
книги / Сварка в машиностроении. Т. 3
.pdfприема последнего узла компоновки-настила пола, располагаемого в подвеске на опорах 6, а затем отправляется на склад.
Со склада подвески «виноградные грозди» системой автоматического адресо вания подаются к главному сборочному кондуктору (рис. 47) челночного типа, включающему многоточечную сварочную машину 4, шесть подвесных сварочных
Рис. 47. Схема главного сборочного кондуктора
машин 3 и связанные между собой кондукторные тележки / и 5. Подвеску с ком поновкой узлов кузова опускной секцией 2 подают на приемную тележку /, узлы снимают, устанавливают в кондуктор тележки и фиксируют прижимами. Затем тележку подают в многоточечную машину 4. Ее электроды сваривают узлы снизу, остальные сварные точки выполняют подвесными машинами 3. В это время вторая тележка находится на другой позиции, где ранее собранный кузов захва тывается рычагами подвески, опускная секция толкающего конвейера поднимает его, и подвеска с кузовом отправляется на линию окончательной сварки,
При изготовлении кузовов автомобиля за рубежом используют промышлен ные роботы, представляющие собой манипулятор, управляемый с помощью ЭВМ. Наибольшее распространение получили роботы типа «Юнимейт» (рис. 48). Вал Î обеспечивает вращение поперечины 2 вокруг вертикальной оси с помощью гидроцилиндра 3 и пары рейка—зубчатое колесо. Поворот поперечины вокруг гори зонтальной оси осуществляется гидроцилиндром 4, закрепленным на валу 1. Поступательное перемещение руки задается гидроцилиндром 5. Вращение кисти
руки 6 вокруг оси 7 и площадки 8 для крепления инструмента вокруг оси 9 обес печивается системой зубчатых колес и гидроцилиндров, расположенных в кор пусе кисти руки 6 ив цилиндрических штоках 10. Применительно к изготовлению кузовов легковых автомобилей роботы этого типа нашли применение главным образом в качестве носителя сварочных клещей. Работе предшествует «обучение» робота. Для этого опытный рабочий на первом узле, поданном конвейером, после довательно перемещает инструмент от одной сварочной точки к другой, вводя эту программу в запоминающее устройство нажатием кнопок «Память» и «Сварка». Выполнение программы начинается после того, как узел, подлежащий сварке, займет на конвейере фиксированное исходное положение и сигнал об этом посту пит в запоминающее устройство. Каждая степень свободы перемещения задается своим гидроцилиндром с управляющим сервоклапаном, и каждый гидроцилиндр
имеет |
детектор |
положения, |
дающий |
|
|
|
||||||
сигнал |
в |
запоминающее устройство. |
|
|£ |
АЛ |
|||||||
Достоинством робота является его уни |
|
|||||||||||
версальность, |
т. е. |
возможность |
бы |
|
|
-ф |
||||||
строй |
смены |
программ, |
хранящихся в |
|
|
|||||||
памяти машины, например, по команде |
|
|
|
|||||||||
системы автоматического адресования. |
|
|
|
|||||||||
Это позволяет использовать роботы на |
|
|
|
|||||||||
конвейере, |
подающем |
узлы |
кузовов |
|
|
|
||||||
автомобиля |
разных модификаций. |
|
|
|
|
|||||||
В условиях |
крупносерийного про |
|
|
|
||||||||
изводства штампосварные изделия |
про |
|
|
|
||||||||
стой формы целесообразно изготовлять |
|
|
|
|||||||||
из рулонной полосы на непрерывно |
|
|
|
|||||||||
действующей |
автоматической |
линии. |
|
h i |
|
|||||||
Например, на таких линиях выпускают |
|
|
||||||||||
отопительные радиаторы (рис. |
49) |
па |
Рис. 49. |
Отопительный радиатор па |
||||||||
нельного |
типа |
[13]. Заготовки |
с |
вы- |
||||||||
нельного |
типа |
|
||||||||||
штампованными в |
них |
каналами |
для |
|
||||||||
циркуляции |
воды соединены по пери |
|
|
|
метру шовной сваркой, а между каналами — точечной. При этом все операции выполняют на полосах с разрезкой их на отдельные элементы только на послед ней стадии изготовления. Это упрощает передачу заготовок с одного рабочего места на другое и обеспечивает непрерывность процесса, но требует выполнения формовки и сварочных операций на движущейся полосе.
Размотка двух рулонов выполняется в двухсекционном разматывателе одно временно, полосы располагаются в два яруса одна над другой (рис. 50). В формо вочной машине две пары валков-роликов, имеющих жесткую кинематическую связь, одновременно производят формовку верхней и нижней полос с зеркальным отображением каналов и перемычек. Штуцера привариваются к верхней полосе «летучей» контактной сварочной установкой методом оплавления. Патрубок 1 (рис. 51) автоматически подается из питателя и с помощью верхнего 2 и нижнего 3 сварочных электродов прижимается к месту приварки. После окончания сварки через отверстие в нижнем электроде пуансон 4 прошивает отверстие 5 и разваль
цовывает лишний металл по стенкам патрубка. |
Летучая |
установка |
приваривает |
к верхней полосе одновременно оба патрубка |
панели |
радиатора. |
После при |
варки патрубков полосы совмещаются и устройством валкового типа подаются в неподвижную многоэлектродную машину для сварки точек между каналами. Два кинематически связанных четырехзвенника (рис. 52) обеспечивают плоско параллельное перемещение траверс, несущих верхние и нижние электроды. В процессе сварки точек электроды перемещаются в результате сцепления с дви жущейся полосой при приложении сварочного давления. Быстрое возвратное движение электродов выполняет пневмоцилиндр 1, В машине предусмотрены четыре одинаковых сварочных блока, имеющих верхние и нижние электроды. Одновременно работают два блока электродов, выполняя два ряда поперечных
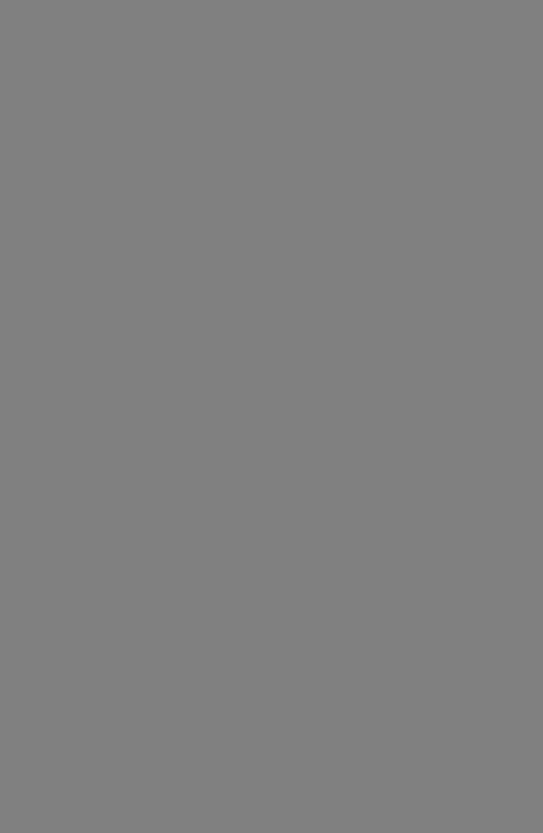
СВАРНЫЕ ДЕТАЛИ МАШИН
В тяжелом и энергетическом машиностроении крупные сварные детали сва ривают в условиях единичного и мелкосерийного производства, используя за готовки из толстолистового проката, поковок или стальных отливок.
На рис. 53 показана рама клети прокатного стана, составленная из четырех литых заготовок из стали 35Л. Места стыков выбраны из условия симметрии сварочных деформаций и относительной простоты формы каждого элемента. Сложное очертание двутаврового сечения в месте стыка заменено сплошным (А—А) для удобства выполнения его электрошлаковой сваркой. Раму собирают в горизонтальном положении с помощью скоб, стыки сваривают попарно. При изготовлении станин из толстолистового проката широко используют электрошлаковую сварку. Угловые и тавровые соединения элементов собирают с помощью
косынок и диафрагм, стыковые — с помощью скоб. В местах, не доступных для постановки формующих медных охлаждаемых подкладок, применяют остающиеся стальные пластины. Последовательность выполнения сборочно-сварочных опера ций выбирают такой, чтобы концы каждого из электрошлаковых швов можно было вывести за пределы детали. Поэтому общей сборке сложной детали обычно предшествуют сборка и сварка относительно простых узлов. При этом для умень шения угловых перемещений целесообразно, чтобы каждый собранный под сварку узел имел замкнутое сечение.
Конструкция валов гидравлических турбин проста — это массивная труба с одним или двумя фланцами. Заготовки обечаек обычно получают ковкой, за готовки фланцев -w ковкой или литьем, стыки между ними выполняют одно проходной электрошлаковой сваркой. На сборку кольцевых стыков заготовки поступают после Предварительной механической обработки. При сборке длин ных валов необходимо предусмотреть некоторый излом оси в месте стыка для компенсации неравномерной поперечной усадки по периметру шва. Точность готового вала обеспечивается чистовой механической обработкой, производимой после нормализации и высокого отпуска.
Крупные валы паровых и газовых турбин изготовляют из жаропрочных сталей путем сварки отдельных поковок — дисков и концевых частей. Наличие внутренних замкнутых полостей, смещение которых относительно оси вращения вызывает недопустимую неуравновешенность вала, приводит к необходимости соблюдения жесткого допуска на искривление его продольной оси. Это достига ется точной сборкой и прецизионной технологией сварки. Кованые заготовки дисков после механической обработки центрируют относительно друг друга на правляющими поясками, требуемый зазор в разделке обеспечивается с помощью проставок. Собранные элементы плотно стягивают тягами 1 (рис. 54) с компенси
рующими |
усадку пружинами 2; в вертикальном положении ротор подается на |
|||||||||||||||
|
|
сварку. Для обеспечения |
равномерной |
поперечной |
||||||||||||
|
|
усадки по периметру кольцевого шва сварку выпол |
||||||||||||||
|
|
няют в несколько слоев. Каждый корневой шов вы |
||||||||||||||
|
|
полняют одновременно двумя |
|
или тремя |
симмет |
|||||||||||
|
|
рично |
расположенными |
|
сварочными |
головками |
||||||||||
|
|
аргонодуговой |
сваркой вольфрамовым |
электродом. |
||||||||||||
|
|
В этом положении несколько слоев укладывают |
||||||||||||||
|
|
плавящимся |
электродом в среде |
углекислого газа. |
||||||||||||
|
|
После |
заполнения |
той |
части |
разделки, |
которая |
|||||||||
|
|
необходима |
для |
обеспечения |
определенной |
жест |
||||||||||
|
|
кости |
ротора, |
его |
переносят |
в |
центровой |
враща |
||||||||
|
|
тель с горизонтальным положением оси и основную |
||||||||||||||
|
|
часть |
разделки |
заполняют |
путем |
многослойной |
||||||||||
|
|
сварки под флюсом в нижнем положении. Такая |
||||||||||||||
|
|
технология |
позволяет предотвратить |
искривление |
||||||||||||
|
|
оси настолько, что биение сваренного |
вала |
не |
пре |
|||||||||||
|
|
вышает 0,5 мм на длине 5 м. |
|
|
|
|
|
|
||||||||
|
|
Рабочие колеса мощных гидротурбин (рис. 55) |
||||||||||||||
|
|
имеют |
настолько |
большие |
размеры, |
что доставка |
||||||||||
|
|
на место монтажа |
целиком |
возможна |
только |
вод |
||||||||||
|
|
ным путем. |
Верхний обод турбины |
Красноярской |
||||||||||||
|
|
ГЭС выполняли из двух литых заготовок из стали |
||||||||||||||
|
|
20ГСЛ |
электрошлаковой |
сваркой с |
последующим |
|||||||||||
|
|
высоким отпуском и механической обработкой. |
||||||||||||||
|
|
Лопасти из той же стали отливали в |
кокиль. |
|||||||||||||
|
|
Часть выпуклой поверхности лопасти, наиболее |
||||||||||||||
Рис. 54. |
Вал газовой тур |
подверженной |
кавитационному |
износу, |
защищали |
|||||||||||
наплавкой |
или облицовкой кавитационно-стойкой |
|||||||||||||||
бины |
|
|||||||||||||||
|
сталью. Нижний обод собирали из четырех штам |
|||||||||||||||
|
|
|||||||||||||||
|
|
пованных заготовок из стали 22К, сваривали |
||||||||||||||
электрошлаковой сваркой и после высокого отпуска |
подвергали |
механи |
||||||||||||||
ческой обработке. Сборку начинали с разметки внутренней поверхности |
верх |
|||||||||||||||
него обода по шагу и профилю |
и установки |
на ней лопастей с зазором под |
электрошлаковую сварку. В верхнем ободе закрепляли ось с цапфами и с ее по мощью собранный узел устанавливали на стойках кантователя с целью поворота каждого стыка в положение, удобное для выполнения его электрошлаковой сваркой плавящимся мундштуком. Плавный переход от лопасти к верхнему ободу обеспечивали с помощью медных подкладок соответствующей формы, охлаждае мых водой. После сварки и промежуточного высокого отпуска торцы лопастей обрабатывали для сопряжения с нижним ободом на карусельном станке, а кромки подготавливали под К-образную разделку. Нижний обод с лопастями одновре менно сваривали два—четыре сварщика полуавтоматами в среде углекислого газа. Сваренное колесо подвергали нормализации и высокому отпуску, после чего выполняли окончательную механическую обработку.
Колеса крупных гидротурбин можно изготовлять и по другой технологии. Рабочее колесо Плявиньской ГЭС выполняли в виде двух частей для перевозки его по железной дороге, причем заводскую сварку осуществляли преимуще
ственно вручную покрытым электродом. На монтаже стыки верхнего обода со бирали на болтах, а нижнего обода сваривали вручную способом «поперечной горки». Подогрев перед сваркой до 120—200° С и последующий высокий отпуск стыков обода выполняли с помощью индукторов.
В отличие от мелкосерийного производства тяжелых и энергетических ма шин для изделий общего машиностроения более характерно серийное и крупно серийное производство. Соответственно требования по технологичности конструк тивного оформления и производительности используемого оборудования в по следнем случае оказываются выше. Применительно к изготовлению сварных станин из литых заготовок большой интерес представляет новая технология сборки и сварки картера блока тепловозного дизеля, освоенная на Коломенском
тепловозостроительном заводе [4]. По этой технологии картеры восьми-, двенад цати-, шестнадцати- и двадцатицилиндровых V-образиых дизелей собирают из унифицированных стоек (рис. 56), отлитых из стали 20Л. Стойки последовательно присоединяют одна к другой контактной сваркой непрерывным оплавлением, причем лапы / и 5, боковые стенки 2 и 4 и верхнюю перемычку 3 сваривают одно
временно |
(суммарное сечение 50 000 |
мм2). Специальный сборочно-сварочный |
|
комплекс |
К-579 |
обеспечивает механизацию операций приема стоек, подачу их |
|
в зону сварки, |
совмещения базовых |
поверхностей, перемещения после сварки |
на заданный шаг и выдачи сваренного изделия. Сварка выполняется автомати чески с программным регулированием, обеспечивая точность по длине картера
± 2 ,5 |
мм, расстояние между осями цилиндров ± 1 мм, смещение стоек в попереч |
ном |
направлении не более 2 мм и по пропеллерности основания стоек ± 2 мм. |
Суммарный припуск на сварку одной стойки 40 мм. Однородность структуры сварных соединений и их механических свойств позволила отказаться от после дующего высокого отпуска картера,
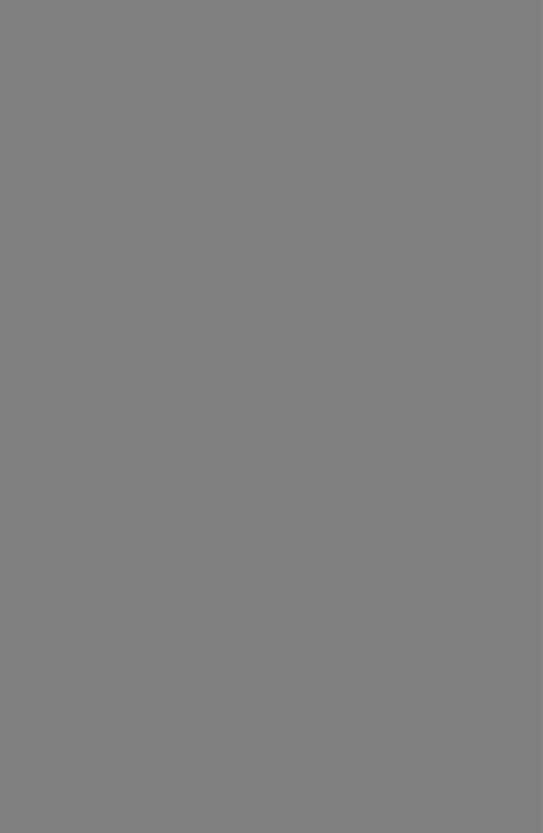
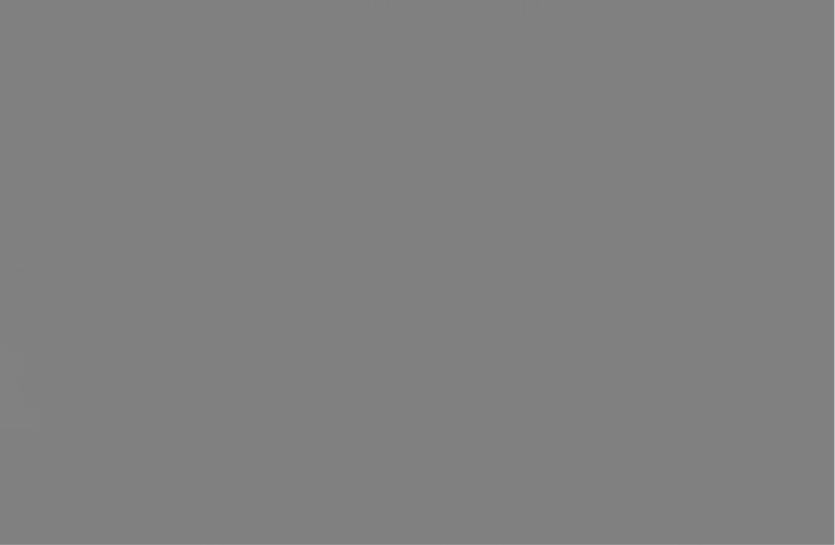
женного системой отсекателей, обе заготовки одновременно поступают в прием ную призму 12 манипулятора. Под действием пневмоцилиндра 4 фиксатор 5 входит в зацепление с ротором 3, после чего манипулятор 7 начинает поворачи ваться вместе с ротором 3 вокруг оси вала 6. При этом пиевмоцилиндр 11 по на правляющим 10 подает призмы 12 вверх до зажимных пинолей 2, центрирую щих половины катка с прижатием их друг к другу. Цилиндр 11 опускает призму 12, цилиндр 4 выводит из зацепления фиксатор 5, и манипулятор 7 возвращается в исходное положение пневмоцилиндром 9, закрепленным на станине 8. Вклю чается сварочный вращатель (см. рис. 58) с приводной 2 и холостой 7 бабками, и начинается процесс сварки. При этом ротор 1 и изделие 8 непрерывно и равно мерно вращаются относительно своих осей. После того как свариваемый каток совершит полный оборот вокруг своей оси и 0,75 оборота вокруг оси ротора, сварка прекращается и изделие выгружается на ходу при определенном поло жении ротора.
Шкивы, барабаны и другие детали подобного типа обычно изготовляют с по |
|
мощью дуговой сварки. При серийном производстве зубчатых колес сварку ис |
|
пользуют в ограниченной степени. В то же время экономичность выпуска блоков |
|
зубчатых колес привода автомобилей и тракторов сварными взамен цельных |
|
не вызывает сомнений. Опыт автомобильной промышленности США свидетель |
|
ствует о целесообразности широкого использования сварки блоков зубчатых |
|
колес электронным лучом. Предполагается широкое внедрение поточных и авто |
|
матических линий сварки зубчатых колес электронным лучом в низком вакууме, |
|
В связи с опасностью образования трещин в этом случае для зубчатых |
колес |
следует использовать хорошо сваривающиеся низколегированные стали, |
напри |
мер 15ХГН2ТА.
Для изготовления сложных сварных узлов необходимо выполнять сбороч ные и сварочные операции в сочетании с операциями механической обработки и транспортирования узла с одной позиции на другую. В крупносерийном произ водстве для этой цели используют автоматические линии, оснащенные специаль ным оборудованием. На рис. 60 показана схема такой линии для производства балок заднего моста автомобиля ЗИЛ-130. На стенде I выполняют сборку балок и сварку корневых швов. Последовательность их выполнения показана на рис. 61. Два оператора укладывают штампованные половинки балки (рис. 61, а) в базы транспортирующего устройства на позиции 1 и клиновые вставки на позиции 2. Поданная на позицию 2 балка поднимается до сварочных головок. Поворотные рычаги 3 устанавливают клиновые вставки 2 в вырезы балки 1 (рис. 62). Затем одновременно четыре сварочные головки 4 с двух сторон на вертикальной пло скости сваривают четыре корневых шва по схеме, приведенной на рис. 63, а, после чего подъемный механизм возвращает балку в базы транспортирующего устройства. В процессе передачи балки с позиции 2 (см. рис. 61, б) на позицию 3 она кантуется на 180°, и здесь оставшиеся корневые швы свариваются двумя горелками (см. рис. 61, в и 63, б). На позиции 4 (см. рис. 61, в и а) механическая рука сбрасывает балку в накопитель, откуда оператор с помощью легкого кон сольного крана подает их на стенд II (см. рис. 60) для выполнения второго про хода. В связи с меньшей скоростью сварки второго облицовочного шва на этом участке линии предусмотрены два параллельных стенда. Сварка выполняется на позициях б и 7 в нижнем положении, между позициями балка кантуется на 180°. Схема сварки одновременно двумя головками показана на рис. 64. Затем балки с двух параллельных стендов механической рукой последовательно пода ются на стенд III (см. рис. 60) для автоматической правки под прессом на по зиции 10 с последующим визуальным контролем на позиции 11а. После механи ческой обработки на стенде IV балка поступает на сборочный стенд V. На пози ции 16 в процессе передачи балки с верхнего транспортирующего устройства на нижнее кольцо подается и прижимается снизу, а на позиции 17 крышка укла дывается сверху, и четыре сварочные головки ставят прихватки. При этом по дача кольца и крышки осуществляется механизмами из питателей. Сварка коль цевых швов выполняется на двух параллельных стендах VI, куда с поворотом
машины детали Сварочные
Рве. 60. Схема автоматической линии для производства балок заднего моста автомобиля ЗИЛ-130:
/ —$0 — рабочие места на линии