
книги / Материаловедение и технологии современных и перспективных материалов
..pdf2. Химические методы:
2.1.Плазмохимический (TiCl4, SiCl4 + реакционные газы C2H2, NH3 = карбиды, нитриды Zr(NO3)4·5H2O = ZrO2 + HNO3).
2.2.Лазерный.
2.3.Ударно-волновой (алмаз, BN, Аl2О3, SiO2,TiO2, MgO, ZrO2).
2.4.Электровзрыв проводника (104–106 А/мм2) в реакционном
газе.
2.5.СВС – самораспространяющийся высокотемпературный
синтез:
горючее (Ti, Zr, Hf, V, Nb, Ta, Mo, W) + окислитель (Si, N, O, S, Se) = продукт реакции + тепловой эффект.
Например: Zr + O2 = ZrO2 + Q.
2.6.Восстановление:
оксид металла + углерод = карбид металла + СО2. Например: WO3 + C = WC + СО2.
2.7. Гидротермальный синтез. Химическая реакция при Т =
=100…70 °С и Р до 100 МПа.
2.8.Химическое осаждение из растворов солей, в том числе золь-гель технология:
соль + осадитель = гидроксид → сушка → → оксид → восстановление.
Например: ZrCl4 + Y(NO3)3 + AlCl3 + NH4Cl = Zr(OH)4↓ +
+Y(OH)3 + Al(OH)3 + NH4Cl + NH4NO3.
2.9.Механохимический синтез: Ti + C = TiC.
2.10.Распылительная сушка.
2.11.Криохимический метод (скоростное замораживание растворов солей, удаление льда).
2.12.Прямой синтез из элементов: Ti + N = TiN. Технологический процесс получения изделий из керамики
включает в себя формование и обжиг.
131
При формовании керамики основным требованием является равномерная укладка частиц без существенных напряжений.
Способы формования:
1.Прессование с пластификатором.
2.Шликерное формование.
3.Инжекционное формование.
4.Изостатическое формование и др.
Кроме традиционного обжига (нагрев и выдержка без давления) могут быть применены горячее прессование или микроволновое спекание.
Для активации спекания используют:
•реакционное спекание,
•жидкофазное спекание,
•уменьшение размеров частиц.
Можно ли ожидать в ближайшем будущем появления принципиально новых керамических материалов? На этот вопрос следует ответить утвердительно. Примером служит полученная сравнительно недавно в Японии сверхпластичная керамика на основе тетрагональной модификации диоксида циркония, легированного 3 мол. % оксида иттрия.
При специфических условиях подготовки сырья и спекания получается поликристаллический материал с размером кристаллитов 0,3 мкм, который способен деформироваться, вытягиваясь под действием внешних нагрузок вдвое по сравнению с первоначальной длиной. Характерно, что после такой вытяжки керамика имеет прочность, превышающую прочность нитрида кремния, считающегося наиболее перспективным конструкционным материалом. Более того, нитрид и карбид кремния могут деформироваться без разрушения не более чем на 3 %, что в 40 раз меньше, чем созданный сверхпластичный материал на основе твердого раствора диоксида циркония и оксида иттрия. Это создает исключительные перспективы применения последнего, делая доступной обработку его такими традиционными в металлообработке приемами, как экструзия, волочение, ковка.
132
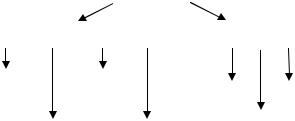
Грандиозные перспективы открыты перед сверхпроводящей керамикой и совсем недавно созданной керамикой с гигантским магнитным сопротивлением, перед новым поколением конструкционной керамики, получившей название синергетической из-за нелинейного эффекта взаимодействия матрицы и наполнителя, давшего возможность производить керамические композиты с рекордно высокой ударной вязкостью.
3.4. Методы получения покрытий и пленок
Многие современные и перспективные материалы, особенно градиентные слоистые, получают методами нанесения покрытий. При формировании покрытия между подложкой и слоем возникают характерные для композиционных материалов взаимодействия:
•химическое и диффузионное (обмен веществом),
•механическое (адгезия, изменение поверхностной энергии, межфазная граница),
•физическое («эффекты близости», фазовые переходы, термическое расширение, анизотропное изменение объема элементарной ячейки).
В зависимости от толщины покрытия делятся на толстые (от микрометров до миллиметров) и тонкие (от нанометров до микрометров). Методы получения тех и других различаются (рис. 3.32).
|
|
|
|
|
|
|
Покрытия |
|
|
|
|
|
|
|
||
|
|
|
|
|
|
|
|
|
|
|
|
|
|
|
|
|
|
|
|
|
|
|
|
|
|
|
|
|
|
|
|
|
|
|
|
|
Толстые |
|
|
|
|
|
|
Тонкие (пленки) |
|
|||||
|
|
|
|
|
|
|
|
|
|
|
|
|
|
|
|
|
|
|
|
|
|
|
|
|
|
|
|
|
|
|
|
|
|
Горячее |
|
|
Электролиз |
|
|
|
|
|
|
|
|
|
||||
погружение |
|
|
|
|
|
|
|
|
CVD |
|
PVD |
|
||||
|
|
|
|
|
|
|
|
|||||||||
|
|
|
|
|
|
|
|
|
|
|
|
|
|
|
|
|
|
|
|
|
|
|
|
|
|
|
|
|
|
|
|
|
|
|
|
|
|
|
|
|
|
|
|
|
|
|
|
|
||
|
|
|
|
|
|
|
|
|
|
|
|
Эпитаксия |
|
|
||
|
Газотермическое |
|
|
Наплавка |
|
|
||||||||||
|
|
|
|
|
|
|
|
|
|
|
||||||
|
|
напыление |
|
|
|
|
|
|
|
|
|
|
||||
|
|
|
|
|
|
|
|
|
|
|
|
|||||
|
|
|
|
|
|
|
|
|
|
|
|
|
|
Рис. 3.32. Классификация методов получения покрытий
133
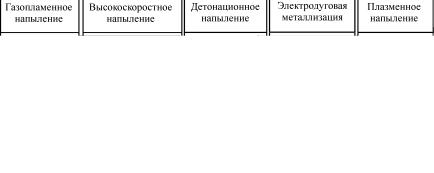
3.4.1. Газотермическое напыление
Под газотермическим напылением (Thermal Spray Coating) понимают совокупность процессов, при которых напыляемый материал расплавляется, диспергируется (распыляется) и переносится на обрабатываемую поверхность посредством газовой струи. При ударе о поверхность частица напыляемого материала мгновенно остывает и деформируется, плотно сцепляясь с ней. Из-за этого газотермические покрытия имеют ленточную или планарную ультрамелкозернистую микроструктуру. Покрытие также может содержать поры, а в случае напыления металлов – частицы их оксидов и нитридов. Классификация методов газотермического напыления в зависимости от источника нагрева приведена на рис. 3.33.
Рис. 3.33. Классификация методов газотермического напыления
Газопламенное напыление. Осуществляется с помощью специальной горелки, в которую вдувается воздух (или кислород) и горючий газ (ацетилен, пропан, водород или др.). В зону горения подается напыляемый материал, который расплавляется пламенем горелки, распыляется и переносится газовой струей на обрабатываемую поверхность. Процессы газопламенного напыления создают покрытия с относительно высокой пористостью (5–12 %) и невысокой адгезией к подложке.
134
Плазменное напыление (Plasma Spraying). При данном способе напыления, источником энергии является электрическая дуга, поджигаемая между двумя электродами. Через область горения дуги продувается инертный газ (как правило, аргон с добавками азота или водорода), который ионизируется и образует плазму. Температура плазмы в области дуги достигает 15 000 °С. В струю плазмы подается порошок напыляемого материала, который расплавляется и переносится на обрабатываемую поверхность. Несмотря на высокие температуры в зоне горения дуги, обрабатываемая поверхность не испытывает сильного нагрева, так как при выходе из области дуги температура резко падает.
Плазменным напылением получают покрытия из никелевых
ижелезных сплавов, карбидов, нитридов, боридов. Чрезвычайно высокая температура плазмы позволяет напылять данным способом огнеупорные керамики, содержащие оксиды алюминия и циркония,
идругие тугоплавкие материалы, не поддающиеся распылению другими способами.
Детонационное напыление (Detonation Gun, D-Gun). Установ-
ка для детонационного напыления напоминает пулемет, стреляющий порциями разогретого порошка. В замкнутую камеру сгорания, к которой прикрепляется ствол, подается смесь кислорода и горючего газа, ствол направляют на напыляемую поверхность. Через загрузочное отверстие в камеру подается порошок. Смесь поджигается электрической искрой и взрывается. Раскаленные частицы вместе с продуктами сгорания вылетают на обрабатываемую поверхность. Температура частиц в момент удара достигает 4000 °С. Частота выстрелов – 3–4 в секунду.
Из-за высокой скорости вылета частиц, покрытия, полученные детонационным напылением, обладают высокой прочностью, твердостью и износостойкостью. Детонационным напылением создают покрытия из металлокерамики: карбидов вольфрама, титана и кобальта, нитридов титана и бора, окиси алюминия.
135
Высокоскоростное напыление (High Velocity Oxygen Fuel– HVOF). Это наиболее современные газотермические методы. Принципиально методы HVOF ничем не отличаются от газопламенных, однако, благодаря особенностям конструкции горелки, в них достигаются очень высокие скорости распыления. В камеру под высоким давлением вдуваются кислород и горючий газ. Строго по оси горелки подается порошок напыляемого материала. Смесь расплавленных частиц порошка и продуктов сгорания газов, проходя через сопло, разгоняется до сверхзвуковой скорости и вылетает в направлении подложки. У систем HVOF первого поколения давление в камере сгорания составляло 0,3–0,5 МПа, скорость вылета частиц достигает
450–1000 м/с.
Покрытия, полученные высокоскоростным методом характеризуются значениями плотности, достигающими 99 % плотности компактного материала, и низким уровнем остаточных напряжений. Поскольку наличие последних является главным фактором, ограничивающим толщину покрытия, HVOF позволяет получать покрытия значительно большей толщины по сравнению с газопламенным напылением. По эксплуатационным характеристикам высокоскоростные покрытия превосходят покрытия, полученные детонационным напылением. В ряде приложений процессы HVOF постепенно вытесняют плазменное напыление.
Ввиду того, что падающие частицы обладают очень большой кинетической энергией, для формирования высококачественных покрытий не требуется их расплавления, что делает данный процесс единственно приемлемым в ряде случаев, например, при напылении металлокерамики.
3.4.2. Физические методы осаждения (PVD)
Ионное распыление. Сущность процесса: распыляемую мишень из наносимого материала располагают на катоде. На другом электроде на расстоянии в несколько сантиметров от катода устанавливают детали (подложки) (рис. 3.34).
136
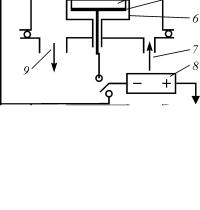
Камеру вакуумируют, а затем |
|
||
наполняют рабочим газом (чаще |
|
||
всего |
аргоном) |
до давления |
|
1,33 Па. На электрод с подложки |
|
||
подают отрицательный потенциал, |
|
||
зажигают газоразрядную плазму и |
|
||
бомбардировкой ионами произво- |
|
||
дят очистку их от поверхностных |
|
||
загрязнений. Далее отрицательный |
|
||
потенциал прикладывают к мише- |
|
||
ни и распыляют ее. Распыляемые |
|
||
частицы |
движутся |
через плазму |
|
разряда, осаждаются на деталях и |
Рис. 3.34. Схема ионного распыле- |
||
образуют покрытие. Большая часть |
ния: 1 – камера; 2 – подложкодер- |
||
энергии ионов, бомбардирующих |
жатель; 3 – детали (подложки); 4 – |
||
мишень (до 25 %), переходит в те- |
мишень; 5 – катод; 6 – экран; 7 – |
||
пло, которое отводится водой, ох- |
подвод рабочего газа; 8 – источник |
||
лаждающей катод. |
|
питания; 9 – откачка |
|
|
|
Широкое применение ионного распыления ограничивают следующие факторы:
•высокий вакуум,
•высокий расход энергии,
•сложность и дороговизна оборудования,
•высокие пересыщения и (в ряде случаев) плохая ростовая морфология,
• ограниченные возможности масштабирования технологии
инепрерывного осуществления процесса,
•послойная сборка (гетеро)структур, структурный дизайн.
Методы вакуумной ионно-плазменной технологии:
1. Модифицирование поверхностных слоев:
•ионно-диффузионное насыщение (ионное азотирование, науглероживание, борирование и др.);
•ионное (плазменное) травление (очистка);
•ионная имплантация (внедрение);
137
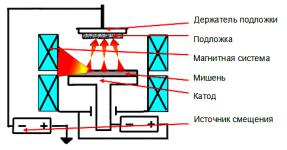
•отжиг в тлеющем разряде. 2. Нанесение покрытий:
•полимеризация в тлеющем разряде;
•ионное осаждение (в триодной распылительной системе, диодной распылительной системе, с использованием разряда в полом катоде);
•электродуговое испарение;
•ионно-кластерный метод;
•катодное распыление (на постоянном токе, высокочастотное);
•химическое осаждение в плазме тлеющего разряда.
Нагрев испаряемого вещества может осуществляться:
•за счет выделения джоулева тепла при прохождении электрического тока через испаряемый материал или через испаритель;
•в результате бомбардировки поверхности металла ускоренным потоком электронов (электронно-лучевой нагрев) или квантами электромагнитного излучения (лазерный нагрев);
•высокочастотным электрическим магнитным полем (индукционный нагрев);
•электрической дугой.
Нанесение дуговых ионно-плазменных покрытий. Сущность метода: при зажигании вакуумной дуги происходит контракция на мишени катода с образованием катодного пятна, из которого выходит пар испаряемого материала, ионизирующийся в электрическом поле вблизи катода (рис. 3.35). Образующаяся при этом плазма
Рис. 3.35. Схема нанесения дуговых ионно-плазменных покрытий
138
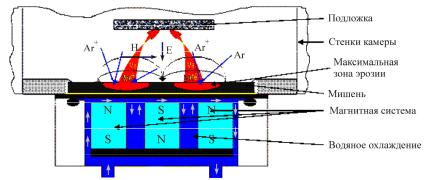
практически полностью ионизирована и состоит из многозарядных ионов и капельной фазы материала мишени, доля которой у легкоплавких металлов составляет ≈10 %, а у тугоплавких металлов ≈1 %.
Магнетронное распыление. Основными элементами магнетрона является катод-мишень, анод и магнитная система. Силовые линии магнитного поля замыкаются между полюсами магнитной системы. Поверхность мишени, расположенная между системами входа и выхода силовых линий магнитного поля, интенсивно распыляется и имеет вид замкнутой дорожки, геометрия которой определяется формой полюсов магнитной системы. При подаче постоянного напряжения между мишенью (отрицательный потенциал) и анодом (положительный потенциал) возникает неоднородное электрическое поле и возбуждается тлеющий разряд. Наличие замкнутого магнитного поля к распыляемой поверхности мишени позволяет локализовать плазму разряда непосредственно у мишени. Эмиттированные с катода под действием ионной бомбардировки электроны захватываются магнитным полем, и им сообщается сложное циклоидальное движение по замкнутым траекториям у поверхностей мишени (рис. 3.36).
Рис. 3.36. Схема магнетронного распыления
Электроны оказываются как бы в ловушке, создаваемой с одной стороны магнитным полем, возвращающим их на катод, а с другой стороны поверхностью мишени, их отталкивающей. Электрон цир-
139
кулирует в этой ловушке до тех пор, пока не произойдет несколько ионизирующих столкновений с атомами рабочего газа, в результате которых он потеряет полученную от электрического поля энергию. Таким образом, большая часть энергии электрона, прежде чем он попадает на анод, используется на ионизацию и возбуждение, что значительно увеличивает эффективность процесса ионизации и приводит к возрастанию концентрации положительных ионов у поверхности мишени. Это, в свою очередь, приводит к увеличению интенсивности ионной бомбардировки мишени и значительному росту скорости осаждения покрытия.
Ионное осаждение покрытий. Осаждаемая пленка подвергается интенсивному воздействию ионного компонента корпускулярного потока, обеспечивающего изменения в структуре и свойствах как переходной зоны, так и самого покрытия. Такой результат возможен либо при высокой степени ионизации корпускулярного потока (газообразного или металлического) осаждаемого вещества, либо при высокой энергии ионного компонента корпускулярного потока.
По типу источника генерации металлического компонента потока различают ионно-термические системы распыления и холодные системы. В первых системах перевод переносимого материала из твердого в парообразное состояние осуществляется в результате термического нагрева, во вторых – в результате распыления с поверхности холодной мишени (катода).
Ионно-диффузионное насыщение. Система ионного насыще-
ния представляет собой вакуумную камеру, в электрическом плане реализующую двухэлектродную схему: катод–электрод с деталями; второй электрод (анод) – заземленный корпус вакуумной камеры. Для проведения процесса ионам насыщения в вакуумную камеру подается легирующий материал (элемент или химическое соединение) в газообразном (парообразном) состоянии, а к деталям прикладывается отрицательный потенциал 300–1000 В. Поверхность детали бомбардируется положительными ионами легирующего элемента из газоразрядной плазмы, что позволяет значительно сократить длительность процесса насыщения поверхности.
140