
книги / Справочное пособие по теплотехнологическому оборудованию промышленных предприятий
..pdfТабл. 9.1. Технико-экономические показатели установок АВТ [76]
Расход топлива (жидкого), кг |
38,50 |
30,7 |
27,70 |
Расход электроэнергии, кВт-ч |
2,62 |
2,26 |
3,97 |
Расход воды, м3 |
21,70 |
15,50 |
4,47 |
Расход водяного пара, МДж |
461 |
377 |
— |
Расход металла на аппаратуру, кг |
1,86 |
1,64 |
0,58 |
Эксплуатационные расходы, руб/год |
1,00 |
0,79 |
0,44 |
Капитальные расходы, руб. |
1,76 |
1,30 |
1,05 |
образности комбинирования АВТ с другими установками, схемы размещения оборудования. Схема должна обеспечивать большую глубину отбора, четкость фракционирования, гибкость процесса, большой межремонтный пробег и высокие технико-экономические показатели.
Существующая в настоящее время при проектировании и строительстве тен денция к укрупнению технологических установок объясняется улучшением тех нико-экономических показателен с ростом их мощности (табл. 9.1).
Экономически целесообразным является также комбинирование технологи ческих установок, при этом уменьшаются протяженность коммуникаций, расход топлива, энергии и металла, занимаемые площади, численность обслуживающего персонала, облегчается использование вторичных эиергоресурсов и автоматиза ция технологических процессов.
В СССР и за рубежом на НПЗ наиболее часто применяют такие комбина ции: ЭЛОУ—АВТ, АВТ — вторичная перегонка бензина, ЭЛОУ—АВТ — вторич ная перегонка бензина. В последнее время в нашей стране практикуется объеди нение установок каталитического риформинга, гидроочистки реактивного и ди зельного топлива, газофракционировання.
Для атмосферного блока АВТ характерны следующие три схемы: 1) с одной сложной ректификационной колонной; 2 ) с предварительным испарителем н рек тификационной колонной; 3) с предварительной отбензшшвающсй и основной ректификационной колонной.
Наиболее широко в. отечественной практике применяется третья схема, основ ными преимуществами которой являются гибкость и универсальность при пере работке различных сортов нефти. Кроме того, наиболее коррозионно-активные вещества удаляются через верх первой колонны, и тем самым осуществляется защита от коррозии основной колонны. Благодаря предварительному удалению бензиновых фракций в змеевиках печи и теплообменниках не создается большого давления, что дает возможность применять более дешевое оборудование. К недо статкам схемы можно отнести высокую температуру нагрева нефти в печи, срав нительно большое количество дополнительной аппаратуры (колонна, насосы печ ные и орошения, конденсаторы-холодильники и т. д.), конструктивную сложность, в некоторой степени громоздкость.
На рис. 9.3 представлена принципиальная схема атмосферно-вакуумной уста новки с вторичной перегонкой бензина. Диапазон мощности ее 1—3,6 млн. т/год. Установка служит для атмосферной перегонки нефти, вакуумной перегонки мазу
та и вторичной |
перегонки |
бензиновой фракции |
на узкие. |
При использовании |
||||||
в качестве сырья ромашкинской нефти |
выход |
составляет: |
сухой |
газ— 1 %; |
||||||
фракция |
ниже |
62 °С — 12 %; |
фракция |
62 — 85°С — 2,7 %; |
фракция |
85— |
||||
120 “С — 4,3 %; |
фракция |
120-140 °С — 3,2 %; |
фракция |
140—160 °С — 6,4 %; |
||||||
фракция |
180—240 °С — 9,9 %; |
фракция |
240—350 °С — 17 %; |
фракция |
350— |
|||||
460 °С — 17,8 %; остаток выше 460 °С — 35 %; потерн — 0,7 %. |
|
|
|
|||||||
Главные секции установки: предварительная эвапорацня (колонна К1, сек |
||||||||||
ция П1)\ |
атмосферная перегонка (колонны К2, Кб, К7, секция П1)\ |
вторичная |
перегонка широкой фракции на узкие (колонны КЗ, К4, Кб, печь /72); вакуумная перегонка мазута (колонна КЮ, печь ПЗ).
171

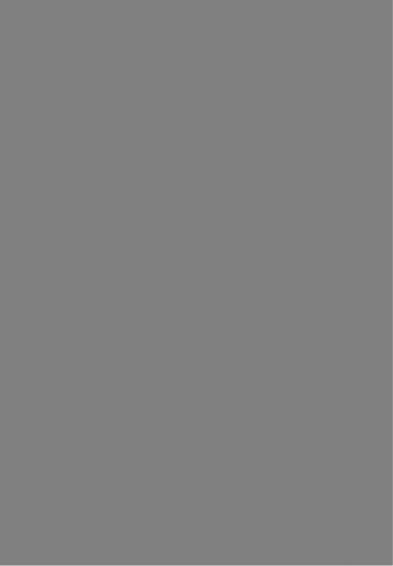
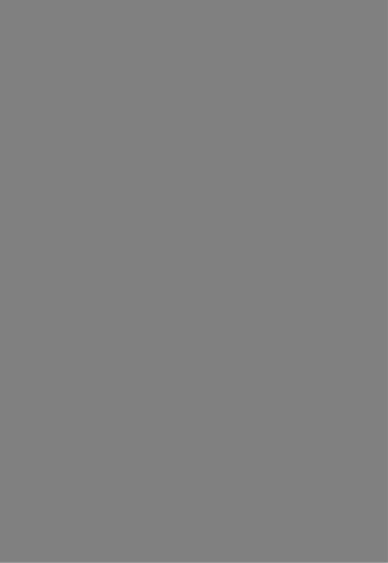
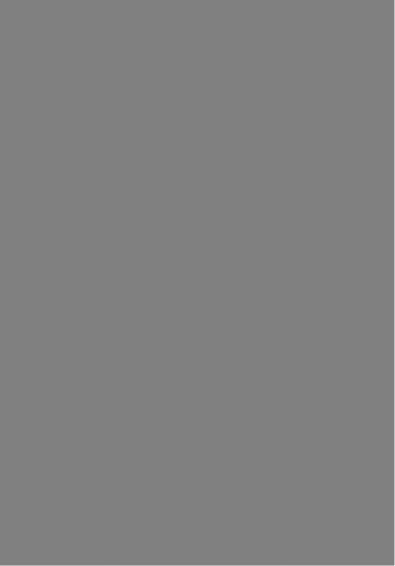
слое пылевидного катализатора. Продукты реакции с верхней части реактора поступают в ректификационную колонну К1 под отбойные тарелки. В нижнюю часть колонны подается острый водяной пар. С верхней части колонны газовые фракции и пары бензина и воды поступают в конденсатор-холодильник 77 по гружного типа, а затем конденсат и газ — в газосепаратор КЗ.
Сверхней части колонны КЗ отводится газ, сбоку насосом Н7 часть бен зина подается в качестве острого орошения в колонну К1, а снизу КЗ балансовое количество бензина откачивается насосом Н6 на компаундирование. Легкий га зойль отходит из колонны К1 боковым погоном и поступает в отпарную колонну К2. Снизу колонны К2 легкий газойль забирается насосом Н5 и через теплооб менник и холодильник Т5 откачивается из установки.
Снижней ректификационной тарелки колонны К1 насосом НЗ забирается продукт, который подается в стояк реакторной системы, где дополнительно на гревается, проходя через регенератор Р2, и поступает в зону реакции регене ратора.
Снизу колонны К1 насосом Н4 забирается тяжелый газойль, который после
охлаждения в теплообменнике ТЗ и холодильнике Т4 откачивается из установки. Отработавший катализатор из реактора самотеком поступает в отпарную зо ну, куда подается острый водяной пар. Последний вместе с десорбированными
скатализатора фракциями идет в зону реакции реактора Р1, а закоксованный катализатор по центральному стояку— в регенератор Р2; компрессором Н2 по специальному маточнику подается воздух, кислородом которого кокс выжигается
скатализатора. Продукты сгорания выводятся из зоны регенерации через ды мовую трубу в атмосферу, а регенерированный катализатор по периферийным
стоякам вместе с потоком свежего сырья возвращается в зону реакции реакто ра PJ. Основные показатели рассматриваемой установки [53]: температура в ре акторе 475—510 °С; давление в реакторе 0,06—0,14 МПа; температура в регене раторе 570—650 .°С; давление в регенераторе 0,1—0,2 МПа; отношение катализа
то р -п р о д у кт 20: 1; |
расход электроэнергии 42,4 кВт-ч; расход |
пара |
16,7 кг, |
|
расход охлаждающей |
воды |
8,85 м3, расход катализатора 0,64— 1,28 кг. |
является |
|
Назначением установки |
гидрокрекинга с кипящим слоем (рис. |
9.6) |
переработка остаточного и тяжелого дистиллированного нефтяного сырья с целью получения малосернистых нефтепродуктов: бензина, реактивного и дизельного топлив, котельного топлива. Сырьем могут служить мазут, гудрон, тяжелые ва куумные газойли, газойли коксования (обычно из сернистой нефти). Выход про дуктов гидрокрекинга меняется в широких пределах в зависимости от глубины процесса и перерабатываемого сырья.
Установка состоит из нагревательно-реакционной части — трубчатой печи, реактора, системы очистки и циркуляции водородсодержащего газа (газосепа ратор высокого давления, очистная колонна осушки, водородный компрессор) — и блока газо- и погоноразделения (газосепаратор низкого давления, стабилиза ционная колонна, колонна перегонки гмдрогенизата).
Сырье смешивается с циркулирующим и свежим водородсодержащим газом н через систему теплообменников 77 и нагревательную печь 771 поступает под распределительную решетку реактора Р1 с кипящим слоем сероустойчивого ка тализатора типа А1—Со—Мо.
В кипящем слое катализатора, создаваемом газожидкостным потоком, осу ществляется процесс гидрокрекинга. Продукты реакции отдают свое тепло в теплообменниках 77 и конденсаторах-холодильниках Т2 и поступают в сепара тор высокого давления £7, где отделяется циркулирующий водородсодержащий газ. После очистки от H2S и осушки (на схеме колонна сушки не показана) газ возвращается компрессором Н2 для смешивания с сырьем.
Катализат снизу сепаратора Е1 после сброса давления перетекает в сепа ратор Е2, где происходит выделение растворенного углеводородного газа и час
тично от H2S. Жидкий катализат после подогрева в подогревателе |
ТЗ поступает |
||
в |
стабилизатор К2 для выделения бутанов. Стабильный |
катализат‘нагревается |
|
в |
печи 172 и разделяется на бензин, легкий и тяжелый |
газойли |
в колонне КЗ |
(на схеме опущены отпарная колонна для вывода легкого газойля, а также си стема конденсации бензина и орошения колонны). Тяжелый газойль с нижней части колонны КЗ насосом Н4 может возвращаться на гидрокрекинг или откачи ваться через холодильник Т4. Регенерация катализатора осуществляется период-
17 6
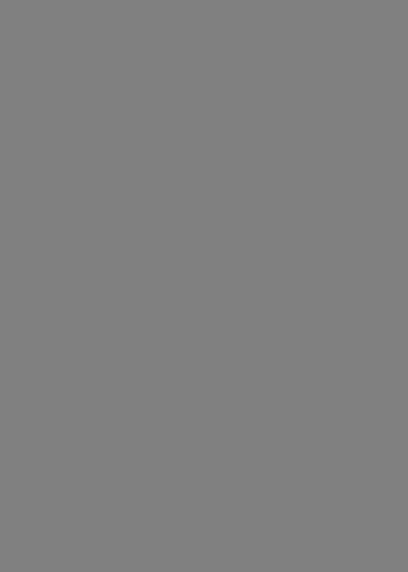
Рис. 9.7. Схема взаимосвязи производств |
азотнотукового комбината: |
|
||||||
/ — группа газопых |
цехов; 2 — цех синтеза |
аммиака; |
3 — цех |
метанола и |
высших |
спиртов; |
||
■4 — цех карбамида; |
5 |
— цех производства |
разбавленной азотной кислоты; |
6 — цех |
аммиач |
|||
ной селитры; 7 — цех |
производства |
комплексных удобрений |
(нитрофоски); в — цех произ |
|||||
водства концентрированной азотной |
кислоты; 9 — цех производства натриевой селитры. |
рованную азотную кислоту. При получении разбавленной азотной кислоты под атмосферным давлением остаточные окислы азота, не переработанные в кислоту, используются для производства натриевой и кальциевой селитры.
Основным углеводородным сырьем АТК является природный газ. Перера ботка природного газа в синтез-газы включает реакции конверсии СН4 и СО, процессы очистки от СО2 и СО (синтез аммиака), дозировку азота для синтеза аммиака и сжатия газовых смесей до давления синтеза.
9.2.2. Технологическая схема цеха конверсии метана и окиси углерода
Назначением цеха конверсии СН4 и СО азотнотукового производства являет ся получение сухой и охлажденной газовой смеси, состоящей из водорода и угле кислого газа. Исходными продуктами химической реакции для получения га зовой смеси являются природный газ, кислород и водяной пар.
Рассмотрим одну из возможных технологических схем цеха конверсии (рис. 9.8) [26]. Смесь природного газа и синтез-газа направляют в сатурационную башню J, которая представляет контактный теплообменник насадочного типа для нагрева смеси газов. Горячим теплоносителем является вода. Из сатурационной башни парогазовая смесь поступает в вертикальный кожухотрубный тепло обменник 2, где она нагревается до 500 °С за счет тепла конвертированного газа, поступающего в аппарат из увлажнителя 5 при температуре 600 °С. Далее паро газовая смесь направляется в смеситель 4, где в нее добавляется кислород. Обо гащенная кислородом газовая смесь далее поступает в конвертор метана 3, где в результате экзотермической реакции между метаном и кислородом образуются
углекислый |
газ |
и водород. На выходе из конвертора газ имеет |
температуру |
||
900 °С. |
|
|
|
|
|
Газ из конвертора поступает в увлажнитель, в котором в поток газа вво |
|||||
дятся конденсат и пар, |
при этом происходит охлаждение газа |
до |
600 °С. Пар |
||
необходим |
для |
реакции |
окисления в конверторе окиси углерода. |
После увлаж- |
178
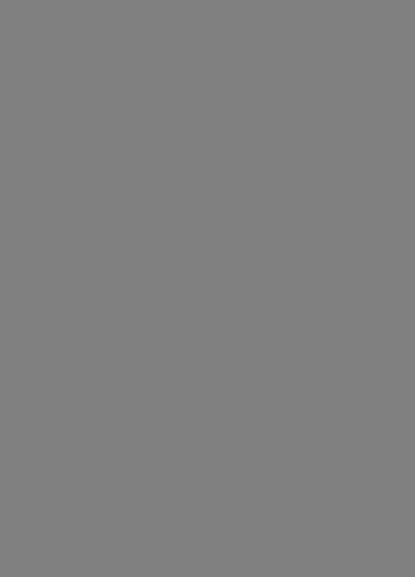
сокой температуры и высокого давления в присутствии катализатора вступают ъ реакцию, и в результате образуется аммиак (NH3). Газообразный аммиак после колонны синтеза следует в водяной конденсатор 5, служащий для охлаждения аммиака и непрореагнровавшей азотно-водородной смеси. Охлаждение газов лроизводится циркуляционной водой и водяным конденсатом. Охлажденная азотно-водородная смесь с частицами аммиака поступает из водяного конденса тора в сепаратор 7, при этом капли жидкого аммиака отделяются от потока газа и стекают вниз. Жидкий аммиак отводится в сборник, а азотно-водородная смесь подается на всасывание циркуляционных компрессоров.
Рис. 9.9. Технологическая схема работы цеха синтеза аммиака и метанола.
Около 96—97 % выработанного аммиака выходит в жидком безводном со стоянии, а оставшийся — в виде 25%-ного водного раствора.
Синтез метанола происходит аналогично. Метанол-сырец, имеющий концент
рацию 94 %, подвергается ректификации (тщательной очистке от легких |
газо |
образных примесей). Концентрация метанола после ректификации |
дости |
гает 99,66 %. |
|
9.2.4. Производство карбамида |
|
Процесс производства карбамида можно |
разделить на |
следующие стадии: |
||
сжатие углекислого газа до давления 2 МПа; |
фильтрация, охлаждение и подача |
|||
жидкого аммиака в |
колонны синтеза |
под давлением 20 МПа; |
синтез карбамида |
|
в колоннах синтеза |
под давлением |
18—20 МПа при температуре 170—205 °С; |
дистилляция плава карбамида (разложение остаточного карбоната аммония и погона избыточного аммиака); фильтрация водного раствора карбамида и вы паривание в пленочном аппарате непрерывного действия; грануляция (превраще ние плава карбамида в мелкие зерна) и сушка; расфасовка и охлаждение гото вого продукта. Одна из возможных технологических схем получения карбамида представлена на рис. 9.10.
Сжатие углекислого газа производится группой поршневых пятиступенчатых компрессоров. Компрессоры устанавливаются в отделении компрессии цеха син теза и дистилляции и подключаются к общему коллектору, из которого углекис лый газ под давлением 18—20 МПа подается в колонну синтеза. Подача жид кого аммиака в колонны синтеза осуществляется насосом со склада аммиачного производства. Жидкий аммиак проходит через фильтр, буферные сосуды и по ступает в холодильник технологического аммиака, где вследствие испарения в межтрубном пространстве температура аммиака понижается примерно до 50 °С. Уровень жидкого аммиака в буферных сосудах поддерживается постоянным.
180