
книги / Принципы технологии основного органического и нефтехимического синтеза.-1
.pdfпри высоких скоростях подачи жидкого сырья (15—25 ч '"'), мольном соотноше нии бензола и пропилена, равном (7—8) : 1, температуре на входе в реактор 210—215 и 250—255 °С на выходе из реактора.
Продукты алкилирования перед подачей их в реактор переалкилирования изотермического типа охлаждают в холодильнике 7до 220 °С. Катализатор при этом не дезактивируется, так как не контактирует с пропиленом. Затем продук ты переалкилирования направляют в депропанизатор 3 для отделения прежде всего пропана, содержащегося в пропан-пропиленовой фракции. Кубовый про дукт направляют в колонну 4пля отделения непрореагировавшего бензола. По следний возвращают в реактор 1. Кубовый продукт колонны 4 направляют в ко лонну 5, где из него выделяют целевой продукт — кумол (изопропилбензол). В качестве промежуточного продукта в колонне 5выделяютдиизопропилбензо лы, которые направляют в реактор 1. В качестве кубового продукта в колонне 5 выводят полиалкилбензолы. Смесь исходных реагентов вначале нагревается за счет тепла продуктов переалкилирования втеплообменнике 8, охлаждая их, а за тем перегревается до температуры алкилирования в подогревателе 6.
Необходимо отметить, что мы рассмотрели только принципиальную техно логию из-за отсутствия данных по длительной промышленной эксплуатации процесса алкилирования на цеолитных катализаторах. Естественно, мы не оста новились на всех возможных путях создания экологически чистого производст ва на основе этой технологии. Однако только отсутствие в ней кислот приводит к резкому уменьшению образования кислых сточных вод, а следовательно, ис ключает стадию их нейтрализации. С этой точки зрения такая технология более приемлема, чем существующие в промышленности и основанные на кислотных катализаторах или на AICI3 . Однако одновременно с моноалкилбензолами ца цеолитных катализаторах получают полиалкилбензолы, протекают процессы крекинга изопропилбензола с образованием этилбензола и толуола, изомериза ция изопропилбензола в н-пропилбензол и полимеризация пропилена. Следо вательно, для создания безотходного производства необходимо найти примене ние перечисленным веществам в качестве целевых продуктов.
Этилбензол можно также получать при алкилировании бензола как чистым этиленом, так и газами, содержащими не менее 10 % этилена, в паровой фазе в
присутствии кристаллического алюмосиликатного цеолита (фирма «Mobil» и «Badger», США). Такой катализатор не вызывает сильную коррозию и позволяет использовать обычные конструкционные материалы. В частности, применение цеолитного катализатора ZSM-5 позволяет проводить реакцию с разбавленным этиленом при концентрациях 15—20 % (мае.). При этом можно использовать от ходящий газ многих нефтехимических производств (например, каталитический крекинг в псевдоожиженном слое). Обычно эти газы используют в качестве топ лива.
Газы нефтехимических процессов требуют той же очистки перед алкилиро ванием, что и топочные газы (главным образом удаление оксида углерода). Ос новными разбавителями этилена являются этан, метан, водород, азот и оксид углерода, которые можно использовать в качестве топлива после отделения ал килата. Процесс алкилирования можно проводить и без предварительной очи стки газов от СО2, воды и H2S (их отделение проводят с помощью стандартных
операций), но тогда будет наблюдаться повышенное «старение» катализатора. Если провести отмывку щелочью H2S и СО2 и осушку охлаждением, то получен
ный газ будет иметь следующий состав (% об.): метан — 37; этан — 19; эти-
i 4 * |
2 1 1 |
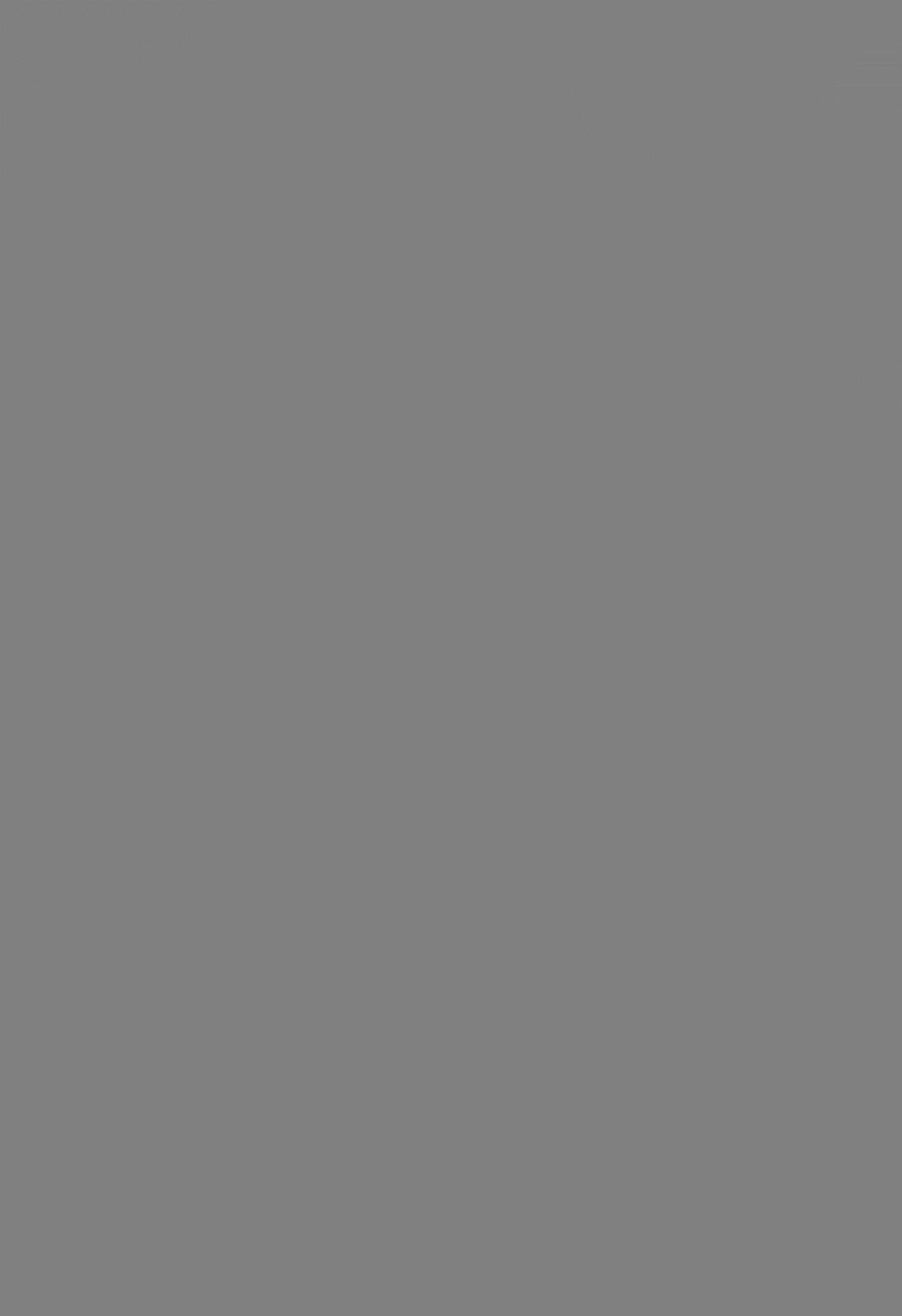
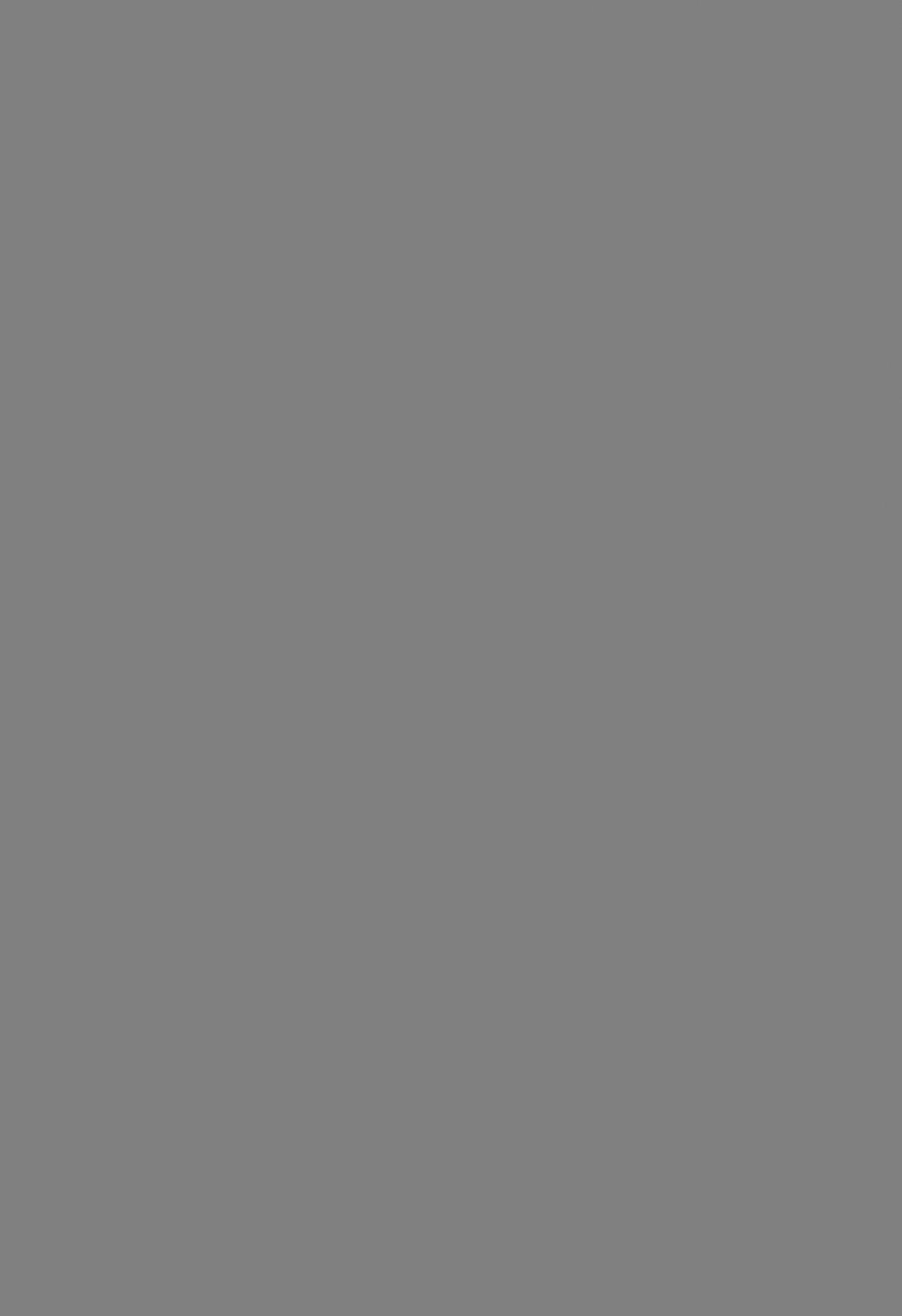
|
Т а б л и ц а |
7 .2 . Показатели |
процесса алкилирования |
бензола пропиленом на различных катализаторах |
|
||||||||||
Катализатор |
|
Мольное со- |
р, МПа |
л °с |
Расход ка |
Выход |
Концентрация |
Конвер- |
Состав |
алкилата. |
% (мае.) |
||||
|
|
|
риир |
|
|
|
тализатора, |
ИПБ с |
пропилена в |
сия про |
|
|
|
||
|
|
птипш1пи ^niiv |
|
|
|
бензол |
ИПБ |
полиал- |
|||||||
|
|
бензол |
|
: оле |
|
|
|
кг/т ИПБ |
1 м3 |
реак |
исходном сы |
пилена, % |
|||
|
|
фин |
|
|
|
|
тора, |
кг/ч |
рье, % (об.) |
|
|
|
килбензолы |
||
Хлорид алюминия |
2,5 |
: |
1,0 |
0,1 -0,5 |
70 -9 0 |
20 |
150-250 |
35 -80 |
99 |
6 0 -7 0 |
31 -26 |
3 - 6 |
|||
Фосфорная кислота на |
4,0 |
: |
1,0 |
1,5-2,5 |
250 |
4 - 6 |
150-300 |
35 |
70 -90 |
76 |
21 |
3 |
|||
кизельгуре |
|
|
|
|
|
|
|
|
|
|
|
|
|
|
|
Серная кислота |
|
4,0 |
: |
1,0 |
0,4 -1,0 |
3 5 -4 0 |
120-150 |
200 |
35 -8 0 |
99 |
73 |
24 |
2 - 3 |
||
Алюмосиликат |
|
3,0 |
: |
1,0 |
3,0- |
1,0 |
350 |
10 |
— |
|
35 -8 0 |
50 -70 |
72 |
24 |
3 |
|
|
|
|
|
|
|
|
|
|
|
|
|
|
|
|
Ортофосфорная |
кисло |
1,2 |
: |
1,0 |
1,2 - |
1,0 |
50 |
10 |
150 |
3 0 -4 0 |
— |
45 |
44 |
1 |
|
та + фторид бора |
( 1:1) |
|
|
|
|
|
|
|
|
|
|
|
|
|
|
Т а б л и ц а 7.3. Технико-экономические показатели установок производства изопропилбензола на различных катализаторах мощностью 200 тыс. т/год
Катализатор |
Расход |
катализа |
Общее число ап |
Капитальные |
Численность об |
Эксплуатацион |
Себестоимость |
Основные |
меро |
|
тора, % |
от изо |
паратов, шт. |
вложения, |
служивающего |
ные расходы, |
изопропилбензо |
приятия по |
охра |
|
пропилбензола |
|
уел. ед. |
персонала |
усл.ед./т |
ла, усл.ед./т |
не природы |
Хлорид алюминия |
0,70 |
54 |
2,926 |
68 |
15,22 |
146,12 |
Очистка сточ |
|
|
|
|
|
|
|
ных вод |
Фосфорная кислота |
0,40 |
40 |
2,877 |
52 |
14,15 |
143,58 |
— |
|
|||||||
на кизельгуре |
|
|
|
|
|
|
|
Трифторид бора на |
0,003 |
45 |
2,915 |
52 |
14,45 |
145,80 |
Очистка отхо |
A IA |
|
|
|
|
|
|
дящих газов ал |
|
|
|
|
|
|
|
килирования |
Цеол итсодержащие |
0,03 |
45 |
2,952 |
52 |
14,52 |
145,20 |
— |
|
катализаторы
ем. Технология обладает высокой эффективностью и при конверсии олефина до 99 % дифференциальная селективность по моноалкилбензолу достигает 91 %. Конверсия бензола за один проход — 30—40 %. Образующиеся в ходе процесса побочные продукты (диалкилбензолы) используют для получения целевого про дукта за счет совмещения реакции алкилирования с реакцией переалкилирования.
Для обеспечения полного использования бензола используют принцип рецирку ляции. Характерной особенностью данной технологии является наличие не скольких рециркуляционных циклов, охватывающих реакторную и раздели тельные подсистемы. В данном случае они направлены на полное использова ние исходного сырья — рецикл по бензолу, на использование побочных продук тов для получения целевого моноалкилбензола (принцип полноты использования отходов) — рецикл по диалкилбензолу, на повышение эффективности процес са — рецикл по бензолу, ди- и полиалкилбензолам, обеспечивающий опти мальную структуру каталитического комплекса. Организация этих рециркуля ционных потоков становится возможной за счет реализации принципа полноты
выделения всех продуктов из реакционной смеси. Технология обладает невысоким энергопотреблением за счет использования тепла реакции, хотя необходимо от метить, что эта энергия используется недостаточно из-за низкого ее потенциала. Существенным недостатком технологии жидкофазного алкилирования на ката лизаторах на основе хлорида алюминия является высокое потребление воды, ко торая используется для приготовления щелочных растворов и промывки в скрубберах и превращается в кислотные, щелочные или солевые стоки.
Принципы в технологии алкилирования бензола на гетерогенных катализато рах. Технология вобрала в себя все принципы, характерные для жидкофазного
алкилирования, но, кроме того, обладает и рядом дополнительных черт, делаю щих ее особенно привлекательной. В гетерогенно-каталитическом алкилированиии существенно выше степень использования тепла реакции. Это становится возможным, поскольку температура проведения процесса достигает 250 °С. Практически отсутствуют водные солевые, щелочные и кислотные стоки (реали зован принцип минимального расходования воды и использования ее кругооборота),
так как отсутствует необходимость очистки алкилата от каталитического ком плекса. Наконец, использование парофазных гетерогенно-каталитических про цессов позволяет с большей легкостью нежели для жидкофазных создавать ап параты и технологические линии большой единичной мощности.
Г Л А В А 8
П РО И ЗВО ДСТВО СТИРОЛА И ОКСИДОВ О ЛЕФ И Н О В
Стирол является одним из многотоннажных мономеров для производства как пластических масс (полистирол), так и синтетических каучуков. Его произ водство только в США превышает 4,0 млн т/год. Основным методом производ ства стирола является дегидрирование этилбензола. В последнее время все боль шее значение приобретает и совместное получение стирола и оксида пропилена. В этом случае его получение основано на дегидратации метилфенилкарбинола, который образуется в результате эпоксидирования олефина гидропероксидом этилбензола. В свою очередь, оксиды олефинов можно получать различными способами, например через соответствующий хлоргидрин или прямым окисле нием олефинов. Наибольшее распространение получили производства оксидов этилена и пропилена.
8.1. ПРОИЗВОДСТВО СТИРОЛА ДЕГИДРИРОВАНИЕМ ЭТИЛБЕНЗОЛА
Теоретические основы процесса дегидрирования. Основную реакцию дегидри
рования можно представить следующим образом:
С6Н5С2Н5 «=* С6Н5СН=СН2 + Н2
Процесс дегидрирования относится к типу гомолитических превращений, в которых важную роль играет хемосорбция реагентов на активных центрах (за счет электронных переходов с участием катализатора ослабляются или полно стью разрываются химические связи в адсорбированной молекуле). В равновес ном процессе гидрирования — дегидрирования каждая элементарная стадия об ратима.
Реакция дегидрирования — эндотермичная, поэтому высокая температура способствует ее протеканию (табл. 8.1). Кажущаяся энергия активации процесса дегидрирования этилбензола довольно высока и равна 152 кДж/моль. Это опре деляет сильную зависимость скорости реакции от температуры. Равновесие ре акции определяется уравнением изменения свободной энергии:
Д(7 = 29 720 —31,1 Г. |
(8.1) |
Согласно принципу Ле Шателье—Брауна, повышению конверсии способст вует снижение исходного парциального давления этилбензола (см. табл. 8. 1 ).
Этого можно добиться, проводя процесс при пониженном общем давлении или разбавляя этилбензол инертным веществом, например водяным паром, азотом или диоксидом углерода, при сохранении общего давления, близкого к атмо сферному. Для того чтобы определить оптимальное разбавление, выведем общее уравнение для равновесия такого процесса.
216
Т а б л и ц а 8.1. Конверсия этилбензола (при разбавлении его водяным паром в мольном соотношении п : 1)
Температура, |
К онстанта |
равно |
К онверсия |
этилбензола, % |
|
|
° С |
весия А'р, |
моль |
п= 16 |
|
|
|
|
|
я = 0 |
/ 7 = 18 |
/7 = 19 |
/ 7 = 20 |
|
5 2 0 |
0 ,0 3 4 |
18 |
5 4 |
55 |
56 |
57 |
5 4 0 |
0 ,0 5 6 |
23 |
6 2 |
68 |
6 8 |
6 9 |
5 6 0 |
0 ,0 8 9 |
29 |
70 |
71 |
7 2 |
73 |
5 8 0 |
0 ,1 3 5 |
35 |
76 |
77 |
78 |
7 9 |
6 0 0 |
0 ,1 9 9 |
41 |
8 2 |
83 |
8 4 |
85 |
6 2 0 |
0 ,2 9 5 |
4 8 |
8 6 |
8 7 |
88 |
8 9 |
6 4 0 |
0 ,4 3 2 |
55 |
9 0 |
9 0 |
91 |
91 |
Если в исходной смеси содержится 1 моль этилбензола и Л/ Нг0 моль водяно
го пара, Л/А, Л/в, Mz моль этилбензола, водорода и стирола, а равновесная кон версия этилбензола составляет хА, то при равновесии общее число молей будет равно
МА 1 хА, Л/в Mz хА, Л/ Н20 = М н2о 5
X М — 1—*А+2хА+ М Нг0 = 1+хА+ Л/Н20,
тогда
К р = К м( £ М ) л\ / С = ХьР<*ш/ [ ( 1 - х а )(1 + х а + Л / Н20)] . |
(8.2) |
Если температура реакции равна 580 °С, то Кр = 0,135, и тогда при />обш ~
= 0,1 МПа (1 кгс/см2) и в отсутствие разбавителя |
получим |
АГр(1-ха)(1+хл) = ха2. |
(8.3) |
Решая квадратное уравнение (8.3), находим хА = 0,36. Если же исходный
этилбензол разбавить водяным паром (в мольном соотношении 10 |
: 1 ), то, решая |
квадратное уравнение (8.3), получаем |
|
АГр(1-ха)(1+ха +10) = хА, откуда х = 0,713. |
(8.4) |
Таким образом, процесс дегидрирования этилбензола необходимо прово дить при достаточно высокой температуре (600—630 °С) при разбавлении водя ным паром в массовом соотношении (2,5—3): 1 и общем атмосферном давле
нии. При дегидрировании этилбензола происходит отщепление водорода, т.е. объем системы возрастает. Следовательно, повышению степени конверсии бла гоприятствует низкое давление. Так, при 595 °С и р - 0,1 МПа равновесная кон версия этилбензола равна 40%, а при /> = 0,01 МПа — 80 %.
В качестве катализаторов дегидрирования применяют сложные композиции на основе оксидов цинка или железа. Раньше наиболее распространенным был катализатор стирол — контакт на основе ZnO. В последнее время используют главным образом железооксидные катализаторы, содержащие 55—80 % FejCb, 2—28 % Сг20 3, 15—35 % К2С 0 3 и некоторые оксидные добавки. В нашей стране
217
широко используется катализатор К-24 следующего состава (% мае.):
2,0 -з- 2,6. Значительное содержание К.2СО3 в катализаторе обусловлено тем, что
он способствует дополнительной самогенерации катализатора за счет конвер сии углеродистых отложений водяным паром. Катализатор работает непрерыв но 2 мес., после чего его регенерируют, выжигая кокс воздухом. Общий срок ра боты катализатора — 2 года.
При дегидрировании этилбензола наряду со стиролом образуются побочные продукты. В наибольших количествах образуются бензол и толуол по следую щей схеме превращений:
f^ll
Поэтому в образующемся газе кроме водорода содержится метан, этилен, этан и оксиды углерода (за счет конверсии кокса). Таким образом, селектив ность дегидрирования этилбензола зависит от катализатора, температуры, сте пени разбавления водяным паром и конверсии этилбензола. Дифференциаль ная селективность по стиролу выражается следующим уравнением:
Фет = d [Стирол]/*/ [Этилбензол] =
(8.5)
= [1 - (г4 + г5)/(п - /•_,)]/[! + (r2 + г3)/(г, —г_|)].
Видно, что селективность сильно падает, если фактическая степень конвер сии приближается к равновесной (r_i = г,). Следовательно, разбавление паром, которое увеличивает равновесную степень конверсии, способствует росту се лективности. Повышение температуры увеличивает как равновесную конвер сию, так и выход побочных продуктов, в том числе кокса, за счет активизации побочных реакций. Оптимальными, таким образом, оказываются температур ные условия 580—600 °С, при которых одновременно обеспечиваются удовле творительная конверсия и селективность. Кроме того, при соответствующих степенях разбавления водяным паром и температурах существует своя опти мальная фактическая степень конверсии (см. табл. 8 .1 ). Следовательно, можно
выбрать необходимые условия, позволяющие достигать экономически целесо образную степень конверсии. При надлежащем подборе катализатора и условий проведения процесса можно проводить дегидрирование этилбензола в стирол с селективностью = 90 %.
Технологическое оформление процесса. Возможны три основных варианта оформления реакторного узла. Первоначально процесс проводили в трубчатом реакторе со стационарным слоем катализатора, в межтрубное пространство ко торого подавался для обогрева топочный газ (рис. 8.1, а). В этом аппарате про филь температуры близок к изотермическому, что позволяет получать достаточ -
2 1 8
Пары этилбензола |
Пар 700JC |
и воды |
Этилбензол |
|
|
|
Водяной |
Топливный |
пар |
газ |
|
х
Я
о
Реакционный
►
Реакционный
газ
а |
о |
в' О о |
в ft
Рис. 8.1. Контактные аппараты для получения стирола:
а — трубчатый; б — адиабатический; в — кольцевой (вертикальный в' и горизонтальный в" разрезы)
но высокую конверсию при хорошей селективности. В таких аппаратах тепло частично подводится с перегретым паром, которым разбавляется этилбензол, а остальное тепло —с помощью топочных газов. Однако с ростом единичной про изводительности трубчатого реактора (увеличением его диаметра) сильно про является температурная неравномерность по радиусу аппарата. Поэтому для достижения необходимой мощности приходится параллельно устанавливать ряд аппаратов, что приводит к увеличению капитальных затрат и усложнению управления такими установками. В связи с этим в 70-х годах прошлого века по явились аппараты со сплошным слоем катализатора без поверхностей теплооб мена. В этих аппаратах тепло целиком подводится в виде перегретого водяного пара, и они работают в адиабатических условиях. В таком единичном аппарате происходит изменение температуры по высоте аппарата с 600—620 до 540— 570 °С, что позволяет достигнуть конверсии этилбензола порядка 40 % (как и в изотермических аппаратах). Впоследствии в промышленности начали применять многоступенчатые (2- или 3-ступенчатые) адиабатические аппараты с промежу точным обогревом реакционной массы (рис. 8.2). При этом в промежуточных теплообменниках реакционная масса вновь подогревается перегретым паром до 600—630 °С. Такие аппараты обеспечивают высокую конверсию этилбензола при относительно низких капитальных затратах (используется только один ре актор).
В последнее время начали использовать так называемые кольцевые реакто ры (рис. 8.1, в). В этих аппаратах имеется два-три слоя катализатора, в которые подается смесь этилбензола и водяного пара. При этом в первый слой подается весь этилбензол и часть водяного пара, а в последующие слои подается только
219
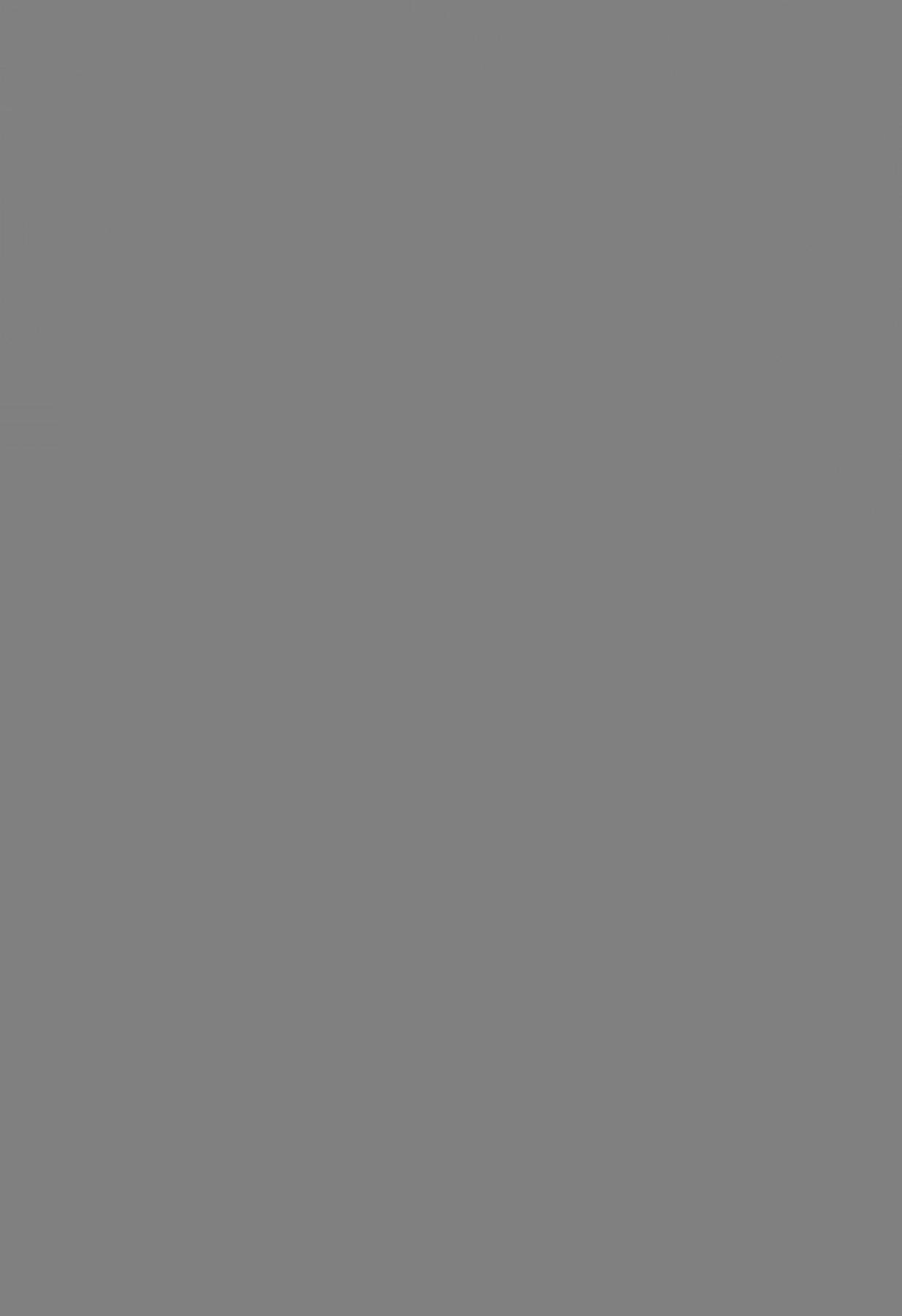