
книги / Технология термического производства. Способы наноструктурирования материалов
.pdfСтанок конструкции проф. В. П. Вологдина производит закалку всех шеек с одной установки вала, так как имеет столько разъемных индукторов, сколько шеек на валу. Верхние половины индукторов смонтированы на раме, которая при помощи гидравлических цилиндров откидывается на шарнирах в сторону. После установки подлежащего закалке коленчатого вала рама опускается и верхние полуиндукторы охватывают одновременно все шейки коленчатого вала. Нижние полуиндукторы при этом оттянуты пружинами вниз.
После включения станка нижние полуиндукторы поочередно поднимаются, соответственно обеспечивается поочередный нагрев шеек. Нагретые шейки охлаждаются водой через отверстия индукторов. Управление станком полностью автоматизировано, его производительность составляет от 15 до 20 коленчатых валов в час. Станок обслуживает один рабочий.
Наряду с закалкой, отжигом и отпуском индукционный нагрев находит применение для скоростной химико-терми- ческой обработки стальных деталей
На рис. 5.13 представлена конструкция двухручьевого агрегата для скоростной газовой цементации зубчатых колес с их последующей закалкой. Зубчатые колеса периодически закладывают стопой в загрузочные устройства 18, 19 – здесь первая цифра относится к первому ручью, вторая – ко второму. При очередном подъеме и опускании штоков гидроцилиндров 25, 26 лапки 20 загрузочных устройств пропускают нижние колеса на лапы 21, 22, закрепленные на крышках перемещаемых штоков гидроцилиндров 23, 24. Затем штоки цилиндров 23, 24 посредством штока гидроцилиндра 32 перемещаются влево. При этом крышки штоков цилиндров 23, 24 закрывают торцы коридоров загрузки 14, 15. После этого открываются дополнительные затворы 16, 17, которые поднимаются при помощи гидроцилиндров 30, 31. Дальнейшее продвижение зубчатых колес в коридорах загрузки до поло-
171
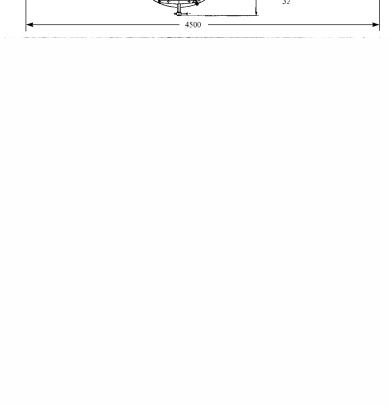
жения, соосно с индукторами 9, 10, производится штоками цилиндров 23, 24. Затем лапы 21, 22 штоков цилиндров 23, 24 перемещаются вправо и дополнительные затворы 16, 17 закрываются. Чтобы газ, оставшийся между основными и дополнительными затворами, не вышел в помещение при следующем цикле и попал в вытяжную трубу 29, предусмотрены специальные клапаны 27, 28. Таким образом, загрузочные коридоры агрегата перекрываются каждый двумя затворами. Это обеспечивает постоянное давление газа в агрегате при загрузке зубчатых колес в индукторы.
Рис. 5.13. Агрегат для газовой цементации зубчатых колес с индукционным нагревом и последующей закалкой
172
Агрегат имеет два многовитковых индуктора, которые изготовлены из медной трубки прямоугольного профиля, охлаждаемой водой. Изнутри индукторы футерованы керамическими гильзами, изолирующими их от теплового излучения нагретых деталей. Съем зубчатых колес, прошедших цементацию, осуществляется при помощи двух специальных лап 11, 12, перемещаемых штоком гидроцилиндра 13. Подстуженные до необходимой температуры зубчатые колеса попадают на опорные площадки штока 8 пневмоцилиндра 7 и опускаются им в закалочный бак 6. Применение в данном случае пневмоцилиндра связано с необходимостью быстрого погружения зубчатых колес в закалочную среду. В закалочном баке зубчатые колеса перемещаются при помощи толкателя 33 с гидроцилиндром 3. Выдача закаленных колес производится штоками гидроцилиндров 1, 2 через разгрузочные устройства 4, 5. Для питания индукторов агрегата применяют два генератора с частотой 2500 Гц мощностью 50–100 кВт каждый в зависимости от размеров деталей и производительности агрегата. Температура нагрева деталей 1060–1080 °С. Контроль температуры осуществляют с помощью фотоэлектрических пирометров. Производительность агрегата 200–
300кг/ч.
5.6.Технология поверхностной индукционной закалки
Основное назначение такой закалки – повышение твердости и износостойкости деталей, повышение усталостной прочности. Основным фактором, обеспечивающим повышение прочности стали, закаленной после скоростного индукционного нагрева, является измельчение зерна аустенита [1, 28, 31, 32]. Получению мелкого зерна способствует также применение мелкодисперсных исходных структур стали
(табл. 5.7).
173
Таблица 5.7
Типичные размеры зерна аустенита для различных видов нагрева и исходной структуры стали
|
|
|
Тип стали и исходной |
|
|
Зерно |
||
Характер нагрева |
|
|
|
|
||||
|
|
Средняя пло- |
||||||
|
|
|
|
структуры |
|
Балл |
||
|
|
|
|
|
|
|
щадь, мкм2 |
|
|
|
|
|
Нагрев в печи |
|
|
||
|
|
|
|
|
|
|||
До температур |
Доэвтектоидная сталь |
|
|
|
||||
в нормализованном или |
|
5–6 |
4000–2000 |
|||||
перегрева |
|
|||||||
улучшенном состоянии |
|
|
|
|||||
|
|
|
|
|
||||
|
|
|
|
|
|
|
||
|
|
Доэвтектоидная сталь |
|
|
|
|||
|
|
в нормализованном или |
|
7–8 |
1500 |
|||
До оптимальных |
улучшенном состоянии |
|
|
|
||||
температур |
Заэвтектоидная сталь |
|
|
|
||||
|
|
в состоянии зернистого |
|
9–10 |
250–125 |
|||
|
|
перлита |
|
|
|
|
||
|
|
|
|
|
|
|||
|
Индукционный нагрев до оптимальных температур |
|||||||
|
|
|
со скоростью v* , °C/с |
|
|
|||
|
|
|
|
|
ф |
|
|
|
|
|
|
Доэвтектоидная, эвтек- |
|
|
|
||
v* |
|
|
тоидная, |
заэвтектоид- |
|
|
|
|
> 100 |
|
ная |
стали |
с улучшен- |
|
14–15 |
8–4 |
|
ф |
|
|
ной |
или |
закаленной |
|
|
|
|
|
|
|
|
|
|||
|
|
|
исходной структурой |
|
|
|
||
|
|
|
|
|
|
|
||
* |
= 2 – 100 |
|
Доэвтектоидная, эвтек- |
|
|
|
||
vф |
|
тоидная, |
заэвтектоид- |
|
|
|
||
|
|
|
|
|
|
|||
|
|
|
ная стали с улучшен- |
11–12 |
60–30 |
|||
|
|
|
ной |
или |
закаленной |
|
|
|
|
|
|
исходной структурой |
|
|
|
||
|
|
|
|
|
|
|
|
|
* vф – средняя скорость нагрева в области фазовых превраще-
ний.
Нормализованная структура доэвтектоидной стали позволяет получить при индукционном нагреве зерно аустенита
174
11–12-го номера (при печном нагреве 7–8-й номер), применение индукционного нагрева со скоростью нагрева в области фазовых превращений vф > 100 °С/c для улучшенной стали обеспечивают сверхмелкое зерно 14–15 номеров. Рекомендуемые скорости нагрева и соответственно удельные мощности нагрева в зависимости от глубины слоя даны в табл. 5.8.
Таблица 5.8
Ориентировочные значения скорости нагрева и удельной мощности, необходимые для достижения
разных глубин изделия
Глубина |
Скорость нагрева |
Удельная мощ- |
|
в области фазовых |
|||
нагрева, мм |
ность, кВт/см2 |
||
|
превращений |
|
|
1–2 |
100–300 |
0,8–1,5 |
|
3–5 |
20–80 |
0,5–1,3 |
|
6–10 |
2–15 |
0,05–0,2 |
|
|
|
|
Примечание. Для глубины 1–2 мм меньшие значения удельной мощности соответствуют радиочастоте, большие – средней частоте.
По выбранной удельной мощности выбирают мощность генератора и питающей сети (табл. 5.9).
Поверхностную закалку применяют, как правило, для деталей из среднеуглеродистых сталей 45, 40Х, 45Г2, 40ХН, 40ХГРТ и 40ХНМА. Схема распределения структур и твердостей, получаемых в результате закалки, дана на рис 5.14.
175
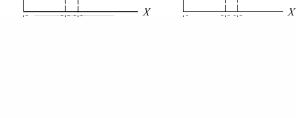
Таблица 5.9 Выбор мощности преобразователя частоты и питающей сети
|
|
|
Мощность, кВт |
|
|
|||
|
|
потребляемая от преоб- |
потребляемая |
|||||
|
пере- |
разователя частоты |
от питающей сети |
|||||
Тип |
Лам- |
Машин- |
Тири- |
Лам- |
Машин- |
Тири- |
||
дава- |
||||||||
установки |
емая |
повый |
ный ге- |
стор- |
повый |
ный ге- |
стор- |
|
|
в де- |
гене- |
нератор |
ный |
гене- |
нератор |
ный |
|
|
таль |
ратор |
|
преоб- |
ратор |
|
преоб- |
|
|
|
|
|
разова- |
|
|
разова- |
|
|
|
|
|
тель |
|
|
тель |
|
Без пони- |
|
|
|
|
|
|
|
|
жающего |
р0·S |
– |
1,45р0·S |
1,45р0·S |
– |
2,05р0·S |
1,6р0·S |
|
трансфор- |
|
|
|
|
|
|
|
|
матора |
|
|
|
|
|
|
|
|
С понижа- |
|
|
|
|
|
|
|
|
ющим |
р0·S |
1,7р0·S |
1,7р0·S |
1,7р0·S |
3,4р0·S |
2,4р0·S |
1,9р0·S |
|
трансфор- |
||||||||
матором |
|
|
|
|
|
|
|
Примечание:
1.Значение удельной мощности р0 (кВт/см2) выбирается по данным табл. 5.3, 5.4 и рис. 5.16.
2.S – поверхность нагрева в см2.
аб
Рис. 5.14. Схема распределения температур при нагреве под закалку, структур и твердости сечении образца из доэвтектоидной стали, подвергаемой поверхностной закалке при поверхностном нагреве (Х – расстояние от поверхности); а – распределение температуры
иструктур; б – распределение твердости и структур; I – мартенсит; II – мартенсит + феррит; III – феррит + перлит
176
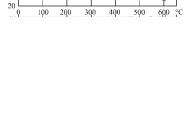
Как видно из рис. 5.14 твердость по сечению поверх- ностно-закаленного изделия соответствует распределению структур. Поверхностная твердость после закалки составляет обычно 60–65 HRC и несколько снижается при последующем низком отпуске. Характер изменения твердости при отпуске поверхностно закаленной стали можно видеть на примере стали 45 (рис 5.15).
Рис. 5.15. Зависимость твердости поверхности поверхностнозакаленной стали 45 от температуры отпуска и самоотпуска: 1 – самоотпуск 30 с; 2 – отпуск
в печи 1,5 ч
Применение самоотпуска (120–150 °С) практически сохраняет твердость на уровне 60–62 HRC и в то же время уменьшает возможность появления трещин при интенсивном охлаждении при закалке, поэтому для сталей типа 40ХНМА рекомендуют применять закалку с самоотпуском [1, 28, 32].
При контроле качества поверхностной закалки одного контроля твердости мало, так как этот контроль не позволяет установить перегрев, неравномерность и неоднородность структуры слоя.
Обязательным поэтому при текущем контроле и особенно при разработки режимов поверхностной закалки является применение металлографического анализа.
Время индукционного нагрева при выбранной неизменной частоте зависит как от температуры нагрева, так и от удельной мощности. На рис. 5.16 приведена номограмма, позволяющая выбрать время и удельную мощность.
Охлаждение при поверхностной закалке должно обеспечивать качество закалки, минимальный разрыв во времени между окончанием индукционного нагрева и началом охлаждения, достаточную равномерность и скорость. При закалке
177
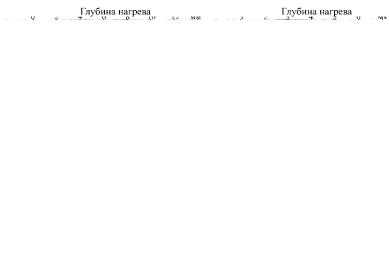
|
|
|
|
|
|
|
|
|
|
|
|
|
|
|
|
|
|
|
|
|
|
|
|
|
|
|
|
а |
б |
Рис. 5.16. Графики для ориентировочного выбора удельной мощности и времени нагрева в зависимости от необходимой глубины нагрева и температуры поверхности, υ0, стали: а – частота тока 10 кГц;
б– частота тока 4 кГц
ссамоотпуском необходимо строго дозированное охлаждение.
Лучше всего этим условиям отвечает охлаждение водой, движущейся относительно поверхности закаливаемой детали со скоростью 10–30 м/с [1, 28, 32]. Наиболее технологически удобный и дешевый вариант охлаждения – это спрейерное
охлаждение. Рекомендуется изготавливать спрейеры с отверстиями в количестве 4–6 отверстий на 1 см2 охлаждаемой поверхности, диаметром 2 мм. Зазор между спрейером и по-
верхностью охлаждения 5–15 мм, расход воды при этом должен быть не менее 0,5 м3/(с·м2).
Внастоящее время для деталей сложной конфигурации (с отверстиями, шпоночными канавками, резкими перехода-
178
ми сечений) возможно применение водных растворов органических и неорганических соединений, например, полиакриламида. Однако такое охлаждение менее технологично с точки зрения ухода за спрейерами (засорение спрейера может привести к некачественной закалке).
Охлаждение путем погружения в воду приводит к неравномерности температур в разных сечениях и, следовательно, к большим тепловым напряжениям и трещинам.
5.7. Приближенные расчеты параметров индукционного нагрева при поверхностной закалке
Расчет индукционной установки для поверхностного нагрева включает в первую очередь расчет индуктора, который состоит из двух частей: теплового расчета и электрического расчета.
Исходные данные для расчета: эскиз детали с указанием поверхностей, требующих упрочнения, и требуемой глубины хк упрочненного слоя; марка стали.
Расчетные параметры: оптимальная частота тока, f, Гц; время нагрева, τ, с; требуемая удельная мощность, Р0, кВт/см2. Конечная температура нагрева при расчетах 900 °С. При небольшой закаливаемой площади (не более 300 см2) рассчитывают способ одновременного нагрева; при больших площадях – способ непрерывно-последовательного нагрева, при котором скорость движения индуктора или детали принимают постоянной. Эта скорость должна быть не менее 0,5 мм/с. В противном случае будет велик промежуток времени между концом нагрева и началом охлаждения, что приведет к частичному диффузионному распаду аустенита и, следовательно, к снижению качества закаленного слоя.
Выбор частоты и соответственно выбор генератора описан в разд. 5.2 и 5.4.
179
Ориентировочно значения времени нагрева и удельных мощностей в зависимости от требуемой глубины слоя, диаметра и частоты можно определить из соответствующих графиков (рис. 5.17–5.22), минуя довольно сложные тепловые расчеты. Графики построены по результатам этих расчетов и многократно подтверждены промышленной обработкой деталей с использованием параметров, определенных по данным графикам.
Тепловой расчет при высоких частотах произведен в предположении, что горячая глубина проникновения тока равна нулю. Это не внесет существенной ошибки при глубинах закаленного слоя больше 1 мм при частотах 250–440 кГц, так как прогрев на указанные и большие глубины происходит при этих частотах главным образом за счет теплопроводности.
При средних частотах (2500–10000 Гц) в расчетах учтена глубина активного слоя. Металл считается двухслойным. Первый слой равен требуемой глубине прогрева хк и является немагнитным. За пределами этого слоя при х > хк сталь ферромагнитна. Средняя величина относительной магнитной проницаемости принята равной 16.
Все расчеты проделаны для конструкционных углеродистых и слаболегированных сталей при температуре поверхности Т = 900 °С.
При других температурах поверхности значения времени нагрева и удельной мощности могут сильно отличаться от приведенных на графиках рис 5.18 и 5.19. Ориентировочно можно принять, что отклонение температуры поверхности на ±50 °С от исходного значения 900 °С приводит к изменению времени нагрева примерно в 1,7 раза в обратном направлении и удельной мощности примерно в 1,5 раза в прямом направлении по отношению к величинам, найденным из графиков.
180