
книги / Разрушение твердых тел
..pdf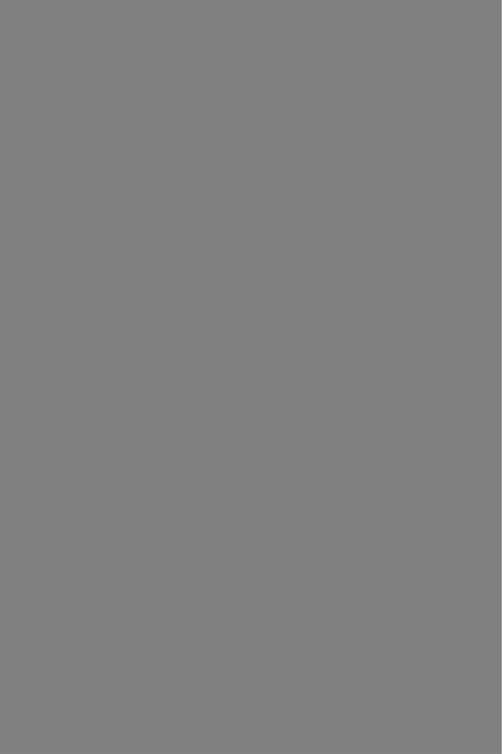
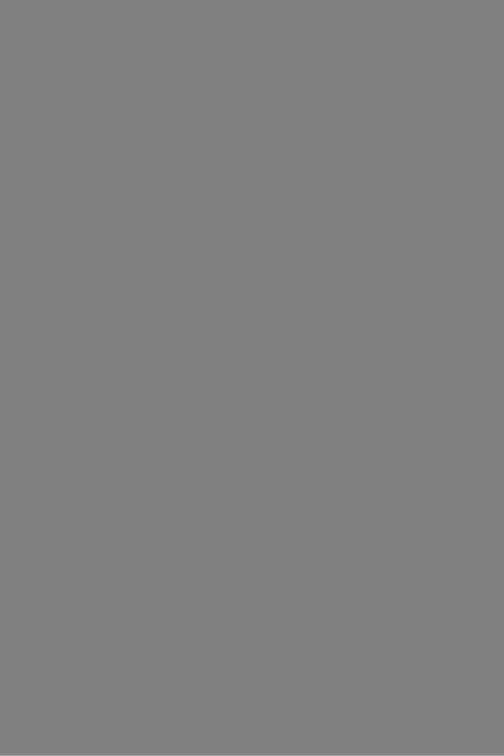
запно, однако также в направлении, параллельном активной си стеме скольжения. Ни в одном случае после разрезки образца и электрополировки не было обнаружено образования пор; однако фрактографические исследования кристаллов из дисперсионно твердеющих сплавов указывают на разрушение типа конус-ча шечка, которое предполагает образование пор. Однако, фрактография кристаллов меди дает совершенно иную картину, кото рую Бивер и Хоникомб связывают с частыми нарушениями про цесса скольжения и с зарождением разрушения в местах нагро
мождений дислокаций. Рози и Абрахамс [8] наблюдали |
поры в |
монокристаллах меди, серебра и сплава Си — 0,1% А1 |
после |
разрушения. Эти кристаллы разрушались с образованием шейки и сужения до острия. Поры были обнаружены после разрезки об разца в области шейки, недалеко от места разрушения и парал лельно его острой кромке. Поры имеют тенденцию к концентра ции вблизи середины поперечного сечения, и существуют опреде ленные признаки того, что удлиненные пустоты развиваются в ре зультате слияния небольших сферических пор.
Выводы
Несомненно, что все рассмотренные виды разрушения имеют характерную общую черту. Зарождение разрушения является результатом негомогенной, пластической деформации в областях микроскопических размеров. В случае низкотемпературного хрупкого разрушения образование областей неоднородной плас тической деформации связано с образованием двойников или полос скольжения; при усталостном разрушении деформация ло кализуется в небольшом числе полос скольжения вследствие из менений хода процесса деформационного упрочнения под дейст вием циклического нагружения; при разрушении в условиях пол зучести первой ступенью в зарождении разрушения оказывается локализация сдвиговой деформации у границ зерен; наконец, при вязком |разрушении этот процесс начинается в результате лока лизации пластической деформации либо у непластичных, вклю чений, либо у полос значительной деформации.
В случае низкотемпературного хрупкого разрушения разви тие трещин в основном определяется сопротивлением пластиче ской деформации у вершины трещины, т. е. сопротивлением дви жению и размножению дислокаций под действием локальных касательных напряжений в области ведущего края трещин. Кро ме того, в процессе разрушения поликристаллов существенную роль приобретают границы зерен, что связано либо с возмож ностью влияния изменения ориентации в области границ на про цесс развития трещин при транскристаллитном разрушении, либо с тем, что границы вследствие сегрегации на них примесей могут стать легким путем для непрерывного продвижения тре щин.
44
В случае усталостного разрушения основная доля всего пе риода испытания образца связана с процессом роста микроско пических трещин вдоль областей интенсивной локальной дефор мации, в конце концов приводящим к образованию макроскопи ческих трещин. Следует полагать, что циклическая деформация приводит к ослаблению полос интенсивного скольжения, в смыс ле облегчения развития трещин, но механизм этого процесса и степень его развития до сих пор остаются неясными.
Развитие разрушения при ползучести, вероятно, увязано с диффузией вакансий либо к вершинам трещин клиновидного ти па, либо к порам, рассеянным по границам зерен, однако эта осо бенность разрушения при ползучести требует дальнейшего изуче ния, необходимого для установления факторов, контролирующих процесс диффузии вакансий, и для выявления различных воз можных источников вакансий.
Развитие разрушения вязкого типа определяется механиз мом локализации деформации, в результате которого образует ся высокая плотность пустот — «слой пустот». По этому «слою» затем под действием либо нормальных, либо касательных напря жений может произойти разрушение.
|
|
|
ЛИТЕРАТУРА |
|
|
1. C o t t r e l l |
A. PL Trans. АКМ'Е, 1958, v. 212, р. 192. |
||||
2 . |
9 t е i n |
D. |
F., iL о w J'. ,R. J. |
Appl. Phys., 1960, |
v. 31, p. 362. |
3. |
L o w J. |
R. |
Deformation and |
Flow of iSolids, |
Springer-Verlag, Berlin, |
1956, |
p. |
60. |
|
E. T. Trans. AIME, |
1957, v. 209, |
p. 930. |
|
|
|
|
|
|
|
|
||||||
4. |
W es s el |
|
|
|
|
|
|
|
|
|||||||||||
5. W o o d |
D. S. a. CT a г k D. S. Trans. ASM, |
1952, v. 43, p. 571. |
|
|
|
|||||||||||||||
6 . O w e n |
W. S. a. o. Trans. ASM, |
1958, v. 50, p. 517. |
|
|
|
|
H. П. В |
сб. |
||||||||||||
7. A l l e n |
N. P. Fracture, Wiley, |
N. Y., 1959, |
p. |
123. ( А л л е н |
||||||||||||||||
«Атомный механизм разрушения». Металлургиздат, |
1963, |
с. 144]. |
807. |
|
|
|||||||||||||||
8. R о s i |
F. Е. a. A b r a h a m s |
М. S'. Acta |
Met., |
1960, |
v. |
8, |
р. |
|
|
|||||||||||
9. |
' Hul l |
D. |
Acta Met., 1960, v. 8, p. 11. |
|
16, |
p. 1309. |
|
|
|
|
|
|
||||||||
10. |
H o n d a |
R. J. Phys. Soc. Japan, 1961, v. |
|
|
|
|
|
|
||||||||||||
11. |
H o r n b o g e n E. Trans. AIME, 1961, v. 221, |
p. 711. |
|
|
|
|
|
|
||||||||||||
12. |
J o h n s t o n |
T. L. a. o. Phil. Mag., 1959, |
v. 4, |
p. 1361. |
|
|
1962, |
v. |
10, |
|||||||||||
13. 'B ee v e r s |
C. J. a. ( Ho n e y c o m b e R. W. K. Acta Met., |
|||||||||||||||||||
p. 17. |
|
J o h n s t o n |
W. G. Phil. M'ag., 1960, v. 5, |
p. |
407. |
|
|
|
|
|
|
|
|
|||||||
14. |
|
|
|
Wiley, |
N. Y., |
|||||||||||||||
15. |
В e e v e r s |
|
C. J. a. H o n e y c o m b e R. W. K. Fracture, |
|||||||||||||||||
1959, p. 4 7 4 . [Б и в е р с К. Дж. и X о н и к о м б Р. В. К. В |
сб. «Атомный меха |
|||||||||||||||||||
низм разрушения». Металлургиздат, 1963, с. 479]. |
|
|
|
Ohio, |
1948, |
p. |
3. |
|
||||||||||||
Ш. Z e n e r |
С. Fracturing in Metals. ASM’, Cleveland, |
|
|
|||||||||||||||||
17. |
S t r o h |
A. N. Advan. Phys., 1957, v. 6 , |
p. |
418. |
1951, v. 22, p. |
1296. |
|
|||||||||||||
18. |
E 1 d i n A. S. а. С о 11 i n s S. C. J. Appl. Phys., |
|
||||||||||||||||||
19. |
O w e n |
W. S. a. o. Trans. Quart. ASM, |
1957, |
v. 50, p.41. |
|
p. |
146. |
|||||||||||||
20. |
C r u s s a r d |
C. a. o. J. Iron |
Steel |
Inst., |
London, |
1956, |
v. |
183, |
||||||||||||
21. |
L o w |
J. R. Fracture, Wiley, |
N. Y., |
1959, |
p. 68. [ Ло у |
Д ж о н |
P. В |
сб. |
||||||||||||
«Атомный механизм разрушения». Металлургиздат, 1963, с. 84]. |
|
|
|
|
|
|||||||||||||||
22. |
G i 1m a n |
J. J. Trans. AIME, |
1955, |
v. 203, |
р. |
1252. |
|
|
|
|
|
|
|
|||||||
23. |
G i l m a n |
J. |
J. J. Appl. Phys. 1960, v. 31, |
p. |
2208. |
|
|
|
|
|
|
|
||||||||
24. |
H o d g e |
J. |
a. o. Trans. AIME, 1949, v. 185, p. 233. |
|
|
|
|
|
|
|
|
25. |
P e t c h |
N. J. Fracture, Wiley, N. Y., |
1959, P- 54. [ Пе т и |
И. Дж. В сб. |
||||||||||||||||||||
«Атомный механизм разрушения». Металлургиздат, 4965, с. 69]. |
|
|
|
|
|||||||||||||||||||||
В |
26. |
С о 11 г е 11 А. Н. Fracture, Wiley, IN. Y., |
1959, p. 20. [К о т г р е л л А. X. |
||||||||||||||||||||||
сб. |
|
«Атомный механизм |
разрушения». |
Металлургиздат, |
1963, |
с. |
109]. |
||||||||||||||||||
|
27. |
IH a h n G. Т. а. о. Fracture, Wiley, iN. Y., |
1959, p. 91. [ Ха н |
Дж. T. и др. |
|||||||||||||||||||||
В сб. «Атомный механизм разрушения». Металлургиздат, 1963, с. 109]. |
|
||||||||||||||||||||||||
|
28. |
K i e s |
J. А. а. о. J. Appl. P'hys., |
1950, |
v. 21, |
р- |
716. |
|
|
|
|
|
|
||||||||||||
|
29. |
Т ti г к а 1 о |
А. М. Trans. AIME, |
I960, |
v. 218, р. |
24. |
|
|
|
|
|
||||||||||||||
|
30. |
P l a t e a u |
J. а. о. ‘Rev. M'ttallurgie, Paris, |
1957, v. 54, p. 3 . |
|
|
|||||||||||||||||||
|
31. |
S p a c i l |
H. S. a. W u l f f |
J. The Metal |
Molybdenum, |
ASM, Cleveland, |
|||||||||||||||||||
Ohio, |
1958, p. |
262. |
D. J. Inst. Metals, 1952, |
v. 81, p. |
121. |
|
|
|
|
|
|
|
|||||||||||||
|
32. |
M c L e a n |
|
|
|
|
|
|
|
||||||||||||||||
|
33. |
P 1a t e a u J'. a. |
0. R’ev. Univers. Mines, |
1956, |
12. |
Inst., |
London, |
1952, |
|||||||||||||||||
v. |
34. |
R e e s |
W. |
P. |
a. |
H o p k i n s |
B. F. |
J. |
Iron |
Steel |
|||||||||||||||
172, |
p. 403. |
|
|
|
|
|
|
|
|
|
|
|
|
|
|
|
|
|
|
|
|
|
|
||
|
35. |
W e s t b r o o k |
J. H. |
a. W o o d |
D. L. Nature, |
1961, |
v. |
192, |
p. |
1280. |
|||||||||||||||
|
36. |
L o w |
J. IR'. a. F e u s |
t e l ;R. G. Acta |
Met., 1953, |
v. |
1, p. 185. |
|
|
||||||||||||||||
|
37. |
A i n s 1 i e N. G. a. 0. Acta Met., 1960, |
v. |
8, P- 528. |
|
|
|
1957,A242, |
|||||||||||||||||
p. |
38. |
W o o d |
W. A. a. S e g a 11 |
R. L. Proc. Roy. Soc. London, |
|
||||||||||||||||||||
180. |
|
|
|
|
|
|
|
|
|
|
|
|
|
|
|
|
|
|
|
|
|
|
|
||
p. |
39. |
С 0 f f i n L. F. |
jr. a. T a v e r n e l l i |
J. |
F. |
Trans. |
AIME, |
1959, v. 215, |
|||||||||||||||||
794. |
|
|
|
|
|
|
|
|
|
|
|
|
|
|
|
|
|
|
|
|
|
|
|
||
|
40. |
E b n e г M. L. а. В а с к 0 f e n W. A. Trans. AIME, |
1959, |
v. |
215, |
p. 510. |
|||||||||||||||||||
|
41. A 1d e n T. H. а. В а с к 0 f e n W. A. Acta Met., |
1961, |
v. 9, p. 352. |
|
|||||||||||||||||||||
|
42. |
F e 11 h a m |
P. Phil. Mag., 1961, v. |
6, |
p. |
1479. |
|
p. |
435. |
[В. А. Б э к о |
|||||||||||||||
|
43. |
B a c k o f e n W. A. Fracture, |
Wiley, |
N. Y., |
1959, |
||||||||||||||||||||
ф е н. В сб. «Атомный механизм разрушения». Металлургиздат, |
1963, с. 438]. |
||||||||||||||||||||||||
|
44. |
М с Е v i 1 у |
A. J. |
jr., М а с h 1 i n Е. ‘S. Fracture, |
Wiley, |
|
N'. Y., |
1959, |
|||||||||||||||||
p. 450 [Мак И в1ли А. Дж. мл., М э ч л и н Е . |
С. |
В |
сб. «Атомный |
механизм |
|||||||||||||||||||||
разрушения». Металлургиздат, 1963, с. 455]. |
|
|
|
|
Properties |
of |
Crystals, |
||||||||||||||||||
|
45. |
S е е g е г A., Dislocations |
and |
the Mechanical |
|||||||||||||||||||||
N. Y., |
1957, p. 243 [ З е г е р |
А. «Дислокации и механические свойства |
кристал |
||||||||||||||||||||||
лов», |
ИЛ, 1960, с. 179]. |
|
|
|
|
1961, v. |
6, р. 1493. |
|
|
|
|
|
|
||||||||||||
|
46. |
S е g а 11 R. L. а. о. Phil. Mag., |
|
|
|
|
|
|
|||||||||||||||||
|
47. |
А1 d en |
Т. Н. Acta |
Met., |
1962, |
v. 10, |
р. |
653. |
|
|
|
|
|
|
|
|
|||||||||
|
48. A l d e n |
J. H. Acta |
Met., |
1963, |
v. 11, |
p. |
65. |
|
|
|
|
|
|
1958, |
v. 87, |
||||||||||
|
49. |
F e g r e d o |
D. M. a. G r e e n |
o u g h |
G. |
B. J. Tnst. Metals, |
p.87.
50.E w i n g J. A. a. H u m p h r e y Jl C. W; Phil. Trans. Roy. Soc., 'London,
1903, v. A200, p. 241. |
|
|
|
|
|
p. 3. |
|
|
|
|
|
|
||||
51. |
G o u g h |
H. J. Proc. ASTM, 1933, v. 33, |
Academic |
Press, |
N. Y., |
|||||||||||
52. |
W o o d |
|
W. A. |
Fatigue in |
Aircraft |
Structures. |
||||||||||
1956, p. |
1. |
|
|
|
N. a. 0. Phil. Mag., |
1956, |
v. 1, p- 113. |
|
|
|
|
|||||
53. |
T h o m p s o n |
|
|
|
|
|||||||||||
54. |
B u l l e n |
F. P. a. 0. Proc. Roy. Soc., |
London, |
1953, v. A216, P- 332. |
сб. |
|||||||||||
55. |
W o o d |
W. A. Fracture. Wiley, N. Y., |
1959, p. |
412. |
[ В у д |
В. А. В |
||||||||||
«Атомный механизм разрушения». Металлургиздат, 1963, с. 438]. |
|
|
||||||||||||||
56. |
С г u s s а г d С. Fracture, W'iley. N. Y., |
1959, р. |
524. [Крюссар Ш. В сб. |
|||||||||||||
«Атомный механизм разрушения». Металлургиздат, 1963, с. 535]. |
|
|
|
|||||||||||||
57. |
F o r s y t h |
Р. J'. Е. Nature, 1953, v. 171, р. 172. |
|
and Fatigue |
щ |
|||||||||||
58. |
Р а г к е г IE. R. a. F e g r e d o |
D. М. |
Internal |
Stresses |
||||||||||||
Metals, Elsevier, Amsterdam, 1959, p. 263. |
1953, v. 82, |
p. |
449. |
|
|
|
|
|||||||||
59. |
F о г s у t h |
P. J. E. J. Inst. Metals, |
|
|
|
|
||||||||||
60. |
H u l l |
D. J. |
Inst. Metals, 1955, |
v. 84, |
p. |
527. |
|
|
1957, v. A242, |
|||||||
61. |
C o t t r e l l |
A. H. a. H u l l |
D. Proc. Roy. Soc., London, |
|||||||||||||
p. 2 1 1 . |
H u l l |
D. J. |
Inst. Metals, 1957, |
v. 86, |
p. |
425. |
|
|
|
^ |
o |
|
||||
62. |
[X ем п ел |
сб. |
||||||||||||||
63. |
H em p e l H. R. Fracture, |
N. Y.. 1959, |
p. 376. |
M. P. В |
||||||||||||
«Атомный механизм разрушения». |
Металлургиздат, 1963, |
с. 376]. |
|
|
64. |
M o t t N. F. Acta Met., |
1958, |
v. |
6, p. 195. |
Plastice |
|
Flow |
and |
Fracture. |
|||||||||||||||||||||
65. |
B r i d g m a n |
|
P. W., Studies |
in |
Large |
|
|
|||||||||||||||||||||||
McGraw-Hill, N. Y., 1952. |
|
|
|
|
|
|
|
|
|
|
|
|
|
|
|
|
|
|
|
|
|
|
||||||||
66 . ' K e n n e d y |
|
A. J. Phil. Mag., 1961, v. 6, |
p. |
49. |
|
|
|
|
|
|
|
|
|
|||||||||||||||||
67. |
|
W a d s w o r t h |
N. J., T h e s i s |
Ph. D. |
Univ. Bristol, 1955. |
|
|
|
||||||||||||||||||||||
68. T h o m p s o n |
N. Fracture. N. Y., |
1959, |
p. |
354. |
|
|
|
|
|
|
|
|
|
|||||||||||||||||
[ Т о м п с о н |
H. В |
сб. «Атомный |
механизм |
разрушения». Металлургиздат, |
||||||||||||||||||||||||||
1963, с. 354]. |
|
|
|
|
|
|
|
|
|
|
|
|
|
|
|
|
|
|
|
|
|
|
|
|
|
|
|
|
||
69. |
|
К е m s 1е у |
|
D1. 'S. J. iPnst. Metals, |
1956, |
v. 85, |
р. |
420. |
Metals, |
1957, |
||||||||||||||||||||
70. |
|
S t u b b i n g t o n C . |
A., |
F o r s y t h |
P. J. |
E. |
J. |
|
Inst. |
|||||||||||||||||||||
v. 86, p. 90. |
|
|
|
|
|
|
|
|
|
|
|
|
|
|
|
|
|
|
|
|
|
|
|
|
|
|
|
|
||
71. |
J a c q u e t |
P. A. Rev. Metallurgie, |
Paris, |
1957, v. 54, p. 489Г^ |
|
|
|
|||||||||||||||||||||||
72. |
|
W a d s w o r t h |
IN’., |
H u t c h i n g s . |
J. Phil. |
|
Mag., |
1958, v. 3, p. 1154. |
||||||||||||||||||||||
73. |
|
S m i t h |
G. C. Proc. ’Roy. Soc., |
London,1957, |
v. A242, |
p. |
189. |
|
A242, |
|||||||||||||||||||||
74. H о n e у с о m b e iR. W. K. Proc. Roy. |
|
Soc., |
|
London, 1957, v. |
||||||||||||||||||||||||||
p. 213. |
|
|
|
|
|
|
|
|
|
|
|
|
|
|
|
|
|
|
|
|
|
|
|
|
|
|
|
|
|
|
75. |
|
E l w o o d |
|
E. |
C. |
a. D u c k e t t R . |
Nature, |
1934, |
v. |
173, |
p. |
497. |
S. |
519. |
||||||||||||||||
76. |
|
S i e b e l |
E. |
u. S t a h l |
i G. Atch. Eisenhiittenw., |
|
1942, |
Bd. |
15, |
|||||||||||||||||||||
77. |
|
M o П е г |
H. u. H e m p |
el |
M. Arch. Eisenhiittenw., |
1954, Bd. 25, S. 39. |
||||||||||||||||||||||||
78. |
|
L i s s n e r |
0 . |
Colloquium |
on |
Fatigue, |
Springer-Verlag, |
|
Berlin, 1955. |
|||||||||||||||||||||
79. |
|
P u 11 i с к |
К. E. Phil. Mag., |
1959, |
v. 4, |
p. |
|
964. |
|
185. |
|
|
|
|
|
|||||||||||||||
80. |
|
О r o w a n |
E. Rtept. Prog. |
Phys., |
1948, |
v. |
12, |
p. |
|
|
|
|
|
|
||||||||||||||||
81. |
|
И e a d |
A. K. Phil. Mag., 1953, |
v. 44, |
p. |
925. |
|
|
|
andAppliedMecha |
||||||||||||||||||||
82. |
|
W e i b u 11 W. International |
Union |
of |
Theoretical |
|
||||||||||||||||||||||||
nics Colloquium |
of |
|
Fatigue, ‘Stockholm, 1955, |
p. |
289. |
|
|
|
|
|
|
|
|
Suppl., |
||||||||||||||||
83. |
T h o m p s o n |
N., a. W a d s w o r t h |
N. J. |
|
Brit. J. Appl. Phys., |
|||||||||||||||||||||||||
1951, v. 6, p. 51. |
IP’. J. E. |
a. o. |
J1. Inst. |
Metals, (London, |
|
1962, v. 90, p. 238. |
||||||||||||||||||||||||
84. |
F o r s y t h |
|
||||||||||||||||||||||||||||
85. |
G if k i n s |
/R. C. Fracture, |
Wiley, |
N. Y., |
1959, |
p. |
|
579. |
|
|
|
Металл |
||||||||||||||||||
[ Д ж и ф к и HI с |
P. К. В сб. «Атомный механизм |
|
разрушения». |
|||||||||||||||||||||||||||
лургиздат, 1963, |
с. |
593]. |
|
|
N. F. Trans. АРМЕ, |
1956, v. 206, |
p. |
554. |
||||||||||||||||||||||
86. C h a n g |
Б. |
С. a. G r a n t |
||||||||||||||||||||||||||||
87. |
M c L e a n |
D. J. 'Inst. Metals, |
1957, |
v. 85, |
p. 468. |
|
1960, |
v. 209, |
p. |
829. |
||||||||||||||||||||
88. C h e n |
C. W. a. M a c h i i n |
E. S. Trans. |
|
AIME, |
||||||||||||||||||||||||||
89. |
G r a n t |
|
N. J. Fracture, Wiley, |
N. Y., |
1959, |
p. |
562. |
[ Г р а н т |
H. |
Дж. |
||||||||||||||||||||
В сб. «Атомный механизм разрушения». Металлургиздат, 1963, с. 575]. |
v. 3, |
|||||||||||||||||||||||||||||
90. |
S e r v i |
I. S. |
a. G r a n t |
N. J. |
J. |
Metals, |
(Trans. |
АШМЕ), |
1951, |
|||||||||||||||||||||
p. 917. |
S t a c e y |
.R. D. Metallurgia, |
1958, |
v. 58, |
p. 125. |
|
|
|
|
|
|
|
|
|||||||||||||||||
91. |
|
|
1957, |
v. 85, |
p. |
480. |
||||||||||||||||||||||||
92. |
N e i l d |
B. |
|
J. |
a. Q u a r r e l |
A. G. J. |
-Inst. Metals, |
|
||||||||||||||||||||||
93. |
H e s l o p |
J. J. |
Inst. Metals, |
1962, v. 91, |
p. |
28. |
|
p. |
1. |
|
|
|
|
|
|
|||||||||||||||
94. |
B a i l ey |
R. W. J. Jun. Inst. |
Eng., |
1935, |
v. |
46, |
|
|
|
|
|
|
||||||||||||||||||
95. |
G l e n |
J. |
J. |
Iron Steel Inst., London, 1958, |
v. |
190, |
p. 30. |
|
|
|
|
|||||||||||||||||||
96. |
W e v e r |
C. W. J. Inst. Metals, |
London, |
|
1960, v. 88, p. 296. |
Creep, |
Iron |
|||||||||||||||||||||||
97. |
К i г к b у H. W. a. T r u m a n |
R. J. Structural |
Processes in |
|||||||||||||||||||||||||||
Steel |
Inst., London, |
1961, |
p. 204. |
|
|
|
|
|
|
1954, v. 2, p. 250. |
|
|
|
|
||||||||||||||||
98. |
G r e e n w o o d |
J. N. a. o. A*cta Met., |
|
|
|
Lon |
||||||||||||||||||||||||
99. |
H у a m |
E. D. Structural |
Processes |
in |
Creep, |
Iron |
a. Steel Inst., |
|||||||||||||||||||||||
don, 1961, p. 76. |
|
|
|
|
|
|
|
|
|
|
|
|
|
|
|
|
|
|
|
|
|
|
|
|
|
|
|
|||
100. C h e n |
C. |
W7. |
a. M a c h |
1in |
E. S. Acta |
Met., 1956, |
v. 4, |
p. |
655. |
|
||||||||||||||||||||
101. H u l l |
D. |
|
a. R i m m e r |
D. !E. Phil. Mag., |
1959, |
v. |
4, |
p. |
173. |
|
|
|||||||||||||||||||
102. P a r k e r |
|
E. R. a. o. Proc. AS'TM, 1946, |
v. 46, |
p. |
1159. |
|
|
|
|
|||||||||||||||||||||
103. P l a t e a u |
|
J'. a. o. 'Rev. Met., Paris, |
1957, v. 54, p. 200. |
|
|
|
|
|||||||||||||||||||||||
104. R o g e r s |
|
H. C. Trans. АРМЕ, 1960, v. 218, |
p. |
|
498. |
|
|
|
|
|
||||||||||||||||||||
105. R o g e r s |
|
H. C. Acta Met., 1959. v. 7, |
p. |
750. |
|
|
|
|
|
|
1962, |
v. 7, |
||||||||||||||||||
106. В e e v e г s |
C. J. a. H о n e у с о m b e R. W. K. Phil. Mag., |
|||||||||||||||||||||||||||||
p. 763. |
|
|
W. |
P. |
a. H o p k i n s |
В. ‘E. J. |
Iron Steel |
Inst., |
London, |
1952, |
||||||||||||||||||||
107. R e e s |
|
|||||||||||||||||||||||||||||
v. |
172, p. |
403. |
|
|
|
|
|
|
|
|
|
|
|
|
|
|
|
|
|
|
|
|
|
|
|
|
|
МЕТАЛЛОГРАФИЧЕСКОЕ ИССЛЕДОВАНИЕ РАЗРУШЕНИЯ СПЛАВОВ А1—Си и A l-Cu—Zn—Mg ПРИ РАСТЯЖЕНИИ
ВВЕДЕНИЕ
За последние несколько лет можно отметить значительные успехи в понимании проблемы вязкого разрушения металлов и сплавов в условиях растяжения. Работами Путтика [1], Роджер са [2] и Коттрелла [3] показано, что разрушение в центральной части конуса и чашечки происходит в результате слияния мик роскопических внутренних пустот, которые растут в результате пластической деформации под действием трехосного напряжен ного состояния, возникающего при развитии шейки образца. Из наблюдений Типпера [4] и Плато с сотрудниками [5], которые для изучения поверхности разрушений ряда металлов и сплавов ис пользовали электронную микроскопию, следует, что внутренние пустоты зарождаются в результате разрушения частиц соедине ний. Работы Путтика, проведенные на чистой меди [1] подтвер ждают эту точку зрения, а Коттрелл [3] особо подчеркивает, что у весьма чистых металлов при испытании на растяжение можно получить очень высокие значения сужения поперечного сечения. Форсайт и Райдер [6] также показали, как хрупкое межзеренное разрушение высокопрочных алюминиевых сплавов может зарож даться у частиц выделений по границам зерен. С другой стороны, Роджерс [2], изучая поликристаллическую медь, не обнаружил признаков зарождения разрушения у частиц соединений, в отли чие от Биверса и Хоникомба [7], исследовавших полностью со старенные монокристаллы сплава А1 с 5,5% Си; однако и те и другие исследователи нашли (с помощью исследования под электронным микроскопом реплик с излома) на поверхностях разрушения ямки, характеризующие вязкое разрушение, проис ходящие в связи с ростом пор.
Большая часть данных, известных до настоящего времени, получена при исследовании поликристаллических чистых метал лов, тогда как работы по сплавам в основном ограничиваются изучением монокристаллов. Целью настоящей серии эксперимен тов явилась проверка соответствия современных идей о разру шении реальному поведению поликристаллических сплавов си стем А1 — Zn — Mg и А1 — Си, имеющих большое значение для авиационных конструкций. Для опытов были использованы спла-1
1 D. A. R у d е г, А. С. S m а 1е.
48
вы указанных систем как высокой чистоты, так и промышлен ные сплавы; при этом в приводимых ниже опытах главным обра зом изменялась длительность старения.
МЕТОДИКА ЭКСПЕРИМЕНТА
Использованные в экспериментах сплавы имели следующие составы:
1.А1 (сверхчистый) + 7,3% Zn + 2,6% Mg.
2.А1 (сверхчистый) + 3,9% Си.
3. А1 |
(промышленной |
чистоты) + 4,66% |
Zn + |
2,25% |
Mg + |
+ 1,35% |
Си (DTD 683, по американской номенклатуре 7075). |
||||
4. А1 |
(промышленной |
чистоты) + 3,95% |
Си + |
1,0% |
M g + |
+ 0,75% Si + 0,56% Mg (BSL 65, по американской номенклату ре 2024).
Все материалы поставляли в виде круглых прутков, получен ных методом экструзии, из которых изготовляли образцы диа метром 6,8 мм для испытаний на растяжение. Образцы закали вали на твердый раствор и подвергали старению разной продол жительности, а затем испытывали при комнатной температуре на тензометре Хаунсфилда при скорости деформации 0,03 мин-К
Из материала в каждом состоянии было испытано как мини мум по три образца, а в некоторых случаях — для уточнения кар тины разрушения испытывались еще добавочные образцы. Ис пытанные образцы разрезали и исследовали обычными металло графическими методами; поверхности изломов во многих случаях исследовали с помощью световой и электронной микроскопии. Для последней использовали три типа реплик: двухступенчатая ацетатная целлюлоза — угольная; одноступенчатая — угольная прямая оксидная.
РЕЗУЛЬТАТЫ ЭКСПЕРИМЕНТА
Деформация и разрушение каждого сплава рассматриваются отдельно; начать удобнее с простого тройного сплава А1 — Zn — Mg.
Сплав сверхчистого алюминия с 7,3% Zn и 2,6% Mg
Образцы из этого сплава проходили закалку при 450° С на твердый раствор; затем их подвергали старению при 150° С раз ной продолжительности и после этого испытывали. Закалка на твердый раствор всегда дает полностью рекристаллизованную структуру; влияние такой обработки на механические свойства сплава показано на рис. 1. Из приведенных данных следует, что
4 За к. 351 |
49 |
максимум прочности достигается в результате старения при 150° С в течение 0,7 суток. Наиболее интересно то, что истинное сопротивление разрушению остается приблизительно постоянным при старении от 0,1 до 10 суток. Металлографические исследова ния шлифов, изготовленных из образцов, прошедших механиче ские испытания, указывают на наличие двух основных типов разрушения; переход от разрушения одного типа к другому со
впадает с началом линейного участка |
кривой |
истинного |
разру |
|||||
шающего напряжения (см. рис. 1). Разрушение первого |
типа, |
|||||||
|
687,9(70,г) |
|
|
|
|
|
v,% |
|
|
|
|
|
|
|
70 |
|
|
£ |
|
л___ |
■•т• |
> |
|
60 |
|
|
|
|
|
50 |
|
||||
I |
|
\ |
|
го^ |
\ |
|
|
|
|
д\ ^ |
|
^ |
х. |
|
|
||
|
|
|
|
* / А |
|
|||
|
|
/V |
|
|
/ \- 40 |
|
||
|
|
|
|
А< о' |
|
|
||
§ |
305,7(31,2) |
А |
|
|
А*/ |
|
30 |
|
; |
-т4-- |
|
го |
|
||||
е |
( |
|
|
|
|
|
|
|
* |
229,3(23,4). |
|
0) |
1,0 |
10 |
|
юо |
|
|
|
|
|
|
1д т ( т 6 сушках)
Рис. 1. Влияние старения при 150° С на механи ческие свойства сплава на основе сверхчистого алюминия с 7,3% Zn и 2,6% Mg (т — продолжи тельность старения, сутки):
1 — поперечное сужение; 2 — истинное сопротивление разрушению; 3 — предел прочности
показанное на рис. 2, имеет транскристаллитный характер и наи более четко выявляется на образцах, прошедших закалку на твер дый раствор, у которых первоначально равноосные зерна перед разрушением сильно вытягиваются; трассы разрушения идут под углом 45° к оси образца. В процессе деформации, как это показа но на рис. 3 и 4, перед разрушением также возникает большое количество продольных интеркристаллитных трещин. Старение продолжительностью 0,02 суток вызывает некоторые изменения характера разрушения: направление трассы разрушения меняет ся при переходе трещины от зерна к зерну, в результате чего по верхность разрушения приобретает более грубо текстурованный характер, чем на образцах, закаленных на твердый раствор. Это различие показано на рис. 3 и 4. Связано оно, вероятно, с тем, что более значительное удлинение образцов, закаленных на твер дый раствор, которое связано со значительными поворотами бо лее крупных зерен, дает возможность отдельным зернам в
50
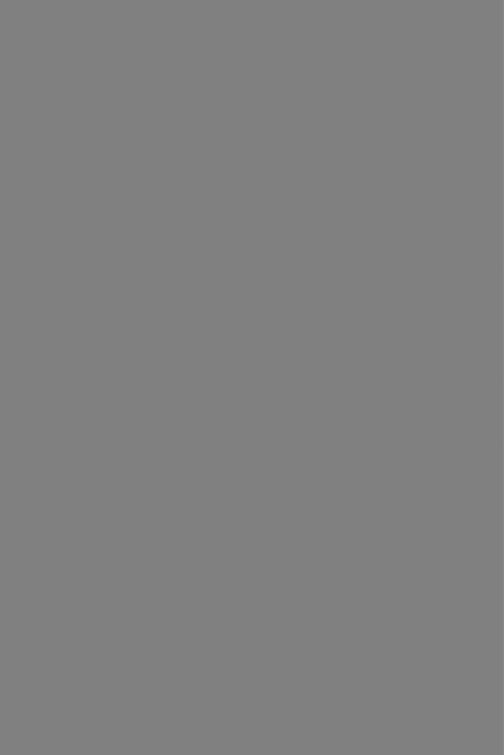