
книги / Металлы и сплавы. Анализ и исследование. Физико-аналитические методы исследования металлов и сплавов. Неметаллические включения
.pdfструктуру сталей выявляют посредством магнит ных полей рассеяния, создаваемых магнитной не однородностью. В случае намагничивания образца внешним магнитным полем эффект выявления ферромагнитных включений обусловливается ве личиной остаточной намагниченности и коэрци тивной силой включений. За счет взаимодействия с полями спонтанной намагниченности структур ных составляющих исследуемого металла частицы образуют локализованные сгущения и узоры. При последующем просмотре с помощью оптических средств (увеличительных стекол, микроскопов) фазы с магнитными свойствами выглядят темны ми, а немагнитные (аустенит и специальные кар биды) — светлыми.
При этом карбиды легко отличить от аустенита по их четкой округлой или угловатой форме.
Применение магнитного метода эффективно для установления наличия остаточного аустенита в углеродистых и легированных инструменталь ных сталях. Высокая чувствительность метода, не уступающая методу рентгеноструктурного анали за, позволяет не только обнаружить присутствие этой фазы, но и оценить ее распределение в струк туре. Магнитный способ удобен для выявления неоднородного распределения мартенсита по сече нию прутков или листов сталей. Магнитная метал лография может быть также применима при кон троле полноты отпуска быстрорежущих сталей. С этой целью необходимо произвести сопоставле ние «магнитной» микроструктуры сдаточного об разца с эталонной, которая получена на шлифе другого образца после дополнительного отпуска. В жаропрочных сталях и наплавленном металле сварного шва таким методом может быть выявле но присутствие а-фазы.
Структуру, выявленную магнитным методом, следует фотографировать во влажном состоянии. При изучении микроструктуры методом магнит ной металлографии детали предметного столика микроскопа, изготовленные из железа, заменяют на медные или латунные.
Литература
1.Киселева С.А., Файвилевич Г.А. Цветная ме таллография. М.: ГНТИЧМ, 1960. 110 с.
2.Способы металлографического травления: Справ. / Пер. с нем. М. Беккерт, X. Клемм. М.: Металлургия, 1988. 400 с.
ЗЛ.З. Решение типовых задач практического материаловедения: определение размера зерна, оценка фазового состава в сталях и титановых сплавах, установление глубины обезуглероженного слоя
В течение XX века были достигнуты выдаю щиеся успехи в области улучшения комплекса свойств металлических сплавов за счет изменения их химического состава. Тем не менее, к концу столетия стало очевидным, что для основных классов конструкционных металлических мате риалов, произведенных с помощью традиционных металлургических технологий, возможности даль нейшего роста их эксплуатационных параметров только за счет легирования практически исчерпаны. Однако для этих материалов еще имеются огром ные, до конца не использованные возможности повышения механических свойств путем целена правленного изменения структуры. Среди основ ных факторов воздействия следует указать на из мельчение зерна, изменение концентрации и рас пределения фазовых составляющих, улучшение свойств межфазных границ и др. Одним из ярких примеров их проявления является появление ново го класса материалов — нанокристаллическик.
Ограничения действия законов классической фи зики, вызванные их малым (< 100 нм) геометриче ским размером, рост удельной поверхности и доли поверхностной энергии до значений, сравнимых с объемной энергией, обнаружили у наночастиц но вые магнитные, электрические, оптические, меха нические и другие свойства. Причем это относится не только к конструкционным металлам и спла вам, но и к очень широкому кругу материалов раз ных сфер назначения.
3.1.3.1. Определение величины зерна в металлах и сплавах
Среди задач, которые в практическом материа ловедении необходимо решать наиболее часто, на первом месте по важности следует указать на не обходимость определения размера зерна. Боль шинство технических металлов и сплавов пред ставляют собой поликристаллические объекты, состоящие из достаточно многих статистически беспорядочно ориентированных кристаллов (зерен). Зерна отделены друг от друга более или менее сильно искаженными приграничными объемами — границами. Очевидно, что физико-химические,
в том числе прочностные и пластические свойства поликристаллов теснейшим образом связаны со свойствами их зерен. Однако механическое пове дение отдельных свободных кристаллитов (моно кристаллов) не определяет свойства поликристал лов, во всяком случае, те, которые обусловлены взаимодействием зерен со своими соседями. Экс периментально установленные и теоретически проверенные различия в механическом поведении моно- и поликристаллов металлических материа лов заключаются в следующем:
1. В главных системах скольжения отдельных зерен поликристаллического тела действуют раз личные приведенные касательные напряжения:
Ту Ф Т)к Ф Тik•
Это неравенство определяется различной ори ентировкой зерен (для монокристаллов т,= const).
2.Границы зерен (приграничные объемы) пре пятствуют развитию скольжения и передаче де формации из зерна в зерно. В поликристаллическом теле заметная макроскопическая деформация наблюдается при более высоких напряжениях, чем
вмонокристалле.
3.При воздействии внешних сил на поликристаллический объект в границах между соседними различно ориентированными зернами должны вы полняться определенные условия совместимости (аккомодации) их деформации в прилегающих приграничных объемах.
4.Приложение внешней нагрузки способно ак тивизировать определенные участки границ зерен, которые начинают действовать как источники дислокаций. Это приводит к увеличению плотно сти дислокаций внутри зерна, из чего следует, что при равной по величине деформации монокри сталла или отдельного зерна в зернах поликри сталла плотность дислокаций будет всегда выше, чем в монокристалле.
5.Из экспериментальных наблюдений за изме нением состояния (геометрии) поверхности поли кристаллического объекта не представляется воз можным непосредственно делать выводы о про цессах, происходящих внутри тела. В случае монокристаллов по образующимся на поверхности уступам и другим нарушениям геометрии поверх ности можно судить о развитии некоторых стадий пластической деформации.
Влияние размера зерна на прочность металли ческих поликристаллов при невысоких (не опре
деляющих развитие приграничного скольжения) температурах связывают с концентрацией напряже ний в индивидуальных полосах скольжения, акти вируемых сдвиговой компонентой приложенного напряжения. Основные положения этой теории:
-границы зерен являются непроницаемыми барьерами для распространения дислокационного скольжения и двойникования;
-внутризеренная концентрация напряжений, которые необходимы для начала текучести и по следующего пластического течения, не зависит от размера зерна.
Исходя из этих положений, зависимость на пряжения сдвига от протяженности полосы скольжения (или среднего диаметра зерна) d запи сывают в виде:
т = то + ks d ~m,
где т0 — напряжение сдвига, необходимое для то го, чтобы вызвать скольжение в отсутствие сопро тивления со стороны границ зерен; ks — коэффи циент, характеризующий концентрацию напряже ний у вершины полосы скольжения.
В случае объемного макроскопического пла стического течения поликристаллического метал ла напряжение течения должно быть достигнуто во всех зернах. При этом необходимо учитывать средний ориентационный фактор М, который определяет трансформацию действующих систем скольжения внутри зерен в систему координат тензора объемной деформации. Тогда т связано с внешним приложенным напряжением: о =Мх. И если предполагать, что каждое зерно поликри сталла деформируется так же, как и объем мате риала, то уравнение, известное как соотношение Холла — Петча, примет вид:
а = Мхо + Mksd~m
Для металлов с ГЦК решеткой М= 3,1. В слу чае ОЦК решетки М = 2,9, а для ГПУ модифика ции М= 6,5.
Так как в каждом зерне пластическая деформа ция осуществляется в результате движения дисло каций в своих системах скольжения, то для обес печения микроскопической связи зерен по их гра ницам и сохранения сплошности среды должны в общем случае действовать пять независимых друг от друга систем скольжения. В субмикроскопиче-
ских областях вблизи границ зерен должны проте кать локализованные, но объемно связанные друг с другом процессы скольжения, обеспечивающие согласование деформаций приграничных объемов. Тогда среднее значение напряжения a(d), возник шего при механическом нагружении поликристаллического материала, должно состоять из двух со ставляющих: оф, которая определяет согласован ную деформацию приграничных объемов, и ствп, которая действует внутри (в сердцевине) зерна. Если (d) — средний поперечник зерна (в дальней шем для краткости называемый величиной зерна), то можно формально записать:
а ((ф ) = Оф + а В||.
Выяснение роли размера зерна в формировании механических свойств металлов и сплавов значи тельно упростилось бы при зависимости величины ствп от величины зерна. Однако в большинстве слу чаев это не выполняется из-за влияния границ зерен (приграничных объемов) и изменений во внутризеренных объемах (формирование субструктуры). Принципиальная трудность оценки влияния вели чины зерна на свойства металлов и сплавов состо ит в том, что чаще всего неизвестно, в каком соот ветствии находятся внутризеренные и пригранич ные объемы для разных образцов одного и того же материала с различной средней величиной зерна.
Иногда разницу в механическом поведении поликристаллического материала и монокристалла сводят к различной интенсивности деформацион ного упрочнения вследствие вариации температу ры, увеличения деформации или изменения ее скорости. При этом деформирующее напряжение а(е) связывают с плотностью дефектов p(s) кри сталлического строения и средним размером зерна (d). В модифицированной записи зависимость Холла — Петча выглядит так:
ст(е) = ст0 + aGbjp(e) + т _ № ) '
Здесь сто — сопротивление пластической де формации за счет других (помимо дислокаций и границ зерен) факторов; b — вектор Бюргерса дислокаций; G — модуль сдвига; а и р — геомет рические множители, причем Р — фундаменталь ная характеристика металла, ибо она есть мера
трудности генерации дислокационных петель у межзеренных границ.
При высоких температурах или деформирую щих напряжениях в приграничных объемах зерен как в наиболее искаженных участках эксперимен тально наблюдается преимущественное развитие деформации, которая вносит значительный вклад в общую деформацию поликристаллического тела. В поликристаллическом металле или сплаве зерна деформируются неизотропно и негомогенно. По этому при упругом и упругопластическом поведе нии поликристалла в процессе его механического нагружения важным положением является сохра нение контакта между отдельными зернами, со прикасающимися по своим границам. Из этого следует, что деформированное состояние соседст вующих зерен должно быть таким, чтобы обеспе чить приспосабливание одних зерен к другим вблизи их границ (в приграничных объемах). В по ликристаллическом теле главенствующее влияние границ на его механические свойства состоит как раз в том, что в определенных (конечных) облас тях зерен по обе стороны от общей границы долж но быть согласованное развитие деформации, обеспечивающее совместимость зерен. Несовме стность их упругой деформации приводит к воз никновению концентраторов напряжений на гра ницах, которые инициируют появление новых дислокаций. Для случая плоской границы раздела между двумя зернами I и II в конгломерате четы рех зерен нагруженного поликристалла картина изменения локальных напряжений представлена на рис. 3.1.29. В схеме «свободных» зерен на гра нице раздела их упругая деформация различается на величину А/. Жесткость связи смежных зерен в поликристалле обусловливает одинаковую длину их границы раздела. Поэтому приграничный слой зерна I упруго более деформирован, чем сопря женный с ним слой зерна II.
Несовместность упругих деформаций зерен I и II на их общей границе приводит к возникновению осциллирующих в пространстве нормальных а,, и тангенциальных хху локальных напряжений. Ха рактер осцилляции локальных напряжений опре деляется выражением
\ х - а J
где х — координата точки границы раздела.
Изменение амплитуды напряжений обязано условию неподвижности граничных точек х =± а в стыках нескольких зерен. Реальный характер осцилляции локальных напряжений на границе раздела двух упруго нагруженных сред сильно зависит от граничных условий в точках х - ± а . Для абсолютно неподвижных точек х = ± а напря жение Т;*-мо. В действительности все точки на границе раздела имеют определенные смещения, поэтому в точках х - ± а напряжения конечны. Малая подвижность точек х = ± а в стыках трех зерен в нагруженном поликристалле обусловлива ет очень высокую концентрацию локальных на пряжений в этих точках. По мере удаления от то чек тройных стыков вдоль границы раздела — а < х < +а амплитуда осцилляции локальных на пряжений уменьшается.
Распределение локальных напряжений, пока занное на схеме (рис. 3.1.29), имеет место не толь ко в условиях растяжения, но и в условиях сжатия при ковке или прокатке, когда размер деформи руемого образца меньше размера недеформируемой плиты пресса (молота, валков).
б
внагруженном поликристалле:
а— деформация «свободных» зерен;
б— локальные напряжения на границе раздела зерен 1 и 11 в «жестком» поликристалле
Для конструкционных сталей массового назна чения измельчение зерна необходимо не только для повышения прочности, но и для понижения температуры перехода в хрупкое состояние — по рога хладноломкости. При этом обычно наблюда ется и повышение уровня вязкости, как при темпе ратурах выше порога хладноломкости, так и ниже его. Одной из главных причин этих эффектов яв ляется увеличение удельной поверхности границ зерен. Во многих металлических сплавах наличие развитой межзеренной поверхности позволяет ис пользовать ее для формирования упрочняющих фаз, которые наряду с упрочнением затрудняют распространение трещин в условиях как статиче ских, так и динамических нагрузок.
З.1.З.2. Выявление границ зерен
Практическое исследование зеренного строения металла или сплава следует начинать с выявления границ зерен. Для этого разработаны различные способы. Из них большинство основано на хими ческом или электролитическом травлении. Реак тив, выявляющий зерно, должен воздействовать только на его границу, не нарушая рельеф на плоскости зерна. Например, для сталей большин ство реактивов для травления содержит пикриновую кислоту. При весьма продолжительном травлении (20-30 ч) насыщенные растворы пикриновой ки слоты воздействуют на границы аустенитных зе рен. Существенно облегчается травление при ис пользовании насыщенных водных растворов пик риновой кислоты с добавками поверхностно активных веществ. Выявление границ ускоряется при горячем травлении. В табл. 3.1.3.1 приведены составы реактивов и способы травления для выяв ления границ аустенитных зерен конструкцион ных углеродистых и легированных сталей.
Химическое и электролитическое травление выявляет первоначальное аустенитное зерно с большей или меньшей достоверностью. Картина может затушевываться в случае протравливания наряду с бывшим аустенитным зерном границ ферритных зерен, карбидных сеток, цепочек раз личных включений. Более точно аустенитное зер но можно выявить нагревом до определенной тем пературы. Однако такие методы также имеют недостатки: выявляется не то зерно, которое было после предыдущей термической обработки, а вновь образовавшееся; температура повторной
аустенитизации не обязательно совпадает с темпе ратурой предыдущей термической обработки; на размере зерна сказывается длительность повтор ной аустенитизации.
Одним из методов выявления аустенитного зерна является цементация образца при 930 °С в течение 8 ч. Этот метод предназначен для уста новления величины наследственного зерна. Мож но также использовать диффузионное насыщение границы зерна при погружении шлифа на 15 мин в расплав 20% сплава меди с оловом или свинцо восеребряного сплава (для очищения поверхности и аустенитизации шлиф предварительно нагрева ют 15 мин в расплавленной буре). Возможно трав ление шлифа в расплавленном стекле при 9301200 °С в течение от 2 мин до 8 ч. Границы зерен проявляются в результате коррозии (интеркристаллитной коррозии).
В основных чертах метод окисления также примыкает к диффузионным методам, т. к. аусте нитное зерно выявляется вследствие проникнове ния кислорода в пограничные слои.
Наиболее объективные данные получаются при нагреве шлифа в вакууме, т. к. миграции границ зерен не препятствуют образующиеся диффузион ные слои, оксиды и другие соединения. Недостат ком метода вакуумного термического травления является нечеткое выявление границ зерна при низких температурах и небольших выдержках.
Заслуживает внимания метод, заключающийся в проведении отжига (например при 350 °С в те чение 1 ч) полированного шлифа с последующим травлением. Рекомендуется реактив следующего состава, мл: соляная кислота 10, азотная кислота 3, метиловый спирт 80. Выявленное зерно подлежит анализу.
Таблица 3.1.3.1
Составы реактивов и способы травления для выявления границ зерен в сталях
Состав реактива |
Специфика травления |
1-4 г пикриновой кислоты, 2 - 3 мл |
Для закаленных углеродисты х и легированных сталей. Длительность трав |
соляной или азотной кислоты, |
ления — до 15 с. Увеличение четкости достигается многократным слабым |
95 -100 мл этанола |
травлением и переполировкой, а также кратковременным низким отпуском |
5% спиртовой раствор пикриновой |
Для закаленных или улучш енны х сталей. Четкость достигается много |
кислоты с добавкой активных м ою |
кратным травлением и легкой переполировкой |
щих средств |
|
20 г пикриновой кислоты, 200 мл |
В см есь воды с эфиром добавляю т пикриновую кислоту и выдерживают |
эфира, 100 мл воды |
1 сут. в закрытой банке. Ш лиф травят 5 мин, затем обрабатывают в 5% рас |
|
творе целлюлозы в ацетоне. О бразующ аяся корочка удаляется через 15 мин |
10 г пикриновой кислоты, 100 мл |
Ш лиф погружаю т изучаемой поверхностью вниз на 1 0 -6 0 мин, затем слег |
ксилола, 10 мл этанола |
ка полируют |
5-6% водный раствор пикриновой |
Ш лиф травят при температуре 5 0 -6 0 °С в течение 1 -4 мин. Увеличение |
кислоты с добавкой активных м ою |
четкости достигается многократным травлением с легкой переполировкой. |
щих средств |
Рыхлый слой оксидов непреры вно удаляется мокрым тампоном |
15 г хлорного железа, 3 мл соляной |
Ш лиф протирают тампоном в течение 4 0 - 6 0 с. Кроме аустенитных зерен |
кислоты, 100 мл воды |
выявляет линии сдвига, карбиды, ликвацию |
1 г хлорного железа, 1,5 г соляной |
Для структуры в улучш енном состоянии. Ш лиф лучш е просматривать в |
кислоты, 100 мл этанола |
темном поле |
50 г хлорного железа, 150 мл эта |
Длительность травления — несколько секунд. Травление в течении 1 0 -25 с |
нола, 100 мл воды, 20% водный |
выявляет границы аустенитных зерен, а также двойники, карбиды, ликва |
раствор бисульфата натрия |
цию, границы феррита |
100 мл насыщенного водного рас |
Травление при 6 0 -7 0 °С в течение 1 мин. П росмотр ш лифа ведется в тем |
твора перманганата калия, 10 г |
ном поле. Границы зерен выявляются в виде упорядоченной окантовки |
едкого кали |
светящихся выделений ф осф идов и карбидов |
При нагреве сталей после достижения темпера туры нижней критической точки начинается обра зование аустенита, которое завершается при тем пературе верхней критической точки, поэтому после окончания полиморфного превращения получен ный размер аустенитных зерен принимают за на чальную величину. Дальнейший нагрев или вы держка при температурах выше верхней критиче ской точки приводят к росту аустенитных зерен.
В зависимости от химического состава, способа выплавки и условий раскисления стали характери зуются различной склонностью к росту зерна. Различают два типа сталей: наследственно мелко зернистую и наследственно крупнозернистую.
Первая характеризуется малой скоростью роста аустенитного зерна при нагреве, вторая — повы
шенной.
Медленный рост зерна при нагреве или терми ческой обработке является следствием ряда фак торов. Из них наиболее существенный — барьер ный эффект мелкодисперсных частиц оксидов и нитридов. Располагаясь преимущественно по гра ницам, они препятствуют росту зерен. При темпе ратурах, превышающих порог растворения частиц, препятствия для роста зерна устраняются, и даль нейший нагрев вызывает усиленный рост зерна. В результате может оказаться, что зерно наследст венно мелкозернистой стали будет крупнее, чем у наследственно крупнозернистой. В структуре на следственно крупнозернистой стали нет частиц, сдерживающих рост зерна. Поэтому увеличение зерен начинается сразу же после завершения по лиморфного превращения. Таким образом, под наследственной зернистостью понимают способ ность зерна аустенита к росту при нагреве стали.
Размер зерна, полученный при конкретной тер мической обработке, называется действительным. Наследственно мелко- и крупнозернистые стали одной марки могут обладать одинаковым действи тельным зерном. В то же время стали одной марки и одинаковой наследственной зернистости могут иметь разное действительное зерно. Большинство физико-механических свойств обусловливается только действительным зерном.
3.1.3.3. Применение эталонных шкал
В матсриаловедческой практике широко рас пространен метод визуальной оценки величины зерна. Он состоит в том, что микроструктура, ви
димая на экране металлографического микроско па, оценивается по специально разработанным и регламентированным шкалам. В России соответ ствующим нормативным документом является ГОСТ 5639, в Америке — ASTM Е 112, в странах Западной Европы — ISO 643. Перечисленные до кументы во многом аналогичны, так же как и при веденные в них микрофотографии структур в классификации шкал. Условный номер шкалы ха рактеризует как размер зерна, так и число зерен,
приходящихся |
на 1 мм2 |
поверхности |
шлифа. |
В этом методе |
некоторой |
структуре со |
средней |
площадью зерна Ао = 0,128 мм2 (средним попереч ником d«0,38 мм) приписывают номер (балл) В = 0. Тогда балл зерна В со средней площадью А по определению есть двоичный логарифм отноше ния AQIA:
B = logA = ig№ j |
=2 logА . |
|
А |
и ) |
и |
Первый балл (номер) соответствует 16 зернам на площади в 1 мм2 (рис. 3.1.30). В связи с тем, что в плоскости шлифа встречаются зерна не одного размера, площадь зерна колеблется в пределах 40000-80000 мкм2 При увеличении хЮО на пло щади 10 см2 видно от 1 до 2,4 зерна. Уменьшение размера зерна на один номер по шкале соответст вует уменьшению вдвое площади зерна или коли чества зерен на 1 мм2
2
%
03
X
X
о
а
о
о
и
£
!Т
Номер зерна
Рис. 3.1.30. Н омограмма, связывающая средний размер зерна с количеством зерен на 1 мм2
и номером зерна по шкалам ГОСТ 5639
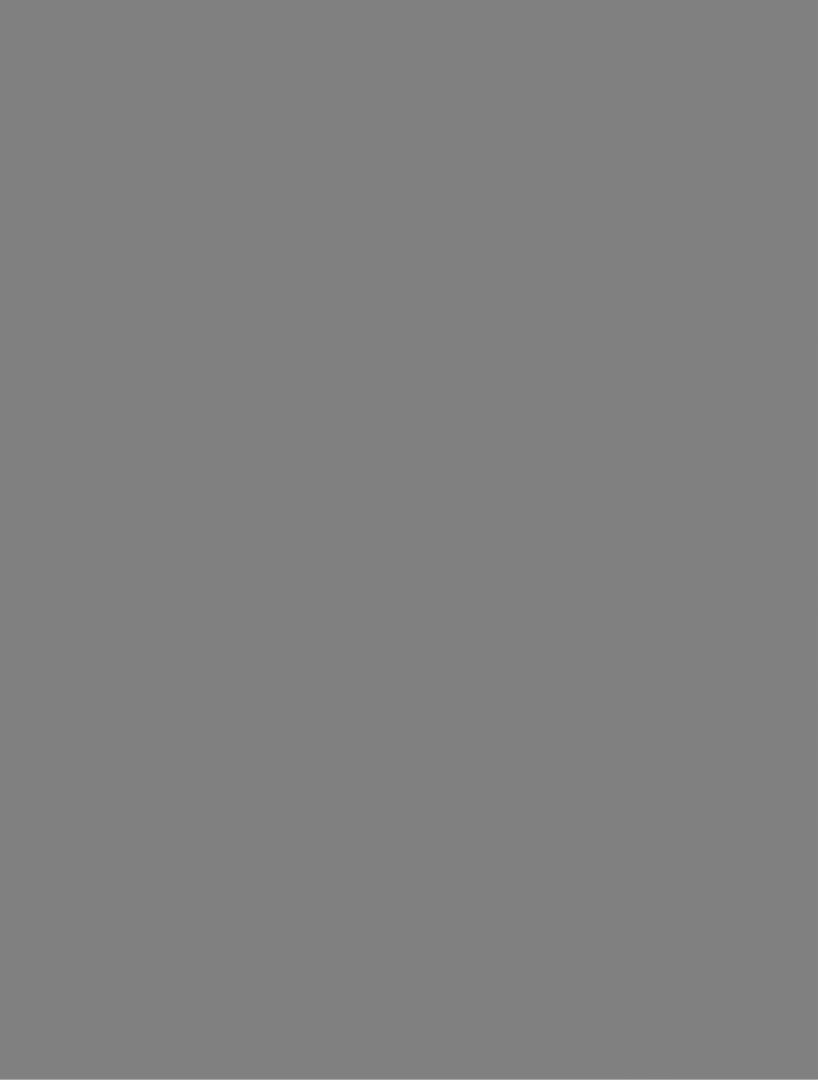
Число зерен подсчитывают в пределах площа ди ограниченной окружностью диаметром 79,8 мм. При увеличении хЮО это соответствует площади на шлифе 0,5 мм2 Число зерен должно быть не менее 50. Если их меньше, то используют меньшее увеличение. Общее число зерен подсчи тывают по формуле
Шюо = т + 0,5/И|,
где т — число зерен внутри круга; т\ —число зе рен, пересекающихся окружностью. Число зерен, приходящееся на 1мм" поверхности шлифа, равно М=2тт - При увеличении, отличном от хЮО,
(
М =2 — I т , где а — применяемое увеличение
\ 100 J 4
и /»,, — число зерен, подсчитанное при этом уве личении.
Среднюю площадь зерен (Scp) и диаметр зерен (Z)cp) вычисляют по формулам:
Scp М ...
Величины равноосных зерен характеризуют средним условным диаметром, который опреде ляют по изображению на матовом стекле микро скопа или по микрофотографии. С этой целью проводят произвольно несколько прямых линий так, чтобы каждая линия пересекала не менее 10 зерен. После этого подсчитывают число пересече ний на длине всех линий (включают и те зерна, которые полностью не пересечены у концов ли ний). Затем, разделив суммарную длину всех ли ний на число пересечений и учитывая выбранное увеличение, получают средний условный диаметр зерен.
Металлографический анализ структуры зерен, производимый с использованием шкал, является полуколичествснным. На основе прямых измере ний выявленной структуры определение размеров
кристаллитов (зерен) реализуется с большей точ ностью.
В однофазной структуре поликристаллического металла или сплава величина зерна определяется
числом зародышей (центров кристаллизации) и линейной скоростью их роста. Если центры кри сталлизации распределены в объеме равномерно, а скорости их роста одинаковы в разных направле ниях, то образующиеся при этом зерна окажутся выпуклыми многогранниками, по форме близкими
ккубическому октаэдру (рис. 3.1.32).
Вэтой фигуре в плоском сечении средний угол между гранями равен 120°, а число зерен, имею щих общее ребро, равно трем. Из этого следует, что в плоском сечении зерна имеют форму, близ кую к правильному шестиугольнику. При осуще ствлении количественной оценки структуры ме талла определяют следующие параметры:
•средний поперечник d (диаметр, мм) зерна на плоскости шлифа;
•средний объемный поперечник Д, (объемный
диаметр, мм). Почти всегда D > d, но если d»D, то d - 8£>/Зл:» 0,85Д
•удельную поверхность границ зерен (в еди нице объема) — Sv (мм2/мм3). Величина Sv = 3ID. Многие физические параметры металлов и спла вов (твердость, прочность, коэрцитивная сила) ли нейно зависят от Sv;
•число зерен в единице объема Nv(1/мм3). Для количественного описания структуры, в
частности с помощью размеров зерен, применяют статистические методы и строят гистограммы или кривые распределения. Так, с помощью окулярмикрометра определяют число зерен, размер кото рых находится в пределах определенного числа делений (например, от 0,5 до 1,5; от 1,5 до 2,5; от 2,5 до 3,5 и т. д.). По этим данным и строят гисто граммы.
1 2 3 4 5
Рис. 3.1.32. Объемная модель зерна
ввиде кубического октаэдра (слева)
исечение структуры зерен случайной аналитической плоскостью (шлифом) А—А (справа)
Все вышеперечисленные характеристики явля ются средними величинами и не описывают из менчивость размеров зерен. В реальной структуре всегда встречаются зерна крупнее или мельче не которого среднего. Учет изменений в структуре зерен осуществляется с помощью функции рас пределения по размерам NV(D), которая показыва ет относительное число (долю) зерен в К размер ных группах, имеющих величину в некотором ин тервале значений от Д до Д + Н, где Н — шаг разбивки, а Д — номер размерной группы. Ти пичный вид функции распределения показан на рис. 3.1.33. Приведенное распределение зерен по размерам является одномодальным (содержит один максимум).
Рис. 3.1.33. Типичная кривая распределения зерен по размерам, построенная в обычных (а)
и полулогарифмических (б) координатах
Распределение, построенное в полулогарифми ческих координатах, называется нормальным.
Если кривая имеет ряд минимумов и максиму мов, то проводят ее сглаживание, подсчитывая число зерен в более крупных интервалах размеров, т. е. увеличивают интервалы группировки. На ос новании кривой распределения подсчитывают средний диаметр зерна:
к^т х
А .
где т частота группы (т. е. число зерен, прихо дящихся на определенный интервал шкалы оку ляр-микрометра); х — диаметр в делениях шкалы (т. е. определенный интервал шкалы); к — средняя цена деления шкалы (в мкм).
Средняя площадь зерен (Scp) может быть вы числена, исходя из формулы определения £>ср, если
принять, что зерно имеет форму шара Х = nDл Л
L ~ l T m
т
Число зерен N, приходящихся на единицу пло
щади, определяют по формуле N = -J- .
5 ср
Функция распределения характеризуется сле дующими величинами:
•модой распределения — наиболее часто встречающимся размером зерен Dm (Dm Ф(D ));
•средним квадратичным отклонением <3ц (мм) размера зерна от средней величины зерен, которое определяется формулой
а D~
Здесь и — количество измеренных зерен, D, — отклонение размеров зерен от среднего (D).
Изменчивость зерен характеризуют также с
помощью безразмерного отношения — , которое
называется коэффициентом вариации.
Методы, основанные на непосредственных из мерениях, намного точнее балловой оценки разме ров зерен. Чтобы ими воспользоваться, необходи мо спроектировать измерительную рамку извест ной площади F на изображение структуры, которая наблюдается на экране микроскопа при
увеличении N. Тогда площадь шлифа, соответст-
р
вующая измерительной рамке, равна —- . Подсчи-
N
тав среднее число п зерен внутри рамки, можно определить среднюю площадь одного зерна:
\А) = ~ ^ г - Число зерен, попавших в поле рамки,
можно определить по формуле
п = /?+—+1,
2
где р — количество зерен, целиком попадающих в поле рамки; g — число зерен, которые рамкой
пересеклись; единица учитывает четыре зерна, которые находятся в углах рамки и принадлежат
ей на 'А(рис. 3.1.34).
Другой способ (метод Салтыкова) предполагает подсчет числа узлов Nv— стыков трех границ зерен:
Эта операция выполняется при таком увеличе нии микроскопа, чтобы в пределы измерительной рамки попало не менее 10-20 зерен. При малом п возникнет большая погрешность вследствие непредставительности выборки, а при большем п утомителен подсчет. Появление коэффициента 14 вызвано тем, что стык трех границ зерен в среднем имеет три угла по 120°, а зерно в виде правильного шестиугольника содержит 6 стыков. Поскольку каждый стык принадлежит трем зернам, то в сред нем на одно зерно приходится 2 стыка.
Удельная поверхность Sr границ зерен опреде ляется методом случайной секущей. Для этого на изображение структуры проектируется секущая — линия любого вида (чаще всего прямая) с извест ной длиной L на плоскости шлифа. Величина L равна наблюдаемой длине линии /, деленной на увеличение N микроскопа или фотографии. Далее подсчитывается число пересечений Р секущей ли нии с границами зерен и вычисляется число пере сечений на единицу длины секущей Рр.
При этом независимо от формы зерен выполня ется равенство
Sv= 2Ру.
Универсальным и простым способом для нахо ждения параметров функции распределения зерен по размерам является метод случайных секущих (хорд). В этом методе последовательно измеряют ся длины хорд /„ которые образованы при пересе чении случайной секущей с границами зерен (рис. 3.1.35). После этого результаты измерения хорд разбивают на размерные группы с шагом Я. Он равен частному от деления округленной длины самой большой хорды на выбранное количество групп разбиения К:
ц_ max
- К
При ручном счете значения величины К выби рают в пределах 8-15, но не более Ру\ где Р — общее число измеренных хорд. Как правило, к первой группе относят все хорды длиной от 0 до Я. Во вторую входят хорды длиной от Я до 2Я. В /-ю группу — хорды длиной от Я(,_1) до Ht. К по следней, к - й группе относят хорды длиной от Щ -\) до Нк, т. е. до /тах. Затем определяют количество хорд в каждой размерной группе Р, и плотность
р
исла хорд Ни = — . Число зерен в единице объема
N Vh которое относится к /-й размерной группе и имеет размер от Щ.\) до Я,, равно;
Рис. 3.1.34. Схема определения количества зерен, |
Рис. 3.1.35. Случайная секущая, |
попавших в пределы измерительной рамки |
спроектированная на изображение структуры зерен, |
в форме квадрата |
ихорды/,(/ = 1, ..., 5) |