
книги / Технология термического производства. Способы наноструктурирования материалов
.pdfлия загружаются на футерованную тележку – подъемный под, который гидравлическим или механическим приводом поднимается в камеру и остается в течение всего времени обработки изделий в печи.
Электропечи с передвижной камерой нагрева исполь-
зуют для азотирования. Печь имеет неподвижный под с двумя последовательно расположенными муфелями, снабженными песочными затворами. Нагревательная камера печи перемещается на колесах с одного муфеля на другой и нагревает муфель с изделиями в установленной последовательности. С торцевых сторон рабочая камера закрывается подъемными дверцами. Нагревательные элементы располагают на боковых стенках и на своде камеры.
Двухкамерные электропечи применяют для ступенчато-
го нагрева высоколегированной быстрорежущей стали. Нижняя камера служит для подогрева, верхняя камера – для окончательного нагрева.
Электрические печи-ванны применяются для мелких де-
талей и инструмента. Для нагрева под закалку широко применяют электродные печи-ванны.
Электродные печи-ванны предназначаются для безокислительного нагрева изделий до температуры, не превышающей 1300 °С. Отпуск мелких деталей и инструмента производится в ваннах с внутренним или внешним обогревом. Нагрев изделий в них осуществляется минеральным маслом или щелочными расплавами.
Печи непрерывного действия
Электропечи непрерывного действия (методические печи) применяют для обработки однотипных деталей в крупносерийном и массовом производстве. Детали в методических печах в процессе нагрева перемещаются от загрузочного окна к разгрузочному. Электропечи непрерывного действия выполняются многозонными. Как правило, печи непрерывного
81
действия совместно с другими видами оборудования связывают в агрегаты для термической обработки изделий. Все применяемое оборудование в агрегате должно иметь равную производительность.
Конвейерные печи применяют для термической обработки мелких и легких деталей весом до 5 кг. Панцирные конвейеры изготавливают из стали 15Х25Н19С2Л, сетчатые конвейеры – из сплавов Х15Н60 и Х20ХН80. Максимальная температура нагрева панцирного конвейера достигает 950 °С. Конвейерные печи связывают с другим оборудованием в конвейерные закалочно-отпускные агрегаты.
Толкательные электропечи. Движение деталей или под-
донов с деталями в толкательных печах осуществляется толкателем по направляющим пода печи. Конструктивно толкательные печи изготавливают одно-, двух- и четырехрядными. Толкательные печи используют для нагрева под закалку, отпуск, отжиг, нормализацию. Толкательные печи применяют также для процессов цементации и нитроцементации. Эти печи конструируют муфельными и безмуфельными. Муфель печи изготавливают из стали Х18Н25С2, поддоны – из стали 30Х24Н12СЛ. Толкательные печи обычно связывают в агрегаты. Толкательные агрегаты располагают в одну линию или они имеют П-образную или Ш-образную компоновку.
Барабанные печи. Перемещение деталей в этих печах осуществляется внутри вращающихся барабанов, выполненных из жаропрочной стали 40Х25Н20СЛ. Барабанные печи применяют для термической обработки мелких деталей (шарики, ролики, гайки, оси, втулки). Наибольший размер детали не более 80 мм. В барабанных печах можно проводить цементацию и нитроцементацию деталей. Барабанные печи часто встраивают в агрегаты барабанного типа.
Карусельные печи имеют вращающийся под, на который укладывают детали, или вращающийся свод с подвешенными к нему ковшами, в которых находятся нагреваемые детали.
82
Карусельные печи компактны, универсальны, что позволяет нагревать детали простой и сложной формы. К недостаткам этих печей следует отнести трудность механизации загрузки и выгрузки деталей и трудность создания герметичности
врабочем пространстве печи.
Вэлектропечах с шагающим подом перемещение изделий вдоль печи осуществляется с помощью шагающих балок, движущихся по замкнутому контуру в продольных щелях пода печи. Печи с шагающим подом применяются для нагрева под закалку, отжиг и нормализацию тяжелых и громоздких изделий: листов, профилей, слитков.
Врольганговых электропечах перемещение изделий достигается вращением жароупорных роликов, размещенных на поду печи. Изменение скорости перемещения изделий допускается в пределах для обычных печей 1:4, быстроходных 1:35. Ролики печи изготовляют из сплавов Х28Н48В5Л, 40Х25Н20С2Л. Х23Н18. Рольганговые печи применяют для термической обработки листового и фасонного проката, труб, прутков. Детали сложной конфигурации в этих печах по рольгангу перемещают на поддонах.
Электропечи с пульсирующим подом служат для терми-
ческой обработки мелких (весом до 3 кг) стальных деталей: шпилек, колец подшипников, осей и т.д. Перемещение деталей в печах с пульсирующим подом осуществляется по поду за счет повторяющихся возвратно-поступательных движений подовой плиты и резкого останова ее при перемещении по ходу движения. Наиболее широко эти печи применяют для нагрева под закалку мелких деталей, высокотемпературного отпуска и отжига. Максимально допустимая температура нагрева деталей не должна превышать 900 °С.
Электропечи с ручьевым подом служат для термической обработки втулок, колец подшипников, осей, труб и т.п. Перемещение деталей осуществляется под действием силы тяжести деталей или путем проталкивания вновь загружаемой
83
деталью с помощью механизма перемещения. Неподвижный под печи выполняется в виде ручьев под термообрабатываемую деталь, что ограничивает возможные боковые смещения детали при перемещении ее вдоль рабочего пространства печи.
Протяжные электропечи предназначаются для термической обработки проволоки, ленты из стали и цветных металлов. Протяжные печи выполняются горизонтальными и башенными. Перемещение изделий в печи осуществляется от специальных размоточно-намоточных устройств, находящихся перед загрузочным или за разгрузочным проемами печи.
Туннельные печи представляют собой туннель, в который изделия помещаются на футерованных тележках, пропускаемых через камеру печи. Движение тележек производится толкателем, лебедкой или непрерывной цепью через определенный промежуток времени, когда все тележки продвигаются на длину, равную длине одной тележки. При этом одна тележка выходит из печи для выгрузки, в то время как с противоположного конца печи в ее камеру входит очередная загруженная тележка. Печи туннельного типа применяют для длительного отжига, например отжига отливок на ковкий чугун.
При проектировании термического нагревательного оборудования следует широко применять вакуумное оборудование, а также оборудование, обеспечивающее прогрессивные методы скоростного нагрева деталей: нагрев токами высокой частоты, нагрев пропусканием тока через изделие, плазменный нагрев, поверхностный нагрев лазерным лучом и др.
3.3.Расчет времени нагрева и охлаждения по критериальным зависимостям
Для расчета нагрева и охлаждения металла задают краевые условия:
84
–начальное условие, характеризующее распределение температур в теле в начальный момент (τ = 0);
–граничные условия, показывающие изменение температуры на поверхности тела.
Граничные условия, в свою очередь, могут быть следующими:
1) задано распределение температур на поверхности те-
ла как функция времени (например tпов.изд = const);
2) задан тепловой поток (например тепловой поток q =
const, скорость нагрева Cн = const);
3) задан закон изменения температуры окружающей
среды (например tпечи = const).
Время нагрева изделия состоит из времени нагрева по-
верхности до заданной температуры τнагр.пов и времени прогрева, т.е. времени выравнивания температуры по сечению
τпрогр. Для тел относительно малого сечения из материала с высокой теплопроводностью разность температур по сечению в процессе нагрева столь незначительна, что её можно не учитывать. Такие тела называют теплотехнически тонкими. Если при нагреве изделий происходит перепад температур по сечению, то такие тела называются теплотехнически массивными.
Для тонких тел применяют одноступенчатый режим, состоящий из одного периода нагрева в печи с температурой tп = const (рис. 3.1, а). При нагреве массивных тел различают следующие режимы: двухступенчатый, состоящий из периода нагрева поверхности и периода прогрева (рис. 3.1, б); комбинированные режимы, например, трехступенчатый, состоящий из периодов предварительного нагрева, ускоренного нагрева и периода прогрева (рис. 3.1, в) и режим, применяемый для изделий сложной формы и изделий из высоколегированных сталей. Применяют комбинированные режимы при нагреве изделий в печах: колпаковых, шахтных, камерных, температура которых при загрузке садки была на 200–300 °С
85
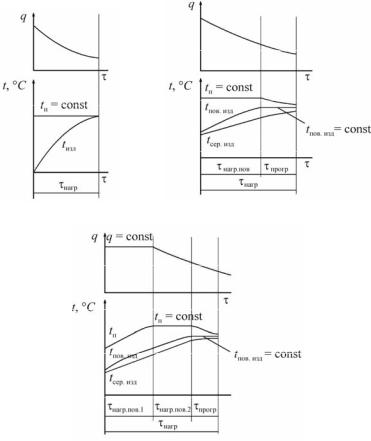
а |
б |
в
Рис. 3.1. Режимы нагрева: а – одноступенчатый, б – двухступенчатый, в – трехступенчатый
ниже требуемой технологической температуры. Например, так нагревают под закалку горячие штампы.
В цикл работы камерных и шахтных печей периодического действия включают также время на загрузку и выгрузку деталей, время на установку муфеля печи, время на предварительную продувку муфеля защитным газом и др.
86
Если охлаждение изделий согласно технологии происходит с печью, то время охлаждения τохл также необходимо включить в общее время нахождения изделий в печи.
При определении общей выдержки изделий в печи необходимо к рассчитанному времени нагрева прибавлять технологическое время выдержки для протекания процессов фазовых превращений и гомогенизации:
τобщ = τнагр.пов+ τпрогр+ τтехн.
Теоретические расчеты показывают, что время аустенитизации для углеродистых сталей составляет всего лишь несколько секунд. Необходимость более длительных выдержек по сравнению с рассчитанными объясняется недостаточной точностью расчета времени нагрева. Поэтому нагрев изделий в какой-то степени гарантируется избыточным временем технологической выдержки.
1.Рекомендуемое технологическое время τтехн для углеродистых сталей 10–20 мин.
2.Время технологической выдержки при закалке, нормализации и отжиге изделий из легированных сталей для массивных изделий можно принимать от 20 мин до 1 ч и более, для тонких тел – от 2 до 20 мин в зависимости от степени легирования.
3.При отпуске углеродистых и низколегированных сталей время технологической выдержки принимают от 20 мин до 1 ч.
4.При термообработке цветных сплавов время технологической выдержки находят по справочным данным, конкретно для каждого сплава.
5.При гомогенизирующем отжиге легированных сталей время гомогенизации назначают от 4 до 10 ч.
6.Выдержку при химико-термической обработке определяют в зависимости от её вида, требуемой глубины слоя, способа обработки, температуры процесса и некоторых дру-
87
гих факторов. Необходимые данные имеются в справочной литературе.
3.3.1. Формирование садки
Для обеспечения качества термической обработки важно правильно разместить детали в печи, обеспечив хороший подвод тепла к нагреваемым поверхностям (активная поверхность детали). В зависимости от условий подвода тепла нагрев может быть односторонним или двухсторонним, и при расчете времени нагрева садка может быть принята как пластина определенной толщины или цилиндр соответствующего диаметра.
В табл. 3.1 приведены примеры расположения деталей на поду печи или на поддоне и соответствующий этому расположению вид тела при расчетах. Размещение мелких деталей на поддонах используют в камерных и толкательных печах, крупные тяжелые детали укладывают непосредственно на под печи. В печах конвейерных, с пульсирующим подом детали обрабатываются без приспособлений с загрузкой в одну, две толщины детали, и нагрев, как правило, считается двухсторонним, т.е. в расчет берется половина толщины или радиус изделия.
При формировании садки необходимо учитывать и условия последующего охлаждения деталей, особенно при закалке; необходимо сопоставить условия отвода тепла от детали и прокаливаемость стали. Например, при поштучном охлаждении длинномерных цилиндрических деталей обеспечивается интенсивное равномерное охлаждение каждой детали. Если же такие детали собраны в пучок, то охлаждение внутренних деталей оказывается замедленным и скорость их охлаждения может не обеспечить сквозной прокаливаемости детали.
При нагреве сложной неоднородной садки, например изделия с воздушной прослойкой, детали в твердом карбюризаторе (цементационные ящики) и т.д., необходимо учитывать
88
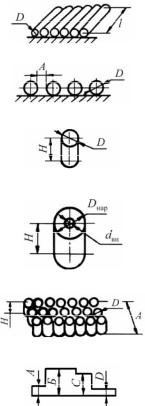
Таблица 3.1
Расположение деталей на поду печи и вид тела при расчетах
|
|
|
|
|
|
|
Значение |
|
||||
Нагреваемые |
Соотношение |
|
толщины, |
Вид тела |
||||||||
подставляемое |
при |
|||||||||||
изделия |
размеров |
в формулу |
расчетах |
|||||||||
|
|
|
|
|
|
|||||||
|
|
|
|
|
|
критерия Bi |
|
|||||
|
l > 2D |
|
|
D |
Пластина |
|||||||
|
|
|
|
|
|
|
|
|
|
|
|
|
|
l < 2D |
|
|
l |
Пластина |
|||||||
|
|
|
|
|
|
|
||||||
|
2 |
|
|
|
||||||||
|
|
|
|
|
|
|
|
|
|
|||
|
|
A > R |
|
|
R |
Цилиндр |
||||||
|
|
|
|
|
|
|
|
|
|
|
|
|
|
|
A < R |
|
|
D |
Пластина |
||||||
|
|
|
|
|
|
|
|
|
|
|
|
|
|
H > |
D |
|
|
R |
Цилиндр |
||||||
|
2 |
|
|
|
|
|||||||
|
|
|
|
|
|
|
|
|
|
|
|
|
|
H < |
D |
|
|
H |
Пластина |
||||||
|
2 |
|
|
|||||||||
|
|
|
|
|
|
|
|
|
|
|
|
|
|
H > |
Dнар −dвн |
|
|
Dнар −dвн |
|
Цилиндр |
|||||
|
|
|
|
2 |
|
|
|
|||||
|
|
|
2 |
|
|
|
|
|
|
|||
|
|
|
|
|
|
|
||||||
|
H > |
А |
|
|
|
А |
|
Пластина |
||||
|
2 |
|
|
2 |
|
|
|
|||||
|
|
|
|
|
|
|
|
|
||||
|
H < |
А |
|
|
H |
|
||||||
|
2 |
|
|
|
|
|
||||||
|
|
|
|
|
|
|
|
|
|
|
|
|
|
Б > С > A > D |
|
|
Б |
Пластина |
|||||||
|
|
|
|
|
|
|
|
|
|
|
|
|
89
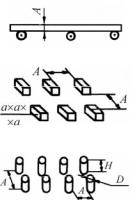
Окончание табл. 3.1
|
|
|
|
|
|
|
|
Значение |
|
||
Нагреваемые |
Соотношение |
толщины, |
Вид тела |
||||||||
подставляемое |
при |
||||||||||
изделия |
размеров |
в формулу |
расчетах |
||||||||
|
|
|
|
|
|
|
|
||||
|
|
|
|
|
|
|
|
критерия Bi |
|
||
|
|
|
|
|
|
|
|
|
А |
|
Пластина |
|
|
|
|
|
|
|
|
2 |
|
||
|
|
|
|
|
|
|
|
|
|
||
|
|
|
|
|
|
|
|
|
A |
Пластина |
|
|
|
|
|
|
|
|
|
|
|
|
|
|
А > |
a |
|
|
|
a |
|
Пластина |
|||
|
|
|
2 |
|
|||||||
|
|
2 |
|
|
|
|
|
||||
|
А< |
a |
|
|
|
|
a |
Пластина |
|||
|
|
|
|||||||||
|
|
2 |
|
|
|
|
|
|
|
||
|
А > |
D |
|
R |
Цилиндр |
||||||
|
2 |
|
|
|
|
||||||
|
|
|
|
|
|
|
|
|
|||
|
А< |
|
D |
|
H |
Пластина |
|||||
|
2 |
|
|
|
|
||||||
|
|
|
|
|
|
|
|
|
неоднородность теплофизических свойств веществ и при расчетах определять эквивалентный коэффициент теплопроводности λэкв и температуропроводности аэкв.
Примеры таких загрузок и методики расчета времени нагрева их дана в разделе «Расчет времени нагрева неоднородных тел».
Расчет времени нагрева насыпных загрузок (в конвейерных, барабанных, карусельных печах) можно вести так же, как монолитных, но обязательно с учетом их насыпной плотности и эквивалентного коэффициента теплопроводности λэкв в соответствии с табл. 3.2
90