
книги / Термическая обработка и волочение высокопрочной проволоки
..pdfкарбидных фаз [16]. Поэтому увеличение концентрации углерода ускоряет процесс образования аустенита.
Вновь образованные зерна аустенита в пределах одного зер на неоднородны по своему составу. В тех участках, где распола гались цементитные составляющие, содержание углерода выше, нежели в участках, где находились ферритные составляющие. Повышение температуры нагрева приводит к выравниванию состава аустенитного зерна, так как при этом диффузионные процессы протекают более интенсивно.
В наследственно крупнозернистой стали рост зерна аустени та начинается еще при температуре, несколько превышающей точку Ас\. В наследственно мелкозернистой же стали он начи нается лишь при достижении температур 900—950 °С. С повы шением температуры зерно аустенита в наследственно мелко зернистой стали растет довольно интенсивно. При температуре выше 1000 °С эта сталь имеет, как правило, более крупное зер но аустенита, чем наследственно крупнозернистая.
Значение влияния размера перлитного зерна заключается не только в том, что он предопределяет ход перлитного пре вращения во время последующего охлаждения, но и в том, что от него зависит величина зерна стали в перлитном состоянии и, в частности, после патентирования. При производстве стальной проволоки это далеко не безразлично.
Исследования А. Помпа [7] и Альтпетера [17] привели к вы воду, что температура нагрева при патентировании должна быть на 20—30 °С выше точки Ас3, т. е. сталь должна иметь мелко зернистое строение.
Работа А. Помпа и Линдеберга позволила сделать вывод о целесообразности нагрева проволоки при патентировании до температур, лежащих значительно выше верхней критической точки [18].
Многие исследователи (19—23] считают, что перегревать про волоку следует для того, чтобы получать крупнозернистое строение стали, позволяющее производить высокую степень де формаций без обрывов, чего не может обеспечить металл, имею щий мелкозернистое строение,
В. Я- Зубовым установлено положительное влияние повыше ния температуры нагрева с 810 до 950 °С на технологические ха рактеристики протянутой .проволоки (числа перегибов и скручи ваний) особенно для стали, склонной к росту зерна при пере греве [10]. Исследование проводилось на стали, содержащей 0,53% С.
Из опытов автора (рис. 1), проведенных на заводе «Серп и молот» в 1948 г., следует, что повышение температуры нагрева от 900 до 1020°С увеличивает числа перегибов и окручиваний протянутой проволоки, т. е. подтверждаются результаты, полу ченные другими исследователями.
И
Положительное влияние повышенных температур нагрева на качество стальной проволоки объясняется в настоящее время, во-первых, тем, что такие температуры способствуют наиболее полному растворению карбидов, диффузии углерода в аустените и росту зерна; а во-вторых, потому, что благодаря получению крупнозернистой стали после патентирования образуется в про тянутой проволоке длинноволокнистая текстура, способствующая получению повышенных чисел .перегибов и скручиваний.
Диаметр пробопоки,мм
Рнс. 1. Влияние температуры нагрева при патентировании в свинцовой ванне с температурой 450 °С на изменение чисел перегибов и скручива ний проволоки после волочения:
/— 900 °С: 2 — 1020 °С
Врекомендациях по выбору температуры нагрева при патен-
тировании иногда не учитывают содержание углерода в стали и диаметр проволоки. На большинстве заводов меняют темпе ратуру нагрева, повышая ее в большей или меньшей степени при уменьшении содержания углерода и увеличении диаметра проволоки.
С уменьшением содержания углерода следует повышать тем пературу /напрева, так как в этом случае, во-первых, уменьшает ся скорость превращения перлита «в* аустенит, во-вторых,
повышается температура |
окончания превращения Fe« в FeT |
(в доэвтектошшых сталях) |
и, в-третьих, снижается склонность |
стали к обезуглероживанию и окислению.
При увеличении диаметра проволоки также необходимо по вышать температуру нагрева, так как это улучшает свойства
проволоки после волочения и, как будет показано ниже, создает предпосылки для повышения скорости патентирования.
Кроме того, при этом снижаются относительные потери ме талла на угар.
Учитывая опыт работы отдельных заводов и результаты ряда исследований, определение температуры нагрева при патентированэти проволоки диам. 6,0 мм и тоньше можно производить
по формуле |
|
tu= 900 — 50С + 10D, |
(1) |
где tu— минимальная температура нагрева |
проволоки, °С; |
С — содержание углерода в стали, %; |
(заготовки), мм. |
D —диаметр патентируемой проволоки |
Рис. 2. Минимальные тем пературы нагрева металла при 1патентированн1и, -рассчи
танные по формуле (1), з зависимости от диаметра проволоки и содержания в стали углерода
0J 0А 05 0.6 0.7 0,6 0.9 Ш
Подержана? углерода, %
Температуры нагрева проволоки, рассчитанные по формуле (1), представлены в виде графика на рис. 2.
3. ВРЕМЯ ПРЕБЫВАНИЯ ПРОВОЛОКИ В ПЕЧИ В ПРОЦЕССЕ ПАТЕНТИРОВАНИЯ
Даже в том случае, если температура нагрева достаточна, нельзя быть уверенным, что процессы, связанные с превраще нием Fea в FeT, совершаются в полной мере. Эти процесы зави сят также от продолжительности пребывания проволоки в печи при заданной температуре и техиолгии нагрева (распределение температур по длине печи).
Время пребывания проволоки в печи на заводах увеличивают с увеличением диаметра проволоки. Для проволоки ряда диа метров длительность пребывания в печи имеет значительные колебания. Так, например, для проволоки диам. 5,0 мм она сосоставляет от 140 до 550 сек.
Учитывая передовой опыт заводов, минимальную продолжи тельность Тмин, сек., пребывания проволоки из углеродистой ста ли в проходной печи, отапливаемой мазутом или электрически ми спиралями, можно определить по формулам:
при диам. до 5,0 мм
тмни = 30 + 5D2; |
(2) |
при диам. более 5,0 мм |
|
*.™ = з о + Ц £ о « . |
(3) |
На рис. 3 указана в виде кривых длительность нагрева, при меняемая на отдельных заводах и рекомендуемая по формулам
(2) и (3).
700 |
|
|
|
|
|
1— __ ___ |
|
|
|
|
|
||
600 |
|
|
|
|
|
|
|
|
|
|
|||
500 |
|
|
|
|
|
f |
|
/ |
|
|
|
|
|
|
|
|
Ч |
|
|
* > |
|
|
|
|
|
||
* 400 |
|
|
|
/ |
|
Рис. |
3. Длительность пребыва |
||||||
'2S |
|
|
|
/ |
|
/ |
ния |
проволоки |
в мазутной |
и |
|||
1' 300 |
|
|
/ |
|
' У 'У |
электрической патентнровочной |
|||||||
43 200 |
/ |
/ |
|
|
|
|
|
печи: |
|
|
|||
|
|
|
|
! — принятое |
на |
заводах; 2 |
— ре |
||||||
100 |
у 4 |
|
|
|
|
|
|
комендуемое |
по |
формулам |
(2) |
и |
|
|
|
|
|
|
|
|
|
13) |
|
|
|
||
О |
3 |
4 |
|
|
5 |
6 |
8 |
9 |
|
|
|
|
|
|
|
|
|
|
|
|
|
Диамет р,мм
Для определения времени пребывания проволоки в анало гичных печах имеются формулы и других авторов [24]:
тмнн = (0>8 + 0,18D2) 60; |
(4) |
S,UH = 63{2T - I ! |
(5) |
Последние две формулы отражают опыт работы Белорецкого сталепроволочно-канатного завода.
4. ОХЛАЖДАЮЩАЯ СРЕДА И ВЛИЯНИЕ ЕЕ ТЕМПЕРАТУРЫ НА СВОЙСТВА ПРОВОЛОКИ
В районе температур Аг\ распад аустенита носит кристалли зационный характер. Структуры перлитного типа (перлит, сор бит, троостит) получаются в результате зарождения центров кристаллизации и их роста. При распаде нелегированного аустенита механизм процесса превращения заключается в пере распределении углерода. Такое перераспределение представ ляет собой процесс диффузии углерода. Вместо равномерно распределенного углерода по объему исходной фазы аустенита
14
получаются зоны с высокой концентрацией (цементит) и малой концентрацией (феррит) углерода.
Количественной характеристикой перлитного образования может быть расстояние между пластинками перлита, которое при прочих равных условиях зависит лишь от температуры изотермического превращения, что доказано экспериментально.
По мере снижения температуры перлитного превращения по вышаются прочностные характеристики металла, так как, с одной стороны, уменьшается количество избыточной фазы — феррита (в доэвтектоидных сталях), а с другой — повышается дисперсность феррито-цементитной смеси, т. е. происходит уве личение поверхности раздела фаз.
Доказано, что твердость пластинчатых структур линейно связана с величиной поверхности раздела феррито-цементитных фаз.
В нижнем районе субкритических температур превращение аустенита происходит по мартенситному типу. MapTencnTHoes превращение совершается без изменения состава фаз и является бездиффузионным процессом. Каждый отдельный кристаллик мартенсита образуется практически мгновенно. Увеличение ко личества мартенсита как при изотермической выдержке, так и при .понижении температуры охлаждаемого металла происхо дит благодаря образованию новых кристалликов мартенсита, а не за счет роста уже имеющихся кристаллов. При температуре ниже 250—300 °С скорость диффузии углерода в железе стано вится -ничтожно малой, эвтектоидный распад аустенита делается практически невозможным, и единственным состоянием, конкури рующим с состоянием аустенита, будет мартенситное состояние.
По современным воззрениям, мартенсит представляет собой аллотропическую модификацию твердого раствора углерода в Fea, а -мартенситное-превращение — аллотропическое превраще ние, начинающееся при строго определенной температуре. , Мартенситное 'превращение -в углеродистой стали характери зуется резко выраженной ориентировкой кристаллической ре шетки вновь образовавшейся фазы по отношению к решетке ис
ходной фазы.
ГВ. Курдюмов пишет: «Мартенситное превращение состоит
взакономерной перестройке решетки, при которой атомы не об мениваются местами, а лишь смещаются друг относительно дру га на расстояния, не превышающие межатомные» [25]. При
обратном превращении атомы 'перемещаются по тем же .путям, что и при прямом мартенситном превращении, но в обратном на правлении.
Мартенситное превращение в процессе патентирования мо жет происходить лишь в случае завышенной скорости пате.нтирования, когда аустенит не успевает полностью распасться на сорбит в пределах ванны. Переохлажденный аустенит при нали-
чин необходимой скорости охлаждения может .превратиться в мартенсит.
В промежуточном интервале температур аустенит превраща ется в игольчатый троостит. Механизм этого превращения до настоящего времени остается полностью не выясненным. На основании работ В. Д. Садовского [26] и других исследователей можно’полагать, что ведущей фязой в этом процессе является феррит. В результате превращения аустенита в игольчатый тро остит получается феррито-карбидная смесь; при этом возникают игольчатые выделения ферритной фазы. В этом случае карбид ные частицы выпадают, по всей вероятности, в виде зерен.
«Верхний» игольчатый троостит, получаемый при небольших температурах данной зоны, непосредственно прилегающей к нижней области перлитного превращения, имеет перистое строе ние структуры. «Нижний» игольчатый троостит, образующийся вблизи мартенситной точки, имеет рёзко выраженное игольчатое строение, напоминающее мартенсит отпуска. Таким образом, структура превращения в промежуточной зоне сочетает в себе признаки перлита (феррито-карбидная смесь) и мартенсита (игольчатая форма ферритных выделений), а кинетика .процесса превращения аустенита в игольчатый троостит совмещает в себе характерные черты перлитного и мартенситного распада аусте нита.
Процесс патентирова.ния протекает в зоне температур пер литного превращения в довольно узком температурном интер вале 420—540 °С.
При патентировании в* качестве среды для превращения аус тенита очень долгое время применялся исключительно расплавленный свинец. Он имеет низкую точку плавления'и облада ет высокой теплопроводностью при температурах патеитирования.
Опыты использования солей -в качестве охлаждающей среды при патентировании проволоки впервые были проведены на од ном из отечественных заводов [27].
Вследствие дефицитности свинца в Германии в начале 40-х годов был поставлен вопрос о замене свинца менее дефицитны ми материалами.
В результате работы, проведенной Люегом и Помпом, были
предложены заменители |
свинца — расплавленные соли (селит |
ра) азотнокислого натрия |
(NaN03) и калия (KN03) и их смеси |
[28]. В годы войны заменители свинца нашли в Германии широ кое применение, тем не менее считалось, что они не могут обес печить в протянутой .проволоке равноценных со свинцом свойств. Поэтому иатентированию в расплавленных солях подвергали только передельную проволоку различных размеров и продук цию неответственных сортов. Пониженные свойства проволоки, латентированной в солях, объяснялись меньшей охлаждающей способностью солей по сравнению со свинцом.
Внашей стране впервые широкое практическое применение
раоплавленных солей в качестве среды для патентирования бы ло начато в 1948 г. на заводе «Красная Этна» во предложению А. И. Зотьева.
Работами ЦНИИЧМ, проведенными при участии автора, установлено, что' скорости охлаждения металла в натриевой и Алиевой селитре, в их смеси, в щелочи, а также в смеси щело чи с селитрами очень близки между собой; но в том случае, когда патентируемый металл и указанные расплавы не имеют относительного .перемещения, они несколько ниже, чем у свин ца *. При незначительном перемещении расплава и иатентируемого металла относительно друг друга скорость охлаждения в солях и щелочах приближается к скорости охлаждения овинца, а при увеличении скорости относительного перемещения рааплава и проволоки охлаждающая способность солей и щелочей может даже значительно превзойти охлаждающую способность свинца. Это наблюдается даже в том случае, когда свинец и патентируемый металл тоже перемещаются относительно друг друга с той же скоростью. При определенной рациональной ско рости перемешивания расплава свойства протянутой проволоки, прошедшей патентирование в солях и щелочах, равноценны, а
• иногда даже превосходят свойства проволоки, подвергнутой па- ^нтированию в свинце. При понижении температуры расплава гна 20—40 °С (в зависимости от размера патентируемой прово локи) по сравнению с температурой свинцовой ванны мож.но и "без перемешивания расплава обеспечить проволоке после воло чения (даже из высокоуглеродистых сталей) свойства, практи чески равноценные со свойствами проволоки, прошедшей патен- ^тироваиие в свинце
Увеличение скорости охлаждения при перемешивании рас плавов солей, щелочей и :их смесей объясняется тем, что охлаж дение в этих средах осуществляется главным образом за счет их теплоемкости. Теплоемкость этих сред при температурах патентироваиия более чем в 10 раз превосходит теплоемкость свинца. Естественно, что чем больше новых частиц расплава будет подходить в единицу времени к поверхности охлаждаемо го металла, тем интенсивнее будет охлаждение. В свинцовых же ваннах охлаждение осуществляется главным образом благодаря высокой теплопроводности свинца, которая почти в 100 раз превосходит теплопроводность солей и щелочей. Поэтому в свинцовых ваннах нельзя, достичь перемешиванием такой ско рости охлаждения, как в расплавах солей и щелочей.
В процессе патентирования в производственных условиях проволока под действием различных причин совершает некото
* В результате работы НИИМЕТИЗа [29] установлено, что охлаждение в свинце происходит быстрее и распад аустенита в свинцовых ваннах более изоте11>мичен, чем.® соли.
2 Заказ 990 |
17 |
рое колебательное движение. Кроме того, расплав солей и ще лочей циркулирует в ванне, двигаясь то ходу .проволоки, чего не наблюдается в свинцовых ваннах из-за значительного удельного веса свинца и малой его жидкотекучесгги.
Тот факт, что даже и без принудительного перемешивания расплава при незначительном изменении температуры .ванны в сторону понижения можно получить .свойства патентированной заготовки и протянутой из тее проволоки, очень близкие к свой ствам проволоки, прошедшей патентирование в свинце, объяс няется циркуляцией расплава.
Процесс превращения переохлажденного аустенита в распла ве солей и щелочей принципиально не отличается от превраще ния в свинце.
Характер микроструктуры патентированной проволоки оп ределяется скоростью охлаждения, устойчивостью аустенита (ин кубационным периодом) и температурой охлаждающей среды.
A. Помп пришел к заключению, что для получения хороших чисел перегибов и скручиваний проволоки после волочения про цесс патентирования необходимо вести при низкой температуре ванны [30].
B. Я. Зубов [10] получил повышенные значения чисел пере-* гибов и пониженные значения чисел скручиваний протянутой проволоки (при различных значениях суммарных обжатий) по мере понижения температуры охлаждающей ванны.
Аналогичные результаты получил Годфрей [31]. Исследова ние выполнено им на сталях с повышенным содержанием угле-., рода при трех температурах свинцовой ванны: 480, 540 и 590 °С. ‘ Проволока после волочения, прошедшая до этого в заготовке патентирование при 480° С, имела самые высокие значения чисел перегибов. Самые низкие числа перегибов были три температуре ванны 590 °С. Наиболее высоким сопротивлением кручению об ладала проволока, подвергнутая патентироваиию при темпера туре ванны 590 °С, а самым -низким—при температуре 480 °С. Проволока из стали с содержанием углерода 0,8%, протянутая из патентированной заготовки при указанных выше температубов и большие числа скручиваний, чем проволока, полученная из патентированной заготовки при указанных выше температу
рах ванны.
В работе ЦНИИЧМ, проведенной при участии автора, иссле довалось влияние изменения предела прочности патентированных заготовок на свойства получаемой из них проволоки из ста лей пяти марок, содержащих 0,39% С; 0,56% С; 0,63% С; 0,70% С и 0,83% С. Каждую из указанных сталей протягивали на заго товку 4,9 и 3,9 мм и патентировали при постоянной температуре расплава (80% NaOH; 20% NaN03) и различной интенсивности перемешивания его с помощью мешалки. Патентирование про изводили в производственных условиях. При этом установлено, что по мере повышения предела прочности патентированной за
готовки до определенных значений у каждой из указанных ста лей происходило повышение числа перегибов 'протянутой прово локи с одновременным понижением числа скручиваний. Эти ре зультаты подтверждены на больших производственных партиях сталей различных ма<рок и диаметров.
Таким образом, по результатам большинства работ можно считать установленным, что понижение температуры ванны до' определенных значений дает лучшие результаты при испытании протянутой проволоки на перегиб, а повышение температуры ванны — лучшие результаты при испытании на окручивание.
Папсдорф [32] указывает, что максимальное значение скоро сти перлитного превращения смещается с повышением содержа ния углерода в сторону более низких температур, поэтому тем пературу ванны при патентировании проволоки о содержанием углерода 0,4% необходимо поддерживать на 50 °С выше, чем для стальной проволоки таких же размеров, но с содержанием углерода 0,9%.
Рекомендации Папсдорфа, по нашему мнению, ошибочны. Известно, чго в ореднеуглеродистой стали, особенно в проволо ке толстых и средних размеров, даже при понижении температу ры охлаждающей среды не удается получить структуру с таким же равномерным распределением феррита и цементита, как в высокоуглеродистых сталях. Ниже будет показано, что механи ческие свойства протянутой проволоки зависят прежде всего от величины цементитных образований, их формы, размещения в феррите и формоизменения в процессе деформации. Для полу чения равномерной структуры в среднеуглеродистой стали патентирование необходимо проводить при пониженных температу рах ванны, а не при повышенных, как это рекомендует Папсдорф.
Не менее ошибочны, по нашему мнению, и рекомендации А. И. Зотьева [33], который считает, что температура ванны не зависимо от охлаждающей среды должна отвечать интервалу образования так называемого «верхнего бейнита» (425 —550 °С) А. И. Зотьев приходит к выводу, что изменение температуры охлаждающей среды в этом интервале не влияет на изменение предела прочности патентированной заготовки. Однако практи ка работы заводов опровергает такое заключение.
При одинаковом содержании углерода и нормальных режи мах патентирования в патентированной заготовке тонкого раз мера предел прочности при растяжении всегда выше, чем в тол стом. По этому принципу построены и нормативные таблицы для разбраковки патентированной заготовки на заводах. С повыше нием температуры охлаждающей среды происходит падение пре дела прочности (табл. 2).
В литературе имеются данные, указывающие, что в стали, содержащей 1,0%С и 1,9% Мп, при снижении температуры охлаждающей среды с 550 до 450 °С происходит даже падение
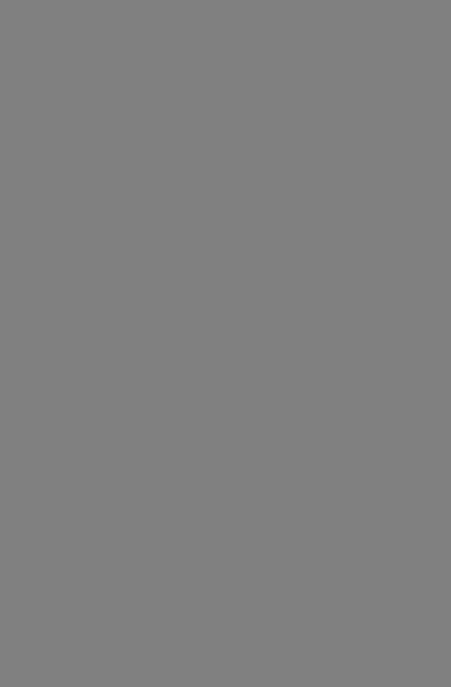