
книги / Термическая обработка и волочение высокопрочной проволоки
..pdf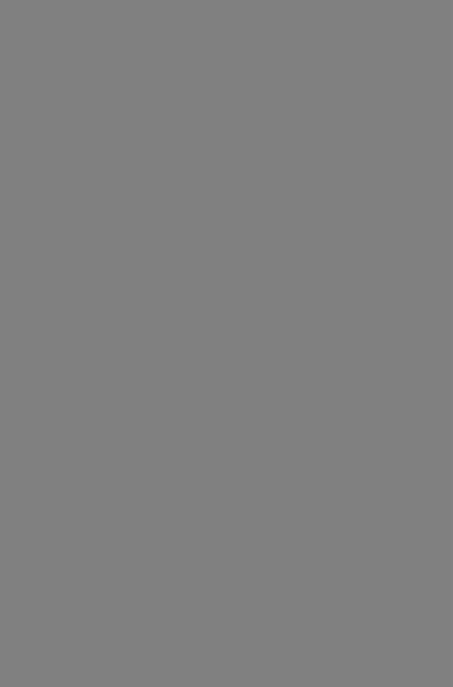
вследствие |
увеличения количества карбидов, |
раздробляемых |
|
в процессе |
деформации. Боас и Харгривс [70], а затем |
Юри |
|
и Вейн [71] установили, что в участках зерен |
алюминия, |
при |
легающих к границе, деформация всегда затруднена. На осно вании этого можно полагать, что увеличение диаметра деформи руемой проволоки приводит к повышению прироста предела прочности вследствие увеличения-протяженности границ между, зернами .в сечении, подвергнутом деформации. На границах зе-' рен, как указывает Рид [61], концентрируютсянесовершенства кристаллического строения; юни и оказывают, по-видимому, влияние на повышение прироста предела прочности при увели чении диаметра заготовки.
Несмотря на сложность выражения, определение прироста предела прочности по формуле, (26) с помощью логарифмиче
ской линейки занимает очень мало времени; можно пользовать ся также построенной автором номограммой (рис. 23), которая соответствует этой формуле.
Сходимость результатов расчета по формуле (26) с экспери ментальными данными удовлетворительна даже при широких вариациях входящих в нее величин (рис. 24).
На рис. 25 и 26 показана, например, сходимость эксперимен тальных данных для сталей марок 55 и У8А* с расчетными по
формуле (26) автора |
и формулам других исследователей: |
|
|
l,9 c b { \ - \ g V 100 — Q ) |
(27) |
|
0,1351^100—7 ^ |
|
|
|
|
|
|
(28) |
О формулах (27), |
(28) см. подробно в [47] и [48]. |
|
На рис. 27 сопоставлены расчетные значения прироста пре дела прочности по формулам (26—28) с фактическим материа лом 1из практики заводов. Металл для проволоки 87 производ ственных партий был выплавлен на девяти различных заводах, а изготовление проволоки производилось на семи заводах. Ис ходные характеристики в производственных партиях проволоки колеблются в широких пределах:
С. % |
аь ,кг/ммг |
D, мм |
q, % |
Q, % |
d, |
0 ,3 3 — 1,01 |
8 5 ,0 — 146,3 |
1,1 — 6,2 |
10,9 — 32,7 |
55,4 — 94,85 |
0,25 — 4,0 |
Для большинства партий число испытаний проволоки пре вышало 100, а для многих составляло до 500 и более.
Анализ сходимости формул с экспериментальными и практи ческими данными показывает, что выражение (26) наиболее универсально и дает наибольшее совпадение, чем формулы (27)
* Состав стали приведен в табл. 14; диаметр патентированной заго товки, ее предел прочности и частные обжатия указаны в табл. 15.
Рис. 24. Прирост преде ла прочности проволоки, протянутой и з. патентированной заготовки диам. 6,1 мм (сплошная ли
ния — фактический; пунктир — расчетный):
1 — сталь с 0,85%С, ча стные обжатия 33,5%; 2 —
сталь с 0,85% С, частные обжатия 18.5%: 3 — сталь
с 0,45% С, частные обжа тия 33.5%
Суммарное обжатие,%
4,ÔÔ |
ДА? |
3,0 Д64 2J3 ДА? 1J9 tjâ IJ9 \Д 1,07 ДО |
|
|
|
Дилметр пробтки.,мм |
|
0 |
37,5 |
61,7 70J 77,0 62,4 66,4 6Д4 91,7 93,7 95,1 |
96,24 |
|
|
CqMMapHoe рбжати.е,% |
|
Рис. 25. Прирост предела прочности проволоки из стали марки 55, протянутой из патентированной за готовки с различными частными обжатиями:
1 — фактический; 2 — расчетный по формуле (26); 3 — расчетный по формуле (27); 4 — расчетный по формуле (28)
,и (28). Формула (27) дает значительно меньшее отклонение от фактических данных, чем формула (28). Из 87 производствен ных партий (рис. 27) формула (26) имеет абсолютное минималь ное отклонение от фактических данных в 55 партиях (63%), формула (27) — в 26 партиях (30%) и формула ((28) — только
W |
3,Ô3 |
3,0 2fi* 2J3 2,03 1,79 tfô \,39 1,22 1,07 0,9* |
|
|
Диаметр продолоки,мн |
о37,6 61,7 7<$ Щ ага вба asa at,7SÔщ,I яала
Суммарное обтатие, %
Рис. 26. Прирост предела прочности проволоки иъ сталей марок 55(0,56% С) и У8А (0,83% С), протя нутой из патентированной заготовки диам. 4,85 мм с частными обжатиями около 22%:
1 — фактический; 2 — расчетный по формуле (26)\ 3 — рас четный по формуле (27); 4 — расчетный по формуле (23)
в 6 партиях (7%). По формуле (27) получаются завышенные (55 из 87 партий), а по формуле (28) в подавляющем большин стве заниженные (80 из 87 партий) результаты, что видно также из рис. 25 и 26.
При расчете получились отклонения от фактических данных не более 2%: по формуле (26) для 31 партии, по формуле (27) для 18 партий и по формуле (28) только для 6 партий (рис. 28). В подавляющем большинстве партий (в 77 из 87) формула (26) дает отклонение, не превышающее 6% от фактических данных.
74
123U5 |
tO' iô |
20 25 |
30 |
33 |
40 45 |
50 |
55 |
60 65 |
70 |
75 QO 65 67 |
|
|
|
|
|
Номера партии. |
|
|
|
|
Рис. 27. Прирост предела прочности фактический и полученный путем расчета по различным формулам:
/ — фактический; 2 — расчетный по фор-муле (26); 3 - расчетный-по формуле (27); 4 — расчетный по формуле (28)
сл
Такое же |
отклонение формула (27) дает только в 46 партиях, |
а формула |
(28) всего лишь в 11 партиях. |
Максимальное отклонение от фактических данных состав |
|
ляет: по формуле (26) — 11,5%, по формуле (27)— 22%, а по |
формуле (28) — 45%.
Формулы (27) и (28) не учитывают влияния диаметра патентированной заготовки, с увеличением которого прирост предела прочности также увеличивается. Поэтому,при толстых заготов
ках формула (27) дает заниженные, а-формула |
(28) — даже рез |
ко заниженные результаты (партии № 1, 3, 7, |
15, 29, 48, 66 на |
32 — - ч |
|
\ |
1 |
|
|
т |
|
|
Г" |
||
|
|
|
|
|
|
|
|
||||
26 |
|
|
|
|
|
|
|
_ | ________ |
|||
гч |
|
|
\ V |
|
|
|
1 |
|
|
I |
|
е 20 |
|
|
1 1-------- I |
|
1 |
|
|
|
|||
— 1 |
и |
|
\ ------ |
|
|
U |
|
||||
% |
|
/ |
\ |
|
|
X |
|
|
|||
|
|
\ |
|
|
|
1 |
|
||||
|
|
-------\N |
------/ |
|
V |
|
j |
|
|||
3 /2 |
3 |
|
V |
|
/ |
ч . |
|
|
|||
|
|
|
|
\1. \ |
|
|
\ |
|
|
||
|
±\ |
|
|
|
~л |
ЧУ""- |
|
**: |
Lji__ |
||
|
|
|
|
|
|
|
|
|
|||
|
} |
|
|
N |
. |
Ч |
V |
|
|||
|
|
|
\ |
т к |
ч , |
|
Н |
|
|||
|
|
|
|
— |
|
|
|
« |
|||
|
|
|
|
|
|
|
N |
|
|
|
|
|
|
|
|
|
|
|
! |
1 |
|
I |
|
|
|
|
|
|
Отклонение от ф а кт и че ски х данных |
|
|
|
|||
Рис. 28. Отклонение прироста предела прочности, полученного путем |
|||||||||||
расчета |
|
по |
различным формулам, |
от фактических результатов за |
|||||||
|
|
|
|
|
|
|
водской практики: |
|
|
|
|
|
1 — |
по формуле |
(26); 2 — по формуле (27); 3 |
— по формуле |
(28) |
||||||
рис. 27); при тонких заготовках формула |
(27) дает завышенные |
результаты, а для формулы (28) наблюдаются меньшие откло нения от фактических данных, чем обычно (рис. 27, партии N° 23, 57, 68, 69, 70, 71, 77 и 78).
С уменьшением диаметра заготовки повышается ее предел прочности после патентирования. В формулах (27) и (28) при рост предела прочности пропорционален пределу прочности патентированной заготовки, поэтому результаты расчетов для тон ких заготовок с повышенным пределом прочности выше, чем для толстых, что не соответствует практическим данным. В партиях № 8, 14, 16, 30, 34, 39, 57, 77, 78 и 82 (рис. 27) предел прочности патентированных заготовок несколько повышен по сравнению с нормальным по формуле (8), а в партиях N° 3, 7, 12, 15, 56, 63, 86 он несколько понижен. Расчётные значения прироста предела прочности по формулам (27) и (28) имеют в первом случае рез*
76
ко повышенные значения по сравнению с партиями, расположен ными слева и справа от указанных, а во втором случае — пони женные; фактический же прирост не имеет резкого изменения, Таким образом, введение в формулы (27) и (28) предела проч ности патентированной заготовки в качестве коэффициента, влияющего на прирост предела прочности проволоки после во лочения, является второй причиной отклонения расчетных зна чений прироста предела прочности от фактических, получаемых
по этим формулам.
Формула (28) не учитывает влияния частных обжатий, что является третьей причиной отклонения. Лишь при обжатиях,
Порвдкобый ы'Ьротмщ |
Порядкобый N*протяжки |
а |
б |
Рис. 29. Прирост предела прочности за каждую отдельно взятую протяжку
аьел для проволоки из стали с содержанием углерода 0,45% |
(а) |
и 0,85% |
(б). |
||
1 — фактический; 2 — расчетный по формуле |
(26); 3 - |
расчетный |
по |
формуле |
(27); |
4 —.расчетный по формуле (28) |
|
|
|
||
частных около 12% и суммарных |
более |
70—80%^ расчеты по |
формуле (28) дают результаты, довольно близкие к фактиче ским. Такие малые частные обжатия попользуются только при изготовлении сравнительно мало применяющейся проволоки с высоким пределом прочности из высокоуглеродистой стали.
При волочении проволоки из патентированной заготовки с
равными частными обжатиями прирост предела прочности за каждую отдельно взятую протяжку Дабед вначале уменьшается
от протяжки к протяжке, достигая минимальных значений при суммарном обжатии около 80%, а затем возрастает (рис. 29). Формулы (27) и (28) не отражают истинного хода кривой при роста предела прочности. В случае равенства частных обжатий формула (27) даег одинаковый прирост предела прочности во
всех протяжках, поэтому расчетные кривые прироста дважды пересекают экспериментальные кривые (рис. 25 и 26), а при оп
ределении прироста предела прочности по формуле (28) эта ха рактеристика повышается от протяжки к протяжке (рис. 29). Формула (26) соответствует истинному ходу кривой прироста предела прочности.
2.ВЛИЯНИЕ СОДЕРЖАНИЯ УГЛЕРОДА, ВЕЛИЧИНЫ ЧАСТНЫХ
ИСУММАРНЫХ ОБЖАТИИ НА ИЗМЕНЕНИЕ ПЛАСТИЧЕСКИХ СВОЙСТВ И ТЕХНОЛОГИЧЕСКИХ ХАРАКТЕРИСТИК ПРОВОЛОКИ
Я. Б. Фридман указывает [72], что относительное сужение точнее характеризует пластические свойства металла, чем отно сительное удлинение; но он считает более совершенной характе ристикой пластичности истинное сужение-истинное удлине ние (е):
где /о — начальная длина образца (до испытания); /к — конечная длина образца (после испытания);
Ф — относительное сужение; |
(до испыта |
Р0 — начальная площадь поперечного сечения |
|
ния); |
(после испы |
FK — конечная площадь поперечного сечения |
|
тания). |
|
Применительно к проволоке влияние степени обжатия на из менение истинного сужения-истинного удлинения в литературе не описано.
Работы, проведенные Бабошиным, Смирновым и Масловым [73], Помпом [74] и другими исследователями, показали, что с увеличением суммарных обжатий пластические свойства прово локи (ф), протянутой из патентированной заготовки, снижаются. М. Вонзель [75] наблюдал возрастание ф, значение которого до стигало максимума при обжатии около 80%, а затем оставалось постоянным или слегка уменьшалось. По данным В. Я. Зубова [10] максимальное значение ф у проволоки из стали У8А соот ветствовало обжатию 82%; эти данные не дают, к сожалению; представления об изменении ф при обжатий до 71%. Таким' об разом, исследователями получены противоречивые результаты и судить по ним о закономерности изменения пластичности прово локи из патентированной заготовки очень трудно. В многочис ленной литературе процесс холодной деформации связывают с непременным падением пластических свойств металла. Авторы книг по волочильному и канатному производству, вышедших за последнее десятилетне .[76, 77], также придерживались мнения,
что |
с увеличением степени обжатия пластичность проволоки |
(ф) |
из патентированной заготовки снижается. |
В исследованиях автора в качестве характеристики пластич ности проволоки принято относительное сужение площади по
перечного сечения < и истинное сужение-истинное удлинение е. Диаметр шейки после разрушения при растяжении образцов проволок измеряли: при диам. 1,8 мм и более микрометром с за остренными концами, при диам. менее 1,8 мм на инструменталь ном микроскопе, обеспечивающем точность измерения ±5 мк.
260
4.6Ô |
3,63 |
3,0 2,64 2ДЗ 2J03 |
179 !Д6 1,39 |
|
|
Диаметр проболоки.мм |
|
О |
37,Ь |
61,7 70,3 ПО 62,4 |
66,4 69,4 91,7 |
|
|
Суммарное обжатие,% |
|
Рис. 30. Влияние содержания углеро |
Рис. 31. Влияние содержания углеро |
|||||||
да в стали и степени обжатия па- |
да в -стали и степени обжатия патен |
|||||||
тентированной |
заготовки при волоче |
тированной заготовки |
при волочении |
|||||
нии на 'изменение предела прочности |
на |
изменение |
относительного суже |
|||||
проволоки: |
ния |
площади |
поперечного |
сечения |
||||
/ - 0,39% С; 2 |
- |
0.56% |
С: 3 - 0.63% С; |
|
проволоки: |
|
||
4 |
- |
0.83% |
С |
/ - |
0.39% С; 2 - |
0.56% |
С: 3 — 0.63% С; |
|
|
|
|
|
|
•; |
- 0.83% |
С |
|
На рис. 30—33 приведены средние значения результатов ис |
||||||||
пытаний патентированной заготовки |
из стали |
марок 35, |
55, 60 |
и У8А* и проволоки-, протянутой из этой заготовки частными обжатиями около 22%.
С повышением содержания углерода в стали пластичность (ср) патентированной заготовки значительно снижается (рис. 31). Но при этом пластичность проволоки, протянутой из iee, повышается, достигая при обжатии около 80% максималь н о значения (рис. 31). С повышением содержания углерода
Химический состав приведен в табл. 14.
в- стали повышение пластических свойств протягиваемой прово локи происходит интенсивнее. .Поэтому различие пластических свойств сталей 35 и У8А у проволоки после волочения меньше, чем у патентированной заготовки.
Для проволоки данного диаметра из стали с повышенным содержанием углерода число перегибов и скручиваний несколько ниже, чем у проволоки из стали с более низким содержанием
2<*
|
22 1 |
|
|
|
|
|
|
|
|
L |
|
|
|
|
|
|
|
|
|
|
|
|
20 |
|
|
|
|
|
|
|
|
|
/ а |
|
|
|
|
|
|
ч |
|
|
|
|
|
|
|
|
|
|
|
|
|
k |
/ |
|
|
|
1 |
|
|
|
|
|
|
|
16 |
|
|
|
|
|
|
|
|
<*0 |
|
|
|
|
JS |
|
|
|
|||
|
|
|
|
|
|
|
|
/ / |
/ |
|
|
|
у |
/ |
|
"Ч |
|
||||
^ /6 |
|
|
|
|
|
|
|
J |
/ / |
|
|
|
|
|
|
|
ч |
|
|||
|
|
|
|
1 |
|
- Â |
У |
// |
|
35 |
|
|
2 |
/ |
|
|
Ч |
|
|||
€ |
|
|
|
|
|
|
|
и |
._____ |
|
|
|
|
|
|
|
|||||
2 /4 |
|
|
2 |
/ |
|
|
г |
|
|
|л> |
|
/ i |
|
г* |
|
|
V \ |
||||
}« |
|
|
|
|
|
|
|
|
|
|
|
|
|
|
|
|
|
\ \ |
|||
|
|
|
|
|
|
|
|
|
|
|
/ / |
|
|
|
|
|
|
\ |
|||
|
|
|
|
|
V/ |
/ |
|
|
|
■о |
|
|
|
|
|
|
|
|
|||
1 10 |
|
|
|
|
|
|
|
|
а |
|
|
|
|
|
|
|
|
|
|||
|
/ / |
к з |
* / |
|
/ |
|
|
|
|
и |
|
! / |
|
|
|
|
|
|
|
||
|
6 |
/ / / |
|
|
|
|
|
т |
^ 4 |
|
|
|
|
|
|
||||||
|
|
|
У |
6 |
|
|
|
|
|
|
120 |
|
|
|
|
|
|
|
|
||
|
6 |
/ / / |
|
|
|
|
|
|
|
|
|
$ |
|
|
|
|
|
|
|
|
|
|
I* |
/7 |
/ |
|
|
|
|
|
|
|
|
15 |
|
|
|
|
|
|
|
|
|
|
|
|
|
|
|
|
|
|
|
|
ЮУ |
|
|
|
|
|
|
|
|
||
|
2 |
V |
|
|
|
|
|
|
|
|
|
|
|
|
|
|
|
|
|
||
|
|
/ |
|
|
|
|
|
|
|
|
|
Г |
|
|
|
|
|
|
|
|
|
|
(*,85 |
3,63 |
|
3,0 |
2,33 |
|
1.79 |
|
1,29 |
5 |
|
|
|
|
|
|
|
|
|
||
|
|
|
|
<*,65 |
3,63 |
|
3.0 |
2,33 |
|
129 |
1,39 |
||||||||||
|
|
|
|
Диаметр проШоки,мм |
|
|
|
|
|
||||||||||||
|
|
|
|
|
|
|
|
|
Диаметр пробопоки.мм |
|
|
||||||||||
|
Ю |
10 |
|
|
7,5 |
5 |
|
5 |
|
3 |
|
|
|
|
|||||||
|
|
|
|
|
О |
|
37,5 |
|
6(7 |
77,0 |
66,6 |
91,7 |
|||||||||
|
|
Радиус гудок при испытаниина перегиб,мм |
|
|
|||||||||||||||||
|
|
|
|
|
Суммарное обжатие,% |
|
|
||||||||||||||
|
О |
37,5 |
|
|
6t,7 |
77,0 |
66,1* |
|
91,7 |
|
|
|
|
|
|||||||
|
|
|
|
|
|
|
|
|
|
|
|
|
|
||||||||
|
|
|
|
Суммарноеобжатие, */, |
|
|
|
|
|
|
|
|
|
|
|
|
|
||||
Рис. 32. Влияние содержания углеро |
Рис. 33. Влияние содержания углеро |
||||||||||||||||||||
да в стали и степени обжатия патеи- |
да в стали и степени обжатия патен |
||||||||||||||||||||
тированной заготовки при |
волочении |
тированной заготовки при |
волочении |
||||||||||||||||||
на |
изменение числа перегибов |
прово |
на изменение числа скручиваний про |
||||||||||||||||||
|
|
|
|
|
локи: |
|
|
|
|
|
волоки |
при |
длине |
образца |
/ = |
100J: |
|||||
1 - |
0.39% |
С; |
2 |
- |
0.56% |
С; |
3 - |
0.63% |
С; |
1 - |
0,39% С; |
2 |
_ 0.56% |
С; |
3 - |
0.63% С; |
|||||
|
|
|
|
4 |
- |
0.83% |
С |
|
|
|
|
|
|
|
4 |
- |
0.83% |
С |
|
|
|
углерода (рис. 32 и 33). Числа скручиваний достигают макси мальных значений при суммарных обжатиях около 80% (рис. 33).
Изучение влияния величины частных обжатий (12, 22 и 39%) на изменение пластических свойств и технологических характе ристик патентированной проволоки показывает (рис. 34—36), что при всех значениях суммарных обжатий проволока, протя нутая с частными обжатиями 12%, имеет самые высокие значе ния относительного сужения q> (рис. 34) и числа перегибов (рис. 35). Самую низкую пластичность (<р) и малое числа пере гибов имеет проволока, протянутая с частными обжатиями 39%; при суммарных обжатиях 86,4% и более наименьшим числом