
книги / Термическая обработка и волочение высокопрочной проволоки
..pdfранстве отдельно для первой, второй и третьей зон, во время пагентирования проволоки диам. 4,4 мм по температурному ре жиму напрева (распределение тем1пературы газов надмуфельного пространства), принятому на заводе, и при скорости патен тарования 4,47 м/мин было 'произведено измерение температуры газов в муфеле при помощи гибкой скользящей термопары по длине -первой и второй зон через каждый метр.
Рис. 12. Схема |
патентировочной |
лени (7 — термопары, |
Ф — форсунки |
|
или |
горелки) |
|
Проволока во выходе из печи имела температуру 940° С. |
|||
Результаты |
измерения .представлены в виде |
графика на |
рис. 13.
После произведенных замеров (см. на рисунке оплошные ли |
|
нии) на электронном потенциометре, регулирующем температу |
|
ру первой зоны, было задано 1200 °С. Несмотря «а то |
что фор |
сунки этой зоны использовались на полную мощность, |
темпера |
тура в надмуфельном пространстве |
повышалась |
очень мед |
ленно и только через 20 час. достигла |
1120 °С. В дальнейшем |
|
повышения температуры не наблюдалось. |
температура |
|
Спустя 4 часа после того, как установилась |
||
1120 °jC, было-произведено следующее |
измерение |
температуры |
газовIв муфеле .печи. Результаты этого измерения и температу ра газов надмуфельного пространства во всех трех зонах указа ны на'рис. 13 пунктирными линиями.
В этом случае проволока по выходе из печи имела темпера туру 940 °С.
Повышение температуры газов в надмуфельном пространст ве первой зоны от 1000 до 1120 °С позволило поднять твхмлературу в различных точках муфеля печи на 35—105 °С.
Несмотря на то что форсунки первой зоны |
использовались |
|
на полную мощность, осуществить повышение |
температуры |
в |
этой зоне оверх 1120 °С все же не представилось возможным. |
|
Для того чтобы выяснить влияние температуры газов в надмуфельном пространстве второй зоны на изменение температу ры газов в муфеле печи по длине первой и второй зон, электрон ный потенциометр, регулирующий температуру второй зоны, был
1250 ]---
тт
|
1200 |
|
|
|
|
2 -я .зона |
|
|
|
1150 |
Зада 10 1210*céL |
т |
|
|
|||
|
Т |
1 |
|
|
|
|
Т |
|
|
1100 |
|
|
|
и |
|||
|
|
/-/? зона |
Н |
|
3 -Я301на |
|||
|
1050 |
1 |
|
|
||||
|
|
|
1 |
|
|
т |
||
|
|
1 |
|
|
|
|
||
«3 1000 |
7* |
|
|
1 |
|
|
|
|
|
|
|
|
|
|
|||
I |
950 |
|
|
|
|
|
|
|
|
|
|
1 |
|
|
|
||
5- |
900 |
|
|
|
|
|
|
|
J |
|
|
|
1 |
/ |
|
|
|
|
Ô50 |
|
|
|
|
|
||
|
|
|
|
! |
|
|
||
|
|
|
|
|
|
|
||
|
|
|
|
|
|
|
|
|
|
800 |
|
--- - |
s |
i-- 3___ г -1 |
|
|
|
|
|
|
|
|
||||
|
|
|
|
|
|
|
|
|
|
|
! |
н |
H i |
|
|
|
|
|
750 |
|
| |
|
|
|
||
|
700 |
|
|
|
i!1 |
|
|
|
|
650 |
|
|
|
|
|
|
|
|
0 |
1.0 |
2.0 3.0 |
Ь.О |
5.0 6.0 7.0 8.0 9.0 |
10.0 11.0 12013.0 |
Расстояние от бхода пробопокибпечь,м
Рис. 13. Распределение температуры в муфеле печи при патентировании проволоки диам. 4,4 мм со ско ростью 4,47 м/мин при различной температуре газов в надмуфельном пространстве (температура в надмуфелыюм пространстве по длине каждой зоны печи условно принята неизменной, фактически же она фик
сировалась только в одной точке зоны):
Т — расположение термопар по длине печи
также установлен на 1200 °С. Через два часа температура газов второй зоны достигла заданной температуры. Лишь после этого произошло повышение температуры нагрева проволоки по выхо де из печи. Затем для сохранения температуры нагрева металла на уровне 940 °С было произведено снижение заданной темпе ратуры третьей зоны (штрих-пунктирные линии).
В результате повышения температуры газов в надмуфельном пространстве второй зоны с 1150 до 1200 °С температура газов в муфеле печи повысилась по длине первой зоны иа 5-т-10 °С, а по длине второй зоны — на 10—70 °С.
На рис. 14 графически показано распределение температуры газов в муфеле патентировочной печи, измеренное при помощи гибкой термопары через каждый метр длины, в трех точках надмуфельного 'пространства (ino показанию приборов, подающих импульс исполнительным механизмам, регулирующим темпера туру всех зон) при патентировании проволоки диам. 6,0 мм со скоростью 3,0 м/мин .по режиму нагрева, принятому на заводе (оплошная линия), и опытному режиму (.пунктирная линия).
1.0 гО 3.0 LÛ-5.0 6.0 70 60 9.0 tOOUOiZOmtU 16.0
Расстояние от Плода пробоша 6печь.*
Рис. 14. Распределение температуры в муфеле печи при патентировании проволоки диам. 6,0 мм со ско ростью 3,0 м/мин при различной температуре газов надмуфельного пространства (температура надмуфельного пространства по длине каждой зоны печи условно принята неизменной, фактически же она
фиксировалась в одной точке каждой зоны):
Т — расположение термопар по длине печи
Повышение температуры газов надмуфельного пространства первой зоны с 1000 до 1120 °С, т. е. на 120 °С (большого повыше ния температуры газов надмуфельного пространства этой зоны достичь не удалось), и второй зоны с 1150 до 1240°С, т. е. на
90 °С, позволило повысить температуру |
газов |
в |
муфеле печи |
первой зоны на 25—120 °С, а второй зоны на |
100—140 °С. |
||
На рис. 15 приведены результаты лабораторных исследова |
|||
ний продолжительности нагрева центра |
образца |
проволоки |
диам. 6,0 мм стали марки 50 при температуре газов 525, 650, 750, 845, 940, 980 и 1087 °С.
Образец помещали в печь с различной температурой, термо пары укрепляли в центре проволоки (на ее глубине в 20 мм) и присоединяли к быстродействующему электронному потенцио метру. Электронный потенциометр записал изменение темпера туры в зависимости от в*ремейи (рис. 15). Пунктирные кривые получены интерполяцией.
Анализ кривых нагрева пока13ыв<ает, что .продолжительность нагрева до определенной заданной температуры резко сокраща
|
ла |
200 |
300 Ш 500 600 |
700 600 300 |
1000 1100 |
|
|
|
Температура. °С |
|
|
Рис. |
15. |
Продолжительность |
нагрева |
проволоки |
|
диам. |
6,0 |
мм в |
зависимости от температуры газов |
||
|
|
|
печи |
|
|
ется при повышении температуры печи. Так, например, для на
грева проволоки |
диам. 6,0 мм до 700 °С при температуре печи |
700 °С требуется |
150 сек., тогда как для нагрева до этой же тем |
пературы при температурах печи 750, 800, 845, 940, 980 и 1087 °С требуется соответственно 110, 90, 70, 40, 30 и 20 сек.
По данным распределения температуры в муфеле печи при
температурном |
режиме, принятом на заводе, и опытном режиме |
для проволоки |
диам. 6,0 мм, патентируемой со скоростью |
3.0м/мин (рис. 14), построены кривые нагрева металла диам.
6.0мм (рис. 16). Кривая 2 соответствует заводскому режиму на грева, кривая — опытному. Обе эти кривые построены из пред положения, что на расстоянии 0,5 м от входа в печь проволока не нагревается. Так как в этой части печи температура очень
низка, а -пребывание проволоки здесь кратковременно, такое допущение не вносит существенной ошибки. На рис. 16 нанесе на также экспериментальная кривая 1 нагрева проволоки диам. 6,0 м , соответствующая температуре лечи 940 °С (ом. рис. 15).
0 1,0 2,0 ?,0 4.0 5,0 6,0 7,0 6,0 9,0 10,011J012,013,014,015,0
^t Расстояние от бхода пробота бпечь,м
О |
50 |
100 |
150 |
200 |
250 |
300 |
время,сек.
Рис. 16. Экспериментальная кривая нагрева проволоки диам. 6,0 мм в сравнении с кривы ми нагрева при различном распределении тем пературы в муфеле патентировочнон печи
Эта кривая может быть получена практически в процессе патентирования проволоки указанного диаметра со скоростью 3,0 м/мин при условии наличия такой температуры в муфеле пе чи по длине всех трех зон.
Анализ кривых показывает, что при опытном режиме нагре ва возможно повышение скорости патентирования, так как про должительность нагрева сокращается. Так, при опытном режи
ме нагрева для достижения температуры проволоки 700 °С тре буется времени на 60 сек. меньше, чем при режиме, принятом на заводе. При .повышении старости патентирования кривая 3 мо жет занять положение кривой 2, и, таким образом, при повы шенной скорости патентирования будет обеспечена та же самая технология напрева .проволоки. Еще более значительного повы шения скорости патентирования, а следовательно, и производи тельности патентировочных агрегатов можно достичь при повы шении температуры газов в муфеле первой и .второй зон печи до 940 °С. Если, например, для напрева проволоки до 940 °С при режиме напрева, принятом на заводе, необходимо 250 сек. (кри вая 2), то, согласно кривой 7, для этого потребуется всего лишь
150сек.
Втабл. 5 приведены данные о paonределении температуры
газов в надмуфельном пространстве печей по зонам, принятом на заводах, в сопоставлении с опытным режимом.
Т а б л и ц а 5
Распределение температуры газов в надмуфельном пространстве по зонам печи, принятое на заводах, и по опытному режиму
Наименование |
№ патентиро |
Диаметр про |
Температура |
газов надмуфелыюго прост |
|
ранства печи по зонам, °С |
|||||
источника |
вочного агре |
волоки, мм |
|
|
|
|
гата |
|
1 |
2 |
3 |
|
|
|
|||
Завод А |
2 |
8 ,0 —4,0 |
1050— 1100 |
1100— 1150 |
1150— 1200 |
|
3 |
6,0—3,7 |
1050— 1100 |
1100— 1150 |
1150— 1200 |
|
8 |
4,4 —3,5 |
1050— 1100 |
1100— 1150 |
1150— 1200 |
|
9 |
3,4— 1,3 |
1000— 1050 |
1050— 1100 |
1100— 1150 |
Завод Б |
Все агрегаты |
6,5 —3,5 |
1000— 1070 . |
1100— 1170 |
1050— 1120 |
3,2 и менее |
950— 1020 |
1050— 1120 |
1000— 1070 |
||
Завод Б |
7 |
6,0 |
1120 |
1240 |
1080 |
(опытный |
(задано 1200) |
||||
режим) |
|
|
|
|
|
П р и м е ч а н |
и е . Распределение температуры надмуфелыюго пространства печей по |
зонам на других |
заводах не отличается от приведенных в данной таблице. |
Из данных таблицы следует, что на заводах еще не полно стью попользуется тепловая мощность существующих патентировочных печей, и, следовательно, резервы скоростей .патентиро вания и производительность агрегатов.
Патентирование проволоки диаметром меньше критического для отдельно взятого патентировочного агрегата экономически невыгодно. При обработке проволоки диаметром больше крити ческого наибольшие скорости процеоса достигаются при интен сивном нагреве металла со стороны входа в печь и повышении температуры по длине всего муфеля. Существующие патенти-
46
ровочные печи еще не отвечают указанным требованиям даже при сравнительно невысоких скоростях патентирования, так как тепловая мощность первой зоны недостаточна.
Для повышения производительности патентировочных печей при .применяемом материале муфелей — шамоте — необходимо перераспределить тепловую мощность зон, усилив ее в -первой зоне с таким расчетом, чтобы при патентировании с максималь ной скоростью температура в муфеле печи по длине последней была не ниже температуры нагрев-а проволоки на выходе. Та кой способ ведения температурного режима нагрева соответст вует варианту 2 (рис. 10). Температурные режимы нагрева, со ответствующие вариантам 3, 4 и 5 (рис. 10), могут быть приме нимы -на существующих и вновь проектируемых печах при ус ловии еще большего усиления тепловой мощности первой зоны и замены материала муфеля (шамота) более теплопроводным, в частности жароупорным, сплавом. Деление надмуфельного про странства печей на зоны должно позволять сосредоточить в первой зоне печи значительно большее количество тепла, чем в последующих зонах, т. е. выполнять роль, противоположную той, которую оно играет на существующих методических печах.
Сопоставление скоростей патентирования, применяемых фак тически и рассчитанных по разработанной методике (см., напри мер, рис. 17), свидетельствует о больших резервах .производи тельности патентировочных агрегатов [49].
Формулы (2), (3), (7), (22) и (23) .применимы для существу ющих патентировочных агрегатов при условии полного исполь зования тепловой мощности первой зоны печи. При изменении способа обогрева или конструкции печи эти формулы изменятся, но рекомендуемая методика расчета максимальной скорости па тентирования останется прежней, так как формулы (11), (19), (20), (21) выведены в общем виде.
Из приведенного анализа процесса патентирования следует, что для увеличения -производительности патентировочных агре гатов необходимы печи, обеспечивающие высокие температуры
нагрева.
На заводе Джон энд Робин Соне Ко (США) работает 12-ни точный п-атентировочный агрегат для углеродистой (0,40— 0,90% С) стальной проволоки средних размеров, выполняющий патентирование и подготовку -поверхности к волочению [52].
Напревательная печь этого агрегата длиной 18,2 м обогрева ется 45 карборундовыми радиационными трубами, расположен ными перпендикулярно к направлению движения проволоки. Отопительная газовая -смесь теплотворной способностью 4900 кал/нм3 с 2,5% избыточного кислорода поступает из смеси теля в горелки, расположенные внутри труб. Металл нагрева ется в защитной атмосфере, что уменьшает окалинообразование. Печь автоматизирована. Применение радиационных нагре вательных труб обеспечивает в рабочем пространстве печи по
всей ее длине температуру 1100°С. При тепловой мощности пе чи 822000 кал/нас в процессе патентирования проволоки диам. 2,8 мм со скоростью 36,5 м/мин производительность печи состав ляет 1360 кг/час.
Для получения высоких температур нагрева проволоки могут быть использованы также расплавы солей, например эвтектиче ская смесь хлористых солей ба)рия (ВаС1 — 46,6%), калия
Рис. |
17. Скорости |
патентирования на |
агрегате с |
печью длиной 12,6 м и ванной длиной 4,5 м (за |
|||
|
|
вод А): |
|
|
1 — фактические; 2 — расчетные |
||
(КС1 — 31,6%) |
и натрия |
(NaCl — 21,8%). |
Скорость нагрева |
проволоки в расплаве солей в 4—6 раз выше, чем в пламенных печах. Использование расплава солей указанного состава не требует оборудования для приготовления защитной атмосферы, так как окалинообразования не происходит [5, 6].
Работа, проведенная работниками Белорецкого завода, а также завода «Красная Этна» [33], показала, что при использо вании солей с высокой температурой плавления для нагрева проволоки при ее патентировании и солей с низкой температу-. рой плавления для распада переохлажденного аустенита про исходит затаскивание солей с высокой точкой плавления-в ван ну для раопада аустенита, что по истечении времени приводит к
48
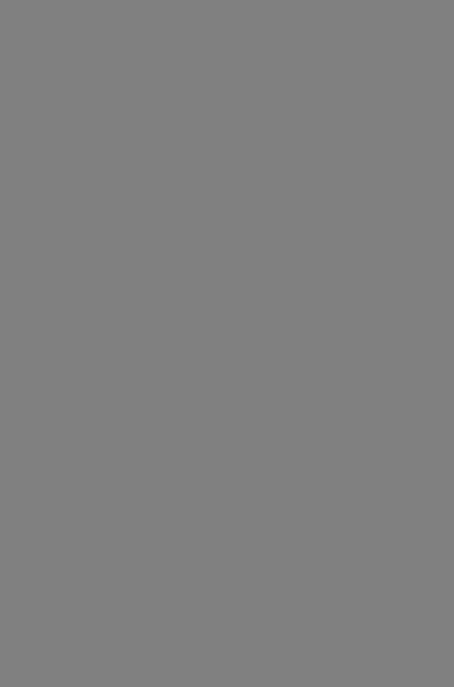
фелей «а 65% дороже, чем шамотных; кроме того, карборундо вые муфели удлиняются (за 13 мес. работы печи муфель удли няется на .470 мм).
На Ленинградском сталепрокатном заводе иатентирование проволоки .толстых диаметров осуществляется ка печи с откры тым1муфелем. Топливо— «природный газ — сго-рает непосредст венно в пространстве, в котором движется проволока, что обес печивает быстрый -нагрев проволоки, получение высоких темпе
ратур |
нагрева .и позволяет вести патентирование на высоких |
скоростях. |
|
При |
определенном соотношении газа и воздуха происходит |
лишь незначительное окал1инообразов'а1ние, при этом обезуглеро живания проволоки не наблюдается.
На этой печи производится также высокотемпературная нор мализация катанки из высокоуглеродистой стали, идущей для изготовления высокопрочных канатов и фортепианной прово локи.
Недостатком печи с открытым муфелем является отсутствие контролируемой атмосферы. В равной степени это относится к большинству патентир'овочных печей.
Использование более прогрессивных способов нагрева про волоки при ее патентировании, обеспечивающих высокие темпе ратуры нагрева, в значительной степени будет способствовать внедрению в народное хозяйство проволоки и изделий с более высокими прочностными характеристиками, что позволит сэко номить значительное количество металла и средств.
3. ПРИМЕРЫ НЕКОТОРЫХ ПРАКТИЧЕСКИХ РАСЧЕТОВ
Используя выводы, приведенные выше, а также формулы (2), (7), (11), (19), (20), (21) и (23), можно решить ряд прак
тических задач путем расчетов. |
с печью |
дли |
|||
П р и м е р |
Л. Для |
патентировочного агрегата |
|||
ной 15,62 м и ванной |
длиной 4,7 м определить |
максимальную |
|||
скорость патентирования проволоки диам. 5,0; 2,0 и 1,6 мм. |
|||||
а. Обозначив L'n — 15,62 м, a LB' = 4,7 м и |
приняв |
Ln = |
|||
= 0,95 |
L'n |
и LB= 0,95 L'B , |
|
|
|
где L'n |
— полезная длина печи; |
|
|
||
L ' |
— полезная длина ванны, |
|
|
находим
0,95-15,62 ^ 14,85
0,9 5 -4 ,7 |
“ |
4,46 |
б. Из соотношения (23) определяем условный критический диаметр данного агрегата:
£>к.у = У 3 ( п — 2 ) = У 3 ( 3 , 3 3 — 2 ) = 2 , 0 мм.