
книги / Материаловедение и технологии современных и перспективных материалов
..pdfлий заданных форм и размеров с требуемой пористостью и обеспечением равномерного или заданного распределения пористости и соответственно проницаемости.
Статическим прессованием изготавливают пористые материалы простейшей формы в виде диска, конуса, втулки, чечевицы и т.п. Достоинства: высокая точность размеров и большая производительность. Недостатки: неравномерность проницаемости и ограниченность форм и размеров. Для увеличения пористости и облегчения прессования труднопрессуемых порошков к металлическим порошкам добавляют специальные наполнители, удовлетворяющие следующим требованиям: не быть гигроскопичными, не разлагаться при комнатной температуре, не вступать в химическое взаимодействие с металлическим порошком во время смешивания и прессования, разлагаться при температуре меньшей температуры спекания, не оставлять продуктов разложения в порах заготовки после спекания. В качестве наполнителя используют поливиниловый спирт, парафин, двууглекислый аммоний, четыреххлористый аммоний и др. Количество наполнителя обычно составляет 3–10 % от массы металлического порошка.
Гидростатическое или гидродинамическое прессование заключается во всестороннем обжатии жидкостью металлического порошка, заключенного в металлическую оболочку. Этими методами удается получить пористые материалы в виде длинных труб, труб с донышком и фланцем с равномерной пористостью. Обычно давление прессования составляет 100–200 МПа. Достоинства: получение тонкостенных изделий и изделий больших размеров, равномерное распределение пористости. Недостаток – невысокая производительность.
Методом мундштучного прессования изготавливают пористые трубы диаметром до 100 мм и длиной до 1 м с пористостью 50–60 %. Для этой цели подготавливают шликер из порошка на крахмальном клейстере. Суспензию экструдируют под прессом в трубу необходимого диаметра и длины. После сушки трубы спекают в защитной атмосфере. Недостатки метода – необходимость введения пластификатора и ограниченность формы.
161
В промышленности используется метод формования металлических порошков прокаткой. Этот процесс состоит в непрерывном уплотнении порошка между вращающимися валками. По сравнению со статическим прессованием прокаткой можно получить изделия больших размеров по длине и ширине. Кроме того, мощность станов для прокатки меньше мощности прессов, а производительность их выше.
Свободная засыпка порошка в форму – простейший способ формования пористых проницаемых материалов (ППМ) без приложения давления. Для лучшего заполнения форм порошком, устранения «арочного эффекта», а также с целью получения ППМ с равномерной пористостью форму при засыпке подвергают вибрации (вручную или на вибровстряхивателе). Основное требование к материалу формы – отсутствие взаимодействия с материалом порошка при температуре спекания. Для порошков цветных металлов применяют стальные или графитовые формы, а для черных металлов – керамические. Предотвращению припекания частиц порошка к стенкам формы способствует их покрытие подходящей суспензией, например, глинозема с водой и последующей сушке. Теоретически габариты заготовок, сформованных свободной засыпкой порошка в формы, не ограничены – они определены размерами пространства печей спекания.
Шликерным литьем изготовляют пористые детали сложной формы.
Спекание пористых материалов, изготовленных из металлов, сплавов или металлоподобных соединений, осуществляется в вакууме или в защитной атмосфере водорода, диссоциированного аммиака, конвертированного природного газа, эндогаза без расплавления.
Получение волокновых материалов. Технология включает
всебя следующие стадии:
1)изготовление волокна;
2)формование волокон – прокатка, прессование, войлокование (жидкостное, воздушное, вибрационное, в магнитном или электрическом полях) или плетение;
3)спекание.
162
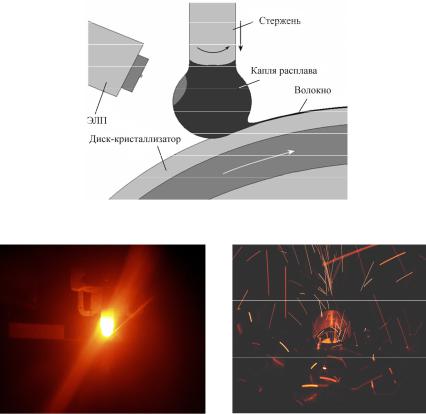
Изготовление волокна. Волокна могут быть получены волочением проволоки, однако для многих малопластичных сплавов и керамики этот вариант неприемлем.
Одной из распространенных технологий получения волокон (как металлических, так и керамических) является экстракция из расплава с помощью вращающегося охлаждаемого диска-кристаллизатора
(рис. 4.8–4.10).
Рис. 4.8. Схема экстракции волокон из расплава
Рис. 4.9. Процесс экстракции во- |
Рис. 4.10. Процесс экстракции из- |
локна Х23Ю5 на установке УПБМ |
нутри волокнопровода установки |
|
УПБМ |
|
163 |
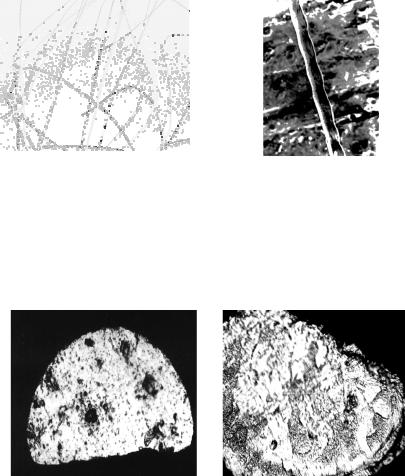
Расплавление металлического стержня производят с помощью электронно-лучевой пушки (ЭЛП) или индукционного нагрева. Минимальный диаметр получаемых таким способом волокон и лент составляет 30 мкм, а длина может быть неограниченной (рис. 4.11).
а |
б |
Рис. 4.11. Внешний вид волокна (а – ×10; б – ×100)
Форма поперечного сечения волокна зависит от адгезионного взаимодействия материалов волокна и диска, угла заточки диска, скорости вращения диска и скорости охлаждения и других параметров (рис. 4.12). Спекание волокновых материалов проводят по тем же режимам, что и для соответствующих порошков.
а |
б |
Рис. 4.12. Форма поперечного среза волокна (а – ×500) и микроструктура (б – ×1500)
164
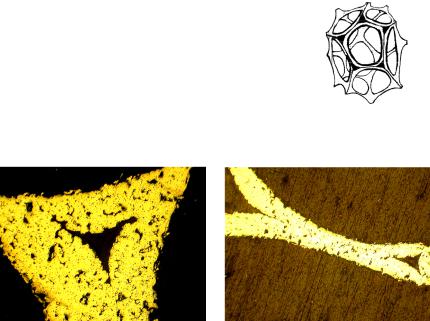
4.1.4. Технология копирования матрицы
Матрицей для получения пористых проницаемых материалов обычно служит пористый пенополиуретан (ППУ). Технология включает в себя следующие стадии:
1)подготовку порошка;
2)подготовку связующего;
3)приготовление шликера;
4)подготовку матрицы (включая придание электропроводно-
сти);
5)нанесение порошка (пропитка шликером или гальваностегия);
6)сушку заготовки;
7)удаление матрицы путем выжигания ППУ;
8)спекание заготовки.
Структура проницаемого ячеистого материала (ВПЯМ) состоит из ячеек, имеющих размеры, соответствующие размерам ППУ
(рис. 4.13).
В структуре различают узлы и перемычки (рис. 4.14), от строения которых зависят прочность и функциональные свойства материала. Вид ВПЯМ показан на рис. 4.15.
Рис. 4.13. Морфология ячеек и ВПЯМ
а |
б |
Рис. 4.14. Микроструктура ВПЯМ: а – узел (×517); б – перемычка (×267)
165
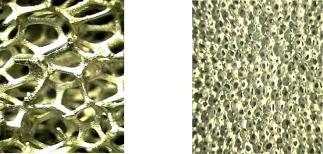
а |
б |
Рис. 4.15. Внешний вид ВПЯМ (пористость П = 96 %):
а– крупноячеистый; б – мелкоячеистый
4.1.5.Производство керамических мембран
Керамические пористые материалы используются как мембраны и фильтры, носители катализаторов, многослойная керамическая мембрана.
В процессе производства керамических пористых материалов следует выделить три стадии:
1)формование порошков;
2)сушка;
3)обжиг.
Формование осуществляют сухим прессованием (воздействие давлением 200–700 атм на порошок, смоченный небольшим количеством масла или воды), шликерным литьем (шликер – суспензия керамики, содержащая до 35 % твердой фазы) и экструзией (керамическая масса продавливается через фильеру с образованием трубок). Керамические мембраны вообще чаще всего формируются в виде трубок (рис. 4.16).
Керамические мембраны обычно состоят из нескольких слоев различной пористости, которые последовательно наносятся на пористую подложку шликерным литьем или с помощью золь-гель технологии, после чего каждый слой подвергается сушке и обжигу
(рис. 4.17).
166
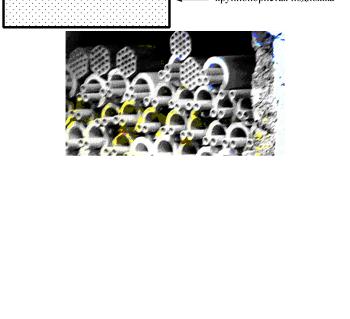
Рис. 4.16. Керамические пористые изделия
Рис. 4.17. Структура керамической мембраны
Мембраны из графита. Существуют два метода получения графитовых мембран:
1)карбонизация (обугливание) полимерных мембран;
2)спекание порошка кокса.
В первом случае готовую мембрану из неплавкого полимера нагревают до 800–1000 °С, полимер обугливается и получается пористая высокоселективная графитовая мембрана низкой механической стойкости (хрупкая).
При втором методе получения графитовых мембран используется смесь порошка кокса и термореактивной смолы, наносящейся на пористую подложку и подвергающейся осаждению в воде и обжигу, в результате чего образуется трехслойная мембрана, состоящая из крупнопористого слоя подложки, среднепористого коксового слоя и мелкопористого селективного слоя из коксосмолы.
167
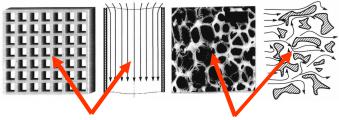
Пористая подложка может быть как графитовой, так и керамической, и в этом случае мембрана композиционная.
Металлокерамические мембраны. Металлокерамические мем-
браны представляют собой плоские или трубчатые мембраны, состоящие из пористой металлической подложки (нержавеющая сталь, титан, различные сплавы) и селективного керамического слоя (SiO2,
TiO2, Al2O3, ZrO2).
Керамический слой наносится шликерным литьем на готовые листы металлической подложки, вода шликера отсасывается через подложку с помощью вакуум-насоса, затем слой прессуется валками и обжигается в печах при температуре до 1000 °С.
По сравнению с керамическими и графитовыми, металлокерамические мембраны обладают значительно большей ударопрочностью.
4.1.6. Катализаторы на носителях ячеистой структуры
Основные виды пористых проницаемых материалов:
1)ячеистые (преимущество – более интенсивный тепло- и массообмен);
2)сотовые (преимущества: меньшие гидравлические потери при высоких скоростях потока; выше стойкость к динамическим нагруз-
кам) (рис. 4.18).
Сотовый материал |
Ячеистый материал |
Рис. 4.18. Структуры пористых материалов и особенности течения газа в поровой структуре
Если нет конструктивных ограничений по площади фильтрации, ячеистые носители однозначно предпочтительнее.
168
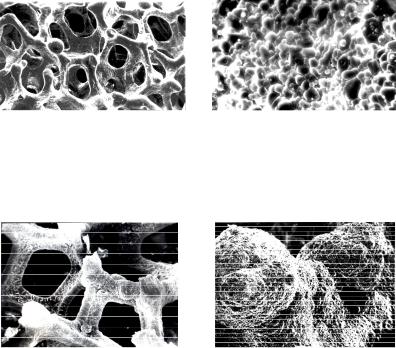
Приготовление ячеистого катализатора включает в себя сле-
дующие стадии:
1)изготовление блочного носителя (проницаемый ячеистый металл или керамика) дублированием структуры ППУ с предварительной пропиткой ППУ керамической суспензией (рис. 4.19) или электрохимическое дублирование ППУ и последующая термодиффузионная обработка (рис. 4.20);
2)нанесение вторичного носителя – γ-Al2O3 (рис. 4.21);
3)нанесение каталитически активного компонента – Pd (про-
питка солью палладия → сушка → прокаливание в среде дисаммиака).
а |
б |
Рис. 4.19. Керамический ВПЯМ на основе муллитокорундовой керамики, кордиерита, полученный дублированием структуры ППУ керамическими суспензиями с центробежным удалением излишков суспензии: а – поровая структура пенокерамического носителя; б – поверхность перемычки пеннокерамического носителя
а |
б |
Рис. 4.20. Металлический ВПЯМ, полученный электрохимическим дублированием ППУи термодиффузионным алитированием: а – поровая структура пенометаллического носителя; б – поверхность перемычки пенометаллического носителя
169
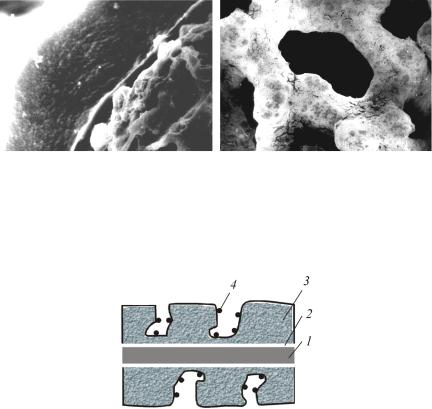
а |
б |
Рис. 4.21. Вторичный слой γ-Al2O3, полученный пропиткой пеноматериала гелем Al2O3 с последующей термообработкой, нанесенный на керамику (а)
и никель (б)
Схематическое изображение ячеистого катализатора показано на рис. 4.22.
Рис. 4.22. Структура пористого материала с нанесенным слоем катализатора: 1 – первичный носитель; 2 – промежуточный слой α-Al2O3; 3 – вторичный носитель γ-Al2O3; 4 – активный компонент
Характеристики катализаторов дожига органических соединений:
•на керамическом носителе (муллитокорундовая керамика): пористость носителя – 85±2 %; удельная поверхность – 7,3 м2/г;
•на металлическом носителе Ni-Al (5 вес.%): пористость носителя – 95±0,2 %; удельная поверхность – 5,3 м2/г.
170