
- •ОГЛАВЛЕНИЕ
- •ПРЕДИСЛОВИЕ
- •ВВЕДЕНИЕ
- •УСТОЙЧИВОЕ РАЗВИТИЕ
- •1.1. РЕСУРСЫ И ОКРУЖАЮЩАЯ СРЕДА
- •1.1.1. Т. МАЛЬТУС И ПЕРВАЯ ОЦЕНКА ПРИРОДНЫХ РЕСУРСОВ
- •1.1.2. КРИЗИСЫ РЕСУРСОВ
- •1.1.3. ОКРУЖАЮЩАЯ СРЕДА И ЭКОЛОГИЯ
- •1.2.2. ДЕМОГРАФИЧЕСКИЙ КРИЗИС
- •1.2.4. ЭНЕРГЕТИЧЕСКИЙ КРИЗИС
- •1.2.5. ГЛОБАЛЬНЫЙ КРИЗИС ЦИВИЛИЗАЦИИ
- •1.3. СТРАТЕГИЯ УСТОЙЧИВОГО РАЗВИТИЯ
- •1.3.1. ОБЩИЕ ПОДХОДЫ
- •1.3.2. УСТОЙЧИВОЕ РАЗВИТИЕ - ИМПЕРАТИВ XXI века
- •РЕСУРСО-ЭКОЛОГИЧЕСКАЯ КОНЦЕПЦИЯ СОЦИАЛЬНО-ЭКОНОМИЧЕСКОГО РАЗВИТИЯ
- •2.1. СУЩНОСТЬ РЕСУРСО-ЭКОЛОГИЧЕСКОГО ПОДХОДА
- •2.2. БИОСФЕРНЫЙ РЕСУРС
- •2.2.1. СОДЕРЖАНИЕ ПОНЯТИЯ
- •2.2.2. БИОЛОГИЧЕСКИЙ ПОДРЕСУРС
- •2.2.3. ХИМИЧЕСКИЙ ПОДРЕСУРС
- •2.2.4. ФИЗИЧЕСКИЙ ПОДРЕСУРС
- •2.3. РЕСУРСЫ
- •2.3.1. КЛАССИФИКАЦИЯ РЕСУРСОВ
- •2.3.2. ПРИРОДНЫЕ РЕСУРСЫ
- •2.3.3. МИНЕРАЛЬНЫЕ РЕСУРСЫ
- •2.3.4. ТОПЛИВНО-ЭНЕРГЕТИЧЕСКИЕ РЕСУРСЫ
- •ТЕХНОСФЕРА И ТЕХНОГЕННЫЕ РЕСУРСЫ
- •3.1. ТЕХНОСФЕРА
- •3.2. ТЕХНОГЕННЫЕ РЕСУРСЫ
- •3.2.1. ЭЛЕМЕНТОПОТОКИ В ТЕХНОСФЕРЕ
- •3.2.4. ТЕХНОГЕННЫЕ РЕСУРСЫ
- •ОСНОВЫ ТЕОРИИ УПРАВЛЕНИЯ МАТЕРИАЛЬНЫМИ РЕСУРСАМИ
- •4.1. ОСНОВНЫЕ ЗАКОНЫ И ПРАВИЛА УПРАВЛЕНИЯ РЕСУРСАМИ
- •4.1.2. ПРАВИЛО КОНКУРЕНТНОГО ИСПОЛЬЗОВАНИЯ РЕСУРСОВ
- •4.1.6. ЗАКОН “ШАГРЕНЕВОЙ КОЖИ”
- •4.1.7. ЗАКОН НЕУСТРАНИМОСТИ ОТХОДОВ И/ИЛИ ПОБОЧНЫХ ВОЗДЕЙСТВИЙ ПРОИЗВОДСТВА
- •4.1.8. ПРАВИЛА МЕРЫ ПРЕОБРАЗОВАНИЯ ПРИРОДНЫХ СИСТЕМ
- •4.1.11. ЗАКОН ЛИМИТИРУЮЩЕГО РЕСУРСА
- •4.1.13. “ВЕНОК ЗАКОНОВ” КОММОНЕРА
- •4.2. ПРОБЛЕМЫ И ПРАВИЛА СУММИРОВАНИЯ РЕСУРСОВ
- •4.4. ЖИЗНЕННЫЙ ЦИКЛ ИЗДЕЛИЯ
- •4.5. ЭКОБАЛАНСЫ И МЕТОДИКА ИХ РАСЧЕТА
- •4.5.1. ПРИНЦИПИАЛЬНАЯ РАСЧЕТНАЯ СХЕМА И ИСХОДНАЯ ИНФОРМАЦИЯ ДЛЯ СОСТАВЛЕНИЯ ЭКОБАЛАНСА
- •ПРИЛОЖЕНИЕ 3
- •ПРИЛОЖЕНИЕ 4
- •ЭКОЛОГИЧЕСКИ ЧИСТОЕ ПРОИЗВОДСТВО
- •5.2. ЭНЕРГОПОТРЕБЛЕНИЕ
- •5.4. ОЦЕНКА ВЫБРОСОВ В ОКРУЖАЮЩУЮ СРЕДУ
- •ЛИТЕРАТУРА
- •ПРОМЫШЛЕННОСТЬ И ОКРУЖАЮЩАЯ СРЕДА
При обработке данных принято, что 1 км3 сброшенных загрязненных вод соответствует 1 млн т выбросов. Государственный доклад не содержит некоторых необходимых, с нашей точки зрения, данных, поэтому мы ссыла емся на сведения 1993 г.
Анализируя данные табл. 3.5, нужно учитывать следующее:
сведения, полученные из различных источников могут существенно от личаться. Так, по данным Госкомстата РФ выбросы предприятий газовой промышленности в 1997 г. составляли 451,135 тыс. т, а по данным Минтоп энерго - 2345,2 тыс. т, что в 5,2 раза больше.
Выбросы предприятий военно-промышленного комплекса и ущерб, причиняемый окружающей среде вооруженными силами, оценены неточно и явно занижены.
Компоненты выбросов имеют разные показатели токсичности, их сум мирование не дает полной картины воздействия на окружающую среду. Кроме того, отсутствуют данные о выбросах суперэкотоксикантов, таких как шестивалентный хром (лидер - химическая промышленность), тяже лых металлов (например, отходы гальванического производства), хлорсо держащих соединений (химическая, деревообрабатывающая и целлюлознобумажная промышленности), соединений фтора (угольная промышлен ность), пестицидов (сельское хозяйство) и др.
Однако приведенные данные позволяют подтвердить разделяемое боль шинством экспертов мнение о том, что наибольшее негативное влияние на окружающую среду оказывают жилищно-коммунальное хозяйство, транс порт, энергетика, химическая промышленность и сельское хозяйство. Все большую озабоченность вызывают последствия быта человека.
3.2.ТЕХНОГЕННЫЕ РЕСУРСЫ
3.2.1.ЭЛЕМЕНТОПОТОКИ В ТЕХНОСФЕРЕ
Основой современного подхода как к оценке эффективности использо вания различного рода ресурсов, так и к оценке техногенного воздействия производств на окружающую природную среду (как это уже отмечалось ра нее) является принцип построения ресурсных циклов, или круговоротов ма териалов. Такой подход позволяет наиболее четко проследить причинноследственные связи многофакторных природно-техногенных процессов.
В современный технический язык прочно вошли термины “ресурсный цикл”, “энергопроизводственный цикл”, “биосферный ресурсный цикл”, “от колыбели до могилы”. Некоторые из них широко используются средствами массовой информации и употребляются на бытовом уровне. После того как были сформулированы понятия и рассчитаны круговороты ряда химиче ских элементов - азота, серы, углерода и др., имеющих особое значение для органических процессов, происходящих на нашей планете, следующим логи ческим шагом в этой тенденции является введение понятия “потока химиче ского элемента”, или “элементопотока”*
Необходимость такого подхода вытекает из следующих соображений. В современных условиях все большее, а часто и определяющее значение, как
Термин “элементопоток” предложен П.И. ЧерноуСовым.
- /
- 2
Рис. 3.5. Принципиальная схема элементопотока:
I - производственный рециклинг материалов и ВЭР; 2 - глобальный рециклинг
ввопросах формирования структуры изделий и влияния на качество продук ции, так и при образовании выбросов суперэкотоксикантов, играют примес ные или, иными словами, микроэлементы, присутствующие в техногенном материале иногда в количестве всего лишь нескольких граммов на тонну материала. Окружающая человека среда становится наиболее сложной по номенклатуре химических соединений и материалов, не свойственных среде природной, и этот процесс развивается все более стремительно. В этих ус ловиях необходимо иметь не только максимально достоверную информа цию о происходящих технологических процессах, но и надежную основу для анализа и прогноза возможных социальных последствий принимаемых тех нических решений. Надежность в подобном анализе может обеспечить только учет движения в рассматриваемой системе каждого химического элемента независимо от его количества, базирующийся на балансовом ме тоде исследования и подтвержденный термодинамическими расчетами со става всех образующихся в системе фазовых составляющих. Количествен ная оценка этого движения выражается в виде элементопотока.
Таким образом, под техногенным элементопотоком мы будем понимать все количественно определенные параметры движения химического эле мента по технологической цепочке начиная от его извлечения из сплошной природной среды (недр) и включающие транспорт сырья и продукции, про изводство энергии и все технологические стадии производства и потребле ния продукта, все формы обращения с отходами производства и потребле ния, в том числе их рециклинг и депонирование, а также распространение исследуемого элемента с выбросами во все природные среды.
В самом общем виде элементопоток, на примере элемента, извлекаемо го из природной среды в составе твердого минерала (такая форма извлече
ния наиболее распространенная), может быть представлен в виде схемы (рис. 3.5).
Данная схема элементопотока в самой полной мере отражает приведен ное выше его определение и демонстрирует глобальный характер распреде ления элемента. Однако в зависимости от цели и глубины проводимых ис следований можно строить и другие схемы элементопотоков, например:
- для отдельных составляющих на стадиях добычи и подготовки ресур
сов к потреблению, транспортировки, производственной или бытовой сфе ры и т.п.;
-Для различных регионов - добывающего, производственного, энергопро изводящего, и территорий, используемых для складирования отходов и т.д.;
- для конкретных производственных подразделений, в том числе отдель ных агрегатов и т.п.
В отличие от глобального эти элементопотоки можно определить кяк локальные (или региональные, если речь идет о построении его по геогра фическому положению). Кроме того, элементопотоки с учетом временного фактора могут подразделяться на среднесуточные, среднемесячные, средне годовые, “мгновенные” и т.п., а также интегральные - за определенный пе риод, например, за время функционирования какого-либо производственно
го предприятия, с момента основания какого-либо региона или промышлен ного центра и т.д.
Возможны различные формы выражения элементопотока: графиче ская, табличная, аналитическая и т.п.
Рис. 3.6. Подразделение химических элементов
Остановимся сщс на одном важном методическом вопросе, а именно подразделении химических элементов на макро- и микроэлементы (рис. 3.6). Как правило, к макроэлементам относят элементы, которые:
- определяют пространственное существо предмета своим количествен
ным присутствием в нем; - существенным образом влияют на ход процессов добычи, производст
ва, потребления или эксплуатации продукта, определяя технико-экономиче ские показатели упомянутых стадий техногенных преобразований природ ных ресурсов.
В количественном выражении можно принять, что к макроэлементам относятся те, содержание которых в рассматриваемом продукте (или систе ме) превышает около 0,01 масс.%. Если содержание элемента составляет менее 0,01 масс.%, то его можно условно отнести к категории микроэлемен тов. Отметим, что в специальной литературе микроэлементы часто подраз деляются на “микропримесные” - существенным образом влияющие на свойства и количественные характеристики продукта, и “следовые”, - со держание которых настолько незначительно, что их присутствие никак не влияет ни на какие из известных в настоящее время потребительских или токсических характеристик продукта.
Детальное рассмотрение элементопотоков проведем на примере индуст рии черных металлов - отрасли, которая является крупнейшим производи телем и переработчиком материалов, а продукция отрасли —сталь, чугун и железо - основными конструкционными материалами.
3.2.1.1. ПРИНЦИПЫ ПОСТРОЕНИЯ СХЕМЫ ДВИЖЕНИЯ ЭЛЕМЕНТОВ
НА ПРИМЕРЕ ЧЕРНОЙ МЕТАЛЛУРГИИ
В зависимости от количества и роли, которую играет химический эле мент в рассматриваемой металлургической системе, его принято относить к элементам^ основы, макроили микропримесям. Применительно к процес сам черной металлургии мы в дальнейшем будет относить;
- к макроэлементам: железо, углерод, кислород, азот, водород, кальций, кремний, алюминий, магний, марганец, фосфор, серу, цинк, калий и натрий.
ачиная с первого, девять элементов являются обязательными составляющи ми любой металлургической системы, мы их будем называть элементами “ос
новы”. Марганец, фосфор и сера - элементы, определяющие свойства готово го металлопродукта, и поэтому контролируются на всем протяжении техноло гического цикла и включаются во все стандарты или сертификаты на изделия из железа. Обычно эти элементы относят в черной металлургии к макропримесным. Калий и натрий играют важнейшую роль в процессах формирования металлургических шлаков, а также совместно с цинком существенным образом влияют на показатели процессов производства первичного металла (главным образом чугуна) и стойкость огнеупоров доменных печей. В связи с этим хими ческому анализу на содержание цинка, калия и натрия, как правило, подверга ются все шихтовые материалы, поступающие на металлургическое предпри ятие (прежде всего, коксующиеся угли, железорудные материалы, флюсы);
- к микропримесям - все остальные химические элементы периодиче ской системы. Установлено, что в металлургических материалах могут при сутствовать в количестве от долей до десятков тысяч ppm (г/т материала) химические элементы, относящиеся ко всем группам периодической систе мы за исключением инертных газов и трансурановых элементов.
Поступая в металлургический передел в составе шихтовых материалов
игазов, макро- и микроэлементы могут:
1.Переходить в готовые продукты металлургического производства, как собственно в изделия из железа, так и в попутные продукты, например,
вметаллургические шлаки или материалы, получаемые в процессе коксохи мического производства и т.п.
2.Попадать в отходы производства (в основном в золы и шламы ТЭС, а так же сталеплавильные шлаки и шламы), которые в настоящее время складируют ся в золошламонакопителях в условиях России, как правило, без сортировки.
3.Накапливаться в металлургических агрегатах в составе гарнисажа, на стылей и т.п.
4.Переходить в шламы в процессе газоочистки, в окалину и другие ма териалы с формированием контура циркуляции внутри металлургического цикла при утилизации этих материалов в агломерационном процессе (а так же и в доменном, конвертерном и т.п.).
5.Выноситься в окружающую среду (атмосферу) в виде газов или возго нов, неулавливаемых очистными устройствами.
Для микроэлементов существует также возможность накопления в так называемых циркуляционных контурах, которые формируются во внутрен нем пространстве металлургических агрегатов в результате возгонки эле ментов при высоких и последующей конденсации при низких температурах.
Основой для определения параметров элементопотока на стадии метал лургических технологических операций является схема движения основных металлургических материалов (см. раздел. 4.5).
3.2.1.1,1. Современные представления о роли микроэлементов в металлургии железа
Последнее десятилетие двадцатого столетия в металлургии развитых индустриальных стран выявило целесообразность производства материа лов, особо чистых по содержанию примесей всех видов.
Это относится как к производству полупродуктов (например, чугуна, ферро сплавов, жидкой стали), так и готовой продукции (проката, специальных сталей,
товарного чугуна), в которых содержание некоторых микропримесей ограничи вается в пределах 1-50 г/г материала. К таким микропримесям относятся как хо рошо известные и изученные металлургами никель, медь, ванадий, хром, сви нец, мышьяк, бор и прочие, так и до настоящего времени малоизвестные - тел лур, селен, висмут и др. На сегодняшний день цена особо чистых металлургиче ских материалов на мировом рынке в 1,5-2 раза превышает цену рядовой про дукции. В соответствии с упомянутой тенденцией развивался горнорудный ком плекс стран производителей металлургического сырья, совершенствовались структура подготовки сырья к плавке, внедрение технологий рафинирования и специальной обработки жидкого металла (обессеривания, обескремнивания, дефосфорации и т.п.). Рассмотрим сложившуюся ситуацию более подробно.
В зависимости от химического и минералогического составов и предысто рии термообработки исходных шихтовых материалов и продуктов металлур гических переделов микроэлементы могут присутствовать в чугунах и сталях в твердом растворе, в виде продуктов ликвации, кристаллизации из расплава или выделений из твердого раствора и т.п. Как правило, существенное влияние микропримесей на свойства металла связано с их присутствием на границах зе рен, определяемым протеканием процессов межкристаллической ликвации. Хотя равновесная концентрация микроэлементов в стали или чугуне чрезвы чайно мала, в результате ликвации на межзеренных и межфазных границах она может оказаться в несколько десятков, сотен и даже тысяч раз выше. Те оретически при диаметре кристаллического зерна 30 мкм и концентрации при месного микроэлемента 10 г/т может оказаться перекрытой вся граница зерна (слоем толщиной в один атом). Если учитывать процессы макроликвации, то нельзя считать безопасной даже концентрацию 1 г/т. Общеизвестно, что гра ницы зерен служат препятствием для развития деформации и трещин, прида ют прочность и вязкость, но, с другой стороны, они же являются самым сла бым местом в структуре материала в целом. Поэтому межкристаллическая ли квация служит причиной охрупчивания границ зерен, межкристаллической коррозии и, как следствие, снижения прочности изделия.
Как правило, механизм снижения прочности сцепления соседних зерен, т.е. ослабевание межзеренной связи из-за присутствия на границах зерен примесных микроэлементов, представляют поэтапно:
-ослабевает сила сцепления между атомами примеси и окружающими их атомами железа;
-сильная ковалентная связь между атомами железа и примеси приводит
кослаблению связи между соседними атомами железа;
-на границах зерен активно формируются фазы (оксиды, карбиды, ни триды, сульфиды, интерметаллиды), обладающие отличными от элементов
исоединений основы механическими свойствами.
Например, известен факт сильного влияния микропримесных элементов олова, сурьмы и мышьяка на прочность некоторых легированных сталей. Проблему повышения качества таких сталей удалось решить за счет реали зации ряда мероприятий, связанных со строгим подбором сырья и примене нием внепечной обработки стали, в результате чего были достигнуты следу ющие уровни содержания микропримесей: олова - менее 20 г/т стали, мышьяка - менее 40 г/т стали, а сурьмы - менее 7 г/т стали.
Особое значение имеет проблема так называемых “бродячих элемен тов” Металлургический термин “бродячие элементы” пришел из америка-
Классификация сталей по содержанию примесных микроэлементов: меди, молибдена, олова и хрома
|
Суммарное содержа |
|
Класс |
ние (Си + Mo+ Sn + |
Область применения |
|
+ Сг), масс.% |
|
0 |
0,033 |
Авиационная промышленность, атомная энергетика; спе |
|
|
циальная нефтяная арматура, специальные подшипники, |
|
|
электроды для ЭШП |
1 |
0,090 |
Стали высокопрочные для сверхглубокой вытяжки, мартен |
|
|
ситостареющие; тонкая проволока, подшипники, белая |
|
|
жесть для вытяжки |
2 |
0,280 |
Стали для глубокой вытяжки, холодной вытяжки, глубокой |
|
|
высадки, штамповки, заготовки для бесшовных труб |
3 |
0,335 |
Сортовой прокат стали для автомобилестроения, штрип- |
|
|
совая сталь; резервуары высокого давления |
4 |
0,390 |
Трубы массового назначения; белая и черная жесть, холод |
|
|
нокатаная калиброванная сталь, колесная сталь, оцинко |
|
|
ванный и эмалированный листы |
5 |
0,600 |
Крупный сортовой прокат, стали для фасонных профилей, |
|
|
горячекатаные рулонные стали; толстая проволока |
6 |
0,800 |
Арматурные и строительные стали |
7 |
>0,800 |
Остальной сортамент |
но-английского слэнга (бесцельно скитающиеся бродяги всегда были неже ланными гостями). В отечественной специальной литературе иногда ис пользуется термин “циркулирующие элементы”. Наиболее важными бродя чими элементами считаются Си, Sn, Zn, Pb, Bi, Sb, Ni, Cr, Mo, V. В общем случае примесный элемент может быть либо микролегирующим, либо бро дячим, что определяется его содержанием и общим составом производимо го металла. Необходимо отметить, что в специальной литературе нет кон кретного разделения на бродячие, микропримесные или “следовые” элемен ты. Существует мнение, что следовые элементы, которые бывают либо ме таллическими, либо неметаллическими, присутствуют в металлах в столь низких концентрациях и в таких формах, что они не оказывают вредного влияния на качество стали, тогда как бродячие элементы не только оказы вают вредное воздействие на качество металла, но и не могут быть легко удалены из него и поэтому постоянно аккумулируются во время кругообо рота сталь - металлолом - сталь.
В результате развития концепции производства чистых по примесям ма териалов в странах ЕЭС в 1999 г. была принята классификация сталей по со держанию основных бродячих (циркулирующих) элементов: меди, молибде на, олова и хрома (табл. 3.6).
Новый взгляд на проблему присутствия микроэлементов в изделиях из же леза сформировался совсем недавно. В процессе глубоких исследований, свя занных с разработкой новых технологий рафинирования стали и чугуна (для повышения чистоты металла), обратили внимание на возможность рациональ-
Полный химический состав (за исключением газообразующих элементов) некоторых металлургических флюсов, г/т
|
Известняк Бар- |
|
Известняк |
Известняк |
|
Химический элемент |
суковский |
Известняк (Украина) |
|||
(Польша) |
(Турция) |
||||
|
(Россия) |
|
|||
|
|
|
|
||
Алюминий |
(0,8)* |
(0,2- 0,6) |
(0,15) |
(0,4) |
|
Барий |
50 |
30-300 |
20 |
200 |
|
Бериллий |
2 |
До 2 |
Следы |
0,2 |
|
Бор |
100 |
10-40 |
7 |
10 |
|
Бром |
Не обн. |
3-10 |
5 |
1 |
|
Ванадий |
40 |
10-30 |
20 |
30 |
|
Вольфрам |
Не обн. |
Не обн. |
Не обн. |
Не обн. |
|
Галлий |
|
Не обн. |
Следы |
1 |
|
Йод |
50 |
20-80 |
10 |
70 |
|
Иттрий |
10 |
До 20 |
4 |
1 |
|
Железо |
(0,4) |
(0,7-1,0) |
(0,3) |
(0,6) |
|
Калий |
(0,2) |
(0,06-0,6) |
(0,2) |
(0,22) |
|
Кальций |
(38,1) |
(37,7-38,0) |
(40) |
(38,4) |
|
Кобальт |
60 |
10-20 |
Следы |
3 |
|
Лантаноиды |
100 |
До 100 |
10 |
20 |
|
Литий |
50 |
30-80 |
10 |
20 |
|
Кремний |
40 |
(До 0,7) |
(0,3) |
(0,9) |
|
Магний |
(0,35) |
(0,2- 1,2) |
(0,6) |
(0,2) |
|
Медь |
40 |
До 50 |
5 |
40 |
|
Молибден |
Не обн. |
Не обн. |
Не обн. |
Не обн. |
|
Мышьяк |
60 |
5-30 |
10 |
9 |
|
Натрий |
700 |
40-100 |
100 |
100 |
|
Никель |
60 |
10-40 |
10 |
10 |
|
Олово |
Не обн. |
До 50 |
20 |
Не обн. |
|
Рубидий |
" |
10-30 |
20 |
30 |
|
Свинец |
|
Не обн. |
40 |
Не обн. |
|
Селен |
(0,2) |
До 30 |
Не обн. |
3 |
|
Сера |
(До 0,5) |
300 |
300 |
||
Скандий |
Не обн. |
Не обн. |
Не обн. |
Не обн. |
|
Стронций |
700 |
600-2000 |
500 |
700 |
|
Сурьма |
Не обн. |
Не обн. |
Не обн. |
Не обн. |
|
Титан |
100 |
100-300 |
80 |
1000 |
|
Фосфор |
300 |
(До 0,2) |
30 |
100 |
|
Фтор |
200 |
50-600 |
60 |
100 |
|
Хлор |
600 |
50-1000 |
100 |
50 |
|
Хром |
100 |
20-70 |
10 |
40 |
|
Цинк |
60 |
До 60 |
40 |
5 |
|
Цирконий |
Не обн. |
До Ю |
2 |
5 |
* В скобках приведены данные в масс. ‘Jo.
ного использования для повышения качества металлургических изделии ком позиций микропримесей, которые ранее считались вредными. К таким компо зициям, в частности, относятся сульфиды, оксиды, фосфиды, нитриды, бориды, галогениды, арсениды, карбиды, соединения алюминия и многие другие.
Известняк до- |
Известняк доло- |
|
|
|
|
|
ломитизиро- |
Оливин |
Боксит |
Кварцит |
Кварцит |
||
митизирован- |
||||||
ванный Туров |
(Норвегия) |
(Греция) |
(Польша) |
(Турция) |
||
ный (Украина) |
||||||
ский (Россия) |
|
|
|
|
|
|
2,0 |
(0,5) |
(0,2) |
(31,7) |
(2,5) |
(4,7) |
|
150 |
20 |
60 |
60 |
70 |
300 |
|
0,2 |
10 |
Следы |
20 |
0,2 |
0,3 |
|
75 |
20 |
4 |
200 |
40 |
10 |
|
50 |
5 |
Следы |
Следы |
Следы |
1 |
|
45 |
70 |
60 |
1000 |
60 |
60 |
|
Не обн. |
Не обн. |
Не обн. |
30 |
Не обн. |
Не обн. |
|
it |
" |
Следы |
70 |
3 |
7 |
|
|
||||||
|
70 |
Следы |
Не обн. |
4 |
100 |
|
4 |
5 |
Не обн. |
60 |
10 |
7 |
|
(0,3) |
(0,4) |
(10,2) |
(16,0) |
(1,4) |
(2,8) |
|
(0,3) |
800 |
700 |
200 |
(0,3) |
(0,5) |
|
(28,5) |
(33,0) |
(0,5) |
(0,6) |
(0,37) |
0,13 |
|
5 |
20 |
200 |
40 |
2 |
4 |
|
55 |
10 |
Не обн. |
500 |
105 |
75 |
|
45 |
100 |
2 |
400 |
70 |
10 |
|
30 |
(0,2) |
(14,9) |
(1,9) |
(42,7) |
(39,7) |
|
(13,2) |
(6,0) |
(30,0) |
125 |
(0,1) |
(0,3) |
|
30 |
4 |
20 |
10 |
40 |
20 |
|
4 |
Не обн. |
Не обн. |
10 |
Не обн. |
Не обн. |
|
12 |
30 |
" |
1000 |
5 |
3 |
|
200 |
20 |
70 |
40 |
5 |
100 |
|
15 |
20 |
(0,7) |
700 |
200 |
800 |
|
10 |
Не обн. |
Не обн. |
7 |
Не обн. |
Не обн. |
|
35 |
10 |
10 |
Не обн. |
30 |
100 |
|
35 |
Не обн. |
Не обн. |
20 |
Не обн. |
30 |
|
3 |
VI |
п |
Не обн. |
" |
4 |
|
|
|
|||||
800 |
400 |
600 |
600 |
200 |
70 |
|
Не обн. |
Не обн. |
10 |
1000 |
7 |
Не обн. |
|
200 |
300 |
60 |
60 |
40 |
20 |
|
Не обн. |
Не обн. |
Не обн. |
6 |
Не обн. |
Не обн. |
|
400 |
200 |
200 |
(1,4) |
800 |
(0,34) |
|
200 |
200 |
70 |
250 |
300 |
80 |
|
1000 |
80 |
90 |
600 |
400 |
200 |
|
2000 |
600 |
300 |
100 |
90 |
200 |
|
35 |
30 |
3000 |
1000 |
600 |
500 |
|
15 |
3 |
20 |
40 |
10 |
30 |
|
30 |
20 |
Не обн. |
800 |
300 |
200 |
Так, в настоящее время были доказаны:
- целесообразность присутствия в никельхроммолибденовых сталях сульфидов марганца (MnS) и микропримесей Ti, Zr и редкоземельных эле ментов;
- полезность связывания в конвертерной стали микропримесей бора в нитриды, что обеспечивается присутствием в металле азота в количестве не менее 50 г/т металла, хотя многими сертификатами рекомендуется содержа ние азота в стали менее 40 и даже менее 20 г/т;
-эффективность микролегирования медьсодержащих сталей фосфором
сцелью замедления процессов поверхностного расслаивания и т.д.
Врезультате исследовательская работа получила новое направление: достижение равномерного распределения микроэлементов в металле и по иск композиций микроэлементов, повышающих качественные характери стики изделий. Следует отметить, что этот факт прекрасно согласуется с данными из истории металлургии - хорошо известно, что лучшими издели ями из железа и в древности, и в Средневековье, да и в последующие време на были изделия - композиты, содержащие значительные количества при месных и микропримесных элементов (но, по-видимому, взятых, сознатель но или невольно, в необходимых для достижения результата пропорциях).
Отметим, что углубленное изучение примесного состава шихтовых мате риалов доменной плавки интересовало многих исследователей. Почти двести лет назад выдающийся шведский химик и минералог Йёнс Якоб Берцелиус отмечал: “Составление шихты имеет большую важность в отношении к каче ству получаемого железа. Железное производство весьма много бы выигра ло, если бы шихтовые материалы были подвергнуты столь же точным анали зам, какие делаются часто из простого любопытства... Так как экономиче ские расчеты редко управляют изысканиями настоящего ученого..., мы долж ны надеяться, что искусные металлурги найдут полезным для собственных выгод посвятить часть времени и средств изысканиям такого рода”. Нет не
обходимости комментировать цитату из книги великого ученого - актуаль ность сказанного двести лет назад очевидна и на сегодняшний день.
К концу XX в. сложилось ясное представление об особых специфиче ских свойствах, которые проявляют в чугунах и сталях микроэлементы. В особенности это касается ряда загрязняющих (Си, Sb, Sn, As, Pb и пр.) и циркулирующих бродячих (Си, Zn, Sn, Cr, Мо и др.) элементов, для борьбы с которыми в настоящее время активно разрабатываются технологии измене ния их морфологии, главным образом через введение в чугун и сталь микро легирующих добавок.
В связи с этим ожидается, что уже в ближайшее время конкурентоспо собными окажутся те предприятия, на которых будет осуществляться по стоянный и полный контроль содержания микроэлементов в исходных ших товых металлургических материалах по всему циклу металлургических пе ределов. На повестке дня нового столетия одним из главных становится во прос об управлении потоками микроэлементов, особенно микропримесей, циркулирующих в рамках производственного и глобального рециклинга ме таллургических материалов и продукции.
З.2.1.1.2. Источники микроэлементов при производстве продукции из железа
Микроэлементы содержатся во всех материалах, используемых на пред приятиях черной металлургии, - железных и марганцевых рудах, углях всех видов, флюсах, ферросплавах, огнеупорах, металлоломе, а также в материа-
Микропримесный состав коксующихся углей некоторых шахт Австралии, Канады и Польши, импортируемых металлургическими предприятиями Германии, масс.%.
Химический |
Среднее содер |
"North Goon- |
"Burton" |
"Elkview" |
|
|
жание в кок |
jella" |
Польша |
||||
элемент |
(Австралия) |
(Канада) |
||||
сующихся углях |
(Австралия) |
|||||
|
|
|
|
|||
Барий |
110-150 |
30 |
20 |
100 |
100 |
|
Бериллий |
1,8- 2,2 |
2 |
1 |
0,7 |
2 |
|
Бор |
40-70 |
8 |
5 |
20 |
10 |
|
Ванадий |
25-35 |
50 |
30 |
70 |
40 |
|
Галлий |
6-8 |
3 |
1 |
1 |
Не обн. |
|
Иттрий |
5-7 |
10 |
8 |
7 |
7 |
|
Кобальт |
5-6 |
3 |
2 |
0,9 |
5 |
|
Лантаноиды |
15-50 |
83 |
И |
28 |
43 |
|
Литий |
15-35 |
30 |
50 |
10 |
10 |
|
Марганец |
80-110 |
10 |
8 |
100 |
7 |
|
Медь |
15-20 |
7 |
10 |
3 |
20 |
|
Молибден |
2-4 |
Не обн. |
Не обн. |
Не обн. |
3 |
|
Мышьяк |
15-25 |
|
|
" |
3 |
|
Никель |
10-20 |
5 |
4 |
|
20 |
|
Рубидий |
12-20 |
Не обн. |
Не обн. |
|
7 |
|
Скандий |
2-3 |
6 |
7 |
5 |
8 |
|
Стронций |
50-100 |
90 |
100 |
20 |
50 |
|
Фтор |
80-150 |
20 |
10 |
4 |
20 |
|
Хлор |
500-2000 |
7 |
10 |
5 |
30 |
|
Хром |
12-15 |
30 |
10 |
8 |
20 |
|
Цезий |
1 |
Не обн. |
Не обн. |
Не обн. |
1 |
|
Цинк |
20-25 |
3 |
2 |
" |
3 |
|
Цирконий |
35-40 |
200 |
90 |
50 |
20 |
|
Калий |
До 2500 |
300 |
400 |
150 |
350 |
|
Натрий |
До 600 |
10 |
20 |
2 |
20 |
|
Титан |
1200-2000 |
1000 |
1000 |
1000 |
400 |
лах, используемых для нанесения покрытий на изделия из железа, и прочих. К сожалению, тонкий химический анализ является дорогостоящим процессом, что существенно затрудняет в отечественных условиях получение достовер ной информации, достаточной для проведения широких статистических иссле дований поведения микроэлементов. Отметим, что и в благополучно развитых странах Запада подобные исследования очень редки и малопредставительны.
Приводимая в табл. 3.7-3.13 информация о микропримесном составе ма териалов, используемых в черной металлургии, получена в середине 90-х го дов специалистами МИСиС.
3.2.1.1.3. Распределение микроэлементов между основными фазами металлургических процессов
Для построения элементопотока особенно важно знать, как конкретный элемент ведет себя в каждом металлургическом переделе. Статистической информации для такого анализа ввиду сложности металлургических систем
Таблица 3.9
Микропримесный состав некоторых российских и зарубежных железных и марганцевых руд, г/т материала
|
|
|
Руда |
|
Химический |
Михайловское |
Замитри |
Хадисолб |
Кардемир |
элемент |
месторождение |
(Бразилия) |
(Египет) |
(Турция) |
|
(Россия) |
|
|
|
Барий |
100 |
200 |
2000 |
1500 |
Бериллий |
3 |
1 |
30 |
3 |
Бор |
300 |
8 |
70 |
300 |
Бром |
Не обн. |
2 |
3 |
4 |
Ванадий |
30 |
100 |
600 |
500 |
Висмут |
Не обн. |
Не обн. |
Не обн. |
5 |
Вольфрам |
м |
90 |
100 |
Не обн. |
|
|
|
|
|
Галлий |
6 |
8 |
10 |
10 |
Германий |
10 |
Не обн. |
ft |
Не обн. |
|
||||
Индий |
5 |
" |
Не обн. |
н |
Йод |
Не обн. |
9 |
20 |
30 |
Иттрий |
20 |
30 |
70 |
20 |
Кобальт |
3 |
10 |
40 |
90 |
Лантаноиды |
45 |
75 |
55 |
55 |
Литий |
200 |
20 |
40 |
20 |
Медь |
50 |
30 |
10 |
100 |
Молибден |
Не обн. |
8 |
10 |
30 |
Мышьяк |
50 |
300 |
60 |
100 |
Никель |
10 |
30 |
80 |
1000 |
Олово |
Не обн. |
Не обн. |
Не обн. |
30 |
Рубидий |
70 |
60 |
100 |
200 |
Свинец |
50 |
30 |
20 |
40 |
Селен |
Не обн. |
4 |
10 |
10 |
Скандий |
3 |
Не обн. |
Не обн. |
Не обн. |
Стронций |
200 |
70 |
600 |
80 |
Сурьма |
Не обн. |
100 |
2 |
7 |
Таллий |
|
Не обн. |
20 |
Не обн. |
Теллур |
|
" |
4 |
и |
Титан |
500 |
500 |
700 |
700 |
Торий |
Не обн. |
Не обн. |
Не обн. |
2 |
Уран |
" |
п |
50 |
10 |
|
||||
Фтор |
8 |
20 |
600 |
400 |
Хлор |
40 |
60 |
20000 |
1500 |
Хром |
50 |
70 |
200 |
400 |
Цезий |
Не обн. |
3 |
3 |
200 |
Цирконий |
30 |
30 |
40 |
40 |
В с е г о |
1783 |
1868 |
25547 |
7386 |
недостаточно. Предлагаемый нами метод исследования поведения микро элементов в металлургических системах базируется на комплексном термо динамическом и балансовом способах их анализа. Покажем это на примере
плавки чугуна в доменной печи для микропримесных элементов —галлия, мышьяка и стронция.
|
|
Окатыши |
|
||
Никопольская |
Михайловского |
Лебединского |
Коспгомукшского |
Кируна (Швеция) |
|
марганцевая |
|||||
ГОК |
ГОК |
ГОК |
|
||
(Украина) |
|
||||
|
|
|
|
||
9000 |
90 |
60 |
30 |
60 |
|
2 |
1 |
0,5 |
0,5 |
0,6 |
|
400 |
10 |
5 |
7 |
20 |
|
Не обн. |
Не обн. |
Не обн. |
Не обн. |
Не обн. |
|
300 |
10 |
20 |
80 |
1000 |
|
Не обн. |
Не обн. |
Не обн. |
Не обн. |
Не обн. |
|
50 |
" |
" |
50 |
40 |
|
20 |
2 |
5 |
6 |
20 |
|
Не обн. |
Не обн. |
Не обн. |
Не обн. |
Не обн. |
|
90 |
10 |
|
|
|
|
80 |
5 |
2 |
10 |
||
200 |
10 |
Не обн. |
20 |
100 |
|
630 |
10 |
10 |
10 |
130 |
|
70 |
200 |
30 |
20 |
40 |
|
300 |
50 |
10 |
5 |
30 |
|
1000 |
Не обн. |
7 |
Не обн. |
Не обн. |
|
300 |
20 |
2 |
3 |
5 |
|
1000 |
10 |
10 |
30 |
400 |
|
Не обн. |
Не обн. |
Не обн. |
Не обн. |
10 |
|
400 |
100 |
20 |
20 |
10 |
|
100 |
Не обн. |
Не обн. |
Не обн. |
6 |
|
Не обн. |
|
|
|
Не обн. |
|
7 |
|
|
|
||
|
|
|
7 |
||
8600 |
300 |
30 |
10 |
||
10 |
|||||
30 |
Не обн. |
1 |
Не обн. |
Не обн. |
|
10 |
|
Не обн. |
|
" |
|
Не обн. |
|
|
|
|
|
1900 |
500 |
200 |
200 |
1000 |
|
Не обн. |
Не обн. |
Не обн. |
Не обн. |
20 |
|
20 |
|
|
|
Не обн. |
|
1000 |
10 |
2 |
10 |
100 |
|
400 |
10 |
1 |
7 |
200 |
|
30 |
60 |
30 |
70 |
600 |
|
30 |
Не обн. |
6 |
Не обн. |
Не обн. |
|
80 |
10 |
30 |
30 |
20 |
|
26049 |
1413 |
485 |
611 |
3839 |
Выбор в качестве объекта исследований доменной печи объясняется тем, что она является наиболее сложным металлургическим агрегатом, а формирующаяся в ней металлургическая система - наиболее представи тельной для анализа, поскольку включает все виды сред: газовую, жидкую и твердую, а также характеризуется сложными закономерностями массооб-
Таблица 3.10
Микропримесный состав некоторых агломератов России
Химический микроэле- |
|
Содержание в агломерате, г/т |
|
|
|
АК "Тулачермет" |
ОАО "НЛМК" |
||
мент |
ОАО "Северсталь” |
|||
Барий |
300 |
200 |
100 |
|
Бериллий |
0,2 |
До 0,5 |
0,1 |
|
Бор |
20 |
30-100 |
40 |
|
Ванадий |
60 |
30-200 |
100 |
|
ДоЗ |
Не обн. |
|||
Висмут |
Не обн. |
|||
50 |
м |
|||
Вольфрам |
4 |
|
||
Галлий |
До 100 |
2 |
До 300 |
|
Германий |
Не обн. |
До 20 |
||
Йод |
4 |
Не обн. |
Не обн. |
|
Иттрий |
5 |
4-20 |
3 |
|
Кобальт |
50 |
1-6 |
Не обн. |
|
Лантаноиды |
35-40 |
40-100 |
15-20 |
|
Литий |
20 |
10 |
Не обн. |
|
Медь |
50 |
5-30 |
20 |
|
Молибден |
100 |
До Ю |
Не обн. |
|
Мышьяк |
2 |
До Ю |
20 |
|
Никель |
20 |
5-30 |
600 |
|
Олово |
40 |
2-5 |
Не обн. |
|
Рубидий |
30 |
2-10 |
30 |
|
Свинец |
60 |
30 |
30 |
|
Селен |
Не обн. |
1-2 |
Не обн. |
|
Скандий |
20 |
Не обн. |
" |
|
Стронций |
300 |
200 |
400 |
|
Сурьма |
3 |
5 |
3 |
|
Теллур |
10 |
Не обн. |
Не обн. |
|
Технеций |
Не обн. |
2-4 |
7 |
|
Титан |
600 |
400-1000 |
30 |
|
Уран |
Не обн. |
До 4 |
3 |
|
Фтор |
40 |
20-40 |
До 200 |
|
Хлор |
20 |
До 100 |
60 |
|
Хром |
200 |
50-200 |
90 |
|
Цинк |
100 |
5-55 |
60 |
|
Цирконий |
70 |
20-60 |
10 |
|
В с е г о |
До 3050 |
До 2600 |
До 2200 |
менных процессов в противоточной системе в широком интервале темпера тур (от 50 до 2500 °С) и давлений (до 5 атм).
Для выбранных микропримесных элементов имеется достаточно необ ходимая достоверная исходная информация, их выбор также обусловлен физическим моделированием, подтверждающим результаты приводимого ниже балансового и термодинамического анализа.
Попадающие в доменную печь микроэлементы распределяются между жидкими продуктами плавки (чугуном и шлаком) и доменным газом, а так же переходят в состав некоторых особых фаз, формирующихся в печи в процессе ее эксплуатации: гарнисажа, настылей, отложений на загрузочных
|
|
Предприятие, вид выплавляемого чугуна |
|
|||
|
|
|
|
|
|
ОАО "Косо |
|
|
ОАО "Северсталь" |
АК "Тулачермет" |
горский ме |
||
|
ОАО |
|
|
|
|
таллургичес |
Химический |
"НЛМК", |
|
|
|
|
кий завод" |
элемент |
передель |
|
Передель |
|
|
|
|
ный |
|
|
|
|
|
|
Передель |
ный "холод |
Передель |
Нодулярный |
Ферромар |
|
|
|
|||||
|
|
ный |
ный" (Si - |
ный |
ганец |
|
|
|
|
||||
|
|
|
< 0,5 масс.%) |
|
|
|
Алюминий |
8-10 |
До 50 |
5 |
8-10 |
8-10 |
50 |
Бериллий |
Не обн. |
2 |
Не обн. |
0,5-1,0 |
Не обн. |
Не обн. |
Бор |
|
Не обн. |
|
Не обн. |
|
3 |
Ванадий |
70 |
600 |
400 |
50 |
40 |
80 |
Висмут |
Не обн. |
Не обн. |
Не обн. |
3 |
Не обн. |
Не обн. |
Вольфрам |
" |
2 |
" |
0,5 |
0,5-1,0 |
" |
Галлий |
20 |
30 |
70 |
100 |
15-20 |
60 |
Германий |
Не обн. |
Не обн. |
Не обн. |
1 |
1 |
Не обн. |
Калий |
20 |
4-8 |
20 |
6-10 |
6-10 |
Следы |
Кальций |
80 |
10-20 |
80 |
20 |
5-10 |
3-5 |
Кобальт |
3-5 |
20 |
50 |
3-5 |
3-5 |
30 |
Литий |
Следы |
10 |
Следы |
Следы |
Следы |
Следы |
Магний |
10 |
10 |
3-5 |
ДоЗ |
ДоЗ |
10 |
Медь |
60 |
30 |
60 |
30 |
20 |
300 |
Мышьяк |
10 |
3-5 |
3-5 |
3-5 |
10 |
400 |
Молибден |
3-5 |
1 |
Не обн. |
Не обн. |
Следы |
10 |
Натрий |
8-10 |
40 |
1-3 |
3-7 |
1 |
Следы |
Никель |
20 |
60 |
40 |
10 |
10 |
100 |
Ниобий |
3-5 |
3-5 |
3-5 |
1 |
1 |
3-5 |
Олово |
5-8 |
10 |
Следы |
1-3 |
4-8 |
20 |
Рубидий |
Следы |
0,5-1 |
Не обн. |
Не обн. |
Не обн. |
Не обн. |
Свинец |
Не обн. |
10 |
1-3 |
200 |
До 50 |
|
Серебро |
|
Не обн. |
Не обн. |
0,5 |
0,3 |
1 |
Скандий |
|
|
|
Не обн. |
Не обн. |
|
Сурьма |
5 |
5-8 |
2-5 |
5-8 |
5-8 |
20 |
Титан |
100 |
500 |
700 |
350-400 |
200-300 |
600-1000 |
Фтор |
Следы |
Следы |
5 |
20 |
Следы |
Следы |
Хлор |
5 |
20 |
10 |
10 |
5 |
2 |
Хром |
100 |
300 |
80-90 |
170-200 |
80-100 |
400 |
Цинк |
20 |
5-8 |
10 |
500 |
300 |
Следы |
В с е г о |
550 |
1250 |
1550 |
1600 |
915 |
2300 |
устройствах, выделений некоторых металлов (например, свинца, титана, лантаноидов) на футеровке горна и лещади и т.п. (см. табл. 3.14). Кроме то го, микроэлементы могут формировать контуры циркуляции во внутреннем пространстве печи в результате возгонки при высоких и последующей кон денсации на поверхности твердых шихтовых материалов при низких темпе-
|
|
|
|
ОАО "Косогорский |
|
Химический |
ОАО "НЛМК" |
ОАО "Северсталь" |
АК "Тулачермет" |
металлургический |
|
завод" (при вып |
|||||
элемент |
|
|
|
лавке ферромар |
|
|
|
|
|
||
|
|
|
|
ганца) |
|
Барий |
800-1200 |
450-600 |
900-1200 |
12000-15000 |
|
Бериллий |
До 5 |
До 1 |
2-4 |
20-30 |
|
Бор |
200-300 |
60-80 |
250-300 |
300-500 |
|
Ванадий |
20-30 |
20-25 |
До 40 |
5-10 |
|
Висмут |
Не обн. |
Не обн. |
15-25 |
Не обн. |
|
Вольфрам |
п |
1-3 |
До 25 |
ff |
|
200-250 |
|||||
Иттрий |
15-25 |
10-15 |
30-60 |
||
Калий |
2400-3500 |
3200-4500 |
До 12000 |
250-300 |
|
Кобальт |
Следы |
1-2 |
До Ю |
Следы |
|
Лантаноиды |
50-80 |
120-160 |
До 600 |
До 1000 |
|
Литий |
50-60 |
100-150 |
25-45 |
200-250 |
|
Медь |
1-3 |
1-2 |
4-6 |
1-2 |
|
Молибден |
Не обн. |
До 20 |
1-3 |
Не обн. |
|
Мышьяк |
8-10 |
4-6 |
3-5 |
2-5 |
|
Натрий |
1500-2000 |
800-1000 |
1600-2200 |
200-250 |
|
Никель |
Не обн. |
1-3 |
До 2 |
5-8 |
|
Рубидий |
70-100 |
50-70 |
20-30 |
Не обн. |
|
Свинец |
2-3 |
6-10 |
5-12 |
и |
|
|
|||||
Скандий |
20-30 |
30-50 |
Не обн. |
700-1200 |
|
Стронций |
400-800 |
40-70 |
600-1000 |
||
Титан |
1200-1500 |
2200-3000 |
1300-1800 |
3000-3500 |
|
Торий |
10 |
Не обн. |
5-10 |
20-25 |
|
Уран |
10 |
" |
5-10 |
30-40 |
|
Фтор |
120-150 |
120-150 |
20-30 |
До 2000 |
|
Хлор |
60-80 |
5-10 |
10-15 |
20-30 |
|
Хром |
15-25 |
40-60 |
40-50 |
1-3 |
|
Цинк |
200 |
До 300 |
До 300 |
Не обн. |
|
Цирконий |
90-140 |
250-400 |
300-450 |
500-600 |
ратурах. Микроэлементы, переходящие в газовую фазу процесса, могут за тем попадать в шламы газоочистных сооружений с последующим накопле нием в цикле “доменная печь —> шлам —> агломерация —> доменная печь” ли бо выбрасываются в окружающую среду, минуя улавливающие устройства.
Поэтому надо иметь в виду, что распределение микропримесных эле ментов между фазами (продуктами) доменного процесса определяющим об разом зависит от того, в составе какого шихтового материала, в каком виде (в составе какого минерального образования, в органической или неоргани ческой части кокса и т.п.) и каким образом (через колошниковое загрузоч ное устройство, через фурмы или другим способом) микроэлементы попада ют в доменную печь.
По виду нахождения в природе г а л л и й представляет собой эле мент, типичный для группы рассеянных металлов. Однако при этом яв-
|
|
|
|
ОАО "Косогорский |
Химический |
ОАО "НЛМК" |
ОАО "Северсталь" |
АК "Тулачермет" |
металлургический |
элемент |
завод" (при вып |
|||
|
|
|
|
лавке ферромар |
|
|
|
|
ганца) |
Барий |
Следы |
Следы |
Следы |
4000-5000 |
Бериллий |
1-3 |
1-3 |
2-5 |
3-5 |
Бор |
5-10 |
5-10 |
3-5 |
300-400 |
Бром |
1-2 |
1 |
1-3 |
5-10 |
Ванадий |
300-350 |
100-120 |
100-120 |
100-120 |
Висмут |
Не обн. |
Не обн. |
1-3 |
40-50 |
Вольфрам |
и |
|
1-2 |
До 80 |
|
|
|||
Галлий |
50-100 |
150-250 |
80-120 |
50-100 |
Германий |
Не обн. |
Не обн. |
Не обн. |
10-15 |
Йод |
" |
" |
ft |
10-15 |
Иттрий |
5-10 |
50-80 |
20-40 |
3 ^ 4 0 |
Кадмий |
1-2 |
1-3 |
3-5 |
8-12 |
Кобальт |
15-25 |
20-30 |
5-10 |
20-25 |
Лантаноиды |
180-200 |
500-700 |
50-60 |
До 500 |
Литий |
Следы |
80-120 |
4—6 |
200-250 |
Медь |
Не обн. |
Не обн. |
20-40 |
400-500 |
Молибден |
Следы |
Следы |
1-4 |
8-10 |
Мышьяк |
Следы |
Следы |
5-7 |
100-150 |
Никель |
200-250 |
100-120 |
80-150 |
300-350 |
Олово |
200-240 |
600-800 |
80-120 |
100-150 |
Рубидий |
10-20 |
5-10 |
10-20 |
2000-3000 |
Свинец |
До 2500 |
До 1500 |
До 2000 |
До 5000 |
Селен |
1-2 |
5-8 |
1-2 |
20-30 |
Скандий |
1-3 |
50-70 |
15-30 |
8-12 |
Стронций |
До 2500 |
300-400 |
До 2000 |
До 10000 |
Сурьма |
Не обн. |
3-5 |
8-10 |
50-70 |
Теллур |
" |
1 |
1 |
30-50 |
Титан |
|
Не обн. |
300-500 |
До 2500 |
Торий |
1-3 |
" |
3-5 |
4-8 |
Уран |
1-3 |
|
5-10 |
5-9 |
Фтор |
80-100 |
220-250 |
100-120 |
До 2000 |
Хлор |
10-20 |
60-80 |
50-60 |
300-500 |
Хром |
100-120 |
500-600 |
600-900 |
100-120 |
Цезий |
Не обн. |
Не обн. |
Не обн. |
200-250 |
Цинк |
До 5000 |
До 25000 |
До 1000 |
До 15000 |
Цирконий |
Не обн. |
До 100 |
10-20 |
90-120 |
но выражена тенденция его присутствия в некоторых минералах. Он яв ляется спутником алюминия, цинка, железа, германия и практически по стоянно присутствует в углях и железных рудах, что наглядно отражено в табл. 3.8-3.10, а также в специально отобранных пробах металлурги ческих материалов предприятий ОАО “Северсталь” и АК “Тулачермет” (табл. 3.15).
Полный примесный состав металлургических материалов, отобранных из доменной печи JY®4
Химический
элемент
ОАО "Северсталь" после выдувки, г/т чугуна
|
|
Материал |
|
|
|
Козловой чу |
"Отложения |
|
Железистый |
"Металл из гар- |
|
гун с шлако |
на загрузоч |
"Цинковая |
шлак из швов |
||
нисажа под |
|||||
выми включе |
ном устрой |
настыль" |
кладки горна |
||
фурмой" |
|||||
ниями |
стве" |
|
печи |
||
|
|
Алюминий |
1%* |
2000 |
1 |
6% |
4 |
|
Барий |
500 |
100 |
Следы |
2000 |
Следы |
|
Бериллий |
1 |
2000 |
" |
6 |
Следы |
|
Бор |
70 |
03 |
Не обн. |
100 |
Следы |
|
Бром |
Не обн. |
30 |
” |
Не обн. |
Не обн. |
|
Ванадий |
600 |
200 |
Следы |
400 |
Следы |
|
Висмут |
Не обн. |
20 |
20 |
Не обн. |
200 |
|
Вольфрам |
" |
Не обн. |
Не обн. |
" |
Не обн. |
|
Галлий |
10 |
20 |
" |
|
" |
|
Германий |
Не обн. |
4 |
200 |
|
6 |
|
Железо |
Основа |
18% |
4% |
|||
Индий |
7 |
30 |
Не обн. |
Не обн. |
400 |
|
Йод |
Не обн. |
10 |
" |
" |
Не обн. |
|
Иттрий |
8 |
6 |
|
60 |
•• |
|
Калий |
1% |
10% |
0,9 |
2% |
Следы |
|
Кальций |
4% |
1,2% |
5 |
29% |
4 |
|
Кобальт |
10 |
5 |
Не обн. |
50 |
Не обн. |
|
Кремний |
4% |
1,3% |
8 |
16% |
6 |
|
Лантаноиды |
83 |
40 |
Не обн. |
360 |
Не обн. |
|
Литий |
100 |
50 |
0,2 |
200 |
Следы |
|
Магний |
2% |
3000 |
4 |
1% |
|
|
Марганец |
4000 |
900 |
Не обн. |
2000 |
Не обн. |
|
Медь |
20 |
10 |
10 |
40 |
400 |
|
Мышьяк |
Следы |
5 |
Не обн. |
Не обн. |
20 |
|
Молибден |
10 |
2 |
и |
|
Не обн. |
|
|
|
|
|
|
||
Натрий |
500 |
300 |
Следы |
2000 |
Следы |
|
Никель |
20 |
40 |
Следы |
40 |
Не обн. |
|
Ниобий |
30 |
Не обн. |
Не обн. |
30 |
|
|
Олово |
Не обн. |
4000 |
" |
50 |
15% |
|
Рубидий |
300 |
2000 |
Следы |
100 |
Следы |
|
Свинец |
Следы |
1600 |
800 |
Не обн. |
Основа |
|
Селен |
Следы |
30 |
Не обн. |
|
Не обн. |
|
Сера |
7000 |
1,6% |
7 |
1,4% |
9 |
|
Скандий |
40 |
3 |
Не обн. |
Не обн. |
Не обн. |
|
Стронций |
300 |
300 |
Следы |
400 |
Следы |
|
Сурьма |
Следы |
30 |
Не обн. |
2 |
1000 |
|
Титан |
||||||
3000 |
1000 |
Следы |
7000 |
Не обн. |
||
Фосфор |
||||||
600 |
70 |
Не обн. |
100 |
8 |
||
Фтор |
||||||
200 |
80 |
Следы |
1000 |
Следы |
||
Хлор |
7 |
300 |
||||
Следы |
60 |
6 |
||||
Хром |
||||||
300 |
100 |
Не обн. |
100 |
Не обн. |
||
Цинк |
||||||
6 |
47% |
Основа |
100 |
900 |
||
|
*_ 30 Не обн. 900 Следы
Если содержание элемента в образце находится на уровне 1масс. % и выше, то оно приводится100Цирконий
Предприятие |
Кокс |
Агломерат |
Окатыши |
Чугун |
|
ОАО "Северсталь" |
5-10 |
70-100 |
5-7* |
60-110 |
|
АК "Тулачермет" |
30-40 |
15-40 |
5-10** |
30-80 |
|
Предприятие |
Шлак |
Колошниковая |
Шлам доменный |
Шламы и зола |
|
пыль |
ТЭЦ |
||||
|
|
||||
ОАО "Северсталь" |
До 2 |
Следы |
150-250 |
2-20 |
|
АК "Тулачермет" |
Д оЗ |
Следы |
До 200 |
Следы |
*Костомукшские окатыши.
**Лебединские окатыши.
Из данных табл. 3.15 следует, что приход галлия в доменную печь в ус ловиях ОАО “Северсталь” изменяется в пределах от 65 до 125 г/т чугуна, при этом в ходе плавки галлий в основном переходит в чугун. Аналогичные результаты получены и для доменных печей АК “Тулачермет”, где при по ступлении в агрегат галлия в количестве 40-80 г/т чугуна его содержание в чугуне составляет 30-80 г/т.
Приведенные данные могут вызвать некоторое недоумение, особенно с точки зрения сложившегося стереотипа о близком сходстве химических свойств галлия и алюминия. Последний, как известно, в ходе доменного про цесса практически полностью переходит в шлак. Кроме того, и эксперимен тально установленный факт накопления галлия в доменном шламе требует физико-химического обоснования.
С целью объяснения полученных результатов на основе расчетов слож ных химических равновесий был проведен термодинамический анализ пове дения галлия и его основных соединений применительно к условиям домен ной плавки.
Поскольку основное количество галлия вносится с железорудными ма териалами, то поведение элемента прежде всего определяется степенью восстановления железа, особенно при температуре 800-1200 °С, когда в ус ловиях доменного процесса осуществляется переход FeO-Fe. Следует также учитывать хорошую растворимость галлия в железе (полная растворимость в жидком железе и около 20% массы - в твердом). Поэтому расчеты прово дили, подбирая состав исходной смеси таким образом, чтобы в равновесии находились как металлическое железо (в избытке), так и его оксид (FeO). При этом использовали два варианта задания восстановленной формы гал лия: как самостоятельной конденсированной фазы и как примеси в раство ре на основе железа (в расчетах использована модель идеального раствора Fe—Ga). При моделировании поведения галлия в интервале температур 1500-2500 °С с учетом реального характера протекания доменного процес са состав исходной смеси включал избыток углерода, что обеспечивало воз можность полного восстановления железа.
Как и следовало ожидать, анализ поведения галлия в системе без учета возможности образования раствора Fe—Ga показал, что при существовании равновесия между Fe и FeO восстановление Са20з до металлического галлия
невозможно. При температуре 1000-1150 °С происходит лишь восстановле ние Ga20 3 до Ga20, который находится в газообразном состоянии. Таким образом, весь галлий переходит в газовую фазу в виде Ga20. Если предполо жить, что данный процесс является доминирующим, то это неизбежно должно было приводить к выносу газовым потоком из печи галлия вместе с мельчайшими частицами шлама, на которых будет осаждаться вновь обра зующийся при низких температурах Ga2 0 3 . Однако по данным проведенных химических анализов этого не наблюдается.
Поведение галлия и его соединений кардинально меняется при рассмот рении возможностей его восстановления не в виде самостоятельной метал лической фазы, а как примеси в растворе на основе железа. В этом случае даже при существовании равновесия между Fe и FeO полное восстановление галлия из Ga20 3 в раствор на основе железа возможно уже при температу ре около 800 °С, т.е. восстановление галлия в раствор возможно, начиная с температуры восстановления самого железа, при этом газообразный Ga20 практически не образуется.
Термодинамическая предпочтительность восстановления элемента в раствор с железом вполне очевидна, особенно с учетом малой концентрации галлия, поскольку его химический потенциал в сильно разбавленном рас творе значительно ниже, чем в самостоятельной фазе. Это обусловливает стабильность состояния галлия как примеси раствора на основе железа и объясняет обнаруженный экспериментально практически полный переход элемента в чугун. Действительно, согласно проведенным термодинамиче ским расчетам для концентраций галлия около 100 г/т чугуна, в интервале температуры 800-1800 °С практически весь галлий должен быть связан в растворе железа.
При более высокой температуре в восстановительных условиях (при из бытке углерода) становится заметным переход галлия из раствора в газо вую фазу в виде паров металла. Этот процесс в реальных условиях домен ной плавки возможен в горне печи. Пары галлия, увлекаемые газовым по током, частично выносятся в верхнюю часть печи, где неизбежно окисляют ся С02 в газовой фазе сначала до Ga20, а затем до Ga20 3.
По-видимому, образование Ga20 3 в виде самостоятельной фазы малове роятно из-за низкой концентрации паров галлия в газовой фазе. Поэтому преобладающим механизмом конденсации является абсорбция оксидов гал лия мельчайшими пылевидными частицами твердой фазы, составляющими основу будущего доменного шлама. Аналогичный процесс может частично развиваться и при рассмотренном выше восстановлении Ga20 3 до Ga20. Этим и объясняется повышенное содержание галлия в проанализированных доменных шламах.
Таким образом, вносимый с железорудной частью шихты галлий прак тически полностью (до 95%) переходит в чугун, что обусловлено возможно стью его восстановления в раствор на основе железа. Обнаруженная повы шенная концентрация галлия в доменных шламах объясняется частичным
переходом галлия и его оксида в газовую фазу и последующей конденсаци ей на твердых частицах.
Основные минералы с т р о н ц и я - стронцианит (SrC03) и целестин (SrS04) —являются породообразующими, они нередко сопутствуют желе зорудным формациям и, как правило, в значительных количествах (ино-
Предприятие |
Кокс |
Агломерат |
Окатыши |
Чугун |
ОАО "Северсталь" |
70-85 |
3-30 |
Следы* |
Не обн. |
АК "Тулачермет" |
160-240 |
190-250 |
40-70** |
и |
|
||||
Предприятие |
Шлак |
Колошниковая |
Шлам доменный |
Шламы и зола |
|
|
пыль |
|
ТЭЦ |
ОАО "Северсталь" |
40-70 |
20-30 |
300-400*** |
20-75*** |
АК "Тулачермет" |
600-1000 |
150-250 |
400-600*** |
0 |
*Костомукшские окатыши.
**Лебединские окатыши.
***В пылеватой фракции до 0,01 мм, составляющей около 2 масс. %, содержание Sr достигает соответственно: в доменном шламе - 800-900 г/т, в шламе ТЭЦ - 110-400 г/т.
гда до 1 масс.%) присутствуют в известняках и доломитах. Кроме того, стронций относится к элементам интенсивного биологического поглоще ния растениями, что предопределяет присутствие его в каменных углях (особенно коксующихся), причем свыше двух третей элемента концентри руется в “органической” части углей. Все это определяет присутствие стронция в сырых металлургических материалах, что подтверждается данными табл.3.8-3.10 и 3.16.
Из приведенных данных следует, что приход стронция в доменную печь в условиях АК “Тулачермет” достигает 400 г/т чугуна. При этом ~ 300 г/т пе реходит в шлак и 15 г/т улавливается в ходе очистки колошникового газа (5 г/т в виде шлама, до 8 г/т в виде колошниковой пыли). Таким образом, не ясно, что происходит примерно с 85 г Sr/т чугуна.
Для условий ОАО “Северсталь” имеют место следующие результаты: приход стронция в печь составляет ~ 60 г/т чугуна (большая часть Sr вносит ся с коксом), переходит в шлак 13-25 г/т, улавливается в виде пыли и шлама 3-6 г/т; “невязка” между приходной и расходной частями баланса Sr состав ляет 30-40 г/т чугуна. Следует отметить, что в обоих случаях величина “раз баланса” примерно соответствует количеству Sr, вносимого в печь в составе “органической” части кокса. Данный факт требует объяснения.
С целью определения характера поведения стронция в доменной плав ке также были проведены термодинамические расчеты. Их результаты по казывают, что в температурном интервале 1300-1800 °С стронций перехо дит в шлаковую фазу процесса, образуя оксид и сульфид в соотношении ~ 1:2. При более высокой температуре (1800-2200 °С) возможен переход Sr в газовую фазу в виде паров металлического стронция. С учетом этого мож но предложить следующую схему поведения Sr в доменной плавке (рис. 3.7).
Стронций вносится в доменную печь в основном в виде оксида (с желе зорудными материалами и золой кокса) и в составе органической части ко кса (30-100 г/т чугуна в зависимости от природы углей, используемых при коксовании), а также (незначительно) в виде SrC03 в составе известняка и, возможно, в виде SrS в золе кокса.
Стронций органической части кокса, попадающий в фурменную зону печи, переходит в газовую фазу в виде паров металла. В ходе последующе-
17. Ю. С. Юсфин |
257 |
Рис. 3.7. Схема поведения стронция в доменной плавке
го движения газа в верхнюю часть печи пары стронция окисляются с обра зованием SrO. Это подтверждается термодинамическими расчетами, кото рые показывают, что уже в интервале 1500-1700 °С практически весь воз гон Sr должен превратиться в SrO. Однако из-за очень малой концентра ции паров стронция в газовой фазе (мольная доля составляет Ю"6) образо вание конденсата SrO в виде самостоятельной фазы затруднено. Поэтому преобладающим механизмом конденсации является абсорбция молекул SrO частицами твердой фазы. Очевидно, что присутствие мельчайших пы левидных частиц в газовом потоке создает наиболее благоприятные усло вия для развития этого процесса. Это, в частности, подтверждается приве денными выше данными результатов анализов, указывающих на повы шенное содержание Sr в пылеватой фракции доменного шлама. Таким об-
Таблица 3.17
Распределевие стронция между фазами доменного процесса
Поступление в доменную печь
В виде SrO или SrS с минеральной частью шихты и кокса
Распределение между фазами, масс.%
Чугун |
Шлак |
Газ |
0 |
100 |
0 |
В составе органической части кокса |
0 |
25-35 |
65-75 |
Баланс мышьяка для доменного производства предприятии России, Германии, Египта и Турции, г/т чугуна (средние данные не менее 10 серий химических анализов)
|
|
|
|
Предприятие |
|
|
|
|
|
|
|
|
|
|
|
ОАО "Косо |
|
|
ОАО "Север |
ОАО "НЛМК" |
АК "Тулачер- |
горский М3" |
||||
Статья баланса |
|
|
||||||
сталь" |
|
|
|
мет" |
|
Производство |
||
|
|
|
|
|
||||
|
|
|
|
|
|
|
ферромарган- |
|
|
|
|
|
|
|
|
' ца |
|
|
г/г |
% |
г/т |
% |
г/т |
% |
г/т |
% |
Приход |
|
|
21 |
|
|
|
|
|
с железорудной частью |
5 |
62 |
91 |
13 |
81 |
720 |
99 |
|
с коксом |
3 |
38 |
2 |
9 |
3 |
19 |
5 |
1 |
В с е г о |
8 |
100 |
23 |
100 |
16 |
100 |
725 |
100 |
Распределение между про- |
|
|
|
|
|
|
|
|
дуктами в ходе доменной |
|
|
|
|
|
|
|
|
плавки: |
|
|
|
|
11 |
|
|
|
чугун |
4 |
50 |
15 |
65 |
69 |
450 |
62 |
|
шлак |
1 |
12,5 |
3 |
13 |
2 |
12 |
2 |
0 |
шлам |
Следы |
0 |
Следы |
0 |
Следы |
0 |
0 |
0 |
газ |
3 |
37,5 |
5 |
22 |
3 |
19 |
273 |
38 |
В с е г о |
8 |
100 |
23 |
100 |
16 |
100 |
725 |
100 |
|
|
|
|
Предприятие |
|
|
|
|
|
ОАО"Косо- |
|
|
|
|
|
|
|
|
горский М3" |
"EKO-Stahl" |
"Хадисолб" |
"Кардемир" |
||||
Статья баланса |
|
|
||||||
Производство |
(Германия) |
(Египет) |
|
(Турция) |
||||
|
|
|||||||
|
литейного чугу- |
|
|
|
|
|
|
|
|
на |
|
|
|
|
|
|
|
|
г/т |
% |
г/т |
% |
г/т |
% |
г/г |
% |
Приход |
|
|
120 |
99,2 |
350 |
100 |
230 |
98 |
с железорудной частью |
33 |
87 |
||||||
с коксом |
5 |
13 |
1 |
0,8 |
0 |
0 |
4 |
2 |
В с е г о |
38 |
100 |
121 |
100 |
350 |
100 |
234 |
100 |
Распределение между про |
|
|
|
|
|
|
|
|
дуктами в ходе доменной |
|
|
|
|
|
|
|
|
плавки: |
|
|
70 |
58 |
220 |
63 |
230 |
98 |
чугун |
30 |
79 |
||||||
шлак |
1 |
3 |
Не обн. |
0 |
Не обн. |
0 |
2 |
1 |
шлам |
0 |
0 |
0 |
0 |
" |
0 |
0 |
0 |
газ |
7 |
18 |
51 |
42 |
130 |
37 |
2 |
1 |
В с е г о |
38 |
100 |
121 |
100 |
350 |
100 |
234 |
100 |
разом, образующийся д фурменной зоне доменной печи возгон стронция выносится из печи с мельчайшими пылевидными частицами, не улавлива емая часть которых, прежде всего размером менее 0 , 0 1 мм, и обусловлива ет вышеупомянутый разбаланс.
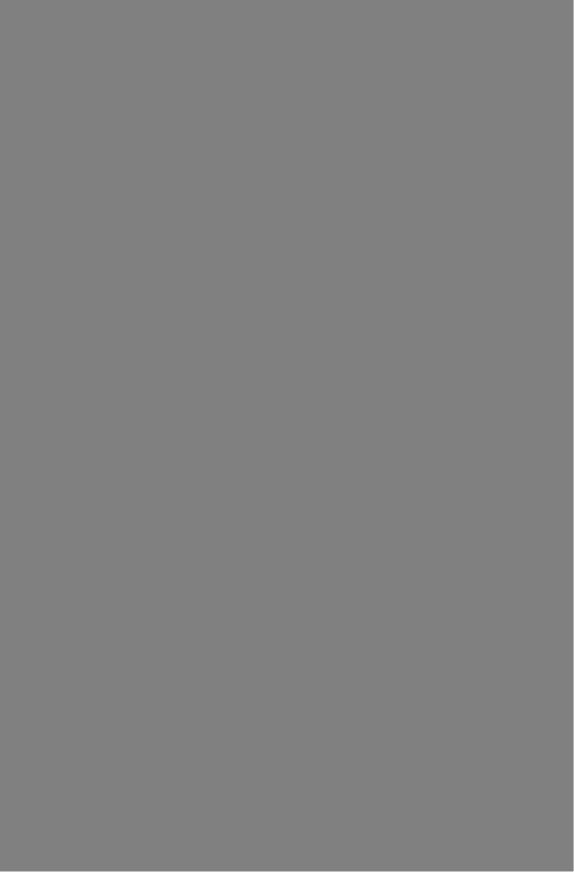
Распределение некоторых примесных элементов между основными продуктами доменной плавки при производстве передельного чугуна, абс. %
Химический элемент |
|
Переходит в основные продукты |
|
|
Чугун |
Шлак |
Газ (возгоны) |
||
|
||||
Ванадий |
88-90 |
8-10 |
1-2 |
|
Медь |
95-98 |
2-5 |
0 |
|
Никель |
90-95 |
2-3 |
2-7 |
|
Свинец** |
6-8 |
3-10 |
50-70 |
|
Титан |
15-15* |
77-82 |
0 |
|
Фосфор |
97-98 |
1-2 |
0,5-0,1 |
|
Хром |
88-92 |
8-10 |
1-4 |
*В доменной печи накапливается (без учета промывок горна) 3-8% чугуна от количества посту пающего в агрегат титана.
**До 40% свинца может накапливаться в лещади доменной печи в виде самостоятельной фазы.
Данные балансов мышьяка, составленных для доменных печей различ ных предприятий, и результаты термодинамического моделирования его поведения в доменном процессе позволяют построить принципиальную схе му поведения элемента в ходе доменной плавки в зависимости от того, в со ставе какого материала он попадает в агрегат.
Анализ показал, что поведение мышьяка в доменной плавке оказывает ся значительно более сложным, чем у рассмотренных ранее галлия и строн ция (см. табл. 3.19).
Анализ распределения между фазами доменного процесса галлия, мышьяка и стронция показывает, что для получения точных схем поведения микроэлементов в доменной печи потребуется надежная статистическая ин формация и проведение большого количества термодинамических расче тов, желательно также выполнение тонкого физического моделирования исследуемых процессов. В табл. 3.20 и 3.21 приведены данные последних ис следований о распределении примесных элементов между фазами доменно го процесса.
3.2.2.ОПРЕДЕЛЕНИЕ ХАРАКТЕРИСТИК
ИПОСТРОЕНИЕ СХЕМЫ ЭЛЕМЕНТОПОТОКА
Элементопотоки могут быть рассчитаны и схематично выражены для различных временных интервалов и характеризовать ситуацию в регионе в различные периоды. Для металлургического производства показательными являются интервалы от нескольких часов до суток. По-видимому, в дальней шем именно они и будут приниматься в качестве основы для анализа. В на стоящее время, особенно в условиях России, где необходимая информация чрезвычайно скудна, исходные данные для расчетов приходится получать из многочисленных источников, часто значительно разнесенных во времени, что несколько снижает точность проводимых вычислений.
Распределение между основными фазами доменного процесса и особенности поведения некоторых примесных микроэлементов при выплавке передельного чугуна
(по данным предприятий Европейской части России)
|
|
Приход в доменную печь |
|
||
|
|
|
В составе, масс. % |
||
Химический |
|
|
|
|
|
элемент |
Всего, г/т чугуна |
железорудной |
|
кокса |
|
|
|
||||
|
|
|
|
||
|
|
части шихты |
Всего |
В том числе в орга |
|
|
|
|
|||
|
|
|
нической части |
||
|
|
|
|
||
Барий |
200-500 |
40-60 |
40-60 |
10-50 |
|
Бериллий |
0,5-5,0 |
20-60 |
40-80 |
30-60 |
|
Бор |
50-70 |
40-70 |
30-60 |
25-45 |
|
Бром |
1-3 |
0 |
100 |
90 |
|
Вольфрам |
До 50 |
100 |
0 |
0 |
|
Иттрий и скан |
30-50 |
40-50 |
50-60 |
20-25 |
|
дий |
|||||
|
|
|
|
||
Кобальт |
До 50 |
До 100 |
До 100 |
До 40 |
|
Лантаноиды |
До 350 |
30-50 |
50-70 |
До 5 |
|
Молибден |
4-8 |
100 |
0 |
0 |
|
Олово |
До 40 |
95 |
5 |
0 |
|
Селен |
До 5 |
До 100 |
До 100 |
До 90 |
|
Сурьма |
5-8 |
80-90 |
10-20 |
До 15 |
|
Уран и торий |
До 10 |
До 80 |
До 20 |
0 |
|
Цирконий |
100-150 |
30-60 |
40-70 |
10-90 |
Наиболее важным результатом расчета элементопотоков является оценка накопления какого-либо элемента на территории региона, для че го необходимо знать параметры элементопотока за весь период функци онирования предприятия, а это в настоящее время для отечественных и зарубежных предприятий затруднительно. Поэтому для примера конкрет ного расчета мы используем некий “усредненный” элементопоток, харак теризующий ситуацию за весь период работы предприятия с момента его основания.
Распределение между продуктами процесса, масс. %
Чугун |
Шлак |
Газ |
Примечание |
(возгоны) |
|
||
|
|
|
0 |
100 |
0 |
|
Следы |
40-70 |
30-60 |
Все находящиеся в органической части кокса обра |
|
|
|
зуют возгоны и выносятся из печи, практически не |
|
|
|
улавливаемые современными очистными сооруже |
2-5 |
95-98 |
|
ниями |
До 1 |
|
||
5-10 |
5-10 |
До 90 |
Частично выносятся из печи, частично образуют |
|
|
|
контур циркуляции совместно со щелочными метал |
60-60 |
20-25 |
|
лами |
2-5 |
До 25% остается в печи в составе гарнисажа, воз |
||
0 |
75-80 |
|
можно в виде карбидов |
20-25 |
В "органической" части кокса возгоняются и выно |
||
95-100 |
До 5 |
0 |
сятся из печи, не улавливаемые в ходе газоочистки |
|
|||
0 |
60-80 |
5-10 |
25-30%-ная невязка баланса объясняется как вы |
|
|
|
носом возгонов через колошник печи, так и накоп |
|
|
|
лением их в гарнисаже и на поверхности лещади, |
100 |
0 |
0 |
возможно в виде самостоятельной фазы |
Возможно накопление в гарнисаже горна в виде |
|||
60-70 |
0 |
10-20 |
карбидов |
До 20% либо выбрасывается в атмосферу, минуя |
|||
До 100 |
До 90 |
До ю |
системы газоочистки, либо растворяется в свинце |
Поступая в печь с железорудным материалом, пере |
|||
|
|
|
ходит в шлак, а поступая в составе кокса, распре |
95-98 |
0 |
|
деляется между чугуном и газом |
До 5 |
|
||
0 |
100 |
0 |
|
0 |
100 |
0 |
|
В качестве объекта исследований возьмем предприятие ОАО “Север сталь” (ранее Череповецкий металлургический комбинат, основанный в 1955 г.). Выбор этого предприятия обусловлен, во-первых, наличием значи тельного количества необходимой для расчетов информации, а во-вторых, тем обстоятельством, что сырьевая база производства оставалась с момен та основания комбината практически неизменной, что позволяет достаточ но корректно распространять данные современных химических анализов на весь исследуемый период.
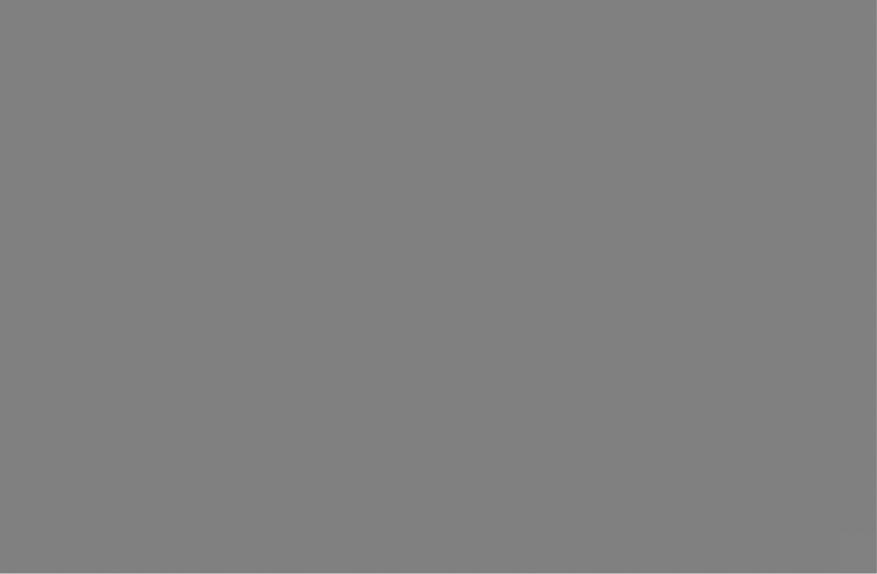
Расчет элементопотока проводим на примере до сих пор малоизученно го для условий черной металлургии примесного элемента - стронция.
Можно выделить ряд этапов развития металлургического производства в Череповецком регионе. Первоначально цеха располагались на возвышен ной местности. При дальнейшем расширении промышленной зоны для раз мещения производства использовались низинные районы, а для переплани ровки местности под застройку широко применялись различные отходы ме таллургического производства: шламы, шлаки, промышленный мусор и т.п. В связи с возрастанием и освоением новых видов производственных мощно стей, и следовательно, увеличением количества отходов (особенно в виде шламов), под их складирование были выделены специальные территории, занятые к настоящему времени шлаковыми отвалами, золошламонакопителями (ЗШН) и свалками. Следует отметить, что техногенные материалы широко применялись на комбинате также при перепланировках, строитель стве автомобильных дорог, прокладке железнодорожных путей, формиро вании производственного стока технических вод, дождевой, ливневой и па водковой канализации, прудов-осветлителей и т.п.
На рис. 3.8-3.10 приведены схемы расположения основных производст венных подразделений ОАО “Северсталь” и распространения техногенных грунтов в период 1955-1988 гг. В последующий период активного ввода но вых производственных мощностей на предприятии не было, а неутилизируемые отходы производства продолжали складироваться в ЗШН № 2.
В настоящее время территория предприятия, занятая производственны ми подразделениями, составляет около 16,5 км2, а территория, занятая тех ногенными грунтами (с учетом площади ЗШН № 1 и № 2), - около 24 км2.
Далее при расчетах накопления количества микроэлементов в грунтах, растворения и миграции их с грунтовыми, подземными и сточными водами и т.п. общая территория промышленной зоны г. Череповца принимается равной 50 км2 с учетом азотно-тукового производства (АТП), Череповецко го сталепрокатного завода (ЧСПЗ), муниципальной свалки твердых быто вых отходов (ТБО) и прилегающих территорий.
Освоение металлургического производства в Череповецком регионе на чалось с выплавки первичного металла - чугуна в доменных печах. Поэто му ретроспективный анализ развития производственных мощностей пред приятия удобно проводить именно на 1 т чугуна. Приведем основные ре зультаты за период функционирования предприятия с 1955 по 1995 г. по оп ределению объемов производств основных видов продукции, полуфабрика тов с учетом отходов производства, выбросов и т.д. Приведем основные чис ла, которые потребуются нам в дальнейшем (вся информация дана в кг на 1 т чугуна усредненно за указанный период):
Поступление шихтовых материалов:
угольный концентрат (в основном печорских углей) |
1290 |
железорудные концентраты (Ковдорского |
923 |
и Оленегорского месторождений) |
58 |
железная руда кусковая агломерационная |
|
окатыши Костомукшского ГОК |
535 |
известняк и доломит |
392 |
металлолом “со стороны” |
387 |
ферросплавы |
62 |
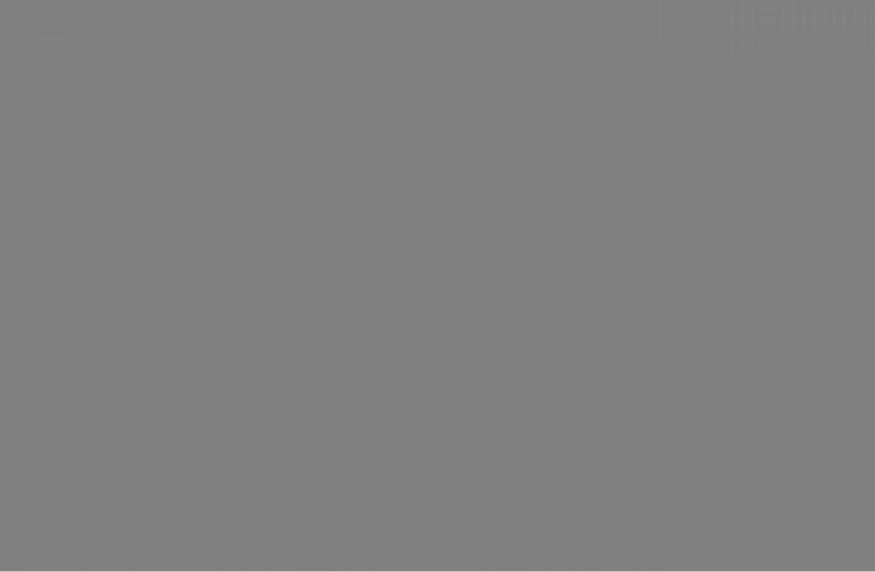
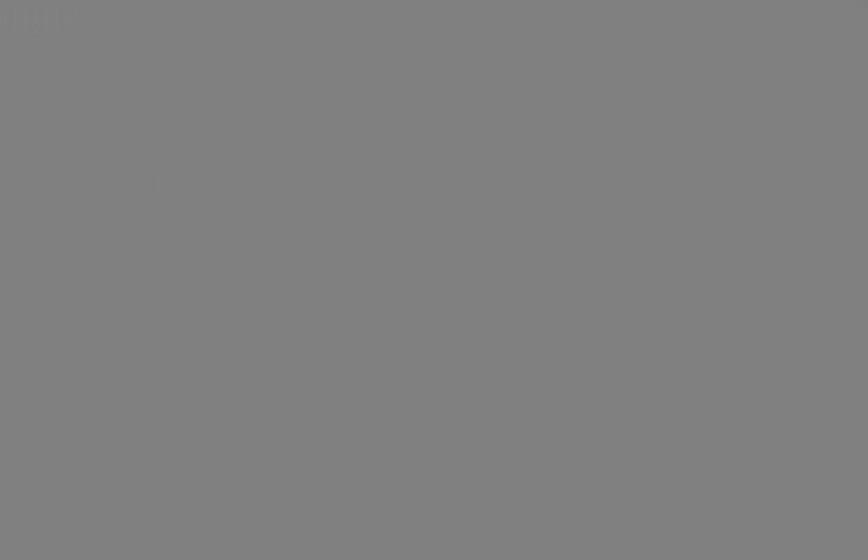
агломерат кокс доменный, литейный и коксик 537
Попутная продукция и отходы производства:
доменный шлак |
320 |
|
1OR |
||
сталеплавильные шлаки |
||
lzo |
||
золошлаковые отходы и шламы ТЭЦ |
85,5 |
|
и углеподготовительного отделения |
9*5 |
|
шламы: доменный |
||
мартеновский |
5 |
|
кислородно-конвертерный |
14 |
|
электросталеплавильный |
2 |
|
цеха изложниц и МНЛЗ |
7 |
|
сварочный шлак и шлам прокатных цехов |
8 |
Приход стронция на предприятие. В соответствии с данными химиче ского анализа (см. табл. 3.7-3.13, 3.15) и изменением структуры производст ва ОАО “Северсталь” приход стронция с угольным концентратом составлял в среднем 60 г/т чугуна. Причем в доменную печь попадало 35 г/т чугуна, а при сжигании угля в ТЭЦ направлялось около 25 г/т чугуна. Приход строн ция с железорудными материалами (концентратом и рудами) и флюсами со ставлял в среднем 7 г/т чугуна (в т.ч. с флюсами - 5 г/т чугуна). Таким обра зом, всего поступило стронция в производственный цикл ЧерМК - ОАО “Северсталь” за период 1955-1995 гг.:
(60 + 7) ■10* • 227,7 106 = 15255,9 т,
где 227,7 106 - количество чугуна, произведенного предприятием за этот период.
Поведение стронция при производстве чугуна. В доменные печи попа дает стронция 35 г/т чугуна с коксом и коксиком, 2 г/т чугуна с железоруд ными материалами и 2,5 г/т чугуна с флюсующими добавками. Согласно ко эффициентам распределения стронция между продуктами доменной плавки, определенным ранее, получим:
- в доменный шлак перейдет
2,0 + 2,5 + 35 1/3 + 35 2/3 • 0,3 = 23,2 г стронция/т чугуна;
- в выбросы попадает
352/3 • 0,7 = 16,3 г стронция/т чугуна;
-улавливается системами газоочистки 4,5 г стронция/т чугуна. Это количество в составе доменного шлама далее отправляется на аглофаб
рику, попадает в состав агломерата и в итоге также оказывается в домен ном шлаке.
Таким образом, 39,5 г стронция/т чугуна в первом приближении распре деляются следующим образом:
- в доменный шлак
23,2 + 4,5 = 27,7 г стронция/т чугуна;
- в возгоны, не улавливаемые газоочистными сооружениями доменного цеха
39,5 - 27,7 = 11,8 г стронция/т чугуна.
Образование шламов на ОАО "Северсталь" с 1986 по 1989 г.
Подразделение предприятия |
Количество шламов, тыс. т/год |
Отделение подготовки угля и коксохимическое производство Доменный цех Мартеновский цех
Электросталеплавильный цех Кислородно-конвертерный цех Теплоэлектроцентраль (№ 1 и № 2) Остальные производства В с е г о
380
42,5
45,0
20
130
365 (в т.ч. зола и шлак)
70,5
1053
Можно видеть, что часть стронция образует контур циркуляции с ко лошниковой пылью, агломерационным и доменным шламами. Принимая эту часть постоянной, мы в дальнейших расчетах ее не учитываем.
Стронций в сталеплавильном производстве. Анализ продуктов стале плавильного производства ОАО “Северсталь” показал присутствие строн ция только в сталеплавильных шлаках: ни в жидкой стали, ни в сталепла вильных шламах стронций не обнаружен. Источником же стронция в стале плавильных переделах является известь. Таким образом, стронций, попадая в сталеплавильные агрегаты в составе извести в количестве 2,5 г/т чугуна, в таком же количестве выносится из них в составе шлаков и направляется на хранение в отвалы или ЗШН (т.е. попадает в техногенные грунты на терри тории предприятия).
Поведение стронция при углеподготовке (УГФ) и углесжигании на ТЭЦ. Как уже отмечалось выше, из 60 г стронция/т чугуна, поступающего на предприятие в составе угольного концентрата, 35 г/т чугуна попадает в аглодоменный передел, а остальные 25 г/т частично переходят в шламы уг леподготовительных производств (УГФ) и в основном направляются на сжи гание на ТЭЦ в составе так называемого “промпродукта”. Определим пара метры движения стронция с углепродуктами.
В табл. 3.22 приведены данные об образующихся шламах в ОАО “Се версталь” с 1986 по 1989 г. Отметим, что среднегодовое производство чугу на в этот период составило 10,3 млн т.
Таким образом, общее количество неутилизируемых шламов (доменный шлам полностью используется в алгопроцессе) составляет
(1053 - 42,5)/10,3 = 98,1 кг шламов/т чугуна,
количество золошлаковых отходов (ЗШО) и шламов УГФ, КХП и ТЭЦ
(380 + 365)/10,3 = 72,3 кг ЗШО и шламов/т чугуна.
Среднее содержание стронция в золошлаковых отходах и шламах УГФ, КХП и ТЭЦ составляет около 58 г/т материала. Тогда на тонну чугуна это количество будет равно:
58 • 0,0723 = 4,2 г стронция/т чугуна.
Таким образом, подавляющая часть стронция (25,0 - 4,2 = 2 0 , 8 г/т чугу на), направляемая на ТЭЦ в качестве “промпродукта для сжигания, в итоге
Содержание стронция в различных фракциях промышленных отходов ЗШН № 1 и № 2
Фракция, мм |
Доля фракции в пробе, масс. % |
Количество стронция, г/т |
|
До 0,005 |
1 |
374 |
|
0,01 |
-0,005 |
1 |
106 |
0,05 |
-0,01 |
7 |
86 |
0,1 |
-0,05 |
27 |
30 |
0,25 |
-0,1 |
44 |
23 |
0,5 |
-0,25 |
И |
26 |
1-0,5 |
3 |
44 |
|
2-1 |
3 |
55 |
|
5-2 |
3 |
24 |
попадает в воздушный бассейн металлургического региона, минуя системы газоочистных сооружений (впрочем, следует отметить, что на ТЭЦ ОАО “Северсталь” такие системы отсутствуют).
Накопление стронция в золоиишмонакопителях. Известно, что микро элементы могут выноситься из ЗШН в составе мельчайшей пыли в резуль тате процессов перевеивания и вымываться в водный бассейн металлурги ческого региона. Оценим количество стронция, оставшегося в ЗШН.
На основании исследований, проведенных в МИСиС, определено содер жание стронция в материалах, складированных в ЗШН № 1 и № 2. В зависи мости от фракционного состава исследуемых материалов данные по содер жанию стронция приведены в табл. 3.23.
Среднее содержание стронция в материалах ЗШН составляет 35,6 г/т шлама.
Исходя из того, что ЗШН № 1 был введен в эксплуатацию в 1972 г., мож но определить, какое количество стронция накоплено в ЗШН:
178,6 • 106 • 0,0981 35,6 • 10^ = 623,7 т стронция,
где 178,6 106 - количество произведенного на предприятии чугуна за 1975-1995 гг., млн т; или 0,0981 35,6 = 3,5 г стронция/т чугуна.
Таким образом, из 4,2 г стронция/т чугуна, поступающего в ЗШН, 4,2 - 3,5 = 0,7 г стронция/т чугуна выносится из ЗШН в воздушный и водный бассейны региона.
Вынос стронция за территорию металлургического региона с пото ком подземных вод. На основе специальных исследований определены па раметры стока подземных вод Череповецкого района и содержание в них стронция (табл. 3.24).
Принимая содержание стронция в подземном стоке равным 0,45 г/мз и полагая интенсивность стока подземных вод равной 1070 м3 /сут., Получим общее количество стронция, выносимого с подземными водами ежегодно:
1070 • 365 • 0,45 • 10- 6 = 0,175 т/год.
При среднем производстве чугуна на предприятии в период с 1 9 3 9 п 0 1991 г. 7,65 млн т в год получим количество стронция, выносимого с цодзем-
Содержание стронция в подземных водах
Место отбора проб |
Количество стронция, г/м3 |
ЗШН N° 2 на левом берегу р. Кошта |
0,54 |
ТЭЦ № 2 |
0,60 |
Прокатные цеха |
0,25 |
Граница ЧСПЗ - прокатные цеха |
0,18 |
ЗШН N° 1 |
0,24 |
Свалка бытовых отходов на правом берегу р. Кошта |
0,23 |
ными водами, на тонну чугуна:
(0,175 106)/(7,65 • 106) = 0,02 г/т чугуна.
Вынос стронция за территорию металлургического региона с поверх ностным стоком. Поверхностный сток с территории металлургического комбината оценивается в количестве 1056 м3 /сут. При этом содержание стронция в поверхностных водах колеблется в пределах 1,32-5,11 г/м3, со ставляя в среднем 3,2 г/м3. Таким образом, количество стронция, выносимо го с поверхностным стоком, составляет:
1056 • 365 |
3,2 • 1 0 = |
1,23 т/год; |
или (1,23 |
106)/(7,65 |
106) = 0,16 г стронция/т чугуна. |
Определение количества стронция, растворенного в грунтовых водах.
Количество стронция, растворенного в грунтовых водах, можно определить следующим образом:
50 • 106 • 20 • 0,25 1,05 10- 6 = 262,5 т,
где 50 • 106 - территория металлургического комбината, м2; 20 - средняя глу бина залегания водонепроницаемого горизонта, м; 0,25 - средняя влажность грунтовых пород (до глубины 20 м), доли ед.; 1,05 • 10- 6 - среднее содержа ние стронция в грунтовых водах, т/м3;
или (262,5 • 106)/(227,7 106) = 1,15 г стронция/т чугуна.
Накопление стронция в грунтах металлургического региона. Накоп ление или рассеивание микроэлемента на территории рассматриваемого региона обусловлено общими закономерностями его миграции в различ ных ландшафтных условиях. В свою очередь, определяющую роль в про цессах миграции играют “геохимические барьеры” (термин предложен А.И. Перельманом). Геохимический барьер представляет собой участок с резкой сменой геохимической обстановки, которая приводит к осаждению мигрирующих химических элементов. Этот вопрос, недостаточно рассмо тренный в ресурсно-экологической литературе, следует изложить не
сколько подробнее.
Геохимические барьеры подразделяются на типы и группы, их класси фикация (по А.И. Перельману) приведена на рис. 3.11.
Механический барьер создается в результате смены рыхлых пород на плотные, поры которых по размерам меньше, чем ионы мигрирующих со-
Рис. 3.11. Классификация геохимических барьеров
единений, поэтому происходит прекращение миграции элементов в мине ральной и коллоидной форме. Механический барьер характерен для эле ментов, образующих малорастворимые соединения, а также для благород ных металлов и металлов, встречающихся в самородном состоянии: Ti, Zr, Сг, Nb, Au, Ru, IT, O S , Pt, W, Hf, Та и др.
Биогеохимический барьер определяется способностью растительных и животных организмов удерживать химические элементы в течение длитель ного времени. Биогеохимические барьеры относятся к числу наиболее рас пространенных в биосфере. Концентрация на этих барьерах химических элементов часто является стадией их биологического круговорота.
Краткая характеристика физико-химических барьеров приведена в табл. 3.25.
Подвижность и накопление мигрирующих химических элементов, хара ктерных для техногенных потоков вещества с точки зрения сочетания кис лотно-щелочных и окислительно-восстановительных условий среды, иллю стрируется данными табл. 3.26.
Таким образом, мигрирующие химические элементы, прежде всего ме таллы, отличаются ярко выраженной тенденцией к накоплению или выно су из основных видов почвообразующих пород (см. табл. 3.27).
Результаты исследований по определению содержания стронция в грун тах Череповецкого промышленного региона приведены в табл. 3.28.
Анализ полученных результатов показал, что среднее содержание стронция в техногенных грунтах, занимающих площадь около 28 км2, соста вляет 178 г/т грунта при фоновом содержании около 140 г Sr/т грунта. Сред няя мощность техногенных грунтов оценивается в 3,5 м. Таким образом, об щее количество стронция, перешедшего за время работы комбината в тех-
Вид барьера
Кислородный
Сероводородный
Глеевый
Физико-химические барьеры
|
Характерные элементы, |
Краткая характеристика |
накапливающиеся на |
|
барьере |
Образование нерастворимых окисленных соеди |
Fe, Мп, Со |
нений в результате реакций со свободным кис |
|
лородом |
|
Образование выпадающих в осадок сульфидов в |
Fe, V, Zn, Ni, С6, Си, |
результате реакций с H2S, присутствующим в |
Pb, As, Hg, Ag, Se |
природных водах в свфбодном или диссоцииро |
|
ванном состоянии, а также в виде раствора |
|
Участки разложения органических веществ без |
V, Se, Mo, Co |
доступа кислорода (краевые зоны болот, солоди |
|
и солонцы в лесостепной зоне и на луговых поч |
|
вах и т.п.), где глеевые воды резко меняют свой |
|
характер |
|
Кислый |
Резкое уменьшение pH |
Si, Mo, Se, V, Ge |
Нейтральный |
Образование слабоподвижных соединений в гу |
Си, Fe, Ba, Sr, Zn, V, |
(кальциевый) |
мусовом и иллювиальном почвенных горизонтах |
As, Hg |
Щелочной |
Скачкообразное увеличение pH |
Fe, Ca, Mg, Mn, Sr, V, |
|
|
Cr, Zn, Си, Ni, Pb, Cd |
Испарительный |
Прекращение миграции всех растворенных |
|
|
в воде веществ |
|
Сорбционный |
Участки встречи водного или газового потоков с |
|
|
сорбентами (глинами, гумусовыми веществами, |
|
|
гидроксидами железа и марганца и т.п.) |
|
Термодинами |
Резкое изменение давления и температуры |
|
ческий |
в конкретной геохимической системе |
|
Таблица 3 2 6
Подвижность химических элементов в зависимости от сочетания кислотно-щелочных и окислительно-восстановительных условии среды
Элементы
Кислотно-ще |
Окислительно-восста |
Слабо подвижны, активно |
лочные условия |
новительные условия |
|
|
|
накапливаются |
Кислые |
Окислительные |
Мп, Мо |
|
Восстановительные |
As, Se, Mo, V |
|
глеевые |
|
Нейтральные |
Окислительные |
Pb |
Щелочные |
Окислительные |
Pb |
|
Восстановительные |
Pb, Cd, Cu, Zn, Co |
|
Восстановительные |
Pb, Cd, Hg, As, Cu, Zn, |
|
сероводородные |
Co, Ni, Cr |
Легко подвижны, накап ливаются только в испа рительных бассейнах
Cu, Zn, Hg
As, Se
As, Se
Ni, Hg
Характерные содержания элементов в основных почвообразующих породах России, не подвергнутых техногенному воздействию
|
------------------------------------------------------------------------------------------------------------------------------- --------- ------ -------------------------------- Г ........ |
1 ■ ---------------------------------------------------- |
|||||||
|
|
|
Основные почвообразующие породы, г/т |
|
|
||||
Химиче |
Лёссы |
Мор |
Озерно- |
Покров |
Сугли |
Супес |
Флюви- |
Шунги- |
Кларк |
ский |
и лёссо |
ледни |
чаная |
огляци- |
|||||
элемент |
ские |
ные суг |
нистая |
и пес |
товые |
лито |
|||
|
видные |
глины |
ковые |
линки |
морена |
чаная |
альные |
породы |
сферы |
|
суглинки |
глины |
пески |
||||||
|
|
|
|
морена |
|
|
|||
|
|
|
|
|
|
|
|
|
|
В |
50 |
130 |
30 |
25 |
22 |
20 |
10 |
55 |
12 |
V |
170 |
140 |
180 |
90 |
80 |
30 |
20 |
200 |
90 |
Сг |
95 |
86 |
140 |
75 |
65 |
40 |
36 |
20 |
83 |
Мп |
500 |
>4000 |
800 |
800 |
600 |
350 |
200 |
1660 |
1000 |
Со |
15 |
10 |
10 |
10 |
9 |
6 |
2 |
30 |
18 |
Ni |
30 |
58 |
40 |
38 |
22 |
15 |
5 |
500 |
58 |
Си |
25 |
23 |
25 |
23 |
20 |
12 |
5 |
260 |
47 |
Zn |
70 |
70 |
54 |
49 |
47 |
28 |
10 |
129 |
83 |
Мо |
0 |
15 |
0 |
0 |
0 |
0,8 |
0,8 |
1,9 |
1,1 |
I |
1,1 |
5 |
1 |
0,9 |
0,9 |
0,1 |
0,1 |
0 |
0,4 |
Таблица 3.28
Содержание стронция в грунтах на территории ОАО "Северсталь"
|
Глубина |
|
Количество стронция, г/т |
||
Место отбора пробы |
|
|
|
||
бурения, м |
в пробе |
среднее |
аномальное (до глубины) |
||
|
|||||
|
|
в пробе |
|||
|
|
|
|
||
Район кислородно-кон |
18 |
123-171 |
140 |
171 (до 0,4 м) |
|
вертерного цеха |
|
|
|
|
|
Район ЧСПЗ |
4 |
117-326 |
168 |
300-326 (до 1,1 м) |
|
Завод бетонных изделий |
3 |
131-195 |
158 |
174-195 (до 0,6 м) |
|
Левый берег р. Кошта |
21 |
94-192 |
150 |
176-192 (до 0,6 м) |
|
Район ЗШН № 2 |
13 |
88-237 |
169 |
197-273 (до 0,6 м) |
|
Берег р. Кошта |
13 |
133-146 |
139 |
Равномерное распределение |
|
у ЗШН № 2 |
|
|
|
|
|
ЗШН № 1 |
23 |
128-247 |
137 |
193-247 (до 0,6 м) |
|
Сток из ЗШН № 1 |
23 |
123-192 |
142 |
Равномерное распределение |
|
Район АТП |
12 |
137-240 |
148 |
240 (до 0,1 м) |
|
Район АТП и КХП |
6 |
167-179 |
174 |
Равномерное распределение |
|
Шлаковый отвал |
8 |
156-286 |
160 |
286 (до 0,1 м) |
|
На границе порта и завода |
3 |
165 |
145 |
Равномерное распределение |
|
бетонных изделий |
|
|
|
|
|
Порт |
4 |
160 |
140 |
Равномерное распределение |
|
На границе прокатного |
5 |
80-350 |
188 |
200-350 (до 2 м) |
|
цеха и жилых районов |
|
|
|
|
ЧСПЗ - Череповецкий сталепрокатный завод; АТП - азотно-туковое производство; КХП - кок сохимическое производство.
Ряды биологического поглощения
Эффективность
поглощения
Ряд |
Группа |
Элементы биоло Энергичного гического накоп-
ления
Сильного
Элементы биоло Среднего гического захвата
Слабого и очень слабого
Коэффициент поглощения Ах
100п |
Юл |
п |
0,1/1 |
0,01-0,1/1 |
Р, S, Cl, Br, I
Са, Na, К, Mg, Zn, В, Se, Sr
Mn, F, Ba, Ni, Cu, Ga, Co, Pb,
Sn, As, Mo, Hg, Ag, Ra
Si, Al, Fe, Ti, Zr, Rb, V, Cr, Li, I, Nb, Be, Cs, Та, W, Se, Sb, Cd
ногенные грунты, составляет:
28 10б • 3,5 • 1,6 • (178 - 140) • 10- 6 = 5958,9 т или 26,17 г/т чугуна,
где 28 • 1 0 б - общая площадь техногенных грунтов на территории металлур гического региона; 3,5 - средняя мощность техногенных грунтов, м; 1,6 - средняя плотность грунта, т/м3; (178 - 140) - разность между содержанием стронция в техногенных грунтах и фоновым содержанием, г/т.
Аккумулирование стронция растительным покровом. Аккумуляция микроэлементов растительным покровом оценивается коэффициентом биологического поглощения А х (табл. 3.29)
А, = 1х/пх,
где 1Х- содержание элемента в золе растения; пх - содержание элемента в гор ной породе или почве, на которой произрастает растение (кларк концентрации).
Стронций относится к элементам очень интенсивного биологического накопления (Ах = 10-100, в среднем для условий Севера Европейской части России - 75). Кроме того, у стронция обнаруживается тенденция к накопле нию в свежем опаде лиственного леса и лесной подстилке. В озеленении тех ногенных грунтов северной и средней полосы России во второй половине XX века наиболее часто использовалась липа мелколистная. Для этой дре весной породы характерно интенсивное накопление таких элементов, как Sr, Мо, Си (табл. 3.30).
Определим количество стронция, аккумулируемого растительным по кровом Череповецкого промышленного района:
178 • КН • 50 • 106 • (0,35/10) • 5 • 0,252 • (3,14/4) • 0,2 • 0,035 • 75 =
= 4,1 т стронция или 0,18 г Sr/т чугуна,
где 178 10- 6 - содержание стронция в технических грунтах, т/м3; 50 • 106 - территория металлургического комбината, м2; 0,35 —площадь, занимаемая зелеными насаждениями, доли ед.; 1 0 —площадь, занимаемая одним дере вом, м2; 5 —средняя высота дерева, м; 0,2 —плотность древесины, т/м3; 0,035 —
Таблица 3 3 0
Интенсивность биологического поглощения микроэлементов липой мелколистно**
Тип насаждений |
|
Коэффициент поглощения Ах |
|
||
Юл |
л |
0,1л |
0,01-0, In |
||
100л |
|||||
Лесопарки |
Sr, Zn |
Mo, Cu, Ag, |
Mn, Pb, Cr, |
Ti, V, Co, Sn |
|
|
|
Ba |
Ni |
|
|
Зона промышленных Ag |
Mo, Ni, Sr, |
Mn, Pb, Sn |
Cr, Co |
Ba, Ti, V |
|
предприятий |
Zn, Cu |
|
|
|
|
Зона предприятий |
Mo, Sr, Sn, |
Ni, Zn, Pb, |
Mn, Sn, Ba |
V, Co, Ti |
|
черной металлургии |
Zn |
Cu, Cr, Ag |
|
|
|
Посадки вдоль ма |
Sr, Mo |
Cu, Ag, Zn, |
Mn, Co, Ba |
Ti,V |
|
гистралей электро |
|
Sn, Pb, Cr, Ni |
|
|
|
передач: |
|
|
|
|
|
5-10 тыс. кВт/ч |
|
|
|
|
|
3-5 тыс. кВт/ч |
Sr, Mo |
Cu, Ag, Zn |
Sn, Pb, Cr, |
V |
|
|
|
|
Ni, Ba, Ti, |
|
|
|
|
|
Mn, Co |
|
|
3-5 тыс. кВт/ч |
Sr, Mo, Cu |
Zn, Ag, Pb, |
Sn, Co, Cr, |
Ti, V |
|
|
|
Ni |
Mn, Ba |
|
Таблица 3 3 1
Элементопоток стронция для Череповецкого металлургического региона за 1955-1995 гг.
Статья баланса |
Количество |
% |
|
|
стронция, т |
|
|
Приход |
|
100 |
|
В с е г о |
15255,9 |
||
В том числе: |
|
|
|
с угольным концентратом |
13662,0 |
89,6 |
|
с железорудными материалами |
455,4 |
3,0 |
|
с флюсами |
1138,5 |
7.4 |
|
Расход |
|
|
|
Продукция (доменный шлак) |
6307,3 |
41,3 |
|
Накоплено в техногенных грунтах |
|
|
|
В с е г о |
7325,1 |
48.0 |
|
в том числе: |
|||
|
|
||
в ЗШН и шлаковых отвалах |
1366,2 |
|
|
собственно в грунтах |
5958.9 |
|
|
Выбросы в водную среду |
|
||
|
|
||
В с е г о |
303,5 |
2,0 |
|
В том числе: |
|||
|
|
||
грунтовые воды |
262,5 |
|
|
поверхностные сточные воды |
|
||
36,4 |
|
||
подземные воды |
4,6 |
|
|
Аккумулировано растительным покровом |
0ЧУ, J3 |
||
40,1 |
|||
Выбросы в воздушный бассейн за территорию предприятия (по |
1279,9 |
8,4 |
|
разности) |
|
|
Таблица 3.32
Элементопотоки V, Cd, Со, Си, Ni, Pb, Сг, Zn для Череповецкого металлургического
Статьи баланса |
Ванадий |
|
|
т |
% |
Приход |
|
|
В с е г о |
46291,4 |
100 |
В том числе: с угольным |
10701,9 |
23,1 |
концентратом |
31718,6 |
68,5 |
с ж/рудным материалом |
||
с флюсами |
3870,9 |
8,4 |
Расход |
33722,4 |
|
В с е г о |
72,8 |
|
Продукция |
31878,0 |
|
В том числе: металлопродукция |
|
|
попутная продукция |
1844,4 |
|
Накоплено в техногенных |
|
|
грунтах |
11885,9 |
|
В с е г о |
25,75 |
|
В том числе: в ЗШН и |
2960,1 |
|
шлаковых отвалах |
|
|
собственно в грунтах |
8925,8 |
|
Выбросы в водный бассейн |
|
|
В с е г о |
68,3 |
0,15 |
В том числе: грунтовые воды |
45,5 |
|
поверхностные сточные воды |
22,8 |
|
подземные воды |
0 |
|
Аккумулировано растительным |
0 |
0 |
покровом |
|
|
Выбросы в воздушный бассейн |
614,8 |
1,3 |
за территорию предприятия (по |
|
|
разности) |
|
|
Химические элементы |
|
|
|
Кадмий |
|
|
Кобальт |
т |
% |
т |
% |
1161,3 |
100 |
23407.6 |
100 |
387,1 |
33,3 |
4280,8 |
18,3 |
728,6 |
62,7 |
17259,7 |
73,7 |
0 |
0 |
1867,1 |
8,0 |
159,4 |
13,7 |
13639,2 |
58,3 |
68,3 |
|
12580,4 |
|
91,1 |
|
1058,8 |
|
842,5 |
72,5 |
9483,7 |
40,5 |
364,3 |
|
1115,7 |
|
478,2 |
|
8368,0 |
|
45,5* |
3,9 |
22,8 |
0,1 |
45,5 |
|
22,8 |
|
0 |
|
0 |
|
0 |
1,0 |
0 |
|
11,4 |
11,4 |
0,005 |
|
102,5 |
8,8 |
250,5 |
1,05 |
среднее содержание золы в древесине, доли ед.; 7 5 —коэффициент интенсив ности биологического поглощения стронция.
Построение схемы элементопотоки стронция. Итак, мы рассмотрели все основные стадии движения стронция в производственном цикле метал лургического предприятия ОАО “Северсталь” и на территории формируе мого предприятием промышленного региона. Теперь можно построить элементопоток стронция в численной форме (табл. 3.31) и в графическом виде (рис. 3.12).
В соответствии с изложенной методикой для рассмотренных выше усло вий Череповецкого металлургического региона были рассчитаны элементо потоки для следующих химических элементов: ванадия, кадмия, кобальта, ме ди, никеля, свинца, хрома и цинка. Элементопотоки приведены в табл. 3.32 и на рис. 3.13-3.20. Анализ полученных результатов показывает, что:
|
|
|
Химические элементы |
|
|
|
|
||
Медь |
|
Никель |
|
Свинец |
|
Хром |
|
Цинк |
|
т |
% |
т |
% |
т |
% |
т |
% |
т |
% |
12717,0 |
100 |
79717,8 |
100 |
29919,8 |
100 |
222690,6 |
100 |
86298,3 |
100 |
3051,2 |
24,0 |
14140,2 |
17,7 |
8197,2 |
27,4 |
15028,2 |
6,7 |
3643,2 |
4,2 |
7798,7 |
61,3 |
64165,9 |
80,5 |
21722,6 |
72,6 |
199692,9 |
89,7 |
77418,0 |
89,7 |
1867,1 |
14,7 |
1411,7 |
1,8 |
0 |
0 |
7969,5 |
3,6 |
5237,1 |
6,1 |
10030,2 |
78,9 |
55490,5 |
69,6 |
7832,8 |
26,2 |
189901,8 |
85,3 |
26185,5 |
30,3 |
9905,0 |
|
55353,9 |
|
7104,2 |
|
185530,0 |
|
7969,5 |
|
125,2 |
|
136,6 |
|
728,6 |
|
4371,8 |
|
18216,0 |
|
2468,2 |
19,4 |
24188,6 |
30,35 |
16781,5 |
56,1 |
22337,4 |
10,0 |
52462,1 |
60,8 |
979,0 |
|
3574,9 |
|
3825,4 |
|
5829,1 |
|
32105,7 |
|
1489,2 |
|
20613,7 |
|
12956,1 |
|
16508,3 |
|
20356,4 |
|
207,2 |
1,6 |
36,5 |
0,05 |
216,3 |
0,7 |
9369,9 |
4,2 |
592,1 |
0,7 |
136,6 |
|
34,2 |
|
102,5 |
|
11,4 |
|
409,9 |
|
63,8 |
|
2,3 |
|
68,3 |
|
3574,9 |
|
113,9 |
|
6,8 |
0,1 |
0 |
|
45,5 |
|
5783,6 |
0 |
68,3 |
|
11,4 |
2,2 |
- |
2,3 |
- |
0 |
409,9 |
0,5 |
||
0 |
0 |
0 |
0 |
5086,9 |
17,0 |
1081,6 |
0,5 |
6648,7 |
7,7 |
-коэффициент извлечения микроэлементов в металлургическую про дукцию колеблется в широких пределах от 13,7% для кадмия до 85,3% для хрома;
-количество микроэлемента, остающегося (накапливающегося) в ме
таллургическом регионе в составе техногенных грунтов, также колеблется в широких пределах: от 10% - для хрома, до 72,5% - для кадмия.
- доля микроэлементов, рассеиваемых в окружающую среду через вод ный и воздушный бассейны, невелика и для большинства исследованных ме таллов равна 1,6—3,2%. Исключение составляют хром, активно мигрирую щий в водной среде (4 ,2 % выбросов), кадмий и свинец (соответственно 8 , 8 и 1 1 ,6 %), распространяющиеся за пределы региона с выбросами в атмосферу.
Таким образом, можно считать установленным фактом, что микроэле менты, поступающие в производственный цикл предприятий черной метал-
лургии в ходе соответствующих технологических операций, преимущест венно попадают в состав готовой продукции или накапливаются на террито рии металлургического региона. Во втором случае они локализуются в техногснных грунтах, т.е. в основном в золошламонакопителях, шлаковых отвалах, на свалках строительного мусора, а также в близлежащих грунтах, причем в основном на небольшой глубине - до 3,5—4 м. В результате на тер ритории промышленного предприятия непосредственно в ходе его функци онирования формируется техногенное месторождение. В рассматриваемом случае это комплексное месторождение цветных и редких металлов, коли чественную основу которого составляют цинк, никель, хром и свинец. По мимо детально рассмотренных микроэлементов в состав месторождения в значимых количествах входят лантаноиды, молибден, марганец, мышьяк, ниобий, литий, рубидий и некоторые другие элементы. Общая мощность месторождения может быть оценена в 200—250 тыс. т цветных и редких ме таллов. Примерная структура месторождения с указанием границ распро странения некоторых элементов приведена на рис. 3.21—3.24 (см. вклейку).
3.2.3. ЭЛЕМЕНТОПОТОКИ И ФОРМИРОВАНИЕ
“ТЕХНОГЕННЫХ МЕСТОРОЖДЕНИЙ”
Проведенные расчеты показывают, что за время существования ОАО “Северсталь” на его собственной и прилегающих к нему территориях сфор мировалось новое антропогенное образование, сравнимое по мощности с крупным месторождением полиметаллического сырья. Подобное образова ние может быть названо “техногенным месторождением”. Череповецкое техногенное “месторождение” содержит более 200 тыс. т цветных и редких металлов, около 18 тыс. т мышьяка и до 3,5 тыс. т фтора.
ОАО “Северсталь” можно отнести к сравнительно молодым предпри ятиям. Вполне очевидно, что на территории других крупных предприятий металлургического, химического, машиностроительного и других комплек сов, особенно существующих более 50-60 лет, могут сформироваться мощ ные техногенные “месторождения” рудных и нерудных материалов. Так, по ориентировочным расчетам, на территориях Магнитогорского, Ново-Ли пецкого, Нижне-Тагильского металлургических комбинатов существуют техногенные “месторождения” объемом более 1 млн т цветных и редких ме таллов каждое.
Техногенное “месторождение” является основным по количеству, наи более разнородным по составу и наименее изученным видом техногенных ресурсов. Материалы, слагающие техногенные “месторождения”, отлича ются широким спектром физических, химических, механических и других характеристик. Составление кадастра этих “месторождений” даже при са мом заинтересованном отношении займет не один десяток лет, и, наверняка»будет предложена не одна классификация подобных “месторождений” Например, по данным ЕЭС, в первой половине 90-х годов XX в. в странах со общества ежегодно образовывалось свыше 2 млрд т техногенных материа лов (отходов), в том числе (в млн т):
твердых бытовых отходов - 150; промышленных отходов - 330; сельскохозяйственных отходов - 700;
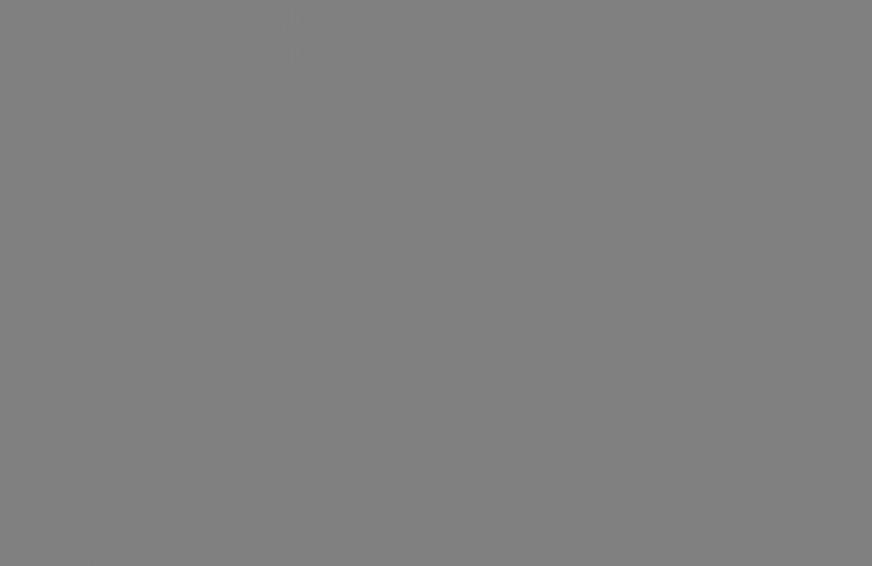
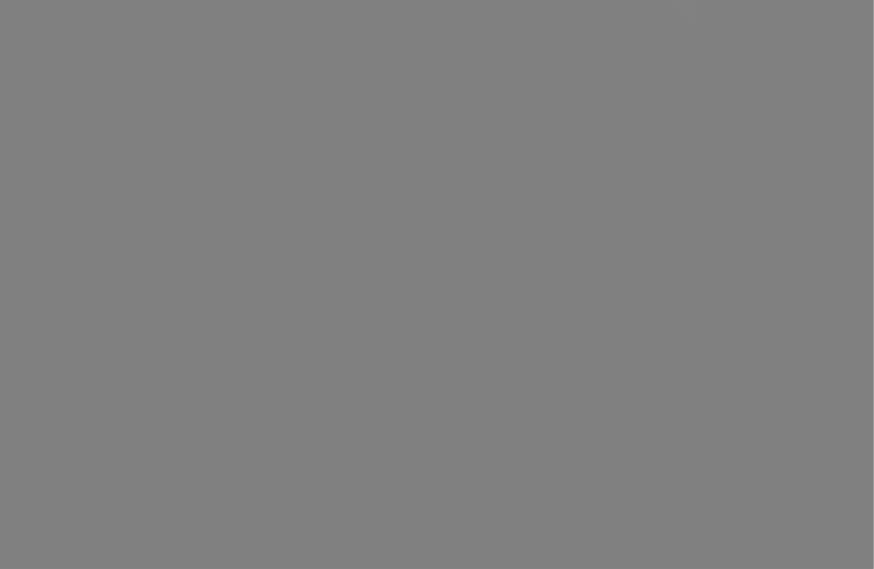
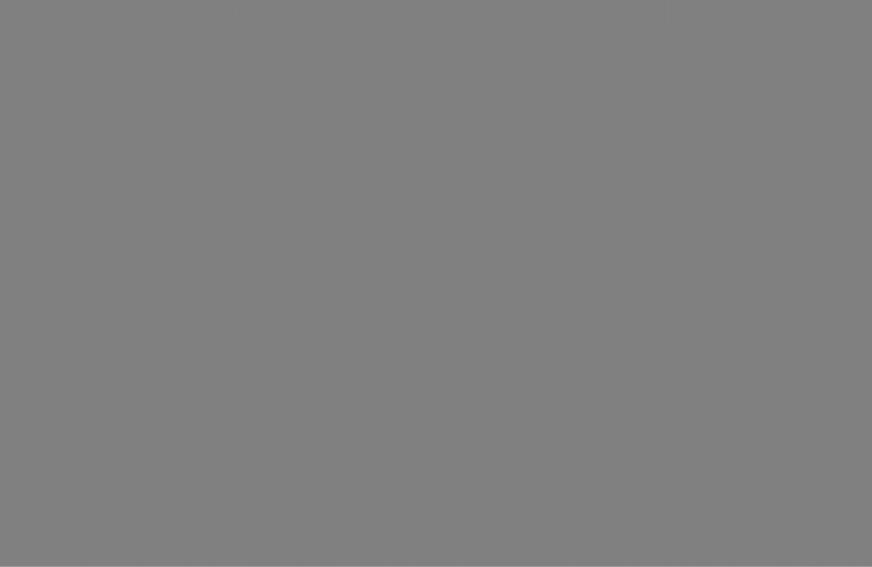
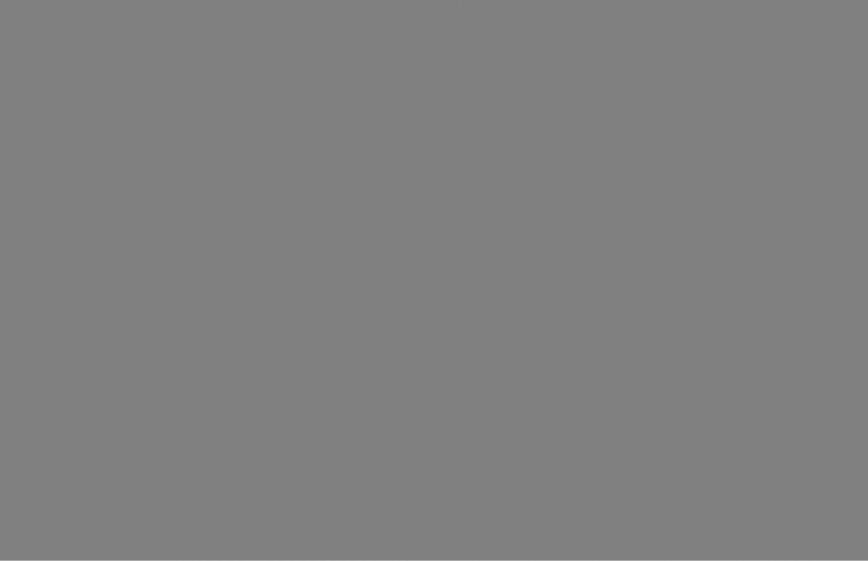
отходов горнорудного производства - 360; различных шламов - 620; строительного мусора - 260; перемещенного грунта - 50; золошлаковых отходов - 30.
Отметим, что страны ЕЭС находятся в относительно благополучном состоянии по сравнению с регионами - производителями основных энер гетических и материальных ресурсов. Во многих странах, к которым от носится и Россия, объем накопления отходов горнорудного и энергетиче ского комплексов существенно выше, чем в странах сообщества. Тем не менее приведенные цифры позволяют оценить значимость анализируе мой проблемы.
Несмотря на все многообразие техногенных месторождений, можно вы делить некоторые их общие черты. Техногенные “месторождения” в отли чие от природных месторождений возникли как “непланируемая” продук ция, и их запасы формировались стихийно. Отраслям народного хозяйства было выгодно использовать первичное сырье, и анализом техногенных ме сторождений практически никто не занимался. Можно сказать, что техно генные отходы - это “сырье неизвестно для чего”, сырье “без дальнейшей судьбы”. Поэтому выделим основные особенности техногенного сырья, от личающие его от природных ископаемых.
1 . Техногенные месторождения - продукт “быстрого созревания”, пери од их жизни - десятки лет вместо миллионов лет, характерных для природ ных месторождений. При этом запасы техногенных месторождений посто янно пополняются за счет “свежих” отходов.
2 . Малый срок жизни техногенного месторождения определяет более низкий уровень его однородности, большой разброс свойств по площади и глубине залегания.
3.“Созревание” техногенного месторождения означает изменение свойств техногенного сырья во времени и сильную зависимость свойств и скорости их изменений от параметров окружающей среды (климат, роза ве тров, изменение влажности и др.).
4.В техногенных отходах могут находиться опасные компоненты, на “дезактивацию” которых природе потребуются миллионы лет.
5.Техногенное сырье имеет, как правило, повышенную концентрацию большинства таких элементов, содержание которых в земной коре мало. С этой точки зрения техногенные материалы - это первичное сырье, прошед шее стадию обогащения.
6 . Для определения качества (стандартов) техногенного сырья методы,
применяемые для контроля свойств природного сырья, неприменимы. Нуж но определить заново набор свойств, характеризующих качество техноген ного сырья, из которых ряд представлен совершенно новыми (скорость из менения свойств, участие в катализе природных, например окислительных процессов, однородность свойств, доля окисленных компонентов и др.). Эти показатели качества должны контролироваться во всех видах техногенного сырья. Наряду с этим следует оценивать те свойства техногенного сырья, которые имеют значение для избранного способа их переработки.
В итоге можно считать, что техногенное сырье не лучше и не хуже при родного Сырья. Оно - другое сырье.