
книги / Технология термического производства. Способы наноструктурирования материалов
.pdf
Придавая индуктору необходимую форму, можно использовать эффект близости для нагрева определенных частей поверхности обрабатываемой детали.
Кольцевой эффект. Если проводник свернуть в кольцо и по нему пропустить переменный электрический ток, то наибольшая его плотность будет на внутренней поверхности (кольцевой эффект).
Кольцевой эффект (рис. 5.3), являющийся также разновидностью поверхностного эффекта, объясняется асимметрией магнитного поля витка или соленоида. Во внутренней полости оно значительно сильнее, чем снаружи, вследствие чего главная часть электромагнитной энергии поступает в проводник изнутри.
Кольцевой эффект ухудшает использование сечения проводников, повышая их активное сопротивление. При расчете сопротивления цилиндрических и овальных индукторов, внутрь которых помещена нагреваемая деталь, можно принимать, что ток сконцентрирован лишь на внутренней
стороне провода. Усиление магнитного поля внутри индуктора в соединении с эффектом близости повышает эффективность нагрева деталей, охваченных индуктором. В этом случае кольцевой эффект полезен, несмотря на увеличение активного сопротивления индуктирующего провода.
151
5.2. Параметры индукционного нагрева
При печном нагреве основными параметрами, определяющими условия протекания фазовых превращения в стали и конечный результат нагрева, являются конечная температура (tк), общее время нагрева. При индукционном нагреве важны не только эти параметры, но и средняя скорость нагрева в области фазовых превращений, которая связана как
степлофизическими свойствами стали, так и с энергетическими параметрами нагрева, т.е. величиной удельной мощности (Р0, кВт/см2), и частотой тока, которая и определяет глубину активного нагреваемого слоя детали. Для поверхност-
ного нагрева необходима большая удельная мощность (0,5–2,0 кВт/см2) и малое время нагрева (2–10 с), для глубинного или сквозного прогрева (например, для объемно-поверх-
ностной закалки удельная мощность должна быть меньше (0,05–0,2 кВт/см2), а время нагрева значительно больше (20–200 с). Время нагрева при этом зависит как от нагреваемого сечения детали, так и от частоты тока. Скорости нагрева при этом лежат в пределах 30–300 °С/с и 2–10 °С/с.
Выбор частоты. При выборе частоты необходимо [1, 24, 29], чтобы выбранная частота обеспечивала оптимальный КПД индуктора и нагрев током, а не теплопроводностью. При соблюдении этих условий затраты электроэнергии будут минимальными, а качество нагрева (равномерность, точность, глубина прогрева) оптимальным. Например, для стальных заготовок диаметром 70–260 мм рекомендуемая частота индукционного нагрева 500 Гц, а для диаметров
30–80 мм уже 2500 Гц.
При поверхностной закалке выбор частоты тока связан
стребуемой глубиной закаленного слоя, Хк, которую можно отождествить с оптимальной глубиной нагрева ∆н. Выбор осуществляют по эмпирическим соотношениям (например,
152

для низколегированной стали ∆н = (10 55) 1f , см) или по
справочным таблицам, в которых выбор частоты связан с требуемой глубиной закалки, размерами изделий и другими параметрами нагрева. Табл. 5.2, 5.3 и 5,4 приведены по источнику [1].
Таблица 5.2
Выбор частоты тока в зависимости от диаметра изделий и требуемой глубины закалки
|
Рациональные |
Минимальные диаметры |
||
Частота, |
при нагреве под закалку |
|||
Гц |
пределы глуби- |
|
|
|
наименьший |
наименьший |
|||
ны нагрева, мм |
||||
|
возможный |
желательный |
||
|
|
|||
50 |
15–80 |
100 |
200 |
|
1000 |
3–17 |
22 |
44 |
|
2500 |
2–11 |
14 |
28 |
|
4000 |
1,5–9 |
11 |
22 |
|
8000 |
1–6 |
8 |
16 |
|
10 000 |
0,9–5,5 |
7 |
14 |
|
70 000 |
0,3–2,5 |
2,7 |
5,4 |
|
400 000 |
0,2–1 |
1,1 |
2,2 |
|
|
|
|
|
Таблица 5.3
Режимы индукционной закалки цилиндрических деталей диаметром 20–80 мм
Глубина |
Удельная мощ- |
Время |
Удельная энергия, |
закалки, мм |
ность, кВт/см2 |
нагрева, с |
кВт·с/см2 |
|
Частота тока 2000 Гц |
|
|
1,5 |
1,4 |
2 |
2,8 |
2 |
1,35 |
2,5 |
3,4 |
3 |
1,2 |
3,4 |
4,1 |
4 |
1,05 |
4,3 |
4,5 |
5 |
0,95 |
5,1 |
4,9 |
6 |
0,8 |
6,3 |
5,1 |
153
Окончание табл. 5.3
Глубина |
Удельная мощ- |
Время |
Удельная энергия, |
закалки, мм |
ность, кВт/см2 |
нагрева, с |
кВт·с/см2 |
|
Частота |
300000 Гц |
|
1 |
0,9 |
2,5 |
2,25 |
2 |
0,5 |
9 |
4,5 |
3 |
0,4 |
15 |
6 |
4 |
0,3 |
22 |
6,6 |
5 |
0,25 |
28 |
7 |
6 |
0,2 |
36 |
7,2 |
8 |
0,15 |
50 |
7,5 |
Примечание: приведенные в таблице данные для частоты 2000 Гц практически не отличаются от данных для частоты 2400 Гц, соответствующей современному стандарту. Данные для частоты 300 000 Гц справедливы для частот от 200000 Гц до 400000 Гц.
|
|
|
|
Таблица 5.4 |
|
Удельная мощность, необходимая |
|
||
|
для осуществления поверхностной закалки |
|||
|
|
|
|
|
Часто- |
Диапазон глубин |
Удельная мощность, кВт/см2 |
||
та, кГц |
закалки, мм |
наименьшая |
оптимальная |
максимальная |
1 |
2 |
3 |
4 |
5 |
500 |
0,4–1,1 |
0,7 |
0,9 |
1,1 |
|
1,1–2,2 |
0,3 |
0,5 |
0,7 |
10 |
1,5–2,3 |
0,7 |
1 |
1,5 |
|
2,3–3 |
0,5 |
1 |
1,4 |
|
3–4 |
0,5 |
1 |
1,3 |
1 |
5–7 |
0,5 |
1 |
1,1 |
|
7–9 |
0,5 |
1 |
1,1 |
Примечание:
1.Данные справедливы для методов одновременной и непре- рывно-последовательной закалки, однако для последней желательно не применять нижний предел удельной мощности.
2.Данные графы 4 соответствуют получению оптимальной структуры.
3.Данные графы 3 дают наименьшую мощность генератора при повышенном расходе электроэнергии.
4.Использование графы 5 обеспечивает наибольшую производительность установки принаименьшемрасходе энергиинаоднудеталь.
154
Во всех случаях при расчетах принимают tк = 900 °С. При этом на внутренней границе нагреваемого слоя температура соответствует температуре потери магнитных свойств для большинства сталей (ориентировочно 750 °С).
Определение удельной мощности и времени нагрева.
Одна и та же глубина слоя закалки (по мартенситу) может быть получена при данной частоте при разных удельных мощностях и разном времени нагрева. Ориентировочно эти параметры можно определить по табл. 5.3 и 5.4 и по графикам источников [1, 2, 28, 29]. Более точные значения определяют расчетом. Заканчивают выбор режима нагрева и закалки посредством выполнения закалочного ряда, когда при неизменной настройке установки обрабатывают несколько деталей с различным временем нагрева. Результат обработки каждой детали оценивают методами металлографического анализа и по твердости.
Выбор индуктора (конструктивные особенности и его характеристики) зависит от применяемого метода закалки, геометрии и размеров детали. В практике высокочастотной поверхностной закалки используют четыре основных метода:
1.Метод единовременной закалки, обеспечивающий одновременный нагрев и охлаждение всей поверхности детали.
2.Метод последовательной закалки отдельных участков деталей, что дает возможность значительно уменьшить потребную мощность индукционной установки.
3.Метод непрерывно-последовательной закалки изделий большой длины и одинакового сечения по всей длине (валы, трубы, профили и т.д.) при непрерывном движении изделия относительно индуктора, что позволяет применить наименьшую мощность установки.
4.Метод закалки под водой, отличающийся от перечисленных методов тем, что индуктор и нагреваемую деталь погружают в воду, где и производится нагрев.
155
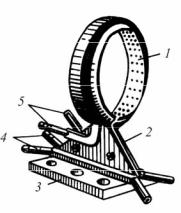
5.3. Индукторы для поверхностной индукционной закалки
Простейшим видом индуктора является виток, согнутый из медной трубки, охлаждаемой водой.
Для единовременной закалки изделий цилиндрической формы применяют одновитковые индукторы, если высота нагреваемой поверхности не превышает примерно радиуса индуктора. Многовитковые индукторы позволяют проводить одновременный нагрев деталей высотой до трех диаметров.
Вид простого одновиткового индуктора дан на рис. 5.4.
Рис. 5.4. Индуктор для закалки способом одновременного нагрева цилиндрической детали: 1 – индуктирующий провод, создающий переменное магнитное поле; 2 – токоподводящие шины; 3 – колодки для присоединения индуктора к понижающему трансформатору; 4 – трубки для подачи воды, охлаждающей соединительные колодки; 5 – трубки для подачи воды, охлаждающей индуктор и нагретую
поверхность детали
Схемы различных одновитковых индукторов для одновременного нагрева деталей приведены на рис. 5.5. На (рис. 5.5, а) показано размещение цилиндрической детали 1 в индукторе 2. Для получения нагретого слоя на поверхности
156
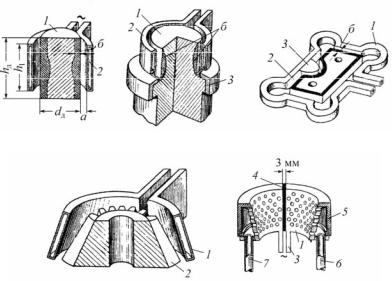
цилиндра по возможности одинаковой толщины δ индуктор должен иметь высоту
hi = hд – 2a,
где hi – высота индуктора; hд – высота детали; а – зазор между индуктором и деталью.
а |
б |
в |
г д
Рис. 5.5. Схемы одновитковых индукторов для одновременного нагрева деталей
Величина воздушного зазора между индуктором и нагреваемой деталью обычно не превышает 2–5 мм. Увеличение зазора вызывает резкое падение КПД индуктора, а при малом зазоре значительно усложняется установка детали в индукторе и увеличивается опасность электрического пробоя между индуктором и деталью.
Если при нагреве детали отдельные ее участки необходимо предохранить от воздействия электромагнитного поля, то применяют защитные экраны. Их выполняют, как правило,
157
из меди толщиной не менее 4δCu. На рис. 5.5, б показан случай нагрева шейки вала 1 в одновитковом индукторе 2. Здесь защита от нагрева выступа вала осуществляется экраном 3, выполненным из меди в виде кольца. В тех случаях, когда проводится длительный прогрев участков детали, экраны рекомендуется выполнять в виде сварных полых конструкций, охлаждаемых водой.
Для равномерного нагрева поверхности изделий разнообразной формы применяют индукторы, форма и размеры которых соответствуют форме и размерам изделий. На (рис. 5.5, г, д) показаны одновитковые индукторы 1 для нагрева и закалки конических шестерен 2. Чтобы увеличить равномерность нагрева поверхности шестерни, угол конусности индуктора делают меньше, чем шестерни. Охлаждение конической шестерни после окончания нагрева может производиться путем сбрасывания шестерни в охлаждающую среду для закалки (рис. 5.5, г) или путем охлаждения нагретой поверхности шестерни водой через отверстия в индукторе (рис. 5.5, д). Во втором случае воду в индуктор подают лишь после нагрева изделия во время его охлаждения, поэтому внутренняя коническая часть индуктора, изготовленная из листовой меди, должна иметь большую толщину, чем в постоянно охлаждаемом индукторе, а именно должна быть не менее 5δCu. Отверстия в индукторе для прохода воды сверлят диаметром 1–2 мм в шахматном порядке на расстоянии 4–8 мм одно от другого. Выводы 3 от конической части индуктора присоединяют к генератору, а в промежутке между началом и концом индуктора помещают изолирующую пластину 4. Наружный кожух 5 индуктора изготавливают обычно из текстолита. Охлаждающая вода подается в индуктор по патрубкам 6 и 7 и через отверстия в конической части индуктора попадает на нагретую поверхность изделия.
На (рис. 5.5, в) изображена форма одновиткового индуктора 1, обеспечивающего равномерный нагрев всей боковой
158
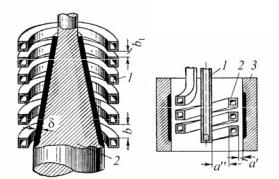
поверхности шаблона 2. Для равномерного нагрева поверхности впадины шаблона, размеры которой меньше удвоенной толщины трубки индуктора, к нему приварен вкладыш 3 из меди.
На (рис. 5.6, а) показана схема многовиткового индуктора 1 для нагрева конической поверхности шейки вала 2. Чтобы толщина нагретого слоя δ была одинаковой вдоль высоты шейки, цилиндрический индуктор выполняют с переменным шагом, причем b > b1. При конструировании многовитковых индукторов для нагрева внутренних поверхностей втулок и отверстий в деталях (рис. 5.6, б) необходимо учитывать, что зазор а" между центральной токоподводящей трубкой 1 индуктора и его витками 2 должен в несколько раз превышать зазор а' между индуктором и изделием 3.
аб
Рис. 5.6. Схемы многовитковых индукторов: а – для нагрева поверхности конической шейки вала; б – для нагрева внутренней поверхности отверстия
Впротивном случае индуктор будет нагревать сам себя,
ане изделие. Чтобы повысить КПД индукционной установки, рекомендуется брать величину зазора а' не более 3 мм при нагреве на воздухе. Для нагрева отверстий небольшой высоты применяют также аналогичные одновитковые индукторы.
159
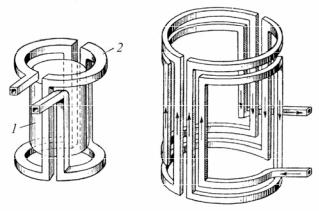
Для одновременного нагрева боковой и торцовых поверхностей цилиндрических деталей применяют петлевые индукторы (рис. 5.7). На боковой поверхности детали 1, помещенной (рис. 5.7, а) в магнитное поле индуктора 2, нагревается полоса, по ширине примерно равная ширине трубок индуктора. Чтобы получить нагретый слой по всей боковой поверхности, деталь приводят во вращение вокруг вертикальной оси. Ускорение процесса нагрева боковой поверхности детали достигается увеличением количества и ширины вертикальных стоек петлевого индуктора (рис. 5.7, б). Для нагрева торцовых поверхностей детали высота индуктора должна быть больше высоты детали на 30–50 мм.
аб
Рис. 5.7. Петлевые индукторы с четырьмя (а) и восемью (б) вертикальными стойками (стрелками во втором случае показано направление тока в один из моментов времени)
Одновременный нагрев плоских поверхностей различных изделий и инструмента осуществляется при помощи плоских спиральных индукторов (рис. 5.8). Нагрев изделий на воздухе плоским индуктором можно проводить на площади не меньше 3–5 см2. При нагреве под водой удается полу-
160