
книги / Редукторы. Атлас конструкций
.pdf(табл. 9.7) и в чертеже делается запись вида: «Неуказанные предельные отклонения размеров поверхностей: Отверстий +t2, валов –t2, остальных ±t2/2, поверхностей ±t3/2 по ГОСТ 25670-85.
|
|
|
|
|
|
|
Таблица 9.7 |
|
Предельные отклонения свободных размеров (из ГОСТ 25670-83) |
||||||||
|
|
|
|
|
|
|
|
|
Класс точности |
|
|
Интервал размеров, мм |
|
|
|||
|
|
|
|
|
|
|
||
до 3 |
св. 3 до 6 |
св. 6 до 30 |
св. 30 до 120 |
св. 120 до 315 |
св. 315 до 1000 |
|||
|
||||||||
|
|
|
|
|
|
|
|
|
Точный t1 |
0,1 |
0,1 |
0,2 |
0,3 |
|
0,4 |
0,6 |
|
Средний t2 |
0,2 |
0,2 |
0,4 |
0,6 |
|
1,0 |
1,6 |
|
Грубый t3 |
0,3 |
0,4 |
1,0 |
1,6 |
|
2,4 |
4,0 |
|
Очень грубый t4 |
0,3 |
1,0 |
2,0 |
3,0 |
|
4,0 |
6,0 |
Отклонения шпоночных пазов приведены в разделе 4 в табл. 4.1.
9.2. Допуски зубчатых и червячных передач
Для цилиндрических передач по ГОСТ 1643-81 установлено 12 степеней точности, которые обозначают цифрами в порядке убывания точности 1, 2, …, 12. Передачи и зубчатые колеса в редукторах обычно выполняют по 7…9 степеням точности с определенным боковым зазором между зубьями, который зависит от вида сопряжения, обозначаемого буквами A, B, C, D.Сопряжение вида B гарантирует минимальную величину бокового зазора, при котором исключается возможность заклинивания стальной или чугунной передачи от нагрева при разности температур зубчатых колес и корпуса 25°C. В случае нереверсивных передач можно увеличить зазор и назначить вид сопряжения A, в этом случае создаются более благоприятные условия для размещения слоя смазки между зубьями.
Для каждой степени точности зубчатых колес и передач установлены комплексы показателей по трем нормам точности:
1)показатели кинематической точности, которые характеризуют погрешность в угле поворота колеса за его полный оборот, для силовых передач эти показатели не играют существенной роли;
2)показатели плавности работы, которые характеризуют циклические погрешности, многократно повторяющиеся за один оборот колеса (резкие местные изменения отклонения углов поворота колеса), от которых зависят дополнительные динамические нагрузки и шум передач;
91
3) показатели контакта зубьев в передаче, характеризующие размеры пятна контакта по длине и высоте зубьев, от которого зависят значения контактных напряжений в зацеплении, что очень важно для силовых передач.
Стандарт разрешает комбинирование тремя нормам точности, исходя из требований к передаче. Например, обозначение 9-8-7-B показывает, что кинематическая точность соответствует 9-й, точность по плавности работы – 8-й, точность по контакту – 7-й степени, зазор – сопряжению B.
Степениточностиможноназначатьпорекомендациям, даннымвтабл. 9.8 [4].
Таблица 9.8
Степени точности эвольвентных цилиндрических передач редукторов и окружная скорость колес
Окружная скорость колеса, м/с |
Точностьне грубее |
|
|
До 5 |
10 – 9 – 7 – B |
До 8 |
9 – 9 – 7 – B |
До 12,5 |
9 – 8 – 7 – B |
Св. 12,5 |
8 – 7 – 7 – B |
Допуск на диаметр окружностей вершин зубьев зависит от способа контроля зубьев: если контроль толщины зубьев ведется зубомером (штангензубомером), при котором базой для установки зубомера является окружность вершин, то допуск можно назначать по h9, если по длине общей нормали, то по h12, но с допуском не более 0,1 модуля для 7-й степени точности и 0,2 m для 8-й–10-й степени точности.
Предельные отклонения на межосевое расстояние и проставляемые на чертеже корпуса высоты осей валов над опорной плоскостью даны в табл. 9.9 и 9.10.
Таблица 9.9
Допустимые отклонения межосевого расстояния цилиндрических передач
(из ГОСТ 1643-81)
Обозначе- |
|
Отклонение, мкм, при межосевом расстоянии, мм |
|
|||||
|
|
|
|
|
|
|
||
|
св. 80 |
св. 125 |
св. 180 |
св. 250 |
св. 315 |
св. 400 |
||
ние нормы |
до 80 |
|||||||
до 125 |
до 180 |
до 250 |
до 315 |
до 400 |
до 500 |
|||
|
|
|||||||
|
|
|
|
|
|
|
|
|
A |
± 100 |
± 110 |
± 120 |
± 140 |
± 160 |
± 180 |
± 200 |
|
B |
± 60 |
± 70 |
± 80 |
± 90 |
± 100 |
± 110 |
± 120 |
92
Таблица 9.10
Предельные отклонения высоты оси тихоходного вала относительно опорной плоскости корпуса редуктора
Высота оси над |
До 50 |
Св. 50 |
Св. 250 |
Св. 630 |
опорной плоскостью, мм |
|
до 250 |
до 630 |
до 1000 |
|
|
|
|
|
Отклонение, мм |
–0,4 |
–0,5 |
–1,0 |
–1,5 |
Конические зубчатые колеса и передачи выполняются в редукторах по 7-й–10-й степеням точности, изготовление и контроль их значительно сложнее по сравнению с цилиндрическими.
Червячные передачи в учебном проектировании обычно выполняются с архимедовыми червяками ZA c межосевым углом 90°. В редукторах применяют степени точности 7…10. Допуски и предельные отклонения определяются по ГОСТ 3675-81.
В табл. 9.11 даны значения предельных отклонений межосевого расстояния в обработке.
Таблица 9.11
Допустимые отклонения межосевого расстояния червячных передач
(из ГОСТ 3675-81)
Степень |
|
Отклонения, мкм, при межосевом расстоянии, мм |
|
||||
|
|
|
|
|
|
|
|
|
св. 80 |
св. 120 |
св. 180 |
св. 250 |
св. 315 |
св. 400 |
|
точности |
до 80 |
||||||
|
до 120 |
до 180 |
до 250 |
до 315 |
до 400 |
до 500 |
|
7 |
45 |
50 |
60 |
67 |
75 |
80 |
85 |
8 |
71 |
80 |
90 |
105 |
110 |
125 |
130 |
9 |
110 |
130 |
150 |
160 |
180 |
200 |
210 |
10 |
180 |
200 |
220 |
260 |
280 |
300 |
340 |
9.3. Допуски формы и расположения поверхностей
Под отклонением формы понимается отклонение формы реальной поверхности или реального профиля от формы номинальной поверхности или номинального профиля.
Под отклонением расположения понимается отклонение реального расположения рассматриваемого элемента от его номинального расположения. Примером может быть перпендикулярность одной поверхности относительно другой.
Допуск формы или расположения – наибольшее допускаемое значение отклонения формы или расположения.
93
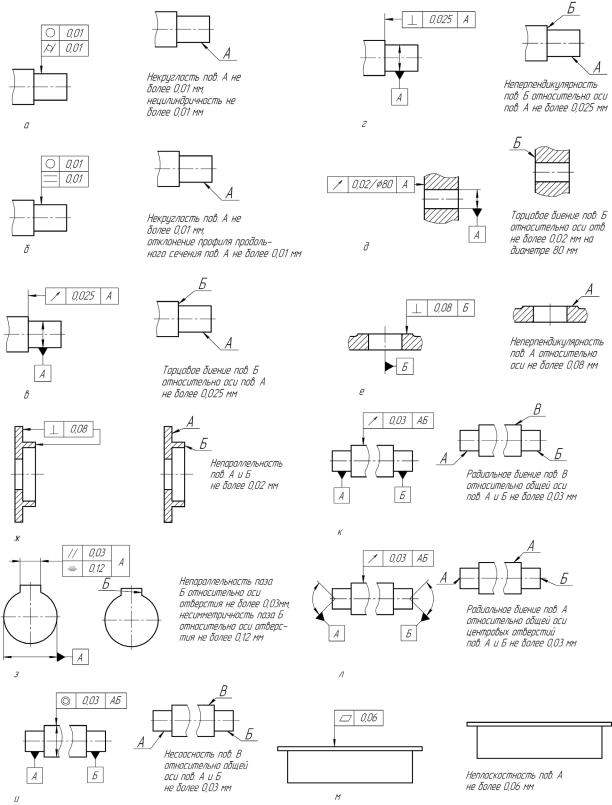
Допуски формы и расположения поверхностей, основные термины и определения, числовые значения, указания на чертежах определяются стандартами:
ГОСТ 24642-81, ГОСТ 24643-81, ГОСТ2.308-79.
Рис. 9.3. Указание на чертежах допусков формы и расположения поверхностей
94
На рис. 9.3 приведены примеры обозначений на чертежах допусков формы
ирасположения в виде условных обозначений и текста, написанного в технических требованиях. На чертежах деталей предпочтительно применение условных обозначений, текстовая запись более удобна в текстовых документах или на чертежах, когда требуется оговорить особые требования к характеру отклонения или условиям базирования.
Допуск формы связан с допуском размера. Поле допуска формы для сопрягаемых поверхностей не может превышать допуск размера (для цилиндриче-
ских поверхностей допуск на диаметр Тd). В зависимости от соотношения между допуском формы и допуском размера различают нормальную (А), повышенную (В), высокую (С) и особо высокую относительную геометрическую точность поверхности, при этом среднее соотношение допусков формы (Тф)
иразмера (Тd) при нормальной точности равно (2Тф/Тd) 100 % = 60 %, при повышенной – 40 %. В соединениях деталей редукторов применяют нормальную относительную геометрическую точность.
Отклонения и допуски формы цилиндрических поверхностей могут опре-
деляться в виде нецилиндричности, некруглости и отклонения профиля продольного сечения. Частными видами отклонений от круглости являются овальность и огранность, отклонениями профиля продольного сечения – конусообразность, бочкообразность и седлообразность.
По ГОСТ 24643-81 допуски цилиндричности (Т/о/), круглости (То), профиля продольного сечения (Т=) при одинаковой степени точности для одного размера являются равными и их можно принимать по соотношению:
Т/о/ = То = Т= ≈ 0,3 Тd,
где Тd – допуск на диаметр поверхности.
Выбор наименования отклонения зависит от выбранных баз и способов контроля, которые определяются метрологическими возможностями изготовителя. Достаточно выбрать два отклонения: некруглости и нецилиндричности (см. рис. 9.3, б) или некруглости и отклонение профиля продольного сечения (рис. 9.3, а), хотя нецилиндричность является более полным показателем по сравнению с отклонением профиля продольного сечения, т.к. измеряется в различных сечениях и направлениях, а последнее – только в одном продольном сечении.
Отклонения от цилиндричности и круглости особенно важны для посадочных мест подшипников качения, так как кольца подшипников сравнительно тонкие детали и при напрессовке частично повторяют неточности формы посадочных поверхностей, что отражается на работе и долговечности подшипников
95
и зубчатых пар. В меньшей мере это влияние проявляется при напрессовке зубчатых колес, так как их ступицы значительно толще колец подшипников, но в случае узких колес неточности формы могут повлиять на положение зубьев относительно оси вращения вала, поэтому нормы точности для посадочных поверхностей зубчатых колес принимаются такими же.
Также на положение подшипников оказывает влияние торцовое биение или неперпендикулярность уступов (заплечиков) валов и корпусов относительно общей оси посадочных поверхностей, непараллельность торцов разделительных втулок, маслоотражательных шайб, крышек и других деталей, в которые упираются торцы колец подшипников, при этом кольца подшипников взаимно перекашиваются, что отрицательно влияет на работу подшипников и зубчатых пар.
Значения торцового биения (неперпендикулярности) уступов (заплечиков) у посадочных мест подшипников (см. рис. 9.3, в, г) даны в табл. 9.12.
Таблица 9.12
Допуски торцового биения ( неперпендикулярности) заплечиков (уступов) валов у посадочных мест подшипников качения класса точности 0
(из ГОСТ 3325-85)
Диаметр посадочного места, мм |
Допуск, мкм, для уступа |
||
|
|
|
|
свыше |
до |
вала |
корпуса |
|
|
|
|
18 |
30 |
21 |
33 |
30 |
50 |
25 |
39 |
50 |
80 |
30 |
46 |
80 |
120 |
35 |
54 |
120 |
180 |
40 |
63 |
На чертеже отклонение от перпендикулярности торцовых поверхностей деталей вращения может задаваться двумя способами – в виде торцового биения (см. рис. 9.3, в) или неперпендикулярности (см. рис. 9.3, г).
Допуски на торцовое биение поверхностей или неперпендикулярность корпусов, стаканов (см. рис. 9.3, д, е), к которым приставляются крышки, упирающиеся в подшипники или торцы других деталей, например, шестерен, в которые тоже упираются подшипники, также могут определяться по табл. 9.11.
Непараллельность опорных торцев крышек (см. рис. 9.3, ж), приставляемых к корпусу и к подшипникам, торцов разделительных втулок, маслоотражательных шайб, стопорных шайб, пружинных колец, фиксирующих положение подшипников, может определяться по табл. 9.13.
96
|
|
|
|
|
|
|
Таблица 9.13 |
|
Допуски параллельности торцов деталей, мкм (по ГОСТ 24643-81) |
||||||||
|
|
|
|
|
|
|
|
|
|
|
|
|
|
Степени точности |
|
|
|
Номинальный |
|
|
допусков параллельности |
|||||
|
|
|
|
|
|
|
||
размер, мм |
6 |
7 |
|
8 |
9 |
|
10 |
|
|
|
|
|
|
|
|
|
|
|
|
|
|
Допуски параллельности |
|
|
||
|
|
|
|
|
|
|||
До 10 |
4 |
6 |
|
10 |
16 |
|
25 |
|
Св. 10 |
до 16 |
5 |
8 |
|
12 |
20 |
|
30 |
Св. 16 |
до 25 |
6 |
10 |
|
16 |
25 |
|
40 |
Св. 25 |
до 40 |
8 |
12 |
|
20 |
30 |
|
50 |
Св. 40 |
до 63 |
10 |
16 |
|
25 |
40 |
|
60 |
Св. 63 до 100 |
12 |
20 |
|
30 |
50 |
|
80 |
|
Св. 100 |
до 160 |
16 |
25 |
|
40 |
60 |
|
100 |
Св. 160 |
до 250 |
20 |
30 |
|
50 |
80 |
|
120 |
Св. 250 |
до 400 |
25 |
40 |
|
60 |
100 |
|
160 |
Примечания:
1.Выбор допуска при данной степени точности производится по длине нормируемой поверхности (если допуск относится ко всей длине) или длине нормируемого участка.
2.По данной таблице назначаются также суммарные допуски непараллельности, неплоскостности и неперпендикулярности.
Допуск параллельности торцов деталей по табл. 9.12 принимается по 7-й или 8-й степени точности при применении подшипников класса точности 0 и 9-й–10-й степени точности применяются в больших редукторах тяжелого машиностроения.
На рабочих чертежах зубчатых колес указывают:
1.Биение базового торца зубчатого венца заготовки, на который её устанавливают на столе зуборезного станка (см. табл. 9.14).
2.Радиальное биение поверхности вершин зубьев, являющейся наружной поверхностью заготовки при использовании её в качестве базы для выверки установки зубчатого колеса на столе зуборезного станка (табл. 9.14).
3.Для шпоночной канавки на валу и паза в отверстии ступицы назначают допуск параллельности относительно оси отверстия, вала, равный половине допуска на ширину паза, и допуск симметричности паза в четыре раза больший допуска параллельности паза (рис. 9.3, з).
4.При коротких ступицах также указывают допуски торцового биения ступицы и уступа вала, в который упирается колесо (табл. 9.16); в случае, если торец ступицы является базой для установки заготовки на стол зуборезного станка, то это биение не должно быть больше указанного в табл. 9.14, 9.15.
97
Таблица 9.14
Допуски торцового биения базового торца зубчатого венца заготовки с m ≥ 1 мм [8]
Степень |
Допуск, мкм, при ширине зубчатого венца или полушеврона, мм |
|||||
точности |
|
|
|
|
|
|
до 40 |
св. 40 до 100 |
св. 100 до 160 |
св. 160 до 250 |
св.250 до 400 |
||
по контакту |
||||||
|
|
|
|
|
||
|
|
|
|
|
|
|
7 |
24 |
12 |
8 |
6 |
4,5 |
|
8 |
40 |
20 |
12,8 |
10 |
7,1 |
|
9 |
64 |
32 |
20 |
16 |
12 |
Примечание: значения допусков приведены при делительном диаметре d = 100 мм, при d ≠ 100 мм табличные значения допуска умножают на величину d /100.
Таблица 9.15
Допуски радиального биения поверхности вершин зубьев (наружной поверхности заготовки)
Степень |
|
Делительный диаметр d, мм |
|||
Модуль m, мм |
|
|
|
||
до 125 |
св. 125 до 400 |
св. 400 до 800 |
|||
точности |
|||||
|
|
|
|
||
|
|
|
Допуск Fda, мкм |
|
|
|
От 1 до 3,5 |
36 |
50 |
63 |
|
7 |
Св.3,5 до 6,3 |
40 |
56 |
71 |
|
|
Св.6,3 до 10 |
45 |
63 |
80 |
|
|
От 1 до 3,5 |
45 |
63 |
80 |
|
8 |
Св. 3,5 до 6,3 |
50 |
71 |
90 |
|
|
Св. 6,3 до 10 |
56 |
80 |
100 |
|
|
От 1 до 3,5 |
71 |
80 |
100 |
|
9 |
Св. 3,5 до 6,3 |
80 |
100 |
112 |
|
|
Св. 6,3 до 10 |
90 |
112 |
125 |
Примечание: допуск на радиальное биение должен быть не более 0,5 допуска на диаметр заготовки.
Таблица 9.16 Допуски торцового биения ступицы зубчатого колеса, бурта или уступа вала
Степень кинематической точности |
Допуск, мкм, при диаметре вала d, мм |
|||
|
|
|
||
до 55 |
св. 55 до 80 |
св. 80 |
||
|
||||
|
|
|
|
|
7 |
20 |
30 |
40 |
|
8,9 |
30 |
40 |
50 |
Примечание: данные приведены при длине ступицы l ≤ d, при длине ступицы l > d допуск увеличивается в 1,5 раза.
98
Для ограничения перекосов колец подшипников, обеспечения кинематической точности и норм контакта зубчатых и червячных передач важное значение имеет соосность или биение (рис. 9.3, и, к) посадочных поверхностей под подшипники и зубчатыt колеса. На практике контроль соосности осуществляется часто через биения по отношению к оси центров вала (рис. 9.3, л), что позволяет осуществить контроль непосредственно на станке при установке вала в центрах. Имеется определенная взаимозависимость между некруглостью и радиальным биением.
Допуск на радиальное биение ТÊ посадочных поверхностей валов можно принимать приближенно по соотношению:
ТÊ ≈ 2,5 То,
где То – допуск на некруглость.
Для корпусных деталей редуктора назначают допуски [1]:
−плоскостности базовых поверхностей (рис. 9.3, м) до 0,15/300 мм/мм – для плоскости основания и от 0,02/300 до 0,03/300 мм/мм – для плоскости разъёма; при длине контролируемой плоскости L указанные значения нужно умножить на L/300;
−параллельности и перекоса осей. Параллельность контролируется в плоскости передачи, а перекос – перпендикулярно к ней.
Обе величины указывают на чертеже на длине, равной расстоянию между торцами подшипниковых гнезд. Допуски параллельности приведены в табл. 9.17, а допуск перекоса принимается вдвое меньше, чем параллельности.
Таблица 9.17
Допуски параллельности рабочих осей зубчатых колес на рабочей ширине зубчатого венца или полушеврона ( из ГОСТ 1643-81)
Степень точности |
|
Допуск, мкм, при ширине зубчатого |
|
|||
|
венца или полушеврона, мм |
|
||||
по контакту |
|
|
||||
|
|
|
|
|
||
до 40 |
св.40 до 100 |
св. 100 до 160 |
св. 160 до 250 |
св. 250 до 400 |
||
|
||||||
|
|
|
|
|
|
|
7 |
11 |
16 |
20 |
25 |
28 |
|
8 |
18 |
25 |
32 |
40 |
45 |
|
9 |
28 |
40 |
50 |
63 |
71 |
Примечание: для подсчета допуска параллельности на расстоянии L между торцами подшипниковых гнезд следует табличное значение умножить на отношение L/b, где b – рабочая ширина зубчатого венца или полушеврона.
99
10. ШЕРОХОВАТОСТЬ ПОВЕРХНОСТЕЙ
Под шероховатостью поверхностей понимается совокупность микронеровностей с относительно малыми шагами. Шероховатость поверхности играет большую роль в подвижных соединениях деталей, в значительной степени влияя на трение и износ трущихся поверхностей подшипников и зубчатых пар. В неподвижных соединениях величина зазора или натяга также зависит от шероховатости поверхностей. Уменьшение шероховатости способствует увеличению прочности деталей, особенно при переменных нагрузках, уменьшая концентрацию напряжений, и улучшает антикоррозийную стойкость деталей. Шероховатость поверхности влияет на точность измерения деталей.
Параметры и характеристики шероховатости поверхности установлены
вГОСТ 2789-73 и ГОСТ 9378-93, по которому определены 14 классов шероховатости, каждому из которых соответствуют параметры шероховатости Ra или
Rz (табл. 10.1). Ra – среднее арифметическое отклонение профиля, определяемое как среднее арифметическое абсолютных значений отклонений профиля
впределах базовой длины; Rz – высота неровностей профиля по десяти точкам, определяемая как сумма средних арифметических абсолютных отклонений точек пяти наибольших максимумов и пяти наибольших минимумов профиля, находящихся в пределах базовой длины.
Детали редукторов обрабатываются с шероховатостью, на практике обычно называемой чистотой обработки, по 4-му–9-му классу. В табл. 10.2 [1] приведены рекомендации по назначению шероховатости деталей редукторов, подвергающихся механической обработке и ковке. В табл. 10.3 приведены значения шероховатостей поверхности при различных видах механической обработки [4].
Ограничения шероховатости в некоторой мере связаны с допуском размера и формы нормируемой поверхности, но однозначной связи между этими параметрами нет, так при относительно низких требованиях к точности размера шейки вала под уплотнительную резиновую манжету чистота ее обработки весьма значительная, – 8-й–9-й класс шероховатости. Табл. 10.2 составлена на основании данных практики о соответствии шероховатости и точности обработки как с эксплуатационной, так и с экономической точки зрения. Шероховатость на чертеже обозначают согласно ГОСТ 2309-73, см. примеры выполнения рабочих чертежей в атласе.
100