
книги / Сварка в машиностроении. Т. 3
.pdfных соединений высокопрочных аустенитных сталей и сплавов таким участком является околошовная зона.
Общие закономерности поведения механически неоднородных сварных сое динений при высоких температурах могут быть поняты при анализе особенно стей деформации образца с мягкой прослойкой [6, 14]. При его нагружении со противление пластической деформации зависит не только от свойств металла про слойки, но и от ее размеров, степени неоднородности и компактности сечения. Такое поведение образца определяется тем, что вблизи границы (контакта) метал лов разной прочности пластические деформации мягкого металла сдерживаются более прочным и в прослойке создается объемное напряженное состояние, уве личивающее за счет эффекта контактного упрочнения ее сопротивление дефор-
Рис. 11. Зависимости дли тельной прочности (а) и пла стичности (б) сварных сое динений с мягкими прослой ками
t
мации при одновременном снижении пластичности до разрушения. С уменьше нием относительной толщины (х) прослойки ее прочность растет, а пластичность снижается.
В условиях ползучести длительная прочность и пластичность сварных сое динений с мягкой прослойкой на стадиях внутризеренного и межзеренного разру шения будут разными (рис. 11). В области / вязких внутризеренных разрушений эффект контактного упрочнения реализуется полностью. Линии длительной прочности образцов с разной относительной шириной мягкой прослойки (щ > Ха) дараллельны и расп<?ложены выше кривой для однородного образца со свойст вами мягкой прослойки. Длительная прочность соединения с мягкой прослой
кой (oj£ в) х тем выше, а пластичность (ф**)* тем ниже, чем меньше величина х;
величина (oJJ в)х = о^вКх, где |
в — длительная прочность |
мягкого |
металла} |
|
/Сх — коэффициент контактного упрочнения, равный — |
Н----- ^— для |
случая |
||
осесимметричной деформации. |
4 |
3 |
Зх |
|
|
|
|
|
В области III хрупких межзеренных разрушений, развитие которых свя зано с уровнем максимальных нормальных напряжений, длительная прочность
сварного соединения (oJJ хр) н становится ниже длительной прочности свобод-
ной |
мягкой прослойки |
хр: |
|
„М |
|
|
м |
|
|
|
|
|
J A . х р |
|
|
|
(ад. хр)«- |
И |
|
|
|
|
|
|
где |
Яц — коэффициент, |
равный для |
случая осесимметричной деформации 1 + |
Н----------р (п — показатель ползучести). В предельных случаях это снижение мо-
1 + т
жет достигать 1,5—3 раз. Переход к хрупким разрушениям сопровождается и заметным снижением пластичности. В области II смешанных разрушений дли-
Рис. 12. |
Влияние исходной прочности стали 12Х1МФ на |
||
длительную прочность и |
пластичность сварных |
соедине |
|
ний; T = 580b С; предел |
прочности основного |
металла: |
|
ф — 81 |
к г с / м м а; Д А — 56 к г с / м м 2; □ — 4 8 к г с / м м 2; м е с т о |
р а з р у ш е н и я : Д й — о с н о в н о й м е т а л л ; ф А — м я г к а я п р о с л о й к а
тельная прочность сварных соединений относительно мягкой прослойки посте пенно снижается.
При использовании термически упрочняемых сталей длительная прочность сварных соединений зависит и от уровня прочности основного металла. Ее зави симости для сварных соединений стали 12Х1МФ при трех значениях прочности основного металла (48, 56 и 81 кгс/мм2) приведены на рис. 12. Хотя в период, охваченный испытаниями, наименьшую прочность показали образцы отожжен ного состояния, а наибольшую низкоотпущенные образцы, с повышением вре мени до разрушения кривые сближаются и при экстраполяции на 106 ч сходятся. Характерна весьма низкая пластичность высокопрочных образцов, связанная с хрупкими разрушениями по мягкой прослойке. Поэтому при наличии в таких сварных соединениях концентратора напряжений может наступить их прежде временное разрушение, В отличие от этого отожженные малопрочные образцы
даже при большой длительности разрушаются вязко и нечувствительны к кон центрации напряжений. Для них дополнительных мер по обеспечению плавности сопряжений в районе соединения можно не принимать. Образцы в высокоотпущенном состоянии (средней прочности) занимают промежуточное положение. Для них разрушения в мягкой прослойке начинаются при длительности испыта ния свыше 300 ч при несколько большей пластичности по сравнению с низкоотпущенными образцами.
Одной из наиболее важных характеристик материала как при высоких тем пературах, так и температуре 20° С, является его чувствительность к трещино
|
подобным |
дефектам. |
Значения |
чувстви |
|||
|
тельности |
позволяют обосновать требова |
|||||
|
ния в условиях ползучести к допустимым |
||||||
580 |
дефектам |
в |
сварных |
соединениях. |
Как |
||
560 |
и в условиях |
испытания при температу |
|||||
ре 20° С, могут быть |
использованы |
поло |
|||||
5W |
|||||||
жения механики разрушения с |
примене |
520нием силовых или деформационных кри териев и проведением испытаний на об разцах тех же типов.
На рис. 13 по данным [13] в пара метрической обработке приведены резуль таты испытания при 560° С сварных об
разцов толщиной 18—20 мм стали 12Х1МФ (шов наплавлен электродом Э-09Х1МФ) с естественным надрезом на внецентренное растяжение. Расчетное значение начального коэффициента интенсивности напряжения kql% характеризующего на
Рис. 13. Параметрическая зависи мость kqt — / для сварных швов,
наплавленных электродом типа Э-09Х1МФ:
1 — исходное состояние; 2 — отпуск при 720—740° С
пряженное состояние в вершине трещины, определялось по формулам линейной ме ханики разрушения. При заданных дли тельности работы / и уровне напряжений о глубину трещины I можно кпредварительно определить по формуле"
1 _ _ Ы
Q |
. h |
где Q — безразмерный параметр трещины; kç( определяется из построений /
и / / на рис. 13; С — постоянная, зависящая от формы и размеров данного эле мента и дефекта, а также от характера нагружения.
Используя данные испытаний, обобщенных на рис. 13, можно подсчитать, что в сварном стыке паропровода с толщиной стенки 20 мм*, эксплуатирующемся при 560° С в течение 106 ч, при напряжении а = 6 кгс/мм2 (построение /) допу стимая глубина дефекта без опасности разрушения стыка может быть 2 мм [13]. Термическое состояние стыка после сварки в этом случае не влияет на его надеж ность. При работе в течение 103 ч (построение / /) сравнительно небольшой дефект D неотпущенном стыке может привести к его разрушению. Опыт эксплуатации подтверждает повышенное развитие трещин у стыков хромомолибденованадиевых сталей, не подвергающихся отпуску, именно в первый период эксплуатации.
Для высокотемпературных установок характерны периодические пуски и остановы, во время которых в зонах концентрации возможны дополнительные пластические деформации из-за проявления температурных и компенсационных напряжений. Как показал опыт эксплуатации, это приводит к возникновению
* При расчете элементов е другой толщиной стенки должны использоваться резуль таты испытания образцов близкой толщины.
трещин в указанных участках сварных соединений (у вершин угловых швов в ме стах стыковки труб с разной толщиной стенки, у непроваров, подрезов и других). Такое проявление эффекта малоцикловой усталости при высоких температурах в отличие от комнатной при оценке повреждаемости требует одновременного учета ее накопления за счет механизмов усталости и ползучести.
Для инженерной оценки циклической долговечности сварных соединений при высоких температурах можно использовать [8] схему Мэнсона, в которой исходными характеристиками являются механические свойства и длительная прочность при рабочей температуре, а также частота нагружения. Долговечность определяется по меньшему из двух значений, подсчитанному по правилу 10%:
^ / = 0,1^/
или по формуле, основанной на линейном суммировании повреждений от уста лости и ползучести при некотором условном (эффективном) цикле нагружения:
N,
m - f 0,12 »
m
где Nf — долговечность в условиях ползучести; N f— долговечность при отсут ствии ползучести, определяемая по методу универсальных наклонов; А и m — постоянные для данного материала и условий испытаний, определяемые по кри вой длительной прочности в логарифмических координатах; F — частота нагру жения; k — условный коэффициент, принимаемый обычно равным 0,3.
Проверка указанной схемы на угловых и стыковых соединениях хромомолиб денованадиевых сталей показала, что для относительно быстрых циклов (в усло виях испытания около 5 мин) или при сравнительно невысоких температурах, когда эффект ползучести относительно невелик, с достоверностью можно исполь зовать формулу 10%. Для циклов большой длительности, характерных для ста ционарных установок, расчет по правилу 10% дает завышенные значения долго вечности и в этих случаях нужно использовать формулу суммирования повреж дений.
Стабильность структуры и свойств. Как отмечалось ранее, на жаропрочность влияют структурное состояние металла и его стабильность во времени. По усло вию формирования сварного соединения его различные зоны в исходном состоя нии имеют неравновесную структуру с высокой степенью пересыщенности твер дого раствора и большой плотностью структурных несовершенств. Во время по следующих высокотемпературных выдержек такое структурное состояние явля ется нестабильным и подвержено значительному изменению, сопровождающемуся и существенным изменением свойств. Хотя термическая обработка заметно сни жает степень структурной неравновесности разных зон соединения, она тем не менее не восстанавливает полностью структуру и свойства сварного соединения до уровня свойств основного металла.
Для шва и околошовной зоны сварных соединений, подвергаемых при сварке перегреву, последующая высокотемпературная выдержка по-разному влияет на структуру и свойства. Если сталь не содержит энергичных карбидообразующих элементов, то с увеличением температуры и длительности выдержки твердость участка перегрева постепенно снижается (кривая 1 на рис. 14), что связано с рас падом неравновесной структуры и коагуляцией дисперсных фаз. При наличии в стали таких элементов как ванадий, титан и ниобий, на начальной стадии ста рения твердость растет тем заметнее, чем выше содержание этих элементов (кри вые 2 и 3). Это связано с эффектом твердения за счет выпадения дисперсных кар бидов ванадия из пересыщенного твердого раствора. Дальнейшая выдержка ведет к постепенному снижению твердости, обусловленному эффектом перестариваиия. Чем выше температура выдержки, тем быстрее достигается максимальная твер дость и тем меньше она.
В зависимости от термического режима сварки исходная структура шва и околошовной зоны может заметно меняться. Соответственно и процессы старения этих зон могут развиваться по-
|
разному. На рис. |
15 приведены |
|||||||
|
зависимости |
изменения |
твердо |
||||||
|
сти |
и |
пластичности |
околошов |
|||||
|
ной |
зоны |
сварного соединения |
||||||
|
стали |
15Х2НМФА |
в |
процессе |
|||||
|
старения. Образцы |
перед испы |
|||||||
|
танием нагревали и |
охлаждали |
|||||||
|
по |
режимам |
для |
околошовной |
|||||
|
зоны с получением конечной ее |
||||||||
|
структуры |
в диапазоне от мар |
|||||||
|
тенситной до бейнитно-феррит- |
||||||||
|
ной. Наложение кривых охлаж |
||||||||
|
дения на диаграмму анизотер- |
||||||||
|
мического превращения |
показа |
|||||||
|
ло, что они охватывают все воз |
||||||||
|
можные режимы сварки и на |
||||||||
|
плавки. Для образцов с наибо |
||||||||
|
лее |
равновесной |
структурой |
||||||
|
(бейнитно-ферритной) четко про |
||||||||
Рис. 14. Влияние содержания ванадия в |
является |
эффект |
старения и |
||||||
низколегированной стали на изменение твер |
кривая |
2 |
имеет |
явно выражен |
|||||
дости в околошовной зоне в процессе старе |
ный максимум; |
с |
повышением |
||||||
ния. Содержание ванадия: |
степени неравновесности исход |
||||||||
1 — 0 % ; 2 — 0,17%; 3 - 0,35% |
ной |
структуры эта |
закономер |
||||||
ность нарушается. Кривая / для |
|||||||||
|
|||||||||
|
образца с |
мартенситной струк |
турой имеет два перегиба, являющиеся следствием одновременного протекания двух процессов: распада закалочных структур и дисперсионного твердения. Если
Рис. 15. Сводные параметрические зависимости изменения твердости и чувствительности к трещинам околошовной зоны стали 15Х2НМФА в про цессе старения:
а — твердость; б — критическое раскрытие; исходная структура околошовной зоны: / — мартенсит; 2 — бейннт с ферритом
на кривых старения разных зон сварного соединения отсутствуют пики твердости, а с увеличением температуры и длительности выдержки твердость монотонно
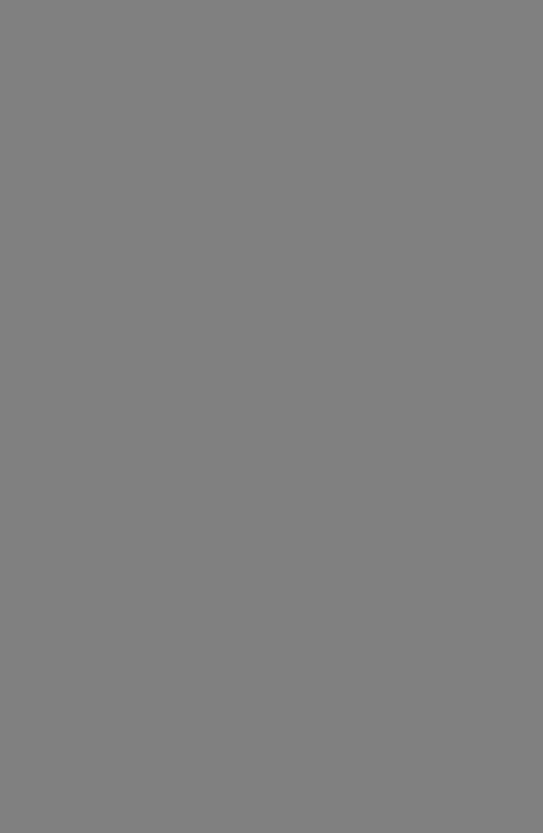
причин отказа в 60-х годах от широкого применения аустенитных паропроводов из стали 12Х18Н10Т. Подобные трещины, возникая при термической обработке при последующих испытаниях или эксплуатации изделия, могут явиться очагами хрупких разрушений.
Склонность к хрупкому разрушению в околошовной зоне наиболее полно мо жет быть выявлена проведением высокотемпературных испытаний сварных образцов на изгиб (рис. 17). В условиях изгиба длительная прочность при 600° С сварного соединения стали 15Х1М1Ф в исходном и недоотпущенном состояниях, когда в наибольшей степени проявляется эффект дисперсного твердения, при мерно на 30% ниже соответствующих значений для основного металла (рис. 17, а). После высокого отпуска, приводящего к перестариванию металла околошовной зоны, длительная прочность повышается и становится близкой к прочности ос новного металла в том же исходном состоянии. Длительная прочность при изгибе
б,кгс/мм2
F 7 -| |
щ |
1 1 I : |
|
щ р |
: z : : |
|
|
w J |
|
|
|
|
|
|
щ |
|
|
■s |
|
|
|
i|_ |
|
|
2 |
^ - |
|
|
1 |
1 |
^ 5 L. |
, |
||
|
= = |
|
* ►. |
|||
— |
|
|
□ |
|
|
|
|
|
^5 |
|
|
||
= |
— = |
|
— |
|
— |
5 |
д,кгс/мм2
Рис. 17. Зависимости дли тельной прочности при испы таниях сварных образцов на изгиб:
а — плоские |
образцы |
15Х1М1Ф: |
состояние после |
# — исходное |
|
сварки; |
|
▲— недоотпуск при 680° С;
?— отпуск при 730° С;
—трубчатые образцы стали 12Х18Н10Т:
О — растяжение; сварные об разцы: Д — растяжение;
А — изгиб
сварных соединений аустенитной стали 12Х18Н10Т (рис. 17, б) также заметно снижается. В условиях растяжения длительная прочность сварных соединений близка к прочности основного металла и разрушений в околошовной зоне, харак терных для эксплуатации, не происходит.
Количественно оценить вероятность хрупких разрушений можно в условиях испытания по методике ЦКТИ [4] сварных образцов на изгиб с постоянной ско ростью деформации. За показатель склонности против хрупких разрушений при нимают относительное удлинение наружного волокна до появления трещины. Для приближенной оценки склонности сварных соединений к хрупким разруше ниям в околошовной зоне можно использовать различные технологические пробы и в первую очередь тавровую [2] и стыковую пробу Л КЗ [4].
Проведенные по методике ЦКТИ испытания позволили четко разделить свар ные соединения по склонности к хрупким разрушениям в околошовной зоне и оценить влияние на нее различных факторов. Наблюдаемая при этом разница в дли тельной пластичности может достигать одного-двух порядков. Так, сварные сое динения стали 15Х1М1ФЛ (рис. 18, а) при высокой прочности основного металла разрушаются в исходном и недоотпущенном состояниях практически бездеформационно ( 0 = 0,1 -н 1,0%). Проведение для них высокого отпуска, который снимает эффект дйсперсного твердения и уменьшает прочность основного металла,
заметно повышает пластичность до 12—20%. Хотя и в этом случае разрушения концентрируются в околошовной зоне, они сопровождаются значительной дефор мацией, что заметно уменьшает вероятность хрупких разрушений.
Высокой склонностью к хрупким разрушениям в исходном и. стабилизирован ном состояниях обладают сварные соединения стали типа 12Х1.8Н10Т, легирован ной титаном (рис. 18, б). Лишь аустенизация, снимая эффект дисперсионного твердения, обусловливает повышение пластичности сварного соединения до уровня основного металла.
С ростом жаропрочности аустенитной стали, достигаемым обычно дополни тельным легированием ее титаном, ниобием и алюминием, склонность сварных
соединений |
к |
хрупким |
раз |
|
||||
рушениям |
в |
околошовной |
|
|||||
зоне |
заметно |
возрастает. |
|
|||||
Особенно велика она в свар |
|
|||||||
ных |
соединениях |
высокожа |
|
|||||
ропрочных |
сплавов |
на нике |
|
|||||
левой основе |
[4]. |
|
|
|
|
|||
|
Одним из основных фак |
|
||||||
торов, |
определяющих |
жаро |
6,% |
|||||
прочность |
сварных |
соедине |
||||||
ний |
аустенитных |
сталей, яв |
|
|||||
ляется охрупчивание их швов |
10 |
|||||||
при |
|
высокотемпературных |
||||||
Рис. |
18. Изменение длитель |
8 |
||||||
|
||||||||
ной |
пластичности |
сварных |
|
|||||
соединений, склонных к хруп |
|
|||||||
ким |
разрушениям |
в |
около |
|
||||
шовной |
зоне. |
Испытания на |
|
|||||
изгиб |
по |
методике |
ЦКТИ: |
|
а — сталь 15Х1М1ФЛ: ф — ис ходное состояние; ■ — недоотпуск при 630° С; А — высокий отпуск при 730° С;
б — сталь 12X18Н10Т; ф — ис ходное состояние; ■ — стаби лизация при 800° С; А — аусте низация при 1150° С;
---------------- основной металл
V -
500 700 900 Tt°C
S )
выдержках. В зависимости от фазового состава шва и его легирования оно может иметь разную природу.
Охрупчивание наиболее распространенных аустенито-ферритных, а также феррито-аустенитных и ферритных швов связано прежде всего с нестабильностью ферритной фазы при высоких температурах. Ответственными за него в данном слу чае являются механизмы 475-градусной хрупкости и ô -охрупчивания. Тонкое распределение ферритной фазы в сварных швах ускоряет процессы распада фер ритной фазы.
По данным испытания на ударную вязкость металла аустенитных и аустенито ферритных швов (рис. 19) выявляются две области их высокотемпературного охруп чивания. Первая из них, расположенная в интервале 300— 500° С, начинает про являться, если содержание ферритной фазы в структуре шва превышает 8— 10%. Увеличение его до 20% приводит уже к резкому падению ударной вязкости даже после относительно кратковременных выдержек в этом интервале температур и может проявляться в появлении трещин в корневых слоях многослойного шва непосредственно во время сварки. Ответственным за охрупчивание в этом интер вале температур является механизм 475-градусиой хрупкости, приводящий к структурным изменениям в первую очередь на границе раздела аустенитной и
ферритной фаз. Хрупкость такого рода в зависимости от содержания феррита в структуре сохраняется до 200—500° С. Она устраняется относительно кратко временным нагревом при 550° С и выше.
В области температур 550—850° С аустенито-ферритные швы подвержены охрупчиванию вследствие образования при этих температурах в участках феррита хрупких интерметаллидных соединений типа a-фазы. Оно сопровождается сниже нием не только вязкости, но и пластичности при комнатной и повышенных тем пературах и проявляется уже при содержании феррита свыше 4— 5% . Повышение стойкости против о-охрупчивания аустенито-ферритных швов достигается прове дением их аустенизации при температурах выше 900—950° С, способствующей более благоприятному распределению ферритной фазы в виде округлых участков.
Рис. 19. Ударная вязкость аустенитного и аустенито-феррит ных швов при 20° С после выдержки в интервале температур 20— 1000° С длительностью 10 ч; содержание феррита:
|
/ - |
0%; 2 - |
4%; 3 — 8%; 4 - |
20% |
|
|
|
По данным исследований [4] по условию |
а-охрупчивания |
сварные соедине |
|||||
ния с |
аустенито-ферритными швами, наплавленными |
электродами |
ти |
||||
пов Э-09Х19Н11ГЗМ2Ф и Э-08Х19Н10Г2Б с |
ограниченным |
содержанием |
фер |
||||
ритной |
фазы, |
могут эксплуатироваться |
до |
10б ч при температуре не |
выше |
||
600° С. Повышение ее до 650° С может быть допущено лишь |
после проведения |
||||||
аустенизации |
сварного |
соединения. |
|
|
18— 19% заметно |
||
Однофазные аустенитные швы с содержанием хрома до |
более стабильны при высоких температурах. При большем содержании хрома, как, например, для электродов типа Э-10Х25Н13Г2, наблюдается интенсивное о-охрупчивание и при однофазном составе аустенитного шва. В высоконикеле вых сварных швах при содержании молибдена выше 14% в процессе старения при температурах выше 700° С проявляется охрупчивание, обусловленное выде лением частиц р-фазы [4].
Пути повышения жаропрочности сварных соединений. Эксплуатационная надежность сварных узлов при высоких температурах зависит от комплекса свойств жаропрочности и определяется выбором материала изделия, степенью неоднород ности сварных соединений, конструктивными формами и условиями работы. Особое внимание должно уделяться опасности хрупких разрушений, развитие
которых является основной причиной преждевременного выхода высокотемпера турных узлов из строя.
Для рассматриваемых сварных конструкций необходимо выбирать стали с учетом условий работы изделия в соответствии с правилами Госгортехнадзора CGCP, стандартами на изделия и нормами расчета. Предпочтение должно быть отдано материалам, обладающим лучшей технологичностью при сварке, обеспе чивающим максимальную однородность сварных соединений при отсутствии в них разупрочненных и хрупких зон и склонности к образованию трещин при термической обработке и эксплуатации.
О го |
150 |
300 |
350 |
m |
450 |
500 |
550 600 650т,°с |
|||
Рис. 20. Зависимость номинальных допускаемых |
||||||||||
напряжений от рабочей температуры |
|
для материа |
||||||||
лов стационарных |
энергетических |
установок |
[1]: |
|||||||
1 — сталь 10; |
2 — сталь |
СтЗ; |
3 — сталь |
20 (20К); |
4 — |
|||||
16ГС (09Г2С); |
5 — 15ХМ; |
6 — 12Х1МФ; |
7 — 16ГНМ: |
|||||||
8 — 12Х11В2МФ; |
9 — 15Х1М1Ф; |
10 — 12Х18Н10Т |
|
|||||||
По температурным условиям работы целесообразно выделить две группы |
||||||||||
высокотемпературных конструкций: |
1) |
работающих |
при повышенных темпера |
|||||||
турах (до 350— 400° С для |
перлитных |
и 500° G для |
аустенитных сталей), когда |
эффектом ползучести можно пренебречь; 2) работающих при более высоких тем пературах в условиях ползучести.
Допустимые напряжения для наиболее распространенных свариваемых ста лей в стационарных энергетических установках приведены на рис. 20. Перегибы кривых связаны с переходом от расчета по пределу текучести (для первой группы конструкций) к расчету по пределу длительной прочности за 105 ч.
Для первой группы сварных узлов, к которым принадлежат такие ответствен ные конструкции, как атомные энергетические установки, барабаны паровых кот лов и сосуды нефтехимических установок, выбор материалов подчиняется общим конструктивно-технологическим требованиям. Стали, обычно используемые для сварных узлов, работающих в нормальном диапазоне температур, можно при менять и в данном случае. Исключение составляют стали, чувствительные к де