
книги / Энергоэффективный термопластичный материал для дорожной разметки
..pdfТаблица 5.1
Последовательность и время выполнения технологических операций при производстве термопласта
№ |
Операции |
Время, |
Примечания |
||
п/п |
мин |
||||
|
|
|
|||
1 |
Подготовка отдельных «малых» на- |
120 |
1 замес – 500 кг. Пред- |
||
|
весок (минерального масла, TiO2, |
|
варительной подготов- |
||
|
SIS, ЭВА, воска и других) на 1 замес |
|
ки отдельных |
компо- |
|
|
из расчета на все количество заме- |
|
нентов не требуется |
||
|
сов в рабочую смену |
|
|
|
|
2 |
Ссыпка «больших» компонентов |
|
|
|
|
|
(смолы, наполнители, стеклошари- |
|
|
|
|
|
ки, песок) в бункеры-дозаторы из |
|
|
|
|
|
тарных мешков (биг-бэгов) или из |
|
|
|
|
|
бункера-накопителя, установка за- |
|
|
|
|
|
данного веса |
|
|
|
|
3 |
Последовательная загрузка в пнев- |
10–12 |
Полное время по дан- |
||
|
мотранспортер «больших» и «ма- |
|
ным операциям в 1 |
||
|
лых» твердых навесок и перемеще- |
|
цикле 12 мин |
|
|
|
ние в зону смесителя |
|
|
|
|
4 |
Загрузка в смеситель жидкого пла- |
2 |
– |
|
|
|
стификатора (минерального масла) |
|
|
|
|
|
и ЭВА, SIS-полимеров |
|
|
|
|
5 |
Перемешивание в смесителе |
5 |
– |
|
|
6 |
Выгрузка смеси, последовательная |
10 |
Вес 1 мешка 12 кг. Вес |
||
|
фасовка в полиэтиленовые мешки, |
|
мешков на |
поддоне |
|
|
запайка их, укладка на поддон, мар- |
|
(нетто) 1000 кг |
|
|
|
кировка и обвязка поддона стрейч- |
|
|
|
|
|
пленкой |
|
|
|
Известно, что характеристики термопласта во многом зависят от концентрации вводимого SIS-полимера и от его тщательного распределения. Эффекта более полной диспергации этой добавки можно добиться, если просто увеличить время перемешивания при рабочей температуре расплава термопласта в маточном котле перед выполнением непосредственно разметочных работ. Особенно характерно это для такого SIS-полимера, как Vector. Время приготовления расплава термопласта из состава, содержащего Vector,
91
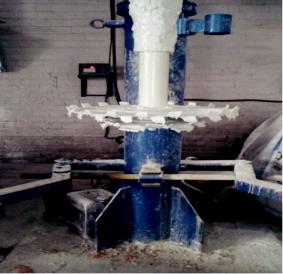
приходится увеличивать на 1,0–1,5 ч, иначе термопласт получается более жестким, как бы содержащим меньшее количества полимера. Однако в таком случае всегда имеет место риск получить более окисленный термопласт и поэтому более темную (с желтизной) разметочную полосу.
Внешний вид рабочего органа смесительной установки приведен на рис. 5.3.
Рис. 5.3. Рабочий орган смесительной установки
Чтобы не подвергать риску качество разметочного материала, не греть лишний раз смолу, этот полимер целесообразно временно вывести из композиции и растворить его во входящем в состав термопласта пластификаторе – минеральном масле. Предварительную пластификацию SIS-полимера при этом необязательно обрывать, чтобы обеспечить приемлемую технологичность этой смеси: ее (пластификацию) можно провести до конца, до получения отвердевшей массы. Для ускорения процесса пластификацию целесообразно провести при повышенной температуре, например 180 °С.
92
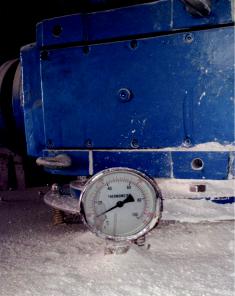
При введении в эту двойную смесь 3-го компонента, входящего в рецептуру, например ЭВА, или части наполнителя эта термопластичная смесь после охлаждения получается твердой и удобной в работе. Свойства смеси регулируются соотношением значений концентрации компонентов.
Установка разогрева расплава термопласта представлена на рис. 5.4.
Рис. 5.4. Установка разогрева расплава термопласта
Расплавленная смесь может быть отформована в виде ленты толщиной 2–3 мм, которая после охлаждения просто дробится на куски 20–40 мм и в таком виде добавляется в качестве навесок в каждое тарное место выпускаемого термопласта.
Предварительно пропластифицированный полимер может выпускаться также в виде желеобразной смеси, затаренной в небольшой (500 г) полиэтиленовый пакет, или в виде отдельных твердых блоков (0,5–1,0 кг).
93
Несмотря на некоторые преимущества (заметное сокращение времени и температуры подготовки расплава термопласта на автомобильной дороге, исключение пластификатора из процесса приготовления порошкообразной смеси), в целом такая технология сопряжена с заметным увеличением трудозатрат.
Другой способ получения разметочного материала заключается в производстве термопласта в виде гомогенных плавленых блоков
(см. рис. 5.1, б).
Такое производство обладает рядом несомненных преимуществ. Это тщательное диспергирование компонентов, входящих
всостав термопласта, что обеспечивает единообразие его свойств
влюбой части партии изготавливаемого материала. В этом случае аттестация готовой продукции даже по небольшой пробе, отобранной из смесителя, будет более надежно характеризовать уровень свойств данной партии термопласта, чем большая проба материала из партии термопласта, изготовленного в виде порошковой смеси.
При приготовлении расплава нет принципиальных ограничений на использование твердых или жидких компонентов, возникающих в связи с возможной слеживаемостью материала, крупных (в разумных пределах) или мелких кусков смол, каучуков или других подобных компонентов, входящих в состав термопласта.
Сучетом особенностей конкретного оборудования производство термопласта в этом случае оказывается более выгодным, чем
вслучае порошковой технологии: большая единовременная загрузка смесителя, меньшее количество подготовительных операций, меньшее количество людей, занятых в процессе его приготовления, сравнительно более короткий технологический цикл в расчете на единицу продукции и др.
Рассмотрим организацию производства термопласта методом свободного литья. Данное производство рассчитано на выпуск 8–9 тыс. т термопласта в год из условия работы в 2 смены 2 смесителями (котлами).
Рассматриваемое производство периодическое. В основе его
лежит стационарный смеситель (котел) GT8HGR с рабочим объемом 3,65 м3 (диаметр 2,3 м) и массой 4 т.
94
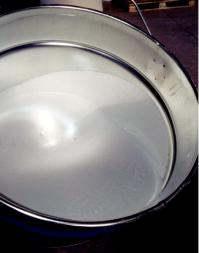
Принципиальными особенностями данного аппарата являются: хорошо регулируемый обогрев (скорость нагрева от 0,5 до 1,0 °С/мин) закрытым форсом пламени сгораемого соляра, автономный 4-тактный двигатель, вращающий с помощью цепной передачи мощную мешалку и работающий также на дизельном топливе, общий расход которого при проведении 1 варки обычно составляет
20 л/ч.
На обслуживание 2 котлов в смене занято 4 человека с общей продолжительностью рабочего дня 10–11 ч. Загрузка каждого котла составляет 6 т. Технологические потери материалов, как правило, не превышают 1 %.
Слив расплава термопласта осуществляется в легкие металлические банки (ведра) с толщиной стенок 0,33 мм, которые устанавливают на поддон по 16 шт. Вес 1 тарного места (нетто) составляет
36 кг (рис. 5.5).
Рис. 5.5. Заполнение тарного места расплавом термопласта
В течение 10–12 ч эти слитые блоки остывают до окружающей температуры и могут быть использованы по прямому назначению.
95
При транспортировке термопласт в таре не требует укрытия от атмосферных осадков и может храниться в неотапливаемых складских помещениях как угодно долго.
Перед использованием металлическую банку с термопластом разрушают механическим приспособлением (несколькими ударами кувалды). Жесть легко отделяется от термопласта, и куски последнего забрасывают в котел разметочной машины.
Термопласт плавится легко и быстро. Разметку ведут при температуре 170–180 °С.
Необходимы пояснения по температурному режиму. Загрузка вяжущего (смолы) в смеситель проводится после предварительного прогрева смесителя до температуры не ниже 100 °С.
Рабочие органы применяемого оборудования должны быть тщательно очищены от предыдущего состава, так как многие термопласты абсолютно несовместимы.
Так, например, присутствие всего 1 % предыдущего состава (а на практике даже меньше) в составе термопласта на основе нефтеполимерной смолы является критическим и недопустимым. Возможные остатки материала в котле могут превышать эту критическую норму и должны быть удалены. Этот вывод в самой полной мере относится и к случаю эксплуатации разметочной машины.
В качестве разметочного материала для сравнения с разработанными составами выбрали состав, полученный в результате исследований, проведенных в работе [95] и представленный в табл. 5.2.
|
|
|
Таблица 5.2 |
Состав разметочного материала на основе |
|||
|
термопласта «Кратер» |
|
|
|
|
|
|
Ингредиенты |
|
Назначение |
Содержание, % |
Смола «Пентанокс» |
|
Связующее |
5,2 |
Смола ГЭК |
|
|
7,8 |
ДОФ (диоктилфталат) |
|
Пластификатор |
3,5 |
Кратон Д |
|
Модификатор – усилитель |
1,7 |
|
|
адгезии |
|
96 |
|
|
|
|
|
Окончание табл. 5.2 |
|
|
|
|
|
Ингредиенты |
Назначение |
|
Содержание, % |
Мраморный песок |
Наполнитель |
|
20,0 |
Кварцевый песок |
|
|
19,9 |
УР-7 |
|
|
18,0 |
TiO2 |
Белый пигмент |
|
2,5 |
Fa-1 (воск) |
Снижение липкости |
|
1,4 |
Стеклянные микрошарики |
Светоотражение |
|
20,0 |
Разработанные составы термопласта представлены в табл. 5.3.
|
|
|
|
|
Таблица 5.3 |
Разработанные составы термопласта |
|
||||
|
|
|
|
|
|
Компонент, мас. % |
Состав 1 UCRP1004L |
Состав 2 UCRP1004L |
|||
НПС |
|
22 |
|
|
22 |
Микродоломит МД-40 |
|
28 |
|
|
23 |
Аппретированный МД-40 |
|
5 |
|
|
10 |
Кварцевый песок |
|
12 |
|
|
10 |
TiO2 |
|
4 |
|
|
4 |
Минеральное масло |
|
4 |
|
|
4 |
ЭВА |
|
1,5 |
|
|
2 |
SIS |
|
1,5 |
|
|
3 |
Воск Fa-1 |
|
2 |
|
|
2 |
Стекломикрошарики |
|
20 |
|
|
20 |
Технологические режимы приготовления термопласта пред- |
|||||
ставлены в табл. 5.4. |
|
|
|
|
|
|
|
|
|
|
Таблица 5.4 |
Технологические режимы приготовления термопласта |
|||||
|
|
|
|
||
Наименование операции |
|
Время, мин |
Т, °С |
||
Загрузка смолы, включение обогрева, обогрев |
|
30 |
20→135 |
||
Включение мешалки, перемешивание |
|
|
20 |
135 |
|
Загрузка ТiO2 , перемешивание |
|
|
15 |
135→150 |
|
Загрузка доломита (1/2 часть), перемешивание |
|
15 |
150 |
||
|
|
|
|
|
97 |
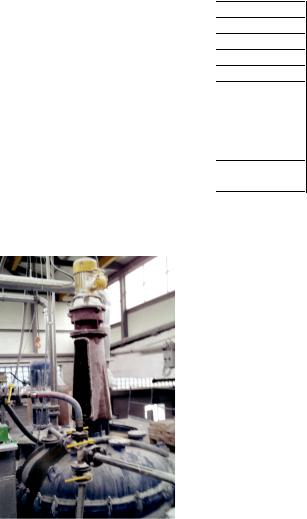
Окончание табл. 5.4
Наименование операции |
Время, мин |
Т, °С |
|
Загрузка песка (1/2 часть), перемешивание |
15 |
150 |
|
Загрузка доломита (остаток), перемешивание |
15 |
150 |
|
Загрузка песка (остаток), перемешивание |
15 |
150 |
|
Загрузка аппрет. доломита, перемешивание |
20 |
150→170 |
|
Загрузка модифицирующих добавок: масла, |
30 |
170 |
|
воска, ЭВА, SIS, перемешивание |
|
||
|
|
||
Загрузка стеклошариков, перемешивание |
60 |
170→190 |
|
Отбор проб на анализ |
Не норми- |
Не норми- |
|
руется |
руется |
||
|
|||
Слив массы |
Не норми- |
Не норми- |
|
руется |
руется |
||
|
Установка окончательного перемешивания представлена на рис. 5.6.
Рис. 5.6. Установка окончательного перемешивания
Из приведенных данных видно, что разработанные составы 1 и 2, полученные в результате выполнения настоящей работы, по
98
сравнению с аналогом обладают повышенными адгезией к асфальтобетону и эластичностью в диапазоне значений температуры от –10
до 20 °С.
Эти показатели позволяют сделать вывод о лучшей стойкости разработанного материала в условиях эксплуатации, особенно при отрицательных значениях температуры.
Сравнительные характеристики разработанных составов представлены в табл. 5.5.
Таблица 5.5
Сравнение характеристик разработанных составов с аналогом
Параметры |
Состав |
Состав 1 |
Состав 2 |
|
«Кратер» |
|
|
Скорость течения расплава V, г/с |
4,8–5,2 |
5,0–5,5 |
4,5–5,2 |
(при Т = 180 °С) |
|
|
|
Температура размягчения Тр, °С |
110–112 |
115–120 |
105–115 |
Белизна, % |
80–83 |
80–82 |
80–85 |
σсж при 20 °С, МПа |
2,4–3,2 |
3,5–4,0 |
2,6–3,0 |
σсж при 0 °С, МПа |
7,5–9,5 |
9,8–11,3 |
7,8–8,4 |
σсж при –10 °С, МПа |
14,5–19,0 |
22,0–25,0 |
15,6–19,4 |
Относительное удлинение при растяже- |
|
|
|
нии ɛ, %: |
|
|
|
при 20 °С |
3,5 |
5,0 |
6,0 |
при 0 °С |
2,0 |
3,0 |
3,5 |
при –10 °С |
1,0 |
2,0 |
2,5 |
Липкость |
Нелипкий |
Нелипкий |
Нелипкий |
Адгезияпри Т = 20 °С, МПа |
1,2–1,5 |
2,4–2,7 |
2,0–2,3 |
Время отверждения, мин |
15–17 |
8–10 |
12–15 |
Сравнение эксплуатационных характеристик разработанных составов с аналогом на стойкость к воздействию автомобильных колес с различными протекторами (в том числе и шипованными) проводили на полигоне «Карусель-2» Московского автомобильнодорожного государственного технического университета – МАДИ
(г. Москва) (рис. 5.7–5.9).
99
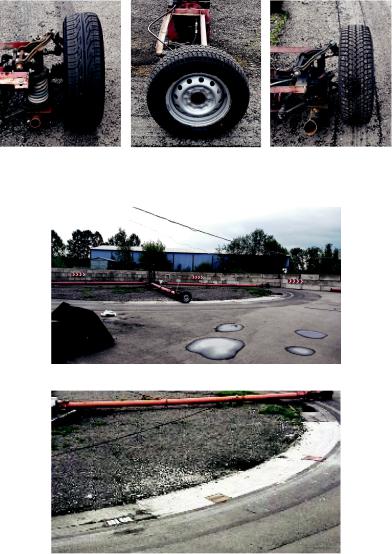
Рис. 5.7. Виды протекторов автомобильных колес, использованных при испытаниях
а
б
Рис. 5.8. Вид полигона для испытания дорожных материалов на многократное воздействие колеса:
а – общий вид; б – исследуемая полоса
100