
книги / Редукторы. Атлас конструкций
.pdf
|
|
|
|
Таблица 10.1 |
|
|
Классы шероховатости поверхности |
|
|||
|
|
|
|
||
Классы шероховатости |
Параметры шероховатости, мкм |
Базовая длина l, |
|||
поверхности |
Ra |
Rz |
мм |
||
|
|
|
|
||
1 |
– |
От 320 до 160 |
|
||
2 |
– |
“ 160 “ 80 |
8,0 |
||
3 |
– |
“ 80 “ 40 |
|
||
4 |
– |
От 40 до 20 |
2,5 |
||
5 |
– |
“ 20 “ 10 |
|||
|
|||||
|
От 2,5 до 2,0 |
|
|
||
6 |
“ 2,0 до 1,6 |
|
0,8 |
||
|
“ 1,6 до 1,25 |
|
|
||
|
От 1,25 до 1,00 |
|
|
||
7 |
“ 1,00 |
“ 0,80 |
|
|
|
|
“ 0,80 |
“ 0,63 |
|
|
|
|
От 0,63 до 0,50 |
|
|
||
8 |
“ 0,50 |
“ 0,40 |
– |
|
|
|
“ 0,40 |
“ 0,32 |
|
|
|
|
От 0,32 до 0,25 |
|
|
||
9 |
“ 0,25 |
“ 0,20 |
|
|
|
|
“ 0,20 |
“ 0,16 |
|
|
|
|
От 0,160 до 0,125 |
|
|
||
10 |
“ 0,125 |
“ 0,100 |
|
0,25 |
|
|
“ 0,100 |
“ 0,080 |
|
|
|
|
От 0,080 до 0,063 |
|
|
||
11 |
“ 0,063 |
“ 0,050 |
|
|
|
|
“ 0,050 |
“ 0,040 |
|
|
|
|
От 0,040 до 0,032 |
|
|
||
12 |
“ 0,032 |
“ 0,025 |
|
|
|
|
“ 0,025 |
“ 0,020 |
|
|
|
|
– |
От 0,100 до 0,080 |
|
||
13 |
– |
“ 0,080 “ 0,063 |
0,08 |
||
|
– |
“ 0,063 “ 0,050 |
|
||
|
– |
От 0,050 до 0,040 |
|
||
14 |
– |
“ 0,040 “ 0,032 |
|
||
|
– |
“ 0,032 “ 0,025 |
|
101
Таблица 10.2
Шероховатость поверхностей деталей редукторов
Детали, поверхности |
Класс шерохо- |
Rz, мкм, |
Rа, мкм, |
|
ватости |
не более |
не более |
||
|
||||
|
|
|
|
|
1 |
2 |
3 |
4 |
|
Зубчатые и червячные передачи |
|
|
||
Поверхность зуба боковая : |
|
|
|
|
|
|
|
||
шестерни при модуле до 5 мм |
7 |
– |
1,25 |
|
свыше 5 мм |
6 |
– |
2,5 |
|
колеса при модуле до 5 мм |
6 |
– |
2,5 |
|
свыше 5 мм |
5 |
20 |
– |
|
Поверхность витка червяка боковая: |
|
|
|
|
червяк цилиндрический |
8 |
– |
0,63 |
|
“ глобоидный |
7 |
– |
1,25 |
|
Поверхность вершин: |
|
|
|
|
при контроле длины общей нормали |
5 |
20 |
– |
|
“ толщины зуба по хорде |
6 |
– |
2,5 |
|
Поверхность впадин |
5 |
20 |
– |
|
Расточка ступицы |
6 |
– |
2,5 |
|
Торец ступицы |
6 |
– |
2,5 |
|
Торец обода |
|
|
|
|
при диаметре колеса до 500 мм |
6 |
– |
2,5 |
|
“ свыше 500 мм |
5 |
20 |
– |
|
Грань боковая шпоночного паза |
5 |
20 |
– |
|
Дно шпоночного паза |
4 |
40 |
– |
|
Поверхности нерабочие в кованом колесе: |
|
|
|
|
диск, обод изнутри, ступица снаружи |
3 |
80 |
– |
|
Валы |
|
|
|
|
Поверхность неподвижного сопряжения – посадоч- |
|
|
|
|
|
|
|
||
ного места под внутреннее кольцо подшипника каче- |
|
|
|
|
ния, под зубчатое колесо, |
|
|
|
|
под муфту: |
|
|
|
|
при d ≤ 80 мм |
7 |
– |
1,25 |
|
при d > 80 мм |
6 |
– |
2,5 |
|
Переход галтельный, торец заплечика |
6 |
– |
2,5 |
|
Шейка, трущаяся по резиновой манжете |
|
|
|
|
при скорости скольжения до 1 м/с |
8 |
– |
0,63 |
|
“ до 10 м/с |
9 |
– |
0,32 |
|
|
|
|
|
|
102 |
|
|
|
Окончание табл.10.2
1 |
|
|
2 |
3 |
|
4 |
|
Резьба крепежная на валу |
|
|
5 |
20 |
|
– |
|
Грань боковая шпоночного паза |
|
|
5 |
20 |
|
– |
|
Дно шпоночного паза |
|
|
4 |
40 |
|
– |
|
Кольцо дистанционное на валу |
|
|
|
|
|||
Поверхность внутренняя |
|
|
5 |
|
20 |
|
– |
|
|
|
|||||
Поверхность наружная |
|
|
3 |
|
80 |
|
– |
Торец |
|
|
6 |
|
– |
|
2,5 |
Корпусные детали |
|
|
|
|
|
||
Расточка гнезда под подшипник качения: |
|
|
7 |
|
– |
|
1,25 |
|
|
|
|||||
при D ≤ 80 мм |
|
|
|
|
|||
при D > 80 мм |
|
|
6 |
|
– |
|
2,5 |
Торец гнезда для подшипника качения |
|
|
5 |
|
20 |
|
– |
Поверхности стыка корпуса и крышки |
|
|
6 |
|
– |
|
2,5 |
Опорная поверхность подошвы |
|
|
3 |
|
80 |
|
– |
Отверстие, сверленное под болт |
|
|
3 |
|
80 |
|
– |
Отверстие, нарезанное под болт |
|
|
4 |
|
40 |
|
– |
Поверхность под крышку люка |
|
|
4 |
|
40 |
|
– |
Поверхность, обработанная под гайку, головку болта |
|
|
4 |
|
40 |
|
– |
Крышки подшипниковых гнезд |
|
|
|
|
|||
Цилиндрическая поверхность крышки, сопрягаемая |
|
|
5 |
|
20 |
|
– |
|
|
|
|||||
с расточкой гнезда |
|
|
|
|
|
|
|
Торец крышки, сопрягаемый с торцом наружного |
|
|
6 |
|
– |
|
2,5 |
кольца подшипника качения |
|
|
|
|
|
|
|
Плоская поверхность фланца, сопрягаемая с торцом |
|
|
5 |
|
20 |
|
– |
гнезда через прокладки регулировочные |
|
|
|
|
|
|
|
|
|
|
|
|
|
|
|
Значения параметров шероховатости для боковых поверхностей зубьев, приведенные в табл. 10.2, относятся к эвольвентным передачам. Допускается увеличение шероховатости на один класс при модуле до 5 мм для эвольвентных шестерен, если диаметр впадин меньше диаметра шеек, расположенных рядом. В большинстве передач Новикова также допускается шероховатость на один класс грубее, чем указано в табл. 10.2 (подробности см. ГОСТ 16162-78).
103
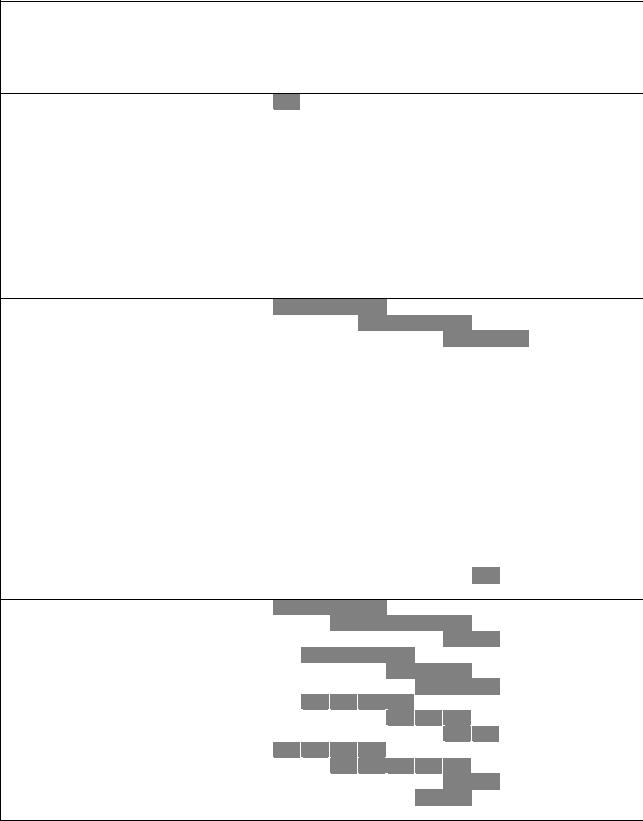
Обрабатываемые |
поверхности |
Наружные цилиндрические |
Внутренние цилиндрические
Плоскости
Таблица 11.3 Шероховатость поверхностей при механических методах обработки
|
|
|
|
|
|
Параметры шероховатости |
|
|
|
|
|||||
|
|
|
|
|
|
|
|
|
|
|
|
|
|
|
|
Методы обработки |
|
|
Rz |
|
|
|
|
|
Ra |
|
|
|
Rz |
||
|
|
|
|
|
|
|
|
|
|
|
|
|
|||
320 |
160 |
80 |
40 |
20 |
2,5 |
1,25 |
0,63 |
0,32 |
0,160 |
0,080 |
0,040 |
0,100 |
|||
|
|
||||||||||||||
|
|
|
|
|
|
|
|
|
|
|
|
|
|
|
|
|
|
|
|
|
|
|
|
|
|
|
|
|
|
|
|
|
|
|
|
|
|
|
|
|
|
|
|
|
|
|
|
|
|
|
|
|
|
|
|
|
|
|
|
|
|
|
|
|
|
|
|
|
|
|
|
|
|
|
|
|
|
|
|
|
|
|
|
|
|
|
|
|
|
|
|
|
|
|
|
|
|
|
|
|
|
|
|
|
|
|
|
|
|
|
|
|
|
|
|
|
|
|
|
|
|
|
|
|
|
|
|
|
|
|
|
|
|
|
|
|
|
|
|
|
|
|
|
|
|
|
|
|
|
|
|
|
|
|
|
|
|
|
|
|
|
|
|
|
|
|
|
|
|
|
|
|
|
|
|
|
|
|
|
|
|
|
|
|
|
|
|
|
|
|
|
|
|
|
|
|
|
|
|
|
|
|
|
|
|
|
|
|
|
|
|
|
|
|
|
|
|
|
|
|
|
|
|
|
|
|
|
|
|
|
|
|
|
|
|
|
|
|
|
|
|
|
|
|
|
|
|
|
|
|
|
|
|
|
|
|
|
|
|
|
|
|
|
|
|
|
|
|
|
|
|
|
|
|
|
|
|
|
|
|
|
|
|
|
|
|
|
|
|
|
|
|
|
|
|
|
|
|
|
|
|
|
|
|
|
|
|
|
|
|
|
|
|
|
|
|
|
|
|
|
|
|
|
|
|
|
|
|
|
|
|
|
|
|
|
|
|
|
|
|
|
|
|
|
|
|
|
|
|
|
|
|
|
|
|
|
|
|
|
|
|
|
|
|
|
|
|
|
|
|
|
|
|
|
|
|
|
|
|
|
|
|
|
|
|
|
|
|
|
|
|
|
|
|
|
|
|
|
|
|
|
|
|
|
|
|
|
|
|
|
|
|
|
|
|
|
|
|
|
|
|
|
|
|
|
|
|
|
|
|
|
|
|
|
|
|
|
|
|
|
|
|
|
|
|
|
|
|
|
|
|
|
|
|
|
|
|
|
|
|
|
|
|
|
|
|
|
|
|
|
|
|
|
|
|
|
|
|
|
|
|
|
|
|
|
|
|
|
|
|
|
|
|
|
|
|
|
|
|
|
|
|
|
|
|
|
|
|
|
|
|
|
|
|
|
|
|
|
|
|
|
|
|
|
|
|
|
|
|
|
|
|
|
|
|
|
|
|
|
|
|
|
|
|
|
|
|
|
|
|
|
|
|
|
|
|
|
|
|
|
|
|
|
|
|
|
|
|
|
|
|
|
|
|
|
|
|
|
|
|
|
|
|
|
|
|
|
|
|
|
|
|
|
|
|
|
|
|
|
|
|
|
|
|
|
|
|
|
|
|
|
|
|
|
|
|
|
|
|
|
|
|
|
|
|
|
|
|
|
|
|
|
|
|
|
|
|
|
|
|
|
|
|
|
|
|
|
|
|
|
|
|
|
|
|
|
|
|
|
|
|
|
|
|
|
|
|
|
|
|
|
|
|
|
|
|
|
|
|
|
|
|
|
|
|
|
|
|
|
|
|
|
|
|
|
|
|
|
|
|
|
|
|
|
|
|
|
|
|
|
|
|
|
|
|
|
|
|
*предварительное
104
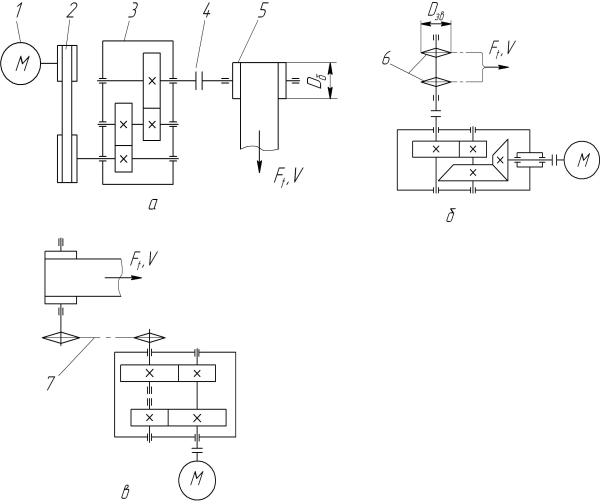
11.АЛГОРИТМ ВЫПОЛНЕНИЯ ПРОЕКТА РЕДУКТОРА
Вбольшинстве случаев курсовой проект по деталям машин дается в виде схемы электромеханического привода к конвейеру, транспортеру, механизму подъема груза крана и других машин, в которых редуктор является передаточным механизмом (рис. 11.1).
Рис. 11.1. Типичные схемы электромеханического привода: а, в – к ленточному конвейеру и транспортеру; б – к цепному конвейеру; 1 – электродвигатель; 2 – ременная передача;
3 – редуктор; 4 – муфта; 5 – барабан; 6 – приводные звездочки конвейера; 7 – цепь;
Ft – окружное усилие на барабане; V – скорость ленты, цепи
Возможны и другие схемы приводов в виде сочетаний зубчатых, червячных и винтовых механизмов. Во всех случаях выполнение проекта рекомендуется начать с изучения схемы привода и нахождения прототипа редуктора в атласе или в другом источнике. До расчета редуктора необходимо определить крутящий момент и число оборотов на его выходном валу, передаточное число редуктора, что выполняется на основании заданной схемы привода.
105
Рекомендуется следующий порядок работы над проектом редуктора:
1.Определение передаточного отношения редуктора и его отдельных ступеней, угловых скоростей и крутящих моментов на валах.
2.Выбор материала и термообработки зубчатых колес и червяков, определение допускаемых контактных и изгибных напряжений для зубьев.
3.Расчет зубчатых или червячных передач: определение размеров и выполнение проверочных расчетов деталей передач на прочность.
4.Разработка эскизного проекта редуктора.
4.1.Вычерчивание в масштабе 1:1 первой компоновки редуктора с определением расстояний между деталями редуктора.
4.2.Определение предварительных диаметров валов.
4.3.Выбор типоразмеров подшипников.
4.4.Вычерчивание редуктора с расположением зубчатых и червячных передач и подшипников на валах, разработка конструкций зубчатых колес, червяков (вторая эскизная компоновка).
4.5.Определение реакций в опорах и долговечности подшипников, конструирование подшипниковых узлов.
4.6.Отработка конструкций валов, определение размеров шпонок, выбор
посадок.
4.7.Выполнение проверочных расчетов валов на прочность с построением эпюр изгибающих и крутящих моментов.
4.8.Выбор системы смазки передач и подшипников, сорта масла, уплотнительных устройств.
4.9.Конструирование крышек, стаканов, корпусных деталей.
5.Выполнение чертежа редуктора на ватмане и спецификации.
6.Выполнение рабочих чертежей деталей.
7.Оформление расчетно-пояснительной записки.
Типичной ошибкой молодых проектантов является стремление вначале все рассчитать, а затем чертить. Этот процесс должен идти параллельно. После определения размеров зубчатых колес следует выполнить первую эскизную компоновку, которая заключается в размещении зубчатых колес и очерчивании внутреннего контура корпуса редуктора (рис. 11.2).
Ширина шестерни обычно выполняется больше ширины колеса на 3…5 мм для редукторов средних размеров (вычерчиваемых на формате А1 в масштабе 1:1). С целью компенсации погрешностей изготовления корпуса и деталей в осевом направлении расстояние b от зубчатых колес до стенок корпуса редуктора рекомендуется принимать a2 = 5…10 мм, расстояние между зубчатыми колесами с≈3…5 мм, в передаче с коническими колесами величину a2 также первоначально можно принимать такой же. В разделе 8 приведены эмпириче-
106
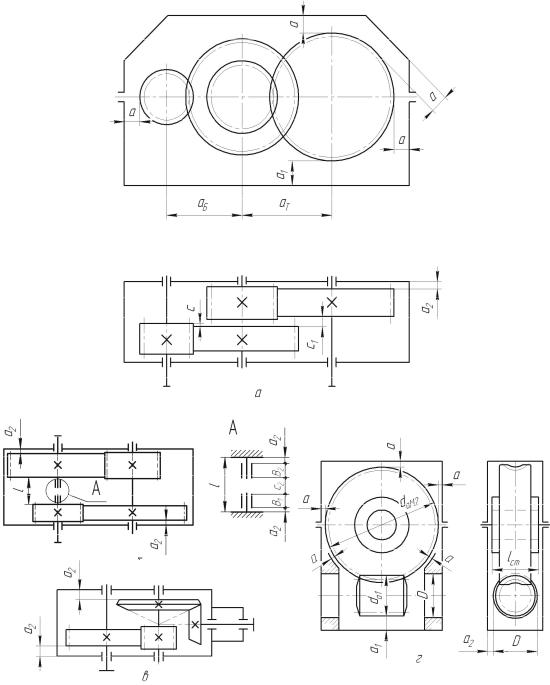
ские формулы для определения указанных значений в зависимости от толщины стенки корпуса. Следует особо отметить, что данные рекомендации являются ориентировочными, они могут изменяться в процессе дальнейшей работы над чертежом. Расстояние от зубчатых колес до стенок корпуса редуктора прежде всего зависит от технологии выполнения корпуса и точности его изготовления, которая на начальной стадии проектирования не берется во внимание.
Рис. 11.2. Первая эскизная компоновка: а – цилиндрический двухступенчатый редуктор
сразвернутой схемой; б – цилиндрический двухступенчатый соосный редуктор;
в– коническо-цилиндрический редуктор; г – червячный редуктор
107
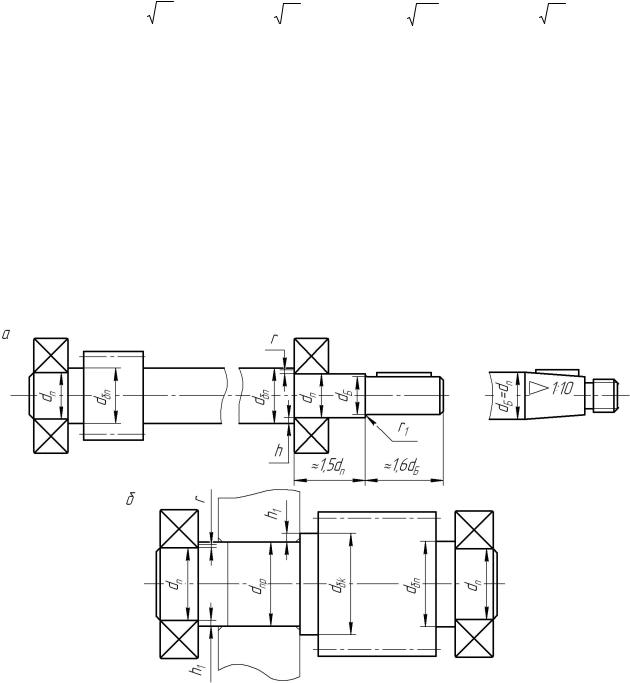
Первая компоновка дает общее представление о габаритах редуктора, размещении зубчатых колес и позволяет зрительно определить пропорции между ними, т.е уже на начальном этапе оценивается гармоничность конструкции. Затем по значениям крутящих моментов на валах, исходя из пониженных допускаемых напряжений кручения, определяют диаметры валов по формулам:
dБ ≥ (5…6) 3 TБ ; dБ ≥ (7…8) 3 TБ ; dпр ≥ (6…7) 3 Tпр ; dТ ≥ (5…6) 3 TТ ,
где dБ, dпр, dТ, ТБ, Тпр, ТТ – диаметры (мм) и крутящие моменты (Нм) быстроходного (входного), промежуточного и тихоходного (выходного) валов соответст-
венно; формула dБ используется при изготовлении вала из легированной стали. Для быстроходного и тихоходного валов это диаметры выходных концов,
для промежуточного вала это диаметры под зубчатыми колесами.
Исходя из технологических соображений и условий сборки валы обычно выполняют ступенчатыми. На рис. 11.3 приведены изображения типичных конструкций валов и ориентировочные формулы для определения диаметров ступеней. Как следует из рисунка, диаметр под внутреннее кольцо подшипника определяется конструкцией вала. Но возможны случаи, что выявляется только после расчета подшипников, когда диаметр вала приходится увеличивать, чтобы взять подшипник с большей грузоподъемностью.
108
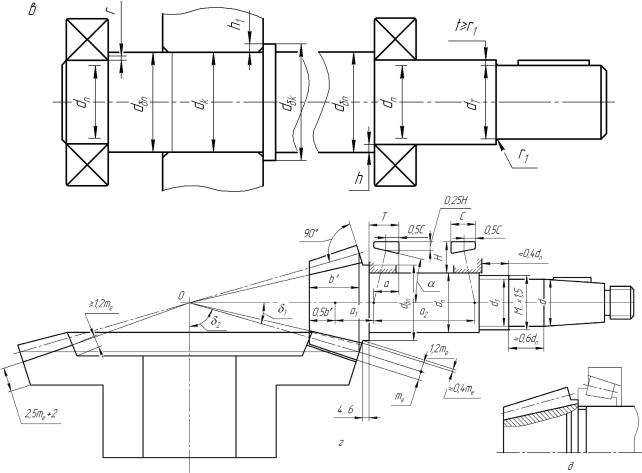
Рис. 11.3. Основные размеры элементов валов: а – входной (быстроходный) вал: dn≥dБ+2t; dбп=dп+2h; б – промежуточный вал: dп≤dпр-2h; dбп=dп+2h; dбк= dпр+2h1; в – выходной (тихоходный) вал: dп≥dт+2t; dп=d (при коническом конце вала); dбк=dк+2h1; dк≥dбп;
г– входной вал конической передачи: d1≥d; dп≥M; dбп=dп+2h; a2=(2...2,5)a1
д– конструкция вала-шестерни при малом диаметре шестерни
Дальнейшая работа над проектом выполняется в порядке, рекомендованном выше, с использованием материалов, приведенных в атласе и в других учебных пособиях.
109
12. КОНСТРУКЦИИ РЕДУКТОРОВ
Зубчатые и червячные редукторы применяют в самых разных отраслях машиностроения, в основном в составе приводов машин, поэтому их схемы и конструктивное исполнение весьма разнообразны. Развитие технологии и творческая мысль конструкторов постепенно приводят к дальнейшему повышению технического уровня редукторов, основными показателями которого являются:
−удельная материалоемкость, т.е. отношение его массы к величине крутящего момента на выходном (тихоходном) валу;
−коэффициент удельных затрат, под которым понимается отношение затрат на изготовление и эксплуатацию к величине реализуемого! крутящегося момента, который для потребителя косвенно выражается в виде относительной стоимости, т. е. отношение цены редуктора к крутящему моменту на выходном валу.
Кроме этих двух показателей важными являются КПД и шум редуктора. Наибольшее применение имеют редукторы (более 50 % общей потребно-
сти промышленности в редукторах) с передаточным отношением от 10 до 40 и частотой вращения выходного вала от 35 до 140 об/мин. Такие характеристики имеют двухступенчатые цилиндрические, планетарные, червячные редукторы и мотор-редукторы.
Редукторные заводы РФ и стран СНГ выпускают в основном редукторы и мотор-редукторы общемашиностроительного применения, на которые имеются стандарты, большинство конструкций которых представлены в настоящем атласе.
Все большее применение находят мотор-редукторы, т. к. они представляют собой готовый агрегат, что позволяет значительно упростить конструкцию рамы (плиты) и уменьшить затраты на монтаж и эксплуатацию привода машины.
Ватласе представлены конструкции различных редукторов и моторредукторов с цилиндрическими, червячными, коническими колесами, и в комбинации двух видов зацепления, например цилиндрического и червячного, конического и цилиндрического; планетарные и волновые редукторы, которые отличаются большой компактностью и малой удельной материалоемкостью, что особенно важно в различных объектах специальной техники.
Ватласе не дается описание конструкций редукторов, т.к. предполагается, что учащиеся вполне способны самостоятельно разобраться в конструктивных особенностях или прибегнуть к помощи преподавателя-консультанта.
110