
книги / Строительные материалы
..pdfРис. 5.4. Технологическая схема с>шки и помола материален (сухой способ) в мельницах с центробежными сепараторами
1 — дозаторы; 2 — ленточный конвейер; 3 — рукавные фильтры; 4 — шлюзовой затвор; 5 — аэрожелоба; 6 — сепараторы; 7 — элева тор; 8 — циклоны; ^ — вентиляторы; 10 — шнеки; / / — мельница; 12 — топка
став клинкера. Стоимость топлива составляет до 26 % себестоимости готового цемента, поэтому на цементных заводах много внимания уделяется его экономии.
Подготовка сырья. Производство портландцемента — сложный технологический и энергоемкий процесс, вклю чающий: а) добычу в карьере и доставку на завод сырь евых материалов, известняка и глины; б) приготовление сырьевой смеси; в) обжиг сырьевой смеси до спекания— получение клинкера; г) помол клинкера с добавкой гип са — получение портландцемента; д) магазинирование готового продукта. Обеспечению заданного состава и ка чества клинкера подчинены все технологические опера ции.
Приготовление сырьевой смеси состоит в тонком из мельчении и смешении взятых в установленном соотно шении компонентов, что обеспечивает полноту прохож дения химических реакций между ними и однородность клинкера. Сырьевую смесь приготовляют сухим, мокрым и комбинированным способами.
Сухой способ заключается в измельчении и тесном смешении сухих (или предварительно высушенных) сырьевых материалов, поэтому сырьевая смесь получа ется в виде минерального порошка, называемого сырье вой мукой. Тонкое совместное измельчение известняка и глины осуществляют в мельницах, в которых совмеща ются помол и сушка сырьевых материалов до остаточ ной влажности 1— 2 %. Совмещение сушки с дроблени ем и тонким измельчением осуществляют подсушивани ем сырья в дробилках и сушкой сырья в мельницах тонкого измельчения. Сушку производят отходящими газами печей, при этом в мельнице можно перерабаты вать сырье с влажностью до 5 %, а при использовании топки до 15 %. В последние годы в цементной промыш ленности используют мощные валковые мельнйцы-су- шилки и мельницы самоизмельчеиия «Аэрофол».
На крупных предприятиях сырьевые мельницы рабо тают по замкнутому циклу (рис. 5.4): установка произ водительностью до 100 т/ч включает сепараторы, отделя ющие крупную фракцию сырьевой муки и возвращающую ее в мельницу для помола. Таким образом повышается тонкость помола сырьевой смеси и качества обжигаемо го из нее клинкера. Сырьевую муку направляют в силосы, в них корректируют состав сырья и создают запас, необходимый для бесперебойной работы печей. При су-
rtoM способе производства затраты теплоты на обжиг клинкера в 1,5—2 раза меньше, чем при мокром. Ввиду технико-экономических преимуществ сухой способ про изводства цемента быстро раззмвается. Сухой способ наиболее выгоден при использовании известняка и гли ны с невысокой влажностью (10—15%), однородного состава и физической структуры, когда можно получить гомогенную сырьевую муку при сухом помоле.
Мокрый способ приготовления сырьевой смеси при меняют, если мягкое сырье имеет значительную влаж ность (мел, глины). Тонкое измельчение и смешение ис ходных материалов осуществляют в водной среде, поэто му сырьевая смесь получается в виде жидкотекучей массы — шлама с большим содержанием воды (35— 45%). Используется способность мягких горных пород
(глины и мела) |
легко распадаться в воде на мелкие час |
|||||||
тицы. |
Глину |
перерабатывают |
в водную |
суспензию в |
||||
глиноболтушках. Иногда гли |
|
|
|
|
|
|
||
ну перерабатывают в шлам |
|
|
|
|
|
|
||
непосредственно в карьере и |
|
|
|
|
|
|
||
далее полученный шлам над |
|
|
|
|
|
|
||
лежащего состава перекачи |
|
|
|
|
|
|
||
вают на завод. |
|
|
|
|
|
|
|
|
Второй компонент сырье |
|
|
|
|
|
|
||
вой смеси — известняк —по |
материалов по мокрому способу в |
|||||||
сле дробления направляется |
||||||||
на совместный помол с гли |
Рис. 5.5. Схема помола сырьевых |
|||||||
открытом цикле |
|
питатель |
||||||
няным |
шламом |
в шаровую |
огарков; 3 — тарельчатый |
|||||
мельницу через |
весовые до |
1 |
— бункер |
известняка; 2 -л бункер |
||||
и |
весоизмеритель; |
4 — питатель |
||||||
заторы |
непрерывного дейст |
глиняного |
шлама; |
5 — ленточный |
||||
конвейер; |
б — мельница; |
7 — ем |
||||||
вия с автоматическим управ- |
кость перед |
насосом; |
3 — насос; |
|||||
|
|
|
9 — подача |
шлама |
в производство |
РИС*5-6. Схема вращающейся печи |
|
|
|
|
|
|||
1 |
сырьевая шихта; |
2 — горячие |
газы; |
3 — вращающаяся |
печь; |
4 — цепные |
||
завесы, |
улучшающие |
теплообмен; |
5 — привод; |
6 — водяное |
охлаждение зоны |
|||
спекания |
печи; 7 — факел; 8 — подача |
топлива |
через форсупку; |
9 — клинкер; |
||||
10 |
— холодильник; U — опоры |
|
|
|
|
|
лением, что позволяет выдерживать точное соотношение между компонентами сырьевой смеси (рис. 5.5). Совмест ное измельчение известняка, глины и корректирующих добавок (например, пиритных огарков, содержащих Fe20 3) обеспечивает тщательное смешение исходных ма териалов и получение однородной сырьевой смеси. Помол сырья производят до остатка на сите № 008 не более 8— 10 %, следовательно, более 90 % частиц смеси имеет раз мер менее 80 мкм.
После мельниц известково-глиняный шлам перекачи вают насосами в вертикальные и горизонтальные резер вуары (шлам-бассейны); в них корректируют и усредня ют химический состав шлама. Состав сырьевой смеси контролируют теперь с помощью автоматического рентгеноспектрометра, обеспечивающего ежечасное опреде ление содержания CaO, Si02, Fe20 3 и А120з. По данным анализа электронно-вычислительная машина рассчиты вает дозировку сырьевых компонентов, исходя из полу чения сырьевой смеси заданного состава, а также соот ветствующий режим работы автоматических дозирующих устройств, что позволяет отказаться от корректирования при достаточном постоянстве состава смеси. Применение разжижителей шлама (добавок СДБ и др.) позволяет снизить влажность шлама, но не устраняет основной не достаток мокрого способа производства цемента — высо кую энергоемкость процесса получения клинкера.
Комбинированный способ дает возможность на 20— 30 % снизить расход топлива по сравнению с мокрым способом. Сущность этого способа заключается в том, что приготовленный шлам до поступления в печь обезво живается на специальных установках. Однако при этом возрастает расход электроэнергии, т. е. энергоемкость производства в целом остается высокой.
Обжиг сырьевой смеси как при сухом, так и при мок ром способе производства осуществляется в основном во вращающихся печах. Шахтные печи применяют иногда только при сухом способе. Вращающаяся печь представ ляет собой длинный, расположенный слегка наклонно цилиндр (барабан), сваренный из листовой стали с огне упорной футеровкой внутри (рис. 5.6). Длина печей 95— 185—230 м, диаметр 5—7 м. В СССР стали применять вращающиеся печи, работающие по сухому способу, раз мером 7x95 м, производительностью 3000 т/сут при рас ходе теплоты на обжиг 3400 кДж/кг. На предприятиях,
работающих по мокрому способу производства, применя ют печи 7X230 м, производительностью 3000 т/сут при расходе теплоты 5600 кДж/кг. Для улучшения теплооб мена внутри печей ближе к верхнему (холодному) концу устраивают цепные завесы, устанавливают теплообмен ники различной конструкции.
Вращающиеся печи работают по принципу противото ка. Сырье в виде порошка (сухой способ) или шлама (мокрый способ) подается автоматическим питателем в печь со стороны ее верхнего (холодного) конца, а со сто роны нижнего (горячего) конца вдувается топливо (при родный газ, мазут, воздушно-угольная смесь),сгорающее в виде 20—30-метрового факела. Сырье занимает только часть поперечного сечения печи и при ее вращении со ско ростью 1— 2 об/мин медленно движется к нижнему концу навстречу горячим газам, проходя различные темпера турные зоны. Выдающийся советский ученый В. Н. Юнг, разработавший основы теории обжига клинкера, услов но разделил вращающуюся печь на шесть температур ных зон в зависимости от характера протекающих в них процессов. Рассмотрим эти процессы, начиная с поступ ления сырьевой смеси в печь, т. е. по направлению с верхнего ее конца (холодного) к нижнему (горячему).
В з оне и с п а р е н и я происходит высушивание по ступившей сырьевой смеси при постепенном повышении температуры с 70 до 200С'С (в конце этой зоны), поэтому первую зону называют еще зоной сушки. Подсушенный материал комкуется, при перекатывании комья распада ются на более мелкие гранулы.
В з оне п о д о г р е в а , которая следует за зоной сушки сырья, при постепенном нагревании сырья с 200 до 700 °С сгорают находящиеся в нем органические приме си, из глиняных минералов удаляется кристаллохимиче ская вода (при 450—500 °С) и образуется безводный као линит Al203-2Si0 2. Подготовительные зоны (испарения и подогрева) при мокром способе производства занима ют 50—60 % длины печи (считая от холодного конца); при сухом же способе подготовка сырья сокращается за счет зоны испарения.
В з оне д е к а р б |
о н и з и ц и и |
(ее протяженность |
20—23 % длины печи) |
температура |
обжигаемого мате |
риала поднимается с 700 до 1100 °С; здесь завершается процесс диссоциации карбонатных солей кальция и маг
ния и появляется значительное количество свободного оксида кальция. Термическая диссоциация СаС03— это эндотермический процесс, идущий с большим поглоще
нием теплоты (1780 |
кДж на 1 кг СаСОз), |
поэтому по |
|
требление теплоты |
в третьей зоне |
печи |
наибольшее. |
В этой же зоне происходит распад |
дегидратированных |
глинистых минералов на оксиды Si02, А120 3, F2O3, кото рые вступают в химическое взаимодействие с СаО. В ре зультате этих реакций, происходящих в твердом состоя
нии, образуются |
минералы ЗСа0*А120 3, СаО-А12Оз и |
|||
частично 2Ca0*Si02. |
р е а к ц и й |
(1100— |
||
В зоне |
э к з о т е р м и ч е с к и х |
|||
1250 °С) проходят твердофазовые |
реакции образования |
|||
ЗСа0 А120 3; |
4СаО-Al20 3*Fe20 3 и белита. Эти |
экзотер |
||
мические реакции |
на сравнительно коротком |
участке |
печи (5—7 % ее длины) сопровождаются выделением большого количества теплоты (до 420 кДж на 1 кг клин кера) и интенсивным повышением температуры материа ла (на 150—200 °С).
В з оне с п е к а н и я (1300—1450—1300СС) темпера тура обжигаемого материала достигает наивысшего зна чения (1450°С), необходимого для частичного плавления материала и образования главного минерала клинкера— алита. В начале спекания, начиная с 1300 °С, образуется расплав в количестве 20—30 % объема обжигаемой мас сы из относительно легкоплавких минералов ЗСаО-А120 3, 4Ca0 *AI203-Fe20 3, а также MgO и легкоплавких приме сей. При повышении температуры до 1450 °С в клинкер ной жидкости растворяются 2Ca0-Si02 и СаО и из них в расплаве происходит образование алита 3Ca0«Si02, проходящее почти до полного связывания оксида каль ция (в клинкере СаОСвоб не более 0,5— 1 %). В расплаве сначала образуются тетраэдры SiO^“ , которые потом со
единяются с ионами Са2+, образуя кристаллическую ре шетку трехкальциевого силиката. Алит плохо растворяет ся в расплаве и вследствие этого выделяется из него в ви де мелких кристаллов, что влечет дальнейшее растворе ние в расплаве 2Ca0*Si02 и СаО. Процесс образования алита заканчивается за 15—20 мин пребывания матери ала в зоне спекания (ее протяженность 10—15% длины печи). Поскольку при вращении печи частично расплав ленный материал непрерывно перекатывается, мелкие частички слипаются в гранулы. Понижение температуры с 1450 до 1300 СС вызывает кристаллизацию из расплава
Рис. 5.7. Схема печного агрегата для обжига клинкера с циклонным тепло обменником и кальцинатором (декарбонизатором)
/ |
— вращающаяся |
печь; 2, 6, 7, 8 — циклопы теплообменника |
I—IV ступеней; |
||
3 |
— электрофильтр; |
4 — отходящие |
газы; 5 — подача |
сырьевой |
смеси; 9 — де- |
карбонизатор; 10 — электрофильтр; |
// — вторичный |
воздух из |
холодильника; |
||
12 — воздух из холодильника; 13 — холодильник клинкера |
|
ЗСаО-А120 3, 4СаО-А120з-Ре20з и MgO (в виде периклаза), которая заканчивается в зоне охлаждения, следую
щей за спеканием. |
|
температура клинкера по |
||
В з оне |
о х л а ж д е н и я |
|||
нижается с |
1300 до |
1000°С; здесь полностью |
формиру |
|
ются его структура |
и состав, |
включающий |
алит C 3S , |
|
белит C2S, С3А, C4AF, MgO |
(периклаз), стекловидную |
фазу и второстепенные составляющие.
Цементный клинкер выходит из вращающейся печи в виде мелких камнеподобных зерен — гранул темно-серого или зеленовато-серого цвета. По выходе из печи клинкер интенсивно охлаждается с 1000 до 100—200 °С в колосни ковых, рекуператорных и других холодильниках возду хом, идущим навстречу клинкеру или просасываемым через слой горячего клинкера. После этого клинкер вы держивается на складе одну-две недели.
Сухой способ производства цемента в последние годы значительно усовершенствован. Наиболее энергоем кий процесс — декарбонизация сырья — вынесен из вра
щающейся печи в специальное устройство — декарбони- затор, в котором он протекает быстрее и с использовани ем теплоты отходящих газов (рис. 5.7).
Из расходных силосов сырьевая мука сначала посту пает в систему циклонных теплообменников, где, нахо дясь во взвешенном состоянии, нагревается движущими ся навстречу (снизу-вверх) отходящими газами и уже горячей подается в декарбонизатор. Непосредственно в декарбонизаторе сжигают около 50 % топлива, что поз воляет быстро и почти полностью (на 90 %) завершить разложение СаСОз. Остальная часть топлива сжигается, как обычно, в горячем конце вращающейся печи, в кото рой получают клинкер из уже подготовленной к обжигу, т. е. декарбонизированной, сырьевой муки. Теплообмен ное устройство с декарбонизатором устанавливают около печи.
Повсеместное распространение сухого способа произ водства с применением декарбонизатора обусловлено возможностью ускорить технологический процесс, повы сить суточную производительность технологических ли ний до 3000 т клинкера, использовать теплоту газов, от ходящих из печи и холодильника, и тем самым снизить затраты топливно-энергетических ресурсов. При системе декарбонизатор — печь сокращается примерно вдвое длина вращающейся печи, компоновка цементного заво да получается более компактной, соответственно умень шается потребность в земельных площадях.
В СССР открыт новый способ производства портланд цемента— путем обжига клинкера в солевом растворе хлоридов. При этом способе основная реакционная среда в печи (силикатный расплав) заменена солевым распла вом на основе хлорида кальция. В солевом расплаве ус коряется растворение основных клинкерообразующих ок сидов (CaO, SiC>2, АЬОз, Fe203) и образование минера лов (алита, белита и др.) завершается при 1100—1150 °С вместо обычных 1400—1500°С, чго существенно снижает энергоемкость получения цементного клинкера. Получен ный клинкер, наряду с алитом, содержит минерал, на званный алинитом.
Алинит — это высокоосновный А1—С1— силикат каль ция, содержащий около 2,5 % хлорида. Клинкер, синте зированный в солевом расплаве, размалывается в 3—4 раза легче, чем обычный. Это позволяет снизить электро затраты на помол и увеличить производительность це
ментных мельниц. При этом сокращается число помоль ных агрегатов. Алинитовый цемент быстрее гидратируется в начальные сроки. Технология нового цемента осва ивается на цементных заводах. Сейчас глубоко изучают ся коррозионная стойкость бетона на этом цементе и по ведение стальной арматуры в бетоне с учетом наличия в нем хлора. Все это позволит определить рациональные области применения алиинтового цемента.
Общий расход энергии на 1 т цемента 325—550 МДж, причем минимальные энергетические затраты достигают ся при сухом способе с применением декарбонизатора*
на помол клинкера |
с добавками затрачивается 125— |
180 МДж. |
в тонкий жпорошок производится |
Помол клинкера |
преимущественно в сепараторных установках, работаю щих по открытому или замкнутому циклу. Грубная мель ница представляет собой барабан, облицованный внутри стальными броневыми плитами и разделенный дырчаты ми перегородками на две — четыре камеры (рис. 5.8). Крупнейшими помольными агрегатами являются мельни цы размером 3,95x11 м, производительностью 100 т/ч и размером 4,6x16,4 м, производительностью 135 т/ч. Ма териал в трубных мельницах измельчается под действи ем загруженных в барабан мелющих тел — стальных ша ров (в камерах грубого помола) и цилиндров (в камерах тонкого помола). При вращении мельницы мелющие тела поднимаются на некоторую высоту и падают, дробя и ис тирая зерна материала.
При работе по открытому циклу мельница работает «на проход», т. е. материал (клинкер и добавки) непре рывно поступает со стороны камер грубого помола че рез полую ось, а измельченный материал выходит из ка меры тонкого помола и далее транспортируется в силосы. Замкнутый цикл помола включает помольный агре гат и центробежный сепаратор, отделяющий крупные зерна, возвращаемые на домол (рис. 5.9), в результате чего достигается высокая тонкость помола. Помольные установки, работающие по замкнутому циклу, дают воз можность тонко измельчить клинкер (до удельной по верхности 4000—5000 см2/г) и регулировать в цементе содержание частиц различного размера, что необходимо для получения быстротвердеющего и.других специальных портландцементов. При помоле к клинкеру добавляют, гипс (так, чтобы общее содержание SO3 в цементе было'
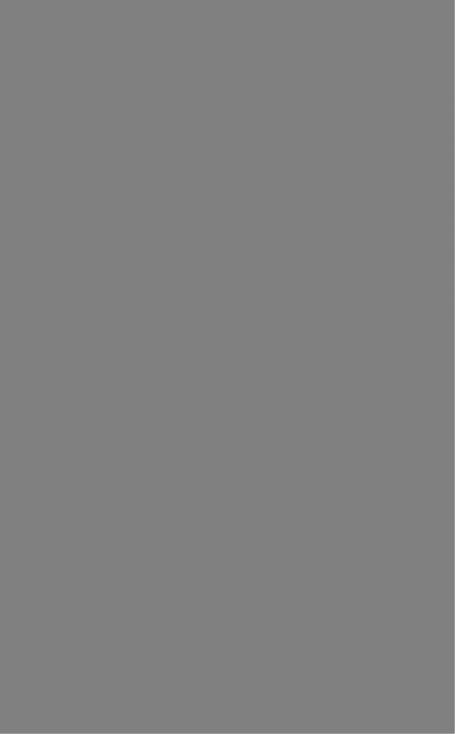