
книги / Теория волочения
..pdf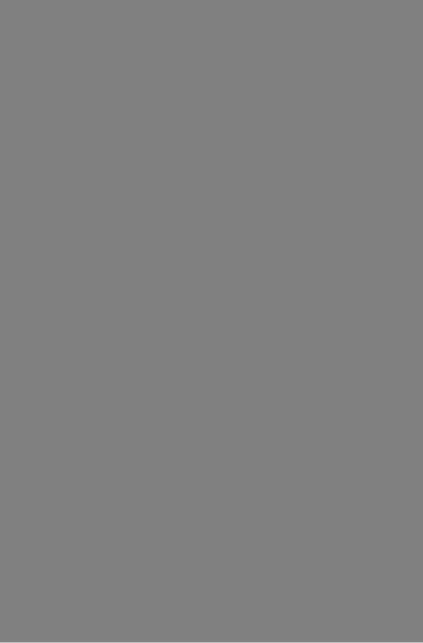
что при обжатиях 10—30% напряжение волочения в радиальных каналах отличается от конических на ± 5 —8%, т. е. напряжения почти равнозначны при одинаковых длинах деформационной зоны. Это объясняется тем, что в первой половине деформацион ной зоны радиального канала траектории главных нормальных продольных напряжений периферийных слоев наклонены к оси канала больше, чем соответствующие траектории в первой поло вине деформационной зоны конической волоки, а во второй половине рассматриваемые траектории в радиальном канале нак лонены к оси канала меньше, чем траектории в коническом.
Рис. 87. Сравнение деформационных зон радиального и конического каналов
Таким образом, некоторое повышение напряжения волочения от увеличенного наклона траекторий в первой половине радиаль ного канала компенсируется некоторым уменьшением напряже ния во второй половине.
Величину угла радиальной образующей определяли по длине деформационной зоны с заменой дуги хордой.
Данную в работе [10] отрицательную оценку канала радиаль ной формы Днестровский и Богорад объясняют неудачной формой примененного канала, отчего получалась большая контактная поверхность. Это объяснение весьма вероятно. Радиальная форма канала имеет перед конической некоторое преимущество: она дает возможность использовать один и тот же канал и для боль ших, и для малых обжатий. В обоих случаях получается необ ходимая контактная поверхность.
Канал конической формы, пригодный для больших обжатий, т. е. имеющий большой угол а, при малых обжатиях дает недо
статочную |
контактную |
поверхность |
и быстро изнашивается. |
Это следует |
из схемы, |
показанной на |
рис. 87. |
122
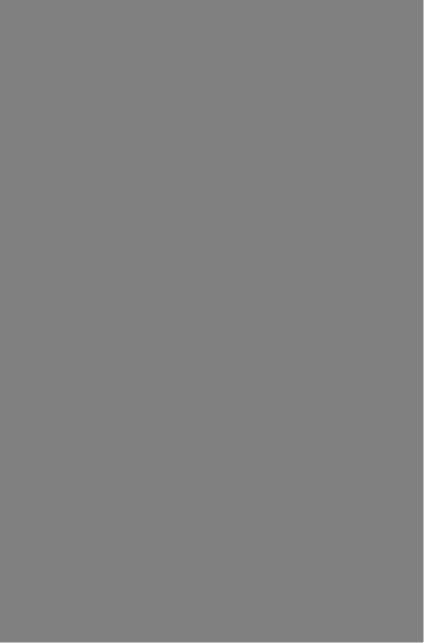
через начало и конец рабочей части радиальной образующей. Естественно, что этот условный параметр изменяется по длине деформационной зоны. Например, он обязательно увеличивается с ростом обжатия, что следует учитывать при анализе процесса
волочения |
проволоки тонких и |
тончайших |
размеров. |
В связи |
с изложенным при |
волочении |
проволоки больших |
и средних диаметров применяют каналы конической и радиальной
Рис. 90. |
Изменение относительного напряжения |
волочения |
по длине деформацион- |
|||||||||
ной |
зоны при |
волочении латуни |
Л63 |
через |
волоки |
с |
STJC |
разного ]профиля |
[17]: |
|||
каналами |
||||||||||||
/ — |
а — |
const, |
tg а = 0,1; 2 — |
tg а д |
= |
0,1, |
tg |
а £ |
= |
0,75, |
= 0,65; 3 — tg <Хд |
= 0, |
|
|
|
tg а £ |
= |
0,86, |
|
= |
0,86 |
|
|
формы (со сравнительно большими радиусами кривизны), для волочения тонких и тончайших размеров используют каналы практически только радиальной формы.
А. В. Юшков и Е. С. Богданов [16] считают радиальную форму канала более рациональной, так как при определенных значениях радиуса кривизны образующей удается сохранить по всей длине деформационной зоны постоянство произведения
интенсивности степени |
деформации 1 |
на предел текучести |
S 7x |
1 Интенсивностью степени деформации называется степень деформации, |
|||
отнесенная к единице длины |
деформационной |
зоны, т. е. отношение |
, |
где х — текущее расстояние поперечного сечения деформационной зоны от ее начала или конца.
124
в каждом его поперечном сечении и этим обеспечить равномерность износа волочильного канала.
Более эффективно для обеспечения равномерности износа во лочильного канала соблюдение условия постоянства произведения интенсивности деформации на напряжение контактного трения. Это произведение может к выходу уменьшаться, вследствие чего более рациональной становится форма канала, приближающаяся к конической.
Сравнение сил волочения через конический и радиальный каналы, выполненное чисто аналитическим путем, описано в более
поздней работе [17]. Результаты этого сравнения приведены на рис. 90. Они показывают, что напряжения волочения при кони ческом канале несколько больше только у самого выхода. При этом не учитывается обязательное существование переходной зоны, которая обеспечивает плавный переход от конической зоны к калибрующей и этим уменьшает силу на выходе. К этому сле дует добавить и то, что в радиальном канале угол у входа при прочих равных условиях больше, чем в коническом, а это увели чивает отгон смазки. Таким образом, и эта работа (несмотря на утверждение ее автора) не указывает на какие-либо заметные преимущества радиальной формы перед конической.
В. В. Зверев [18] предложил форму обжимающей зоны во лочильного канала, образованную кривой АБ (рис. 91), вогну той в тело волоки и построенной по формуле
|
Fx sin 2ах = const, |
(VI-1) |
где Fx — текущее |
поперечное сечение канала; |
А Б (см. |
ах — текущий |
угол наклона касательной к кривой |
|
aXl и аХ2 |
на рис. 91). |
|
125
К этой зависимости В. В. Зверев пришел аналитическим путем, задавшись целью получить такой профиль, который, изнашиваясь, сохранял бы свою форму, отчего увеличивался бы срок службы канала. В своих расчетах В. В. Зверев сделал следующие допу щения:
а) нормальное давление металла на стенки обжимающей зоны канала постоянно;
б) отсутствует давление металла на стенки калибрующей части канала и, следовательно, отсутствует износ этой части канала;
в) рассмотрен идеальный случай — совершенно равномерный износ стенок канала под влиянием равномерного распределения
давления.
В работе [7] отмечено за метное повышение силы воло чения, вызываемое примене нием профиля такой формы.
Следует, однако, отметить, что, несмотря на это и ука занные допущения, изношен ные каналы часто имеют фор му, весьма сходную с пред ложенной В. В. Зверевым. Объясняется это тем, что
в обжимающей зоне канала поверхность протягиваемого металла увеличивается по направлению его движения и, следова тельно, растет воздействие сил трения на стенки канала, отчего он быстрее изнашивается по направлению к выходу. Это скорее указывает на целесообразность делать профиль обжимающей зоны с выпуклыми стенками волоки, т. е. радиальным.
Дальнейшие исследования [19, 20] привели к предложению так называемого «сигмоидального» профиля волочильного ка нала, представляющего собой комбинацию конической и радиаль ной форм (рис. 92), образующую которой можно считать вогнутовыпуклой линией.
В работе [19] проведено сравнительное исследование волоче ния полос из алюминия через волоки с каналом четырех форм: сигмоидальной, конической, вогнутой и выпуклой.
Результаты экспериментов приведены в табл. 8.
Эти результаты показывают, что при сигмоидальном профиле напряжения волочения снижаются мало заметно. Но так как в рассматриваемых экспериментах волочение проводили при малых скоростях, когда гидродинамический эффект не мог про явиться, эти результаты нельзя считать окончательными.
В работах [20] и [86] показано, что волоки с сигмоидальным профилем не имеют заметных преимуществ перед волоками дру гого профиля.
126
|
|
|
|
|
|
|
Т а б л и ц а 8 |
|
Напряжения |
волочения алюминиевых |
полос |
шириной 12,7 м м |
|||
|
через волоки |
с различным |
профилем канала [19] |
|
|||
|
|
|
Толщина П1олосы, |
м м |
Относи |
|
|
|
|
|
|
|
|
Напряжение |
|
Профиль канала |
до воло |
после |
тельное |
||||
обжатие, |
волочения, |
||||||
|
|
|
чения |
волочения |
% |
к Г / м м 2 |
|
Сигмоидальный |
. |
9,593 |
4,915 |
48,8 |
9,62 |
||
Конический |
. |
9,588 |
4,902 |
48,9 |
10,00 |
||
Радиальный |
вогнутый |
|
9,588 |
4,927 |
48,6 |
9,67 |
|
Радиальный |
выпуклый |
|
9,58 |
4,992 |
49,0 |
10,38 |
Недостаток сигмоидальных каналов — повышенная трудность их изготовления и невозможность использования одной волоки для разных относительных деформаций, так как при уменьшении деформации часть канала с малым углом исключается из работы.
Несмотря на указанные отличия профилей волочильного канала, при всех формах профиля основная деформация происхо дит в той части канала, которая имеет коническую или близкую к ней форму.
Поэтому для всех разновидностей каналов представляет инте рес определение величины оптимального угла аопт. Аналитиче ское определение величины аопт, как показано в гл. VII, встре чает заметные трудности.
В связи с этим рядом авторов на основе статистической обра ботки экспериментальных данных предложены различные эмпи рические и полуэмпирические формулы для определения аопт. Основные из этих формул рассмотрены в работе [21]. Сравнение значений аопт, рассчитанных по этим формулам, с приведенными на рис. 79 показывает, что наиболее удовлетворительную сходи мость дает формула Ш. Гелей:
sinaonT= ] / § ^ - . (VI-2)
Рассматривая эту, как и другие аналогичные зависимости, следует иметь в виду, что вследствие гидродинамического эффекта
суменьшением угла а (он же угол смазочного клина) понижается
ивеличина /л, а также и то, что эти формулы получены при ана лизе процессов без внешнего противонатяжения и без учета диаметра профиля.
На силу и напряжение волочения заметно влияет длина ка либрующей зоны канала. Это происходит потому, что протягивае мый металл попадает в калибрующую зону под некоторым сжи мающим напряжением от упругих деформаций, вследствие чего между металлом и калибрующей поверхностью возникают силы трения. Очевидно, что с увеличением длины калибрующей зоны
127
растут и силы трения, а с ними и сила волочения. По данным Минина (рис. 93), увеличение длины калибрующей зоны в усло виях исследованного им процесса в два раза повлекло увеличение силы волочения на 5—10%.
Последующие опыты Н. 3. Днестровского и Р. А. Блюмкиной [22], проведенные с цветными металлами и сплавами, подтвердили указанный характер влияния калибрующей зоны на напряжение волочения.
Ввиду того что по направлению к выходу из канала продоль ные напряжения повышаются, радиальные напряжения к выходу
|
|
|
|
|
из канала |
понижаются. С ними соот |
||||||
|
|
|
|
|
ветственно |
падают |
и |
напряжения |
||||
|
|
|
|
|
контактного |
трения в калибрующей |
||||||
|
|
|
|
|
зоне канала. Это, а также воздей |
|||||||
|
|
|
|
|
ствие предыдущего участка деформа |
|||||||
|
|
|
|
|
ционной |
|
зоны |
на последующий и |
||||
|
|
|
|
|
в некоторой степени релаксация на |
|||||||
|
|
|
|
|
пряжений за время продвижения ме |
|||||||
|
|
|
|
|
талла по калибрующей зоне приво |
|||||||
|
|
|
|
|
дят к тому, что с увеличением длины |
|||||||
|
|
|
|
|
калибрующей зоны повышается и ее |
|||||||
|
|
|
|
|
стойкость. Однако такое |
увеличение |
||||||
|
|
|
|
|
стойкости |
приводит |
к |
повышению |
||||
|
Угол конуса волокисс0 |
напряжения |
волочения, |
а |
иногда, |
|||||||
Рис. 93. Зависимость силы волоче |
как следствие,—к увеличению обрыв |
|||||||||||
ния стальных прутков |
диаметром |
ности. Поэтому |
практикой |
устано |
||||||||
30 м м |
от длины |
калибрующей зо |
влены |
сравнительно |
ограниченные |
|||||||
ны |
/ к, обжатия |
и |
угла а [П : |
|||||||||
|
• -------- • — |
/к |
= |
12 м м ] |
длины |
калибрующей |
зоны |
нового |
||||
|
О----------- О /к = |
® |
канала. Они колеблются в пределах |
|||||||||
|
|
|
|
|
(0,1 —1,5) DK. Меньшие значения при |
меняют при повышенной стойности на истирание материала волоки и при волочении больших сечений, когда поле допусков сравнительно велико. Более высокие значения используют при волочении тонких и тончайших размеров, когда поле допусков мало и когда это позволяют получающиеся напряжения волоче ния (практически применяющиеся длины калибрующей зоны приведены в приложении 4). Изготовление каналов с заданными длинами калибрующей зоны, особенно каналов тонких и тончай ших размеров, встречает серьезные технические затруднения. Поэтому указанные величины, определяющие длину калибрующей зоны, ориентировочны, а их приближенное измерение и учет часто приходится вести методом «приведенного» угла (см. гл. VII).
Влияние длины калибрующей зоны на напряжение волочения зависит от степени деформации: при малых деформациях оно больше, так как в этом случае часть напряжения волочения, идущая на преодоление сил трения в калибрующей зоне, состав ляет заметную долю общего напряжения волочения, и наоборот.
128
При волочении тонкой проволоки, когда калибрующей зоне (чтобы повысить стойкость) придают длину, равную (0,8—1,5) DK, ее влияние на напряжение волочения возрастает, особенно при небольших обжатиях (10—15%), часто применяемых при воло чении профилей тонких и тончайших размеров. Например, при обжатии 10% и угле волоки 6 град, длина обжимающей зоны составляет около одной трети выходного диаметра, т. е. она в 1,5—4 раза меньше длины калибрующей зоны. Поэтому в прак тике волочения проволоки тонких и тончайших размеров измене ние обжатий в пределах 10—25% сравнительно мало влияет на
Волоки Волоподерт/пель
Рис. 94. Схема осаживания трубы с применением строенной волоки
напряжение волочения. Так, например, при волочении медной проволоки диаметром 0,05—0,3 мм через алмазные волоки уве личение обжатия с 10 до 25% приводит к повышению напряжения волочения не в 1,75—2 раза, как должно быть при отсутствии калибрующей части, а лишь в 1,4—1,5 раза.
При волочении сплошных профилей, осаживании и профили ровании труб иногда целесообразно применять сдвоенные и даже строенные (так называемые многосекционные) волоки. Схема осаживания трубы с помощью строенной волоки показана на рис. 94. Сущность такого метода заключается в разделении де формационной зоны на две-три самостоятельные части.
В отличие от многократного волочения общая степень дефор мации при таком методе не может заметно превышать допустимой степени деформации для волочения через одинарную волоку. Однако этот метод имеет следующие преимущества:
1.Во второй и третьей волоках процесс идет с противонатя-
жением от предыдущих волок, что, как показано далее, ведет к понижению давления металла на стенки волочильного канала и уменьшает его износ. Поэтому появляется возможность более длительного использования выходных волок и замены каждой из них по мере износа независимо от остальных.
9 И. Л Перлин |
129 |
2.Могут быть значительно улучшены условия смазки и охлаж дения протягиваемого металла, так как в межсекционные про межутки легко ввести смазку.
3.При волочении с большими углами наклона образующей
канала (а = 20ч-25 град.), например при осаживании трубы с обязательным уменьшением толщины стенки, применение много секционной волоки позволяет достигнуть наименьшего расхож дения между осями каналов и направлением тянущей силы, так как при такой конструкции общая длина канала увеличивается и этим облегчается более правильная установка основной цен тральной секции волоки.
Недостатки многосекционной волоки:
1.Усложнение конструкции волокодержателя.
2.Увеличение отходов металла на захватку.
3.Некоторое повышение силы волочения по сравнению с во лочением в односекционной волоке (при прочих одинаковых деформационных условиях). Это увеличение отмечено в работах [15, 23 и др.1 и объясняется тем, что в промежутках между сек циями волоки размеры протягиваемого металла вследствие его
упругости несколько возрастают в радиальном направлении по сравнению с теми, которые у него были в момент выхода из канала предыдущей секции. Для ликвидации этого упругого последействия в каждой последующей секции должна быть про ведена определенная работа. Кроме того, при применении много секционных волок увеличивается суммарная длина калибрующей зоны, что вызывает дополнительные затраты энергии на преодоле ние трения.
При определении размеров волочильного канала, а также размеров заготовок для волок необходимо учитывать также следующее:
а) длина обжимающей зоны должна быть несколько больше расчетной, чтобы исключить возможность начала деформации за пределами обжимающей зоны (т. е. во входной зоне канала) вследствие несовпадения оси канала с осью заготовки, а также в результате возможного превышения начальных размеров про тягиваемой полосы против расчетных (это может быть при раз работке канала предыдущей волоки). По этой же причине расчет ная длина деформационной зоны должна в производственных условиях определяться по максимальному обжатию;
б) длина входной и выходной зон, кроме чисто технологиче ского назначения, должна обеспечить достаточную прочность волоки против расклинивающего действия радиальных сил, метод определения которых указан на стр. 171.
Эти соображения положены в основу ГОСТов и ведомственных технических условий на заготовки для волок. Методика расчетов заготовок и волочильного канала изложена в п. 17 и в ра боте [24].
130