
книги / Энергоэффективный термопластичный материал для дорожной разметки
..pdf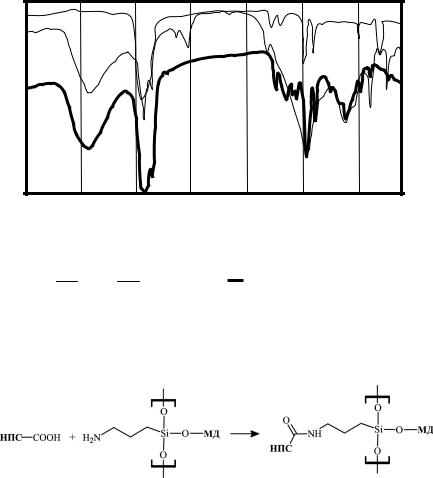
доломите, с выделением простого алифатического диэтилового эфи-
ра СН3CH2ОCH2СН3.
ИК-спектры НПС, наполненной микродоломитом (МД), представлены на рис. 4.6.
НПС; МД + АГМ-9; (МД+АГМ-9) + НПС
3500 3000 2500 2000 1500 1000
Частота, см–1
Рис. 4.6. ИК-спектры НПС, наполненной микродоломитом: НПС; МД + АГМ-9; (МД + АГМ-9) + НПС
При введении аппретированного наполнителя (МД + АГМ-9) в состав нефтеполимерной смолы происходит реакция присоединения аппрета к макромолекулам полимеров, входящих в состав смолы
(рис. 4.7).
Рис. 4.7. Реакция присоединения аппрета к макромолекулам полимеров
После обработки модификатором АГМ-9 частицы доломитанаполнителя из нейтральных становятся активными, что проявляет-
81
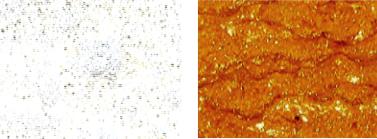
ся в повышении их диспергируемости и, соответственно, степени наполнения полимера. Это становится возможным за счет образования химического мостика из связи доломит–силан–смола. Образование сшивающих мостиков приводит к тому, что объем композита, состоящий из матрицы нефтеполимерной смолы и аппретированного силаном наполнителя (доломита), образует пространственно сшитую структуру.
Казалось бы, такие морфологические изменения должны привести к созданию прочной структуры, устойчивой к эксплуатационным воздействиям, однако это оказывается совсем не так.
При повышенной температуре и активном перемешивании ингредиентов в процессе приготовления смеси в пропорции 70 % доломита, 30 % НПС 1 происходит бурное выделение углекислого газа СО2, источником которого являются заряженные карбонатные группы СО32–.
Из-за быстрого протекания реакции сшивания нейтральные молекулы СО2 превращают композит в пористый материал, а ионы кислорода окисляют смоляную часть, что проявляется в потемнении всей массы (рис. 4.8).
Рис. 4.8. Изменение цвета композита, наполненного МД, модифицированного АГМ-9
Динамические характеристики композита представлены на рис. 4.9.
Из приведенных экспериментальных данных можно сделать вполне обоснованное заключение, что полученный композиционный
82
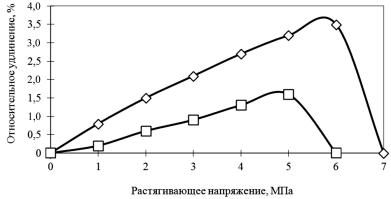
материал является твердым и хрупким и для целей использования в дорожной разметке не подходит.
Рис. 4.9. Эластические характеристики состава 1 с немодифицированным и модифицированным доломитом: состав 1;
состав 1М
На первый взгляд, полученные результаты говорят о том, что аппретирование доломита органосиланами нецелесообразно из-за получения сильно сшитой и хрупкой структуры. Однако эффект повышения прочности в результате образования пространственно сшитой структуры позволяет предположить возможность использования этого эффекта для повышения свойств композита.
Фактически полученный результат аналогичен процессу формирования эбонита – продукта вулканизации каучука с большим количеством сшивающего агента (серы). Часто сшитая структура эбонита исключает наличие эластичности, но при этом придает высокую прочность.
С целью избежать достижения высокой прочности композиции за счет формирования сильно сшитой структуры (ее критического состояния) в настоящей работе предложено применение комбинированного сочетания микродоломита аппретированного и неаппретированного в соотношении (10–15) : (85–90) соответственно.
При этом достигается формирование структуры, которая представляет собой редкую сетку (по аналогии с резиной), обладающую
83
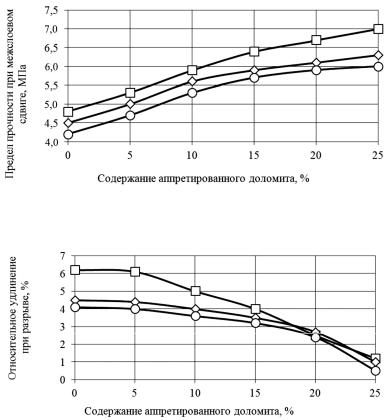
повышенной прочностью и одновременно достаточной эластичностью, обеспечивающей хорошие эксплуатационные характеристики.
Зависимость прочности от содержания модифицированного АГМ-9 доломита представлена на рис. 4.10. Зависимость удлинения композита от содержания аппретированного доломита ‒ на рис. 4.11.
Рис. 4.10. Зависимость прочности от содержания модифицированного АГМ-9 доломита: состав 1;
состав 2;
состав 3
Рис. 4.11. Зависимостьудлинениякомпозитаотсодержанияаппретированного доломита: состав 1;
состав 2;
состав 3
Исследования показывают, что лучший результат получается при использовании смеси доломита аппретированного и неаппретированного в соотношении (10–15) : (85–90).
84
Содержание смолы, являющейся связующим в термопласте дорожной разметки, является фактором, от которого зависят износостойкость и коэффициенты температурного расширения композита.
С учетом того, что разметка наносится на асфальтобетон, который обладает иными температурными коэффициентами расширения, деформативные характеристики разметки должны превосходить аналогичные свойства асфальтобетона. Ввиду этого при сильном сцеплении термопласта и дорожного покрытия при изменении температуры внешнего воздуха происходит разрыв материала, если его температурный коэффициент оказывается меньше, чем аналогичный показатель у асфальтобетона. В результате возникают нарушения в сплошности, что приводит к разрушению дорожной разметки.
Считается, что адгезия термопласта к дорожному покрытию прямо пропорциональна долговечности разметки. Это утверждение довольно спорно, так как трудно представить, что физические и химические связи могут возникнуть достаточно быстро в местах разрыва. Скорее всего, зарубежные термопласты обладают большей эластичностью по сравнению с отечественными и лучше реагируют на трещинообразование в асфальтобетоне.
4.2.Выводы по главе 4
1.Спектр микродоломита проявляется набором пиков, харак-
теризующих наличие функциональных групп анионов СО3–2 (2628, 2536, 1097, 880, 727 см–1), и сорбированной поверхностью частиц влаги – гидроксильных групп ОН (3445 и 1638 см–1). Пики 2921
и2853 см–1 относят к валентным колебаниям метиленовой группы
(CH2). Спектр нефтеполимерной смолы, наполненной микродоломитом, представляет собой суперпозицию спектров микродоломита
инефтеполимерной смолы, что говорит об отсутствии химического взаимодействия между компонентами системы.
2.С целью придания повышенных адгезионных связей между наполнителем и полимером в работе использовалась модификация (аппретирование) органосиланом марки АГМ-9. При этом кремний-
85
функциональная группа реагировала с наполнителем, а органофункциональная группа – со смолой.
3.Доказано, что при модификации органосиланом марки АГМ-9 происходит повышение адгезионных связей между наполнителем и полимером. При этом кремний-функциональная группа органосилана реагирует со смолой. Для исключения потемнения и охрупчивания при одновременном повышении свойств композита предложено использование смеси доломита аппретированного и неаппретированного в соотношении (10–15) : (85–90).
4.Установлена зависимость функциональных свойств полимерных разметочных композиций от их рецептурного состава, обеспечивающая направленное регулирование долговечности покрытия
сучетом дорожно-климатических условий эксплуатации, характера и интенсивности автотранспорта.
5.Эффект повышения прочности в результате образования пространственной сшитой структуры позволяет предположить возможность использования этого эффекта для повышения свойств композита.
6.Лучший результат получается при использовании смеси аппретированного и неаппретированного доломита в соотношении
(10–15) : (85–90).
86
Глава 5. НАУЧНО-ТЕХНИЧЕСКОЕ СОПРОВОЖДЕНИЕ ПРОИЗВОДСТВА ТЕРМОПЛАСТИЧНЫХ МАТЕРИАЛОВ ДЛЯ ДОРОЖНОЙ РАЗМЕТКИ В ООО ПХ «ТЕХНОПЛАСТ»
5.1.Участие авторов в научно-техническом сопровождении производства материалов для дорожной разметки
вООО ПХ «Технопласт»
Входе проведения научных изысканий в период с 2010 г. по настоящее время авторами осуществлялось научно-техническое сопровождение разработки составов и производства разметочных материалов в ООО ПХ «Технопласт» [87].
Всоставе организации имеется испытательный лабораторный центр контроля качества дорожно-строительных материалов и дорожной разметки, осуществляющий контроль качества термопластичных материалов, микростеклошариков для разметки дорог, лакокрасочных покрытий для противокоррозионной защиты, грунтов, бетонных смесей, нерудных строительных материалов, асфальтобетонных, дорожных, аэродромных смесей и асфальтобетонов.
Специалистами ООО ПХ «Технопласт» проводятся работы по нанесению дорожной разметки на автомобильные дороги федерального и территориального значения, расположенные в 14 субъектах Российской Федерации – Самарской, Саратовской, Ульяновской, Кировской, Нижегородской, Оренбургской, Пензенской областях, Пермском крае, республиках Башкортостан, Марий Эл, Мордовия, Татарстан, Удмуртия, Чувашия, а также за пределами Приволжского федерального округа.
При входном контроле качества испытано более 20 видов термопластичных материалов, более 10 видов микростеклошариков для разметки дорог, проведен операционный, приемочный и эксплуатационный контроль дорожной разметки.
Воснове технологической оценки состава термопласта для дорожной разметки лежит калькуляция производственных затрат,
87
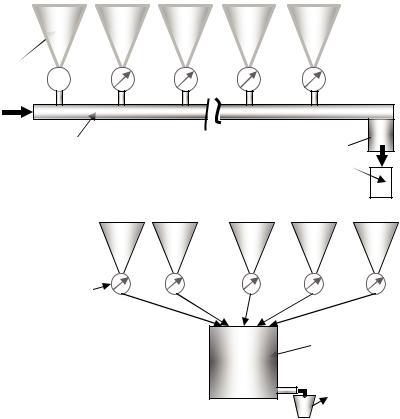
связанных с конкретной технологической схемой. В настоящее время существует 2 таких схем (рис. 5.1): схема, определяющая производство термопласта в виде сухой механической смеси (см. рис. 5.1, а); схема, определяющая производство термопласта в виде гомогенных плавленых блоков (см. рис. 5.1, б) [1–8].
1
2
3 |
4 |
|
5
а
1
2
3
4
б
Рис. 5.1. Технологическая схема производства термопласта для дорожной разметки: а – технология получения сухой смеси: 1 – бункер для сыпучих продуктов; 2 – дозатор весовой; 3 – пневмотранспорт; 4 – смеситель; 5 – мешкотара; б – технология получения плавленых блоков (рис. авторов): 1 – бункер сыпучих продуктов; 2 – дозатор весовой; 3 – смеситель
с электроподогревом; 4 – тара (ведро)
88
В самом общем виде любой процесс получения маркировочных термопластов состоит из следующих технологических операций: подготовка компонентов, приготовление термопластичной смеси, растаривание и упаковка.
Реальная схема производства сухой механической смеси (см. рис. 5.1, а) состоит из последовательного дозирования компонентов и их подачи в пневмотранспортер. Под действием сжатого воздуха в процессе перемещения происходит их перемешивание с образованием достаточно однородной смеси. Полученная масса поступает в механический лопастной смеситель, где окончательно перемешивается до гомогенного состояния.
Смешивание всех компонентов в смесителе производят в течение 3–5 мин. Во время смешивания в смеситель вводят навески жидких компонентов, если последние предусмотрены рецептурой. Выгрузку готовой смеси производят через отверстие в днище корпуса смесителя. Готовую смесь из приемного бункера шнеком подают в мешки, установленные на весах.
После достижения заданного веса (30 кг) мешки передвигают на транспортер, зашивают с помощью зашивочной машины, загружают в поддон-контейнер, отвозят и складируют до момента отгрузки потребителю. Тарные мешки могут быть бумажными, бумажными с полиэтиленовыми вкладышами или малогабаритными (емкостью 12–20 кг) запаянными мешками из термоусадочного полиэтилена специальных марок. В последнем случае имеется возможность использования термопласта вместе с тарными мешками при загрузке его в котел разметочной машины. Как правило, в таких мешках выпускает порошкообразный термопласт большинство зарубежных фирм.
Помимо того, что это является хорошим экологическим решением, в этом случае еще и исключается пыление материала при его загрузке в котел, а также технологические трудности при использовании, например, слежавшегося в ком термопласта.
Материал мешка не растворяется в расплаве, но при общей доле его всего лишь 0,1 % и форме в виде крайне мелких сгустков
89
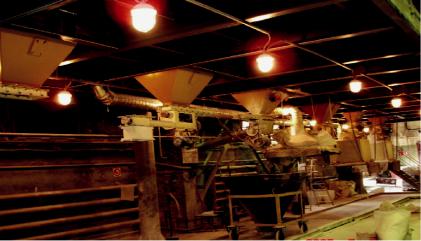
(термоусадочный) он не является основанием для потери качества при производстве разметочных работ, особенно с учетом использования фильтрующей сетки при переливе расплава из маточного котла в котел разметочной машины.
Общий вид производственного комплекса приведен на рис. 5.2.
Рис. 5.2. Общий вид производственного комплекса
Типичный цикл производства термопласта представлен в табл. 5.1.
Из приведенных данных следует, что оборот технологического смесителя осуществляется за 27–30 мин, а в рабочую смену (6 ч, без учета времени на подготовку) смеситель находится в обороте 12 раз, при этом может быть изготовлено около 5 т термопласта. Это и есть производительность данного способа производства термопласта, технологические простои оборудования при этом практически отсутствуют.
Следует отметить, что присутствие в современных составах термопластов таких компонентов, как SIS-полимеры, вносит определенные коррективы в организацию технологического процесса.
90