
книги / Строительные материалы
..pdfЧем выше содержание основных оксидов (CaO+MgO) в извести, тем пластичнее известковое тесто и тем выше ее сорт. Содержание непогасившихся частиц, к которым относятся частицы недожога и пережога, снижает каче ство извести. Недожогом называют оставшиеся зерна сырья-извёстняка, которые отощают известковое тесто, ухудшают его пластичность и пескоемкость. Пережог представляет собой остеклованный трудногасящийся ок сид кальция, уплотненный при высокой температуре. Ча стицы пережога гидратируются очень медленно с увели чением своего объема, что может вызвать растрескива ние штукатурки или известковых изделий.
2. Твердение гашеной извести
Известь применяется в виде строительных растворов, т. е. в смеси с песком и другими заполнителями. На воз духе известковый раствор постепенно отвердевает под влиянием двух одновременно протекающих процессов: а) высыхания раствора, сближения кристаллов Са(ОН)2 и их срастания; б) карбонизации извести под действием углекислого газа, который в небольшом количестве со держится в воздухе: С а(0Н )2+С 02= С аС 03+ Н 20.
Образующийся карбонат кальция срастается с крис таллами Са(ОН)2 и упрочняет известковый раствор. При карбонизации выделяется вода, поэтому штукатур ку и стены, в которых применены известковые растворы, подвергают сушке. Известковые растворы твердеют мед ленно, сушка ускоряет процесс их твердения. Для ускоре ния твердения к извести добавляют цемент и гипс. Це мент и активные минеральные добавки повышают также водостойкость известковых растворов.
3. Молотая негашёная известь
Молотую негашеную известь получают путем тонкого размола комовой извести без предварительного гашения. Строительные растворы и бетоны, приготовленные на молотой негашеной извести, быстро схватываются и отвердевают вследствие гидратациониого твердения нега шеной извести. При правильно подобранном водоизвест ковом отношении (0,9—1,5) кристаллы гидроксида каль ция, получившиеся при гидратации оксида кальция непо средственно в растворе С аО Н 20, срастаются между
собой и быстро образуют прочный кристаллический срос ток. Саморазогревание материалов (раствора или бето на), со своей стороны, способствует ускорению твердения и росту прочности раствора, что особенно важно при зим них работах (каменной кладке, штукатурке и др.).
Во избежание чрезмерного разогрева нужно позабо: титься об отводе излишней экзотермической теплоты, при этом трещин от гашения извести не образуется, а воздуш ная известь ведет себя как быстросхватывающееся и быстротвердеющее вяжущее вещество.
В молотую негашеную известь и гидратную известь (пушонку) разрешается вводить тонкомолотые минераль ные добавки: доменные и топливные шлаки, золы, извест няк. Продукт совместного помола негашеной извести и карбонатной породы называют карбонатной известью. Молотую негашеную известь обычно используют сразу после помола, так как вследствие поглощения влаги из воздуха она теряет свои вяжущие свойства.
4. Виды и применение воздушной извести
В зависимости от содержания оксида магния воздуш ная известь разделяется на кальциевую (M g 0 ^5 % ),
магнезиальную (MgO = 5—20%) и высокомагнезиаль ную, или доломитовую (MgO = 20—40 %). Наиболее важ ные показатели качества извести: активность — процент ное содержание оксидов, способных гаситься; количество непогасившихся зерен (недожог и пережог); время га шения.
В зависимости от времени гашения извести всех сор тов различают: быстрогасящуюся известь с временем га
шения до 8 мин, среднегасящуюся — время |
гашения не |
превышает 25 мин и медленно гасящуюся |
с временем |
гашения более 25 мин. |
|
Строительные растворы на воздушной извести имеют невысокую прочность. Так, известковые растворы через 28 сут воздушного твердения имеют прочность при сжа тии: на гашеной извести 0,4—1 МПа, на молотой нега шеной извести до 5 МПа. Поэтому сорт воздушной изве сти устанавливают не по прочности, а по характеристикам ее состава (табл. 5.1). Чем меньше глинистых и дру гих примесей в исходном известняке, тем выше актив ность извести, быстрее происходит ее гашение и больше выход известкового теста.
Т А Б Л И Ц А 5J> ВАЖНЕЙШИЕ ПОКАЗАТЕЛИ КАЧЕСТВА ВОЗДУШНОЙ ИЗВЕСТИ. (НЕГАШЕНОЙ КОМОВОЙ ИЛИ МОЛОТОЙ)
Показатели
Содержание активных (CaO + MgO) в пересчете на сухие вещества, не ме
нее, % У Содержание непогасившихся зерен в
негашеной комовой извести, не бо лее, %
|
Сорт |
|
первый |
второй |
трети 1 |
90 |
80 |
70 |
7 |
11 |
14 |
Большое количество извести идет на изготовление си ликатного кирпича и силикатных бетонов: ячеистых, лег ких, тяжелых, а также используется в смешанных вя жущих.
5. Известково-шлаковые и известково-пуццолановые вяжущие
Получение известково-шлаковых вяжущих основано на способности тонкоизмельченных гранулированных до менных шлаков твердеть при добавке извести. Обычно шлак размалывают совместно с воздушной известью, со держание которой в вяжущем составляет 20—30 %. При помоле добавляют до 3—5 % гипса для улучшения про цессов твердения. Известь, реагируя с алюминатами и силикатами шлака, способствует образованию низкоос новных гидроалюминатов и гидросиликатов кальция. Добавляемый гипс реагирует в водном растворе с алю минатами кальция, образуя гидросульфоалюминат каль ция. В результате этих процессов возрастает прочность вяжущего.
Известково-шлаковые вяжущие схватываются п твер деют медленно, но при теплозлажностной обработке твердение ускоряется. Они стойки в пресной воде, по имеют невысокую морозостойкость. Известково-шлако вые вяжущие применяют в бетонах невысоких марок и в строительных растворах.
Известково-пуццолановые вяокущие изготовляют пу тем совместного помола трепела, диатомита и других активных минеральных добавок с известью. При тверде нии смешанного вяжущего во влажных условиях образу
ются низкоосновные гидросиликаты кальция. На воздухе в сухих условиях гидросиликаты способны дегидратиро ваться, при этом прочность изделия может сильно сни жаться. Прочность этих вяжущих невысока, и они при меняются там же, где и известково-шлаковые вяжущие.
6. Безотходное производство воздушной извести
В ЧССР освоено производство комовой и порошкооб разной извести, обеспечивающее полное использование карбонатного сырья (автор системы — НИИстройматериалов, г. Брно).
Производство порошкообразной негашеной извести осуществляется в кооперации с обычным производством негашеной извести в шахтных печах (на данном пред приятии две печи, работающие на коксе по пересыпному способу). Шахтные печи используют дробленый извест няк местного карьера с размером кусков 7—18 см. Бо лее мелкие куски известняка (менее 7 см) подвергаются дальнейшему измельчению в молотковой дробилке, а за тем путем воздушной сепарации продукт разделяется на две фракции: более грубая фракция (0,2—2,5 мм) пере рабатывается на известь, а тонкая (менее 0,2 мм) ис пользуется для известкования кислых почв. При воздуш ной сепарации из тонкой фракции удаляются глинистые вещества и периклаз, т. е. происходит обогащение окси дом кальция известняка, идущего на обжиг. В результа те порошкообразная негашеная известь имеет высокую активность.
Производство негашеной извести включает: предвари тельный прогрев порошка известняка до 700—800 °С газами, отходящими из вращающейся печи; обжиг подо гретого порошка в короткой вращающейся печи; охлаж дение по выходе из печи в слоевом холодильнике. Не смотря на высокий расход теплоты, производство себя оправдывает из-за комплексного полного использования сырья.
§ 4. ГИДРАВЛИЧЕСКАЯ ИЗВЕСТЬ И РОМАНЦЕМЕНТ
Гидравлическая известь. Такую известь получают об жигом в шахтных печах не до спекания (900—1100°С) мергелистых известняков с содержанием глины 6—20 %.
Полученную известь размалывают и применяют в виде порошка либо гасят в пушонку. В процессе обжига мер гелистых известняков после разложения карбоната кальция (900 °С) часть СаО остается в свободном состо
янии, а часть соединяется |
с оксидами Si02, А120з и |
||
Fe20 3, входящими |
в состав |
глинистых минералов. При |
|
этом образуются |
низкооснбвные |
силикаты 2Ca0-Si02, |
|
алюминаты Са0-А120 3 и ферриты |
кальция Ca0-Fe20 3, |
которые и придают извести гидравлические свойства. Гидравлическая известь начинает твердеть на возду
хе (в первые 7 сут) и продолжает твердеть и увеличи вать свою прочность в воде. Предел прочности при сжа тии после 28 сут комбинированного хранения образцов из раствора 1:3 по массе (7 сут во влажном воздухе и 21 сут в воде): а) слабогидравлической извести не менее 1,7 МПа; б) сильиогидравлической извести не ниже 5 МПа. Гидравлическая известь твердеет медленно: на чало схватывания 0,5—2 ч; конец 8—16 ч.
Растворы и бетоны на гидравлической извести обла дают удовлетворительной долговечностью в сухих и влажных условиях, поэтому ее применяют для изготов ления кладочных и штукатурных растворов и бетонов невысоких марок и бетонных камней. Ее хранят в закры тых помещениях, при перевозке предохраняют от увлаж нения.
Романцемент — гидравлическое вяжущее вещество, получаемое тонким помолом обожженных не до спекания (900 °С) известняковых и магнезиальных мергелей, со держащих 25 % и более глины. Образующиеся при об жиге низкооснбвные силикаты и алюминаты кальция придают романцементу гидравлические свойства.
В романцементе нормального обжига нет свободной извести или она содержится в небольшом количестве (2—3% ). Романцемент измельчают (после обжига) в шаровых мельницах, нередко совместно с гипсом (3— 5 %) и активными минеральными добавками (10—15 %)• Схватывание и твердение романцемента обусловлено гидратацией силикатов и алюминатов, образовавшихся при его обжиге.
Романцемент выпускают трех марок (МПа): 2,5; 5 и 10; он должен выдерживать испытание'на равномерность изменения объема. Применяется для изготовления строи тельных растворов, бетонов, бетонных камней. Гидрав лическая известь и романцемент ранее широко применя-
ллсь. Однако теперь эти материалы постепенно уступили свое место более совершенным гидравлическим вяжущим веществам и прежде всего портландцементу. Однако применяя эти вяжущие вещества для изготовления стро ительных растворов, стеновых камней и бетонов невысо ких марок, можно сэкономить энергоемкий и дорогой портландцемент.
§5. ПОРТЛАНДЦЕМЕНТ
1.Общая характеристика портландцемента
Портландцементом называют гидравлическое вяжу щее вещество, в составе которого преобладают силика ты кальция (70—80 %). Портландцемент — продукт тон кого измельчения клинкера с добавкой (3—5%) гипса. Клинкер представляет собой зернистый материал (в ви де горошка), полученный обжигом до спекания (при 1450 °С) сырьевой смеси, состоящей в основном из кар боната кальция (различных видов известняков) и алю мосиликатов (глин, мергеля, доменного шлака и др.). Небольшая добавка гипса регулирует сроки схватыва ния портландцемента. Допускается применение фосфогипса и борогипса.
Для производства портландцемента имеются неогра ниченные сырьевые ресурсы — побочные продукты про мышленности (шлаки, золы, шламы) и распространенные карбонатные й глинистые горные породы. Автомати зация производственных процессов и переход к произ водству цемента на заводах-автоматах значительно снижают потребление энергии и трудоемкость, позволя ют значительно увеличить выпуск цемента в соответствии с широким масштабом строительства в нашей стране.
Изобретение портландцемента (1824 г.) связано с именами Егора Герасимовича Челиева — начальника мастерских военно-рабочей бригады в Москве и Джозе фа Аспдина — каменщика из английского города Лидса.
2. Клинкер
Качество клинкера определяет все свойства портланд цемента; добавки же, вводимые в цемент, лишь регули рует его свойства. Качество клинкера зависит от его хи мического и минерального состава, тщательности подго-
тонки сырьевой массы, условий проведения ее обжига и режима охлаждения. Клинкер обычно получают в виде спекшихся гранул размером 10—40 мм, имеющих слож ную микроструктуру, так как клинкер включает ряд кри сталлических фаз и некоторое количество стекловидной фазы.
Химический состав клинкера определяется содержа нием оксидов (% по массе), причем главных из них: СаО 63—66, Si02 21—24, А120з 4—8, Fe20 3 2—4; их сум марное количество составляет 95—97 %. В небольших количествах в виде различных соединений могут входить MgO, S 03, Na20 и К2О, а также ТЮ2, Сг20 3, Р2О5. В про цессе обжига, доводимого до спекания, главные оксиды образуют силикаты, алюминаты, алюмоферрит кальция в виде минералов кристаллической структуры, а некото рые из них входят в стекловидную фазу.
Минеральный состав клинкера. Основные минералы клинекера: алит, белит, трехкальциевый алюминат и алюмоферрит кальция.
Алит 3Ca0*Si02 (или C3S*) — самый важный мине рал клинкера, определяющий быстроту твердения, проч ность и другие свойства портландцемента; содержится в клинкере в количестве 45—60 %. Алит представляет со бой твердый раствор трехкальциезого силиката и неболь шого количества (2—4 %) MgO, А120 3, Р2О5, Сг20 3 и других примесей, которые могут существенно влиять на структуру и свойства. Согласно Регур и Гинье, в интер вале между нормальной температурой и 1100°С трех кальциевый силикат кристаллизуется в шести поли морфных формах. Алит в клинкере фиксируется в виде тригональной модификации. На микрофотографии (рис. 5.3) кристаллы алита имеют обычно шестиугольную или прямоугольную форму. Предпочтительнее правильно сформировавшиеся кристаллы вытянутой формы разме ром 3—20 мкм, благоприятствующие повышению марки цемента.
Белит 2Ca0-Si02 (или C2S) — второй по важности и содержанию (20—30 %) силикатный минерал клинкера. Он медленно твердеет, но достигает высокой прочности при длительном твердении портландцемента. В интерва ле между нормальной температурой и 1500 °С существу-
* Приняты сокращенные написания химических формул: СаО—С; S1O2—S; А120 3—A; Fe20 3—F; Н20 —Н.
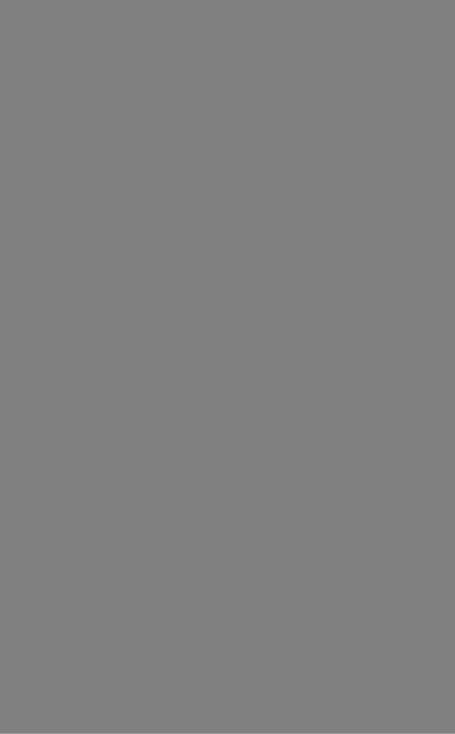
ре в количестве 4—12 % и при благоприятных условиях обжига получается в виде кубических кристаллов разме ром до 10—15 мкм; образует твердые растворы сложно го состава. Плотность СзА 3,04 г/см3, он очень быстро гидратируется и твердеет, но имеет небольшую проч ность. Является причиной сульфатной коррозии бетона, поэтому в сульфатостойком портландцементе содержание С3А ограничено 5 %•
Четырехкальциевый алюмоферрит C4AF в клинкере содержится в количестве 10—20 %. Алюмоферритная фа за промежуточного вещества клинкера представляет собой твердый раствор алюмоферритов кальция разного состава, в клинкерах обычных портландцементов ее со
став близок к 4СаО • Al20 3-Fe20 3. |
Плотность C4AF |
3,77 г/см3. По скорости гидратации |
минерал занимает |
как бы промежуточное положение между алнтом и белитом, поэтому он не оказывает определяющего влияния на скорость твердения и тепловыделение при гидрата ции портландцемента.
Клинкерное стекло присутствует в промежуточном веществе в количестве 5—15 %. Оно состоит в основном из СаО, А120 3, Fe20 3, MgO, К20, Na20.
Оксид магния входит в состав алюмоферритной фа зы и клинкерного стекла, а также присутствует в сво бодном состоянии в виде кристаллов медленно гидрати рующего минерала периклаза. Гидратация MgO длится долго, возможно, несколько лет, и переход в Mg(OH)2 сопровождается увеличением объема твердой фазы в уже затвердевшем цементном камне. При содержании MgO более 5 % это явление может явиться причиной не равномерного изменения объема цемента при твердении и растрескивания бетона.
Свободный оксид кальция СаОСВОб находится в свежеобожженном клинкере в виде зерен; его содержание в цементе не должно превосходить 1 %• При более вы соком содержании СаОсвоб может проявиться нерав номерное изменение объема цемента при твердении, связанное с переходом СаО в Са(ОН)2 и увеличением
объема.
Щелочи (Na20, К20) входят в алюмоферритную фа зу клинкера, а также присутствуют в цементе в виде сульфатов. Содержание щелочей в портландцементе ограничивается в случае применения заполнителя (пес ка, гравия), содержащего реакционноспособные опало-
видные модификации двуокиси кремния, из-за. опасности растрескивания бетона в конструкции.
3. Принципы получения клинкера
Сырьевыми материалами для производства клинкера служат известняки с высоким содержанием карбоната кальция (мела, плотного известняка, мергелей и др.) и глинистые породы (глины, глинистые сланцы), содержа щие Si02, А120 3 и Fe20 3. В среднем на 1 т цемента рас ходуется около 1,5 т минерального сырья; примерное со отношение между карбонатной и глинистой составляю щими сырьевой смеси 3 1 (т. е. берется около 75 % известняка и 25% глины). В сырьевую смесь вводят добавки, корректирующие химический состав, регулиру ющие температуру спекания смеси и кристаллизацию минералов клинкера. Например, количество Si02 повы шают, добавляя в сырьевую смесь трепел, опоку. Добав ление колчеданных огарков увеличивает содержание Fe20 3.
Для производства портландцемента все шире исполь зуют побочные продукты промышленности.
На Седьмом Международном конгрессе по химии це мента (Париж, 1980 г.) ученые многих стран отмечали целесообразность широкого использования промышлен ных отходов (металлургических и топливных шлаков, зол ТЭС). Весьма ценным сырьем являются доменные шлаки, содержащие необходимые для получения клинке ра составные части (CaO, Si02, А120 3, Fe20 3). Нефели новый шлам, получающийся при производстве глинозе ма, содержит 25—30 % Si02 и 50—55 % СаО; достаточ но к нему добавить 15—20% известняка, чтобы получить сырьевую смесь. Использование нефелинового шлама повышает производительность печей примерно на 20 % и снижает расход топлива на 20—25 %.
Основной и наиболее эффективный вид топлива — природный газ\ он отличается высокой удельной тепло той сгорания. Сокращается применение мазута и твердо го топлива, приготовляемого в специальных установках для сушки и помола угля (антрацита, каменного угля). Удельная теплота сгорания твердого топлива ниже газо образного; углевоздушные смеси подвержены взрывам; зольность углей 10—20%; зола, попадая в обжигаемую сырьевую смесь, искажает расчетный минеральный со-