
книги / Энергоэффективный термопластичный материал для дорожной разметки
..pdfГлава 2. ОБЪЕКТЫ И МЕТОДЫ ИССЛЕДОВАНИЙ
2.1.Объекты исследований
Внастоящей главе рассматриваются объекты и методы исследований по отношению к рецептуре и технологическим особенностям получения полимерных композиционных материалов (термопластов) для дорожной разметки [40, 88, 91, 95, 100].
Технические требования и методы испытаний материалов и покрытий дорожной разметки подробно освещены в современной технической литературе и нормативных документах [1, 5–7, 28, 38, 41–47, 49, 52, 78, 92, 93, 97, 99, 102].
Нефтеполимерные смолы представлены в табл. 2.1.
|
|
|
|
Таблица 2.1 |
|
Технические характеристики (паспортные данные) |
|||
|
нефтеполимерных смол |
|
||
|
|
|
|
|
|
|
Норма по техническим условиям, производитель |
||
№ |
Наименование |
UCRP1004L, |
Алифатиче- |
UCRP100L, |
United Chemical |
ская смола С5 |
United Chemical |
||
п/п |
показателя |
Company, Китай |
100, Китай |
Company, Китай |
|
|
|||
|
|
Смола 1 |
Смола 2 |
Смола 3 |
1 |
Внешний вид |
Желтоватые |
Светло-желтые |
Желтоватые |
|
|
гранулы |
гранулы |
гранулы |
2 |
Температура размяг- |
От 95 до 105 |
От 95 до 105 |
От 95 до 104 |
|
чения, °С |
|
|
|
3 |
Кислотное число, мг |
От 1,0 до 2,4 |
0,81 |
0,1 |
|
КОН/г |
|
|
|
4 |
Цветность, Gardner, |
4,0 |
4,0 |
5,0 |
|
не более |
|
|
|
5 |
Вязкость кинемати- |
От 140 до 180 |
От 240 до 270 |
Не менее 250 |
|
ческая расплава при |
|
|
|
|
200 °C, мм2/с |
|
|
|
6 |
Удельный вес, г/см3 |
0,98 |
От 0,89 до 0,95 |
0,97 |
7 |
Модификация |
Модифицирова- |
– |
– |
|
|
на малеиновой |
|
|
|
|
кислотой |
|
|
|
|
|
|
41 |
Микродоломит (МД) ТУ 5743-001-55363468–05 (производства Балаковского завода минеральных наполнителей), основным исходным сырьем для которого является природный (карьерный) доломит Тарабукинского месторождения доломитовых мраморов, находящегося в Заиграевском районе Республики Бурятия. Минерал из класса карбонатов химического состава CaCO3·MgCO3 (СаМg(CO3)2) (табл. 2.2).
Таблица 2.2
Технические характеристики микродоломита [26, 49]
Наименование показателя |
МД-5 |
МД-10 |
МД-40 |
МД-60 |
МД-100 |
Массовая доля углекислых магния |
98,0 |
98,0 |
98,0 |
98,0 |
98,0 |
и кальция в пересчете на СаСО3, |
|
|
|
|
|
%, не менее |
|
|
|
|
|
Массовая доля оксида магния |
18,0 |
18,0 |
18,0 |
18,0 |
18,0 |
(МgO), %, не менее |
|
|
|
|
|
Массовая доля оксида железа в |
0,23 |
0,23 |
0,23 |
0,23 |
0,23 |
пересчете на Fe2O3, %, не более |
|
|
|
|
|
Массовая доля окисида кремния |
2 |
2 |
2 |
2 |
2 |
(SiO3), %, не более |
|
|
|
|
|
Массовая доля нерастворимых в |
1 |
1 |
1 |
1 |
1 |
соляной кислоте веществ (HСl), %, |
|
|
|
|
|
не более |
|
|
|
|
|
Массовая доля влаги, %, не более |
0,2 |
0,2 |
0,2 |
0,2 |
0,2 |
Значение pH |
8–9 |
8–9 |
8–9 |
8–9 |
8–9 |
Твердость (по шкале МООС) |
3 |
3 |
3 |
3 |
3 |
Белизна, %, не менее |
96 |
95 |
94 |
94 |
93 |
Массовая доля остатка, %, не бо- |
|
|
|
|
|
лее, на сите с сеткой |
|
|
|
|
|
0,1 |
– |
– |
– |
0,8 |
5,0 |
0,063 |
– |
– |
0,5 |
7,0 |
30,0 |
0,045 |
0,1 |
0,3 |
5,0 |
25,0 |
50,0 |
0,032 |
– |
– |
– |
– |
– |
0,028 |
– |
– |
– |
– |
– |
Плотность, насыпная, г/см3 |
0,8–0,9 |
0,8–0,9 |
0,9–1,0 |
1,0–1,1 |
1,1–1,3 |
Плотность, уплотненная, г/см3 |
1,0–1,1 |
1,0–1,1 |
1,1–1,2 |
1,2–1,3 |
1,3–1,5 |
42 |
|
|
|
|
|
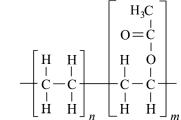
Поверхностно-активное вещество – γ-аминопропилтриэтокси-
силан(АГМ-9) H2N(CH2)3Si(OC2H5)3 (ТУ6-02-1077–85) (табл. 2.3) [95].
|
|
Таблица 2.3 |
|
Типичные физические свойства АГМ-9 |
|
|
|
|
№ п/п |
Физическая форма |
Жидкость |
1 |
Цвет |
Соломенный |
2 |
Удельный вес при 25/25 °С |
0,946 |
3 |
Температура кипения 760 мм Hg, °C |
217 |
Этиленвинилацетат EVA С6Н10О2 (Южная Корея). Сополимер этилена и винилацетата – легкий и упругий материал с хорошими амортизирующими свойствами, обладающий эластичностью при низких значениях температуры, повышенной адгезией к различным материалам. Температура плавления от 80 до 90 °C. Плотность
0,931 г/см³.
Диоксид титана TiO2 марки Kemira 405 производства компа-
нии Kemira (Финляндия) (табл. 2.4) [88].
Обработка поверхности необходима для увеличения устойчивости к внешним воздействиям. Неорганическая обработка (Al2O3) увеличивает стойкость частиц диоксида титана к кислотному воздействию, которое может приводить к разрушению частиц пигмента. Органическая обработка улучшает распределение частиц пигмента в объеме композиции.
43
|
|
Таблица 2.4 |
|
|
Характеристики диоксида титана марки Kemira 405 |
||
|
|
|
|
№ п/п |
Характеристика |
|
Норма |
1 |
TiO2, мас. % (мин) |
|
96,0 |
2 |
Al2O3, мас. % |
|
+ |
3 |
Удельный вес, г/см3 |
|
4,1 |
4 |
Средний размер частиц, мкм |
|
0,19 |
5 |
Маслоемкость, г/100 г пигмента |
|
19,0 |
6 |
Насыпная плотность, кг/м3 |
|
900 |
8 |
Органическая обработка |
|
+ |
Примечание. + Поверхности частиц подвергнуты обработке.
Масло индустриальное И-50А – дистиллятное нефтяное по ГОСТ 20799–88 (табл. 2.5).
Таблица 2.5
Масло индустриальное И-50А
№ |
Наименование показателя |
Норма |
п/п |
|
по ГОСТу |
1 |
Вязкость кинематическая при 40 °С, мм2/с |
От 90 до 110 |
2 |
Кислотное число, мг КОН/1 г масла, не более |
0,05 |
3 |
Плотность при 20 °С, кг/м3, не более |
910 |
4 |
Температура застывания, °С, не выше |
–15 |
5 |
Температура вспышки, определяемая в открытом тигле, |
225(215) |
|
°С, не ниже |
|
Стирольный блочный сополимер (SIS) марки Kraton D (Ве-
ликобритания) – сополимер стирол-изопрен-стирол – двухфазный термопластичный полимер, состоящий из твердых концевых блоков полистирола и мягких средних блоков каучука. Концевые блоки полистирола образуют области, которые запирают молекулу. Такая структура макромолекулы обеспечивает материалу специфические свойства: концевые блоки полистирола определяют его прочность, а средние блоки каучука – эластичность. Благодаря гибкой структу-
44
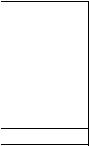
ре SIS совместим со многими пластмассами, при этом он улучшает их ударопрочность и повышает гибкость при низких значениях температуры. Имеет низкую температуру стеклования (–60 °С) и может перерабатываться при температуре от 180 до 225 °С [95].
Воск полиэтиленовый ПВ 200 (ТУ РБ 37493248.002–99) [95].
Воск содержит сложные эфиры, образованные высшими жирными кислотами и высокомолекулярными одноатомными спиртами. Является хорошей внешней смазкой, препятствует липкости затвердевшей композиции (табл. 2.6).
|
|
Таблица 2.6 |
|
Технические свойства воска полиэтиленового ПВ 200 |
|
|
|
Норма |
№ |
Наименование показателя |
|
п/п |
|
От 180 до 300 |
1 |
Вязкость расплава при 140 °С, 103, Па·с |
|
2 |
Температура каплепадения, °С, не более |
103 |
3 |
Твердость по пенетрации, 10–1, мм, не более |
5,0 |
4 |
Массовая доля золы, %, не более |
0,02 |
5 |
Удельное объемное сопротивление при 110 °С и на- |
1014 |
|
пряжении не ниже 100 В, Ом·см, не менее |
550±10 % |
6 |
Насыпная плотность, г/л |
2.2. Методы исследований
Определение физико-механических и технологических свойств композитов
Испытания проводили в соответствии с методиками следующих ГОСТов [95]:
Метод определения плотности – ГОСТ 15139–71.
Методопределениятемпературыразмягчения– ГОСТ11506–73. Метод определения прочности при сжатии – ГОСТ 12801–98. Метод определения прочности при межслоевом сдвиге –
ОСТ 190032–71.
Метод определения сроков отверждения – ГОСТ 23789–79. Метод определения морозостойкости – ГОСТ 7025–91.
45
Оценка достоверности результатов измерений физико-меха- нических показателей проводилась по ГОСТ 8.011–72. Испытания полученных образцов согласно разработанной схеме планового эксперимента проводились в химической лаборатории кафедры «Оборудование и технологии обработки материалов» Саратовского государственного технического университета имени Ю.А. Гагарина [91].
Сведения об использованном оборудовании и методах испытаний представлены ниже.
Оптическая микроскопия
Универсальный металлографический микроскоп «Альтами МЕТ 5С» использовался для работы в отраженном свете по методам светлого поля и по методу поляризации, а также для исследований прозрачных и полупрозрачных объектов в проходящем свете в светлом поле. Увеличение ×50–2000.
Универсальная электромеханическая испытательная машина
WDW-5E с максимальной нагрузкой 5 кН и климатической установкой использовалась для проведения испытаний материалов с целью определения параметров прочности при статическом растяжении, сжатии, изгибе, циклических испытаниях на усталость.
Метод инфракрасной спектроскопии
ИК-спектры снимали на ИК-Фурье-спектрометре IRTracer-100 фирмы Shimadzu в области 350–4000 см–1. Для регистрации ИКспектров исследуемые образцы наполнителя, связующего и композиционных материалов измельчали в керамической ступке до тонкодисперсного состояния. Образцы готовили в виде прессованных с KBr таблеток (1:300).
Определение прочности термопласта (пенетрация)
Глубина проникновения иглы косвенно характеризует такие эксплуатационные качества термопласта, как твердость, прочность и теплостойкость. Пенетрометр – прибор для измерения сопротивления термопласта вдавливанию иглы или конуса стандартных размеров и массы (индентора) в испытываемую среду. Измеряет глубину проникновения индентора в миллиметрах. Определяется в числах пенетрации как глубина погружения индентора под воздействием
46
силы тяжести в течение определенного времени (обычно 5 с) при заданной температуре.
Определение времени высыхания термопласта
Определение времени высыхания термопласта проводили с помощью валика ZTR 2070, который моделирует опорное давление автомобильной шины при проходе через дорожную разметку.
Определение удельной поверхности
Прибор ПСХ-К использовали для определения удельной поверхности, среднего размера частиц и газопроницаемости дисперсных материалов. Работа прибора основывается на методе газопроницаемости Козени и Кармана. Метод измерения заключается в определении времени прохождения фиксированного объема воздуха через слой образца.
Оценка внешнего вида, наличия посторонних включений, стеклошариков и крупных нерасплавленных частиц
Испытание проводят путем визуальной оценки материала (навеска массой 200 г). Пробу помещают на лист ватмана, жести или фольги белого цвета. Используя лупу, оценивают однородность материала, его цвет, наличие стеклошариков.
Для определения наличия крупных нерасплавленных частиц навеску материала (200 г) просеивают через сито с диаметром отверстий 2–3 мм. По остатку на сите оценивают наличие посторонних включений, слежавшихся комков пластика, крупных кусков смолы.
При наличии комков (материал в мешке может вообще слежаться в сплошной ком, который может быть удовлетворительно использован по своему целевому назначению), а также в случае оценки материала, поставленного в виде плавленых блоков, материал расплавляют при температуре, равной рабочей температуре (по паспорту), и процеживают через сито диаметром отверстий 2–3 мм, после чего проводят повторную оценку (визуально), фиксируя цвет, наличие крупных нерасплавленных частиц, однородность.
Для сплава наличие стеклянных микрошариков хорошо фиксируется на изломе с помощью лупы.
47
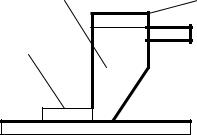
Определение рабочей температуры расплава
Навеску термопласта массой 0,5 кг разогревают в керамической или металлической емкости объемом не менее 0,5 л до рабочей температуры по паспорту и выдерживают при этой температуре 40 мин. Затем материал перемешивают не менее 2 раз. Из полученного расплава изготавливают тестовую полосу с использованием протяжной колодки – ручной каретки (рис. 2.1).
2 |
3 |
1
Направление
движения
Рис. 2.1. Изготовление тестовой полосы с помощью протяжной колодки: 1 – тестовая полоса; 2 – термопласт; 3 – протяжная колодка
Для этого в предварительно разогретую до температуры термопласта колодку заливают расплав, колодку предварительно ставят на лист подложки – фольги, смазанной глицерином или силиконовой смазкой и лежащей на ровной деревянной поверхности. Сдвигая колодку по поверхности со скоростью около 25 см/с, распределяют материал по листу подложки. Полученную массу охлаждают при комнатной температуре.
Визуально оценивают качество полученной тестовой полосы: она не должна иметь признаков недогрева (когда имеет место затрудненное истечение расплава, возникают нарушения сплошности и высокая степень неровности поверхности) или перегрева (имеют место расслоение материала и повышенная растекаемость) [86].
При наличии признаков недогрева или перегрева изготовление тестовых полос повторяют, увеличивая температуру разогрева на
48
5 °С, и, наоборот, при наличии признаков перегрева температуру разогрева снижают на 5 °С. За рабочую температуру принимают температуру разогрева материала, при которой признаков недогрева или перегрева не наблюдается.
Определение растекаемости расплава
Расплав термопласта (200 г), разогретый до рабочей температуры в фарфоровой чашке диаметром 120 мм, разливают на лист фольги, смазанной глицерином (силиконовой смазкой) и лежащей на деревянной поверхности. Розлив ведут с высоты 5 см при температуре окружающего воздуха 20±2 °С в 1 точку по центру лепешки в течение 1 мин. После остывания замеряют толщину лепешки в 4 точках посередине наибольшего и наименьшего радиусов лепешки и вычисляют среднее значение. Значение 8±2 мм следует считать предпочтительным.
Определение температуры размягчения термопласта
В основе определения лежит нормативный метод «кольцо
ишар», который заключается в том, что термопласт, помещенный в специальное кольцо, нагревается и отмечается температура, при которой стальной шарик, находящийся на поверхности термопласта, проходит через его размягчаемый при нагреве слой.
Испытание проводится на установке, состоящей из стеклянного стакана, в который помещен латунный штатив с гнездами для размещения кольца с термопластом и термометра. В стакан заливают теплоноситель – обычно глицерин.
При подготовке к испытанию кольцо укладывают на фольгу или гладкую металлическую пластину, смазанную глицерином или силиконовой смазкой. В кольцо заливают расплав термопласта (заподлицо) и дают ему застыть. После этого кольцо с термопластом снимают с фольги и помещают в гнездо латунного штатива.
На поверхность термопласта помещают стальной шарик. Проводят нагрев теплоносителя в стакане (на электроплитке или газовой горелке) со скоростью 5 °С/мин.
По мере повышения температуры термопласт размягчается
ишарик постепенно продавливается вниз. Момент, когда шарик
49
касается дна стакана, и принимается за величину температуры размягчения.
Определение степени белизны
Значения цветности определяли с помощью специального прибора – спектрофотометра СА-22 производства фирмы X-Rite (США), предназначенного для определения координат цветности, оттенков цвета и равномерности окраски.
В результате измерения получали координаты цветности X и Y точек пересечения граничных линий цветовых областей дорожной разметки, соответствующих колориметрической системе МКО (Международной комиссии по освещению), 1931 г.
Определение скорости течения расплава
Скорость течения расплава, или индекс расплава определяли по времени истечения расплава полимера через выдавливающий пластомер при заданных условиях температуры и нагрузки (анализатор индекса расплава – UMI4) по ГОСТ 11645 (метод А, С) – ISO 1133 – DIN 53735 – ASTM D 1238.
Выдавливающий пластомер состоял из вертикального цилиндра с головкой диаметром 2 мм в нижней части и съемного поршня в верхней части.
Автоматические анализаторы фиксировали скорость течения расплава термопласта, прошедшего через калиброванное отверстие фильеры пластомера.
Определение адгезии термопласта к асфальтобетону
Определение адгезии термопласта к асфальтобетону проводили методом прямого отрыва. Для этого образцы асфальтобетона цилиндрической формы диаметром 100±1 мм помещали во фторопластовую обойму и сверху заливали расплавом термопласта слоем
5–7 мм (рис. 2.2).
Образцы выдерживали в обойме при комнатной температуре в течение 24 ч. Затем извлекали из обоймы и эпоксидным клеем сверху и снизу приклеивали металлические грибки.
Испытания проводили на разрывной машине ИР-100М-авто при скорости деформирования 2,5 мм/мин.
50