
книги / Сварка в машиностроении. Т. 3
.pdfДля предотвращения опасности хрупкого разрушения и уменьшения техно логических трудностей при изготовлении весьма толстостенных сосудов (200— 400 мм) наиболее целесообразно изготовлять их многослойными — навивкой на основную обечайку толщиной 20— 40 мм требуемого числа слоев рулонной стали толщиной 4—8 мм (рис. 32). В зависимости от рабочей среды центральная обе чайка может быть двухслойной или из коррозионно-стойкой стали, а слои наруж ной части корпуса — из низколегированной стали.
Линия для изготовления многослойных рулонированных обечаек диаметром до 5 м на Уралхиммаше состоит из разматывателя рулона, подающих вальцев правильной машины, машины для обрезки и сварки концов полосы, отклоняю щих валков и машины для намотки обечаек. После закрепления конца навитой полосы и сварки облицовочной обечайки торцы многослойной обечайки прота чивают и подвергают наплавке слоем толщиной не менее 10 мм, который механи чески обрабатывают для получения требуемой формы разделки кромок. Кольце вые швы между обечайками, а также между обечайкой и днищем или фланцем выполняют многослойными. Кромки монолитных днищ и фланцев также иногда подвергают предварительной наплавке с целью исключения необходимости тер мической обработки после выполнения кольцевых швов. Сварочные напряжения в этих швах в значительной степени снимаются при обязательном приемочном испытании готового сосуда в результате нагружения внутренним давлением, превышающим рабочее.
СВАРНЫЕ ТРУБЫ
Трубы для магистральных трубопроводов выполняют дуговой сваркой под флюсом; шов располагают либо по образующей, либо по спирали. Из-за ограни ченной ширины листов прямошовные трубы диаметром до 820 мм сваривают одним продольным швом, а при диаметре более 820 мм — двумя. Листы проходят обра ботку кромки и формовку. Листоукладчик по одному подает листы на рольганг,
Рис. 33. Схема выполнения наружного шва трубы на стане проходного типа
направляющий их на строгальный станок. Одновременная обработка обеих кро мок листа до проектного размера со снятием фасок происходит при движении листа через станок. Формовку выполняют либо в формовочном стане, либо в по точной линии на трех рабочих местах, где сначала в валковом стане осущест вляют подгибку кромок, а затем осуществляют предварительную гибочную и окончательную формовочную операции на двух прессах.
На Челябинском трубопрокатном заводе сварку прямошовных труб выпол няют с двух сторон, причем наружный шов укладывают первым на стане про ходного типа (рис. 33). При подаче в стан трубная заготовка надвигается на оправку 7, подвешенную к направляющему ножу 4 и опирающуюся роликами на внутреннюю поверхность трубы 2. Движение трубы через стан со сварочной скоростью обеспечивается приводными горизонтальными валками стана, причем зазор между кромками по мере продвижения заготовки постепенно устраняется за счет бокового давления вертикальных неприводных валков; в зоне сварки
зазор отсутствует. Вытекание сварочной ванны предотвращается установленным на раме оправки 1 гусеничным башмаком 3. Сварка под флюсом производится двумя дугами, горящими в одной сварочной ванне, что обеспечивает хорошее
формирование шва при скорости сварки |
170— |
190 м/ч для стенок толщиной 7 мм |
и 115— 135 м/ч для стенок толщиной |
12 мм. |
|
Трубы с двумя продольными швами собирают из двух предварительно от формованных корыт, подаваемых укладчиком на две параллельные нитки вход ных рольгангов сборочного устройства. Выравнивающим приспособлением кромки заготовок устанавливают в одной горизонтальной плоскости, и в таком положении корыта рольгангами подаются в раскрытое сборочное устройство (рис. 34, а). Штоки 1 пневмоцилиндров (рис. 34, б), поворачивая рычаги 2, устанавливают заготовки в исходное для подачи в сварочный стан положение, образуя цилин дрическую трубу с вертикальным разъемом, задаваемым деталями 3 и 4. Собран ная труба подается в сварочный стан упором цепного заталкивателя. При этом направляющий нож непрерывного стана для выполнения первого наружного шва
Рис. 34. Устройство для сборки трубы из двух корыт
попадает в зазор между верхними кромками корыт, направляя стык под свароч ную головку. Сваренная первым наружным швом заготовка поворачивается разъемом вверх и по рольгангу поступает на стан для сварки второго наружного шва. Последовательно один за другим выполняют и оба внутренних шва. Приемы их выполнения такие же, как и для труб с одним швом, Для обеспечения требуемой формы поперечного сечения и допуска на диаметр трубы с прямым швом подвер гают правке. Трубу заключают в толстостенную матрицу и уплотняют конус ными заглушками по концам. Внутренним гидравлическим давлением создается раздача трубы до 1,0— 1,2%, чем достигается правка трубы по всей длине и ка либровка по диаметру.
Технология изготовления прямошовных труб диаметром 1220— 1620 мм на Харцызском трубном заводе отличается от изложенной выше как порядком вы полнения швов, так и приемами калибровки труб. Сборка трубы из двух полуцилиндрических заготовок завершается наложением технологического шва либо в среде С 02 одновременно шестью головками, либо сваркой ТВЧ. Под флюсом сначала выполняют внутренние швы, а затем наружные. Для автоматического направления электродов по стыку используют риски, нанесенные параллельно кромкам при их строгании. Калибровку труб осуществляют гидромеханическим экспандером путем последовательной раздачи по всей длине. Для этого трубу шагами надвигают на калибровочную головку экспандера. При неподвижной трубе шток силового цилиндра перемещает центральный граненый клин и раздви гает рабочие сегменты, обеспечивая раздачу участка трубы до заданного диа метра.
На трубных заводах фирмы Маннесман (ФРГ) используют листы большой ширины, что позволяет выпускать трубы диаметром 1420 мм с одним продольным швом.
Сборка и сварка труб из рулонной стали спиральным швом позволяет полу чать трубы любого диаметра независимо от ширины полосы. При использовании такого метода процесс изготовления осуществляется непрерывно, обеспечивая требуемую точность размера и формы труб без последующей калибровки. Схема стана [8J приведена на рис. 35. Полоса из рулона накапливается в компенсацион ной петле, обеспечивая непрерывность выполнения спирального шва при обрезке концов полос гильотинными ножницами, а также сборке и сварке их стыка. Спи ральный шов выполняют сваркой под флюсом тремя сварочными головками. Две из них крепятся на общей штанге, вводимой внутрь трубы, третья головка расположена снаружи. Первый внутренний шов, приваривающий кромку полосы к сформованной трубе, имеет малое сечение и является технологическим. Его назначение — устранить возможность взаимного перемещения кромок и предот вратить вытекание сварочной ванны при выполнении наружного рабочего шва. Такая технология позволяет гарантировать отсутствие кристаллизационных тре щин при сварке низколегированных сталей на скоростях до ПО м/ч. По сравне нию с изложенным выше процесс изготовления спиральношовных труб диаметром 530— 1420 мм на станах Волжского трубного завода является более совершенным. Фрезерование продольных кромок после обрезки их на дисковых ножницах,
Рис. 35. Схема стана для изготовления труб из ленты спиральным швом
более совершенное формующее устройство по принципу трехвалковых гибочных вальцев в виде обойм роликов и автоматическое поддержание требуемого зазора между кромкой полосы и кромкой сформованной трубы обеспечивают сборку и сварку стыка практически без смещения кромок. В процессе выполнения спи рального шва осуществляется непрерывный контроль ультразвуком с автомати ческой маркировкой мест обнаруженных дефектов. Летучая установка, обеспечи вающая механизацию обрезки, сборки и сварки концов полос, позволила обойтись без компенсационной петли. Схема такого агрегата, объединяющего гильотинные ножницы /, сварочную установку II с калибровочными ножницами и суппорт III, показана на рис. 36, а и б. Концы полос 1 и 2 последовательно обрезаются ножни цами / и закрепляются прижимами калибровочных ножниц II (рис. 36, а). После выполнения калибровочного реза обоих концов сразу, передвижением суппорта до упора (рис. 36, б), задний конец полосы I устанавливается по оси канавки под кладки сварочной установки. Перемещением до упора гильотинных ножниц передний конец полосы 2 подается в сварочную установку с обеспечением требуе мого зазора в стыке, концы полос зажимаются и производится сварка. При выпол нении этих операций агрегат движется вместе с полосой У, а затем отпускает ее и возвращается в исходное положение.
При увеличении диаметра магистральных трубопроводов требуется одновре менное увеличение толщины стенки. Так как толщина полос рулонной стали не превышает 14 мм, то при диаметре 1420 мм и более трубы со спиральным швом приходится изготовлять из листовой стали. Непрерывный процесс изготовления спиральношовных труб диаметром до 2500 мм из отдельных листов осуществляется в специальном стане Волжского трубного завода. В этом стане листы предва рительно попарно собирают и сваривают встык на неподвижной установке, а за тем рольгангом подают в «летучую» установку, где укрупненная карта пристыко
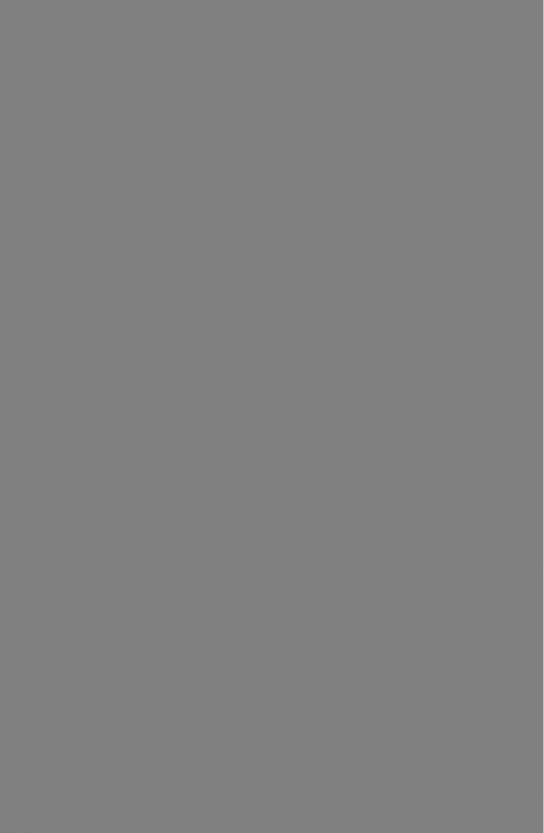
В последние годы для изготовления труб диаметром от 8 до 529 мм и более с толщиной стенки 0,3— 10 мм все шире используют сварку ТВЧ. По сравнению с контактной сваркой сопротивлением на токах промышленной частоты высоко частотная сварка обеспечивает значительно более высокие скорости (до 120 м/мин и более), возможность изготовления труб из сталей, цветных металлов и сплавов, использование горячекатаной нетравленой ленты, значительное умень шение удельного расхода электроэнергии на 1 т готовых труб. Кроме того, при высокочастотной сварке одно и то же оборудование можно использовать для изготовления труб из разных материалов, изменяя только электрические и ско ростные параметры процесса.
Рис. 38. Схемы высокочастотной сварки труб
При контактном подводе тока (рис. 38, а) необходимость смены контактов / вследствие их износа заставляет периодически останавливать стан. Поэтому все шире используют подвод энергии кольцевым индуктором (рис. 38, б). В этом слу чае для уменьшения потерь энергии в результате прохождения тока по заго товке в трубу вводят магнитный сердечник, который изменяет сопротивление так, что почти весь сварочный ток направляется по свариваемым кромкам [8].
Дуговую сварку в инертном газе вольфрамовым электродом применяют для изготовления труб с прямым швом диаметром 6— 426 мм с толщиной стенки 0,2— 5 мм и специальных труб со спиральным швом диаметром до 2000 мм и толщиной стенки до 10 мм. Материал труб может быть разный, однако скорость сварки неве лика (до 1,5—2,0 м/мин).
ТРУБОПРОВОДЫ
Укладка трубопроводов может быть либо непрерывная, либо секционная. В СССР на строительстве магистральных трубопроводов применяют главным образом секционный способ укладки труб. Трубы длиной 12 м, поступающие на полевые сварочные базы, соединяют в секции, транспортируют на трассу и наращи вают в нитку.
При сборке и сварке секций на полевых базах используют механизированные линии (рис. 39). Трубы с накопителя 1 поочередно манипулятором укладывают на рольганг 3. Сборку выполняют с помощью гидравлического внутреннего цен тратора 2, закрепленного штангой и используемого в качестве вращателя. Пер вая труба рольгангом 3 надвигается на центратор и фиксируется первым рядом жимков центратора. Вторая труба подается рольгангом до соприкосновения с пер вой и фиксируется разжатием второго ряда жимков. Используя центратор как вращатель, два сварщика одновременно выполняют корневой шов полуавтоматами в среде углекислого газа или ручной дуговой сваркой. После сварки первого слоя двухтрубная секция отводится рольгангом вперед, на ее место на центратор надвигается третья труба, и цикл сборки и сварки первого слоя повторяется. Со бранная трехтрубная секция перегружателем передается на промежуточный стеллаж 4, затем на второй стенд 6, где стыки окончательно сваривают автоматами под флюсом с помощью торцового вращателя 5,
Увеличение диаметра труб до 1420 мм и толщины стенки до 17 мм потребовало замены односторонней сварки поворотных стыков двусторонней. Такой процесс осуществляют на механизированных линиях типа БТС. Торцы труб подвергают механической обработке с одновременным нанесением риски на внутреннюю по верхность для автоматического направления внутренней сварочной головки по
Рис. 39. Схема механизированной линии для сварки поворотных стыков труб
стыку «Сборку выполняют с помощью центратора, вращение обеспечивается попе речными роликами стенда. Сначала выполняют первый наружный шов, затем од новременно второй наружный и внутренний швы.
Выполнение неповоротных стыков магистральных трубопроводов большого диаметра продолжает оставаться весьма трудоемким. Использование трубоуклад чиков и внутренних гидравлических центраторов обеспечивает механизаций) процесса сборки, однако сварку по-прежнему выполняют вручную поточно-рас члененным методом. Одновременно работают звено сборщиков и несколько звеньев
Рис. 40. Схема сборки и сварки магистрального трубопровода с помощью внутритрубной машины:
/ |
— трактор с подъемной стрелой; 2 — внутритрубиая сварочная машина; |
3 — штанга; |
||
4 |
— трубоукладчик; |
5 — передвижная электростанция; 6 — трактор с |
подъемником; |
|
7 |
_ подвесная машина для зачистки внутренних поверхностей |
труб под контакты; 8 — |
||
кабель-удлинитель; |
9 — кабель; /0 — штепсельный разъем; // |
— наружный грато^ни- |
||
матель и индуктор для термической обработки стыков |
|
|
сварщиков. Впереди движется звено сборщиков, собирая стыки с помощью вну треннего центратора. За ними от стыка к стыку каждое звено сварщиков выпол няет свой слой шва, а каждый сварщик — определенный участок этого слоя.
В ИЭС им. Е. О. Патона создана внутритрубиая машина для сборки и сварки магистральных трубопроводов диаметром 720— 1420 мм [12]. Внутритрубный центратор с двумя распорными патронами обеспечивает передачу усилия осадки при сварке. С помощью внутреннего кольцевого сварочного трансформатора осу ществляется процесс контактной сварки оплавлением автоматически по заданной программе. Схема сборки и сварки магистрального трубопровода с использова нием внутритрубной машины приведена на рис. 40. Производительность агрегата
составляет шесть стыков в час. Широкое использование таких машин, по-видимому, позволит обеспечить комплексную механизацию всего цикла сборочно-сварочных работ при укладке магистральных трубопроводов большого диаметра.
При укладке трубопроводов диаметром 114—529 мм используют оборудова ние для контактной сварки стыков труб с внешним кольцевым трансформатором (установки ТКУС и ТКУП). Стационарная установка ТКУС имеет неразъемную сборочно-сварочную головку. Передвижная установка ТКУП, используемая для сварки стыков на трассе, имеет разъемную сварочную головку, подвешиваемую на стреле специального трактора.
Огромное число стыков труб приходится выполнять при сооружении заводов нефтяного, химического, металлургического и атомного машиностроения. Сборку и сварку большинства этих стыков выполняют в трубозаготовительных цехах,
ана монтаже сваривают только стыки, соединяющие готовые секции или узлы.
Вкрупных трубозаготовительных цехах при выпуске больших партий узлов одинаковых размеров используют специализированные установки дуговой авто матической сварки, а также применяют контактную сварку встык. Неповоротные монтажные стыки заводских трубопроводов сваривают вручную или специаль ными автоматами в среде защитных газов. Использование автоматических головок, обегающих стык, особенно необходимо в труднодоступных местах.
КОРПУСНЫЕ ЛИСТОВЫЕ КОНСТРУКЦИИ
Представителями конструкций этого типа являются кузова цельнометалличес ких вагонов, корпуса судов и автомобилей. Общим для них является использо вание плоских и криволинейных листовых элементов с последующим объединением их в жесткую пространственную конструкцию, способную воспринимать разно образные нагрузки.
Рис. 41. Стенд для сборки и сварки плоских узлов вагона
При изготовлении кузовов пассажирских вагонов преимущественно исполь зуют контактную сварку — шовную и точечную. Общей сборке предшествуют сборка и сварка крупногабаритных узлов: крыши, боковых стен, настила пола, концевых и тамбурных стен. Плоские узлы вагона обычно изготовляют из тонких стальных листов толщиной 2—4 мм и гнутых профилей зетобразного, уголкового и омегообразного сечений. Сборку и сварку их осуществляют на специальных стендах (рис. 41). Обшивку укладывают по фиксаторам на один из стендов 2, обслуживаемых соответствующей портальной сборочной скобой-кассетой 4. Скобу по рельсовому пути передвигают над стендом из одного фиксированного положе ния в другое, задавая расположение элементов жесткости и обеспечивая их при жатие к обшивке с созданием предварительного прогиба под сварку перед поста новкой прихваток. Сварку обшивки с элементами жесткости выполняют с по мощью портальной трехэлектродной контактной машины 1 с двусторонним под водом тока. Для этого собранный узел приподнимают над поверхностью стенда подъемными опорами 3, которые затем попарно опускаются, пропуская сварочную
машину. По мере продвижения машины вдоль стенда попарно выполняют точки, приваривающие продольные элементы жесткости. Приварку элементов другого направления осуществляют поперечным перемещением сварочных головок. Сва рочная машина 1 обслуживает оба стенда 2. При работе ее на одном из них на дру гом собирают следующий элемент с помощью другой скобы-кассеты.
Крыша вагона представляет собой корытообразную конструкцию с элемен тами жесткости зетового сечения. Сборку и сварку крыши производят целиком или из отдельных секций. Схема поточной линии для изготовления секций крыши элек тровагона показана на рис. 42. Полотнище обшивки секции собирают на столе 3 стенда, где по фиксаторам укладывают средний лист 2 и два листа 1 округлений. Нахлесточное соединение листов сваривают дуговой сваркой, для прижатия ли стов и направления сварочной головки вдоль шва используют самоходный пор тал 4. Сборку секций выполняют в стапеле 5. Дуги крыши укладывают на мед ные шины дуг стапеля, сверху накладывают полотнище обшивки, приварку ее выполняют специальной контактной машиной 6 портального типа.
При постройке судов общей сборке корпуса на стапеле предшествуют сборка и сварка элементов, секций и блоков. Большинство сборочных элементов состоит
Рис. 42. Схема поточной линии для изготовления секций крыши электровагона
из листовых деталей, балок и рам. При сборке и сварке листовых полотнищ ис пользуют специальные стенды. При изготовлении плоскостных секций применяют способ раздельной сборки и сварки набора. На полотнище первым устанавливают набор главного направления и приваривают его угловыми швами автоматической сваркой. Затем устанавливают набор другого направления, приваривают его к полотнищу и в последнюю очередь сваривают элементы набора друг с другом.
Для сборки секций с погибыо используют постели, образуемые набором лекал, закрепленных на жестком основании и воспроизводящих обводы изготов ляемой секции. Постели применяют специализированные— для секции одного типоразмера и универсальные, переналаживаемые.
Наиболее перспективным методом общей сборки корпуса судна является блоч ный, когда сборку на стапеле осуществляют из крупных блоков, представляющих собой часть корпуса от киля до палубы. Схема организации работ при использо вании такого метода показана на рис. 43. Корпус каждого блока формируют ца предстапельном участке из секций, подаваемых из сборочно-сварочного цеха. Днищевые секции устанавливают на поперечные балки. При этом средняя часть с колеей для транспортных тележек грузоподъемностью 500 т и монтажных те лежек грузоподъемностью 100 т остается свободной. Центровку и стыковку дни щевых секций производят с помощью монтажных тележек. По окончании форми рования блоков производят испытания отсеков на непроницаемость. С горизон тальной предстапелыюй площадки готовые блоки с помощью двух 500-тонных транспортных тележек перемещают на трансбордер, который передвигается по трансбордерной горке. После совмещения рельсовых путей трансбордера и на клонного стапеля блок на транспортных тележках спускают по наклонному ста пелю до места установки. Под концы судоводных балок блока подводят центри рующие устройства, расположенные на спусковых дорожках стапеля, блок сни мают с транспортных тележек и возвращают их на предстапельную площадку для перевозки очередного блока. Так как монтажные стыки между блоками имеют
большую протяженность, то для равномерного поперечного укорочения по пери метру их выполняют одновременно несколько сварщиков.
При изготовлении крупнотоннажных судов сборку и сварку корпусов иногда выполняют на плаву. После спуска двух частей на воду точную их стыковку обес печивают балластировкой. Затем под корпус подводят специальный кессон, пов торяющий обводы судна в зоне стыка и имеющий уплотнения. Из пространства, ограниченного кессоном и корпусом, откачивают воду и после удаления влаги и очистки кромок производят сварку стыка с последующей его окраской. При про изводстве судовых корпусных конструкций сварочные деформации часто оказы ваются выше допустимых; их устраняют главным образом правкой с помощью местного нагрева.
Рис. 43. Схема блочного метода сборки корпуса судна
Кузова автомобилей собирают и сваривают из заготовок, штампованных из листа. Такой метод обеспечивает требуемую точность размеров и формы заго товок под сварку внахлестку и по отбортовке, позволяя создавать технологичные детали малой массы при заданной жесткости. В условиях крупносерийного про изводства сборку и сварку кузовов легковых автомобилей выполняют в автома тических линиях, представляющих собой сложный комплекс транспортирующих устройств и многоточечных машин, работающих в едином цикле. На рис. 44 показано расположение линий сборки и сварки боковых стенок на ВАЗе. На стол 1 (рис. 45) многоточечной машины, расположенной в начале линии, штампованные заготовки укладывает рабочий; остальные операции выполняются автоматически. Сварочные пистолеты и клещи, закрепленные на кронштейнах 2, подводятся к заготовкам гидроцилиндрами 3 и после сварки возвращаются в исходное поло жение. Гидроподъемник 4 приподнимает собранный узел до уровня расположения транспортного устройства, которое захватывает его и передает на следующие сва рочные позиции линии. Сваренные боковины поступают в конце линии на меха низмы перегрузки 1 (см. рис. 44), где они из горизонтального положения пере водятся в вертикальное и подаются на напольный конвейер 2, транспортирующий их к месту комплектации 4. Рядом с напольным конвейером расположены нако пители 3 для хранения готовых боковин. Подача с напольного конвейера в нако пители и обратно происходит автоматически. К месту комплектации поступают правая и левая боковины, а также крыша. Комплектация их осуществляется с помощью опускной секции толкающего конвейера 2 (рис. 46) с подвеской 7. Навешивание боковин на выступы 5 выполняют поворотом рычагов 3. Крыша подается горизонтально и подхватывается крюками 4. Скомпонованная таким образом «виноградная гроздь» подъемной секцией поднимается, захватывается выступом тяговой цепи толкающего конвейера и автоматически адресуется к месту
Оевая боковина —
з\ Г Т П Г Т Г П г-
х ::г
цR II
Правая боковина —
Рис. 44. Схема автоматической линии сборки и сварки боко вых стенок кузовов автомобилей на ВАЗе
Рис. 46. Схема комплектации кузова в опускной Се кающего подвесного конвейера екцни тол-