
книги / Энергоэффективный термопластичный материал для дорожной разметки
..pdf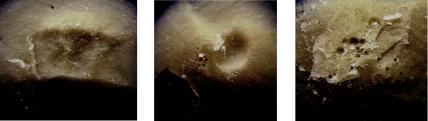
верхность которого представляет собой структуру, состоящую из гидрофобных и гидрофильных участков.
В1-м случае термопласт, находящийся в жидком состоянии при высокой температуре в момент нанесения, и разогретый термопластом до жидкого состояния битум образуют смесь. Поскольку основные компоненты этой смеси нефтеполимерная смола–битум имеют одну природу, при застывании образуется прочное соединение.
Вслучае контакта жидкого термопласта с поверхностью минеральных наполнителей асфальтобетона происходит затекание смолы в поры и трещины частиц наполнителя и образование также прочного соединения при застывании. Таким образом, несмотря на различные механизмы взаимодействия битума и расплавов термопласта, а также термопласта с поверхностью наполнителя, образуется контакт на разделе асфальтобетон–термопласт. Это подтверждается данными оптической микроскопии, показывающими, что отрыв пленки термопласта от поверхностного слоя асфальтобетона имеет когезионный характер.
На рис. 3.4 заметно повышение когезионной прочности термопласта по мере роста степени наполнения (до 60 %) минеральным наполнителем – доломитом, проявляющееся в уменьшении потерь термопласта при отрыве от асфальтобетона. Однако такая простая рецептура термопласта (смола + доломит) не обеспечивает необходимые эксплуатационные характеристики в качестве материала для дорожной разметки.
а |
б |
в |
Рис. 3.4. Места отрыва смолы 1 с различной степенью наполнения от асфальтобетона: а – 10 %; б – 30 %; в – 60 %
61
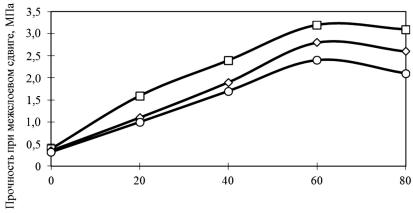
По этой причине производители термопластов для разметки вводят в состав рецептур другие различные наполнители и модификаторы, обеспечивающие технологические параметры и необходимую долговечность продукции.
Для изучения результатов взаимодействия различных компонентов и модификаторов, вводимых в рецептуру термопласта, интерес представляла оценка каждого ингредиента при его последовательном введении в состав смеси.
Так, наполнение доломитом применяемых в работе нефтеполимерных смол показывает типичную картину для дисперснонаполненных композитов.
Предел прочности при межслоевом сдвиге достигает максимальных значений на уровне от 60 до 75 % по степени наполнения
(рис. 3.5).
В зависимости от дисперсности наполнителя эксперименты также показывают рост прочности по мере уменьшения размеров частиц наполнителя (рис. 3.6).
Степень наполнения Мд-40, %
Рис. 3.5. Зависимость прочности при сдвиге от степени наполнения: смола 1;
смола 2;
смола 3
В качестве пластификатора для улучшения перерабатываемости состава термопласта ранее часто использовали масло ПОД ‒ продукт окисленияидегидратирования, отходпроизводствакапролактама.
62
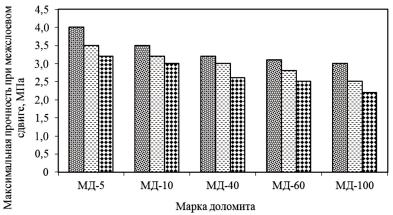
Рис. 3.6. Зависимость прочности при сдвиге от марки доломита: смола 1;
смола 2;
смола 3
Однако из-за повышенной токсичности данного продукта в современных разметочных материалах вместо него используют различные технические масла.
Так, введение дистиллятного нефтяного масла марки И-50А способствует улучшению условий переработки смесей в экструдере разметочной машины. При содержании масла около 4–5 мас. % прочностные характеристики композиции несколько возрастают, что, видимо, связано с более высокой степенью гомогенизации расплава при перемешивании (рис. 3.7).
Реологические свойства также возрастают, что проявляется как повышение текучести расплава при температуре от 180 до 190 °С в условиях переработки (рис. 3.8).
Опыт эксплуатации дорожной разметки при различных значениях температуры в условиях зима-лето показывает, что наиболее быстро разметка разрушается при отрицательных значениях температуры. Связано это с тем, что при отрицательных значениях температуры значительно снижаются эластические свойства материала, возрастает его хрупкость. Следует также учитывать тот факт, что термопласт формируется на подложке из другого материала – асфальтобетона, обладающего обычно более низкой активностью.
63
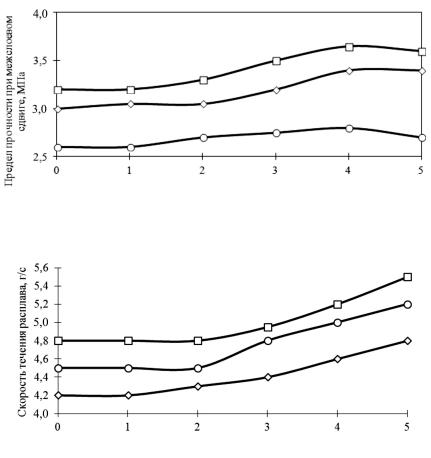
Содержание масла индустриального, мас. %
Рис. 3.7. Зависимость прочности при сдвиге от содержания масла: смола 1 + МД-40;
смола 2 + МД-40;
смола 3 + МД-40
Содержание масла, мас. %
Рис. 3.8. Зависимость скорости течения расплава НПС + МД-40 от содержания введенного индустриального масла при 180–190 °С:
смола 1 + МД-40;
смола 2 + МД-40;
смола 3 + МД-40
Вусловиях низких значений температуры влага, проникающая
васфальтобетон, превращается в лед, что приводит к образованию трещин в дорожном покрытии. Возникающие при этом касательные напряжения на границе термопласт–асфальтобетон приводят либо
к разрыву (рис. 3.9, а), либо к отслоению дорожной разметки
(рис. 3.9, б).
64

а |
б |
в |
Рис. 3.9. Состояние термопласта при образовании трещины в асфальтобетоне
Для повышения эксплуатационных характеристик в условиях низких значений температуры производители дорожной разметки вводят в состав собственных рецептур модификаторы ‒ термопластичные эластомеры этиленвинилацетат и(или) блок-сополимеры на основе стирола и синтетического каучука. Эти вещества предназначены для повышения эластичности композита при низких значениях температуры и, соответственно, усиления контакта на границе с асфальтобетоном (рис. 3.9, в).
Этиленвинилацетат (ЭВА, EVA), получаемый в результате сополимеризации этилена и мономера винилацетата, является высокомолекулярным соединением, относящимся к группе полиолефинов. Представляет собой прозрачные гранулы со слабым запахом уксусной кислоты, обладает высокой эластичностью при низких значениях температуры, имеет хорошую адгезию к различным материалам.
Термопластичный эластомер стирол-изопрен-стирол (SIS) представляет собой полимер, в котором на концах молекулярной цепи содержатся полистирольные фазы, а в качестве звеньев выступают полиизопреновые фазы.
Такое строение SIS позволяет обеспечить высокие характеристики при низкой температуре – относительное удлинение и гибкость. Кроме того, введение SIS в композит обеспечивает повышение адгезионных характеристик при повышенных значениях температуры, что является как раз положительным качеством при нанесении термопласта на подложку из асфальтобетона.
Введение ЭВА в количестве до 2,5 % не приводит к скольконибудь заметному изменению прочности термопласта (рис. 3.10), но при этом возрастает адгезия к асфальтобетону на 10–15 % (рис. 3.11).
65
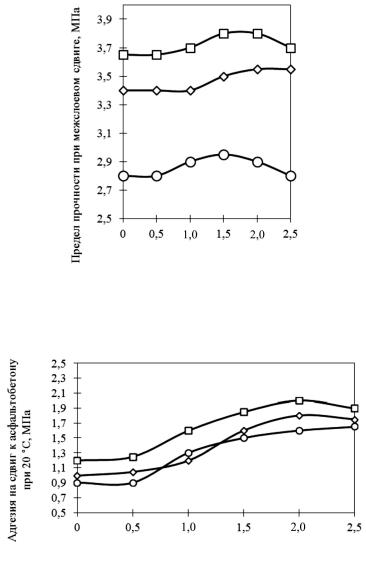
Содержание ЭВА, мас. %
Рис. 3.10. Зависимость прочности при межслоевом сдвиге от содержания ЭВА: смола1 + МД-40 + 4 % масла;
смола2 + МД-40 + 4 % масла;
смола 3 + МД-40 + 4 % масла
Содержание ЭВА, мас. %
Рис. 3.11. Зависимость адгезии на сдвиг от содержания ЭВА: смола 1 + МД-40 + 4 % масла;
смола 2 + МД-40 + 4 % масла;
смола 3 + МД-40 + 4 % масла
66
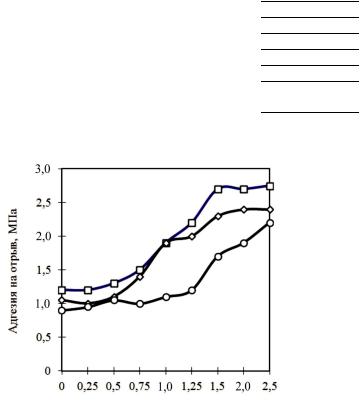
Для исследования влияния компонента SIS на адгезию к асфальтобетону были испытаны следующие модельные составы
(табл. 3.3).
Таблица 3.3
Модельный состав термопласта для определения адгезионных и эластических характеристик при введении SIS
Наименование |
Содержание компонента, мас. % |
||
компонента |
Состав 1 |
Состав 2 |
Состав 3 |
Связующее |
Смола 1 |
Смола 2 |
Смола 3 |
Наполнитель МД-40 |
60 |
60 |
60 |
Масло индустриальное |
4 |
4 |
4 |
ЭВА |
1,5 |
1,5 |
1,5 |
SIS |
0; 0,5; 1,0; 1,5; |
0; 0,5; 1,0; 1,5; |
0; 0,5; 1,0; 1,5; |
|
2,0; 2,5 |
2,0; 2,5 |
2,0; 2,5 |
Результаты испытаний представлены на рис. 3.12 и 3.13.
Содержание SIS, мас. %
Рис. 3.12. Адгезия модельных составов композита к асфальтобетону в зависимости от содержания SIS: состав 1;
состав 2;
состав 3
67
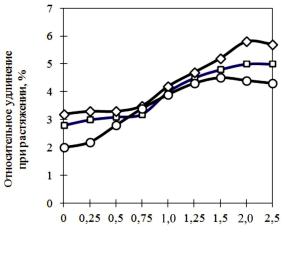
Содержание SIS, мас. %
Рис. 3.13. Относительное удлинение модельных составов композита в зависимости от содержания SIS: состав 1;
состав 2;
состав 3
Из экспериментальных данных видно, что полистирольная часть молекулы SIS в соединении с изопреновой частью повышает адгезию термопласта к асфальтобетону. Видимо, это связано с тем, что стирольные компоненты SIS хорошо адсорбируют масляные компоненты битума, что способствует более прочному контакту термопласта и асфальтобетона – повышению их адгезионного взаимодействия.
С другой стороны, каучукообразная изопреновая часть является эффективным препятствием для развития микротрещин в дис- персно-наполненном композите и существенно повышает эластичность всего материала.
Таким образом, введение в рецептуру около 2 % SIS для выбранных рецептур термопластов увеличивает адгезию к асфальтобетону и эластические свойства примерно в 2 раза.
Известно [85–90], что для получения разметочного термопласта с наилучшими характеристиками в его состав в качестве наполнителей необходимо вводить и другие компоненты: кварцевый пе-
68
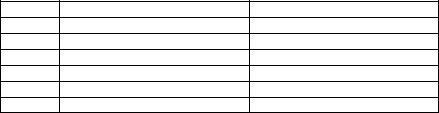
сок (повышение твердости), диоксид титана (повышение белизны), стекломикрошарики (обеспечение световозвращения в темноте).
Оценку основных эксплуатационных характеристик, зависящих от указанных ингредиентов, добавленных в основной состав, проводили методами математического моделирования. При этом применяли градиентный метод оптимизации состава.
Базовый состав композиции для разметочного термопласта был выбран по результатам экспериментов, осуществленных в настоящей работе (табл. 3.4).
Таблица 3.4
Базовый состав ингредиентов для термопластичной композиции
№ п/п |
Ингредиент |
Содержание, мас. % |
1 |
НПС |
22 |
2 |
Масло индустриальное |
4 |
3 |
SIS |
2 |
4 |
ЭВА |
2 |
5 |
Воск ПВ-200 |
2 |
6 |
Наполнитель МД-40 |
68 |
Введение дополнительных ингредиентов проводили за счет соответствующего снижения доли доломита МД-40 так, чтобы сохранялись общие пропорции базового состава.
При проведении полного факторного эксперимента в качестве параметров оптимизации были выбраны следующие характеристики:
–прочность при межслоевом сдвиге – Y1, МПа;
–относительное удлинение при разрыве – Y2, %;
–адгезия к асфальтобетону – Y3, МПа;
–прочность при сжатии – Y4, МПа.
В качестве факторов, оказывающих влияние на параметры оптимизации, выбраны следующие:
–содержание кварцевого песка – X1;
–содержание диоксида титана (TiO2) – X2;
–содержание микростеклошариков (МСШ) – X3.
69
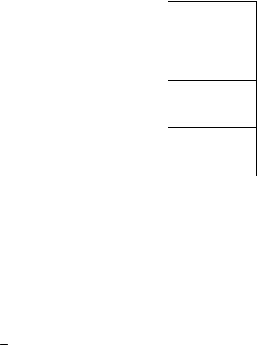
Уровни факторов и интервалы их варьирования представлены в табл. 3.5.
Таблица 3.5
Основные уровни факторов и интервалы варьирования
Наименование |
Нижний |
Основной |
Верхний |
Интервал |
|
|
|
уровень |
уровень |
уровень |
варьирования |
Фактор X1 |
Значение, |
5 |
10 |
15 |
5 |
|
мас. % |
–1 |
0 |
+1 |
|
|
Код |
2 |
|||
Фактор X2 |
Значение, |
3 |
5 |
7 |
|
|
мас. % |
–1 |
0 |
+1 |
|
|
Код |
5 |
|||
Фактор X3 |
Значение, |
15 |
20 |
25 |
|
|
мас. % |
–1 |
0 |
+1 |
|
|
Код |
|
Проверка воспроизводимости результатов осуществлялась по данным, полученным при проведении серий из 5 параллельных опытов в 3 различных точках факторного пространства (табл. 3.6).
Алгоритм обработки результатов экспериментов выглядел следующим образом:
1. Вычисляли среднее арифметическое значение функции отклика для каждой серии параллельных опытов по формуле
Yj k1 |
k |
|
i 1Yj,i , |
(3.1) |
где j – номер серии параллельных опытов; k – количество параллельных опытов; Yji – текущее значение параметра оптимизации i-го опыта j-й серии.
2. Оценку дисперсии для каждой серии параллельных опытов определяли по формуле
2 |
1 |
|
|
|
2 |
|
|
|
|
|
|
|
|||||
s j |
|
|
|
Yji YJ |
. |
(3.2) |
||
k 1 |
70