
книги / Материаловедение и технологии современных и перспективных материалов
..pdf4.2.Свойства пористых проницаемых материалов
иметоды определения
Свойства пористых проницаемых материалов (ППМ) разделяют на три большие группы: структурные, функциональные, каркасные.
Структурные свойства ППМ: пористость и ее распределение, размер пор и их распределение, форму пор и степень их извилистости.
Пористость, просвет. Пористостью П называется отношение объема Vп пустот в материале к его полному объему V. Пористость определяют по одной из формул:
П = Vп/V или П = (mн – m)/(γжV),
где mн – масса насыщенного жидкостью материала; γж – плотность жидкости. Если известны объем и масса пористого тела, а также плотность компактного материала, то пористость материала определяют по формуле
П = 1 – γ/γк.
Поры в материалах разделяют на три вида: открытые (пористость По), тупиковые (пористость Пт) и закрытые (пористость Пз). Общая пористость тела слагается из этих трех видов пористости:
П = По + Пз + Пт.
Открытая пора сообщается с поверхностями пористого тела
иучаствует в фильтрации жидкости или газа при наличии градиента давления на пористом теле.
Закрытая пора не сообщается с поверхностью пористого тела
ине участвует в фильтрации жидкости или газа. Часть пор соединяется только с одной поверхностью пористого тела, образуя тупиковую пористость.
Тупиковые (полуоткрытые или полузакрытые) поры при фильтрации частично заполняются жидкостью, но не влияют на проницаемость пористого материала.
Закрытые и тупиковые поры образуются в результате пластической деформации частиц порошка при высоких давлениях прессова-
171
ния, а также из-за наличия внутренней пористости частиц. Доля тупиковой и закрытой пористости при П > 0,18 составляет 2–5 % общей пористости материала. При П < 0,18 эта доля возрастает. При П = 0,07…0,08 открытая пористость практически исчезает. Пористость отдельных участков проницаемого изделия зависит прежде всего от равномерности распределения частиц по размерам в объеме шихты перед формованием и от технологических режимов обработки этих участков при прессовании и спекании.
При одно- и двустороннем прессовании шихты в пресс-формах всегда наблюдают изменение пористости изделий в направлении прессования. Например, втулки, изготовленные этими способами, имеют существенную неравномерность пористости по высоте (до 80 % от средней), при этом увеличение соотношения высоты втулки к диаметру всегда увеличивает неравномерность распределения пористости по высоте.
Распределение пористости в материале можно определить методом микрофотографий, методом измерения расхода газа при его фильтрации через отдельные участки пористой поверхности, разрезкой материала на отдельные элементы с последующим определением пористости каждого из них и другими методами.
Просветом Ф называется доля площади сечения пористого материала, приходящаяся на пустоты. Часто полагают, что пористость и просвет пористого материала численно равны. Основным методом определения величины просвета является исследование шлифов или микрофотографий поверхности материалов. Этот метод часто используют и для определения пористости материалов с анизотропной структурой.
Форма и состояние поверхности пор. Форма пор сложна и зави-
сит от формы и размеров частиц, давления прессования, режимов спекания и т.п. Наиболее простую форму пор имеют пористые материалы из сферических частиц одного размера. Однако даже в случае плотнейшего расположения эта форма достаточно сложна, например, для сфер поперечные сечения порового канала – криволинейные треугольники с переменной площадью по длине канала.
172
В пористых материалах, изготовленных из несферических частиц разного размера, форма пор носит ярко выраженный случайный характер. Поры имеют по всей длине большое число сужений и расширений; на поверхности пор, как правило, встречаются макронеровности в виде выступов и впадин. Поры соединяются с соседними пустотами через сужения в плоскости, непараллельной направлению фильтрации жидкости; направление движения жидкости в порах почти всегда не совпадает с направлением фильтрации жидкости; путь частицы жидкости при фильтрации всегда больше толщины образца вследствие извилистости пор и т.п.
На структуру порового пространства существенно влияют состояние поверхности и форма частиц. Чем сложнее форма частиц и больше число неровностей на поверхности частиц, тем неоднороднее поры спеченного пористого материала.
При спекании порошковых пористых материалов состояние поверхности частиц может измениться в том случае, если интенсивно протекают процессы диффузии и межчастичной собирательной рекристаллизации. Эти процессы интенсивны при повышении температур спекания и использовании мелких частиц при изготовлении материалов. Степень сглаживания шероховатостей на поверхности пор при спекании оценивают по результатам измерения удельной по-
верхности пор прессованных образцов до спекания SудV .н и после спе-
кания SудV .к.
Результаты опытов показывают заметное изменение поверхности пор лишь у мелкозернистых материалов (dч = 10…12 мкм). В остальных случаях уменьшение удельной поверхности пор образцов при спекании не превышает 10–20 %.
Для определения формы и состояния поверхности пор обычно применяют метод исследования микрофотографий, позволяющий получить представление о строении порового пространства и некоторые сведения о шероховатости поверхности пор.
Известен также метод изучения структуры порового пространства наполнением пор жидким веществом. После отвердения этого
173
вещества и удаления основного материала (растворением, травлением и т.п.) остается твердая губка, точно воспроизводящая поровое пространство. Исследуя эту губку, можно определить форму и размеры пор, шероховатость их поверхности и некоторые другие параметры порового пространства.
Коэффициент извилистости пор. Минимальная длина поровых линий в порах всегда равна (или больше) толщине пористого тела в направлении фильтрации среды. Это увеличение длины пор по сравнению с толщиной пористого тела характеризует коэффициент
извилистости пор: аизв = lп/l.
Для тела, образованного сферическими частицами одного диаметра, теоретически показано, что коэффициент извилистости пор меняется от 1,065 до 1,0 при изменении пористости от 0,259 до 0,476. Для насадки сферических частиц одного диаметра коэффициент извилистости пор равен 1,13 при пористости 0,425. Насадки сфер из частиц разного диаметра с отношением dч mах/dч min = 1,8…3,0 при изменении пористости от 0,29 до 0,355 имеют коэффициент извилисто-
сти пор 1,15–1,49.
У реальной пористой среды коэффициент извилистости почти всегда больше, чем у идеальной. Это объясняется дисперсностью порошков, искажением формы частиц по сравнению со сферической и наличием макрошероховатостей на поверхности пор. Уменьшение пористости, усложнение формы и увеличение дисперсности частиц сопровождается ростом коэффициента извилистости (аизв). Обычно значения коэффициента извилистости пор находятся в пределах 1,0– 1,5 при изменении пористости от 0,84 до 0,26. Значениям пористости 0,3–0,4 соответствуют значения коэффициента извилистости пор 1,3– 1,2, соответственно.
Коэффициент извилистости пор определяют либо из геометрических соображений (для пористых структур с относительно несложным строением порового пространства), либо по результатам измерения электрического сопротивления электропроводной жидкости, заполняющей поры неэлектропроводного материала.
174
Размеры пор. Распределение пор по размерам обычно подчинено одному из следующих законов: нормальное распределение или логарифмически нормальное распределение. Распределение пор по размерам используют для определения таких распространенных характеристик, как максимальный и средний размеры пор.
Наиболее распространенные методы определения размеров пор следующие: вдавливание ртути, вытеснение жидкости из пор, исследование микрофотографий.
Метод вдавливания ртути основан на свойстве ртути не смачивать многие твердые тела. Для заполнения объема пор тела ртутью с краевым углом смачивания, превышающим 90°, необходимо внешним давлением преодолеть сопротивление поверхностных сил (сил капиллярного сопротивления). По известному давлению вдавливания ртути в поры р, поверхностному натяжению для ртути σ и краевому углу смачивания θ на границе раздела фаз ртуть – поверхность пор определяют размер пор по следующей формуле, полагая, что они имеют в сечении форму круга: dп = 4σ cos θ /p.
По размеру пор и массе ртути, вошедшей в поры данного размера, определяют их количество. Изменяя давление, можно определить распределение пор по размерам.
Метод вытеснения жидкости из пор, как и метод вдавливания ртути, основан на использовании сил капиллярного взаимодействия. Для определения размеров пор по той же формуле свободный объем пористого образца предварительно заполняют смачивающей жидкостью (спирт, вода и др.), а затем определяют давление газа, необходимое для вытеснения жидкости из пор. Если одновременно учесть расход газа через открывшиеся поры, то можно определить количество пор данного размера. Последовательно увеличивая давление, можно найти распределение пор по размерам.
Удельная поверхность пор. Удельная поверхность пор – это площадь внутренних поверхностей пор в единице объема SудV (м2/м3)
или в единице массы Sудm (м2/г) пористого материала. Величины SудV
175
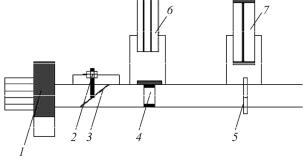
и Sудm связаны соотношением SудV = Sудm γк(1 – П)106, где γк – плот-
ность компактного материала.
Удельную поверхность пор определяют несколькими методами, из которых наибольшее применение нашли: исследование шлифов (микрофотографий) пористого материала; методы, основанные на адсорбции газов; фильтрации газов; ртутная порометрия и др.
Равномерность распределения проницаемости по площади фильтрации материалов определяют различными способами. Простейший способ предусматривает вырезку контрольных образцов из отдельных участков пористого образца и их продувку или проливку при одинаковых перепадах давления (рис. 4.23).
Рис. 4.23. Схема установки для определения проницаемости ВПЯМ: 1 – центробежный вентилятор с электродвигателем; 2 – регулировочный вентиль открытия канала; 3 – регулирующая задвижка; 4 – образец ВПЯМ; 5 – диафрагма измерения скорости; 6 – встроенный дифференциальный микроманометр; 7 – жидкостный компенсационный микроманометр
Основной параметр, характеризующий проницаемость в пористой среде – коэффициент проницаемости k, который вычисляется после измерения перепада давления ∆P (рис. 4.24), в соответствии с законом Дарси:
Q = (k/µ)(∆P/h)S,
где Q – объем жидкости или газа, прошедший через ППМ за единицу времени, м3/с; k – коэффициент проницаемости, м2; ∆P – перепад
176

давления на образце, Па; h – толщина образца, м; S – площадь фильтрации, м2.
Коэффициент проницаемости связан с характеристиками пористой структуры:
k = 3·10–8 (D – 0,112)П2,
где D – диаметр частиц; П – пористость.
Рис. 4.24. Характерная экспериментальная зависимость проницаемости ∆P/(h·V) (Па·с/м2) от скорости подачи воздуха (V, м/с) для ВПЯМ
Зависимость вязкостного коэффициента проницаемости от среднего размера ячеек выражается уравнением (1/α)вязк = 0,39d 2
(рис. 4.25).
Функциональные свойства пористых проницаемых мате-
риалов. Абсолютная тонкость очистки определяется максимальным размером частиц, прошедших через фильтрующий материал.
Номинальная тонкость очистки соответствует такому размеру частиц, которые материал задерживает с эффективностью очистки –
0,95–0,97; медианная тонкость очистки – соответственно с эффек-
тивностью 0,5.
Капиллярный потенциал – потенциальная энергия капиллярных сил, отнесенная к единице массы жидкости.
177
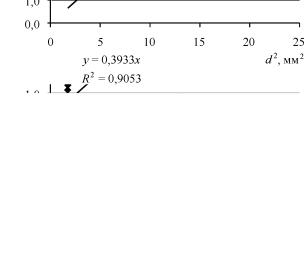
Рис. 4.25. Зависимость вязкостного коэффициента проницаемости от среднего размера ячеек
Грязеемкость фильтра представляет собой массу загрязнений, задержанных на единице площади фильтрующего материала во время повышения давления от начального до предельного.
К каркасным свойствам относятся:
•плотность и ее распределение,
•характеристики межчастичных контактов.
От каркасных свойств зависят свойства проводимости (электро- и теплопроводность), механические свойства (предел прочности, предел текучести, предел упругости, относительное удлинение) и свойства, определяющие коррозионную стойкость материала.
Методом копирования матрицы могут быть изготовлены и керамические материалы. Кроме того, находят широкое применение керамические мембраны.
178
4.3.Применение пористых материалов
4.3.1.Применение пористых проницаемых материалов
Применение проницаемых пористых материалов (ППМ) в соответствии с их функциональными свойствами разнообразно. В авиации для борьбы с обледенением передние кромки крыльев и хвостовое оперение самолетов, подвергающиеся опасности намерзания льда, иногда покрывают медно-никелевым пористым слоем, через сквозные поровые каналы которого циркулирует незамерзающая испаряющаяся жидкость (антифриз).
В настоящее время в связи с развитием техники высоких температур большое внимание уделяют применению ППМ для охлаждения «выпотеванием» (так называемых «потеющих» материалов): к нагретой поверхности «потеющих» деталей через поры в материале поступает охлаждающая жидкость или газ и, испаряясь, понижает температуру поверхности.
Порошковые пористые материалы используют в качестве эффективной преграды распространению пламени, которое гаснет, проходя через узкие капилляры. Такие огнепреградители из порошков нержавеющих сталей, титана и тугоплавких соединений получают прессованием и спеканием и применяют при гашении ацетилено- и водородно-киспородного пламени при газопламенной обработке металлов, в конструкции взрывобезопасных электровыключателей, в резервуарах взрывоопасных жидкостей.
Изделия из пористых материалов могут обеспечивать равномерный подвод газа или жидкости, например, в устройствах, создающих кипящий слой, осуществляющих пневмотранспортирование сыпучих тел, их охлаждение или сушку, смешивание и т.п. Так, в аэрожелобах при подаче сжатого воздуха через пористую пластину с расходом 1,5–3 м3/(м2·мин) осуществляют транспортирование цемента со скоростью 1 м/с; по пористым металлическим желобам транспортируют расплавленное стекло от печи к форме, а сжатый воздух, поступая через поры, препятствует контакту стекла со стенкой желоба.
179
Пористые электроды находят широкое применение в различных электрохимических процессах: суммарная рабочая поверхность электрода складывается из его внешней габаритной поверхности и гро-
мадной |
внутренней поверхности поровых каналов, находящихся |
в объеме |
материала, что улучшает условия протекания процессов |
и во многих случаях позволяет уменьшить расход электроэнергии на их проведение. Из пористого железа, серебра, алюминия, никеля изготовляют электроды аккумуляторов, благодаря чему снижается расход металла, уменьшаются габариты и упрощается производство.
Во время Второй мировой войны в Германии было начато производство ведущих снарядных поясков из пористого железа взамен литых или штампованных из литой меди. Такие пояски, хотя их твердость такая же, как и литых, меньше изнашивают нарезку ствола орудия благодаря наличию смазки в порах спеченного материала. Пояски прессуют из порошка железа при давлении 200–250 МПа и спекают в защитной атмосфере при 1000–1200 °С.
Новой областью использования высокопористых материалов является капиллярный транспорт жидких сред как основа работы тепловых труб.
Область применения пористых металлов в качестве фильтров довольно широка. Ими можно отделять твердые частички, например сажи, от жидкостей или газов.
Вследствие развитой внутренней поверхности в комбинации с хорошей проницаемостью пористый алюминий может использоваться в качестве несущей решетки для катализаторов. Высокая теплопроводность материала имеет значение при сильных экзотермических реакциях, например, при окислении этилена в этиленоксид.
Высокая теплопроводность алюминия предполагает использование пористых конструкций из этого металла с развитой поверхностью для теплообмена между жидкостями, газами или между жидкостью и газом. Фирма Erg Materials & Aerospace (г. Окленд, штат Калифорния, США) производит пористый алюминий, который используется в компактных низкотемпературных теплообменниках для искусственных спутников земли.
180