
книги / Сварка в машиностроении. Т. 3
.pdf
|
|
|
СПИСОК ЛИТЕРАТУРЫ |
|
|
|
|
|
|
||
|
1. |
Браун У., Сроули Д. Испытания высокопрочных металлических материалов на |
|||||||||
вязкость разрушения |
при плоской деформации. М., |
Мир, |
1972. |
246 с. |
|
||||||
|
2. |
Винокуров В. А. Учебное пособие по курсу «Специальные главы прочности свар |
|||||||||
ных конструкций*. МВТУ им. |
Баумана, 1973. |
ПО |
с. |
|
|
|
|
||||
ния |
3. |
Винокуров В. А., Трегубов Г. П. Метод испытания образцов на изгиб для определе |
|||||||||
пластичности. — «Заводская |
лаборатория», |
1975, |
№ |
12. |
1497— 1500 |
с. |
|||||
|
4. |
Качанов |
Л.М. Основы механики разрушения. М., |
Наука, |
1974. |
312 с. |
|||||
М., |
5. |
Махутов |
Н.А. Сопротивление элементов |
конструкций |
хрупкому |
разрушению. |
|||||
Машиностроение, |
1973. 200 |
с. |
|
|
|
|
|
|
|||
|
6. |
Партон В. 3., Морозов Е. М. Механика упругопластического разрушения. М., |
|||||||||
Наука, |
1974. 416 с. |
|
|
|
|
|
|
|
|
||
ных |
7. |
Разработка методики исследования статической прочности и пластичности свар |
|||||||||
соединений |
металлов при низких температурах. |
В. А. |
Винокуров, |
С. М. Исаев, |
В. |
А. Парахин и др. Кн.: — Остаточные напряжения и прочность сварных соединений |
|
и |
конструкций. |
Л»133. М., Машиностроение, 1969. с. 57—72. |
|
8. Хрупкие |
разрушения сварных конструкций. У. Дж. Холл, X. Кихара, В. Зут, |
А.А. Уэллс. М., Машиностроение, 1974. 320 с.
9.Черепанов Г. П. Механика хрупкого разрушения. М„ Наука, 1974. 640 с.
Г л а в а 6
ЖАРОПРОЧНОСТЬ СВАРНЫХ СОЕДИНЕНИЙ
СВОЙСТВА ОСНОВНОГО МЕТАЛЛА
Жаропрочность, определяющая способность материалов сопротивляться воздействию нагрузки при высоких температурах, является комплексной харак теристикой, зависящей от стабильности их свойств при высокотемпературной выдержке, сопротивления ползучести, длительной прочности, пластичности, тер мической усталости и других факторов.
Из промышленных металлов и их сплавов наименьшую жаропрочность имеют сплавы алюминия (до 250° С), а наибольшую (до 1000° С) — сплавы молиб дена. Сплавы титана можно использовать до 400—450° С, перлитные стали — до 500— 580° С, аустенитные — до 650—700° С, а сплавы на кобальтовой и никеле вой основе — до 800—900° С. Применяя композитные материалы, можно поднять
рабочую температуру до 1100— 1200° С. |
сравнивать, используя понятие |
|
В первом приближении металлы можно |
||
гомологической температуры, определяемой как |
а = |
Т |
------ , гдеТ* и Тпл— темпера- |
Т чл
туры испытания и плавления, выраженные в градусах абсолютной шкалы. При а ^ 0,3—0,4 развитие пластической деформации, определяющее разрушение металла и осуществляемое движением и размножением дислокаций, приводит к деформационному упрочнению (наклепу) и возрастанию сопротивления ее раз вития. Это упрочнение стабильно во времени, и поэтому свойства, полученные по результатам кратковременных механических испытаний, справедливы и для длительного нагружения металла конструкции в эксплуатации. Так как пласти ческая деформация локализуется скольжением внутри зерен, то разрушение носит внутризеренный характер и для большинства конструкционных материалов сопровождается заметной деформацией при разрыве.
С ростом температуры повышается тепловая энергия колебания атомов и снижается прочность межатомных связей, что приводит и к снижению прочности металлов. Его интенсивность зависит от вида металла и его сплавов. Прочность низкоуглеродистой стали с 400° С резко снижается и при 600° С становится весьма малой (рис. 1, а). Легирование перлитных сталей в первую очередь хромом, мо либденом и ванадием несколько повышает их прочностные характеристики, делая возможной длительную эксплуатацию до 550— 580° С. Повышение прочности в ин тервале 500—600° С аустенитной хромоникелевой стали связано с изменением структурного состояния (рис. 1, б). В интервале 650—850° С наиболее эффективно использовать жаропрочные сплавы на никелевой основе (рис. 1, в).
С ростом температуры увеличивается интенсивность диффузионных процес сов в металле, что делает его наклепанное состояние нестабильным и приводит к разупрочнению и восстановлению исходных свойств. В зависимости от темпера туры последнее может осуществляться механизмами возврата и рекристаллиза ции. При возврате восстановление свойств не сопровождается видимыми измене ниями структуры металла; при рекристаллизации оно связано с образованием но вых недеформированных зерен. Процессы возврата проходят при средних гомоло гических температурах (0,25—0,5 Г пл), что соответствует уровню рабочих темпе ратур высокотемпературных установок. Рекристаллизация развивается при более высоких температурах (0,4—0,8 Тпл) и сопровождается резким снижением прочности металла. Поэтому верхняя температурная граница эффективного при
менения того или иного материала расположена ниже температуры его рекристал лизации.
Развитие процессов возврата приводит к влиянию скорости нагружения на свойства металла, проявляющемуся в снижении его прочности с уменьшением скорости деформации и изменении пластичности [1, 10, 11]. Оно обуслов ливает также процесс ползучести — способность материала непрерывно де формироваться (ползти) пбд действием постоянной нагрузки. Процессом, род ственным ползучести, является релак сация, приводящая к переходу упру гой деформации в пластическую при условии постоянства суммарной де формации нагруженного элемента. В крепежных элементах релаксация при водит к ослаблению затяжки болтов.
В сварных конструкциях развитие процесса релаксации определяет эф фективность снятия сварочных напря жений при термической обработке [3].
Протекание процесса высокотем пературной ползучести во времени приводит к исчерпанию деформацион ной способности и разрушению мате риала, закономерности поведения ко торого определяются зависимостями длительной прочности и пластичности. При их определении широко исполь зуют предложенную А. В. Станюкови чем степенную зависимость типа t =
|
|
|
= Во~п\ где t — время до разрушения; |
|||||
|
|
|
В и т — постоянные. |
|
||||
|
|
|
|
На рис. 2 эта зависимость выра |
||||
|
|
|
жена в виде наклонной прямой, что |
|||||
|
|
|
позволяет приближенно экстраполиро |
|||||
|
|
|
вать |
результаты относительно |
кратко |
|||
|
|
|
временных испытаний на длительный |
|||||
|
|
|
срок службы. |
Для получения досто |
||||
|
|
|
верных |
данных |
такой экстраполяции |
|||
|
|
|
максимальная длительность испытаний |
|||||
|
|
|
должна быть не менее чем на порядок |
|||||
Рнс. 1. Механические |
свойства сталей |
меньше расчетного срока службы. Для |
||||||
стационарных энергетических |
устано |
|||||||
и сплава |
на никелевой |
основе при вы |
||||||
вок |
при |
сроке |
службы 10б |
длитель |
||||
соких температурах: |
|
|||||||
|
ность испытаний должна быть не ме |
|||||||
а — сталь |
15; 0 — сталь 08Х18Н10; |
|||||||
нее |
104 |
ч. |
|
|
||||
в — сплав |
ХН80ТБЮ |
|
|
Основной расчетной характеристи |
||||
|
|
|
кой |
прочности металла и сварных сое |
динений при высоких температурах является предел длительной прочности сгдп, соответствующий напряжению, вызывающему разрушение при данной темпера туре за расчетный срок службы (обычно 10б—2-10* ч для стационарных и 102, 103 и 10* ч для транспортных установок).
Длительность высокотемпературных испытаний можно сократить, исполь зуя параметрические зависимости типа показанной на рис. 3 [4]. Для ее построе ния необходимо иметь результаты нескольких относительно кратковременных ис
пытаний на длительную прочность при рабочей температуре и температурах на 50— 100° С выше ее. Подобная параметрическая обработка позволяет прибли женно оценить предел длительной прочности за заданный срок службы в опреде ленном интервале температур. В верхней части рисунка приведено дополнитель
ное построение для определения температуры и |
длительности работы. |
С повышением температуры и длительности |
испытания (см. рис. 2) наблю |
дается перегиб кривых длительной прочности, связанный с переходом от вязкого внутризеренного к хрупкому межзеренному излому. Этот переход приводит не только к снижению длительной прочности. Он обусловливает также повышенную вероятность преждевременных хрупких разрушений конструкций, особенно при наличии в них концентраторов напряжений. В связи с этим необходимо знать за кономерности изменения длительной пластичности и условия, приводящие к ее снижению.
Изменение длительной пластичности со временем и температурой подчиня ется определенным закономерностям, наиболее полно выявляемым в условиях
|
|
|
6,кгс/мм* |
|
|
|
30 |
Рис. |
2. |
Длительная прочность |
25 |
20 |
|||
металла |
шва, наплавленного |
ю |
|
электродами типа Э-09Х1МФ |
12 |
||
(марки ЦЛ-20М). Температура |
10 |
||
испытания: О — 500°С; • — |
в |
||
565°С; |
д — 600°С |
6 |
и
испытаний с постоянной скоростью деформации [10]. При относительно низких температурах Тг (рис. 4, а) и прохождении внутрикристаллического разрушения пластичность с уменьшением скорости деформации v (с увеличением длительно сти работы) меняется сравнительно мало. С повышением температуры до Т2 и уменьшением скорости деформации наблюдается переход к межзеренному излому, сопровождаемый снижением пластичности до определенного значения.
В координатах |
lg Ô — Т зависимости изменения пластичности имеют вид |
V -образных кривых |
с минимумом, смещающимся в область более низких темпера |
тур с уменьшением скорости деформации (рис. 4, б). Провалы пластичности обычно наблюдаются в интервале рабочих температур и поэтому должны учитываться при анализе работоспособности изделий. Пластичность перлитных сталей заметно падает в интервале 500—600° С, аустенитных сталей при 550—650° С и сплавов на никелевой основе при 600—750° С. С повышением легирования и прочности стали или сплава, ростом зерна и при наклепе снижение пластичности в темпе ратурном интервале хрупкости становится все более заметным. Пластичность резко уменьшается при наличии концентраторов напряжений, что можно оценить по результатам испытания образцов с надрезом. Для сварных соединений, в связи с практической невозможностью исключения в них концентраторов, закономер ности изменения длительной пластичности необходимо изучать особо тщательно.
На жаропрочность металлов влияют их структурное состояние и его стабиль ность во времени. Аустенитные стали с гранецентрированнон кубической решет кой, обладая более высокой температурой рекристаллизации, чем перлитные стали с объемноцентрированной решеткой, можно применять как жаропрочные
материалы при температурах на |
100— 120° С выше. |
|
Для металлов, предназначенных к использованию при высоких температу |
||
рах, характерны два |
вида структурного упрочнения: I) образование твердого |
|
раствора с введением |
элементов, |
повышающих температуру рекристаллизации |
и снижающих интенсивность диффузионных процессов в сплаве; 2) получение высокодисперсной смеси фаз путем закалки многокомпонентного сплава и после дующего отпуска. Для промышленных металлов характерно одновременное ис пользование упрочнения обоих видов. Fro стабильность во времени, определяе мая степенью развития процесса коагуляции упрочняющихся фаз, оценивается по результатам испы тания образцов после старения раз ной длительности при высоких тем
пературах.
IgS
*) igv
Рис. 3. Параметрическая |
зависимость |
Рис. |
4. Изменение длитель |
||||
длительной |
прочности металла |
шва, |
ной |
пластичности при высо |
|||
наплавленного |
электродом |
типа |
ких |
температурах: |
|||
Э-09Х1МФ |
(обозначения |
точек |
см. |
а — удлинение — скорость де |
|||
рис. 2) |
|
|
|
|
формации; |
б — удлинение — |
температура
Многие ответственные высокотемпературные конструкции работают в усло виях повторного или малоциклового нагружения при переменных температурах и сложном напряженном состоянии. При оценке их прочности и ресурса работы необходимо учитывать накопление повреждаемости по двум механизмам: ползу чести и усталости. Примерами малоциклового повреждения сварных узлов явля ются разрушения штуцерных соединений труб с коллекторами котлов, мест при варки ранжирующих элементов к трубам.
СВОЙСТВА СВАРНЫХ СОЕДИНЕНИЙ
Требуемые свойства металла и сварных соединений для высокотемператур ных установок зависят от условий их эксплуатации. Для большинства из них основными являются показатели стабильности свойств и длительной прочности и пластичности, определяющие вероятность разрушения данного узла за срок
его работы. Для отдельных конструкций, например камер сгорания газовых турбин, определяющими являются показатели жаростойкости металла. Работо способность узлов, подвергаемых большому числу теплосмен, будет зависеть прежде всего от их сопротивления усталости. Для узлов химических аппаратов кроме жаропрочности должна оцениваться и коррозионная стойкость сварных соединений.
Прочность и пластичность. При высоких температурах изменение струк туры и свойств отдельных зон соединения, обусловленное сваркой, проявляется заметнее, чем при нормальной температуре. Из-за нестабильности структурного состояния этих зон интенсивность развития в них диффузионных про цессов, определяющих степень разупрочнения свар ного соединения, будет выше по сравнению с основ ным металлом, что приводит, как правило, к до полнительному снижению прочности и пластич ности.
Механические свойства металла шва (рис. 5) при высоких температурах, как и при температу ре 20° С, зависят от термического режима сварки, жесткости соединения и термической обработки. С повышением жесткости соединения, например при переходе от наплавки на кромку к сварке много слойного стыкового шва, прочность шва в исходном состоянии, обусловленная его высокотемператур ным наклепом при воздействии 1ермодеформационного цикла сварки, заметно возрастает. Пластиче ские свойства (штриховые кривые) аустенитных швов разного исполнения меняются сравнительно мало; для перлитных швов характерно более за-
Рис. 5. Механические свойства металла шва, на |
|
|
|
|
||||||||
плавленного электродом типа Э-27Х15Н35ВЗГ2Б2Т |
|
|
|
|
||||||||
при |
высоких |
температурах |
(1 — наплавка |
на |
|
|
|
|
||||
кромку; |
2 — стыковой |
шов): |
|
|
|
|
|
|
|
|||
а — исходное |
состояние; |
б — стабилизация при |
900° С, |
fl 2оо |
m |
боо |
т/с |
|||||
10 ч + при 700° С, 35 ч; в — аустенизация и стабилизация |
||||||||||||
при |
1100° С, |
1 ч |
+ при 900° С, |
10 ч + при 700° С. |
35 ч |
|
|
|
|
|||
метное снижение пластичности с повышением жесткости соединения. Кратко |
|
|||||||||||
временная прочность многослойных стыковых швов обычно выше прочности |
|
|||||||||||
близкого по легированию основного металла. Их большая прочность сохра |
|
|||||||||||
няется до температур интенсивного разупрочнения, что в условиях типовых |
|
|||||||||||
скоростей деформирования при испытаниях составляет |
около 600—650° С для |
|
||||||||||
перлитных сталей и 700—750° С для аустенитных. |
|
|
|
|
||||||||
|
Большая прочность сварных швов за счет их развитой субструктуры по |
|
||||||||||
сравнению с основным металлом сохраняется и после термической обработки по |
|
|||||||||||
режиму отпуска для перлитных и стабилизации для аустенитных сталей (рис. 5, б). |
|
|||||||||||
Снижение и выравнивание свойств металла швов разных условий выполнения |
|
|||||||||||
обеспечивается лишь после полной термической обработки — нормализации с от |
|
|||||||||||
пуском |
для |
перлитных и аустенизации |
со |
стабилизацией для |
аустенитных |
|
(рис. 5, в), снимающей эффект наклепа.
Выявленные закономерности изменения при высоких температурах механи ческих свойств сварных швов справедливы и для их длительной прочности и пла стичности. При относительно умеренных температурах и внутризеренном харак тере разрушения длительная прочность швов несколько выше прочности основ ного металла близкого легирования, а пластичность может быть несколько меньше.
Для сварных швов характерен больший разброс точек при испытаниях, что обус ловлено нестабильностью их структуры и наличием наклепа. При повышении тем пературы до значения, являющегося переходным в отношении появления межзеренных трещин (565° С для шва; рис. 2), этот переход у металла шва осущест вляется раньше, чем у основного металла. На стадии межзеренного разрушения (при большой продолжительности испытания) длительная прочность шва, наплав ленного электродом типа Э-09Х1МФ, будет уступать прочности близкой по леги рованию стали марки 12Х1МФ. Пластичность шва при межзеренном разрушении будет снижаться больше, чем пластичность основного металла. Подобные законо мерности справедливы для сварных швов в исходном и отпущенном (стабилизи рованном) состояниях после сварки (рис. 6). Так, металл шва, наплавленного
Рис. |
6. Влияние |
термической обработки |
на |
длитель |
||||
ную |
прочность |
и |
пластичность |
при |
565° С |
металла |
||
стыкового сварного шва, наплавленного электродом |
||||||||
типа Э-09Х1МФ: |
|
|
|
|
|
|
||
■ |
— исходное состояние; ▲ — отпуск |
при |
730° С. 5 ч; |
|||||
□ |
— нормализация при 980° С, 1 ч + |
отпуск |
при 730° С, 5 ч |
|||||
электродом типа Э-09Х1МФ, |
при 565° С в исходном |
и отпущенном состояниях |
при длительности испытания до 104 ч по прочности превосходит основной металл; в дальнейшем его прочность становится ниже прочности основного металла. В состоянии нормализации и отпуска металл шва при испытании малой длитель ности менее прочен, чем сталь и швы в двух первых состояниях. Резкое уменьше ние его прочности связано со снятием эффекта наклепа при нормализации, а также обусловлено меньшим содержанием углерода в шве по сравнению с основным металлом (заштрихованная область). С повышением длительности испытания наб людается сближение длительной прочности швов, подвергнутых отпуску и норма лизации с отпуском.
Швы в исходном состоянии имеют повышенный разброс точек на кривой длительной прочности и низкую пластичность при сравнительно малом времени до разрушения. При увеличении длительности испытания пластичности в исход ном и отпущенном состояниях близки. Наибольшую длительную пластичность имеют швы после полной термической обработки,
Для некоторых сварных узлов, например труб большого диаметра из легиро ванных сталей с продольным швом, полная термическая обработка после сварки является обязательной по требованию калибровки сваренных труб. В таких слу-
6,игс/мм2 |
|
|
|
|
- |
• |
|
|
|
|
|
|
|
Ь*4 |
---------- |
|
|
> х |
|
|
|
\ |
. ( |
|
|
2 |
|
if --------— — |
1 1 1 -------------— |
1 *' 11--------— —* |
I’1» |
10г |
103 |
10й |
ч |
Рис. 7. Длительная прочность сварных соединений стали 15Х1М1Ф при 540° С в состоянии нормализации с по следующим отпуском; швы:
1 — однослойный, |
полученный |
электрошлаковой сваркой; |
2 — многослойный, |
полученный |
автоматической сваркой под |
флюсом |
|
|
чаях, например для толстостенных труб из теплоустойчивых перлитных или высокохромистых мартенситных сталей, можно рекомендовать электрошлаковую сварку. Из-за большого проплавления свариваемых кромок при использовании тех же проволок содержание углерода в шве, полученном электрошлаковой
Рис. 8. Пределы длительной прочности металла сварных швов, наплавленных электродами различных типов за 10Бч:
/ - Э50А; |
2 — Э-09Х1М; 3 — 09Х1МФ; |
||
4 — Э-12X13; 5 — Э-12Х11НМФ; |
6 |
- |
|
Э-07Х20Н9; |
7 — Э-08Х19Н10Г2Б; |
8 |
- |
Э-07Х19Н11МЗГ2Ф; Р -Э -11Х15Н25М6АГ2;
10— Э-27Х15НЗБВЗГ2Б2Т;
11— Э-08Х14 Н65М5В4 Г2
сваркой, будет близким к содержанию углерода в основном металле, что урав няет их свойства. Использование электрошлаковой сварки вместо многослойной автоматической сварки под флюсом применением одной и той же проволоки марки СВ-08ХМФА для изготовления труб ф 980 X 40 мм из теплоустойчивой стали 15Х1М1Ф, повысило длительную прочность сварных соединений и снизило ве роятность разрушений по шву (рис. 7),
5 п/р. Винокурова В. А., т. 3
Поданным большого числа испытаний на рис. 8 приведены значения пределов длительной прочности металла стыковых швов, которые можно принимать при расчетах сварных соединений. Большинство полученных значений совпадает со значениями для основного металла близкого состава. У высоколегированных свар ных швов, например жаропрочных на никелевой основе, длительная прочность уступает прочности основного металла.
Длительная прочность и пластичность сварных соединений определяются степенью их неоднородности и с повышением легирования основного металла и
d, кес/мм2
14
12
10
в
6
и
14
12
10
в
6
4
Рис. 9. Длительная прочность оребренных сварных труб поверхностей нагрева котлов:
а — трубы из стали 20; Тисп » 475° С; / — гладкие трубы;
2 — оребренные |
трубы; б |
— трубы из стали 12Х1МФ; |
7исп 1=3 600° С; |
/ — гладкие |
трубы; 2 — оребренные трубы, |
отпуск после сварки; 3 — оребренные трубы, после сварки, нормализации с отпуском
особенно с переходом к термически упрочняемым материалам имеют тенденцию к снижению. На рис. 9 по данным испытания под внутренним давлением при вы соких температурах приведены зависимости длительной прочности гладких и сварных оребренных труб ф 32 X 6 мм из сталей 20 и 12Х1МФ. Эксперименталь ные точки для сравниваемых вариантов (рис. 9, а) располагаются вокруг общей линии, лежащей выше средней прямой гарантированных значений длительной прочности стали 20 (сплошная линия). Оребренные трубы разрушаются вне зоны оребрения (рис. 10, а); разрушение характеризуется высокой пластичностью (окружная деформация около 22—38%), одинаковой для гладких и оребренных труб.
Для стали 12Х1МФ длительная прочность гладких и оребренных труб (см. рис. 9, б) различается значительно. Если для гладких труб экспериментальные точки расположены выше кривой гарантированной длительной прочности стали 12Х1МФ (сплошная линия), то для оребренных труб, отпущенных после сварки, они находятся в области нижней границы допустимого отклонения результатов
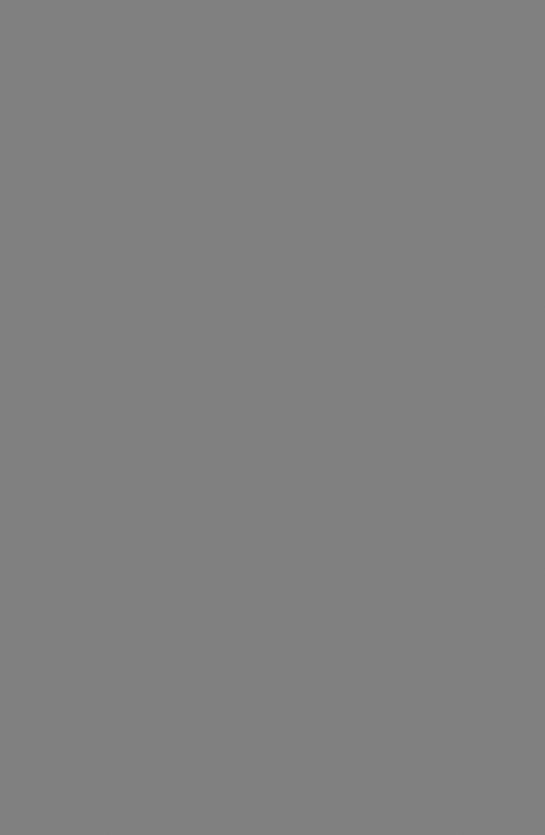