
книги / Принципы технологии основного органического и нефтехимического синтеза.-1
.pdf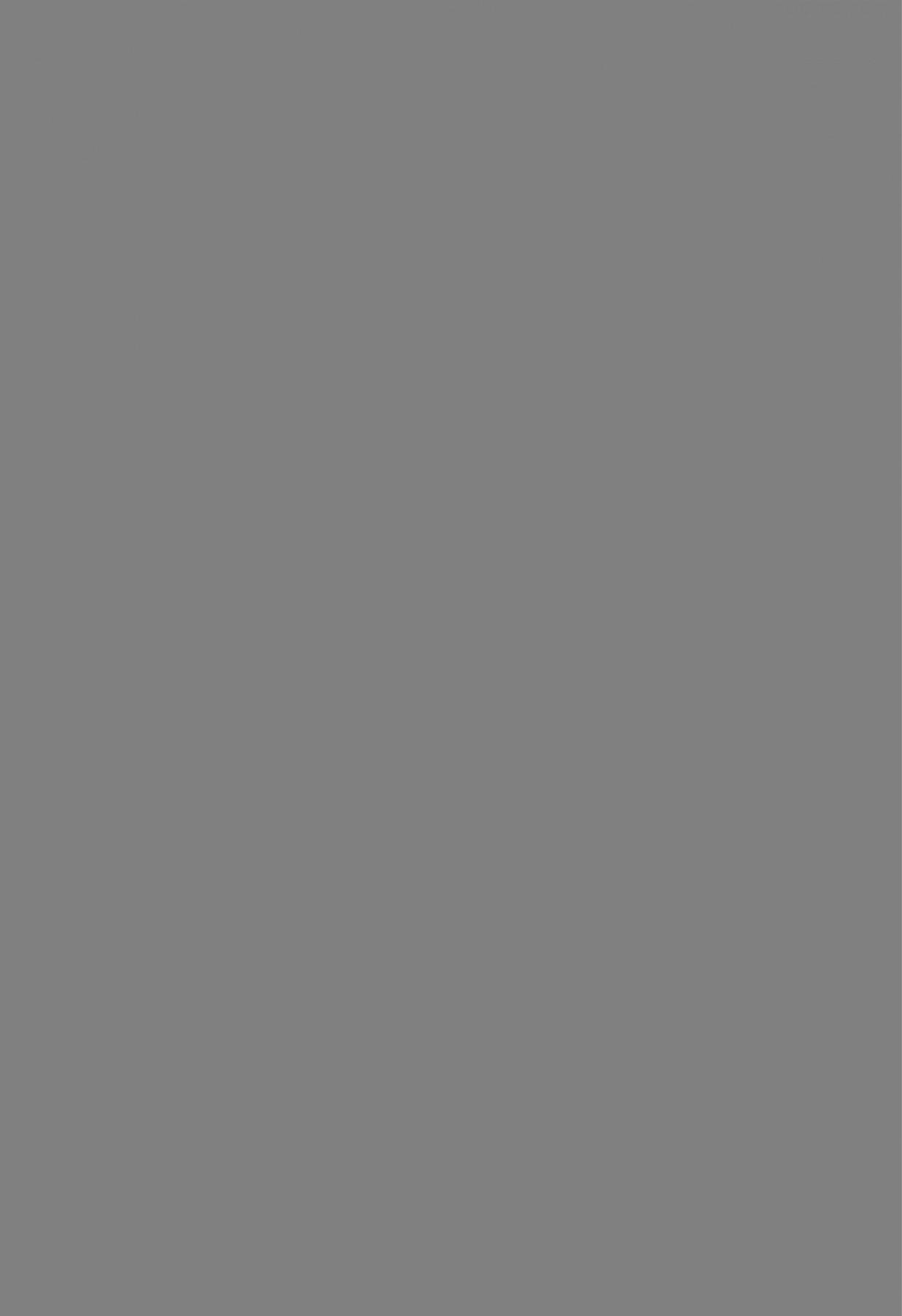
8.4. ПРИНЦИПЫ В ТЕХНОЛОГИИ ПРОИЗВОДСТВА ОКСИДА ЭТИЛЕНА ОКИСЛЕНИЕМ ЭТИЛЕНА
Технология относится к непрерывным, одностадийным и использует дешевое и доступное сырье — этилен и технический кислород. Процесс при невысоких конверсиях обеспечивает относительно высокую — до 81—82 % — селектив ность (кислородный процесс). Температура в реакторе окисления позволяет по лучать пар с высоким энергетическим потенциалом (давление 4,5—5 МПа), ко торый в дальнейшем может использоваться в производстве.
Интенсивное использование рециркуляции позволяет несмотря на низкие конверсии (20—30 %) олефина за один проход обеспечить полное использова ние исходного сырья. Относительно невысокими оказываются затраты на выде ление целевого продукта из циркуляционного потока абсорбцией. Эффектив ная система хемосорбции С 0 2 из рециркуляционного потока (кислородный ва
риант) позволяет существен но снизить количество газов сдувки и тем самым по тери исходного сырья. Технология обеспечивает невысокие потребности в воде, так как имеет по ней внутренний цикл. Оптимальным для данной технологии является применение аппаратов средней мощности, поскольку именно кожу хотрубные реакторы обеспечивают минимальные локальные перегревы реакци онной смеси, что позволяет повысить дифференциальную селективность по це левому продукту. Таким образом, возможно создание линий большой единич ной мощности, включающих в себя несколько параллельно работающих реакто ров.
Г Л А В А 9
ПРО И ЗВО ДСТВО Ф ЕНОЛА И АЦЕТОНА
ИЗ И ЗО П РО П И Л БЕН ЗО Л А
Внастоящее время используются различные методы получения фенола: ка талитическое окисление толуола; прямое окисление бензола; кумольный метод; окисление циклогексана с последующим дегидрированием циклогексанона до
фенола; хлорбензольный метод; окислительное хлорирование бензола (метод Рашига); сульфонатный метод. Из перечисленных методов в промышленности используются четыре: каталитическое окисление толуола, прямое окисление бензола, метод Рашига и кумольный метод. Основное количество фенола (более 90 %) получают кумольным методом. Суммарная мощность установок, произ водящих фенол кумольным методом, составляет около 5 млн т/год. Доля кумольного метода в общем производстве фенола составляет в США — 98 %, в ФРГ — 95,3 %, вЯпонии — 100 %. Особенно привлекателен кумольный метод производ ства фенола тем, что одновременно позволяет получать другой ценный продукт органического синтеза — ацетон. Кумольный способ производства фенола и ацетона является ярким примером реализации химического принципа приме нения «сопряженных» методов втехнологии органического синтеза (см. гл. 6).
Разработка комплексного кумольного метода, который позволяет получать не только фенол и ацетон, но и пропиленоксид, показала, что получение пропиленоксида эпоксидированием пропилена гидропероксидными соединениями является наиболее эффективным методом синтеза этого вещества.
Кумольный метод получения фенола и ацетона разработан советскими уче ными Г1.Г. Сергеевым, Б.Д. Кружаловым, Р.Ю. Удрисом и внедрен в 1944 г. За рубежом аналогичные производства были пущены позднее: в Канаде и во Фран ции — в 1953 г., в США и ФРГ — в 1954 г.
Процесс производства фенола и ацетона кумольным методом состоит из 7 стадий: алкилирование бензола, окисление изопропилбензола, выделение гид ропероксида, разложение гидропероксида, нейтрализация гидропероксида, вы деление фенола, выделение ацетона (рис. 9.1 ).
Стадия алкилирования достаточно подробно была рассмотрена в гл. 7. По этому в этой главе мы рассмотрим остальные стадии.
9.1. ТЕОРЕТИЧЕСКИЕ ОСНОВЫ ПРОЦЕССА
Окисление изопропилбензола. Реакция окисления изопропилбензола
С6Н6(СН3)2СН t0i > С6Н5(СН3)2СООН
относится к реакциям, протекающим по механизму сложных цепных реакций с вырожденным разветвлением цепи. Получить 100 %-ю селективность по гидро пероксиду в реакции окисления изопропилбензола невозможно, так как парал лельно с основным продуктом образуются такие побочные продукты, как диме-
16* |
243 |
Отработанные
газы
Рис. 9.1. Блок-схема совместного получения фенола и ацетона
тилфенилкарбинол, ацетофенон, муравьиная кислота, в незначительной степе ни пероксидные продукты типа дикумилпероксида.
В промышленных условиях в настоящее время селективность стадии окис ления изопропилбензола по гидропероксиду составляет 91—95 % (мол.). Такая селективность обеспечивается конструктивным оформлением реактора, ис пользованием оптимальных концентраций гидропероксида в реакционной мас се (15—25 %), оптимальной температуры ( 1 00— 1 20 °С) и наиболее активного ка
тализатора.
Окисление можно проводить как в жидкой, так и в паровой фазе на разных катализаторах. Наиболее широко в качестве катализаторов процесса, проходя щего в жидкой фазе при температурах выше 100 °С (100—120 °С), применяются резинаты и нафтенаты кобальта и марганца. Можно применять и инициаторы, в качестве которых могут служить сами гидропероксиды, которые добавляют в шихту в количестве 2,5—3,5 %.
Образующийся гидропероксид изопропилбензола частично подвергается термическому разложению. С повышением температуры скорость распада гид ропероксида возрастает. Основными продуктами распада гидропероксида изо пропилбензола являются диметилфенилкарбинол, ацетофенон и метиловый спирт:
С 6 Н 5 ( С Н з ) 2С О О Н - » С б Н 5 ( С Н з ) 2С О Н
С 6 Н 5 ( С Н 3) 2С О О Н - > С 6 Н 5 С О С Н 3 + С Н з О Н
2 4 4
Образующийся метанол окисляется в формаль |
|
|
дегид и муравьиную кислоту, являющуюся ингиби |
|
|
тором процесса окисления изопропилбензола. |
|
|
Как отмечалось ранее, на выход гидропероксида |
|
|
влияют температура и продолжительность окисле |
|
|
ния (рис. 9.2). Однако чрезмерное понижение тем |
|
|
пературы уменьшает скорость реакции. Так, за 1 ч |
|
|
при 120 °С выход гидропероксида составляет 8—10, |
|
|
а при 100 °С — 2—3 % (мае.). |
|
|
Распад гидропероксида начинает протекать со |
|
|
значительной скоростью при его концентрации в |
Рис. 9.2. Зависимость содержа |
|
реакционной массе 18 % и выше. При повышенных |
||
температурах его распад может идти со взрывом. |
ния гидропероксида в реакци |
|
Даже при оптимальной концентрации пероксида в |
онной |
массе от продолжитель |
оксидате содержится от 0,5 до 5 % продуктов распа |
ности |
окисления при различ |
|
ной температуре |
да. Процессу окисления благоприятствует щелоч
ная среда (pH 7,5), так как нейтрализуются кислоты-ингибиторы, образующие ся в процессе окисления. В этом случае будет осуществляться совмещенный процесс, так как параллельные реакции нейтрализации позволяют ускорять ос новную реакцию. В связи с этим окисление иногда ведут кислородом воздуха в водно-щелочной эмульсии (1 %-й раствор ЫагСОз) при интенсивном переме
шивании и в присутствии поверхностно-активных веществ.
Таким образом, процесс окисления чаще всего проводят при 120—130 °С, р —0,5—1,0 МПа, pH 8,5—10,5; в этих условиях конечное содержание гидропе роксида составляет около 25 %. Для проведения процесса окисления применя ют различные реакторы (рис. 9.3) колонного типа; с перемешивающим устрой ством (каскад реакторов); эрлифтового типа.
В аппаратах колонного типа для отвода тепла устанавливаются змеевики (от водится 1967 кДж на 1кг превращенного изопропилбензола). Реактор колонно го типа является компактным. Каскад аппаратов с перемешивающими устрой ствами или каскад реакторов эрлифтового типа требуют использования боль шого количества арматуры, управлять процессом втаких реакторах сложно.
Учитывая, что в оксидате содержится около 25 % пероксида, а на дальней шую переработку должен подаваться концентрированный раствор, проводят его концентрирование в мягких условиях (в вакууме, при низких температурах). Наиболее широко для этой цели используют вакуумную ректификацию (чаще всего на двухколонной установке). Получаемый технический гидропероксид имеет следующий состав (в %): гидропероксид изопропилбензола — 90—91; диметилфен илкарбинол — 5—7; ацетофенон — 1,0—1,5; дикумил пероксид — 0,4—0,6; муравьиная кислота — 0,01—0,04.
В дальнейшем в зависимости от целей процесса (получают только фенол и ацетон или фенол, ацетон и пропиленоксид) пероксид направляется на разло жение или эпоксидирование пропилена.
Разложение гидропероксида изопропилбензола. Технический гидропероксид
изопропилбензола направляют на сернокислотное разложение, в результате ко торого образуются фенол и ацетон, атакже побочные продукты (а-метилстирол, кумолфенол, димеры а-метилстирола и смолы):
С 6 Н 5(С Н з) 2С О О Н " iSOi >С6Н5ОН + СНзСОСНз
245
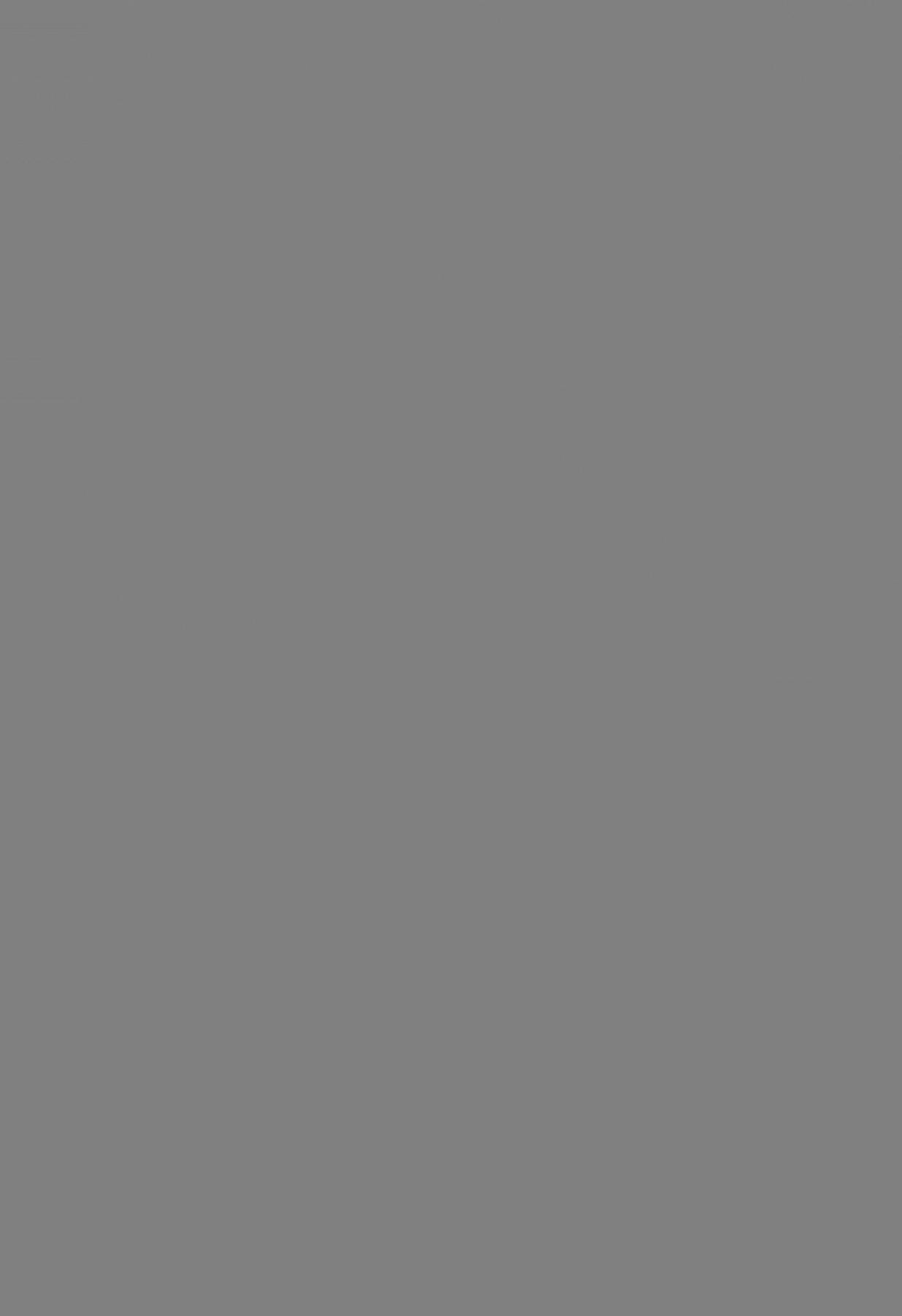
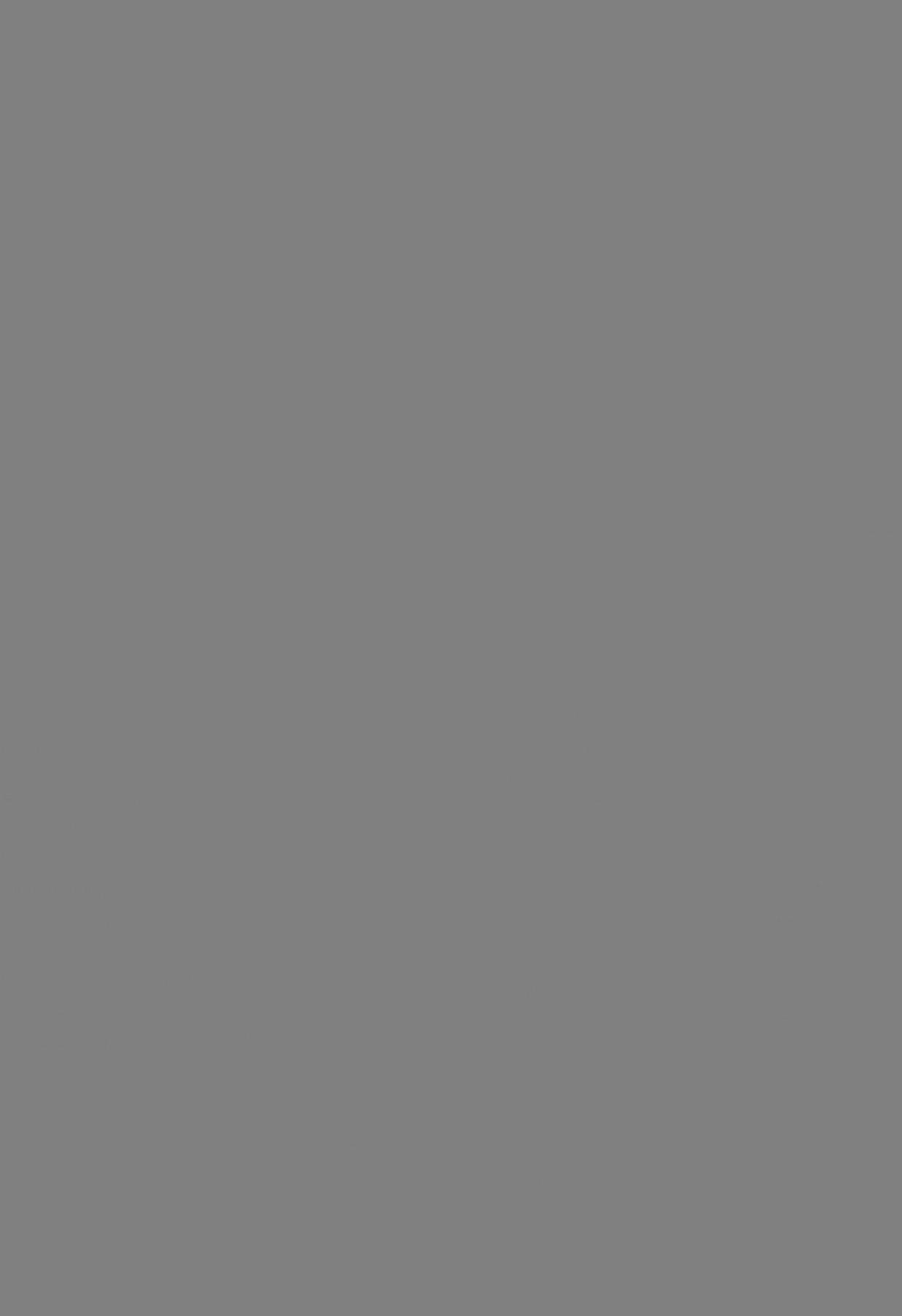
водой. При этом часть реакционной смеси отводится на дальнейшую переработ ку, а остальная часть — на рециркуляцию. В этом случае рециркуляция приводит к повышенному выходу побочных веществ.
Более совершенным является изотермический реактор (рис. 9.4, в), в кото ром тепло отводится за счет испарения избытка ацетона. Такой реактор можно секционировать поперечными перегородками, что снижает выход побочных продуктов за счет уменьшения времени контакта. Выход фенола и ацетона в этом реакторе может достигать 98 % от теоретического.
9.2.ТЕХНОЛОГИЯ СОВМЕСТНОГО ПРОИЗВОДСТВА ФЕНОЛА
ИАЦЕТОНА ИЗ ИЗОПРОПИЛБЕНЗОЛА
Технологическая схема производства фенола и ацетона кумольным методом представлена на рис. 9.5. Свежий изопропилбензол смешивают с возвратным изопропилбензолом и гидропероксидом изопропилбензола (6 % от массы ших
ты) в смесителе 7. Шихту насосом ^прокачивают через теплообменник J и пода ют в верхнюю часть колонны окисления 2. В теплообменнике шихта подогрева ется за счет тепла оксидата до 110 °С. В нижнюю часть колонны подают воздух, предварительно подогретый водяным паром также до 110 °С в подогревателе 7. На схеме показана полая окислительная колонна со встроенными змеевиками для отвода тепла. Также может использоваться более эффективная тарельчатая колонна, в которой осуществляется прямоток между шихтой и воздухом. В этом случае оксидат выводится из верхней части колонны. Отработанный воздух вме сте с парами изопропилбензола, кислот и других примесей проходит вначале те плообменник 3 и конденсаторы 4, а затем отстойник-нейтрализатор 5, в котором содой или щелочью нейтрализуют кислоты. Отработанный воздух выводится из системы, а очищенный от кислот изопропилбензол с примесями возвращается в смеситель 7. Соли из нейтрализатора 5 также выводят из системы для утилиза ции.
Оксидат из нижней части окислительной колонны 2через теплообменник 3, где он охлаждается шихтой до 60 °С, направляется в колонну <?для концентриро вания гидропероксида изопропилбензола.
В связи с тем что гидропероксид при высоких температурах быстро разлага ется со взрывом, концентрирование проводят при глубоком вакууме (остаточ ное давление в кубе колонны 0,79 кПа). Поэтому температура в кубе не должна превышать 100 °С. Дистиллят колонны ^(изопропилбензол с примесями кислот и углеводородов) поступает в нейтрализатор 5, а кубовый продукт (концентри рованный гидропероксид изопропилбензола) — в реактор разложения 10. Туда же подается серная кислота в ацетоне. Однако несмотря на большие энергетиче ские и капитальные затраты, часто для концентрирования используют «двой ную» ректификацию (рис. 9.6), т.е. ректификацию в двух колоннах. В этом слу чае процесс концентрирования протекает в более безопасных условиях и не требу ется глубокий вакуум. Такой вариант еще более предпочтителен при совместном производстве фенола, ацетона и пропиленоксида, так как на эпоксидирование мо жет направляться разбавленный гидропероксид (30—35 %), а концентрация гидропероксида вдистилляте второй колонны составляет 35—45 %. Разложение проводят при 60 °С. При этом тепло отводится за счет испарения ацетона. Пары ацетона конденсируются в конденсаторе 77, и ацетон возвращается в реактор.
248
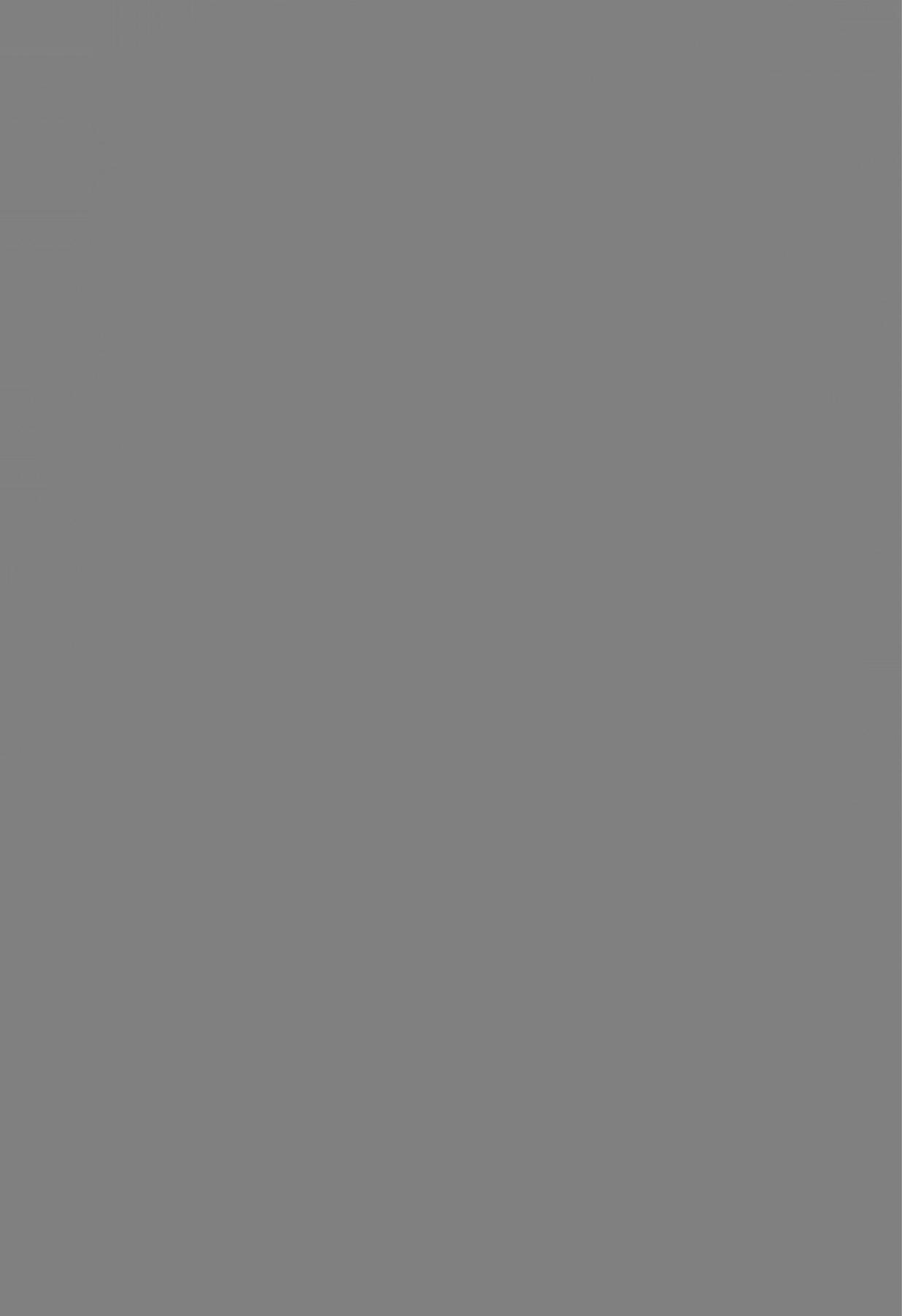
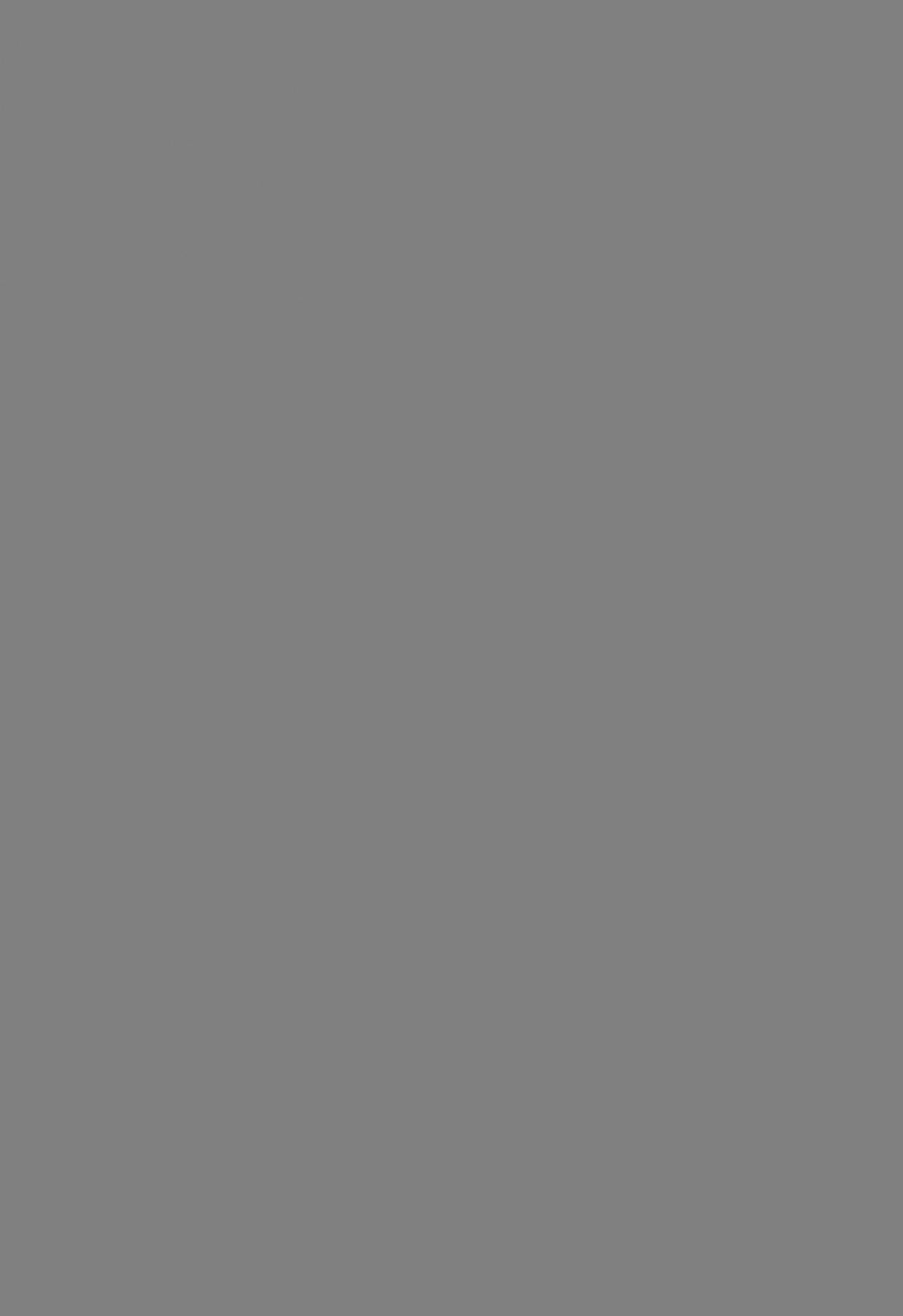