
книги / Энергоэффективный термопластичный материал для дорожной разметки
..pdf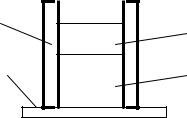
2
3
1 |
4 |
Рис. 2.2. Подготовка образцов для определения адгезии термопласта к асфальтобетону [15]: 1 – рабочий стол; 2 – обойма; 3 – термопласт; 4 – асфальтобетон
Величину адгезии определяли по формуле [15, 80]
А = Р/S, |
(2.1) |
где Р – усилие отрыва, кгc; S – площадь контакта асфальтобетона и термопласта, см2.
Определение степени обжатия
Параметр характеризует ползучесть материала под действием нагрузки, действующей постоянно. Определяется как степень сохранения первоначальной геометрии образца.
Эксперимент проводился следующим образом:
–из расплава (при температуре от 170 до 180 °С) во фторопластовых формах формировались цилиндрические столбики высотой от 20 до 30 мм;
–столбики подвергались обжатию с постоянным давлением 0,22 кгс/см2 в течение 24 ч при температуре 20–22 °С;
–изменение высоты столбика по сравнению с первоначальным значением является мерой степени обжатия материала, выраженной в процентах.
2.3.Выводы по главе 2
1.В данной главе рассмотрены объекты и методы исследования по отношению к рецептуре и технологическим особенностям получения полимерных композиционных материалов для дорожной
51
разметки, реализованные в настоящей работе, в том числе определение физико-механических и технологических свойств композитов.
2.Испытания полученных согласно разработанной схеме планового эксперимента образцов проводились в химической лаборатории кафедры «Оборудование и технологии обработки материалов» Саратовского государственного технического университета имени Ю.А. Гагарина.
3.Проведена оценка внешнего вида, наличия посторонних включений, стеклошариков и крупных нерасплавленных частиц компонентов материалов для дорожной разметки.
4.Оценка достоверности результатов измерений физико-меха- нических показателей проводилась по ГОСТ 8.011–72.
5.Проведен обзор испытательного оборудования для материалов, предназначенных для дорожной разметки на полимерной основе.
52
Глава 3. ИЗУЧЕНИЕ ВЛИЯНИЯ КОМПОНЕНТОВ РЕЦЕПТУРЫ ТЕРМОПЛАСТА НА ЕГО ТЕХНОЛОГИЧЕСКИЕ
И ЭКСПЛУАТАЦИОННЫЕ СВОЙСТВА
3.1. Выбор наполнителя
Малоизученной проблемой современной технологии термопластов для дорожной разметки является исследование зависимости структура–свойства. Формирование полимерной капсулы на поверхности частицы минерального дисперсного наполнителя сопровождается образованием межфазного слоя, которому способствуют поверхностные процессы вблизи границ полимер–наполнитель, неравномерная усадка компонентов, приводящая к внутренним напряжениям, образованию микротрещин, и другие причины [72–74].
Межфазный слой имеет разную толщину в зависимости от природы наполнителя, формы и размера частиц, рельефа их поверхности, что оказывает существенное влияние на свойства термопласта.
Химическая структура термопласта задается составом компонентов и окончательно формируется в процессе отверждения последнего на поверхности асфальтобетона. Для обеспечения необходимых эксплуатационных характеристик в термопласте присутствуют компоненты, каждый из которых предназначен для усиления какой-либо функции [4, 45, 46].
Согласно традиционной технологии при изготовлении термопласта для дорожной разметки его компоненты в заданных пропорциях в виде твердых гранул смолы, частиц минеральных наполнителей, стеклосфер, а также жидкие ингредиенты перемешиваются и засыпаются в герметичные полиэтиленовые мешки, где хранятся до момента использования в котле разметочной машины [2]. При этом может пройти достаточно длительное время между приготовлением смеси и ее применением. Поскольку минеральные дисперсные наполнители обладают высокой поверхностной энергией, это приводит к образованию агрегатов [88].
53
Помимо этого поверхность наполнителей обычно загрязнена, так как наполнитель стремится снизить избыточную энергию за счет адсорбции низкомолекулярных веществ, в первую очередь атмосферной влаги [39].
Если после производства смеси ее состав достаточно однороден, то со временем происходит перераспределение частиц – более тяжелые опускаются вниз, а более легкие фракции вытесняются вверх. Кроме того, образуются агрегаты в виде комков из мелкодисперсных частиц. Исходя из этого одной из существенных проблем, как и для всех сыпучих многокомпонентных продуктов, является слеживаемость смеси [46].
При выборе материала основного дисперсного наполнителя особое внимание в работе было уделено доломиту – материалу дешевому и достаточно прочному. Введение такого наполнителя придает композиту структурную и механическую прочность. Белый цвет доломита позволяет обеспечить необходимую белизну разметки и снизить расход дорогостоящего пигмента – диоксида титана
(TiO2) [45].
При введении наполнителя в смолу необходимо обеспечить хорошую адгезию полимера к полярному наполнителю, а это может быть осуществлено при хорошем смачивании частиц наполнителя смолой. При этом улучшение смачивания приводит к увеличению прочности композита и усилению некоторых других характеристик. Качество смачивания и, как следствие, адгезия, в свою очередь, существенно зависят от размера частиц и топографии поверхности наполнителя. Кроме того, на прочность связи влияет поверхностная энергия на границе раздела фаз.
Физико-химические параметры дисперсного доломитанаполнителя в системе композиционного материала определяются степенью дисперсности, химической активностью и топографией поверхности его частиц.
При измельчении крупнозернистых минеральных материалов получаются частицы разных фракций, при этом увеличивается их удельная поверхность и повышается ее поверхностная энергия [1, 71].
54
Это приводит к тому, что усиливается способность дисперсных наполнителей к взаимодействию с другой фазой.
При механическом измельчении доломита происходит разрушение кристаллической решетки, приводящее к возникновению на поверхности частиц некомпенсированных электрических потенциалов в результате выхода катионов Са2+ и Mg2+ и анионов (СО3)2–. В результате образуются дефектные кристаллические решетки, которые представляют сложные пространственные конструкции, взаимодействующие с другими фазами как электрические системы.
Химический состав вещества, размеры и топография поверхности частиц определяют знак и величину электрического потенциала.
Сформированная поверхность минеральных частиц имеет повышенную реакционную способность, причем у доломита она заряжается преимущественно положительно [95].
3.2. Особенности наполнителя и их влияние на характеристики термопласта
При изучении материала дисперсного наполнителя для разметочного термопласта необходимо иметь представление об энергетических свойствах его поверхности, в том числе о знаке потенциала на границе раздела фаз в высокодисперсном состоянии.
Методом фильтрации газа через пористые тела (метод Козени и Фармана) получены экспериментальные данные об удельной поверхности частиц в различных фракциях доломита (табл. 3.1).
Таблица 3.1
Экспериментальные данные об удельной поверхности частиц в различных фракциях доломита
Наименование |
|
Марка доломита |
|
|
||
показателя |
МД-5 |
МД-10 |
МД-40 |
|
МД-60 |
МД-100 |
Удельная |
От 3,5 |
От 3,35 |
От 3,15 |
|
От 3,0 |
От 2,5 |
поверхность, м2/г |
до 3,6 |
до 3,45 |
до 3,2 |
|
до 3,1 |
до 2,7 |
|
|
|
|
|
|
55 |
Из данных табл. 3.1 видно, что исследуемые фракции доломита обладают достаточно развитой поверхностью, что, очевидно, отражается на реологических и функциональных характеристиках композиционного материала.
Улучшение механических свойств термопласта достигается путем однородного распределения частиц твердой фазы в его структуре, чему способствует уменьшение размера частиц. Однако однородное распределение частиц наполнителя в структуре термопласта обеспечивается высоким диспергированием и дезагрегированием наполнителя в смоле. В этом случае значительное влияние оказывают адсорбционные связи смол с поверхностью частиц наполнителя.
Развитая удельная поверхность наполнителя значительно влияет на адсорбционное взаимодействие смолы, в первую очередь на смачиваемость поверхности смолой. Хорошее смачивание определяет условия прочного адгезионного соединения смолы с наполнителем и повышает физико-механические характеристики композита.
Очевидно, что на формирование равновесной адсорбции ассоциатов макромолекул нефтеполимерной смолы на поверхности наполнителя оказывает ингибирующее действие адсорбция воды, содержащейся как в наполнителе, так и в смоле.
По этой причине было исследовано время попадания воды и расплавов смол в массу порошка доломита. Из представленных
втабл. 3.2 экспериментальных результатов видно, что доломит характеризуется значительной адсорбционной активностью по отношению к воде и существенно меньшей активностью по отношению к смоле.
На значение адсорбции кроме удельной поверхности сильное влияние оказывает общая химическая природа поверхности наполнителя, которая определяется по величине рН и для применяющихся
внашем случае доломитовых наполнителей равна 8–9.
Основной характер доломитового наполнителя, определенный присутствием на его поверхности ионов Са2+, Mg2+, обусловливает большую адсорбцию молекул воды на поверхности за счет создания водородных связей.
56
|
|
|
|
Таблица 3.2 |
Время смачивания порошков доломита водой и смолами |
||||
|
|
|
|
|
Время смачивания, с |
Смола 1 |
|
Смола 2 |
Смола 3 |
|
МД-5 |
|
|
|
Водой |
|
|
15–22 |
|
Смолой |
750–780 |
|
750–800 |
800 |
|
МД-10 |
|
|
|
Водой |
|
|
9–12 |
|
Смолой |
650–700 |
|
550–700 |
600–700 |
|
МД-40 |
|
|
|
Водой |
|
|
5–8 |
|
Смолой |
220–240 |
|
220–230 |
200–210 |
|
МД-60 |
|
|
|
Водой |
|
|
4–6 |
|
Смолой |
160–170 |
|
160–180 |
140–155 |
|
МД-100 |
|
|
|
Водой |
|
|
3–5 |
|
Смолой |
110–140 |
|
110–140 |
100–120 |
Реакция воды с поверхностью наполнителя понижает адсорбцию смолы и может не допустить перехода ассоциатов молекул исследуемой смолы на поверхность наполнителя. Это должно положительно сказаться на реологических свойствах и процессе диспергирования частиц наполнителя в смоле из-за отсутствия значительного структурирования системы.
Поскольку на поверхности частиц доломита присутствуют ионы Ca2+ и Mg2+, при попадании частиц доломита в смолу сначала на их поверхности формируется слой адсорбированной воды, что подтверждают результаты исследования смачиваемости.
Вдальнейшем взаимодействие поверхности частиц доломита
снефтеполимерной смолой осуществляется за счет замены адсорбированных слоев воды на макромолекулы смолы, происходящее при повышенных значениях температуры.
Физическое и химическое взаимодействие ингредиентов ком-
позиционного материала подтверждают данные термогравиметрического анализа (ТГА). С учетом того, что в маточном котле разметоч-
57
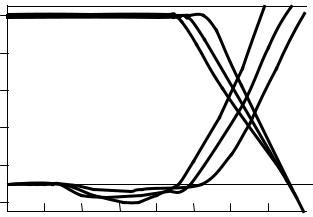
ной машины сухая смесь ингредиентов редко разогревается даже до температуры 220 °С, интерес представляют процессы, происходящие в интервале значений температуры 25–250 °С.
При этом возникает возможность достоверной оценки изменения структурных характеристик термопласта под влиянием поверхности дисперсных наполнителей на полимерное связующее на основе данных по кинетике разложения.
Для образцов ненаполненных смол медленный нагрев до значений температуры 200–220 °С не приводит к сколько-нибудь заметному изменению массы, однако при дальнейшем росте температуры до 400 °С происходит интенсивная деструкция полимера с по-
терей 50 % массы (рис. 3.1).
|
100 |
|
|
3* |
2* |
|
исходной |
|
|
2 |
1 |
||
90 |
3 |
1* |
||||
|
|
|||||
|
|
|
|
|||
|
|
|
|
|
||
от |
80 |
|
|
|
|
|
потери |
|
|
|
|
||
70 |
|
|
|
|
||
% |
|
|
|
|
||
|
|
|
|
|
||
Масса, |
60 |
|
|
|
|
|
|
|
|
|
|
||
|
50 |
|
|
|
|
|
|
100 |
200 |
|
300 |
Т, оС |
|
|
|
5 |
температуры |
|
|
|
||
|
|
|
|
|
|
|
|
4 |
|
|
|
|
||
|
|
|
3 |
значений |
|
|
|
||
|
|
|
2 |
|
|
|
|
||
|
|
1 |
||
|
|
Разность |
||
|
0 |
|||
|
|
|||
|
|
|
|
|
образца и эталона (ДTA), °С
Рис. 3.1. Потери массы: 1 – смола 1; 2 – смола 2; 3 – смола 3; кривые ДТА: 1* – смола 1; 2* – смола 2; 3* – смола 3
У смолы 1 этот процесс начинается при достижении температуры 272 °С, у смолы 2 – 240 °С, у смолы 3 – 260,4 °С. Кроме того, эндотермические процессы, наблюдаемые согласно кривым ДТА для каждой из смол и связанные с плавлением материала, позволяют определить значения температуры начала плавления: 95 °С – смола 1; 77 °С – смола 2; 82 °С – смола 3.
58
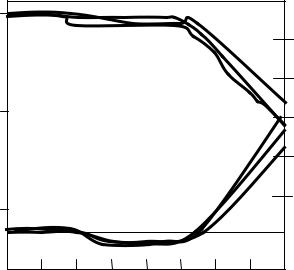
При введении минерального наполнителя МД-40 повышается термостойкость композиции за счет снижения массовой доли менее устойчивой к термоокислению смоляной части и ее замены на термостойкую минеральную часть. Для всех 3 композиций наблюдается смещение точки начала термодеструкции и, соответственно, начала потери массы в сторону более высоких значений температуры: для композиции на основе смолы 1 на 12 °С, для композиции на основе смолы 2 на 7 °С и для композиции на основе смолы 3 на 4 °С (рис. 3.2). Кроме того, наблюдаются потери массы в области температуры не менее 100 °С, связанные с дегидратацией поверхности частиц наполнителя.
Масса, % потери от исходной
100 |
2 |
1
3
90
3*
2*
1*
80
100 |
200 |
300 |
Т, °С |
5 |
эталона |
|
|
и |
|
4 |
образца |
|
3 |
температуры |
|
|
||
2 |
значений |
|
1 |
||
Разность |
||
0 |
||
|
(ДTA), °С
Рис. 3.2. Потери массы (при введении наполнителя МД-40): 1 – смола 1 + + МД-40; 2 – смола 2 + МД-40; 3 – смола 3 + МД-40; кривые ДТА: 1* – смола 1 + МД-40; 2* – смола 2 + МД-40; 3* – смола 3 + МД-40
Следует отметить, что на кривых потери массы ТГ и ДТА наблюдаются эндотермические изменения, связанные с процессом испарения влаги, которая сорбируется наполнителем с развитым рель-
59
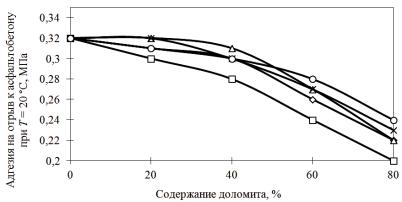
ефом поверхности – доломитом, имеющим к тому же положительный заряд поверхности частиц. Такой эффект приводит к потере массы всех 3 композиций на уровне 0,2–0,5 % начиная с температур
85–90 °С.
Однако использование только доломита в качестве наполнителя термопласта не позволяет получить комплекс свойств, необходимых для разметочного материала, из-за недостаточной адгезии к асфальтобетону (рис. 3.3) и других эксплуатационных характеристик.
Рис. 3.3. Влияние содержания доломита различных фракций на адгезию наполненной смолы 1 к асфальтобетону:
– МД-5;
– МД-10;
– МД-40
Стандартный асфальтобетон дорожного полотна состоит из органического вяжущего (битума) в количестве 7–9 % и уплотненной смеси различных минеральных дисперсных наполнителей.
Естественно, величины адгезии смолы к битуму и минеральной части асфальтобетона должны различаться, однако опыты показали, что адгезия на отрыв от асфальтобетона термопласта с возрастающей степенью наполнения снижается (см. рис. 3.1), что связано
суменьшением содержания смолы.
Вработе [16] установлено, что наиболее прочное сцепление термопласта с асфальтобетонным покрытием осуществляется при нанесении разметки на частично состаренный асфальтобетон, по-
60