
книги / Справочное пособие по теплотехнологическому оборудованию промышленных предприятий
..pdfОпределив параметры 1\ и dx (точка 1), можно найти количество воздуха п, добавляемого в 1 кг продуктов сгорания:
Рис. 8.22. Построение процесса сушки с рециркуляцией дымовых газов:
а —процесс в / — (/-диаграмме; б — схема |
сушки: / — камера сгорания (топка): // — смеси |
|||
тельная камера; /// — вентилятор; I V — сушильная камера; О, |
I. /'. /", 2 — сечения, соот |
|||
ветствующие состояниям сушильного агента на |
/ — d-днаграмме. |
|||
Расход дымовых газов на 1 кг испаренной влаги |
|
|||
/ = |
1000 |
|
кг/ кг нсп* влаг,ь |
|
(з __ 2) M~d~ |
||||
Расход сухих дымовых газов |
|
|
|
|
|
1000 |
|
|
|
= |
( у - 2 'Щ |
; |
кг/кг исп* влапи |
Процесс сушки с рециркуляцией дымовых газов изображен на рис 8.22. Как видно из этого рисунка, продукты сгорания органического топлива, поступающие
в камеру смешения с параметрами |
(/д.г, /д.г, и ^д.г), разбавляются атмосфер |
ным воздухом с параметрами (/о, to, |
d0). Количество атмосферного воздуха, по |
ступающего на разбавление, характеризуется п кг воздуха на 1 кг продуктов сго
рания. Значение п |
находится в соответствии |
с температурой |
tx (которая задается |
и в конце расчета |
может быть уточнена) по |
формулам (8.5) |
и (8.6). Кроме того, |
11. З а к . 2571 |
161 |
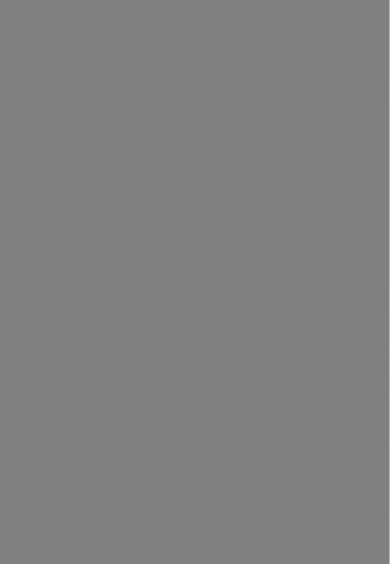
Для летних условий |
|
|
|
|
|
0,59 • 2,6! |
= 10,3 г/кг; |
dQ= 622- |
|||
|
|
1 0 0 -(0 ,5 9 - 2,65) |
|
для /0=22,2 ри=2,65 кПа [61]. |
|
||
Для зимних условий |
|
|
|
, |
_ |
0,84-0,343 |
- = 1,82 г/кг; |
d0 = |
622------ -------------------- |
||
|
|
100 — (0,84 • 0,343) |
|
при /0= - 7 ° С рп= 0,343 кПа.
Теплосодержание наружного воздуха определяем в соответствии с выраже нием (8.3):
для летних условий |
|
|
|
/о = 0,24 • 2 2 ,^4 -(5 9 5 + 0 ,4 7 - 2 2 , 2 ) - ^ 4 , 1 6 |
= |
48,173 кДж/кг; |
|
для зимних условии |
1000 |
|
|
1,82 |
|
|
|
/о = 0,24 • (—7 )+ |
|
|
|
(595 — 0,47 ■7 )- j j ^ - 4 , 16 = - 2 ,4 9 6 кДж/кг. |
|||
6. Параметры сушильного агента на входе в сушило: температура /i = 110°C; |
|||
энтальпия 1\ для летних условий |
|
|
|
Л = 0,24 - ПО+ |
10,3 |
= |
136,7 кДж/кг; |
(595+ 0,47 - ПО)- ^ - 4 , 1 6 |
|||
для зимних условий |
1,82 |
|
|
h = 0,24 - ПО+ |
|
|
|
(595 + 0,47ПО) 1000 4 ,1 6 = |
114,4 кДж/кг; |
начальное влагосрдержанне для летних условий d|=rfo=10,3 г/кг; для зимних
условий d ,= d 0=l,82 г/кг.
7. Параметр^ сушильного агента на выходе из сушила: f2=60°C, <р2=17% . Влагосодерэк'анне
d, = 622-------° ,1 7 ‘ |
19>9f |
~ |
= 22,02 |
г/кг; |
|
|||
100 — (0,1719,92) |
|
|
|
|
|
|||
при f=60°C рп = 19,92 кПа [61]. |
|
|
|
|
|
|
|
|
Энтальпия |
|
|
22 |
|
|
|
|
|
/ 2 = 0,24 • 60 + (595 + 0,47 - 60) |
-4,16= |
116,9 кДж/кг. |
||||||
|
|
1000 |
|
|
|
|
|
|
8. Составляем материальный баланс сушила. |
|
|
|
|
|
|||
Количество влажного материала на входе в сушило |
|
|
|
|||||
100 |
___ |
100 |
= |
1595 кг/ч |
(0,443 |
кг/с). |
||
- = |
1500 - |
100 — 6 |
||||||
Gi = G('сух 100 — Wi |
|
|
|
|
|
|
|
|
Количество материала на выходе из сушила |
|
|
|
|
|
|||
0 2 = GcvxTT^100-- - ' = 1500 — |
|
= |
1501 |
кг/ч |
(0,417 |
кг/с). |
||
х 100 — 1 |
100 — 0,1 |
|
|
|
|
|
|
|
Количество удаляемой влаги: |
|
|
|
|
|
|
|
|
1Р= 1595—1501 = 94 кг/ч |
(0,0261 |
кг/с). |
|
9. Производим предварительный выбор размеров барабанного сушила (диа
метр Do и длину Lo барабана).
В соответствии с табл. 8.20 принимаем значение напряжения объема бараба на по влаге W/Vx^ai кг/(м3*ч).
Объем барабана |
К=94/7 = 13,4 м3. |
II |
163 |
По рис. 8.23, используя значения <?Сух=1500; W\—W2—6; W/Vx=7, находим, что .Do= 1600 мм (L6=6—8 м).
Длина барабана
г1 3 ,4 -4
= 6,67 м.
б _ я • 1 , 62
Принимаем Lo= 8 м.
10.Составляем тепловой баланс сушила для зимних условий.
Удельный расход сухого воздуха на испарение 1 кг влаги [см. формулу (5.40)]
,1000
|
|
|
|
|
' = |
|
2 2 - 1.82 |
= 50 *г/“г м а ™ |
|
|||||
ЩШЩ |
t0 |
,3 |
2 0 |
25 |
30 |
35 |
45 |
50 |
55 |
60 |
65 |
70 |
75 |
80 |
Общий расход воздуха |
|
|
|
/.=/117=50 • 94=4700 |
кг/ч (1,31 кг/с). |
|
|
Объем воздуха на входе в сушило V\=V\/, на |
выходе из суш ила, V2 = г»2/, где |
||
«ь «2 — соответственно удельные объемы |
воздуха |
при температурах |
110 и 60 °С: |
«1 = 1,11; «2 =0,994 м3/кг. Следовательно, |
V\ —1,11 • 4700=5220 м3/ч; |
У2 =0,994Х |
X 4700=4670 м3/ч.
Расход тепла на подогрев воздуха в калорифере [см. формулу (5.32)] ?к=50(114,4+2,496) =5844,8 кДж/кг влаги.
Общий часовой расход тепла на испарение влаги (сушку)
Q=5844,8 - 94=0,5494 МДж/ч.
Определяем потерю тепла через ограждающую конструкцию сушила. Для су шил данного типа (температура сушильного агента 120— 150 °С) можно принять, что дп=200 кДж/кг исп. влаги. Подробный расчет величины qn см. в работе [116].
Составляем таблицу приходных и расходных статей теплового баланса су шила (см. табл. 8 .2 1 ).
164
Табл. 8. 21. Тепловой баланс сушила (зимние условия)
|
|
Приход тепла |
|
|
Расход тепла |
|
|||
|
|
|
реличина |
|
|
|
величина |
||
|
статья прихода |
кДж/кг |
|
статья расхода |
кДж/кг |
% |
|||
|
|
|
ИСП. |
% |
|
|
|
нсп. |
|
|
|
|
плат |
|
|
|
|
влаги |
|
1 . С атмосферным воз* |
■-124,8 |
2,04 |
1. С воздухом |
5845 |
85,88 |
||||
духом |
//о= 50(—2,496) |
//о = |
50-116,9 |
|
|||||
2. |
С влагой материала |
83,2 |
1,36 |
2. |
С материалом |
|
|
||
д - 4 ,16 = |
20-4,16 |
Go |
1501 |
|
|
||||
3. |
С материалом |
|
|
~\ЦГСм |
94 |
0,95-50 |
761,28 |
1 1 , 2 |
|
G2 |
п |
1501 Л _ |
306,18 |
5,01 |
3. |
Потерн |
в окру |
|
2,92 |
\у с м |
94 0,957-20 |
жающую среду |
200 |
||||||
4. |
От |
калорифера |
5844,8 |
91,59 |
|
|
|
|
|
|
И т о г о . . . |
6109,38 |
100 |
И т о г о . . . |
6806,28 |
100 |
Определяем невязку теплового баланса:
6806,28 — 6109
1 0 0 = 10,23%.
6806,28
Как видим, невязка баланса превышает 10 %, что является основанием для вы полнения пересчета. Изменяем параметр сушильного агента на выходе из сушила. Принимаем <р2=13 % (вместо ср2=17 %). Находим:
d. = 622-------° ' 13' *9- |
--------= |
16,53 г/кг; |
|||
- |
ю о — (0 .13 - |
19,92) |
|
|
|
/ 2 = 0,24 - 60 + |
|
|
16,53 |
|
102,75 кДж/кг; |
[595 + (0,47 - 60)] - ^ g - 4 , 16 |
|||||
|
1000 |
= |
67,98 |
кг/кг |
влаги; |
/ = |
■ 16,53— 1,82 |
£,=67,98-94=6390,2 кг/ч (1,78 кг/с);
К,=7093,12 м3/ч; 1^=6351,85 м3/ч;
Як—67,98(114,4+2,496) = 7605 кДж/кг влаги;
<3=7605 ♦94= 714 870 кДж/ч; </„=200 кДж/кг нсп. влаги.
Составляем уточненный баланс тепла для зимних условий (см. табл. 8.22). Определяем невязку баланса во втором приближении:
7946 - 7824
100= 1,54 %.
7946
Как видим, во втором приближении тепловой баланс составлен с точностью, необходимой для инженерных расчетов.
Теплоемкость материала на входе и выходе из сушила может быть найдена
более точно, чем это сделано в табл. 8.21 |
и 8.2 2 : |
|
ЮО — U7j |
\Уг |
|
°м 100 |
+ |
100 ; |
165
|
|
Табл. 8.22. Уточненный тепловой |
баланс сушила (зимние |
условия) |
|
||||
|
|
Приход тепла |
|
|
|
Расход тепла |
|
||
|
|
|
величина |
|
|
|
величина |
||
|
|
статья прихода |
кДж/кг |
% |
|
статья расхода |
кДж/кр |
% |
|
|
|
|
исп. |
|
|
|
исп. |
||
|
|
|
плагн |
|
|
|
|
влаги |
|
|
1 . С атмосферным воз |
|
|
1. |
|
С воздухом |
6984,9 |
87,90 |
|
духом |
Но = |
— 169,68 |
2,69 |
/ / 2 = |
67,98-102,75 |
||||
= |
6 7 ,98(—2,496) |
2. |
„ |
С материалом |
|
|
|||
|
2. |
С влагой материа |
|
|
G2 |
1501________ |
|
|
|
ла |
^ 4 , 1 6 = 20.4,16 |
83,2 |
1,26 |
^M V 2 = -g 4 -u ,y 5 /r-5U |
761,28 |
9,58 |
|||
|
3. |
От калорифера |
7605 |
96,05 |
3. |
|
Потери в окру |
|
2,52 |
|
|
|
|
|
жающую среду |
200 |
|||
|
|
И т о г о . . . |
7824 |
100 |
И т о г о . . . |
7946,18 |
100 |
100 — т L+ JE L
100 100
где см — теплоемкость сухого материала, кДж/(кг • К).
11.Аналогично составляем тепловой баланс сушила для летних условий
(/о=22,2 °С и ф0=59 %) при ф2= 13 %.
12.Для зимних условий определяем величину Д [см. формулу (5.35)]: Д=А,— (<7м+<7п) =20- (761,28-306,18) +200= -635,1 кДж/кг влаги.
13.Находим отношение
653,1
АД = ~~ б~ 98 = ~ 9,61 кДж/кг*
14. Определяем скорость сушильного агента в начале барабана:
ил = |
AVX |
709 3 ,1 2 |
-4 |
_ |
. |
-------------3600nd2 |
= ----------------------------- |
. 1,62 |
= 0 .9 8 |
м/с. |
|
1 |
3 6 0 0 -3 ,1 4 |
’ |
' |
15. Находим скорость сушильного агента в конце барабана:
6351,85 - 4
= 0,878 м/с.
3600 • 3,14 • 1,6*
Как видим, скорости сушильного агента находятся в допустимых пределах, что дает основание остановиться на размерах барабана, принятых в начале рас чета.
К установке принимаем стандартный сушильный барабан с Do = 1,6 и Lo— = 8,0 м (см. рис. 8.23).
9. ТЕПЛОТЕХНОЛОГИЧЕСКОЕ ОБОРУДОВАНИЕ ХИМИЧЕСКИХ ПРОИЗВОДСТВ
9.1. Классификация и описание основных технологических схем нефтеперерабатывающего производства
9.1.1. Общие сведения
Химическая промышленность является одной из важнейших отраслей народ ного хозяйства. При проектировании химических предприятий особое внимание должно уделяться выбору и конструированию тепломассообменных аппаратов, так как расчет и выбор основного оборудования тесно связаны с технологией производства и рациональным использованием топливно-энергетических ресурсов.
Нефть представляет сложную смесь парафиновых, нафтеновых и аромати ческих углеводородов. Нефтепродукты получают в результате разделения нефти на фракции и группы. Различают первичные и вторичные методы переработки нефти. Первичными называются процессы разделения нефти на фракции пере гонкой, вторичными — процессы деструктивной (или химической) переработки.
Перегонка бывает с однократным, многократным и постепенным испарением. Примером однократного испарения является нагревание смеси и испарение неф ти в трубчатой печи. Исходный продукт нагревают в змеевике печи, где он час тично испаряется, а затем направляют в испаритель (колонну), где происходит однократное отделение образовавшихся паров от жидкости. Многократное испа рение состоит из повторяющихся несколько раз процессов однократного испа рения. Образующиеся при испарении пары отделяются в несколько ступеней. На второй ступени обрабатывается жидкая фаза, оставшаяся при отделении паров, образовавшихся на первой ступени, на третьей ступени — жидкость, оставшаяся после второй ступени разделения, и т. д.
Для четкого разделения компонентов и получения заданной концентрации применяют ректификационные колонны, в которых возможно разделение много компонентных смесей на отдельные составляющие.
По техническому исполнению различают процесс перегонки при атмосфер ном давлении, в вакууме и с использованием водяного пара. В первом случае во избежание крекинга (разложения) углеводородов перегонку нефти ведут'при температуре, не превышающей 360—380 °С. При использовании в промышленно сти вакуумных колонн процесс проводят при остаточном давлении 2—15 кПа, что позволяет при 410—420 °С отобрать из мазута дистилляты с температурой кипения до 500 ^С. Для увеличения отбора дистиллятов применяют перегретый водяной пар, вводя его в нижнюю часть ректификационных колонн. Это позво ляет снизить парциальное давление нефтяных паров. Расход водяного пара зависит от молекулярного веса отгоняемых фракций, температуры перегонки и доли отгона. На практике широко используют перегонку нефти при одновремен ном применении вакуума и водяного пара. *
Существует несколько вариантов технологических схем переработки. На практике применяют три: топливный, топливно-масляный и нефтехимический (комплексный). При выборе схемы проектируемого нефтеперерабатывающего за вода учитывают качество перерабатываемой нефти, потребность экономического района в моторных и котельных топливах, маслах, технический уровень разра ботки отдельных процессов.
Принципиальная поточная схема комплексной переработки нефти на совре менном нефтеперерабатывающем заводе представлена на рнс. 9.1. Предваритель но подготовленная и обезвоженная нефть поступает на комбинированные уста новки ЭЛОУ—АВТ для обессоливания и перегонки. По схемам прямого питания в едином комплексе сосредоточены каталитический риформинг для производства
167
|
|
|
|
| Нефть |
|
|
|
|
|
|
|
|
Кот ельное |
э л о у - л в т |
н.к. - 62°с |
|
|
|
|
|
|
|
|
|
|
|
|
|
|
|
|
|
|
Остаток > 450°С топливо >350°с с Вторичной, пере |
б2-105°С |
|
|
|
|
||||
|
|
|
|
гонкой бензина |
|
|
|
|
|
|
|
|
|
| Г а з |
|
|
|
|
|
|
|
Г а з |
|
Производство |
|
|
Платформинг |
Платформинг |
Газ |
|
Газ |
|
К окс |
Коксование |
Гидрокрекинг |
|
|||||||
|
Изомеризация |
|||||||||
|
|
битума |
|
|
с гидроочисткой |
с гидроочисткой — |
|
|
||
|
|
| битум |
|
|
Компонент бензина |
( |
|
|
компонент |
|
|
|
|
|
|
|
|
|
|
бензина |
|
|
|
|
|
|
|
э _ |
|
|
|
|
Б е н зи н |
Гидроочист ка |
Га з |
|
|
|
|
Экстракция |
Бензол _ |
||
Кат алитический |
Д еп а р а ф и н и |
Толуол |
||||||||
|
бензина,газойля |
|
крекинг |
Гидроочист ка |
з а ц и я |
и разделение |
||||
|
* |
Бензин |
|
Летневг дизель-1 Зимнее дизель- |
1Жидкий |
|
|
|
|
|
Водород |
|
Газойль |
|
|
|
|
||||
|
* Hoemiопливо |
нов топливо |
пЪрафин |
Ксилолы |
|
|
|
|||
|
|
|
|
|
|
|
||||
Гидродеалкили\.экст ракт |
|
|
|
* |
|
|
|
|
|
|
Экст ракция |
Гидроочист ка |
Чет кая |
Разделение |
|
Гидродеалкили-, |
|||||
|
рование |
|
Кристаллизацией |
|
рование |
|||||
|
|
|
рект и ф и ка ц и я |
|
||||||
|
Нафталин_ |
|
|
1Реактивное |
|
I о - и м -ксилолы |
|
|
I Бензол г |
топливо |
Бензол |
Рис. 9.1. поточная схема перераооткн iieqmt.
высокооктановых бензинов, гидроочистка дизельных топлив, газофракционнрующая установка. Наличие в такой схеме процесса гидроизомеризации дизельных топлив позволяет наряду с обессериванием нормальных парафиновых углеводо родов проводить их изомеризацию для снижения температуры застывания. Для выработки высокооктановых бензинов в схеме служит процесс гидрокрекинга тяжелой бензиновой фракции. В схеме предусмотрена также выработка арома тических углеводородов. С целью подготовки сырья для пиролиза используется денормализация рафинатов. Имеется также битумное производство. Для “снаб жения гидрокрекинга водородом в схеме завода предусмотрено водородное про изводство на основе конверсии углеводородсодержащнх газов и извлечения вы сококонцентрированного водорода при низких температурах.
Существуют схемы, рассчитанные на более глубокую нефтехимическую пе реработку.
Рассмотрим подробнее отдельные этапы переработки нефти.
9.1.2.Технология процесса обессоливания
иобезвоживания
На нефтеперерабатывающие ьаводы нефть поступает с содержанием воды примерно 5 %. Количество растворенных в ней солей может доходить до не скольких граммов на литр. Большая часть воды находится в нефти в виде мел кодисперсных капелек. Есть несколько методов разрушения нефтяных эмульсий: механические (отстой, центрифугирование, фильтрация), химические (основанные на применении деэмульгаторов) и электрические. Последние два могут комбини
роваться вместе.
Электрообессоливаиие производится на установках ЭЛОУ. Схема электро обессоливающей установки представлена на рис. 9.2 . Производительность уста новки: по сырой нефти 2 050 000 т/год, по обессоленной нефти 2 000 000 т/год; степень обезвоживания и обессоливания: для сырой нефти: Н20 2 %, солей 5000 мг/л; после первой ступени Н20 0,5 %, солей 250 мг/л; после второй ступени: Н20 0,5 %, солей 20 мг/л; расход воды (% по весу нефти) 11,5 %; расход едкого натра 0,1 %; расход водяного пара 10—20 т/ч; расход электроэнергии 682 кВт-ч.
Рис. 9.2. Схема электрообессолнвающен установки.
Сырая нефть, подлежащая обессоливанию, забирается одним из сырьевых насосов HI н подается в трубчатые теплообменники 77, где нагревается до 20— 50 °С за счет тепла уходящей с установки нефти. Из теплообменников нефть поступает в паровой трубчатый подогреватель, где происходит ее нагрев мятым паром до 70—95 °С. Затем нефть поступает в электродегидратор первой сту пени Э1. На линии от паровых подогревателей до электродегидратора находится смесительный клапан, в котором посредством перепада давлений устанавливается требуемая степень смешения сырой нефти с водой, нагретой до 70—95 °С, и реа гентом— раствором едкого натра. Смесь нефти, воды и реагентов поступает в электродегидратор, где создается электрическое поле. Регулирование равно мерной подачи нефти через каждую головку осуществляется дифманометрами. Отстоявшаяся в электродегидраторе вода с растворенными в ней солями (соля ной раствор) автоматически удаляется через смотровой фонарь Ф1.
Частично обезвоженная и обессоленная нефть из верхней части электроде гидратора Э1 поступает в электродегндратор второй ступени Э2. В линию нефти от Э1 до Э2 перед смесительным клапаном подается горячая вода. Работа элек тродегидратора второй ступени аналогична работе электродегидратора первой ступени.
С верхней части Э2 обезвоженная и обессоленная нефть, пройдя теплооб менники 77, при температуре около 40 °С поступает в промежуточную емкость £7, откуда насосом Н2 откачивается из установки. Вода на обе ступени обес соливания подается одним из насосов НЗ из линии технического водопровода. Подогрев воды производится в трубчатых подогревателях мятым водяным па ром. Давление и уровень воды в электродегидраторах поддерживается автома
тически. |
Также автоматически |
регулируется подача |
нефти, |
воды и реагента. |
В случае |
нарушения работы |
электродегидратора |
эмульсия |
направляется в |
емкость. Отстоявшаяся нефть из Е2 поступает на вход насоса Н1 и подается на повторную переработку. Давление в электродегидраторе Э1 — 0,55 МПа, в Э2 — 0,4 МПа.
После обессоливания нефть поступает на установки первичной переработки нефти АВТ.
9.1.3. Технология первичной переработки нефти
На типовых нефтеперегонных заводах (НПЗ) единичная мощность установок АВТ достигает 6—12 млн. т в год перерабатываемой нефти. В перспективе пред полагается строительство еще более мощных установок. Ассортимент и количе ство получаемых на АВТ фракций должны обеспечивать все производства НПЗ. Для снижения затрат на транспортировку готовой продукции способ переработки нефти выбирается с учетом народнохозяйственных потребностей района, приле гающего к НПЗ. Наименьшее число фракций отбирается при чисто топливном варианте (бензил, керосин, дизельное топливо, вакуумный газойль — сырье для каталитического крекинга или гидрокрекинга и остаток, добавляемый в котель ное топливо или используемый как сырье установок коксования, гидрокрекинга, получения битума). Как при топливном, так и при нефтехимическом вариантах переработки нефти в схему АВТ необходимо включать вторичную перегонку бензина с получением сырья для каталитического риформинга или для выделения бензольной, толуольной и ксилольной фракций.
При переработке высококачественной нефти товарную продукцию получают непосредственно на АВТ. В этом случае соответствия свойств фракции требо ваниям ГОСТа добиваются путем изменения пределов отбора фракций. Однако в большинстве случаев фракции, полученные на установках АВТ, являются сырь ем для установок платформинга, изомеризации, гидроочистки, каталитического крекинга, гидрокрекинга, коксования, масляных и битумных производств. В этих случаях качество отбираемых фракций определяется межцеховыми нормами.
Таким образом, вопрос о качестве отбираемых на АВТ фракций многоварнантен и решается методом подбора в зависимости от отмеченных условий.
Технологическая схема установки должна обеспечивать получение принятого ассортимента продуктов из заданного сырья наиболее экономичным способом. Схема АВТ выбирается на основании оптимальной мощности установки, целесо-
170