
книги / Металлы и сплавы. Анализ и исследование. Физико-аналитические методы исследования металлов и сплавов. Неметаллические включения
.pdf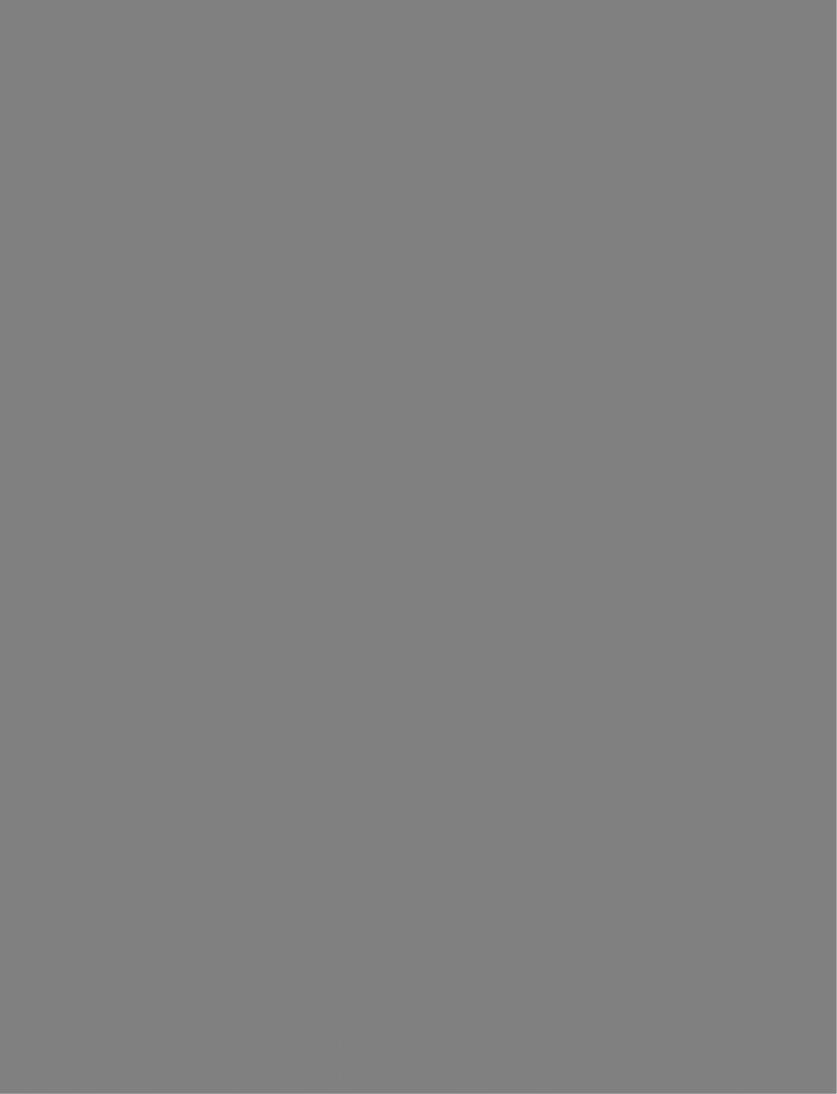
3.1.3.5. Определение глубины обезуглероженного слоя
Косновным механизмам упрочнения металлов
исплавов относятся: измельчение зерна, образо вание твердых растворов, выделение частиц вто рой фазы, превращения при термообработке и увеличение плотности дислокаций. Эксперимен тальные исследования показали, что для большин ства металлических материалов справедлив прин цип линейной аддитивности (суммирования) вкла дов от работы отдельных механизмов упрочнения:
СТ, = 00 "Ь Д0т.р. ДсГд "1*ДОд.ч. ДСТз,
где 0Т— условный предел текучести; 0 о — сопро тивление кристаллической решетки движению дислокаций (напряжение трения или напряжение Пайерлса — Набарро); Дсттр. — упрочнение твер дого раствора за счет растворения легирующих элементов (механизм твердорастворного упроч нения); Да, — вклад структурных дислокаций (iдислокационный механизм); Дад.ч. — эффект (дис персионного) упрочнения за счет выделения из твердого раствора мелких выделений (фаз); Да3— упрочняющее влияние границ зерен (механизм
зернограничного упрочнения).
Твердорастворное упрочнение особенно эф фективно при введении элементов внедрения — углерода и азота. Их влияние объясняется асим метричным искажением кристаллической решетки и сильным взаимодействием атомов этих элемен тов с дефектами кристаллического строения — дислокациями. При образовании твердых раство ров внедрения эффект упрочнения в 10-100 раз превышает упрочнение в твердых растворах за мещения. Углерод образует с железом твердые растворы внедрения и является эффективным упрочнителем. Однако в феррите его раствори мость невелика, что приводит к снижению упроч няющего эффекта. В кристаллической решетке металла сохранение повышенной концентрации углерода достигается быстрым охлаждением из области высоких температур, за счет чего форми руются структуры «закалки» игольчатого (видманштетгового) вида, придающие сплаву высокую прочность. С целью улучшения комплекса экс плуатационных свойств за счет повышения вязко сти и пластичности, структуры закалки (мартен сит) металл подвергают нагреву (отпуску). При
отпуске образуются карбиды, мартенсит обедняет ся углеродом, а вклад твердорастворного меха низма упрочнения снижается. Образующиеся час тицы цементитного типа (карбиды) более тверды и хрупки, чем ферритная матрица. Поэтому, если в процессе эксплуатации на поверхностях раздела между матрицей и частицами создается объемно напряженное состояние, возможно образование микротрещин. В явлении возникновения объемов с измененным строением, определяющих эксплуа тационные характеристики металлов и сплавов, состоит одна из причин, которые делают важным и актуальным практическое определение глубины обезуглероженного слоя.
Глубина обезуглероженного слоя зависит от химического состава сталей и газовой (окружаю щей) среды, а также от температуры нагрева. На металлургических предприятиях глубину обезуг лероженного слоя проверяют в готовой металло продукции, а также на этапах промежуточного пе редела (после горячей деформации, «черного» от жига и т. д.). Результаты контроля позволяют определять степень обезуглероживания на каждом этапе и подбирать условия последующей обработ ки, обеспечивающие выполнение требований по требителя к предельно допустимой глубине обез углероживания. Обычно произвольно отбирают по 3-5 образцов от прутков партии металла или из определенных участков садки (например сверху и снизу) и др. На этапах промежуточных переделов методика контроля устанавливается заводом, про изводящим металл. Для готовой металлопродук ции рекомендуемый метод контроля указывают в стандартах и технических условиях. Действующий ГОСТ 1763 устанавливает следующие методы контроля: термоиндукционный по замерам термо электродвижущей силы ТЭДС, химический (X) и металлографический (М, М 1, М2, а также с изме рением твердости — Т).
Метод измерения термоэлектродвижущей си лы ТЭДС применяется (обычно в качестве внутри заводского) для контроля всех сталей. Особенно часто метод используется при контроле шлифо ванной поверхности стали, где обезуглероженный слой не допускается, или прутков диаметром до 30 мм, когда разрешается лишь незначительная глубина обезуглероживания. Замеры производятся на обезуглероженной и необезуглероженной по верхностях образца.
В случае стальной металлопродукции, в кото рой обезуглероживание не допускается, для объ ективного испытания с одной стороны образца (абразивным кругом или другим способом) гото вят площадку (лыску) длиной 10-15 мм, позво ляющую полностью удалить обезуглероженный слой. В случае прутков, на которых допускается обезуглероживание, обезуглероженный слой сни
мают, а затем готовят образец.
В установку для определения ТЭДС. (рис. 3.1.43) входят: 1 — нагреваемый (медный) стержень; 2 — медное основание; 3 — исследуе мый образец; 4 — измерительный прибор (микро амперметр). Установку градуируют по этало нам— образцам, в которых заранее металлогра фическим методом определено наличие или отсутствие обезуглероживания. Для сталей кон кретных марок экспериментально заблаговремен но устанавливают разницу в показаниях прибора, полученных при анализе обезуглероженного и необезуглероженного образцов.
С помощью внешней электрической цепи тем пература стержня 1 поддерживается в интервале 150-160 °С. Образец 3 помещают на медное осно вание 2 прибора так, чтобы лыска находилась точ но под рабочей частью нагретого стержня 1. По результатам 3—5 замеров, произведенных в преде лах лыски, подсчитывают среднюю величину по казаний микроамперметра 4. Такие же замеры (5 - 10) выполняют в различных точках поверхности образца (вне лыски) и подсчитывают среднее зна чение. Образец считается необезуглероженным, если разница в показаниях прибора на лыске и на поверхности образца не превышает величины, установленной по эталонам.
Химический метод (X) состоит в определении содержания углерода в стружке, снятой послойно с поверхности образца. Образцы отбирают от го тового металла. Длина образцов должна обеспечи вать количество стружки, достаточное для прове дения анализа. Стружку снимают слоями толщи ной не более 0,1 мм. В каждом слое содержание углерода определяют до получения химического состава, соответствующего марочному. Образец считается необезуглероженным, если в первом слое содержание углерода соответствует марке стали. Глубина обезуглероживания определяется по суммарной толщине слоев, в пределах которых стружка снималась до получения марочного со става.
Метод X применяется только выборочно при проверке других методов или проведении иссле дований. В заводских условиях глубину обезугле роженного слоя иногда контролируют визуально по излому. В этом случае он используется для отожженных прутков (до 30 мм) из углеродистой и легированной инструментальной стали. На прутке делают зарубку, по которой отламывают его конец длиной 30-50 мм. При наличии обезуглероженно го слоя в изломе видна кайма из блестящих, обыч но более крупных зерен. Появление каймы при отжиге заэвтектоидных сталей связанно с тем, что обезуглероженный слой перегревается (вследствие отсутствия избыточных карбидов) и при охлажде нии в нем образуется крупнопластинчатый перлит. Хрупкий излом проходит по границам зерен аустенита или перлитных колоний, вязкая мелко кристаллическая сердцевина имеет структуру зернистого перлита.
Металлографически различают зоны полного и частичного обезуглероживания. Зона полного обез углероживания характеризуется структурой толь ко феррита. Зона частичного обезуглероживания
имеет строение, которое отличается от структуры основного металла. Также различают равномерное обезуглероживание (по всему периметру образца) и местное обезуглероживание, которое обнаружи вается только на отдельных участках периметра.
Сущность металлографических методов (М, M l, М2) состоит в определении глубины обезуг лероженного слоя по структуре, видимой в микро скопе при увеличении х(63-И50). Измерения про водят с помощью окуляр-микрометра с точностью ±0,02 мм (рис. 3.1.44).
Металлографический метод М применяют при определении глубины обезуглероженного слоя конструкционных — углеродистых и легирован ных сталей с содержанием углерода не менее 0,3 %, инструментальных — углеродистых и леги рованных, а также рессорно-пружинных и под шипниковых сталей. Метод Ml (метод карбидной сетки) используется для анализа заэвтектоидных сталей, а метод М2 (метод Садовского) — для бы строрежущих.
С помощью метода М определяют глубину обезуглероженного слоя на поперечных травленых шлифах металла, находящегося в состоянии по ставки. Образцы вырезают так, чтобы плоскость шлифа была перпендикулярна исследуемой по верхности (рис. 3.1.45). Рекомендуемая площадь шлифа — до 10 см2
Шлиф изучается по периметру, соответствую щему поверхности проката. На образцах, вырезан ных из полосы и ленты, исследуют широкую сто рону на расстоянии не менее 2 мм от внешней кромки. Травление шлифа производят в реактивах, позволяющих отчетливо выявить структурные со ставляющие (2-4% раствор азотной или пикрино вой кислоты в этаноле). Зона частичного обезуг лероживания характеризуется:
•для доэвтектоидной стали феррито-перлит ной структурой, причем содержание феррита больше, чем в основной структуре;
•для заэвтектоидной стали — феррито-пер литной структурой или структурой пластинчатого
перлита при основной структуре зернистого пер лита.
У сталей со структурой зернистого перлита зо на частичного обезуглероживания обеднена кар бидами по сравнению с основной структурой.
Рис. 3.1.45. Схемы вырезки образцов с указанием площади перпендикулярного сечения полуфабриката (проката различных профилей) для определения глубины обезуглероживания по методу М:
а— диаметр или толщина до 30 мм — все сечение;
б— диаметр или толщина от 30 до 60 мм — половина сечения; в — диаметр или толщина от 60 до 100 мм— четвертая часть сечения; г — диаметр или толщина от 100 до 150 мм — шестая часть окружности
или угол квадрата
Общая глубина обезуглероживания измеряется от края внешней поверхности образца до основной (внутренней) структуры стали. Если зона полного обезуглероживания отсутствует, то измеряют зону частичного обезуглероживания металла от края шлифа до основной структуры. Общую глубину обезуглероженного слоя (в мм) определяют в мес те его наибольшего развития. Допускается рас смотрение шлифа при увеличениях х(20(Ь-500).
Глубину обезуглероживания И также можно определить в процентах по формуле
И= 100-,
ь
где а _ глубина обезуглероженного слоя при од ностороннем измерении, мм; Ъ — толщина прока
та или полуфабриката, мм.
Метод М имеет ряд преимуществ: простота подготовки образцов, высокая точность оценки, контроль металла непосредственно в состоянии
поставки.
Для использования методов Ml и М2 из прутков вырезают образцы длиной 5-12 мм. Если диа метр прутка меньше 25 мм, то на образце сошлифовывают площадку (лыску) до полного удаления обезуглероженного слоя (рис. 3.1.46).
Плоскость
Рис. 3.1.46. Отбор образцов и площадь исследуемого участка при определении глубины обезуглероженного слоя по методу М2:
а— прутки диаметром до 25 мм— по всему сечению, лыска (2-3 мм) снимается до полного удаления обезуглероженного слоя;
б—прутки диаметром от 25 до 40 мм — на половине площади сечения;
в— прутки диаметром более 40 мм
В методе Ml, который используется преимуще ственно в исследовательской практике, образщ подвергаются специальной термообработке окрашивающему травлению. Вначале образцы на гревают до 950 °С в ваннах с различными распла вами, чтобы исключить обезуглероживание, на пример в расплаве поваренной соли с добавление: 0,5-2,0 % активированного угля. Там их выдержи вают 5-7 мин, а затем охлаждают со скоросты 15-30 С/мин до температуры, которая на 30—50 ниже точки Аг\, и остужают на воздухе.
При |
использовании м ет о д а |
М 2 (м е т о д СадоЕ |
ского |
для оценки гл уби н ы |
о б е зу г л е р о ж е н н о г |
слоя в быстрорежущих сталях) образцы предвари тельно нагревают до 820-840 °С, затем их перено сят в хорошо раскисленную хлорбариевую ванну, где выдерживают в течение 1-3 мин. В зависимо сти от марки сталей температура ванны выбирается в интервале 1210-1290 °С (табл. 3.1.3.15). После этого образцы охлаждают в масляной или соляной (первой) ванне в течение 10 мин. Температура этой ванны также зависит от марки сталей и нахо дится в пределах 160-220 °С. Далее образцы пере носят в другую соляную или свинцовую (вторую) ванну с температурой 580-560 °С, где их выдер живают 10 мин, а затем охлаждают на воздухе. Объем ванны должен быть достаточным для под держания температуры в заданных пределах.
Таблица 3.1.3.15
Режимы термической обработки образцов некоторых марок быстрорежущих сталей*
|
Температура закалки |
Температура |
Марка стали |
(хлорбариевая ванна), |
первой ванны |
|
°С |
охлаждения, °С |
Р9 |
1220-1240 |
160-180 |
Р12 |
1240-1260 |
175-195 |
Р18 |
1270-1290 |
175-195 |
Р6МЗ |
1210-1230 |
175-195 |
Р9Ф5 |
1230-1250 |
190-210 |
Р14Ф4 |
1240-1260 |
200-220 |
Р18Ф2 |
1270-1280 |
180-200 |
Р9К5 |
1220-1240 |
160-180 |
Р9ЮО |
1220-1240 |
160-180 |
Р10К5Ф5 |
1230-1250 |
180-200 |
Р18К5Ф2 |
1270-1280 |
180-200 |
* Температура второй ванны (отпуска) 580-600 °С.
Для выявления структуры шлифы травят в 2-4% растворе азотной или пикриновой кислоты в эта ноле (можно и в других реактивах) до четкого вы явления структурных составляющих. Если шлиф травят в 4% растворе азотной кислоты в метаноле, то после промывки его необходимо просушить теплым воздухом. После травления в течение 5-30 мин в кипящем реактиве, окрашивающем карбидную сетку, в пределах зоны частичного обезуглероживания сетка выглядит светлой на фо не феррито-перлитной структуры (в методе M l) и трооститной или игольчатой троостито-мартенситной
структуры (в методе М2). У поверхности образцов зона полного обезуглероживания характеризуется структурой феррита. Следует обратить внимание на методическую сложность методов Ml и М2, а также зависимость получаемых результатов от колебаний температуры в первой и второй ваннах. Поэтому эти методы часто заменяют способом измерения ТЭДС.
В дополнение к металлографическому методу определения глубины обезуглероженного слоя разработан и находит применение способ Т, осно ванный на замерах твердости образцов после тер мической обработки. Он применяется для прутков из шлифованной и калиброванной стали диамет ром не более 30 мм. Образцы длиной 20-50 мм подвергают термической обработке в условиях, исключающих возможность дополнительного обезуглероживания. Режимы регламентируются установленными стандартами или техническими условиями на поставку полуфабрикатов. Твер дость (по Роквеллу) замеряют на поверхности об разцов для продукции, в которой обезуглерожива ние не допускается, а также для продукции, где обезуглероживание допускается, но после снятия допуска на обезуглероживание. Образец считают необезуглероженным, если его твердость соответ ствует установленным нормам или техническим условиям для данной марки стали. Метод Т можно использовать для всех сталей, но обычно его при меняют только для калиброванной шарико- и ро ликоподшипниковой стали.
Приведенными примерами решения типовых матсриаловсдческих задач методами металлогра фии не исчерпывается их многообразие, которое встречается на практике. Можно указать доста точное количество рекомендаций и требований нормативных документов, управляющих качест вом металлопродукции. В основу многих из них заложен принцип полуколичественной оценки вы явленных структурных особенностей. Например, для углеродистых инструментальных сталей в ГОСТ 1435 приводятся шкалы для оценки перлит ной составляющей по 10-балльной системе. Опи сание структуры перлита в инструментальных легированных сталях, приведенное в ГОСТ 5950, несколько другое. Встречаются отличия в оценках карбидной неоднородности, рекомендуемые для быстрорежущих сталей лсдебуритного класса (ГОСТ 19265) и заэвтсктоидных (ГОСТ 801). Сис
тема оценок с помощью баллов используется и для определения содержания a -фазы металлографиче ским методом (ГОСТ 11878) в нержавеющих ста лях аустенитного класса. Несмотря на то что спо собы полуколичественного описания достаточно просты и удобны при текущем экспресс-контроле производимой металлопродукции, они все меньше соответствуют возрастающим требованиям к каче ству металла и надежности металлоконструкций, которые работают в экстремальных условиях с высокими динамическими нагрузками и при низ ких температурах. Общемировая тенденция в со вершенствовании технологии контроля и методов испытаний материалов состоит в отказе от субъек тивности оценок с помощью шкал и переходе к автоматизированным анализаторам структурного состояния в металлах и сплавах с участием кон троллера-оператора. Например, в американских стандартах ASTM Е 112 уже с середины 1980-х гг. определение размеров зерна в сталях аустенитного класса регламентируется как для ручного режима измерений, так и с помощью автоматического ана лизатора изображений (ААИ). Разработаны спе циализированные методики для работы с ААИ: при обнаружении включений (ASTM Е 1122), описании структур (ASTM Е 1245), оценке разнозернистости (ASTM Е 1382) и др. Активное вне дрение способов компьютерной обработки и ана лиза изображений структур происходит во всех промышленно развитых странах, в том числе и в России.
Литература
1.Ежегодный сборник стандартов ASTM. 1987.
Ч.З(Е). Т. 3.01.
2.Металловедение и термическая обработка ста ли: Справ.: В 3 т. Т. 1 Методы испытаний и исследования / Под ред. М.Л. Бернштейна, А.Г. Рахштадта. М.: Металлургия, 1983. 352 с.
3.Методы контроля и исследования легких спла вов: Справ. / А.М. Вассерман, В.А. Данилкин, О.С. Коробов и др. М.: Металлургия, 1985. 510с.
4.Справочник по практическому металловеде нию / В.Л. Пилюшенко, Б.Б. Винокур, С.Е. Конд ратюк и др. Киев: Техника, 1984. 135 с.
5.Vander Voort G.F. Новое в стандартах по ме таллографическим испытаниям // Advanced Mater, and Processes. 1990. V. 138, N 5. P. 30-38.
3.1.4. Автоматизация эксперимента и применение анализаторов изображений
Современная |
м еталлограф ия н е |
м о ж е т |
о гр а н и |
|||
чиваться |
только |
к ачественны м |
(о п и са т ел ь н ы м ) |
|||
исследованием вн утр ен н его ст р оен и я |
м атери ал а . |
|||||
В связи |
с уж есточ ен и ем |
т р еб о в а н и й |
к |
к ач еств у |
||
производимой м етал л оп р одук ц и и , |
р азр а б о т к о й и |
|||||
внедрением материалов с о |
сп ец и ал ь н ы м и |
св о й с т |
||||
вами, появлением новы х т ех н о л о ги ч еск и х |
п р о ц е с |
сов все больш ее вним ание уд ел я ет ся п р о б л ем е п о лучения достовер н ой к ол и ч еств ен н ой и н ф о р м а ц и и
о процессах, п р ои сходя щ и х в |
м етал л ах и сп л ав ах |
как на стадии их изготовления, |
так и эк сп луатац и и . |
Благодаря интенсивному развитию средств вы числительной техники в практическом материало ведении получают распространение приборы, оснащенные специализированными приставками, фотокамерами и программными продуктами, дающими возможность быстро и эффективно об рабатывать изображения с распознаванием основ ных объектов структуры, таких как неметалличе ские включения, границы зерен, отдельные фазы, слои с измененным строением и пр. Внедрение средств автоматизации в оптические методы ис следования и анализа структур осуществляется на основе представлений стереологии — науки о пространственном строении материалов и спосо бах его определения.
3.1.4. L Основы количественной металлографии
Чтобы установить соответствие между внут ренним строением материала и его свойствами, выражаемыми количественно (напряжения, дефор мации, магнитные характеристики и др.), необхо димо также количественно описывать и структуру как область, доступную для наблюдения.
Существует несколько критериев, на основании которых можно классифицировать структуры. Один из них — количество фаз или структурных составляющих. Как известно, в термодинамике фазой называется часть системы, имеющая одина ковые физико-химические свойства и отделенная от остальной системы поверхностью раздела. Од нофазной структурой обладают чистые металлы и твердые растворы. В зависимости от масштаба частицами в этой структуре являются зерна (кри сталлиты), двойники и субзерна. В однофазном поликристалле фаза идентична структурной со ставляющей и существуют границы только одно
го типа — межчастичные. Многофазную структу ру имеют композитные материалы, а также литые и деформированные сплавы после определенных режимов термической обработки (состаренные твердые растворы, отожженные, нормализованные стали).
Наиболее типичной многофазной структурой является матричная структура, в которой частицы избыточных фаз (например, неметаллических включений) погружены в основную фазу — мат рицу. Часто матрицей считают ту фазу, которая занимает наибольшую часть объема структуры, например кристаллиты твердого раствора в соста ренном сплаве. В этом случае матричная фаза оправдывает свое название — частицы избыточ ной фазы «рождаются» в ней.
Существуют и другие критерии для выбора матрицы, например сопротивление разрушению. Так, в спеченных твердых сплавах, состоящих из хрупких частиц карбидов, занимающих до 90 % объема структуры, и вязкой металлической связки, матрицей, как правило, считают связующую фазу, хотя ее объем невелик.
Взависимости от количества избыточной фазы
исочетания физико-химических свойств этой фа зы и матрицы матричные структуры различаются степенью непрерывности или связанностью час тиц избыточной (второй) фазы. Два предельных случая матричной структуры (рис. 3.1.47) — пол ностью связанная (в которой между любыми дву мя частицами второй фазы существует непрерыв ный путь по другим частицам этой фазы) и полно стью разделенная (ни одна пара частиц второй фазы не образует контакта). Фаза и структурная составляющая в матричной структуре — понятия идентичные. В такой структуре имеются границы (поверхности раздела) двух типов — межфазные и межчастичные.
Рис. 3.1.47. Виды матричных структур:
а — несвязанная; б — связанная
Сущ ествование границ первого типа н е зависит от степени непреры вности второй фазы . В п ол н о - стью разделенной матричной структуре отсутст вуют межчастичные границы. Частицы несколь ких фаз, сосущ ествую щ их в сравнимы х количест
вах и достаточно равномерно распределенны х по
объему материала, образую т см еш анную структу ру. В общ ем случае смеш анная структура с точки
зрения стереологии — один из видов связанной
матричной структуры, в которой ф аза идентична
структурной составляющ ей. О днако в некоторы х случаях бывает удобно считать см еш анной такж е однофазную структуру. Тогда частицы одн ой ф а зы, имею щ ие, например, различную ф орм у (р аз
личное число граней или ребер), будут представ лять различные структурные составляю щ ие.
Понятия фазы и структурной составляю щ ей
могут оказаться неидентичными в доэвтек тои дн ы х (доэвтектических) или заэвтектоидны х (заэвтекти -
чсских) структурах. Например, для оп ределен и я
количества, размеров и других характеристик п ер
литных колоний в доэвтектоидны х отож ж ен н ы х
сталях частицами считают эти колонии (хотя они состоят из двух фаз), а структуру представляю т
как матричную. |
|
С позиций рационального сп особа |
изм ерения |
выделенных структурных элем ентов и |
п о сл ед у ю |
щей статистической обработки данны х |
независи |
мо от специфических особенностей строения (ф аз) в металловедении выделяют пять геом етрических типов структур (рис. 3.1.48).
О д н о ф а з н о п о л и э д р и ч е с к а я структура состои т
из примерно равноосных зерен одной и той ж е ф а зы (за исключением неметаллических вклю чений, пор и других дефектов). Рассматриваю тся только
поверхности раздела одинаковых структурны х
составляющих. Такой тип структуры характерен для чистых металлов и тверды х растворов (напри мер аустенитных и ферритных сталей, одн оф азн ы х а-латуней, сплавов Си— N i и др.).
М н о г о ф а з н о |
п о л и э д р и ч е с к а я структура в осн о в |
|
ном состоит |
из |
приблизительно равноосны х кри |
сталлов двух |
или более фаз (структурны х состав - |
ляющих), причем поверхности раздела проходят между фазами как одного типа, так и ф азам и р аз ных типов. Структуры такого типа встречаю тся
в феррито-перлитных доэвтектоидны х сталях и двухфазных а + р латунях.
д
Рис. 3.1.48. Основные геометрические типы металлографических структур:
а— однофазно полиэдрическая;
б— многофазно полиэдрическая; в— сетчатая;
г— матричная; д — ориентированная
Сетчатая структура характеризуется образова нием более или менее сплошной сетки одной фазы вокруг зерен второй фазы (структурной состав ляющей). В случае сплошной сетки существуют только поверхности раздела между структурными составляющими разных типов. Характерным при мером сетчатого строения является структура вто ричного цементита в заэвтектоидных сталях.
Матричная структура состоит из фазы, обра зующей основу (матрицу), в которой более или менее равномерно располагаются частицы одной или нескольких дисперсных фаз другой природы. Такая структура характерна для стареющих спла вов с выделениями вторичных фаз, для легирован ных сталей с карбидными или нитридными части цами, для чугунов с графитными включениями.
Ориентированная |
стр уктур а |
ха р а к т ер и зу ется |
|
пространственным вы тягиванием |
о д н о й |
и л и н е |
|
скольких фаз. П р и м ер ом такого ст р оен и я |
я в л я ю т |
||
ся вытянутые зерн а |
п ласти ч еск и |
д еф о р м и р о в а н |
|
ных металлов и сплавов. |
|
|
На практике встречаются комбинации приве денных видов. Путем выбора методики подготов ки образца, соответствующих увеличений микро скопа или режимов наблюдения (например, иссле дования травленого и нетравленого шлифов) даже в случае сложных структур удается произвести их идентификацию с помощью рассмотренных гео метрических типов.
Таким образом, различные структуры компакт ных материалов можно рассматривать либо как однофазные, либо как двухфазные матричные с различной степенью связанности частиц второй фазы. Структуру спеченных пористых материалов, получивших широкое распространение в совре менной технике, также можно считать двухфазной матричной, в которой второй фазой являются поры.
Особый случай представляет неконсолидиро ванная структура неспрессованного и неспеченного порошка, которая может состоять из частиц не скольких фаз (например, карбида вольфрама и ко бальта — в смесях, предназначенных для произ водства твердых сплавов). Хотя в этом случае фи зические контакты между частицами отсутствуют, для описания распределения фаз можно использо вать представление о связанности (степени непре рывности), рассмотренное выше для двухфазной матричной структуры.
Из двух рассмотренных критериев классифика ции структуры — количества фаз (структурных составляющих) и связанности частиц — один из них (второй) является стереологическим парамет ром. Он характеризует взаимное расположение фаз (составляющих), т. е. распределение элемен тов структуры в пространстве.
Другой характеристикой распределения струк турных элементов является их ориентировка, ко торая также может служить критерием для клас сификации структур. Полностью изотропной (изометрической) называется структура, в которой равновероятны все возможные ориентировки рас сматриваемых структурных элементов (частиц, поверхностей и линий). Подробная классификация ориентированных структур рассматривает в ос
новном симметричные ориентированные структу ры трех типов:
•линейную, в которой элементы структуры преимущественно параллельны определенному направлению, являющемуся осью симметрии. Так ориентированы зерна и вытянутые частицы неме таллических включений в доэвтектоидных сталях после волочения;
•плоскостную, в которой элементы структу ры параллельны некоторой плоскости и имеют все возможные ориентировки относительно направле ния, перпендикулярного этой плоскости. Это на правление является осью симметрии. Такое строе ние может возникнуть в результате листовой про катки, осаживания и некоторых других видов пластической деформации;
•плоскостно-линейную, элементы которой параллельны одновременно и некоторой плоско сти, и одному из направлений этой плоскости. Такая структура не обладает цилиндрической сим метрией и возникает при вальцовке, прокатке лен ты и т. п. (рис. 3.1.49).
Рис. 3.1.49. Типы ориентировки частиц в структуре:
а — линейная; б— плоскостная; в— плоскостно-линейная; НО — направление ориентировок;
ПО — плоскость ориентировки; ОС — ось симметрии
Структура реальных металлов и сплавов, как правило, не бывает идеально ориентированной. Приближенно ее можно представить как суперпо зицию изотропной и ориентированной частей. В этом случае отношение ориентированной доли структуры ко всему ее объему будет характеризо вать степень ориентировки. Более строгий способ описания ориентировки дает распределение эле ментов структуры по ориентировкам.
Таким образом, в дополнение к вышерассмот ренным двум характеристикам структуры — свя занности и ориентировке — для полной классифи кации структурных типов необходимо добавить другие количественные параметры:
• суммарную протяженность (плотность) двумерных (поверхностей раздела) и одномерных (линейных) элементов в заданном объеме или единице объема;
•объем всех частиц данной фазы в заданном объеме или в единице объема структуры (объем ная доля фазы);
•характеристику формы частиц и кривизны
поверхностей с угловыми параметрами.
Но количественные характеристики простран ственной структуры нельзя определить путем «не посредственного» ее наблюдения или изображе ний, поскольку они дают информацию о внутрен нем строении лишь в виде проекций или сечений. Переход от первичных измерений в плоскости изображения к пространственному представлению структуры осуществляется методом стереологической реконструкции. Он предполагает последова тельное решение следующих задач:
•выбор оптимальных параметров пространст венной структуры в связи с рассматриваемой материаловсдческой проблемой;
•подбор или разработку способа получения первичной информации (проведения измерений) о необходимых параметрах;
•преобразование первичной информации в
количественную оценку параметров объемной структуры.
При изучении шлифов, фолы и экстракцион ных реплик реальные размеры частиц не соответ ствуют в полной мере своим изображениям в плоскости наблюдения. Реальные размеры можно воссоздать путем реконструкции изображения. При изучении порошковой пробы реконструкция либо нс нужна вообще (в случае сферических час
тиц), либо невозможна, когда частицы имеют про извольную форму. Для осуществления стереологической реконструкции необходимо установить количественную зависимость между числами и размерами изображений и частиц в исследуемой структуре, т. е. получить решение интегрального уравнения:
n{d) = \\PiJ{D ,f)N {D )dD df
в виде |
7V(D) = F[n(dj\, |
где ру — геометрическая вероятность, опреде ляющая вклад частиц различных размеров и ори ентировок D{f) в размерные интервалы изображе ний dj.
Количественное описание структур дается сте реологией на основе представлений о геометриче ской структуре как совокупности точечных, ли нейных, поверхностных и объемных элементов, определенным образом размещенных в простран стве. В качестве примера для металлов и сплавов можно назвать следующие геометрические струк туры:
•точечные (общие вершины четырех зерен, углы дислокационной сетки);
•линейные (общие ребра трех зерен — «трой ные стыки», сегменты дислокаций);
•поверхностные (границы между фазами);
•объемные (зерна, выделения, поры). Реконструкция реальной пространственной
структуры металла или сплава по элементам гео метрической структуры может быть осуществлена двумя принципиально различными способами. В первом, который называется непосредственной реконструкцией, воссоздается пространственная модель — точная копия реальной структуры — с последующим количественным определением ее свойств. Такая модель строится с помощью после довательных сечений серией параллельных плос костей с малым шагом в предположении, что ис комые характеристики структуры типичны для исследуемого материала (выполнение требования представительности выборки). В данном методе предусматривается только одна статистическая выборка — представительный объем (образец ма териала), по отношению к которому структура представляет генеральную совокупность. Другой подход, называемый статистической реконструк