
книги / Справочное пособие по теплотехнологическому оборудованию промышленных предприятий
..pdf
|
|
|
|
|
|
|
|
|
|
Окончание табл.8.8 |
|
|
I |
|
|
|
1 |
2 |
1 |
3 |
1 |
4 |
|
|
|
|
|
|
|
||||||
снятие |
напряже |
|
Простой |
кон |
773 |
|
12-16 |
||||
ний |
|
|
|
|
фигурации |
|
|
|
|
|
|
|
|
|
|
|
|
Сложной |
кон |
773 |
|
21-25 |
|
Ковкий |
чугун, |
от |
фигурации |
|
|
|
|
|
|||
|
|
|
|
|
|
|
|||||
жиг: |
|
|
|
|
|
|
|
|
|
|
|
элеваторные |
|
|
Менее |
100 |
1223-1243 |
|
31-39 |
||||
электропечи типа |
|
Свыше |
100 |
1223-1243 |
|
37-45 |
|||||
П-650 |
|
|
|
|
|
|
|
|
|
|
|
туннельная |
печь |
|
|
|
|
1283-1243 |
|
39-58 |
|||
«ЗИЛ» |
|
|
|
|
|
|
|
|
|
|
|
камерная печь |
|
|
|
|
|
1253-1303 |
|
46-50 |
|||
Чугунные |
отливки, |
|
|
|
|
1123-1223 |
|
18-22 |
|||
залитые в |
кокиль, |
от |
|
|
|
|
|
|
|
||
жиг |
|
|
|
|
|
|
|
|
|
|
|
Примечания: |
1. |
Для |
определения |
количества |
камерных |
печей периодического |
действия продолжительность цикла термообработки принята из условий работы ка меры с одним выдвижным подом.
2. В цикл |
термообработки входит время, затрачиваемое на нагрев, выдержку |
и охлаждение |
в печи, охлаждение на воздухе при продолжении режима термической |
обработки в.той же печи и окончательное охлаждение на воздухе, которое состав ляет в зависимости от условий 1—5 ч.
3. |
Пределы |
температуры |
нагрева и продолжительность занятости термических |
печен |
приняты |
из расчета |
возможных режимов термической обработки отливок по |
их видам в литейных цехах. |
При необходимости они уточняются. |
4.Продолжительность цикла термообработки принимается ближе к верхнему значению для разностенных отливок, а также имеющих сложную конфигурацию.
5.Нормативы данной таблицы применяются при отсутствии технологических данных о термообработке отливок.
паспорту или рассчитанную производительность, в результате чего находится число часов работы печи, необходимое для обеспечения заданной программы. Получен ная величина округляется до целого (в сторону увеличения). Делением установ ленного количества печей на расчетное вычисляется коэффициент загрузки обо рудования.
Согласно второму методу, по нормам времени для каждой детали (табл. 8.8) определяется общее время, необходимое для термообработки в данной печн (со ставляются ведомости загрузки оборудования). Делением этой величины на фонд времени вычисляется количество печей.
В соответствии с выражением (8.1) определяем величину коэффициента за грузки оборудования k3:
|
k 3 = ^ 1 0 0 %, |
|
(8.2) |
|
где п, |
п' — соответственно расчетное (8.1) |
и фактически |
принятое к |
установке |
число |
однотипного оборудования (печей, |
сушил). Если |
в результате |
расчетов |
коэффициент загрузки окажется небольшим (30—50 %), следует выполнить пе рерасчет программы цеха на печн меньшей производительности или перенести термообработку части деталей на менее загруженное оборудование. Если коэффи циент загрузки превышает 95 %, необходимо принять к установке в цехе резерв ную печь.
Подробные сведения о методике выбора количества необходимого вспомо гательного (не печного) оборудования для термических цехов приведены в ли тературе [86, 114].
9* |
131 |
Число единиц кузнечно-прессового оборудования находится в соответствии с табл. 8.9 по формуле
р
ГОД
ш =
Для объемной штамповки коэффициент загрузки А3= 0,8 —0,9.
Заготовительное производство включает большую группу цехов металлур гического цикла, в которых важная роль отводится сушке компонентов рабочей смеси и форм. Технология смесеприготовительиых отделении литейных цехов на ряду с другими включает операции сушки песка и его охлаждения перед поступ лением в смесеприготовительные машины.
Компоновка отделения сушки песка с барабанными сушилами приведена на рис. 8.9. Выбор числа и типоразмера сушил производится в соответствии с го довой (часовой) производительностью формовочного цеха и фактическим фондом времени работы сушил.
Часть поковок и отливок после термической обработки подвергается грунтов ке перед поступлением в механосборочное производство. На рис. 8.10 показан участок для нанесения и сушки защитного покрытия (грунта ГФ-020) на поков ки после отжига. Участок расположен в термическом отделении корпуса.
132
Табл. 8.9. Производительность кузнечно-прессового оборудования
Кривошипные ковочно-штамповочные прессы |
Горнзонтзлыю-ковочные Мац»ны |
|||||||
|
|
|
производительность |
|
|
производитель |
||
|
масса |
|
масса |
ность |
||||
|
|
|
усилие ма |
|||||
усилие |
|
шт. (при |
|
шт. (при |
||||
штампуе |
|
штампуе |
|
|||||
пресса 10*, |
мых поко |
кг/ч |
средней |
шины 10', |
мых поко |
кг/ч |
среднеП |
|
Н |
вок, кг |
массе по |
И |
вок, кг |
массе по |
|||
|
|
|
|
ковок) |
|
|
|
ковок) |
Изготовление |
поковок средней сложности на штамповочных прессах и ГКМ |
|||||||
6,3 |
До |
1 |
400-500 |
310 |
1 |
До 0,2 |
80 |
290 |
10 |
1—2,5 |
500—600 |
1 ,6 |
0 ,2- 0 ,5 |
100 |
|||
16 |
1 ,5 - 4 |
600—800 |
2 10 |
2,5 |
0 ,5 -1 |
200 |
270 |
|
20 |
4—7 |
800—1200 |
180 |
4 |
1— 2 |
300 |
200 |
|
25 |
7— 12 |
1200—1600 |
145 |
6,3 |
2 - 5 |
500 |
140 |
|
31,5 |
12— 18 |
1600—2000 |
125 |
8 |
5 - 8 |
600 |
95 |
|
40 |
18—30 |
2000—3000 |
100 |
10 |
8 - 1 0 |
700 |
80 |
|
63 |
30—50 |
3000—4000 |
90 |
12,5 |
1 0 - 1 2 |
800 |
70 |
|
80 |
50—80 |
4000—5000 |
70 |
16 |
12-16 |
900 |
65 |
|
100 |
80—100 |
5000—6000 |
60 |
20 |
16-20 |
1000 |
55 |
|
|
|
|
|
|
25 |
20-25 |
110 0 |
50 |
|
|
|
|
|
31 |
25-30 |
1200 |
44 |
|
Штамповка средней сложности из среднеуглеродистой стали |
|
||||||
0 ,0 1 |
До |
25 |
300 |
_ |
0,005 |
До 1 |
100 |
130 |
0 ,0 2 |
2,5—7 |
600 |
125 |
0 ,0 1 |
1 - 2 |
200 |
||
0,03 |
7— 17 |
1000 |
85 |
0 ,0 2 |
2 - 5 |
400 |
115 |
|
0,04 |
17—30 |
1500 |
55 |
0,03 |
5 -1 2 |
700 |
80 |
|
0,06 |
30—50 |
2000 |
50 |
0,05 |
12-25 |
1100 |
60 |
|
0,08 |
50—80 |
2500 |
40 |
0,08 |
25-50 |
1600 |
45 |
|
0 , 1 0 |
70— 100 |
3000 |
35 |
|
|
|
|
|
0 , 1 2 |
100— 180 |
4000 |
30 |
|
|
|
|
|
0,15 |
180—360 |
5000 |
19 |
|
|
|
|
|
0 ,2 0 |
360—700 |
6000 |
11 |
|
|
|
|
8.3. Компоновка и выбор теплотехнологического оборудования механосборочного производства
Детали, которые получаются путем обработки металлической заготовки ре занием в механических цехах механосборочного производства, подвергаются термической обработке. Назначение термической обработки деталей в термиче ских цехах механосборочного производства — их упрочнение, при этом^ исполь зуются методы как чисто термического воздействия, когда химический состав поверхностных слоев остается прежним, так и термического воздействия с изме нением не только микроструктуры, но и химического состава поверхностного слоя.
Упрочнению в большинстве случаев подвергают детали, прошедшие механи ческую обработку перед операциями шлифовки и сборки. Поэтому к качеству и структуре поверхностных слоев детален предъявляются высокие требования, ре ализация которых возможна только при условии применения в процессах термо обработки контролируемых атмосфер. На передовых отечественных предприятиях почти всю продукцию механосборочного производства подвергают термической обработке с применением контролируемых атмосфер.
Термообработка деталей машин производится, как правило, в отделениях цехов (на участках). Иногда печи или печные агрегаты встраиваются в линии
133
Табл. 8.10. Температурные графики термообработки стальных деталей механо-
|
сборочного производства |
Примерный температурный |
Последовательность технологических операций |
график |
тепловой обработки |
1
' г К к .
i,4
г Ш к
гл 1 2
2
1— нитроцементацня; 2— закалка в холодном или горячем масле; 3— низкий отпуск
1— цементация; 2— подстуживание под закалку и выравнива
ние температуры и концентрации (в отдельной камере);
I?— закалка в холодном или горячем масле; 4— низкий отпуск
1— цементация;
2— охлаждение (в камере); 3— закалка в холодном или горячем масле; 4— низкий отпуск
1— цементация;
2— охлаждение (в камере); 3— высокий отпуск (с охлаждением в камере);
4— повторный нагрев под закалку;
5— закалка в холодном или горячем масле;
6— низкий отпуск
1— закалка в холодном или горячем масле;
2— низкий отпуск
1— цементация или нитроцементация; 2— охлаждение (в камере)
1— цементация с подстуживанием до темпера туры закалки;
2— закалка в холодном или горячем масле;
3— высокий отпуск; 4— охлаждение (в камере)
134
Окончание табл. 8.10
1 |
2 |
1— закалка в холодном или горячем масле;
2— высокий отпуск;
3— закалка в воде
1— цементация; 2— охлаждение (в камере);
3— высокий^отпуск; 4— охлаждение (в камере)
t,4
или участки механической обработки. Термические участки (отделения) могут располагаться либо в отдельных зданиях, либо в блоке цехов.
Наибольшее количество процессов термической обработки характерно для автотракторных и машиностроительных предприятий. В мелкосерийном производ стве для этой цели применяют преимущественно камерные и шахтные печи, в серийном и крупносерийном — проходные печи (конвейерные, толкательные ит. п.), а также автоматические линии термической обработки, совмещающие ряд тер мических операций.
Процессы, в которых осуществляют насыщение деталей каким-либо элемен том, относят обычно к операциям хнмико-термнческой обработки. Однако деле ние операций на термические и хнмнко-термнческие чисто условное, так как и при закалке, отжиге, нормализации также происходит физико-химическое взаимо действие между железом, углеродом стальных деталей и печной атмосферой.
На металлургических заводах, выпускающих прокат, основными видами тер мообработки товарной продукции являются нормализация и отжиг. В связи с повышением требований к качеству проката с целью экономии металла в послед ние годы разработаны методы реставрационного науглероживания при отжиге. При этом специфическом, но перспективном процессе одновременно с отжигом происходит восстановительное насыщение углеродом обедненных при предыдущих операциях поверхностных слоев металла (табл. 8.10).
На рессорных, пружинных, метизных предприятиях основным технологиче ским процессом является закалка с последующим отпуском. Для закалки дета лей чаще всего используют масло и воду. Иногда применяют водные растворы солей, щелочей, кислот, эмульсин, псевдоожиженный слой инертного дисперсного материала, водные растворы полимеров и т. д.
При единичном и серийном производстве применяются печи универсального назначения (камерные, шахтные, печи-ванны), а при массовом — специализиро ванные с высоким уровнем механизации (толкательные, конвейерные).
При планировке термического цеха предварительную оценку производствен ной площади можно сделать на *основе укрупненных норм: в инструментальном термическом отделении требуется 25—30 м2 площади на печь, в термическом цехе с толкательными и конвейерными печами — 80—130 м2. Площадь проездов н проходов составляет 20—30 % производственных площадей. Выполняя расста новку печей, необходимо стремиться к тому, чтобы в общем грузопотоке (дви жение деталей по операциям) не было встречных перемещений. Для этого выби раются места поступления деталей в цех и точки выхода. После расстановки печей намечаются площади для вспомогательного оборудования, складских н подсобных помещений.
135
Оборудование по общему назначению следует группировать в отдельные участки термообработки (цементации, азотирования и т. д.). Крупное оборудова ние — агрегаты толкательного и конвейерного типов — размещают в несколько рядов, оставляя проходы между ними (2—3 м). Если проходные агрегаты за мкнутого типа (загрузка и выгрузка деталей в одном и том же месте), удобнее их устанавливать поперек цеха, если же загрузка и выгрузка на разных концах агрегата,— вдоль. Проходы между камерными печами обычно принимают рав
ными 1,5—2 м.
При расстановке оборудования фасады печей стремятся располагать в одни
общий ряд (вдоль |
стен). Расстояние между стенами и оборудованием не |
ме |
нее 1—1,5 м. |
цехах с крупным оборудованием должно быть не менее |
1— |
В термических |
2 проездов в середине цеха или по краям: один должен быть пожарным и иметь ширину 5—5,5 м, другой — 3,5—4 м [86].
Закалочные баки, не встроенные в агрегаты, устанавливаются на минималь ном расстоянии от закалочных печей. Прессы для правки, измерения твердости, пункты ОТК, электролитические ванны для травления могут быть размещены в том же помещении, что и печи. Участки с печами цианирования, в которых применяются особо опасные цианистые соединения, отделяются перегородкой.
Генераторы защитных атмосфер располагаются непосредственно у печей (ав тономная схема снабжения) или в определенном месте (централизованная схема). Вопрос о преимуществах и недостатках каждой из схем рассмотрен в литера туре [14].
Втермических цехах должно быть предусмотрено помещение для службы механика, хранения радиационных труб, муфелей, вентиляторов приточной и вы тяжной систем, а также для маслоохладительных установок и насосов (послед ние обычно устанавливают в подвале цеха).
Вцехах поточно-массового производства склады продукции не предусматри ваются. В цехах другого типа (серийного, индивидуального, массового произ водства) следует устраивать помещение для складов. Кроме того, в цехе необ ходима кладовая для хранения технологических материалов и других ценностей. Общая площадь вспомогательных помещений составляет обычно 25—30 % про изводственной площади.
Компоновка участка термообработки стальных изделий показана на рис. 8.11.
Для отжига, нормализации, закалки, отпуска, |
цементации, нитроцемента |
||
ции, азотирования выпускаются стандартизированные печи |
с электрическим обо |
||
гревом. Число единиц теплотехнологического оборудования |
(печи, сушила) |
меха |
|
нического производства выбирается в соответствии |
с выражениями (8.1), |
(8.2) |
|
и табл. 8.3—8.7. |
|
|
|
Исключительное внимание в последние годы уделяется декоративному и за щитному покрытию деталей механосборочного производства машиностроительных заводов. Изделия, подвергаемые окрашиванию, делятся на две группы. К первой относя? крупногабаритные, обладающие сравнительно небольшим весом изделия (кабины, элементы обшивки кузовов, лонжероны, различного рода емкости и т. п.); ко второй группе — менее крупные, но обладающие большой массой
детали, полученные путем литья или обработки давлением (элементы мостов, картеров и т. п.).
Всостав технологической линии окрасочного участка входят камеры моечные
иокрасочные, а также сушильные и охлаждения.
Оборудование технологической линии окрасочного отделения объединяется конвейером (подвесным или напольным тележечного типа).
Часто изделия заготовительных цехов подвергаются только грунтовке без на несения декоративного слоя.
Технологический процесс окраски заключается в мойке и сушке перед на несением на деталь грунта или слоя эмали и охлаждении на воздухе или в спе циальной камере. Затем деталь конвейером подается в одноили многопозицион ную окрасочную камеру, где на ее поверхность наносится слой грунта или пер вый слой краски (эмали), и направляется к тамбуру загрузки конвективного пли терморадиационного сушила. В сушиле происходит испарение паров растворите
ля |
и полимеризация первого слоя покрытия. После |
сушки деталь охлаждается |
до |
температуры 293—323 К в специальной камере |
(реже на открытом воздухе |
136
по мере перемещения ко второй окрасочной камере), где происходит нанесение слоя окраски после грунтовки или второго слоя покрытия. После окраски детали направляются в сушило, затем охлаждаются в камере или на воздухе и посту* пают на участок разгрузки конвейера. В промежутке между первым н вторым покрытием краской предусматривается возможность подкраски деталей. Сушка после грунтовки и окраски происходит при температуре 383—423 К; после мойки (банденизацин) — при температуре 353—393 К. Как уже отмечалось, для сушки
Рис. 8.11. Компоновка участка термообработки с электропечными агрегатами СТЦА:
/ — пульт управления; 2 — моечно-сушильная машина; 3 — механизмы перемещения; 4 — электропечь низкого отпуска; 5 — электропечь цементации; 6 — камера подстужнвання; 7 — закалочным бак; 8 — электропечь закалочная; 9 — эндотсрмнческн/i генератор; 10 — гидропанели; // — трансформатор; 12 — щнт управления; 13 — панель контроля н распределения газа; 14 — маслонанорная установка.
после нанесения грунта и окраски обычно используются горизонтальные много ходовые сушила конвективного или термораднацнонного типа. В качестве тепло носителя используются пар, электрическая энергия и природный газ. Сушильным агентом являются воздух или продукты сгорания топлива (их смесь с атмосфер
ным воздухом).
Общее число оборудования (окрасочные камеры, сушила и др.) определяется технологическим процессом сушки, а его производительность — годовой програм мой цеха (заготовительного или механосборочного). Сушильное отделение, как правило, включает оборудование, объединенное одиониточным, реже двухннточ-
ным конвейером. При этом |
предусматривается незначительный |
резерв (10— |
15 %) по производительности |
теплового оборудования отделения. |
Регулирование |
производительности при наличии такого резерва достигается изменением скорости движения конвейера.
137
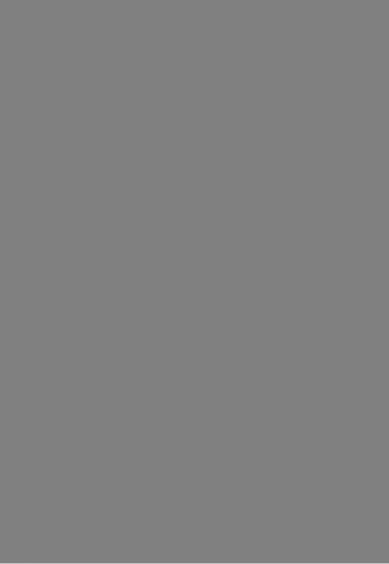
Табл. 8.11. Коэффициент полезного действия термических печей
Операция термической |
|
КПД печей |
|
||
обработки |
|
пламенных. |
|
электрических |
|
|
|
|
|||
Отжиг стального ли- |
Камерные |
0 , 10- 0 ,1 2 |
|
0,50 |
-0,70 |
тья продолжительностью |
Шахтные |
0,11-0,13 |
|
0,55-0,70 |
|
4— 6 ч |
С выдвижным подом |
0,08 -0,12 0,45-0,70 |
|||
|
|||||
Отжиг ковкого чугуна |
Непрерывного действия |
0,12 -0,15 0,60-0,75 |
|||
Камерные |
0,06—0,10 |
0,50-0,65 |
|||
Нормализация и закал |
Непрерывного действия: |
|
|
|
|
ка |
толкательные |
0,18-0,25 0,70-0,80 |
|||
|
|||||
|
конвейерные |
0,18-0,25 |
0,70 |
-0,80 |
|
|
Карусельные |
0,18-0,25 |
0,70 |
-0,80 |
|
|
Камерные и шахтные |
0,15-0,22 |
|
0,65 |
-0,75 |
скорость нагрева в объемных пламенных печах, что объясняется повышенной ин тенсивностью теплообмена.
В |
качестве |
нагревательного |
оборудования в отделениях горячей штампов |
ки на |
молотах |
н кривошипных |
горячештамповочных прессах чаще всего при |
меняются полуметоднческие толкательные печи.
Камерные печи устанавливаются у штамповочных молотов и прессов неболь шой производительности, а также в случаях, когда нагреваются заготовки очень широкой номенклатуры, сильно отличающиеся друг от друга по размерам, кон фигурации, технологии штамповки.
Полуметоднческие печи значительно экономичнее камерных и позволяют ме ханизировать загрузку, перемещение и выгрузку заготовок. Однако механизация нагревательных операций может быть успешно решена лишь при массовом и крупносерийном производстве, когда за одним штамповочным агрегатом закреп лена узкая номенклатура поковок. При нагреве однотипных по форме заготовок с достаточно большим отношением длины к эквивалентному диаметру могут при меняться печи с «шагающим» подом («шагающими» балками). Проблему меха низации транспорта при нагреве заготовок разнообразной формы позволяют ре шить печи с вращающимся подом. Конструкции и техническая характеристика наиболее распространенных в машиностроении полуметодическнх и методических печей даны в литературе [103].
8.4.2. Печи для термической обработки поковок и отливок
Основными видами термической обработки поковок являются следующие. Нор мализация (нормализации подвергаются поковки, содержащие, до 0,4 % углерода), при которой поковки нагреваются до температуры выше верхней критической точки 1Лс3 на 50—60 °С и после непродолжительной выдержки выгружаются из печи н
охлаждаются на воздухе. Термоулучшение — закалка и высокий отпуск (применяют для среднеуглеродистых (0,4—0,6 % углерода) и легированных сталей) с целью по лучения заданной микроструктуры и твердости.
При закалке поковки нагревают до температуры tA C3 + (30—50) °С, а при от
пуске — до 550—680 °С. Закалку поковок из легированных сталей осуществляют в масле, а из углеродистых сталей — в воде. Охлаждение после отпуска производит ся в атмосфере печи, на воздухе либо в воде (ванне или под душем). Отжиг огне термический, которому подвергаются поковки из легированных сталей с высоким содержанием углерода. Операция отжига позволяет не только уменьшить неодно
родность структуры, но и |
снять напряжения, снизить твердость перед последующей |
обработкой резанием. При |
отжиге поковки нагревают до температуры * А С 3 + (30— |
139
—50) СС, выдерживают при этой температуре, |
а затем охлаждают до 600—500 °С |
со скоростью 20—60 °С (легированные стали) |
и 50—150 °.С (углеродистые стали) |
в час.
Указанные операции термического упрочнения выполняют в различного типа проходных (при серийном и крупносерийном производстве) или садочных (в мел косерийном производстве) печах. Из проходных печей применяются толкатель ные и конвейерные (с ленточным или подвесным конвейером), а из садочных — камерные с выкатиым и шаровым подом, печи с перемещающимся корпусом и т. д. [103].
При производстве поковок точными методами, когда величина припуска со ставляет 0,5—1,0 мм, применение защитных атмосфер в процессе термообработки поковок обязательно. Использование защитных атмосфер предотвращает окисле
ние (угар), |
а иногда |
и обезуглероживание металла, устраняет потребность |
в очистных |
операциях. |
При штамповке обычными методами целесообразность |
применения защитных атмосфер определяется экономическим анализом для каж дого конкретного случая (с учетом реальной экономии затрат на очистку, реаль ной экономии металла за счет снижения припуска). Экономический анализ пцказывает, что если поковки перед термообработкой имеют неглубокий поверхност ный обезуглероженный слой (до 0,4 мм), целесообразно совмещать операцию термической обработки с-реставрационным науглероживанием в контролируемых атмосферах до исходной марочной концентрации углерода в данной марке стали.
Термическая обработка чугунных отливок занимает исключительное место среди операции тепловой обработки литейных цехов. Ее назначение — придание ■требуемых свойств за счет изменения структуры при нагреве, выдержке и охлаж
дении. |
чугуна — графитизирующий от |
Термообработка отливок из ковкого (белого) |
|
ж иг— предназначена для получения ферритной |
структуры основной металличе |
ской массы и графита хлопьевидной формы. В результате термообработки про исходит коренное изменение фазового состава и структуры белого чугуна в результате полной или частичной графитизации. Чугун из твердого и хрупкого превращается в пластичный и хорошо обрабатываемый.
Термообработка отливок из |
серого |
чугуна применяется |
главным |
обра |
зом для улучшения технологических |
и эксплуатационных |
свойств |
(обра |
|
батываемости, износостойкости |
и т. п.) |
как операция дополнительной |
обра |
ботки для исправления отливок, полученных с отклонениями от требуемого качества.
Из других методов термической |
обработки отливок следует |
отметить от |
жиг, нормализацию, закалку и отпуск. |
величин зерен и получение |
равновесных |
Отжиг обусловливает изменение |
структур распада аустенита. Для стальных отливок используется полный и диф фузионный отжиг. Полный отжиг применяется с целью снижения твердости, что способствует улучшению механической обработки резанием и снятию внутренних напряжений. Микроструктура стали в литом состоянии обладает крупным зерном с грубыми включениями феррита. Отжиг литой стали приводит к получению мелкозернистой структуры с равномерно распределенными зернами феррита. Диффузионный отжиг (гомогенизация) применяется преимущественно для круп ных стальных отливок из легированных сталей с целью выравнивания химической неоднородности зерен твердого раствора.
Нормализация отличается от полнога отжига характером охлаждения и при меняется для устранения структурной неоднородности, получения мелкозерни стой структуры.
Закалка представляет собой процесс получения структуры аустенита, тростита и применяется для отливок из стали с целью повышения твердости и требуе мых физико-механических свойств. Закалка заключается в нагреве стали до за калочной температуры, выдержке при ней и последующем охлаждении с большой скоростью.
Отпуск следует после закалки отливок из стали для получения более равно мерных структур. Осуществляется он путем нагрева стали до температуры ниже •интервала превращений, выдержки и последующего охлаждения.
Перечисленные операции выполняются в камерных и проходных печах, тех-
,140