
книги / Строительные материалы
..pdfТехническим показателем пластичности является чис ло пластичности
П л = №т — Г р, |
(3.2) |
где WT и Wp — значения влажности, соответствующие пределу теку чести и пределу раскатывания глиняного жгута, % (рис. 3.3).
Для производства строительных керамических изде
лий обычно |
применяют умеренно пластичные глины с |
числом пластичности Пл = 7—15. Малопластичные гли |
|
ны с Пл<7 |
плохо формуются, а высокопластичные гли |
ны с П л > 15 растрескиваются при сушке и требуют отощения.
Связующая способность глины проявляется в связы вании зерен непластичных материалов (песка, шамота, и др.), а также в образовании при высыхании достаточ но прочного изделия — сырца. Связующую способность глиняных строительных растворов используют при клад ке печей, труб.
2. Отвердевание глины при высыхании и усадка
Особенность глиняного теста — в способности отвер девать при высыхании на воздухе. Прочность высушен ной глины обусловлена действием ван-дер-ваальсовых сил и цементацией зерен минералов ионами примесей. Силы капиллярного давления стягивают частицы глины, препятствуют их разъединению, вследствие этого проис ходит воздушная усадка. При насыщении водой мениски исчезают, прекращается действие капиллярных сил, час тицы свободно перемещаются в избытке воды, и глина
размокает.
Усадка — это уменьшение линейных размеров и объе ма глиняного сырца при его сушке (воздушная усадка) и обжиге (огневая усадка) глин. Усадку выражают в процентах от первоначального размера изделия.
Для различных глин линейная воздушная усадка ко леблется от 2—3 до 10—12 % в зависимости от содер жания тонких фракций. Для уменьшения усадочных на пряжений к Жирным глинам добавляют отощители. По верхностно-активные вещества (СДБ и др.), введенные в глиняную Масу в количестве 0,05—0,2%, улучшают смачивание частиц глины водой, позволяя сократить формовочную влажность и снизить воздушную усадку.
Огневая усадка получается из-за того, что в процессе обжига легкоплавкие составляющие глины расплавля
ются, и частицы глины в местах их контакта сближают ся. Огневая усадка может составлять 2—8 % в зависи мости от вида глины.
Полная усадка, равная алгебраической сумме воз душной и огневой усадок, колеблется от 5 до 18 %• Со ответственно увеличивают размеры форм, чтобы полу чить готовое изделие необходимых размеров.
3. Переход глины при обжиге
вкамневидное состояние
Впроцессе высокотемпературного обжига глина пре терпевает физико-химические изменения. Сначала ис паряется свободная вода, затем выгорают органичес кие вещества. При температуре 700—800 °С происходит разложение безводного метакаолинита Al20 3*2Si02, ко торый образовался ранее (при 450—600°С) вследствие дегидратации каолинита; затем АЬ03 и SiCb при повыше
нии температуры (до 900 °С и выше) вновь соединяются, образуя искусственный минерал — муллит 3Al20 3-2Si02. Муллит придает обожженному керамическому изделию водостойкость, прочность, термическую стойкость. С его образованием глина необратимо переходит в камневид ное состояние. Вместе с образованием муллита расплав ляются легкоплавкие составляющие глины, цементируя и упрочняя материал.
Обжиг кирпича и других пористых изделий обычно заканчивается при 950—1000 °С. Дальнейшее повышение температуры резко интенсифицирует образование и на копление жидкой фазы — силикатного расплава, кото рый не только цементирует частицы глины, но и уплот няет керамический материал. В результате получают изделия с плотным керамическим черепком, отличаю щимся малым водопоглощением (менее 5 %)•
Кварц присутствует в глине в виде кварцевого песка, его добавляют для отощения высокопластичных глин. Кварц претерпевает полиморфные превращения, сопро вождающиеся объемными изменениями. Наиболее часто встречающийся в природе p-кварц при 573 °С обратимо переходит в а-кварц с увеличением объема на 0,82%; эта форма устойчива до 1050 °С. Поэтому при охлажде нии керамических изделий, обожженных до 1050 °С, а-кварц снова переходит в p-кварц с соответствующим уменьшением в объеме. При температуре выше 1050 °С
а-кварц переходит в а-кристобалит, который, в свою очередь, в интервале температур 1400—1450°С перехо дит в а-тридимит с объемным изменением 0,6%. Кварц плавится при 1723 °С. Изменения объема зерен кварца, происходящие в процессе обжига, влияют на прочность
ирастрескивание керамического изделия.
4.Спекаемость
Спекаемостыо глин называют их свойство уплотнять ся при обжиге и образовывать камнеподобный черепок.
На рис. 3.4 видно, что с повышением температуры обжи га возрастает степень спекания и уменьшается водопоглощение до точки С, так как при температуре tc отме чаются признаки пережога — оплавление и вспучивание материала. Интервал спекания равен tc—tA, где tA— температура начала спекания. Интервал спекания лег коплавких глин (для производства кирпича, керамзита) 50—100 °С, огнеупорных глин — 400 °С.
Огнеупорные глины (и изделия из них) противостоят действию высоких температур, не деформируясь и не расплавляясь. Чистый каолинит плавится при 1770°С, однако различные примеси (Fe203, СаС03 и др.) пони жают эту температуру. Представляя собой сложные при родные смеси, глины не имеют определенной температу ры плавления. При 750—800°С вследствие частичного плавления легкоплавких эвтектических смесей начина ется уплотнение черепка и закрытие пор, т. е. происхо дит спекание.
Цвет глины после обжи га имеет существенное зна чение для облицовочных ке рамических изделий (лице вые кирпич и керамические камни, терракотовая плит ка), а также для тонкой ке рамики. Для получения бе лого черепка обжиг ведут в восстановительной среде (при наличии свободных СО и Нг в газах) и при опреде
ленных температурах, |
что |
Рис. 3.4. |
Зависимость изменения |
|
водопоглощения керамического ма |
||||
бы |
Fe20 3 перевести в |
FeO. |
териала |
от температуры обжига |
(А, В, С — интервалы водопоглоще |
||||
Не |
желательны в |
глине |
ния) |
|
крупные зерна пирита FeS2 и оксидов железа, образую щие на черепке после обжига черные точки. Выделение свободного оксида железа при нагревании между 450 и 800 °С придает изделию красноватое и желтоватое окра шивание. Оксиды титана вызывают глубокую синеватую окраску черепка.
Для получения некоторых видов цветной керамики в сырьевую массу добавляют оксиды металлов (железа, кобальта, хрома и др.).
§ 4. ОБЩАЯ СХЕМА ПРОИЗВОДСТВА КЕРАМИЧЕСКИХ ИЗДЕЛИИ
1. Обработка глиняной массы
Производство керамических изделий включает следу ющие этапы: карьерные работы, механическую обра ботку глиняной массы, формование изделий, их сушку и обжиг.
Карьерные работы включают добычу, транспортиро вание и хранение промежуточного запаса глины. Выле живание замоченной глины и ее вымораживание в тече ние годичного срока на открытом воздухе разрушает природную структуру глины, она диспергируется на элементарные частицы, что повышает пластичность и формовочные свойства керамической массы.
Механическая обработка глины осуществляется с по мощью глинообрабатывающих машин и имеет цель: вы делить либо измельчить каменистые включения, гомоге низировать керамическую массу и получить необходимые формовочные свойства. Каменистые включения выделя ют из глины, пропуская ее через винтовые камневыдели тельные вальцы или применяя другие специализирован ные машины. Можно добиться полного выделения кам ней из глины гидравлическим обогащением: глину распускают в глиноболтушках, а затем шликер пропус кают через сито, на котором отделяются камни размером более 0,5 мм; шликер обезвоживают в мощных распыли тельных сушилках.
Глину измельчают после выделения каменистых включений. Если их нет в глине, то после доставки на завод ее сразу подвергают грубому дроблению, потом тонкому измельчению. После тонкого измельчения гли ну надо промять, чтобы получить глиняную масу с необ
ходимой формовочной влажностью. На кирпичных заво дах глину проминают в открытых лопастных глиномял ках с водяным орошением и паровым увлажнением гли няной массы. Паровое увлажнение увеличивает произ водительность ленточных прессов и снижает потребляе мую ими мощность на 15—20 % по сравнению с водя ным орошением глины.
2. Формование
Стеновые керамические изделия изготовляют спосо бами пластического формования и полусухого прессова ния. Из жидких глиняных масс (шликеров) изготовляют некоторые виды облицовочной плитки, санитарно-техни ческие и другие фаянсовые и фарфоровые изделия.
Способ пластического формования. Изделия стеновой керамики формуют из пластичных глиняных масс на ленточных шнековых прессах, которые могут быть ваку умными и безвакуумными (рис. 3.5). В корпусе этого пресса вращается шнек — вал с винтовыми лопастями. Глиняная масса, поступающая через воронку и питаю щий валик, перемещается с помощью шнека к сужаю щейся переходной головке и мундштуку. В этом месте глиняная масса уплотняется, выравниваются давления и скорости по сечению глиняного бруса. Мундштук лен точного пресса для производства обыкновенного кирпи ча имеет прямоугольное сечение. Для формования пус тотелых кирпича и керамических камней в мундштуке пресса устанавливают пустотообразующий сердечник, состоящий из скобы с прикрепленными к ней стержня ми — пустообразователями. Применяются также фасон ные вставки с узкими щелями — для формования чере пицы, кольцевые — для керамических труб.
Из мундштука пресса выходит глиняный брус, кото рый разрезают автоматически резательным аппаратом, получая изделия заданного размера. Отбор сырца от пресса и укладку его на транспортные средства выпол няют автоматы. Плотный вакуумированный сырец уста навливают рядами на печную вагонетку и он поступает в туннельную сушилку в штабеле (без полок). Вакууми рование глины позволяет извлечь из нее воздух, снизить формовочную влажность на 3—4 % и вследствие этого улучшает ее формовочные и прочностные свойства. Проч ность сырца возрастает в 2—3 раза, т. е. примерно в 1,5 раза упрочняется высушенное изделие, прочность обож:*
Рис. 3.5. Схема устройства ленточного пресса
/ — мундштук; 2 — головка пресса; 3 — цилиндр пресса; 4 — лопасти шнека; 5 — воронка
женного изделия увеличивается до 2 раз, его водопоглощение снижается на 10—15 %.
Способ полусухого прессования. Керамические изде лия формуют способом полусухого прессования из ших ты с влажностью 8—10%, уплотняемой прессованием под значительным давлением (15—40 МПа). Керамичес кие пресс-порошки должны иметь определенный зерно вой состав и влажность. Их готовят шликерным и су шильно-помольным способами.
При сушильно-помольной подготовке глины предус матривают следующие операции: дробление глины на дезинтеграторных вальцах; сушку глины в сушильных барабанах; помол высушенной глины в корзинчатых дез интеграторах; отсеивание крупных зерен на ситах; ув лажнение порошка, прошедшего через сито, паром до равномерной влажности 8—10 %, необходимой для прес сования.
Для полусухого способа производства целесообразно применять глины с небольшой естественной влажностью, не требующие сушки перед помолом. Способ полусухого прессования применяют в производстве обыкновенного и пустотелого глиняного кирпича, фасадных плиток. Глав ное преимущество полусухого прессования перед пласти ческим формованием — сокращение затрат энергии. На искусственную сушку 1000 шт. сырца пластического фор мования влажностью 18—22 % расходуется до 100 кг условного топлива.
Способ литья. Рассмотрим особенности способа литья применительно к производству тонких (толщиной
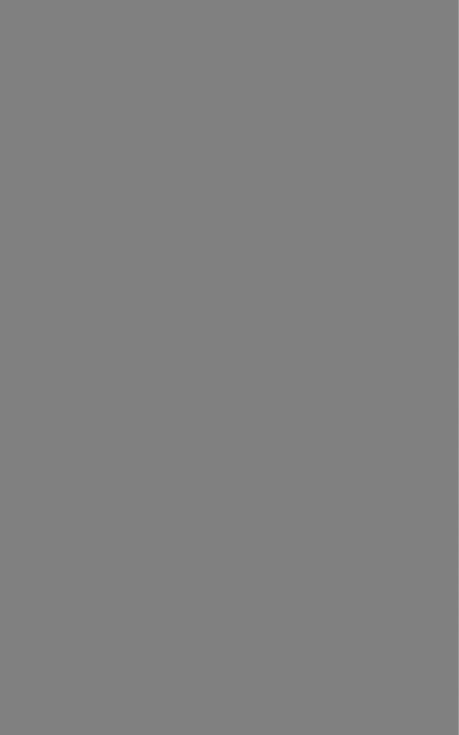
нельных сушилках 16—36 ч при начальной температуре теплоносителя 120—150 °С.
Камерные сушилки представляют собой систему ка мер, каждая камера обогревается горячим воздухом или горячими газами, отходящими из печей. В стены камер встроены лопастные реверсивные вентиляторы, создаю щие интенсивную циркуляцию теплоносителя внутри ка меры. После сушки керамические изделия, имеющие влажность не более 5 %, поступают в печь.
4. Обжиг изделий
Обжиг завершает изготовление керамических изде лий. В процессе обжига,формируется их структура, опре деляющая технические свойства изделия. Суммарные затраты на обжиг достигают 35—40 %, а потери от бра ка достигают 10 % себестоимости товарной продукции.
Обжиг керамических изделий осуществляется в тун нельных печах с автоматическим управлением (хотя на действующих кирпичных заводах работает значительное количество кольцевых печей). Туннельная печь пред ставляет собой длинный канал, выложенный внутри ог неупорной футеровкой (рис. 3.7). Вагонетки с изделия ми, составляющие сплошной поезд, перемещаются в пе чи и постепенно проходят зоны подогрева, обжига и охлаждения: при подаче новой вагонетки с сырцом в зо ну подогрева из зоны охлаждения выходит вагонетка с обожженными изделиями.
Максимальная температура обжига кирпича и дру гих стеновых керамических изделий (950—1000°С) не обходима для спекания керамической массы. Спекание
а) |
Зона |
В) |
Зона подогрева |
обжига |
Зона охлаждения |
Топливо
Рис. 3.7. Схема туннельной печи |
|
|
а — план; б — разрез; / — газопровод; |
2 — трубопровод |
для подогретого воз |
духа; з — газовая горелка; 4 — топка; |
5 — вагонетка; 6 |
— обжигаемый сырец |
происходит вследствие цементирующего действия расп лава эвтектик (жидкостное спекание), реакций в твер дой фазе и кристаллизации новообразований.
При избыточном количестве расплава, что характер но для пережога, изделия теряют форму, оплавляются с поверхности. Недожог обусловлен незавершенностью процесса спекания. Он проявляется в характерных приз наках: «алый» цвет кирпича, снижение прочности, силь ное уменьшение водостойкости и морозостойкости. В тун нельных печах щелевого типа достигается равномер ность обжига, а следовательно, высокое качество и однородность продукции. После выгрузки из печи их сортируют с учетом технических условий, приводимых
вГОСТах.
§5. СВОЙСТВА КЕРАМИЧЕСКИХ ИЗДЕЛИЙ
Пористость керамического черепка (пористых изде лий) обычно составляет 10—40%, она возрастает при введении в керамическую массу порообразующих доба вок. Стремясь снизить плотность и теплопроводность, прибегают к созданию пустот в кирпиче и керамических камнях.
Водопоглощение характеризует пористость керами ческого черепка. Пористые керамические изделия имеют водопоглощение 6—20 % по массе, т. е. 12—40% по объе му. Водопоглощение плотных изделий гораздо меньше: 1—5 % по массе (2—10 % по объему).
Теплопроводность абсолютно плотного керамического черепка большая — 1,16 Вт/(м-°С). Воздушные поры и пустоты, создаваемые в керамических изделиях, снижа ют плотность и значительно уменьшают теплопровод ность, так, например, снижение плотности стеновых кера мических изделий с 1800 до 700 кг/м3 понижает их теп лопроводность с 0,8 до 0,21 Вт/(м-°С). Соответственно уменьшается толщина наружной стены и материалоем кость ограждающих конструкций.
Прочность зависит от фазового состава керамическо го черепка, пористости и наличия трещин. Марка стено вого керамического изделия (кирпича и др.) по прочнос ти обозначает предел прочности при сжатии, однако при установлении марки кирпича наряду с прочностью при сжатии учитывают показатель прочности при изгибе, по
скольку кирпич в кладке подвергается изгибу. Изделия с пористым черепком выпускаются марок 75—300, а плотные изделия (дорожный кирпич и др.) — более вы соких марок (400—1000).
Между прочностью керамического черепка Rcж и его
коэффициентом плотности КПл прослеживается |
зависи |
мость в виде кубической параболы |
|
Ясж = * 0«пл. |
(3.3) |
где Ro — предел прочности при сжатии абсолютно плотного черепка; Кал — коэффициент плотности; Кал = рт/р; Pm и р — соответственно
средняя плотность и истинная плотность керамического черепка.
Морозостойкость. Марка по морозостойкости обозна чает число циклов попеременного замораживания и от таивания, которое выдерживает керамическое изделие в насыщенном водой состоянии без признаков видимых повреждений (расслоение, шелушение, растрескивание, выкрашивание). Керамические изделия имеют марки по морозостойкости: 15, 25, 35, 50, 75, 100 в зависимости от своей структуры.
Керамический материал морозостоек, если в нем объем резервных пор достаточен для компенсации прироста объ ема замерзающей воды в «опасных» порах. К резерв ным относят открытые поры (диаметром больше 200 мкм), в которых капиллярное давление недостаточ но для удержания воды, а также закрытые поры. «Опас ные» поры удерживают воду, замерзающую при слабых морозах (—10°С).
Паропроницаемость стеновых керамических |
изде |
лий способствует вентиляции помещений. Малая |
паро |
проницаемость нередко служит причиной отпотевания внутренней поверхности стен помещений с повышенной влажностью воздуха. Паропроницаемость зависит от пористости и характера пор. Например, коэффициент паропроницаемости фасадных плиток полусухого прес сования с водопоглощением 8,5; 6,5 и 0,25 % соответст венно равен 0,155; 0,0525 и 0,029 г/(м-ч-Па). Неодина ковая паропроницаемость слоев, из которых состоит наружная стена, вызывает накопление влаги. Так, фа садная облицовка стен глазурованными плитками может привести к накоплению влаги в контактном слое стена— плитка; последующее замерзание влаги вызывает отсло ение облицовки.
но