кривым течения можно также рассчитать вязкость:
η = |
τw |
|
|
|
. |
(28) |
|
γw |
|||
Для «степенной» пластической массы кривая течения опре- |
|||
деляется выражением (27), следовательно, вязкость |
|
||
η= Kγn−1 . |
(29) |
Для определения реологических характеристик был подготовлен набор капилляров с различными соотношениями L/D, где L, D – длина и диаметр капилляра соответственно (L = 4, 8, 12, 16, 20, 30, 50 мм; D = 2, 3, 5 мм). Для каждого капилляра проводилась серия экспериментов при различных скоростях течения γ (10 ≤ γ ≤ 100 с–1). При этом рабочий узел, состоящий из капилляра и вискозиметрического резервуара, устанавливался на разрывной машине Р-5 и подвергался нагружению при различных скоростях движения поршня Vп: 0,17 10–3; 0,25 10–3; 0,33 10–3 м/с. По величине нагрузки, фиксируемой динамометрами сжатия, для заданной геометрии капилляра и скорости деформации сдвига рассчитывалось напряжение сдвига τw по формуле (14), при этом величина «входовой» поправки определялась графически (см. рис. 16). Истинная скорость сдвига на стенке капилляра γw рассчитывалась с помощью выражений (19) и (26), а для оп-
62
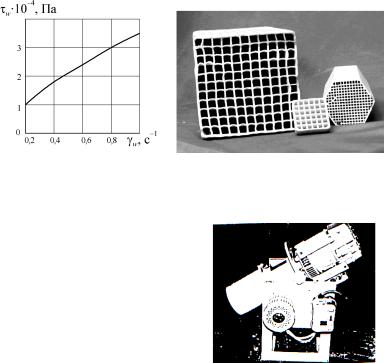
ределения реологических констант K и п использовалась кривая течения (рис. 17).
Из пластифицированной керамической массы были изготовлены сотовые конструкции (рис. 18), представляющие интерес для каталитических систем. Установлено, что изготовление сотовой структуры оптимально при τw в пределах
(2–4) 104 Па [67].
Рис. 17. Кривая течения керами- |
|
Рис. 18. Сотовые конструкции |
||||
ческой массы из TiO2 Al2O3 |
|
|
||||
Пластифицированные порош- |
|
|||||
ки TiO2 Al2O3 были конгломе- |
|
|||||
рированы |
в грануляторе |
[68] |
|
|||
(рис. 19) по технологии, пред- |
|
|||||
ставленной в работах [69, 70]. |
|
|
||||
Для |
исследования влияния |
|
||||
количества связующего на порис- |
|
|||||
тость |
конгломерированного |
по- |
|
|||
рошка фракции (60–100 мкм) бы- |
|
|||||
ло приготовлено несколько сме- |
Рис. 19. Гранулятор |
|||||
сей с |
различным |
содержанием |
||||
(опытный образец) |
||||||
связующего (табл. 10). |
|
|||||
|
|
|||||
Перспективным |
технологическим направлением исполь- |
зования композиционных порошков из оксидной керамики является формирование многофункциональных покрытий
[71, 72].
63
|
|
|
Таблица 10 |
|
|
Влияние связующего на пористость смеси |
|||
|
|
|
|
|
Номер смеси |
Количество |
Пористость смеси, |
||
связующего, % |
% |
|||
|
|
|||
I |
|
10 |
17 |
|
II |
|
16 |
12 |
|
III |
|
20 |
30 (рыхлая смесь) |
Показано, что наименьшей пористостью обладают композиционные конгломерированные порошки с содержанием 16 % связующего, которые и были использованы в качестве материалов для нанесения плазменных покрытий на изделия. Покрытия наносили на установке УПУ-3Д при следующих параметрах режима напыления: J = 400 А; U = 70 В; Q = 40 дел. шк; L = 80 мм.
Испытания износостойкости покрытий проводили на машине трения СМЦ-1. Контртело было выполнено из СтХ13 в виде ролика диаметром 50 мм с твердостью 60–63 НRС. Скорость скольжения по поверхности трения составляла 0,785 м/с, продолжительность испытания – 8 ч при осевой нагрузке на па-
ру трения 40, 50, 60, 70 кг.
В результате исследований установлена следующая зависимость износа от нагрузки на пару трения (количество связующего 16 %):
нагрузка, кг |
40 |
50 |
60 |
70 |
износ, мкм/км |
0,66 |
0,673 |
0,696 |
0,854 |
Разработанные покрытия были испытаны в качестве износостойких на титановых и стальных порошковых тяговых роликах.
Контрольные вопросы
1.Какой метод используется для получения композиции на основе титана, содержащих дисперсные включения оксидов?
2.С какой целью в титановую матричную основу вводится дисперсная фаза Al2O3?
64
3.Какое оборудование используется для формирования дисперсной фазы и порошковой композиции TiO2·Al2O3?
4.В чем состоит содержание основных технологических этапов подготовки композиции Ti2·Al2O3 ?
5.Что представляет собой явление механического легирования?
6. Какая структура композиции Ti-Al2O3 формируется
впроцессе механического легирования?
7.Как влияет температура на прочность титановых композиций Ti·Al2O3 ?
8.При каких температурах рекомендуется использовать детали, изготовленные из дисперсно-упрочненных титановых композиций?
9.Каким способом формируются порошковые компози-
ции TiO2·Al2O3?
10.Что такое пластификаторы и какова их роль при фор-
мировании непластичных по своей природе материалов?
11.Какие типы связующих композиций используются для получения порошковых материалов TiO2·Al2O3 ?
12.Каким образом используются термопластичные связующие при создании композиционных материалов на основе диоксида титана?
13.Какие связующие материалы на основе водорастворимых полимеров используются для получения композиционных материалов на основе диоксида титана?
14.Какие особенности использования связующих на основе органических растворителей?
15.Чем объясняется современная тенденция к использованию элементоорганических соединений для связывания формуемой массы?
16.Какими характеристиками описываются свойства пластифицированных керамических масс?
17.Что представляет собой закон течения и какие параметры формируемой керамической массы он связывает?
18.Какие методы и приборы используются для определения свойств пластифицированных керамических материалов?
19.Каким образом метод капиллярной вискозиметрии используется для определения закона течения пластической массы?
65
20.Что представляют собой сотовые конструкции на основе диоксида титана и где они могут применяться?
21.Каким образом используются композиционные порошки из оксидной керамики для формирования многофункциональных покрытий?
22.Каким образом используется гранулятор при создании композиционных материалов на основе диоксида титана?
6.СВОЙСТВА КОМПОЗИЦИОННЫХ МАТЕРИАЛОВ
ИСОТОВЫХ КОНСТРУКЦИЙ НА ОСНОВЕ ОКСИДОВ
ТИТАНА
Исследовалась керамика на основе оксида титана (ТiO2), армированная стекловолокном, спеченная в интервале температур 673–723 К со следующими свойствами компонентов:
свойства матрицы: модуль упругости Е1 = 60 000 МПа; модуль сдвига µ1 = 2609 МПа; модуль Пуассона ν1 = 0,15; модуль объемного сжатия K1 = 2857 МПа;
свойства волокна (ВМПС): Е2 = 100 000 МПа; µ2 =
=41 320 МПа; ν2 = 0,21; K2 = 57 470 МПа [73].
6.1.Прогнозирование эффективных упругих и прочностных характеристик композиционных материалов на основе керамики, армированной дискретными волокнами
Для прогнозирования упругих характеристик композиционного материала с хрупкой матрицей, армированного стекловолокном, использовались теоретические зависимости, полученные на основе структурно-феноменологического подхода механики неоднородных сред; исследуемый материал рассматривался как двухкомпонентный стохастически армированный композит, свойства компонент которого детерминированы и изотропны. При этом модули объемного сжатия и сдвига волокнистых композиционных материалов рассчитывались по формулам [74]
K* = <K> – Dk /(ν1K2 + ν2K1 + a), |
(30) |
66
µ* = <µ> – Dµ /(v1µ2 + v2/µ1 + b),
где a = 4/3<µ>; b = <µ> <9K+8µ/ >/6<K+2µ>; Dk, Dµ – дисперсия модулей объемного сжатия и сдвига, определяемые соотношениями
Dk = (K1 − K 2 )2 ν1 ν2,
Dµ = (µ1 −µ2 )2 ν1 ν2,
а знак < > означает операцию интегрирования по объему (усреднение).
Прочность композиционных материалов, армированных дискретными волокнами, рассчитывались по формуле [75]:
σ* = [τ12 ](lкр/d2)V2 +[σ1] V1, |
(31) |
где [τ12], [σ1] – предел прочности межфазного напряжения сдвига и матричного материала соответственно; lкр, d2 – критическая длина волокна и диаметр; V1, V2 – объемное содержание матрицы и волокна соответственно.
Результаты расчетов эффективных характеристик композита по формулам (30) сведены в табл. 11.
|
|
|
|
Таблица 11 |
Эффективные упругие характеристики керамики, |
||||
|
армированной стекловолокном |
|
||
|
|
|
|
|
Объемная |
K, МПа |
µ, МПа |
Е, МПа |
ν |
доля волокон |
||||
|
|
|
|
|
0,20 |
5872 |
4892 |
11490 |
0,174 |
|
|
|
|
|
0,25 |
7221 |
5893 |
13900 |
0,179 |
|
|
|
|
|
0,30 |
8811 |
7065 |
16730 |
0,183 |
Считая [σ1]+ = 2 МПа, l/d2= 20, V2 = 0,3, V1 = 0,7; [τ12], = = 0,5 МПа, можно получить эффективную прочность композита
на растяжение σ*+ = 4,4 МПа. Аналогично, считая [σ1]– = 3 МПа, получим эффективную прочность на сжатие σ* = 5,1 МПа.
67
Таким образом, при условии, когда длина волокон меньше критической, прочность волокнистого композиционного материала, упрочненного дискретными волокнами, возрастает пропорционально объемной доле волокон, отношению l/d2, прочности границы раздела и прочности матрицы, оставаясь при этом меньше прочности композиционного материала, армированного непрерывными волокнами. Достичь прочности, сопоставимой с прочностью волокнистого композиционного материала с непрерывными однонаправленными армированными волокнами, возможно лишь при отношении l/d2 больше критической величины. В этом случае соотношение между прочностями керамических материалов, упрочненных дискретными и непрерывными волокнами, можно представить в виде [76]
(σв )диск |
=1− |
1 |
, |
(32) |
(σв )непр |
2(l / lкр ){1+ σ′1 / (σв )2 ][(1/V2 )−1 } |
где σ′м – напряжение в матрице в момент разрушения волокон; (σв )2 , V2 – предел прочности волокна и его объемное содержа-
ние.
Как показывают расчеты, уже при l/lкр = 10 прочность композиционных материалов с дискретными волокнами достигает 95 % прочности композиционных материалов с непрерывными волокнами.
Для изготовления сотовых носителей катализаторов использовались дискретные волокна с объемным содержанием ~ 5 %, что было обусловлено заданными прочностными требованиями изделия, а также технологическими ограничениями, связанными с трудностями достижения высокой степени упорядоченности армирующего каркаса, со значительными концентрациями волокнистой фазы при формовании тонкостенной пространственной конструкции.
Экспериментальные результаты подтвердили теоретические расчеты. Такого рода данные свидетельствуют о том, что разработанная технология позволила уменьшить, а может и ликвидировать недостаток керамики, связаны с ее низкой трещино-
68
стойкостью. В отличие от металлов, в которых возникающие в процессе эксплуатации напряжения релаксируют вследствие пластической деформации в зоне трещины, диссипация энергии разрушения в керамике достигается рациональной организацией микроструктуры материалов – армированием дискретными волокнами. Упрочнение волокнами позволяет манипулировать полями напряжений, не формируя собственно пластичность керамики. Более прочные волокнистые включения, находящиеся в объеме керамического материала, который под воздействием приложенных напряжений подвергается растрескиванию, остаются неизменными, а вершина трещины упирается в границу волокно–матрица. При этом, если взаимодействие на границе достаточно слабое, включения могут изменять свое исходное положение. Такое перемещение требует преодоления силы трения на контактной поверхности. Стенки трещины сжимаются под действием силы трения, т.е. концентрация напряжений у вершины трещины снижается, энергия рассеивается, и материал становится более вязким. Разрушение композиционных материалов сводится таким образом к ряду последовательных дискретных этапов локализации трещины, каждый из которых отделен друг от друга и не приводит к катастрофическому разрушению материала, позволяя реализовываться механизму разрушения согласно рассмотренной теоретической модели.
6.2. Разрушение сотовых конструкций на основе оксидных композиционных материалов
Выработка ресурса решетчатых конструкций на основе диоксида титана, предназначенных для использования в химически агрессивных средах, в качестве фильтров, катализаторов для очистки газовых выбросов, связана главным образом с накоплением необратимых повреждений в их структурных элементах. Эти повреждения имеют как механическую (растрескивание, унос вещества под действием движущейся газовой среды), так и физико-химическую природу, связанную с протеканием химических реакций взаимодействия материала тонкостенного каркаса с газовой средой, подлежащей очистке в процессе выброса. Накопление повреждений химического происхождения в эле-
69
ментах каркаса связано с особенностями технологического процесса получения изделий на основе диоксида титана с применением многокомпонентных связующих, включающих органические и элементоорганические соединения. Ограничение верхнего предела температуры спекания (723 К), связанного с высокой активностью диоксида титана, приводит к тому, что процесс спекания не завершается полностью. Так, анализ процесса пиролиза диоксида титана с кремнезолем, а также диоксида титана смеси с кремнезолем и элементоорганикой показал, что в процессе пиролиза идет выделение воды и углекислого газа. Наличие в структуре элементов готового изделия остаточных компонентов такого рода является дополнительным фактором физико-химического происхождения, приводящим к возможному ухудшению механических свойств материала каркаса в условиях воздействия агрессивных сред. В целом, как правило, виды повреждений элементов структуры рассматриваемых изделий не поддаются дифференциации и могут быть одновременно механического, физического и химического происхождения. Такие повреждения в совокупности определяют прочностные свойства конструкции при различных сроках эксплуатации. Несмотря на многообразие перечисленных явлений, их можно описать в рамках единой полуэмпирической теории, связывающей кинетику накопления повреждений с действующими нагрузками и условиями взаимодействия с окружающей средой. При этом для прогнозирования ресурса конструкции в целом достаточно эффективным является структурно-феноменологический подход микромеханики неоднородных сред, описывающий процесс деформирования элементов конструкций на микро- и макроструктурных уровнях с учетом кинетики разрушения механического, физического и химического происхождения, в совокупности определяющих изменение прочности элементов решетчатого каркаса, а следовательно, характера накопления повреждаемости конструкции в реальных условиях эксплуатации. Таким образом, располагая эмпирическими данными об изменении упругих и прочностных свойств материала каркаса вследствие протекания каталитических процессов и уменьшения толщины стенок каркаса под воздействием агрессивных сред, можно теоретиче-
70