
книги / Термическая обработка и волочение высокопрочной проволоки
..pdfРежим патентирования проволоки диам. 1,8 мм из стали У9А (0,92% С)
|
|
Темпера!ура, °С |
|
|
|
|
||
надмуфельного |
пространства |
проволоки по |
свинцовой |
|
Скорость |
|||
|
по зонам |
|
патентнро- |
|||||
1 |
|
2 |
|
выходе из печи |
ванны |
вания, м/мин |
||
|
|
|
|
|
|
|
||
1200 |
1240 |
|
980 |
|
500 |
|
7,8 |
|
|
|
|
|
|
|
|
Т а б л и ц а 9 |
|
Режим патентирования проволоки диам. |
1,8 мм из стали У9А (0,94%С) |
|||||||
|
и диам. 1,4 мм из стали У12А (1,15%С и 1,17%С) |
|
||||||
|
|
|
Температура, °С |
|
|
|
|
|
|
|
по зонам печи |
|
|
|
|
Скорость |
|
1 |
|
2 |
|
|
|
|
|
|
|
|
3 |
|
проволоки |
соляной |
патенти |
||
|
|
|
|
|
|
по выходе |
рования |
|
над му |
муфеля |
над му |
муфеля |
над му |
муфеля |
из печи |
ванны |
м/мин |
фелем |
фелем |
фелем |
|
|
|
|||
1090 |
1020 |
1120 |
1060 |
1235 |
1140 |
970 |
490 |
9 |
Далее производилось волочение патентированных заготовок на проволоку диам. 0,3 мм на сухой мыльной смазке с частными обжатиями около 10%.
В табл. 10 приведены результаты испытаний патентирован ных заготовок и проволоки после волочения.
При испытании протянутой проволоки, кроме предела проч
ности, |
определяли также |
отношение разрушающего |
усилия с |
||||
узлом |
(Ру3) к разрушающему усилию без узла (Р). |
|
|||||
|
|
|
|
|
|
Т а б л и ц а 10 |
|
|
|
Механические |
свойства патентированной заготовки |
|
|||
|
|
и полученной из |
нее проволоки диам. |
0.3 мм |
|
||
|
|
|
Патентированная заготовка |
Проволока диам. 0,3 мм |
|||
Марка стали |
Содержание |
|
|
|
|
|
|
углерода, % |
диаметр, мм |
, кг/мм* |
оь, кг/мм* |
% |
|||
|
|
|
|
|
|
|
Р |
У9А |
|
0,92 |
1,8 |
139-7-142 |
346-г 374 |
55-т-59 |
|
У9А |
|
0,94 |
1,8 |
138-И 40 |
365 т 372 |
57—59 |
|
У12А |
1,15 |
1,4 |
170-Ь172 |
380 1-391 |
56-Т-59 |
||
У12А |
1,17 |
1,4 |
173-г 174 |
373-г 382 |
55-7-58 |
В табл. 11 приведены механические свойства промышленной партии проволоки диам. 0,3 мм, (изготовленной на одном из за водов из стали с высоким содержанием углерода. Патентирование заготовки производили на печи длиной 16 м. Режим патентирования был близким к приведенному в табл. 9.
Т а б л и ц а 11
Механические |
свойства партии |
проволоки диам. |
0,3 |
мм |
|
|
№ бунта |
|
|
|
Число скручиваний |
||
к г / м м 2 |
■ ^ 1 . % |
при |
длине образца |
|||
|
|
|
P |
|
50 м м |
|
1 |
348 4- 349 |
58-*-59 |
|
60 4 |
-71 |
|
2 |
351 4- 353 |
5 5 -b 58 |
|
50 4 |
-58 |
|
3 |
346 - - |
354 |
56-*-59 |
|
44 4 -6 8 |
|
4 |
344 |
345 |
56 -*- 58 |
|
58 4-71 |
|
5 |
365 4 - 370 |
56 ч - 59 |
|
43 4 -6 0 |
||
6 |
354 |
365 |
55 -4- 57 |
|
54 4-67 |
|
7 |
365 4 - 370 |
58 4 -5 9 |
|
60 4 |
-75 |
|
8 |
364-*-373 |
55-*-58 |
|
67 4- 76 |
||
9 |
334 4- 376 |
56 4 -58 |
|
61 4 |
-74 |
|
10 |
371-*-376 |
55 4 -58 |
|
58 4-64 |
||
11 |
373-*-384 |
56 4 -5 8 |
|
52 4- 63 |
||
12 |
351 4- 370 |
57 4-58 |
|
59 4 |
-60 |
|
13 |
354 4- 362 |
58 4 -59 |
|
60 4 |
-75 |
|
14 |
344 -+- 350 |
59 4 -60 |
|
50 4 -79 |
||
15 |
341 -*-346 |
58 4 -60 |
|
46 4 |
-6 3 |
|
16 |
361-*- 369 |
57 4 -5 9 |
|
43 4 |
- 60 |
|
17 |
380 4-366 |
54-*-5S |
|
48 4- 60 |
||
18 |
383 н- 400 |
53 4-54 |
|
50 4 -58 |
||
19 |
373 -s- 386 |
5 3 4 -5 6 |
|
53 4 |
-54 |
|
20 |
380 4 - 393 |
56 ч- 58 |
|
44 4 |
-6 3 |
|
21 |
355 -4- 380 |
57 4 -5 9 |
|
48 4 |
-64 |
|
22 |
365 |
370 |
56 4 - 57 |
|
6 1 4 -7 0 |
|
23 |
348 4- 360 |
55 4-58 |
|
65 4 -78 |
||
24 |
360 -*- 373 |
54 4-57 |
|
60 4 -70 |
||
26 |
368 -*-371 |
56 4-56 |
|
54 4-72 |
||
27 |
361 -4- 372 |
55 4 -58 |
|
54-*-61 |
||
28 |
356 -s- 371 |
56 4- 57 |
|
56 4- 71 |
||
29 |
365 4- |
371 |
57 4-59 |
|
64 4-71 |
|
30 |
356 4- 356 |
57 -ь 58 |
|
54 4- 60 |
||
31 |
360-^361 |
54 4 - 60 |
|
43 4-57 |
После травления патентованные заготовки фосфатировали. Волочение осуществляли на машине со скольжением частными обжатиями около 18%. В качестве смазки применяли мыльную эмульсию.
Как видно из табл. 10 и 11, проволока диам. 0,3 мм имеет высокие прочностные и пластические свойства, а также высокую равномерность этих свойств. Некоторый разброс предела проч ности металла промышленной партии (табл. И) объясняется тем, что проволока изготовлена из стали нескольких плавок, от личающихся друг от друга по химическому составу и диаметру
62
патенти'рованных заготовок. Разброс предела прочности в каж дом отдельном бунте незначителен.
В табл. 12 приведены свойства проволоки диам. 0,3 мм, изго товленной по различной технологии из стали с высоким содер жанием углерода.
|
|
|
|
Т а б л и ц а 12 |
|
Механические свойства проволоки диам. 0,3 мм, |
изготовленной |
||||
|
по различной |
технологии |
|
|
|
|
|
|
Механические свойства |
||
Сталь |
Способ термической |
|
|
|
|
обработки заготовки |
аь, |
кг/мм2 |
% |
||
|
|
|
|||
|
|
|
|
|
р |
У9А |
Патентирование по |
обычной |
|
315 |
57,7 |
|
технологии |
|
|
367 |
38,0* |
У9А |
Высокотемпературное |
патенти |
|
362 |
56,3 |
|
рование |
|
|
370 |
56,3 |
Различного соста |
Высокотемпературное |
патенти |
|
364 |
57,0 |
ва с высоким |
рование |
|
|
|
|
содержанием |
|
|
|
|
|
углерода |
|
|
|
|
|
У12А |
Высокотемпературное |
патенти |
|
376 |
57,3 |
|
рование |
|
|
|
|
У12А |
Высокотемпературная нормализа |
|
384 |
56,3 |
|
|
ция и патентирование |
|
|
|
* Хрупкая.
Анализ данных, приведенных в табл. 12, показывает, что про волока, изготовленная из стали У9А и У12А с применением вы сокотемпературного нагрева, имеет при близких значениях вяз кости значительно более высокий предел прочности (362— 384 кг/мм2) по сравнению с проволокой, изготовленной по обыч ной технологии (315 кг/мм2).
Проволока, полученная из стали У12А с применением высо котемпературных режимов обработки, имеет также значительно более высокие свойства, чем проволока из стали У9А. При близ ких свойствах вязкости предел прочности проволоки из стали У12А более высокий по сравнению с проволокой из стали У9А, подвергнутой высокотемпературному патентированию в состоя нии заготовки. Свойства проволоки из стали У12А, изготовлен ной двумя различными способами (высокотемпературное патентирование и высокотемпературная нормализация с последующим патентированием), очень близки.
Высокие свойства проволоки из металла, подвергнутого вы сокотемпературному патентированию, свидетельствуют о целесо
образности использования такого способа термической обработ ки для заготовок тонких сечений из высокоуглеродистых сталей.
Режимы высокотемпературного патентирования для проволо ки диам. 1,4 и 1,8 мм (табл. 8 и 9) очень резко отличаются от обычных /применяемых на заводах режимов для указанных диа метров как по температуре в надмуфельном пространстве и тем пературе нагрева проволоки по выходе из печи (обычно они зна чительно ниже), так и" по .скорости патентирования, которая обычно в несколько раз больше.
Высокотемпературный режим нагрева и малая скорость па тентирования способствует росту зерна аустенита, а это обеспе чивает получение крупного зерна в патентированной стали, что в свою очередь приводит к повышению прочностных и пласти ческих свойств проволоки после волочения.
Высокие прочностные и пластические свойства проволоки (табл. 11) послужили основанием для разработки новых Техни-
ЧМТУ
ческих условий ■цНИИЧМ 395—60 на проволоку с пределом
прочности более 350 кг/мм2. Проволока с таким высоким преде лом прочности «ранее не производилась.
3. ВЛИЯНИЕ ОБЕЗУГЛЕРОЖИВАНИЯ НА СВОЙСТВА ПРОВОЛОКИ
Обезуглероживание оказывает отрицательное влияние на свойства проволоки. С увеличением глубины обезуглероженного строя снижаются прочностные свойства патентированной за готовки и полученной из нее проволоки (табл. 13).
Кроме того, при волочении с высокой степенью обжатия про волока из обезуглероженной заготовки рвется, так как внутрен ний (необезуглероженный) слой, обладая высоким сопротивле нием пластической деформации, вызывает такие высокие усилия волочения, что они превышают прочность обезуглероженных слоев, в результате чего на поверхности проволоки образуются микронадрывы, приводящие к концентрации напряжений и раз рушению металла.
|
Т а б л и ц а |
13 |
|
Предел прочности а ь патентированной заготовки из |
высокоуглеродистой |
стали |
|
диам. 1,8 мм с различной глубиной обезуглероживания и проволоки |
|||
диам. 0,3 мм, протянутой из этой заготовки |
|
|
|
Патснтированная заготовка |
|
Проволока |
|
глубина обедненной зоны, |
о^, кг/м м 2 |
а к г / м м 2 |
|
Не более 0,05 (обезуглероживание не до феррита) |
138-М 40 |
365ч-372 |
|
Около 0,18 (частичное обезуглероживание до феррита) |
119-М26 |
2974-314 |
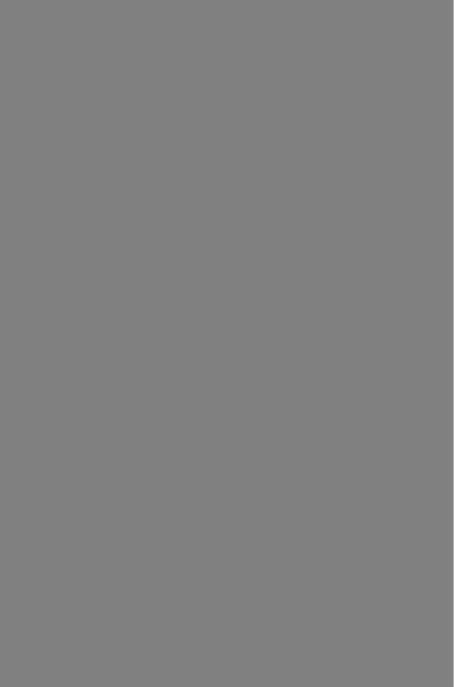
ВЛИЯНИЕ ХОЛОДНОЙ ПЛАСТИЧЕСКОЙ ДЕФОРМАЦИИ
НА ИЗМЕНЕНИЕ СТРУКТУРЫ И СВОЙСТВ ПРОВОЛОКИ
В результате холодной пластической деформации свойства металла, полученные после прокатки или приобретенные в ре зультате термической обработки, существенно меняются.
На изменение свойств металла при деформации оказывают влияние многие факторы: химический состав, структура, вели чина зерна, степень деформации, величина и распределение част ных обжатий в маршруте волочения, профиль волочильного ин струмента, скорость волочения, температура деформации и др.
Принято считать, что при холодной пластической деформации металла повышаются его прочностные характеристики и снижа ются свойства пластичности. Это явление называют накле пом.
1. ВЛИЯНИЕ СОДЕРЖАНИЯ УГЛЕРОДА, ДИАМЕТРА ПАТЕНТИРОВАННОИ ЗАГОТОВКИ, ВЕЛИЧИНЫ ЧАСТНЫХ
И СУММАРНЫХ ОБЖАТИЙ НА ИЗМЕНЕНИЕ ПРЕДЕЛА ПРОЧНОСТИ ПРОВОЛОКИ
Известно, что предел прочности проволоки повышается с уве личением содержания углерода в стали, а также частных и сум марных обжатий.
Вопросу предопределения предела прочности проволоки по святили свои работы многие исследователи [7, 8], [46—48], [56], [58], [63-69].
Предел прочности проволоки после волочения а6п можно
представить себе в виде суммы двух слагаемых: предела проч ности термически обработанной (патентированной) заготовки аь и прироста предела прочности Деть, полученного в результате деформации.
Предел прочности патентированной заготовки на заводах обычно обусловливается нормативными таблицами или может быть определен по формуле (8), а также по формулам других авторов [47, 48].
6В
Для определения прироста предела прочности проволоки, протянутой из патентированной заготовки с различным содержа нием углерода, автором еще в 1948 г. [46] была предложена фор мула.
При сравнении результатов расчета по этой формуле с экспе риментальными данными, опубликованными в литературе, а также с данными повседневной заводской прокатки установлено, что прирост предела прочности проволоки при ее волочении за висит от размера патентированной заготовки, а именно — с уве личением диаметра заготовки при неизменных частных и сум марных обжатиях прирост предела прочности протягиваемой проволоки увеличивается.
Формулы, приведенные в работах [8], [46], [48], [64], [69], и графические зависимости, указанные в трудах [7], [65-5-67], не учитывают этого фактора, а также .влияния частных обжатий (за исключением [47]). Для выяснения количественной зависимости изменения прироста предела прочности патентированной заго товки при изменении содержания углерода, диаметра заготовки, величин частных и .суммарных обжатий автором в 1949— 1950 гг. было выполнено специальное исследование.
|
|
|
|
|
|
|
|
|
|
|
Т а б л и ц а |
14 |
|
|
|
Химический состав |
исследованных сталей |
|
|
||||||||
|
|
|
|
Содержание элементов. % |
|
|
|
|
|||||
стали |
г- |
1 Мп |
S* |
|
1 |
s |
|
P |
1 |
Сг |
Ni |
Си |
|
|
|
|
|||||||||||
45 |
0,45 |
0,47 |
0,27 |
■ 0,023 |
0,013 |
|
0,04 |
0,16 |
__ |
||||
70 |
0,70 |
0,48 |
0,27 |
|
0,025 |
0,010 |
|
0,08 |
0,16 |
||||
У8А |
0,85 |
0,25 |
0,18 |
|
0,013 |
0,014 |
Следы |
0,10 |
__ |
||||
35 |
0,39 |
0,49 |
0,25 |
|
0,030 |
0,014 |
|
0,05 |
0,14 |
0,16 |
|||
55 |
0,56 |
0,43 |
0,25 |
|
0,029 |
0,015 |
|
0,04 . |
0,12 |
0,15. |
|||
60 |
0,63 |
0,31 |
0,22 |
|
0,027 |
0,012 |
|
0,05 |
0,14 |
0,21 |
|||
У8А |
0,83 |
0,35 |
0,26 |
|
0,020 |
0,012 |
|
0.04 |
0,14 |
0,21 |
|||
|
|
|
|
|
|
|
|
|
|
|
Т а б л и ц а |
15 |
|
|
Размеры патентированной заготовки, ее пределы прочности |
|
|||||||||||
|
и применяемые* частные обжатия при волочении |
|
|
||||||||||
Показатели |
|
|
|
При содержании углерода, •% |
|
|
|||||||
0. 45 |
0,70 |
0.85 |
| |
0.39 |
0.56 |
|
0,63 |
0, 83 |
|||||
|
|
|
|||||||||||
Диаметр заготовки, |
6,1 |
2; 1 |
|
|
|
|
|
|
|
|
|
|
|
мм |
|
6,1 |
|
2.1 |
2,3 |
4,85 |
4,85 |
4,85 |
4,85 |
2 .3 |
|||
Предел |
прочности |
|
|
|
|
|
|
|
|
|
|
|
|
а*,, к г /мм* |
90,2 |
119,1 |
127,9 |
133,1 93,7 |
89,1 |
104,к 112,3' 132,3 |
135,-5 |
||||||
Частные обжа |
|
|
33.5 |
|
|
f |
12 |
. J 22 |
|
Л;1,12. |
I1 2 - |
|
|
тия, % |
33,5 |
18,5 |
118.5 |
18,5 |
22: 1 |
22 |
|
22 |
ч22 |
22 |
|||
39* |
439- |
139 |
139 |
Исследование проводили на стали марок 45, 70 и У8А (табл. 14). Диаметры патентированной заготовки, ее пределы прочности (среднее значение из пяти испытаний) и частные об жатия при волочении приведены в табл. 15.
Влияние различных факторов на изменение прироста преде ла прочности проволоки приведено в табл. 16, 17 и 18. Анализ этих таблиц позволяет сделать следующие выводы.
|
|
|
|
|
|
|
|
|
|
|
Т а б л и ц а |
16 |
||
Влияние содержания углерода на |
изменение прироста предела прочности |
|||||||||||||
|
проволоки из патентированной заготовки |
диам 6,1 |
м м |
|
|
|||||||||
|
Показатели |
|
|
При диаметре протянутой проволоки .d, мм |
||||||||||
|
|
|
4,98 |
4,06 |
3,31 |
2.7 |
2.2 |
1.8 |
||||||
|
|
|
|
|
|
|||||||||
Суммарное обжатие Q, |
% |
А аь, |
33,5 |
55,7 |
70,5 |
80,4 |
87,0 |
91,85 |
||||||
Прирост |
предела |
прочности |
|
|
|
|
|
|
|
|
||||
кг/мм2: |
|
|
|
|
|
|
|
|
|
|
|
|
||
для стали У8А (0,85% С) |
|
28,2 |
52,2 |
72,9 |
92,1 |
118,0 |
145,9 |
|||||||
для стали 45 (0,45% С) |
. . |
20,7 |
38,5 |
52,5 |
64,7 |
80,7 |
98,1 |
|||||||
Разность |
приростов, к г /мм2 . |
|
7,5 |
13,7 |
20,4 |
27,4 |
37,3 |
47,8 |
||||||
Изменение à o b на 0,1% |
С, |
кг/мм2 |
1,87 |
3,43 |
5,1 |
6,85 |
9,33 |
11,95 |
||||||
|
|
|
|
|
|
|
|
|
|
|
Т а б л и ц а |
17 |
||
Прирост предела прочности при |
волочении проволоки из |
стали У8А |
||||||||||||
частными обжатиями |
q = |
33,5% |
при диаметрах |
патентированной заготовки |
||||||||||
|
|
6,1 |
(числитель) и 2,1 |
м м |
(знаменатель) |
|
|
|
|
|||||
|
Показатели |
|
|
|
|
При суммарных обжатиях Q, % |
||||||||
|
|
|
33,5 | 55.7 | |
70,5 |
80,4 |
87,0 |
91.35 |
|||||||
|
|
|
|
|
|
|||||||||
Диаметр |
протянутой проволоки d , мм |
4,98 |
4,06 |
3,31 |
2,7 |
2.2 |
1,8 |
|||||||
1,71 |
1,40 |
1,14 |
0,93 |
0,76 |
0,62 |
|||||||||
Прирост |
предела |
прочности |
|
|||||||||||
А а ь, |
|
|
72.9 |
92,1 |
118,0 |
145,9 |
||||||||
кг/мм2 . |
|
|
|
|
28,2 |
|
||||||||
|
|
|
|
|
|
26,1 |
4 M |
67,3 |
85,0 |
108,2 |
133,3 |
|||
Разность |
приростов, кг/мм2 |
|
|
2,1 |
4,2 |
5,6 |
7,1 |
9,8 |
12,6 |
а. Прирост предела прочности проволоки после волочения по вышается с увеличением содержания углерода в стали, диамет ра заготовки, а также частных и суммарных обжатий.
б. Изменение содержания углерода (С) на 0,1% оказывает влияние на прирост предела прочности протягиваемой проволо ки в такой же степени, как и изменение диаметра D патентиро ванной заготовки на 4 мм или частных обжатий q на 10%. Такая зависимость характерна при всех значениях суммарных обжа тий.
|
|
|
|
|
|
Т а б л и ц а |
18 |
||
Влияние величины частных обжатий на |
прирост предела прочности |
проволоки |
|||||||
|
из патентированной заготовки стали У8А диам. |
6,1 мм |
|
||||||
|
Показатели |
|
При диаметре протянутой проволоки d, мм |
||||||
|
|
4,98 |
4,06 |
3,31 |
2,7 |
j| |
2,2 |
1.8 |
|
|
|
|
|||||||
Суммарное обжатие Q, % |
|
33,5 |
55,7 |
70,5 |
80,4 |
87,0 |
91,35 |
||
Прирост предела прочности аь, кг/мм2, |
|
|
72,9 |
|
|
|
145,9 |
||
при частных обжатиях g = |
33,5% |
28,2 |
52,2 |
92,1 |
118,0 |
||||
То же, |
при q = 18,5% |
|
25,3 |
46,0 |
64,6 |
82,1 |
103,1 |
127,1 |
|
Разность приростов, кг/мм2 |
изме |
2,9 |
6,2 |
8,3 |
10,0 |
14,9 |
18,8 |
||
То же, |
кг/мм2, по расчету на |
1,93 |
4,13 |
5,53 |
6,67 |
|
9,93 |
12,5 |
|
нение |
частного обжатия в 10% |
|
При суммарном обжатии Q= 87% прирост предела прочно сти с достаточной для практических целей точностью может быть определен по уравнению
До*(87) = (с + ^ - + 0,01?) Q = AQ, |
(24) |
в чем можно убедиться по данным, приведенным в табл. 19.
|
|
|
|
|
Т а б л и ц а |
19 |
Сопоставление фактического прироста |
предела прочности проволоки |
|
||||
при суммарном обжатии 87% и |
расчетного по формуле (24) |
|
||||
Содержание |
Диаметр патен- |
Частные об |
Фактический |
Расчетный при |
||
прирост пре |
рост предела |
|||||
углерода С, % |
тированной за |
жатия д, |
% |
дела прочности |
прочности |
|
|
готовки D, мм |
|
|
Л <?£, кг/мм2 |
Д з ь, кг/мм2 |
|
0,45 |
6,1 |
33,5 |
|
80,7 |
81,5 |
|
0,85 |
6,1 |
18,5 |
|
103,1 |
103.4 |
|
0,85 |
2,1 |
33,5 |
|
107,8 |
107,0 |
|
0,85 |
6,1 |
33,5 |
|
118,0 |
116,2 |
|
|
|
|
|
|
Т а б л и ц а |
20 |
Прирост предела прочности |
проволоки из сталей 70 (числитель) |
|
и45 (знаменатель) с изменением содержания углерода, диаметра заготовки
ичастных обжатий при величине А = 0,9375
Показатели |
|
При суммарных обжатиях. % |
|
|||||
33,5 | |
55,7 |
70,5 |
80.4 |
87,0 |
91.35 |
|||
|
|
|||||||
Диаметр протянутой |
проволоки d, мм |
1.71 |
1,40 |
1,14 |
0,93 |
0,76 |
0,62 |
|
4,98 |
4.06 |
3,31 |
2,70 |
2,20 |
1,80 |
|||
Прирост предела |
прочности A abt |
|||||||
19,5 |
37,2 |
53.4 |
66,1 |
82.4 |
100,9 |
|||
кг/мм3 . . |
|
|||||||
|
20,7 |
38.6 |
52.5 |
64,7 |
80.4 |
98,1 |
||
|
|
Если в выражении (24) будут меняться два или даже все три слагаемых без изменения величины суммы, то прирост пре дела прочности при данном значении суммарного обжатия оста нется примерно одинаковым.
Данные табл. 20, а также данные, приведенные ниже, иллю стрируют справедливость высказанного положения для сталей с различным содержанием углерода, диаметром заготовки и част ными обжатиями, но с одинаковой суммой А:
|
С, % |
D, мм |
Я. % |
|
А = (С + |
|
+ 0 .019) |
||
45 |
0,45 |
6,1 |
33,5 |
0,45 |
+ |
0,1525 |
+ |
0,335 = |
0,9375 |
70 |
0,70 |
2,1 |
18,5 |
0,70 |
+ |
0,0525 |
+ |
0 ,1 8 5 = |
0,9375 |
Из данных табл. 21 следует, что при суммарных обжатиях Q<87% произведение A -Q больше прироста Даь. При Q= 87%, А меньше прироста Да*,, а при Q= 87% оно примерно равно при росту Деть,
Т а б л и ц а 21
Зависимость между произведением AQ (числитель) и приростом предела прочности, кг/мм2 (знаменатель), при волочении проволоки
из патентированной заготовки
Характеристика процесса |
|
Произведение AQ и прирост Д |
|
|||||||
|
при суммарном обжатии Q, % |
|
||||||||
|
|
|
|
|
|
|||||
С. % |
D, мм |
я. % 1 - |
33,5 |
55,7 |
70,5 |
1 80,4 |
87,0 |
91,35 |
||
|
|
|||||||||
0,45 |
6,1 |
33,5 |
0,9375 |
31,4 |
54,4 |
66,0 |
75.3 |
81,5 |
85,5 |
|
20,7 |
38,5 |
52,5 |
64,7 |
80,7 |
98,1 |
|||||
|
|
|
|
|||||||
0,70 |
2,1 |
18,5 |
0,9375 |
31,5 |
53,5 |
66,1 |
75,4 |
81,3 |
84,8 |
|
19,5 |
37,2 |
53,4 |
66,1 |
82,4 |
100,9 |
|||||
|
|
|
|
|||||||
0,85 |
6,1 |
18,5 |
1,1875 |
39,8 |
66,1 |
83,7 |
95,5 |
103,4 |
108,3 |
|
25,3 |
46,0 |
— |
82,1 |
103,1 |
127,1 |
|||||
|
|
|
|
64,6 |
||||||
0,85 |
2,1 |
33,5 |
1,2375 |
41,2 |
68,5 |
86,8 |
99,0 |
107,0 |
101,2 |
|
26/7 |
48,5 |
— |
87,5 |
107,8 |
132,0 |
|||||
|
|
|
|
68,0 |
||||||
0,85 |
6,1 |
33,5 |
1,3375 |
44,8 |
74,25 |
94,4 |
107,5 |
116,2 |
122,0 |
|
28,2 |
52,2 |
72,9 |
92,1 |
118,0 |
— |
|||||
|
|
|
|
145,9 |
Чтобы результаты расчетов по формуле (24) удовлетвори тельно сходились с опытными данными также и при суммарных обжатиях, отличных от 87%, в нее следует ввести коэффициент, снижающий прирост Даь при обжатиях Q<87% и повышающий его при обжатиях Q>87% в соответствия с фактическими пока зателями.